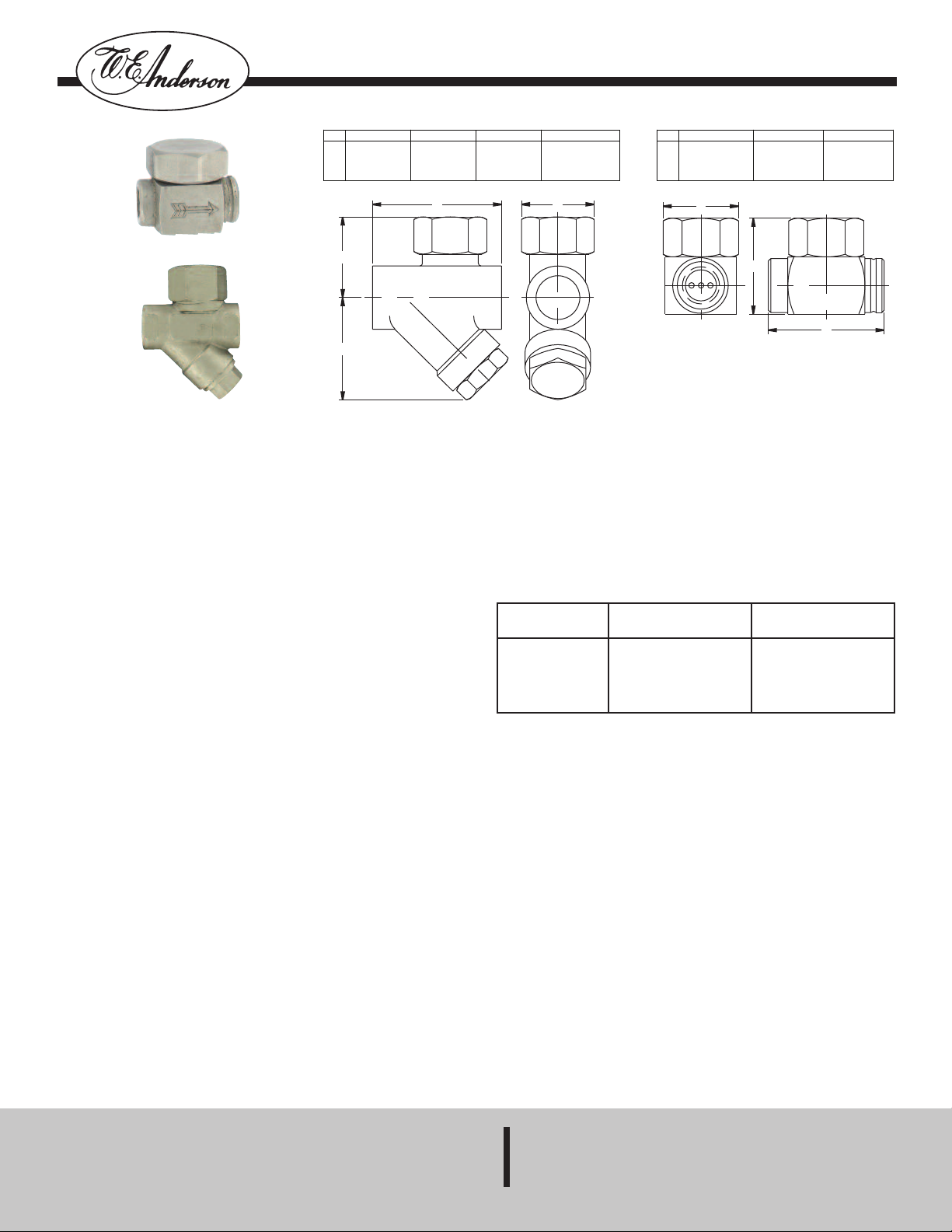
SIZE
3/8˝
1/2˝
3/4˝
1˝
A
3˝ (76.2MM)
3˝ (76.2MM)
3˝ (76.2MM)
3-1/4˝ (82.5MM)
B
2-3/8˝ (60.3MM)
2-3/8˝ (60.3MM)
2-3/8˝ (60.3MM)
2-1/2˝ (63.5MM)
C
1-7/8˝ (47.6MM)
1-7/8˝ (47.6MM)
1-7/8˝ (47.6MM)
2-1/8˝ (53.9MM)
D
1
-11/16˝ (42.84MM)
1
-11/16˝ (42.84MM)
1
-11/16˝ (42.84MM)
1
-11/16˝ (42.84MM)
SIZE
3/8˝
1/2˝
3/4˝
1˝
A
2˝ (50.8MM)
2-11/16˝ (76.2MM)
2-13/16˝ (71.4MM)
3-5/16˝ (84.1MM)
B
1-3/4˝ (44.5MM)
1-3/4˝ (44.5MM)
2-5/19˝ (58.7MM)
2-1/2˝ (63.5MM)
C
1-3/4˝ (44.5MM)
2˝ (50.8MM)
2-7/16˝ (61.9MM)
2-7/8˝ (73.0MM)
A
B
D
A
C
B
C
Series TDST Thermodynamic Steam Trap
Specifications - Installation and Operating Instructions
No Strainer
With Strainer
Series TDST Thermodynamic Steam Traps control
steam and condensate movement to maximize removal of
latent heat from steam for efficient system operation. The
thermodynamic trap has cyclic on-off operation with a disk
that is pushed open by incoming condensate and closes
tightly when steam tries to escape. The compact design
allows the steam trap to be mounted in any position and
models available with an integral strainer remove the
need for additional apparatus. When the trap is mounted
vertically, it self-drains, making it freeze-resistant. The
trap also handles water hammer, superheat, is resistant to
internal and external corrosion, and is easy to install. A
hardened 316 SS disc is the only moving part in the trap
ensuring long service life. Audible discharge cycling
makes it simple to check steam trap operation.
