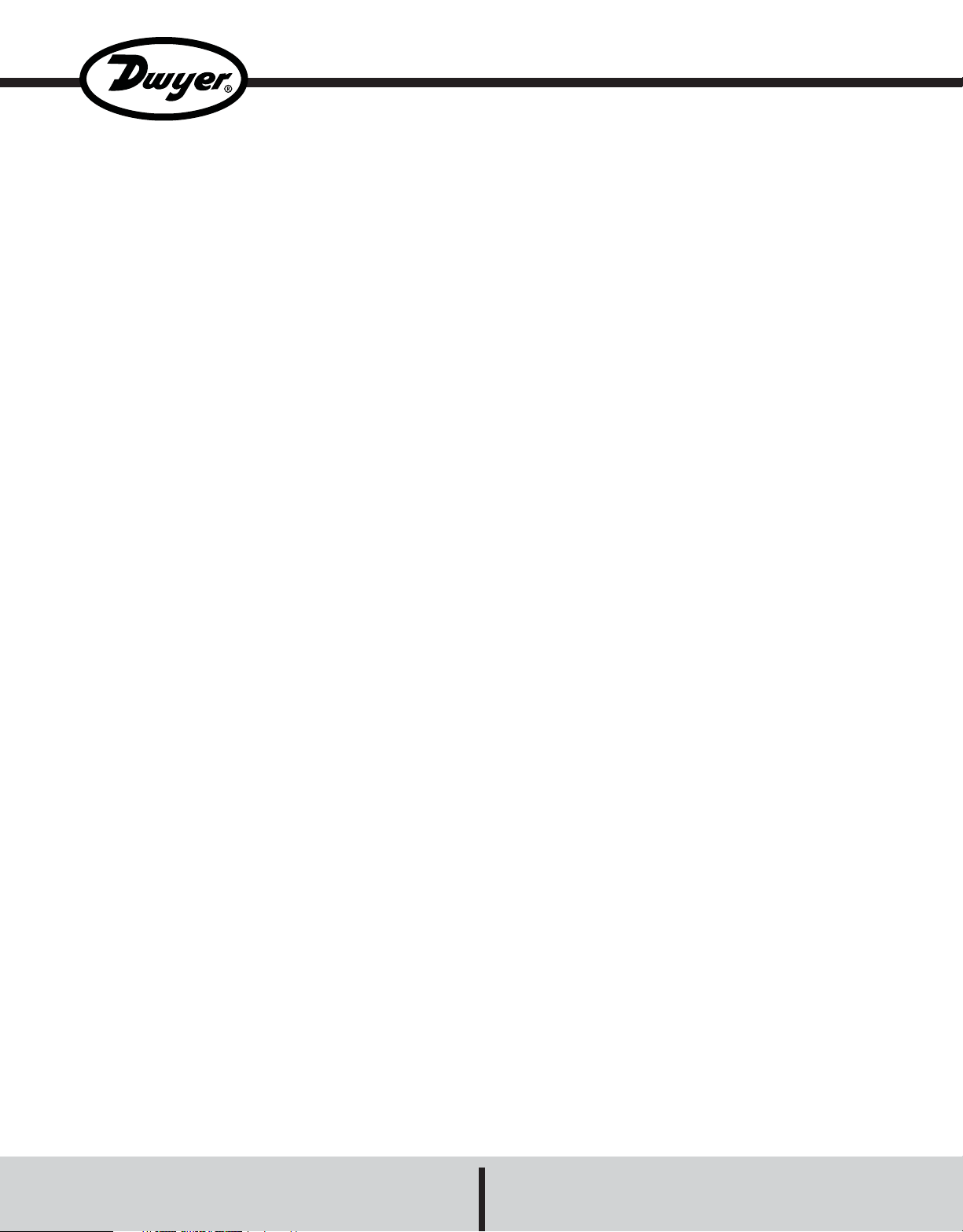
Bulletin A-1000
Series A-1000 Fitting Line
Specifications - Installation and Operating Instructions
The Series A-1000 quality tube fittings have been designed and manu-
factured to provide reliable leak-free connections in a wide variety of
applications. A reliable leak-free tubing system will be achieved by combining the proper selection and handling of tubing with the proper tube
fitting selection and installation. The following information is provided to
assist in the tube selection process.
