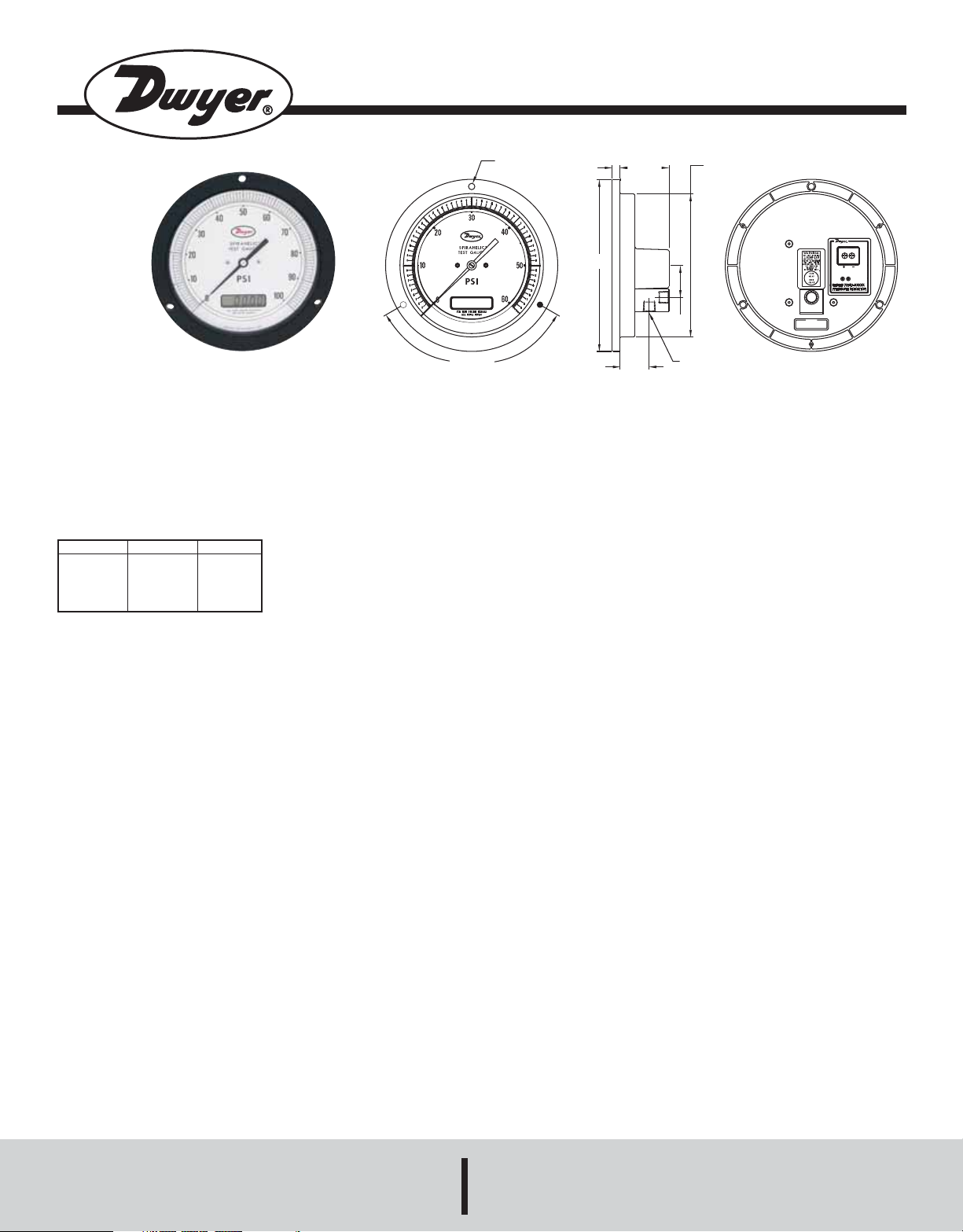
SERIES 7214D & 7314D
SPIRAHELIC
®
PRESSURE GAGE WITH DIGITAL DISPLAY
Specifications - Installation and Operating Instructions
Bulletin A-33-B
Series 7214D & 7314D Dwyer
helical/spiral Bourdon tube, formed from Inconel
®
Spirahelic®Gages employ a unique triple-wound
®
Alloy X-750 material for exceptionally wide media compatibility and reliability. Units provide ASME Grade 3A
accuracy (1/4%), readable on both a large 6˝ (7214D), 8.5˝ (7314D) analog dial
and a 4-1/2 digit liquid crystal display. A 316 SS connection block includes dual 1/4˝
NPT female ports for a choice of vertical or horizontal piping. Block includes an
integral filter plug to prevent dirt or other foreign material from entering the gage.
