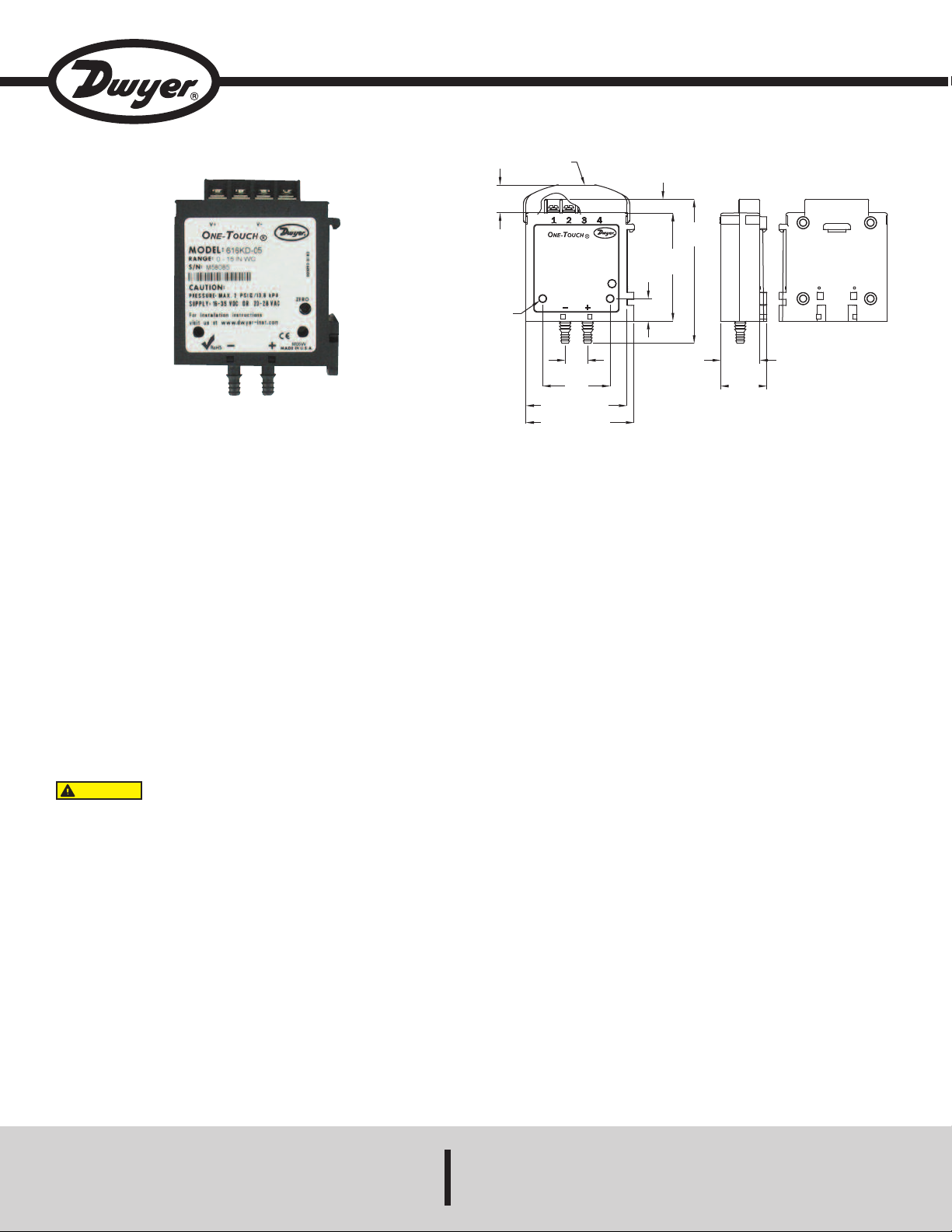
Bulletin P-616KD
O
PTIONAL
T
ERMINAL
C
OVER
5
/16
[
7.94]
5/8
[15.88]
Ø
5/32
[3.97]
MOUNTING
HOLE
2 PLACES
3-21/64
[84.53]
2
-13/32
[
61.12]
1
/2
[
12.70]
1/2
[12.70]
1-1/2
[38.10]
2
-1/4 [57.15]
2-13/32 [61.12]
7/8
[22.23]
1-1/32
[26.19]
Series 616KD Differential Pressure Transmitter
Specifications – Installation and Operating Instructions
The Series 616KD One-Touch®Differential Pressure Transmitter
senses the pressure of air and compatible gases and sends a standard
4 to 20 mA or optional voltage output signal. A wide range of models are
available factory calibrated to specific ranges. A single push button
properly adjusts both zero and span. New enclosure enables the 616KD
to be mounted on a 35 mm DIN rail either via its side or back DIN rail
clips.
