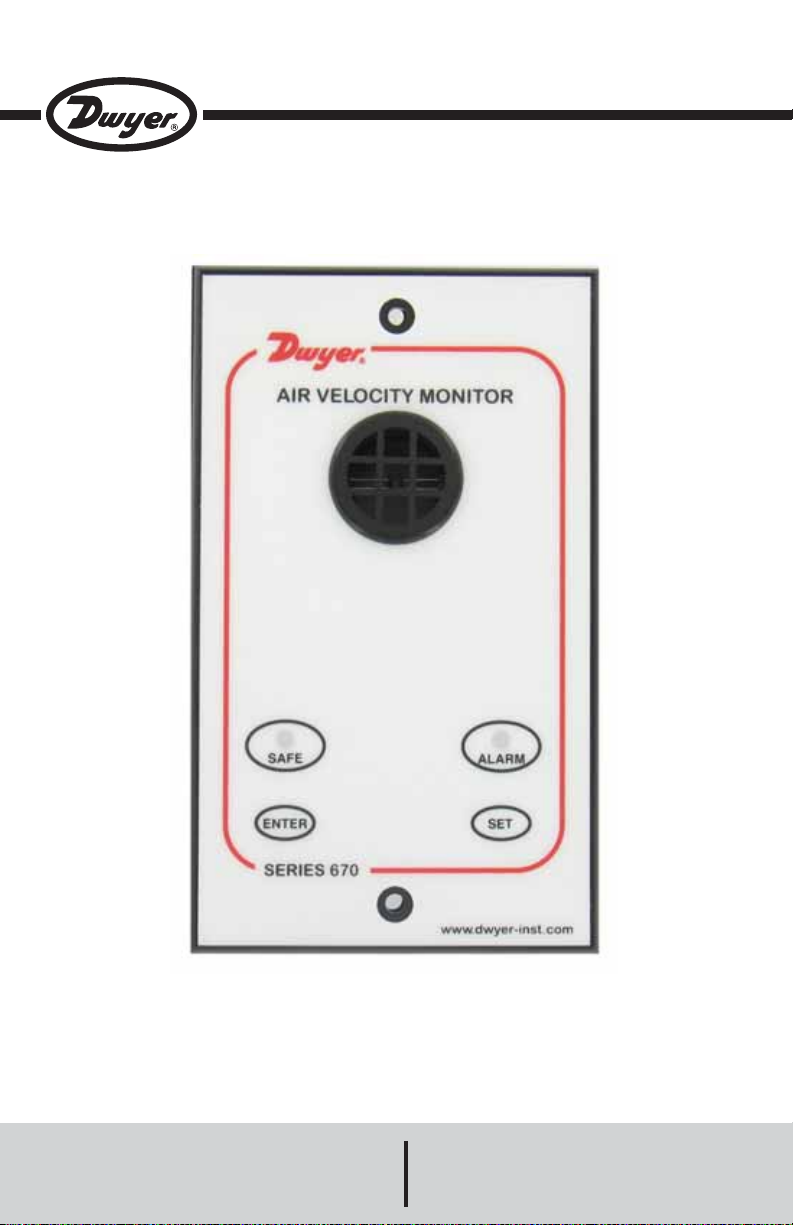
Bulletin AV-670
Series 670 Hood Monitor
Specifications - Installation and Operating Instructions
DWYER INSTRUMENTS, INC.