Gage fits standard ASME 9.0˝ (229mm) panel cut out.
Series 7214D & 7314D Models and Ranges
Model
7214D-G100
7214D-G200
7214D-G300
7214D-G600
Model
7314D-G100
7314D-G200
7314D-G300
7314D-G600
Range, PSI
0-100
0-200
0-300
0-600
Installation
1. Select a location free from excess vibration where the temperature limits of 20
to 120°F (-6.7 to 48.9°C) will not be exceeded. Mounting surface should be vertical to match the position in which all standard gages are calibrated. Avoid locations
in direct sunlight which can cause accelerated discoloration of the clear acrylic
lens or where exposure to oil mist or other airborne vapors could likewise result in
lens damage. Make sure the case relief area on the rear is not obstructed. This
hole is designed to direct pressure rearward in the event of a Bourdon tube failure.
See complete safety recommendations on the back of this sheet.
2. Make a panel cutout of 6.5˝ (165.1mm) for Series 7214D gages. Make a panel
cutout of 9˝ (229mm) for Series 7314D gages. See drawing above for bolt circle
diameters and bolt hole sizes.
3. Two 1/4˝ NPT female pressure connections are provided allowing a choice of
vertical (below gage) or horizontal piping. Plug unused port. Use minimal amount
of thread sealant. Too much could block the internal pressure passage.
Caution: When installing fittings or pipe, always use a second wrench on the 1˝
connection block. Do Not allow torque to be transmitted from the block to the gage
case.
Electrical Connections
Caution: Do not exceed specified supply voltage ratings.
Permanent damage not covered by warranty will result.
This unit is not designed for 120 or 240 VAC line operation.
Electrical connections to the Series 7214D & 7314D Spirahelic
®
Pressure gage
with digital display are made to the electrical terminal strip on the rear of the case.
See drawing above. It is not necessary to observe polarity when making electrical
connections. Do observe the maximum VDC and VAC limits listed at left.
120° TYP.
B
11/32
[8.732]
2-9/64
[54.37]
A
1-13/32
[35.71]
1-9/32
[32.54]
C
1/4 NPT TYP 2 PLACES
DWYER INSTRUMENTS, INC.
MICHIGAN CITY, IN 46360, U.S.A.
CAUTION
ALWAYS USE WRENCH ON PRESSURE
BLOCK WHEN TIGHTENING FITTINGS
NEVER PUT STRESS ON HOUSING
ZERO SPAN
SPECIFICATIONS
Size: 6˝ (7214D), 8.5˝ (7314D). Size conforms to ASME B40.1.
Accuracy: ASME Grade 3A (1/4% of full scale).
Pressure Connections: 1/4˝ NPT female, duplicated back and bottom.
ASME Specifications: Conforms to ASME B40.1.
Housing: Impact resistant mineral filled nylon.
Position: Calibrated for mounting with scale in vertical position.
Wetted Parts: Inconel
®
Alloy X-750 Bourdon tube, 316 SS connection block.
Movement: Direct drive of pointer.
Temperature Limits: 20 to 120°F (-6.7 to 48.9°C).
Overpressure: 150% of full scale. Recommended operation should be between
25 and 75% of full scale.
Finish: Black.
Weight: 7214D-21 oz. (595 grams) 7314D-1 lb, 11 oz. (765 grams) .
Accessory: (1) 1/4˝ NPT pipe plug.
Electrical
Power Supply: 10-35 VDC; 16-26 VAC.
Warm-Up Time: 10 minutes.
Current Consumption: DC: 38 mA max.; AC: 76 mA max.