SPECIFICATIONS
Service: Air and non-combustible, compatible gases.
Wetted Materials: Consult factory.
Accuracy: ±2.0% FS.
Stability: ±1% FS/yr.
Temperature Limits: 32 to 122°F (0 to 50°C).
Pressure Limits: 2 psi (13.8 kPa).
Thermal Effect on Span: ±0.11% FS/°F (±0.19% FS/°C) typ.
INSTALLATION
Select a clean, dry mounting location free from excess vibration.
Distance from the receiver is limited only by total loop resistance. See
Electrical Connections below. The tubing supplying pressure to the
instrument can be practically any length required, but long lengths will
increase response time slightly.
Thermal Effect on Zero: 616KD-X0: 0.6%/°F (1%/°C); 616KD-X1:
0.3%/°F (0.5%/°C); 616KD-X2: 0.2%/°F (0.33%/°C); 616KD-X3:
0.12%/°F (0.2%/°C); 616KD-X4: 0.06%/°F (0.1%/°C) FS max.
Power Requirements: 16 to 36 VDC (2 or 3 wire); 20 to 28 VAC (3
wire).
Output Signal: 4 to 20 mA or unit with field selectable 0 to 10 & 0 to 5
volt.
Pressure Connections
Two integral barbed tubing connections are provided. They are dualsized to fit both 1/8˝ and 3/16˝ (3.12 and 4.76 mm) ID tubing. Be sure the
pressure rating of the tubing exceeds that of the operating ranges.
Zero and Span Adjustments: Push button.
Loop Resistance: DC: 1000 Ω max.; AC: 1200 Ω max.
Current Consumption: 21 mA max.
Warm Up Time: 30 minutes.
Electrical Connections: Screw-type terminal block.
ELECTRICAL CONNECTIONS
CAUTION
designed for 120 or 240 volts AC line operation.
Do not exceed specified supply voltage ratings. Permanent
damage not covered by warranty will result. This unit is not
Shielding cabling is required. Cable shield must be attached to a reliable
earth ground. Electrical connections are made to the terminal block
located on the top of the transmitter. Terminals are marked 1, 2, 3, 4.
Determine which of the following circuit drawings applies to your
application and wire accordingly.
Process Connections: Barbed, dual size to fit 1/8˝ & 3/16˝ (3 mm & 5
mm) ID rubber or vinyl tubing.
Enclosure Rating: NEMA 1 (IP20).
Mounting Orientation: Position insensitive.
Weight: 1.8 oz (51 g).
Agency Approvals: CE, RoHS
Tested to the following standards:
IEC 61000-4-2: 2008
IEC 61000-4-3: 2006
IEC 61000-4-4: 2004
IEC 61000-4-5: 2005
Wire Length
The maximum length of wire connecting transmitter and receiver is a
function of wire size and receiver resistance. Wiring should not
contribute more than 10% of the receiver resistance to total loop
resistance.
DWYER INSTRUMENTS, INC.