Material
The tubing material chosen must be compatible with the system’s contained media, pressure and temperature, as well as with the environment in which it will be installed. Also, the tubing and fittings materials
should be similar for optimum sealing action to occur (stainless fittings
for stainless tube, brass fittings for copper tube, carbon steel fittings for
carbon steel tube, etc.). The mixing and contact of dissimilar materials
may leave the system susceptible to galvanic corrosion and/or not allow
proper tube fitting makeup to be achieved.
Pressure and Flow
The size of the tube’s outside diameter (O.D.) and the necessary wall
thickness are determined by the system’s pressure and flow requirements. Table A details the suggested tubing sizes and wall thickness for
use with instrumentation tube fittings. If no pressure is shown on the
table for a particular size, the tube is not recommended for use with
instrumentation tube fittings. The tubing system should not be utilized
above the tube’s maximum allowable working pressure.
Temperature
The system’s operating temperature may affect the initial choice of tubing material and may also affect the maximum allowable working temperature for the given tube size (see Table B for temperature stress factors).
Light Gas Service
To provide a successful connection for light gas service, the tubing must
have a thick enough wall to provide resistance for the setup action of the
ferrules to further compensate for the tube’s potential surface condition.
Handling and Installation
Surface scratches and gouges on tubing are a source of potential leaks.
Some precaution when handling the tubing can help reduce surface
scratches and maintain the surface finish as originally intended by the
manufacturer. Tubing should never be dragged across rocks, blacktop,
pavement, or tubing storage racks as scratches and gouges can occur.
Sharp blades should always be used in the tube cutters or hacksaws
used to cut the tubing so as to provide a clean, square cut. Dull cutting
blades can cause internal and external hanging burrs, and cause the
tubing to become oval and affect proper insertion within the fitting. As a
good handling practice, tubing should always be deburred prior to tube
fitting installation to help assure easy and complete tube insertion.
Additionally, for bent tube assemblies, it is important to bend tubing prior
to installing tube fittings, and to provide a sufficient straight length of tubing after the bend to allow the tube to be fully inserted into the fitting.
Also, to eliminate weight stress from the tubing upon the fitting and to
provide additional system support for vibration and thermal shock resistance, the tubing should always be supported by tube hangers, clamps
or trays.
Safety
To help ensure the safe and reliable performance of tube fitting products,
complete system design must be considered prior to the installation of
the tubing and tube fittings. Determining the design compatibility of
materials, media, flows, temperatures and pressures; as well as implementing proper installation, operation and maintenance of the system
are the responsibilities of the systems’ owners, designers and users.
Dwyer Instruments, Inc. Safety Reminders
All Dwyer Instruments, Inc. products are designed and manufactured
with safety in mind. The following is a limited list of general safety tips as
reminders of good safety practices:
• Do not install, tighten, or loosen a tube fitting while the system is
under pressure.
• Do not loosen a tube fitting, nut or plug to relieve or bleed system
pressure.
• Always use a back-up wrench to hold the tube fitting body steady
when tightening or loosening tube fitting nuts.
• There is no need to disassemble a new tube fitting prior to use.
• Use proper thread lubricants and sealants on tapered pipe threads.
• Very soft, pliable plastic tubing requires a tube insert.
• Tube fittings and tubing material should be similar (stainless steel
fittings on stainless steel tubing, etc.) with the tubing material being
fully annealed.
• Do not weld tube fittings that are assembled. Prior to welding remove
the nut and ferrules and protect the seat and thread area of the tube
fitting by covering with a plug or another nut.