Calibration Test
To check calibration, use a dead weight tester or certified test gage with accuracy
of 0.1% or better for ASME Grade 3A gages. The test gage range should be comparable to the range of the Dwyer
®
Spirahelic®gage being tested. Connect lines
from the two instruments to a tee and a third line from the tee to a controllable
source of pressure. Apply pressure slowly so pressure can equalize throughout the
system. Compare readings. If gage being tested is found to need calibration,
return it freight prepaid to the address below.
Maintenance
No lubrication or periodic servicing is required. Keep case exterior and lens clean.
Use only cleaners compatible with acrylic plastic.
Repairs
Field repair is not recommended and can void warranty. Gages needing calibration
or other service should be returned freight prepaid to:
Dwyer Instruments, Inc.
Attn: Repair Department
102 Indiana Highway 212
Michigan City, IN 46360
Inconel® is a registered trademark of Huntington Alloy Corporation
DWYER INSTRUMENTS, INC.
Phone: 219/879-8000 www.dwyer-inst.com
P.O. BOX 373 • MICHIGAN CITY, INDIANA 46361, U.S.A. Fax: 219/872-9057 e-mail: info@dwyer-inst.com
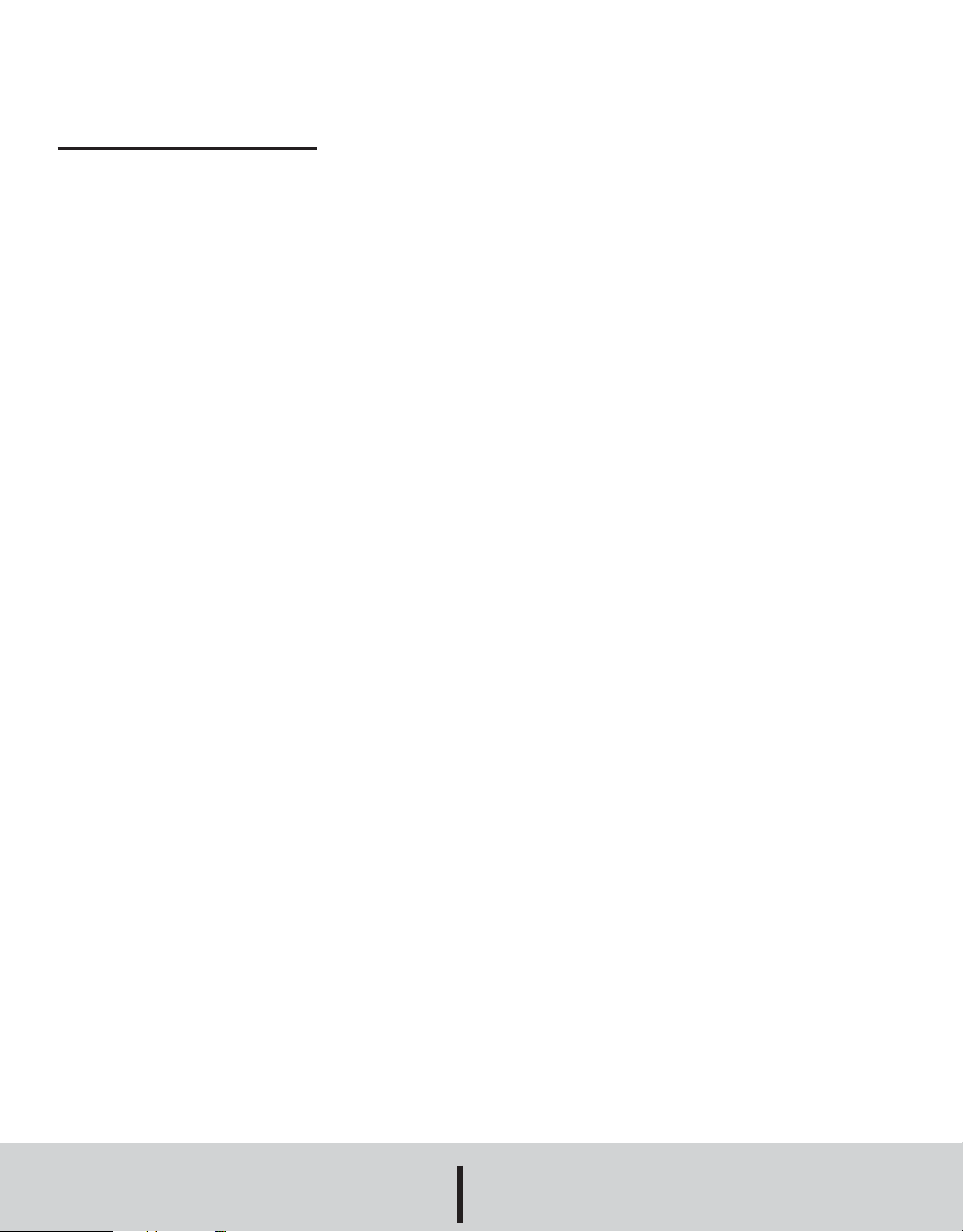
The following material is excerpted from a standard titled
Gauges-Pressure Indicating Dial Type-Elastic
Element (ANSI/ASME B40.1-1985) as published by The
American Society of Mechanical Engineers, 345 East
47th St. New York, NY 10017. This information is furnished to assist the user of Dwyer Spirahelic
properly evaluating their suitability for the intended application and conditions.