P.O. BOX 373 • MICHIGAN CITY, INDIANA 46360, U.S.A. Fax: 219/872-9057 e-mail: lit@dwyer-inst.com
Phone: 219/879-8000 www.dwyer-inst.com
IEC 61000-4-6: 2006
CENELEC EN 61000-6-2: 2005
CENELEC EN 61000-6-4: 2007
CENELEC EN 55011: 2007
FCC Part 15 CFR Title 47: 2009
ICES-003: 2004 Digital Apparatus (Industry Canada)
ANSI C63.4-2003: 2003
CENELEC EN 61326-1: 2006
2004/108/EC EMC Directive
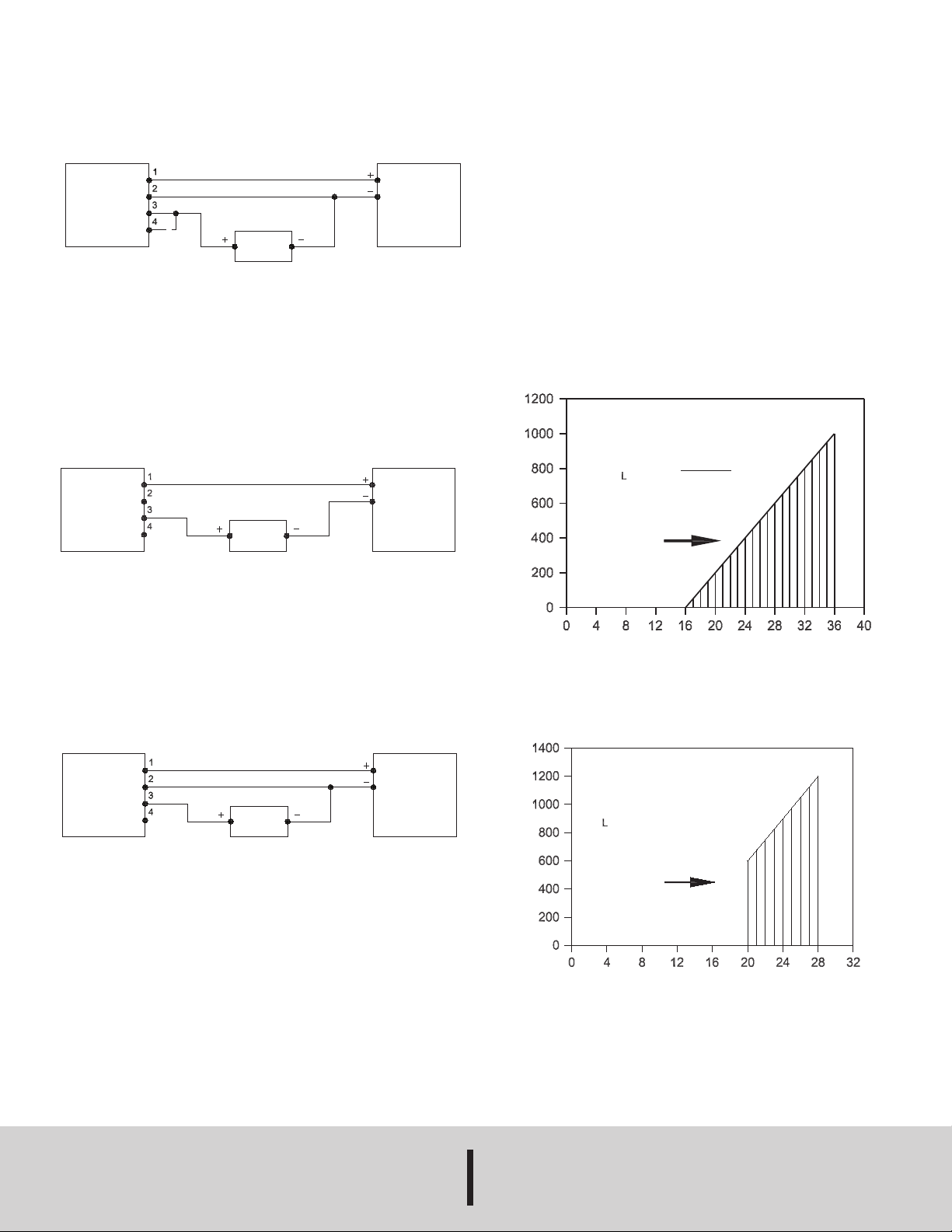
Voltage Units (0 to 5 or 0 to 10 V)
MAXIMUM LOOP RESISTANCE (DC POWER)
MAXIMUM VALUE (1000 Ω)
TOTAL LOOP RESISTANCE (Ω)
POWER SUPPLY VOLTAGE (VDC)
OPERATING
REGION
R Max. =
Vps - 16 V
20 mA
MAXIMUM LOOP RESISTANCE (AC POWER)
MAXIMUM VALUE (1200 Ω)
R Max. = 75 Ω/V x Vps - 900 Ω
TOTAL LOOP RESISTANCE (Ω)
POWER SUPPLY VOLTAGE (VAC)
OPERATING
REGION
P
RESSURE
T
RANSMITTER
R
ECEIVER
POWER SUPPLY
16 TO 36 VDC
O
R
2
0 TO 28 VAC
PRESSURE
TRANSMITTER
R
ECEIVER
P
OWER SUPPLY
1
6 TO 36 VDC
2 - WIRE CONNECTIONS (4 TO 20 mA)
PRESSURE
TRANSMITTER
RECEIVER
POWER SUPPLY
16 TO 36 VDC
OR
20 TO 28 VAC
3 - WIRE CONNECTIONS (4 TO 20 mA)
An external power supply delivering 16 to 35 VDC or 20 to 28 VAC with
minimum current capability of 16 mA DC (per transmitter) must be used to
power the control loop. Connect terminals 3 & 4 to select the 0 to 5 V output
mode. Leave terminal 4 disconnected to select the 0 to 10 V output mode.
Figure A
See Figure A for connection of the power supply, transmitter and receiver.
2-Wire Operation (4 to 20 mA units)
An external power supply delivering 16 to 35 VDC with minimum current
capability of 21 mA DC (per transmitter) must be used to power the control
loop. See Figure B for connection of the power supply, transmitter and
