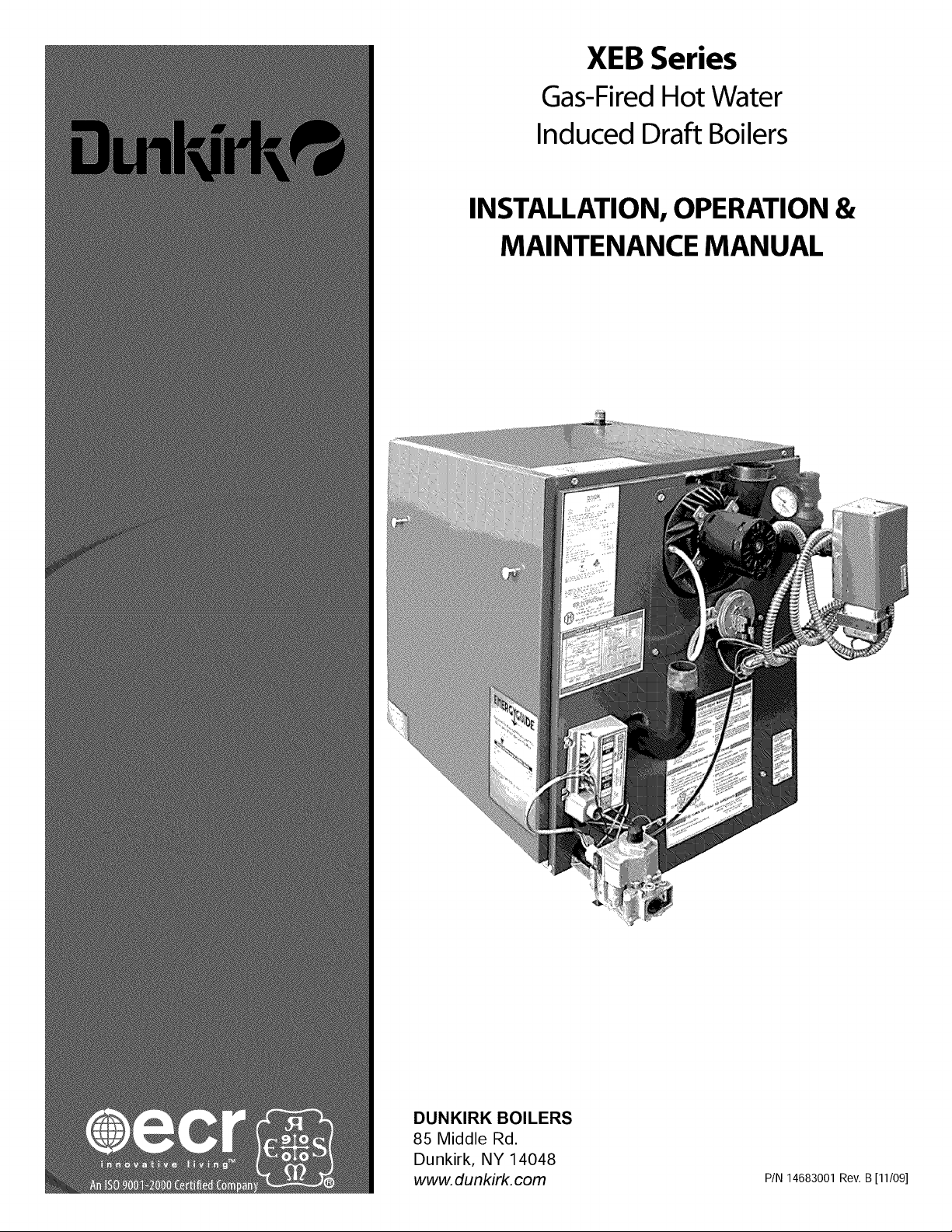
XEB Series
Gas-FiredHot Water
Induced Draft Boilers
INSTALLATION, OPERATION &
MAINTENANCE MANUAL
DUNKIRK BOILERS
85 Middle Rd.
Dunkirk, NY 14048
www. dunkirk, corn
P/N14683001 Rev.B[11/09]
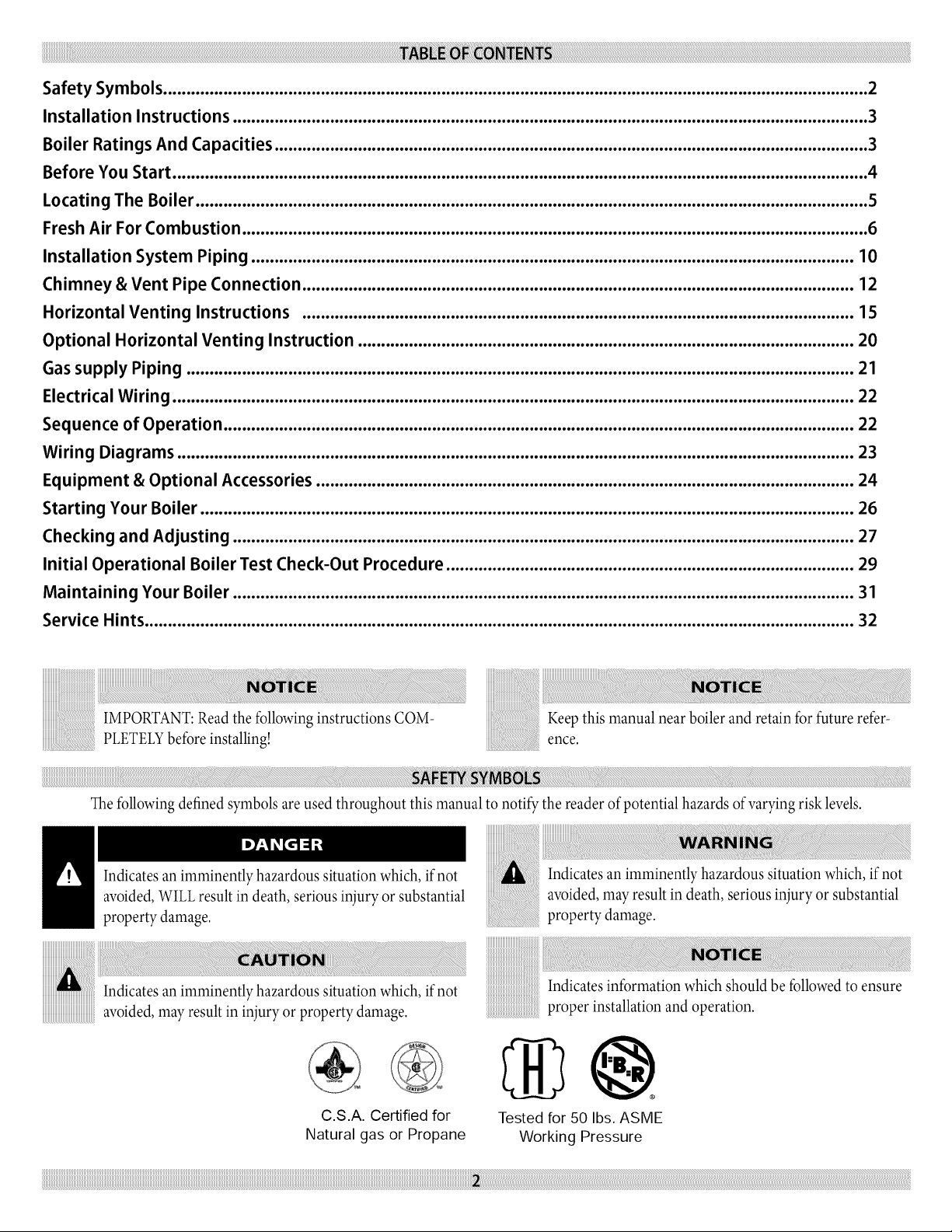
Safety Symbols ........................................................................................................................................................ 2
Installation Instructions ......................................................................................................................................... 3
Boiler Ratings And Capacities ................................................................................................................................ 3
Before You Start ...................................................................................................................................................... 4
Locating The Boiler ................................................................................................................................................. 5
Fresh Air For Combustion ....................................................................................................................................... 6
Installation System Piping .................................................................................................................................. 10
Chimney & Vent Pipe Connection ....................................................................................................................... 12
Horizontal Venting Instructions ....................................................................................................................... 15
Optional Horizontal Venting Instruction ........................................................................................................... 20
Gas supply Piping ................................................................................................................................................ 21
Electrical Wiring ................................................................................................................................................... 22
Sequence of Operation ........................................................................................................................................ 22
Wiring Diagrams .................................................................................................................................................. 23
Equipment & Optional Accessories .................................................................................................................... 24
Starting Your Boiler ............................................................................................................................................. 26
Checking and Adjusting ...................................................................................................................................... 27
Initial Operational Boiler Test Check-Out Procedure ........................................................................................ 29
Maintaining Your Boiler ...................................................................................................................................... 31
Service Hints ......................................................................................................................................................... 32
IMPORTANT:Readthe followinginstructions COM-
PLETELYbeforeinstalling!