4 SAFETY
4.1 Scope
This Section of the Standard presents certain information to guide users, suppliers, and manufacturers
toward minimizing the hazards that could result from misuse or misapplication of pressure gauges with elastic elements. The user should become familiar with all sections
of this Standard, as all aspects of safety cannot be covered in this Section. Consult the manufacturer or supplier
for advice whenever there is uncertainty about the safe
application of a pressure gauge.
4.2 General Discussion
4.2.1 Adequate safety results from intelligent planning
and careful selection and installation of gauges into a
pressure system. The user should inform the supplier of
all conditions pertinent to the application and environment
so that the supplier can recommend the most suitable
gauge for the application.
4.2.2 The history of safety with respect to m use of
pressure gauges has been excellent. Injury to personnel
and damage to property have been minimal. In most
instances, the cause of failure has been misuse or misapplication.
4.2.3 The pressure sensing element in most gauges is
subjected to high internal stresses, and applications exist
where the possibility of catastrophic failure is present.
Pressure regulators, chemical (diaphragm) seals, pulsation dampers or snubbers, syphons, and other similar
items, are available for the use in these potentially hazardous systems. The hazard potential increases at higher
operating pressure.
4.2.4 The following systems are considered potential-
ly hazardous and must be carefully evaluated:
(a) compressed gas systems
(b) oxygen systems
(c) systems containing hydrogen or free hydrogen
atoms
(d) corrosive fluid systems (gas and liquid)
(e) pressure systems containing any explosive or
flammable mixture or medium
(f) steam systems
(g) nonsteady pressure systems
(h) systems where high overpressure could be acci-
dentally applied
(i) systems wherein interchangeability of gauges
could result in hazardous internal contamination or where
lower pressure gauges could be installed in higher pressure systems
(j) systems containing radioactive or toxic fluids (liquids or gases)
(k) systems installed in a hazardous environment
4.2.5 When gauges are to be used in contact with
media having known or uncertain corrosive effects or
known to be radioactive, random or unique destructive
phenomena can occur. In such cases the user should
always furnish the supplier or manufacturer with information relative to the application and solicit his advice prior
to installation of the gauge.
4.2.6 Fire and explosions within a pressure system
can cause pressure element failure with very violent
effects, even to the point of completely disintegrating or
melting the pressure gauge. Violent effects are also produced when failure occurs due to:
(a) hydrogen enbrittlement
(b) contamination of a compressed gas
(c) formation of acetylides
(d) weakening of soft solder joints by steam or other
heat sources
(e) weakening of soft soldered or silver brazed joints
caused by heat sources such as fires
(f) corrosion
(g) fatigue
(h) mechanical shock
(i) excessive vibration
Failure in a compressed gas system can be expected
to produce violent effects.
4.2.7 Modes of Elastic Element Failure. There are
four basic modes of elastic element failure, as follows.
4.2.7.1 Fatigue Failure. Fatigue failure caused by
pressure induced stress generally occurs from the inside
to the outside along a highly stressed edge radius,
appearing as a small crack that propagates along the
edge radius. Such failures are usually more critical with
compressed gas media than with liquid media.
