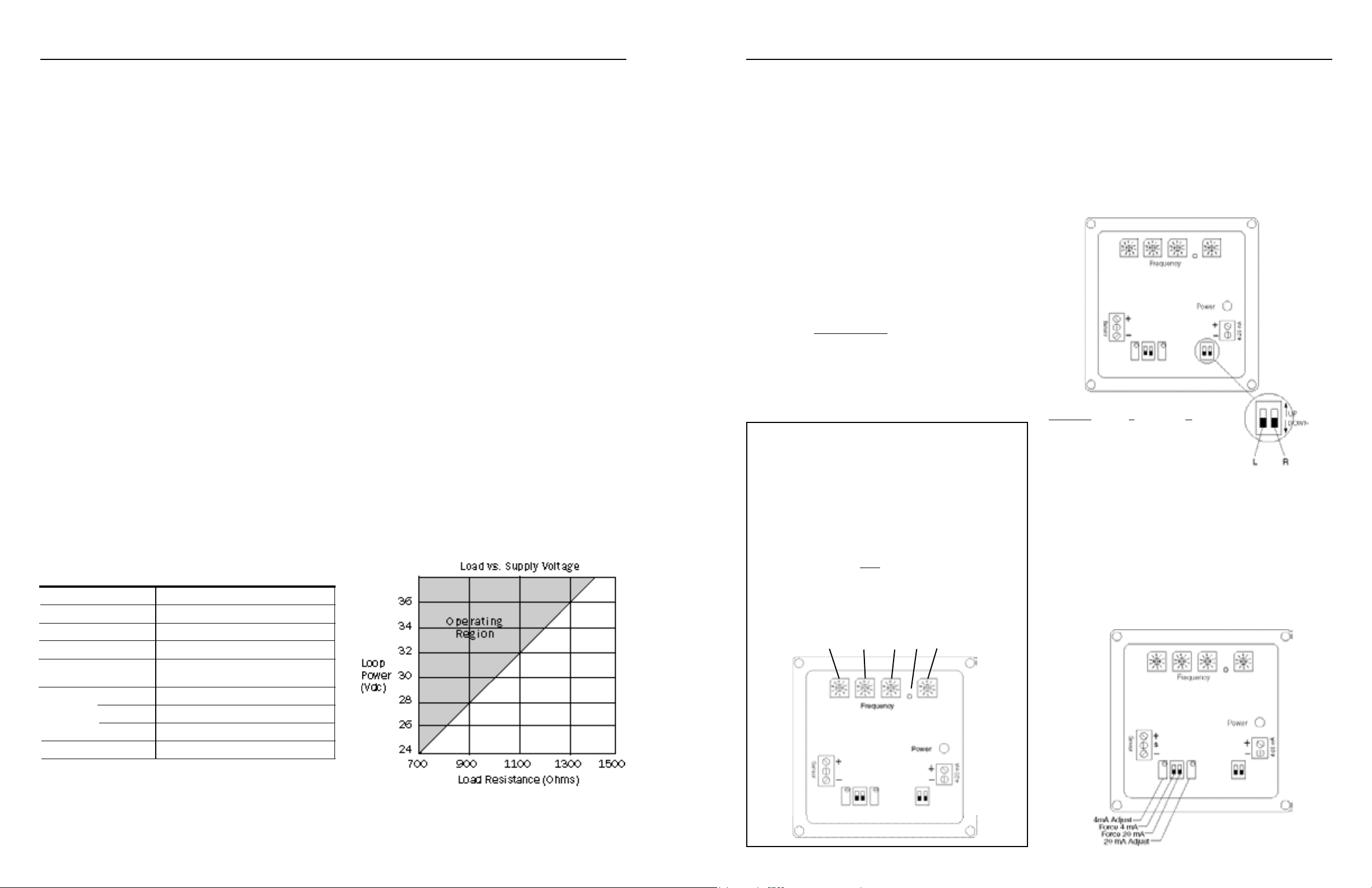
GENERAL INFORMATION, SPECIFICATIONS and INSTALLATION
SETTINGS, CALIBRATION and FREQUENCY
GENERAL INFORMATION INSTALLATION
The Dwyer Instruments Inc. Series BAT is a blind (nonindicating) 4 to 20 mA transmitter, designed for use with Series
EFS2, IEFS, PDWS, TBS and FLMG ow sensors. It accepts a
Mounting. The BAT-M can be mounted on the ow sensor.
The BAT-W wall mount comes with mounting feet and
requires four screws to attach it to any stable surface.
pulse frequency input from the ow sensor, and converts this
input into a continuous analog output signal. Power for the
transmitter is taken from the current loop itself, so only two
wires are required. The digital design makes it possible to span
the unit in the eld without tools. The frequency at which 20
mA is desired is entered on a set of rotary switches, and an
Connection. On either style of housing, the upper portion
must be removed to make connections. Use a standard hex
wrench (5/32” or 4 mm) to loosen the screws, then remove
the upper half. The connections are made to terminal blocks
in the upper half, which contains the potted electronics.
internal microcontroller automatically scales all other values
accordingly. An additional benet of the microcontroller is its
ability to average inputs, for smoothing of the output signal.
The degree of averaging can be selected in the eld, from 2 to
16 seconds.