INSTALLATION
1. Blow out the piping thoroughly to remove loose scale
and dirt before installing the trap. When installing the trap
use pipe dope or sealing tape sparingly when attaching
the trap to the piping.
2. Install the trap as close as possible to the equipment
being drained in a location easily accessible for
maintenance and inspection. Be certain to install with flow
in the proper direction shown on the steam trap body. For
freeze-proof operation, install the trap so flow direction is
vertical.
Note: Approved practice is to install a separate trap on
each piece of apparatus to be drained.
3. To ensure easy maintenance and service, install an
isolation valve on each side of the trap and install a
strainer ahead of the inlet connection to the trap for the
SSSD models. The strainer must always angle downward.
Note: Piping upstream and downstream of the trap should
be at least equal to or one size larger than the trap
connection.
Bulletin V-10-TDST
Line Size: 3/8˝, 1/2˝, 3/4˝, 1˝.
End Connection: Female NPT.
Wetted Materials: Body: 420F SS, Cap & Disc: 416 SS,
Strainer: SS.
Pressure Limit: 600 psig (41.3 bar).
Temperature Limit: 800˚F (426.67˚C).
Weight: See chart below.
Capacity: See capacity chart.
Connection (in)
3/8
1/2
3/4
1
SSSD Model Weight
in Lbs. (kg)
0.8 (0.36)
1.2 (0.55)
1.85 (0.86)
3.1 (1.8)
SSST Model Weight
in Lbs. (kg)
2.4 (1)
2.3 (1)
2.7 (1.2)
3.3 (1.5)
W.E. ANDERSON DIV., DWYER INSTRUMENTS, INC.
P.O. BOX 358 • MICHIGAN CITY, INDIANA 46360 U.S. A.
Phone: 219/879-8000 www.dwyer-inst.com
Fax: 219/872-9057 e-mail: info@dwyermail.com
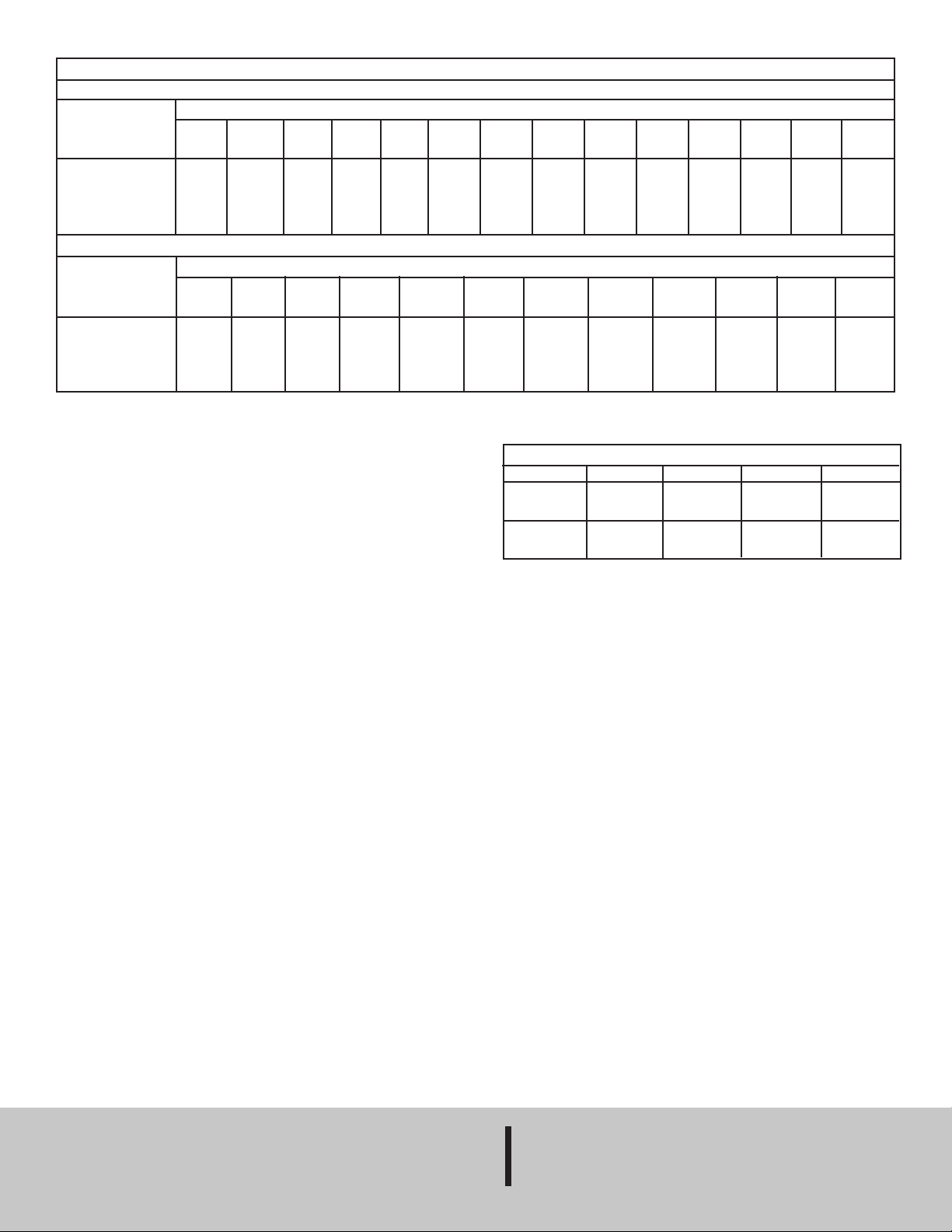
NPT
Connection
/8˝
3
1/2˝
3/4˝
˝
1
NPT
Connection
3/8˝
1/2˝
3/4˝
1˝
3.5
(0.24)
180
300
405
640
10
(0.7)
315
315
650
650
Capacity Chart
TDST-SSSD Maximum Capacity - lbs/hr 10°F Below Saturation
Differential Pressure psig (bar)
5
(0.34)
185
310
420
670
2
(1.4)
370
370
740
740
10
(0.7)
190
345
470
725
TDST-SSST Maximum Capacity - lbs/hr 10°F Below Saturation
0
30
(2.1)
425
425
800
800
20
(1.4)
200
410
560
865
50
(3.4)
520
520
1000
1000
30
(2.1)
215
465
640
980
50
(3.4)
245
575
810
120
ifferential Pressure psig (bar)
D
75
(5.2)
575
575
1100
1100
75
(5.2)
305
700
1000
147
100
(6.9)
800
800