Keepthis manual near boiler and retainfor future refer-
ence.
Thefollowingdefined symbolsareused throughout this manual to notify the reader ofpotential hazards ofvarying risk levels.
Indicates an imminently hazardous situation which, ifnot
avoided,WILLresult in death, serious injury or substantial
property damage.
Indicates an imminently hazardous situation which, ifnot
avoided,may result in injury or property damage.
Indicates an imminently hazardous situation which, ifnot
avoided,may result in death, serious injury or substantial
property damage.
Indicates information which shouldbe followedto ensure
proper installationand operation.
C.S.A. Certified for
Natural gas or Propane
Tested for 50 Ibs. ASME
Working Pressure
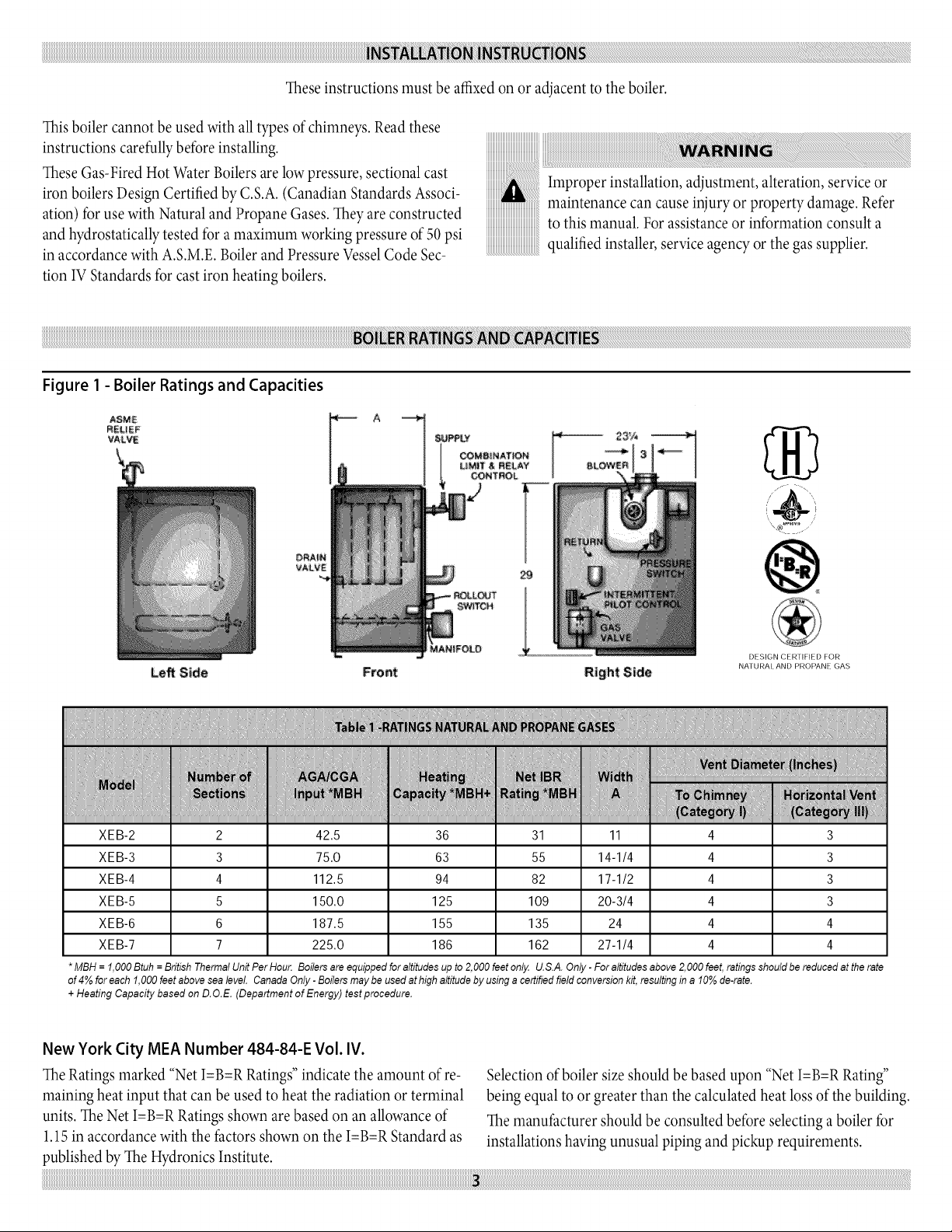
Theseinstructions must be affixedon or adjacent to the boiler.