®
gages in
Fatigue cracks usually release the media fluid slowly so
case pressure buildup can be averted by providing pressure relief openings in the gauge case. However, in high
pressure elastic elements where the yield strength
approaches the ultimate strength of the element material,
fatigue failure may resemble explosive failure.
A restrictor placed in the gauge pressure inlet will
reduce pressure surges and restrict fluid flow into the partially open Bourdon tube.
4.2.7.2 Overpressure Failure. Overpressure failure
is caused by the application of internal pressure greater
than the rated limits of the elastic element and can occur
when a low pressure gauge is installed in a high pressure
port of system. The effects of overpressure failure, usually more critical in compressed gas systems than in liquid
filled systems, are unpredictable and may cause parts to
be propelled in any direction. Cases with pressure relief
openings will not always retain expelled parts.
Placing a restrictor in the pressure gauge inlet will not
reduce the immediate effect of failure, but will help control
flow of escaping fluid following rupture and reduce potential of secondary effects.
It is generally accepted that solid front cases with
pressure relief back will reduce the possibility of parts
being projected forward in the event of failure.
The window alone will not provide adequate protection against internal case pressure buildup, and can be
the most hazardous component.
4.2.7.3 Corrosion Failure. Corrosion failure occurs
when the elastic element has been weakened through the
attack by corrosive chemicals present in either the media
inside or the environment outside it. Failure may occur as
pinhole leakage through the elements walls or early
fatigue failure due to stress cracking brought about by
chemical deterioration or embrittlement of the material.
A chemical (diaphragm) seal should be considered for
use with pressure media that may have a corrosive effect
on the elastic element.
4.2.7.4 Explosive Failure. Explosive failure is
caused by the release of explosive energy generated by
a chemical reaction such as can result with adiabatic
compression of oxygen occurs in the presence of hydrocarbons. It is generally accepted that there is no known
means of predicting the magnitude or effects of this type
of failure. For this mode of failure, a solid wall or partition
between the elastic element and the window will not necessarily prevent parts being projected forward.
4.2.8 Pressure Connection. See recommendations
in para. 3.3.4.
4.3 Safety Recommendations.
4.3.1 Operating Pressure. The pressure gauge
selected should have a full scale pressure such that the
operating pressure occurs in the middle half (25 to 75%)
of the scale. The full scale pressure of the gauge selected should be approximately two times the intended operating pressure.
Should it be necessary for the operating pressure to
exceed 75% of full scale, contact the supplier for recommendations.
This does not apply to test, retarded, or suppressed
scale gauges.
4.3.2 Use of Gauges Near Zero Pressure. The use
of gauges near zero pressure is not recommended
because the accuracy tolerance may be a large percentage of the applied pressure. If, for example, a 0/100 psi
Grade B gauge is used to measure 6 psi, the accuracy of
measurement will be ±50% of the applied pressure. In
addition, the scale of a gauge is often laid out with takeup, which can result in further inaccuracies when measuring pressures that are a small percentage of the gauge
span.
For the same reasons, gauges should not be used for
the purpose of indicating that the pressure in a tank, autoclave, or other similar unit has been completely exhausted to atmospheric pressure. Depending on the accuracy
and the span of the gauge and the possibility that takeup
is incorporated at the beginning of the scale, hazardous
pressure may remain in the tank even though the gauge
is indicating zero pressure. A venting device must be used
to completely reduce the pressure before unlocking covers, removing fittings, or performing other similar activities.
4.3.3 Compatibility With the Pressure Medium. The
elastic element is generally a thin walled member, which
of necessity operates under high stress conditions and
must, therefore, be carefully selected for compatibility
with the pressure medium being measured. None of the
common element materials is impervious to every type of
chemical attack. The potential for corrosive attack is
established by many factors, including the concentration,
temperature, and contamination of the medium. The user
should inform the gauge supplier of the installation conditions so that the appropriate element materials can be
selected.
4.3.4 In addition to the factors discussed above, the capability of a pressure element is influenced by the design,
materials, and fabrication of the joints between its parts.
Common methods of joining are soft soldering, silver
brazing, and welding. Joints can be affected by temperature, stress, and corrosive media. Where application
questions arise, these factors should be considered and
discussed by the user and manufacturer.
