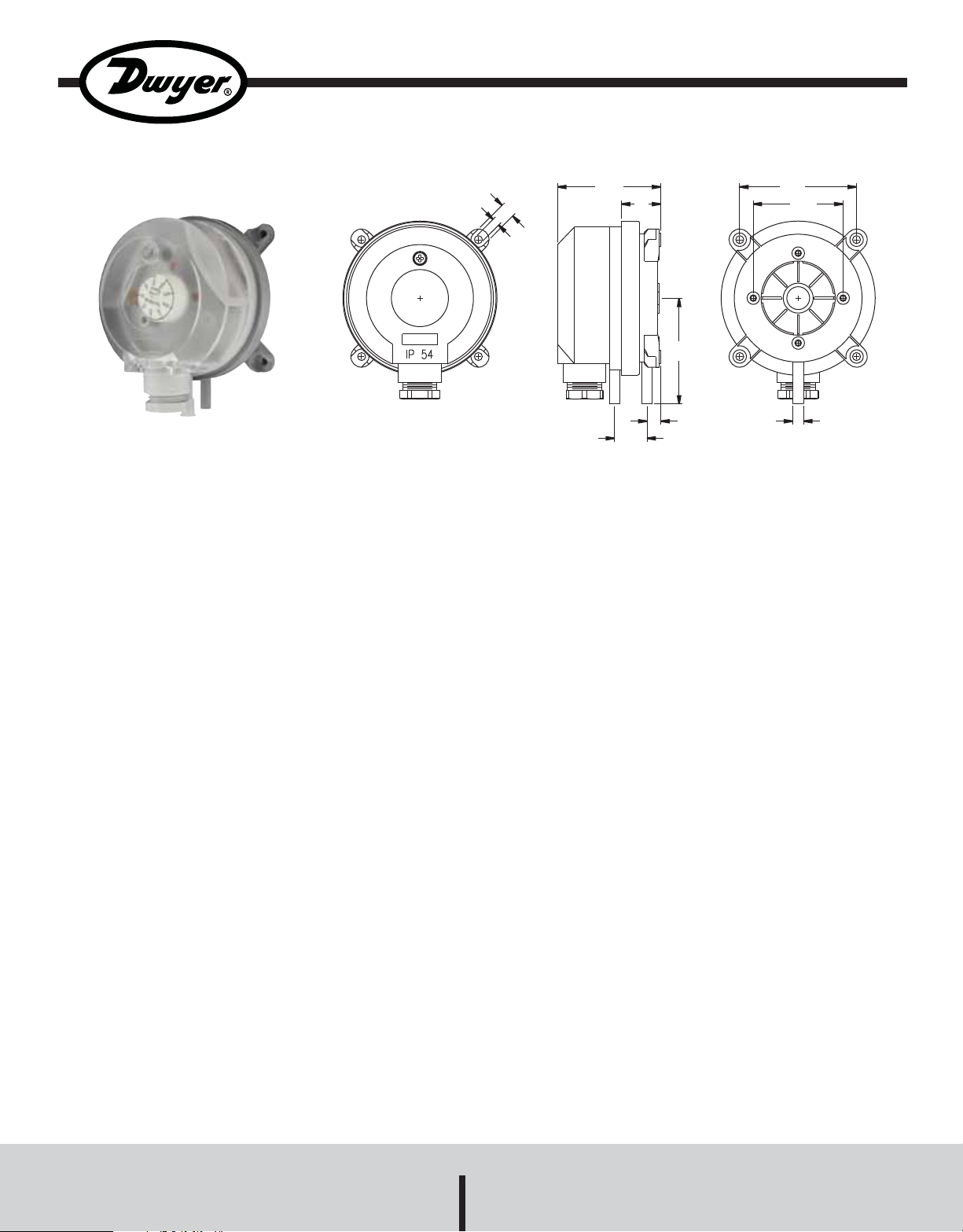
Series ADPS Differential Pressure Switch
Specifications - Installation and Operating Instructions
E-80-ADPS
The Series ADPS Adjustable Differential Pressure Switch is designed for
overpressure, vacuum, and differential pressure applications. The scaled
adjustment knob allows changes to the switching pressure to be made without a
pressure gage. The ADPS is available with settings from 0.08˝ w.c. (20 Pa) to 20˝
w.c. (5000 Pa). The silicone diaphragm and PA 6.6 body make the Series ADPS
perfect for use with air and other noncombustible gases. The Series ADPS can be
used in monitoring air filters, ventilators, and industrial cooling-air circuits along
with controlling air and fire-protection flaps and many other applications.