Thisboiler cannot be usedwith alltypes ofchimneys.Read these
instructions carefullybefore installing.
TheseGas-Fired HotWater Boilersare lowpressure, sectionalcast
iron boilers Design Certifiedby C.S.A.(Canadian StandardsAssoci-
ation) foruse with Natural and Propane Gases.Theyare constructed
and hydrostaticallytested for amaximum workingpressure of 50psi
in accordancewith A.S.M.E.Boilerand PressureVesselCode Sec-
tion IV Standardsfor castiron heating boilers.
Figure 1 - Boiler Ratings and Capacities
ASME
R_LIEF
VALVE
iiiiiiiiiiiiiiii
iiiiiiiiiiiiiiiiiiiiiiiiiiiiiiiiiiiiiiiiiiiiii
iiiiiiiiiiiiiiiiiiiiiiiiiiiiiiiiiiiiiiiiiiiii_
iiiiiiiiiiiiiiiiiiiiiiiiiiiiiiiiiiiiiiiiiiiiii
iiiiiiiiiiiiiiiiiiiiiiiiiiiiiiiiiiiiiiiiiiiiii
iiiiiiiiiiiiiiiiiiiiiiiiiiiiiiiiiiiiiiiiiiiiii
Improper installation, adjustment, alteration, serviceor
maintenance can cause injuryor property damage.Refer
to this manual. For assistanceor information consult a
qualifiedinstaller,serviceagency or thegas supplier.
\,® .
VALVE
DESIGN CERTIFIED FOR
LeR Si_e Fro_t Right Side
XEB-2 2 42.5 36 31 11 4 3
XEB-3 3 75.0 63 55 14-1/4 4 3
XEB-4 4 112.5 94 82 17-1/2 4 3
XEB-5 5 150.0 125 109 20-3/4 4 3
XEB-6 6 187.5 155 135 24 4 4
XEB-7 7 225.0 186 162 27-1/4 4 4
*MBH = f,O00 Btuh = British Thermal Unit Per Hou_ Boilers areequipped foraltitudes up to 2,000 feet on!_ U.S.A. Only - For altitudes above 2,000 feet, ratings should be reducedat therate
of 4% for each f,O00feet above sealevel. Canada Only -Boilers may be used at high altitude by using a certified field conversion kit, resulting in a 10%de-rate.
+ Heating Capacity based on D.O.E. (Department of Energy) testprocedure.
NATURAt AND PROPANE GAS
New York City MEA Number 484-84-E Vol. IV.
TheRatingsmarked "Net I=B=RRatings"indicate the amount of re-
maining heat input that can be usedto heat the radiation or terminal
units. The Net I=B=RRatingsshown are based on an allowanceof
1.15in accordancewith thefactors shownon the I=B=RStandard as
publishedby TheHydronicsInstitute.
Selectionofboiler sizeshould be basedupon "NetI=B=RRating"
being equalto or greaterthan the calculated heat lossofthe building.
Themanufacturer shouldbe consulted before selecting a boiler for
installations havingunusual piping and pickup requirements.