P.O. BOX 373 • MICHIGAN CITY, IN 46361, U.S.A. Fax: 219/872-9057 e-mail: info@dwyer-inst.com
Phone: 219/879-8000 www.dwyer-inst.com
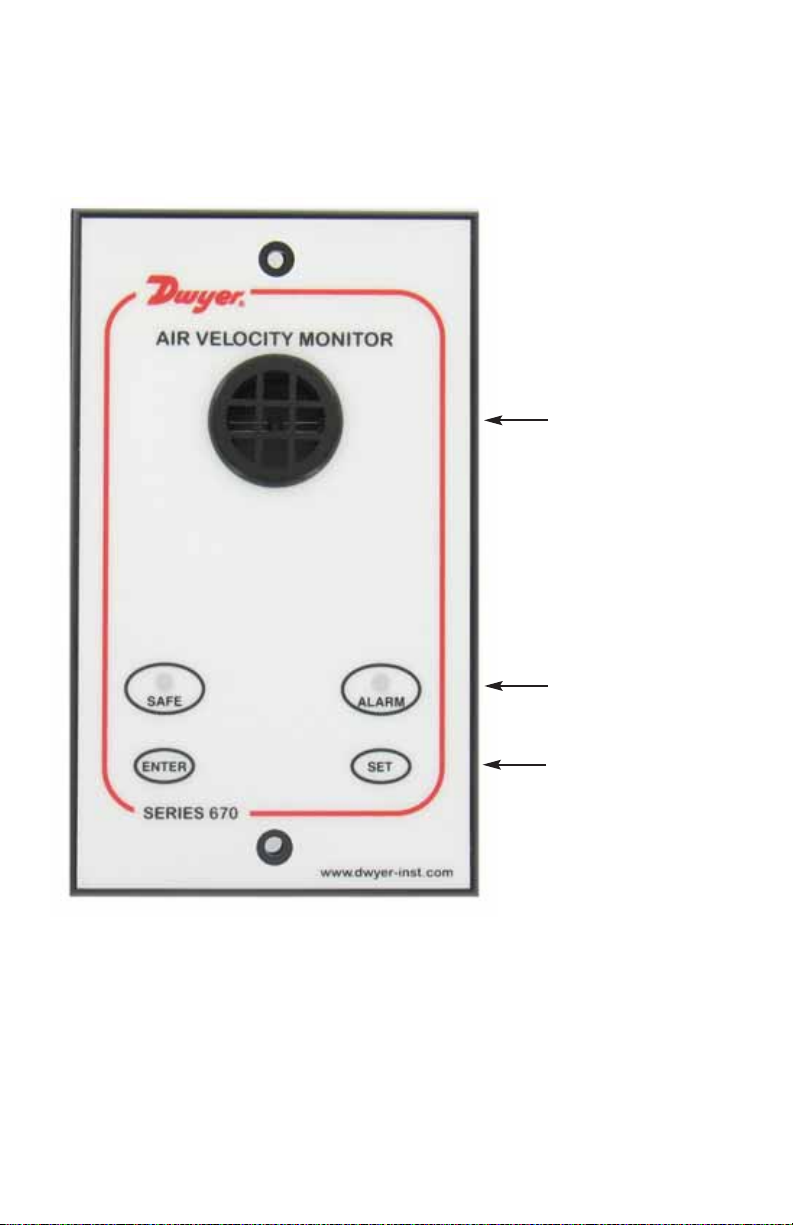
Operator Display Panel
Built-in AIRFLOW
SENSOR
LED indicators
Function buttons
Calibration.
ENTER- also used as
Mute button for audible
alarm
1
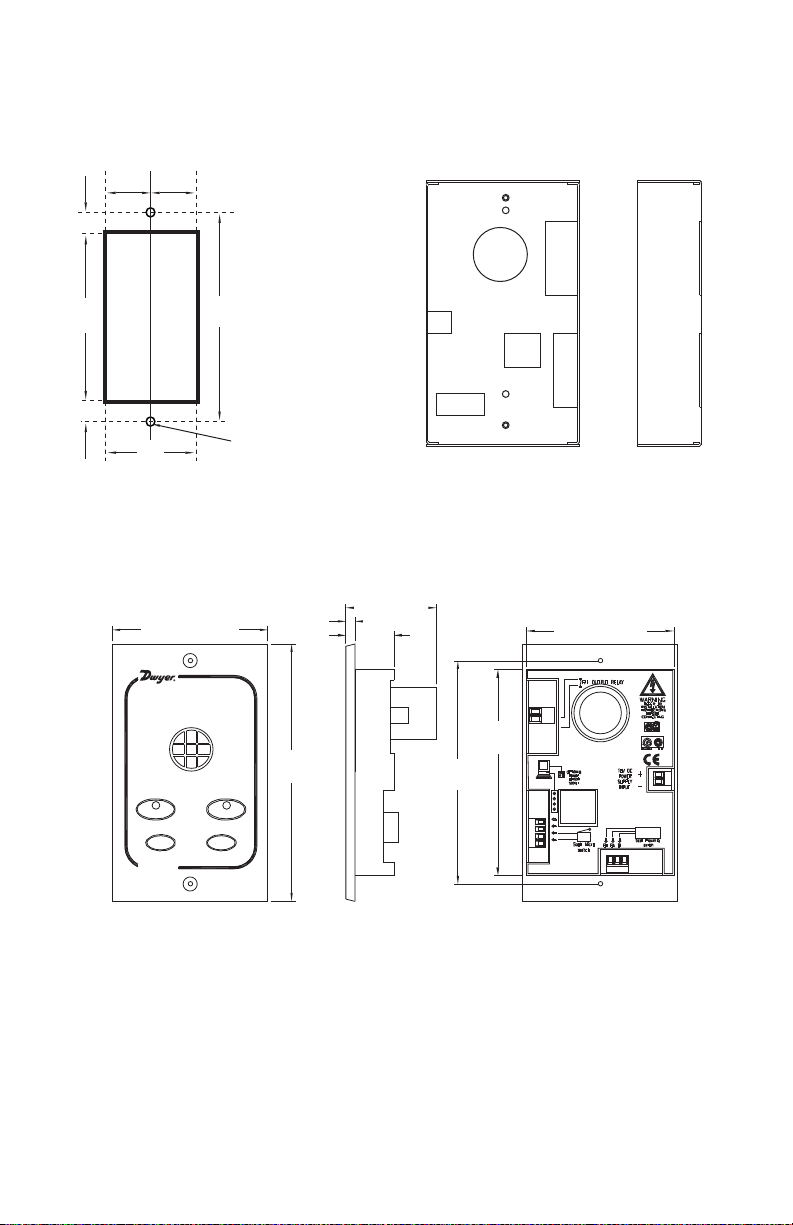
0.16 [4]
1.67
[42.55]
1.67
[42.55]
4.65
[118]
0.16 [4]
3.35
[85]
PANEL CUTOUT DIMENSIONS
4.65˝ x 3.35˝ [118 mm x 85 mm]
3-29/64 [87.88]
AIR VELOCITY MONITOR
SAFE
ENTER
SERIES 670
4.96
[126]
2 x FIXING HOLES
2.5 mm DIAMETER
FOR 2 x No. 4
SELF TAPPING
SCREWS PROVIDED
5-45/64
[145.03]
ALARM
SET
www.dwyer-inst.com
2-1/64 [51.05]
13/64 [5.08]
1-1/16
[27.10]
4-61/64
[125.98]
4-9/16
[116.08]
3-17/64 [83.06]
2
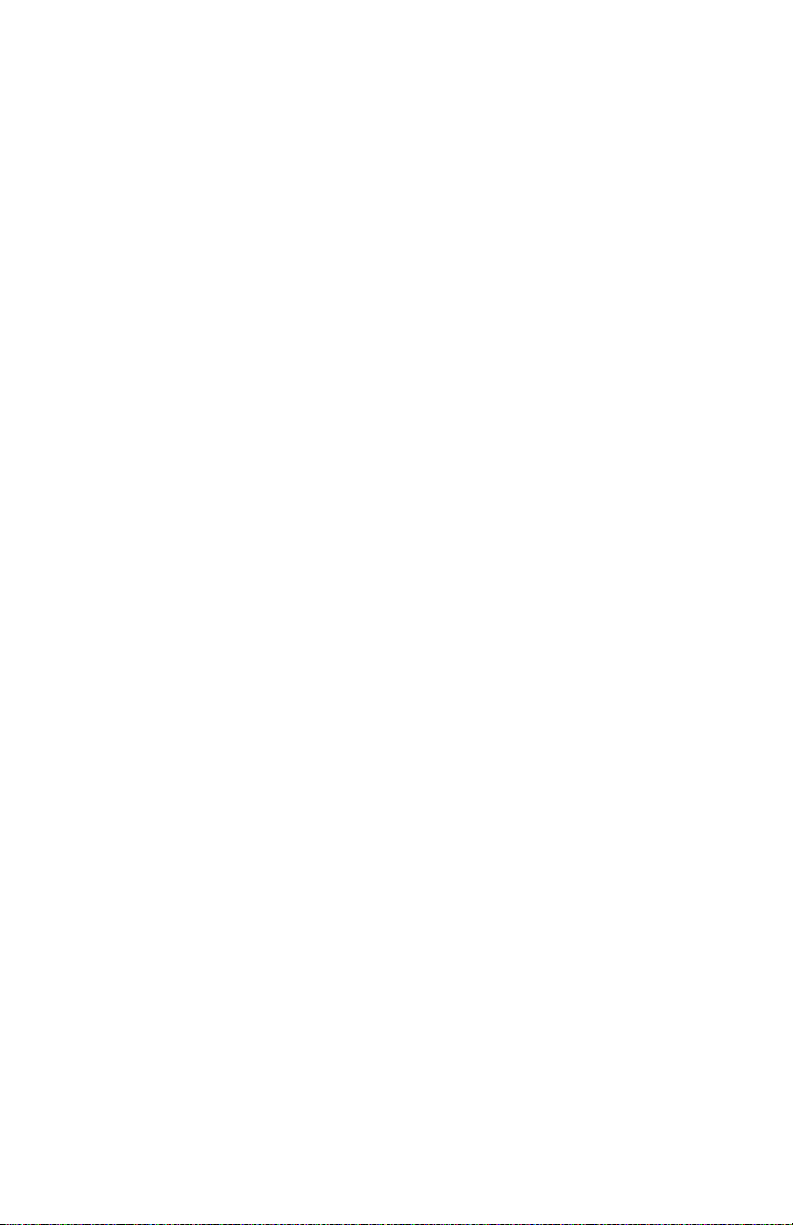
SPECIFICATIONS
Service: Fume hood face velocity air flow.
Alarm Range: 30-400 FPM (0.15-2.0 m/s).
Alarm Indication: Red LED & audible alarm.
Low Air Velocity Alarm Delay: Fixed 5 secs.
Display:
Visual LEDs:
Red: Alarm.
Green: Normal.
Horn Silence: Yes-temporary and permanent.
Accuracy: Face velocity ±10%.