Use only with mediums such as air, or other noncombustible or non-aggressive
gases. Otherwise operating faults or accidents may occur.
Mounting Switch
First check the pressure switch to ascertain whether any damage is visible on the
housing. If the housing is leaky because of damage, the pressure switch must not
be used.
Switching pressure specifications apply to vertical installation which is also the
recommended position with pressure connections pointing downwards.
Only if there is no potential for condensate forming can you mount the pressure
switch horizontally. In this case, however, the switching values are approximately
0.08 in w.c. (20 Pa) higher as indicated on the scale. In the horizontal position, the
pressure switch should be mounted ‘lying down’ only (that is to say with the
electrical connections pointing upwards). Do not mount the pressure switch in a
hanging position (that is to say, not ‘overhead’ with the electrical connections
pointing downwards). Otherwise the device will function inaccurately.
a) Mounting with screws or brackets
Ø11/64
[Ø4.5]
2-9/16
[65]
1-31/32
[50]
Ø15/64
[Ø6]
21/64
[8.5]
2-17/64
[57.5]
(P2)
-
51/64
[18]
7/8
[22]
(P1)
2-21/64
[59]
19/64
[7.5]
+
SPECIFICATIONS
Service: Air and noncombustible, compatible gases.
Wetted Materials: Diaphragm material: Silicone; Housing material & switch
body: POM and PA 6.6; Cover: Polystyrene.
Temperature Limits: Process ambient temperature from -4 to 185˚F
(-20 to 85˚C).
Pressure Limits: Max. Operating Pressure: 40” W.C. (10 kPa) for all pressure
ranges.
Switch Type: Single-pole double-throw (SPDT).
Repeatability: ±15% FS.
Electrical Rating: Standard: Max., 1.5A/250 VAC, max. switching rate: 6
cycles/min.; Gold Contact Option: 0.4 A/ 250 VAC.
Electrical Connections: Push-on screw terminals. M20x1.5 with cable strain
relief or optional 1/2˝ NPT connection.
Process Connections: 5/16˝ (7.94 mm) outside diameter tubing, 1/4˝ (6.0 mm)
inside diameter tubing.
Mounting Orientation: Vertically, with pressure connections pointing
downwards.
Mechanical Working Life: Over 10
6
switching operations.
Weight: 5.6 oz (160 g).
Enclosure Rating: IP54.
Agency Approvals: CE, RoHS.
Installing Hoses
Important: Pressure tubing cannot be kinked. Pay particular attention to this point
if you run hoses over an edge. It is better to form a loop. If the hoses are kinked,
the device cannot function accurately.
1. To mount the pressure switch, L-shaped A-288 and S-shaped A-289
mounting brackets can be ordered separately. To secure the device on the rear
a) For connection to the pressure switch two fittings inherent in the housing are
provided for hoses with an internal diameter of 1/4˝ (6.0 mm).
side of the housing, only use the sheet metal screws (3.5 x 8 mm) which are
supplied together with the mounting brackets. Under no circumstances must
you use longer screws. Otherwise, the base of the housing could be punctured
1. Connect a hose with the higher pressure to socket P1 which is located on the
lower section of the housing.
resulting in the pressure switch leaking.
2. Connect a hose with the lower pressure to socket P2 which is located on the
2. You can also mount the pressure switch directly on a wall. To do this use
middle section of the housing.
screws with a maximum diameter of 0.315˝ (8.0 mm), if you use the outer
mounting lugs to screw the device in place. Do not tighten the screws so much
that the base of the device is deformed. Otherwise, the pressure switch can be
shifted out of position, or leak.
DWYER INSTRUMENTS, INC.
After you have installed the hoses, it is absolutely essential to check them for
tightness of fit at the connection points and to make sure that they run without any
kinks.