Lifetime Limited Warranty
Dwyer Instruments, Inc. guarantees all tube fittings and components to
be free from defects in materials and workmanship. To initiate a warranty claim, suspected defective product must be returned to Dwyer
Instruments, Inc. with the nature of potential defect documented for factory evaluation. Any product with a determined defect in material or
workmanship will be replaced with equivalent product at no charge.
This warranty comprises the sole and entire warranty pertaining to items
provided here under. There is no other warranty, guarantee express or
implies representation of any kind whatsoever. All other warranties
including, but not limited to, merchantability and fitness for purpose,
whether expressed, implied, or arising by operation of law, course of
dealing, or trade usage are hereby disclaimed. There are no warranties
which extend beyond the description on the face hereof: and this warranty does not apply in cases of abuse, mishandling, or normal use
depreciation. In no event, whether alleged to arise from breach of contract, expressed or implied warranty, by operation of law, negligence or
otherwise, will Dwyer Instruments, Inc. be liable for any incidental, consequential, lost property, or other special damages of any kind whatsoever. The exclusive, only remedy under this warranty is the replacement
of determined defective parts as set forth above.
Dwyer Instruments, Inc. standard terms and conditions of sale apply with
the exception of item #8 which is superceded by the above Lifetime
Limited Warranty for the specific A-1000 fittings shown on the previous/following pages.
DWYER INSTRUMENTS, INC.
Phone: 219/879-8000 www.dwyer-inst.com
P.O. Box 373 • Michigan City, IN 46361-0373, U.S.A. Fax: 219/872-9057 e-mail: info@dwyer-inst.com
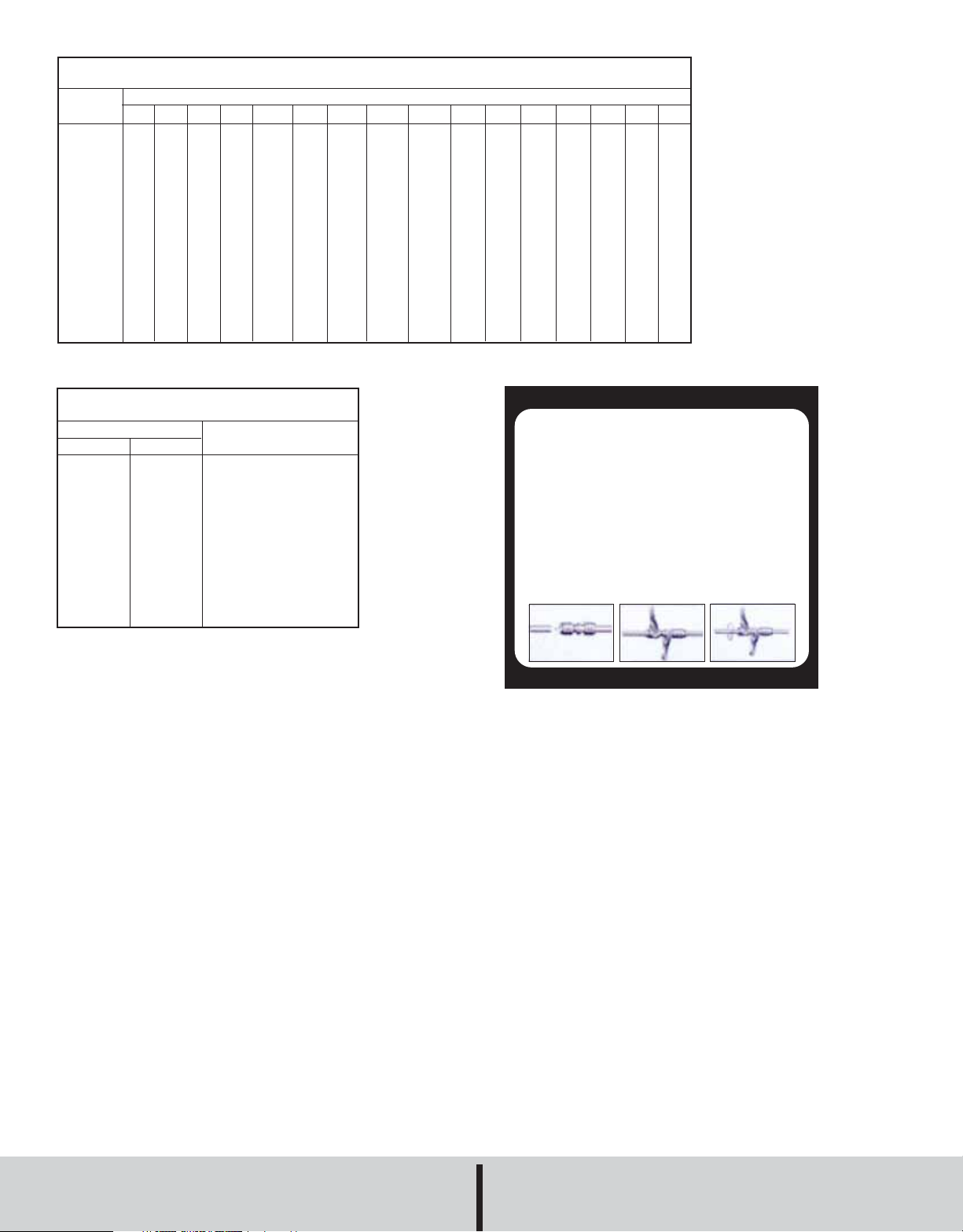
Tube O.D.
[Size (in)]
1/16
1/8
3/16
1/4
5/16
3/8
1/2
5/8
3/4