Operating Temperature: 55-86°F (13-30°C).
Storage Temperature: -40 to 150°F (-40 to 65°C).
Power Requirement Input: 15 VDC 500 mA; 120 VAC, 60 Hz power transformer included.
Relay Output Low Air Flow Alarm: 5 amps @ 250 VAC.
Relay Input For Night Setback: 2 wire rated for 24 VDC usage.
Sash High indication: Using a two wire micro switch or 3 wire proximity switch input,
rated for 24 VDC usage.
Comm Port: RS232- Can be connected via serial interface to LAN network.
Mounting: Semi flush, flush or surface mounted when using included bracket.
Agency Approval: CE.
3
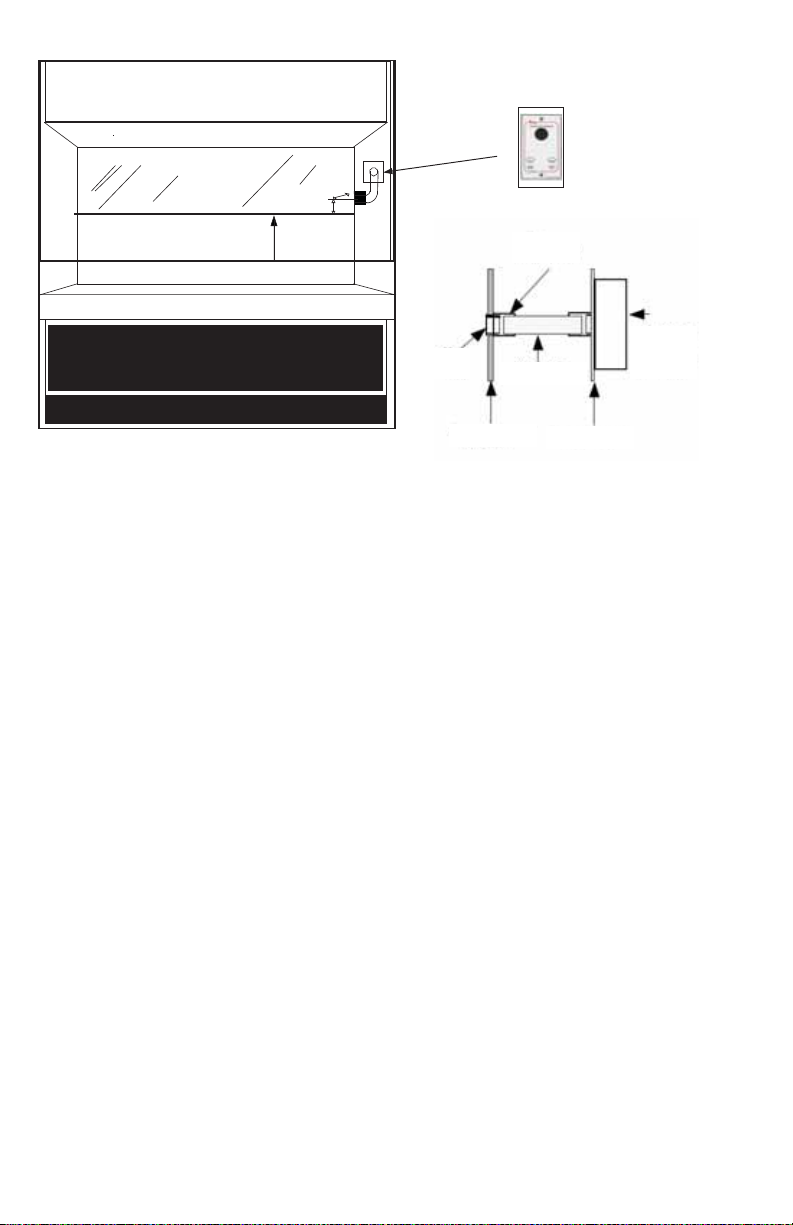
4.0 Fume Hood Installation
Norm al Sash
w ork in g h e igh t.
eg. 500mm
100mm
100mm
670
25mm
Female adapter
670 Face
Open to the
25mm
Male
bush
25mm Tube
laboratory
Fume cupboard
inner skin
Fume cupboard
outer skin
It is very important to position the Series 670 airflow sensor in the correct position to give long term
stable reading of the face velocity. Please read the INSTALLATION NOTES below and if in doubt
contact us for further advice.
Installation Notes:
1. The Series 670 must be positioned where it can "see" the room pressure of the laboratory. The
back connection spigot of the sensor is designed to accept a 25mm OD tube which should be
connected to the inner chamber of the fume hood. (This tube and fittings is known as the "vent
kit").
The ideal position for the end of the 25mm tube for most fume hoods is 100mm back from the
sash glass and 100mm higher than the normal sash opening height through the inner side wall.
2. If possible mount the sensor on the front of the fume hood and use a short length of tube. Tube
lengths of more than 1 meter or smaller diameter will restrict the airflow through the sensor.
This will lead to too much sensitivity being required to calibrate the unit which can lead to some
instability of the reading or incorrect readings at low velocities.
3. For fume hoods with a single skin side wall or a double skin with a small gap between them it
may not be possible to achieve the ideal sensing position using a flexible tube. With a single skin
side wall it is possible to fix the sensor on the outside of the fume hood and connect directly to
the inner chamber in the ideal position. This method can only be used for up to two fume hoods
when they are positioned side by side (using the two outer walls).
An alternative method is to mount the sensor on the front of the fume hood and connect using a
short flexible tube to a rigid wall tube attached to the inner side wall. The open end of this rigid
wall tube should be positioned in the ‘ideal position’, i.e., 100mm back from the sash and 100mm
higher than the normal sash opening.
Fume hoods with a high internal height can present a difficulty because the tube length to reach
the ideal position may be longer than 1 meter. In this case it is better to use a tube no longer
than 1 meter which may result in a sensing position higher than the ideal. When fitting a sensor
to a ’narrow wall’ fume hood for the first time it may be necessary to try various combinations of
rigid and flexible tube to find the best combination and position.
4. The sensor should not be mounted in a position were it is subject to drafts from the
laboratory air input or ventilation system.
4