Phone: 219/879-8000 www.dwyer-inst.com
P.O. BOX 373 • MICHIGAN CITY, INDIANA 46361, U.S.A. Fax: 219/872-9057 e-mail: info@dwyer-inst.com
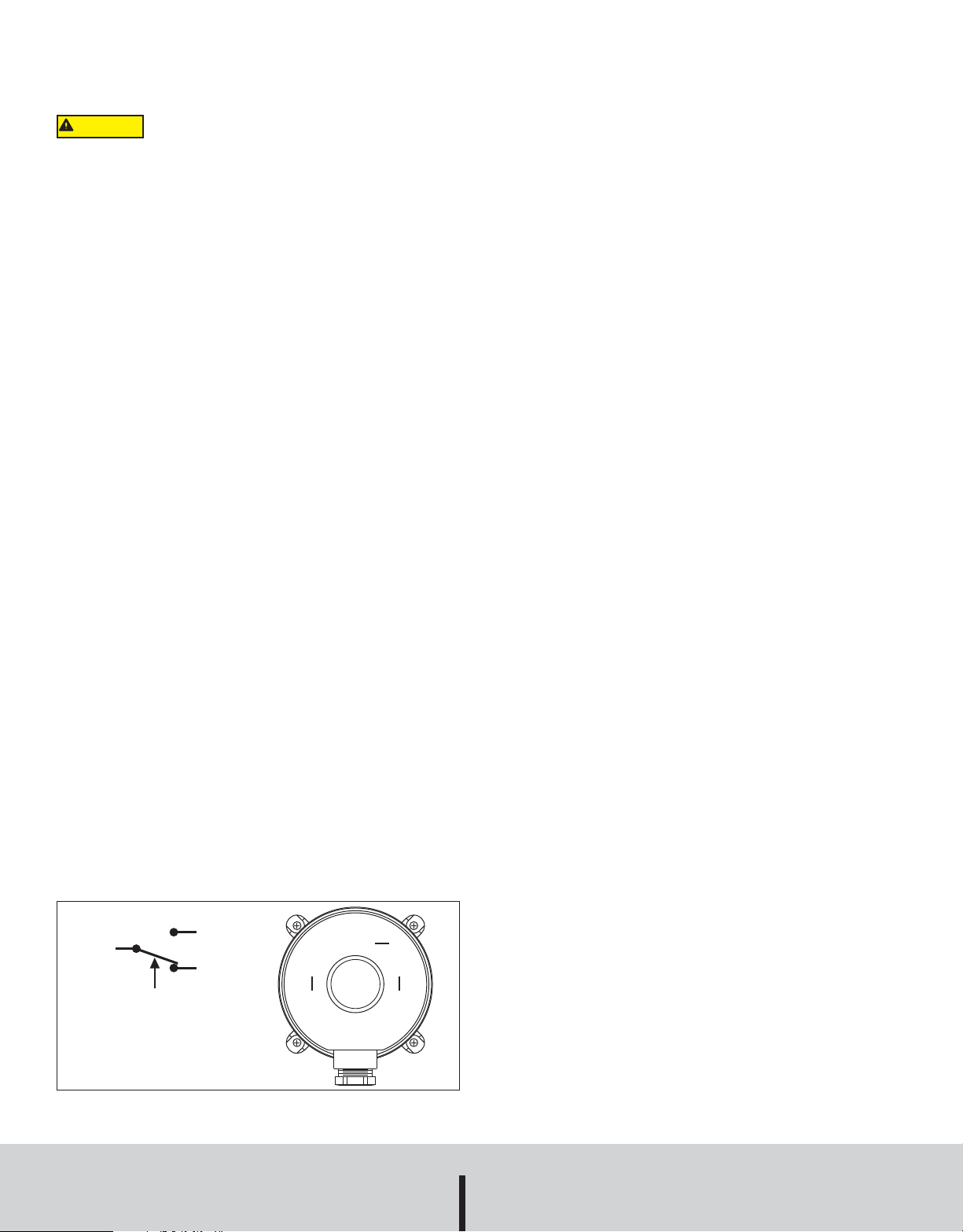
Electrical Connection
Work on electrical installations must only be carried out by electricians who are
specifically trained for this purpose.