receiver. The range of appropriate receiver load resistance (RL) for the DC
power supply voltage available is expressed by the formula and graph in
Zero Adjustment
Allow transmitter to warm up for 30 minutes. Transmitter should be zeroed
at the temperature it is to be operated at.
A single push button is provided to zero the transmitter. Span is factory
calibrated to the range specified on the label. There is no user span
adjustment necessary.
MAINTENANCE/REPAIR
Upon final installation of the Series 616KD no routine maintenance is
required. The Series 616KD is not field serviceable and should be returned
if repair is needed. Field repair should not be attempted and may void
warranty.
WARRANTY/RETURN
Refer to “Terms and Conditions of Sales” in our catalog and on our website.
Contact customer service to receive a Return Goods Authorization number
before shipping the product back for repair. Be sure to include a brief
description of the problem plus any additional application notes.
Figure B
Figure D.
3-Wire Operation (4 to 20 mA Units)
An external power supply with minimum current capability of 21 mA DC
(per transmitter) delivering 16 to 35 VDC or 20 to 28 VAC is required. See
Figure C for connection of power supply, transmitter and receiver. The
range of appropriate receiver load resistance (RL) of DC and AC power
Figure C
supplies is expressed by the formula and graph in Figures D & E.
Figure D
Figure E
©Copyright 2013 Dwyer Instruments, Inc. Printed in U.S.A. 8/13 FR# 01-443641-50 Rev. 2
DWYER INSTRUMENTS, INC.
P.O. BOX 373 • MICHIGAN CITY, INDIANA 46360, U.S.A. Fax: 219/872-9057 e-mail: lit@dwyer-inst.com
Phone: 219/879-8000 www.dwyer-inst.com