1400
1400
100
(6.9)
370
810
1160
175
150
(10.3)
900
900
1540
1540
150
(10.3)
500
1000
1450
2200
200
(13.8)
1080
1080
1630
1630
200
(13.8)
610
1140
1670
2600
300
(20.7)
1280
1280
1760
1760
300
(20.7)
790
1410
2100
3250
400
(27.6)
960
1630
2430
3780
400
(27.6)
1380
1380
1930
1930
500
(34.5)
1100
1830
2750
4250
500
(34.5)
1480
1480
2070
2070
600
(41.3)
1250
2000
3050
4700
600
(41.4)
1650
1650
2200
2200
MAINTENANCE
When using the SSSD models it is strongly recommended
to blow-off accumulation in the strainer a day or two after
the system has been installed. A periodic blow-off or
cleaning of the strainer should be instituted.
If trap fails, close isolation valves and remove cap using a
suitable spanner. Dirt or sediment on the disc or body
seating will cause abnormal operation. To clean these
parts use a soft cloth and solvent. DO NOT WIRE BRUSH
OR USE ANY ROUGH IMPLEMENT. Reassemble the
unit with the groove in the disc facing down. Apply
antiseize compound on the cap threads. Avoid getting
compound on the disc or body seating surfaces. See the
torque table to the right for recommended torque values.
For the SSST option a peroidic cleaning of the strainer
should be instituted. Unscrew the strainer plug using a
suitable spanner, withdraw the screen and clean it or
replace it if damaged. To reassemble, reverse the
procedure. A periodic check of system calibration is
recommended. The Series TDST is not field serviceable
and should be returned if repair is needed (field repair
should not be attempted and may void warranty). Be sure
to include a brief description of the problem plus any
relevant application notes. Contact customer service to
receive a return goods authorization number before
shipping.
Trap Size
TDSTSSSD
TDST-SSST
Torque Values for Cover ft-lb (N-m)
3/8˝
65-75
(88-102)
105-115
(142-156)
1/2˝
85-95
(115-129)
105-115
(142-156)
3/4˝
105-115
(142-156)
105-115
(142-156)
1˝
120-130
(163-176)
105-115
(142-156)
©Copyright 2014 Dwyer Instruments, Inc. Printed in U.S.A. 3/14 FR# RV-443580-00 Rev. 2
W.E. ANDERSON DIV., DWYER INSTRUMENTS, INC.
P.O. BOX 358 • MICHIGAN CITY, INDIANA 46360 U.S. A.
Phone: 219/879-8000 www.dwyer-inst.com
Fax: 219/872-9057 e-mail: info@dwyermail.com