CAUTION
a possible electric shock may result and the connected equipment may be
damaged. The connecting cable can be run to the pressure switch from three
sides, according to choice. The screw cable connection has a plug-in design for
this purpose. Rotate protective cover accordingly.
First make sure that there is no voltage on the connecting cable
while you are working on the electrical connections. Otherwise,
Setting the Pressure Range
Make absolutely certain that there is no voltage on the electrical connections
before you carry out any setting on the pressure switch. Otherwise, it could be fatal
if you accidentally touch the electrical connections or the metal adjusting screw
while you are performing the settings.
a) Use the adjustment dial to set the pressure which should trip the switch on an
increase of pressure.
1. The indications on the dial are only correct for the vertical mounting position.
For cable gland models, the seal in the screw cable connection is designed for
cables with alternative sheath diameters of 0.275˝ (7 mm) or 0.393˝ (10 mm). Only
use these sizes – otherwise the screw cable connection cannot seal adequately.
1. If using a 0.275˝ (7 mm) connecting cable, you can line up the press nut, the
plain washer and the sealing ring directly on the cable.
2. If using a 0.393˝ (10 mm) connecting cable, you must first break the inner
rubber ring out of the sealing ring directly on the cable. Then line up the press
nut, the plain washer and the sealing ring on the cable.
Wiring
The switching device in this pressure switch is designed as a change-over contact
as can be seen from the wiring diagram (Figure 1). The rest position is shown in
Figure 1 (pressure below the activation switch point on dial).
1. In the instance where pole 3 (COM) closes to Pole 2, the pressure is
increasing (NO).
2. In the instance where pole 3 (COM) closes to Pole 1, the pressure is
decreasing (NC).
Protect the feed line (to pole 3) by fuse, either in control system or along the line,
and do so with:
1. Max. 1.5 A / 250 VAC, if you are loading the contact with an resistive load;
2. Max 0.4 A / 250 VAC, if you are loading the contact with an inductive load
(such as relay);
3. Max. 0.1 A / 250 VDC, if you are using the pressure switch in the weak current
version with gold-plated contacts.
2. When the pressure falls, the switch returns to its resting position as soon as
the pressure falls below the dead band.
Attaching Cover
a) Insert the screw cable connection into the recess provided for this purpose on
the housing.
b) Then place the housing cover in position and screw it down evenly on to the
pressure switch.
Testing the Setting
Do not operate the system until the housing is closed. Otherwise there is the
possibility of an electric shock if you accidentally touch live parts.
Check the trip and reset pressures by slowly increasing the pressure and then
allowing it to fall again.
IMPORTANT: Observe the maximum permissible operating pressure of 40˝ w.c.
(10 kPa) which is indicated in the data sheet. Otherwise the pressure switch may
be damaged.
MAINTENANCE
Upon final installation of the Series ADPS Adjustable Differential Pressure Switch,
no routine maintenance is required. A periodic check of system operation is
recommended. The Series ADPS is not field serviceable and should be returned if
repair is needed (field repair should not be attempted and may void warranty). Be
sure to include a brief description of the problem plus any relevant application
notes. Contact customer service to receive a return goods authorization number
before shipping.
The connections are intended for crimp-type sockets, 0.25 in (6.3 mm).
1. Make sure the crimp connection is perfect, and that the cable lugs fit properly
on to the connections.
2. If you do not have any crimp-type sockets available, you can also use the
cable lugs which are supplied with mounted screw terminals. However, these
are only intended for rigid copper wire.
3. On flex, it is either necessary to crimp on strand end sleeves – and then you
can also screw the strands on – or to crimp cable lugs on directly as previously
described.
2 NO
3 COM
1 NC
P
1. Break Contact
2. Operating Contact
3. Power Supply Line
Figure 1
©Copyright 2010 Dwyer Instruments, Inc. Printed in U.S.A. 9/10 FR# R1-443602-00 Rev.1
1
23
DWYER INSTRUMENTS, INC.
Phone: 219/879-8000 www.dwyer-inst.com
P.O. BOX 373 • MICHIGAN CITY, INDIANA 46361, U.S.A. Fax: 219/872-9057 e-mail: info@dwyer-inst.com