4.3.5 Some special applications require that the pres-
sure element assembly have a high degree of leakage
integrity. Special arrangement should be made between
manufacturer and used to assure that the allowable leakage rate is not exceeded.
4.3.6 Cases
4.3.6.1 Cases, Solid Front. It is generally accepted
that a solid front case per para. 3.3.1 will reduce the possibility of parts being projected forward in the event of
elastic element assembly failure. An exception is explosive failure of the elastic element assembly.
4.3.6.2 Cases, Liquid Filled. It has been general
practice to use glycerine or silicone filling liquids.
However, these fluids may not be suitable for all applications. They should be avoided where strong oxidizing
agents including, but not limited to, oxygen, chlorine, nitric
acid, and hydrogen peroxide are involved. In the presence of oxidizing agents, potential hazard can result from
chemical reaction, ignition, or explosion. Completely fluorinated or chlorinated fluids, or both, may be more suitable for such applications.
The user shall furnish detailed information relative to
the application of gauges having liquid filled cases and
solicit the advice of the gauge supplier prior to installation.
Consideration should also be given to the instantaneous hydraulic effect that may be created by one of the
modes of failure outlined in para. 4.2.7. The hydraulic
effect due to pressure element failure could cause the
window to be projected forward even when a case having
a solid front is employed.
4.3.7 Restrictor. Placing a restrictor between the
pressure connection and the elastic element will not
reduce the immediate effect of failure, but will help control
flow of escaping fluid following rupture and reduce the
potential of secondary effects.
4.3.8 Specific Service Conditions
4.3.8.1 Specific applications for pressure gauges
exist where hazards are known. In many instances,
requirements for design, construction, and use of gauges
for these applications are specified by state or federal
agencies or Underwriters Laboratories, Inc. Some of
these specific service gauges are listed below. The list is
not intended to include all types, and the user should
always advise the supplier of all application details.
4.3.8.2 Acetylene Gauges. A gauge designed to
indicate acetylene pressure. It shall be constructed using
materials that are compatible with commercially available
acetylene. The gauge may bear the inscription ACETYLENE on the dial.
4.3.8.3 Ammonia Gauge. A gauge designed to indi-
cate ammonia pressure and to withstand the corrosive
effects of ammonia. The gauge may bear the inscription
AMMONIA on the dial. It may also include the equivalent
saturation temperature scale markings on the dial.
4.3.8.4 Chemical Gauge. A gauge designed to indi-
cate the pressure of corrosive or high viscosity fluids, or
both. The primary material(s) in contact with the pressure
medium may be identified on the dial. It may be equipped
with a chemical (diaphragm) seal, pulsation damper, or
pressure relief device, or a combination. These devices
help to minimize potential damage to personnel and property in the event of gauge failure. They may, however,
also reduce accuracy of sensitivity, or both.
4.3.8.5 Oxygen Gauge. A gauge designed to indi-
cate oxygen pressure. Cleanliness shall comply with
Level IV (see Section 5). The dial shall be clearly marked
with a universal symbol and/or USE NO OIL in red color
(see para. 6.1.2.1).
4.4 Reuse of Pressure Gauges
It is not recommended that pressure gauges be
moved from one application to another. Should it be necessary, however, the following must be considered.
4.4.1 Chemical Compatibility. The consequences of
incompatibility can range from contamination to explosive
failure. For example, moving an oil service gauge to oxygen service can result in explosive failure.
4.4.2 Partial Fatigue. The first installation may
involve pressure pulsation that has expended most of the
gauge life, resulting in early fatigue in the second installation.
4.4.3 Corrosion. Corrosion of the pressure element
assembly in the first installation may be sufficient to cause
early failure in the second installation.
4.4.4 Other Considerations. When reusing a gauge,
all guidelines covered in the Standard relative to application of gauges should be followed in the same manner as
when a new gauge is selected.
©Copyright 2011 Dwyer Instruments, Inc. Printed in U.S.A. 3/11 FR# 17-440958-00 Rev. 3
DWYER INSTRUMENTS, INC.
Phone: 219/879-8000 www.dwyer-inst.com
P.O. BOX 373 • MICHIGAN CITY, INDIANA 46361, U.S.A. Fax: 219/872-9057 e-mail: info@dwyer-inst.com