iiiiiiiiiiiiiiiiiiiiiiiiiiiiiiiiiiiiiiiiiiiiiiiiiiiiiiiiiiiiiiiiiiiiiiiiiiiiiiiiiiiiiiiiiiiiiiiiiiiiiiiiiiiiiiiiiiiiiiiiiiiiiiiiiiiiiiiiiiiiiiiiiiiiiiiiiiiiiiiiiiiiiiiiiiiiiiiiiiiiiiiiiiiiiiiiiiiiiiiiiiiiiiiiiiiiiiiiiiiiiiiiiiiiiiiiiiiiiiiiiiiiiiiiiiiiiiiiiiiiiiiiiiiiiiiiiiiiiiiiiiiiiiiiiiiiiiiiiiiiiiiiiiiiiiiiiiiiiiiiiiiiiiiiiiiiiiiiiiiiiiiiiiiiiiiiiiiiiiiiiiiiiiiiiiiiiiiiiiiiiiiiiiiiiiiiiiiiiiiiiiiiiiiiiiiiiiiiiiiiiiiiiiiiiiiiiiiiiiiiiiiiiiiiiiiiiiiiiiiiiiiiiiiiiiiiiiiiiiiiiiiiiiiiiiiiiiiiiiiiiiiiiiiiiiiiiiiiiiiiiiiiiiiiiiiiiiiiiiiiiiiiiiiiiiiiiiiiiiiiiiiiiiiiiiiii_¸i__i_!_!_l_i_!i!!_i_i_!!i_!i_!i_!i_!!_iii_i_ii_ii_i_ii_i!i__!i_!i_!ii!i_i_i__i_!i!i_!i!i_i!_i!_i¸_ii¸_iiiiii¸_ii¸_iiiiii¸_ii¸_iiiiii¸_ii¸_iiiiii¸_ii¸_iiiiii¸_ii¸_iiiiii¸_ii¸_iiiiii¸_ii¸_iiiiii¸_ii¸_iiiiii¸_ii¸_iiiiii¸_ii¸_iiiiii¸_ii¸_iiiiii¸_ii¸_iiiiii¸_ii¸_iiiiii¸_ii¸_iiiiii¸_ii¸_iiiiii¸_ii¸_iiiiii¸_ii¸_iiiiii¸_ii¸_iiiiii¸_ii¸_iiiiii¸_ii¸_iiiiii¸_ii¸_iiiiii¸_ii¸_iiiiii¸_ii¸_iiiiii¸_ii¸_iiiiii¸_ii¸_iiiiii¸_ii¸_iiiiii¸_ii¸_iiiiii¸_ii¸_iiiiii¸_ii¸_iiiiii¸_ii¸_iiiiii¸_ii¸_iiiiii¸_ii¸_iiiiii¸_ii¸_iiiiii¸_ii¸_iiiiii¸_ii
Theseboilers must stand on a noncombustible floor.If installed on
a combustiblefloor,pleaserefer to the Repair Parts manual for the
appropriate CombustibleFloor Basepart number.
TheseGas-Fired HotWater Boilersare lowpressure, sectionalcast
iron boilers Design Certifiedby CSA(Canadian StandardsAssocia-
tion) foruse with Natural and Propane Gases.Theyare constructed
and hydrostaticallytested for amaximum workingpressure of 50psi
(pounds per square inch) in accordance with A.S.M.E.(American
Societyof Mechanical Engineers)Boilerand PressureVesselCode
Section IV Standards forcast iron heating boilers.
Boilers For UseAt High Altitude
Thisboiler is factory equipped for useat altitudesof 0-2,000feet
abovesealevel.For useat altitudes above2,000feet abovesea level,
the input ratings arereducedby a change in main burner orificesize.
U.S.A.Only- For altitudesabove2,000feet abovesea level,input
ratingsshould be reduced atthe rateof 4% for each 1,000feet above
sealevel.Consult the NationalFuel GasCode (NFPA54/ANSI
Z223.l-latest revision), orthe manufacturer for correct orifice siz-
inginformation. Highaltitude orificesare availablefrom theboiler
manufacturer.
Canada Only - For altitudes in the rangeof2,000-4,500feetabove
sealevel,boilers maybe fieldequipped foruse at high altitudeby
usinga certified fieldconversion kit.Thechangein main burner
orifice size results in the boiler'sinput rating beingreduced by 10%.
Theconversionshall be carried out by a manufacturer'sauthorized
representative,in accordancewith the requirements of the manufac-
turer, provincialor territorial authorities havingjurisdiction and in
accordancewith the requirements of the CSA-B149.1and CSA-
B149.2Installation Codes. Thecertifiedfield conversionkit includes
aconversion data plate,which must beattached to the boileradja-
centto the ratingplate, indicatingthat the boiler hasbeen converted
for high altitude use.The conversiondata platemust be filledin with
the correct conversioninformation.