7/8
1
1-1/4
1-1/2
2
STAINLESS STEEL TUBING - TABLE A
Maximum Allowable Working Pressure (PSIG)
Wall Thickness of Tube (Inches)
.010
5600
.012
6850
.014
8150
.016
9500
.020
12100
.028
8550
5450
4000
.035
11000
7000
5100
4050
3300
2450
.049
10300
7500
5850
4800
3500
2950
2400
2050
.065
10300
8050
6550
4750
4000
3300
2800
2400
.083
6250
5200
4250
3600
3150
2450
.095
6050
4950
4200
3650
2850
2350
.109
5800
4850
4200
3300
2700
2000
.120
4700
3650
3000
2200
.134
4150
3400
2500
.156
4900
4000
2900
.188
4900
3600
Stress Factors For Determining Tubing Pressure
Ratings at Elevated Temperatures - TABLE B
Temperature
°F
100
200
300
400
500
600
700
800
900
1000
1200
°C
38
93
149
200
260
316
371
427
482
538
649
Stainless Steel
316
1.00
1.00
1.00
.97
.90
.85
.82
.80*
.78*
.73*
.37*
* The precipitation of chromium carbides potentially
resulting in intergranular corrosion may occur when
exposed to operating temperatures.
Dwyer®Tube Fittings
INSTALLATION INSTRUCTIONS
1. Dwyer®tube fittings come individually bagged and completely assembled for immediate use. There is no need for disassembly prior to use. Simply remove the tube fitting from its
bag, insert the tube until it bottoms in the Dwyer
body and then hand tighten the Dwyer
2. While holding the fitting body stable with a back up wrench
scribe the nut for a reference point and wrench tighten the nut
1-1/4 turns for sizes 1/4˝ - 1˝ and 3/4 turn for sizes 1/16˝ - 3/16˝.
See figures #2 and #3.
[Note: For all sizes, tighten plugs (P), machined ferrule and at
port connector (PC) and the Dwyer end of the AN adapter
(ANF) only 1/4 of a turn.]
®
®
nut. See Figure #1.
tube fitting
231
MADE IN USA
©Copyright 2010 Dwyer Instruments, Inc. Printed in U.S.A. 8/10 FR# R1-443417-00 Rev. 1
DWYER INSTRUMENTS, INC.
Phone: 219/879-8000 www.dwyer-inst.com
P.O. Box 373 • Michigan City, IN 46361-0373, U.S.A. Fax: 219/872-9057 e-mail: info@dwyer-inst.com