Consult the Connections diagram before connecting to the
current loop. The only connections required on a BAT-M are
the positive and negative loop connections. On a BAT-W,
the sensor must also be connected, since it is remote from
the transmitter. Be careful to follow the color coding of the
For maximum environmental protection, the electronic
components are encased in a special semi-exible urethane
ow sensor wires in order to establish the correct polarity.
Incorrect polarity can damage the sensor.
potting material. The housing is cast from aluminum and
fuse-coated. The clamshell housing offered in the BAT-M is
connected directly to the ow sensor or, in the wall mount
version, BAT-W, provided with mounting feet.
The BAT will operate on a relatively wide range of current loop
voltages, 24 to 36 Vdc. Lower voltages limit the load that can
be applied to the loop without distortion of the signal. (See
Load/Supply chart if there is a question regarding voltage vs.
WARRANTY/RETURN
Refer to "Terms and Conditions of Sale" in our catalog or on
our website. Contact customer service to receive a Returns
Goods Authorization number before shipping your product
back for repair. Be sure to include a brief description of the
problem plus any relevant applciation notes.
load.) A built-in power regulator supplies the appropriate power
to the ow sensor.
Typical applications for this transmitter are telemetry (or
SCADA), distributed control systems, programmable controllers,
SPECIFICATIONS*
Power
Temperature
Input
Input Averaging
Response Time
Frequency Minimum
Maximum
Setting
Output
*Specications subject to change
24 to 36 Vdc
32 to 130˚ F (0 to 55˚ C)
Open-collector solid state sensor
2 to 16 seconds (switch selectable)
2 to 60 seconds; 90% of full-scale
(dependent on input averaging)
10 Hz (@20 mA)
999.9 Hz
4 Rotary DIP switches
Proportional 4 to 20 mA
SETTINGS
Setting Frequency. The BAT converts a train of off/on pulses
from the ow sensor into a continuous mA signal that ranges
from 4 mA at zero ow to 20 mA at the desired maximum ow.
The desired maximum is determined by the user and entered
as a frequency as follows:
Decide what ow rate should represent the top of the
1)
scale. This is ordinarily the maximum expected ow, or
a value just above it, in gallons per minute.
Locate the K-factor of the ow sensor (found on the
2)
meter or tting, or in the instruction manual, depending
on meter model). The K-factor is the number of pulses
the ow sensor produces per gallon of ow.
Calculate frequency, using this formula:
3)
K-Factor x Top Flow (GPM) = Frequency
60
Enter the frequency using the four rotary Frequency
4)
switches. Note the decimal point between the third
and fourth switches.
SETTING FREQUENCY EXAMPLE
In an installation with an estimated maximum ow rate
1)
of about 150 GPM, a ow rate of 170 GPM is selected
as the full-scale maximum, the ow at which the current
loop will register 20 mA.
In this example, the K-factor (found on the meter or
2)
tting, or in the manual) is “K = 54.50”.
Calculate the frequency as
3)
54.50 x 170
60
4)
Rounding to one decimal point, enter 154.4 on the
= 154.42
rotary switches by turning the rotary switch pointers
to the desired digits.
1 5 4
.
4
Setting Averaging Time. For most applications this step can
be ignored, as the standard setting will work ne. However,
when a particularly steady output signal is desired, or in a
large pipe, a larger averaging period may be desirable. Note
however that the averaging period requires a tradeoff, since
a longer averaging period implies a slower response time. If
steady signal is more important than fast response, increase
the averaging time as desired. See the diagram below for the
switch positions and their corresponding times.
Switch Position
Seconds L R
2 down down
4 down up
8 up down
16 up up
Checking Calibration
Normally it should not be necessary to check calibration, since
the digital design of this unit virtually eliminates drift. However,
there are two types of calibration check that can be performed.
Look at the diagram below to locate the 4 and 20 mA force
switches. To force the 4 mA output, put its switch in the up
position. Check the current output at the Power terminals, and
if necessary, trim to 4.00 mA using the appropriate trimpot.
Return the switch to the down position, and repeat the process
with the 20 mA switch and appropriate trimpot.

CONNECTIONS and TROUBLESHOOTING
CONNECTIONS
The Series BAT can be wired to either a mechanical meter or an
electromagnetic ow meter. See alternative congurations below.
B AT
TROUBLESHOOTING
Problem
No analog signal at
reading device
Output stuck at 4 mA
mA signal does not
match ow rate
Probable Cause Try...
Break in current loop
Dead power supply
Reversed polarity
No frequency input from ow sensor
Inadequate voltage
Wrong frequency setting
Check if loop indicator light is on
Check multimeter voltage on power supply
Check polarity
Check if ow sensor rotor is turning freely
(mechanical meters only)
Check ow sensor connections
Check ow sensor polarity
Be sure terminal blocks are rmly plugged in
With ow sensor disconnected, use short wire
to repeatedly short between sensor “sig” and
“-” terminals. Output should rise.
Verify 3-second pulse output (Series EFS2
and IEFS meters only)
Check load vs. supply chart
Review setting procedure
Check multimeter voltage on power supply
Dwyer Instruments, Inc. • 102 Indiana Highway 212 • Michigan City, IN 46360 • USA
(P) 219.879.8868 • (F) 219.872.9057 • 1.800.872.9141 • www.dwyer-inst.com
PL-OM-65200384-082012
8/20/12