Checkto be sureyou havethe right sizeboiler beforestarting the
installation. Seerating and capacitytable on previous page.Also be
sure thenew boileris for thetype of gas youare using. Checkthe
rating plateon the right side of the boiler.
Verifythat the boiler is suppliedwith the correct type ofgas,fresh air
for combustion,and a suitableelectricalsupply.Also,the boilermust
be connectedto a suitablechimney or horizontal venting systemand
an adequatepiping system. Finally,athermostat, properly located,is
needed for controlof the heating system.Ifyou haveanydoubts as
to the variousrequirements, checkwith localauthorities and obtain
professionalhelp whereneeded. Takethe time to completeallof the
stepsfor SAFEand PROPERoperation ofthe heating system.
Ifthis boiler is installed in a building under construction, special
caremust be taken to insure a clean combustion air supplydur-
ing the construction process.Airborne particulates such asfrom
drywalldust and from fiberglassinsulation can clogthe burner ports
and causeincompletecombustion and sooting. Where required by
the authority having jurisdiction, theinstallation must conform to
American SocietyofMechanicalEngineers SafetyCode for Controls
and SafetyDevicesfor AutomaticallyFired Boilers,No. CSD-1.
Theinstallationmust conformto the requirements ofthe authority
havingjurisdiction or,in the absence of suchrequirements, to the
NationalFuel GasCode, ANSIZ223.l-latest revision.
In Canada,the boiler shallbe installed accordingto CSA-B149.1and
.2,Installation Code for GasBurning Appliancesand Equipment.
iiiiiiiiiiiiiiiiiiiiiiiiiiiiiiiiiiiiiiiiiiiiii
als, gasoline and other flammable vapors and liquids
Keep boiler area clean and free from combustible materi-
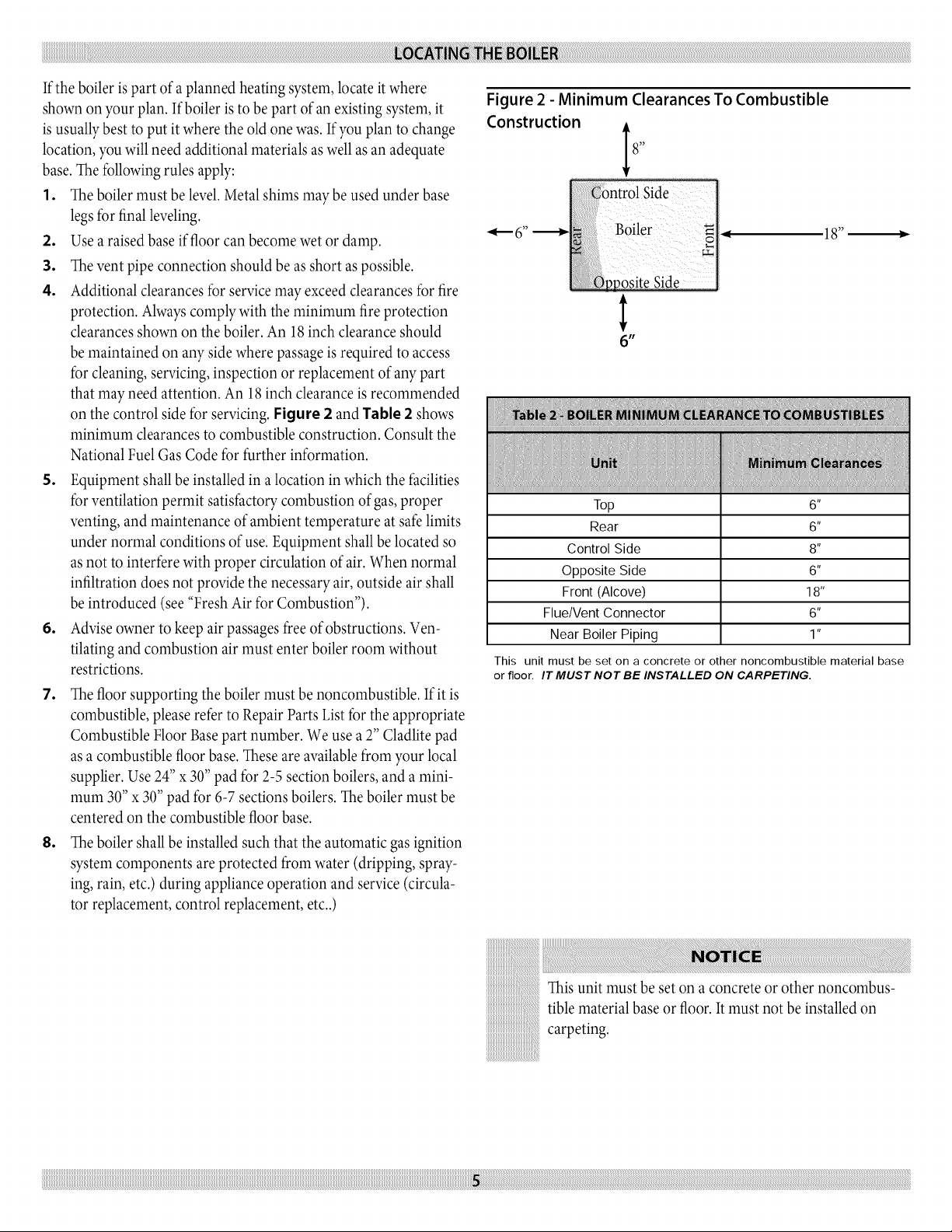
Ifthe boiler is part of a planned heatingsystem, locateit where
shown on your plan. If boiler isto be part of an existingsystem,it
is usuallybest to put it where the oldone was. Ifyou plan to change
location,you willneed additionalmaterials aswellas an adequate
base.Thefollowingrules apply:
1. Theboiler must be level.Metal shimsmay be used underbase
legsfor finalleveling.
2. Use a raised baseif floor canbecomewet or damp.
3. The vent pipe connection should be asshort aspossible.
4. Additional clearancesfor servicemay exceedclearancesfor fire
protection. Alwayscomplywith theminimum fireprotection
clearancesshownon the boiler.An 18inchclearance should
bemaintained on anyside where passageisrequired to access
for cleaning,servicing,inspection or replacement ofany part
that may need attention. An 18inch clearanceis recommended
on the control sidefor servicing. Figure 2 and Table2 shows
minimum clearances to combustible construction. Consult the
National Fuel Gas Code for further information.
5. Equipment shallbe installedin alocation in whichthe facilities
forventilation permit satisfactorycombustion ofgas,proper
venting,and maintenance of ambient temperature atsafelimits
under normal conditions ofuse. Equipment shallbe located so
asnot tointerfere with proper circulation ofair. When normal
infiltration doesnot provide the necessaryair, outside airshall
beintroduced (see"Fresh Air for Combustion").
6. Adviseowner tokeep airpassagesfree ofobstructions. Ven-
tilating and combustion air must enter boiler room without
restrictions.
.
Thefloorsupporting the boilermust benoncombustible. If itis
combustible,pleaserefer to RepairParts Listfor the appropriate
Combustible Floor Basepart number. We usea 2" Cladlitepad
asa combustible floorbase. Theseare availablefrom your local
supplier. Use24" x30"pad for 2-5 sectionboilers,and amini-
mum 30"x 30"pad for 6-7sections boilers. Theboiler must be
centered on the combustible floor base.
8,
Theboilershall be installedsuch that the automatic gasignition
systemcomponents are protected from water (dripping, spray-
ing,rain, etc.) during applianceoperation and service(circula-
tor replacement, control replacement,etc..)
Figure 2 - Minimum Clearances To Combustible
Construction i8,,
_1_ 6 _'
Boiler _ ,_
18"
_ositeSide
6"
Top 6"
Rear 6"
Control Side 8"
Opposite Side 6"
Front (Alcove) 18"
Flue/Vent Connector 6"
Near Boiler Piping 1"
This unit must be set on a concrete or other noncombustible material base
or floor. IT MUST NOT BE INSTALLED ON CARPETING.
Thisunit must be set on a concreteor other noncombus-
tiblematerial base or floor.It must not be installed on
carpeting.
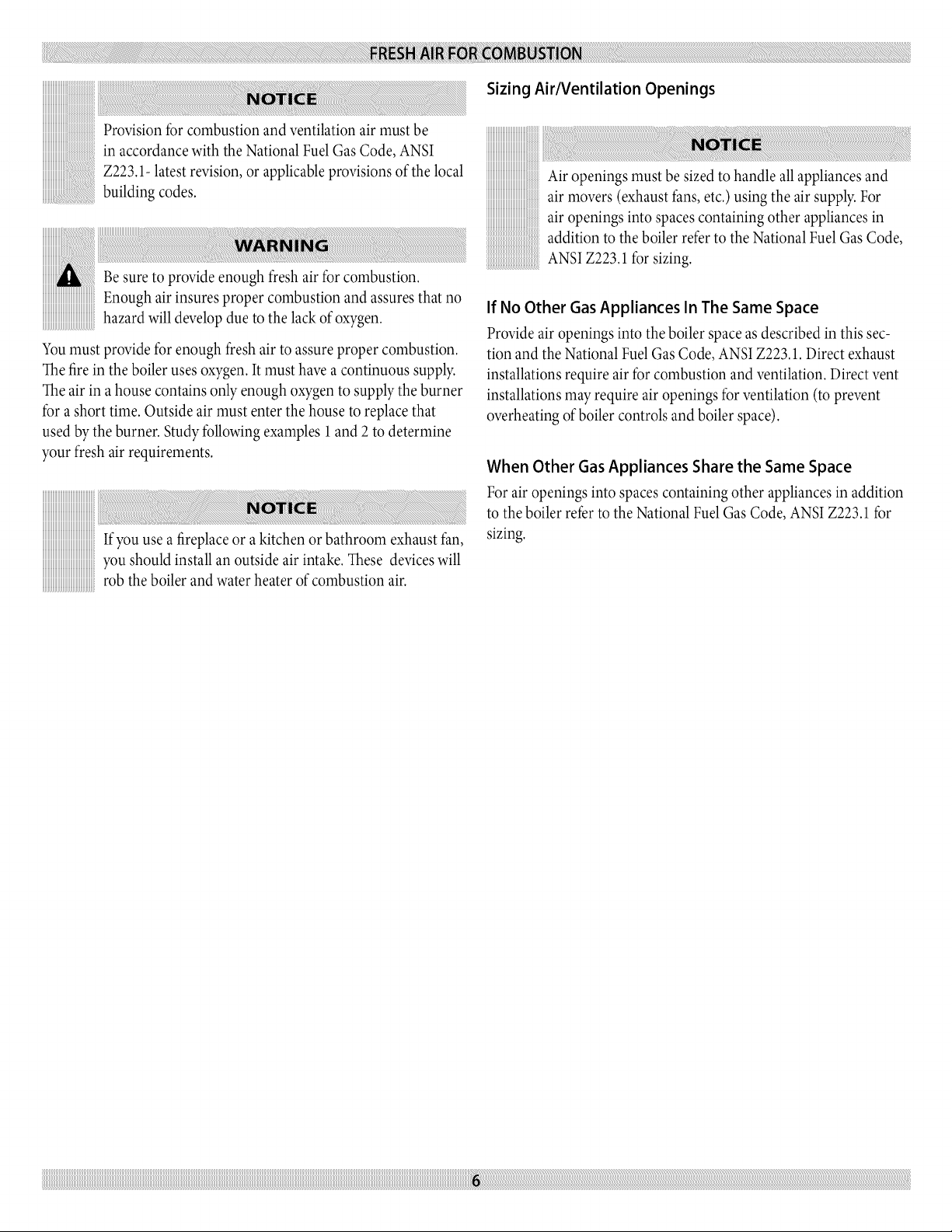
Provisionforcombustionandventilationairmustbe
inaccordancewiththeNationalFuelGasCode,ANSI
Z223.1-latestrevision,orapplicableprovisionsofthelocal
buildingcodes.
Besuretoprovideenoughfreshairforcombustion.
Enoughairinsurespropercombustionandassuresthatno
hazardwilldevelopduetothelackofoxygen.
Youmustprovideforenoughfreshairtoassurepropercombustion.
Thefireintheboilerusesoxygen.Itmusthaveacontinuoussupply.
Theairinahousecontainsonlyenoughoxygentosupplytheburner
forashorttime.Outsideairmustenterthehousetoreplacethat
usedbytheburner.Studyfollowingexamples1and2todetermine
yourfreshairrequirements.
iiiiiiiiiiiiiiiiiiiiiiiiiiiiiiiiiiiiiiiiiiiiii_
iiiiiiiiiiiiiiiiiiiiiiiiiiiiiiiiiiiiiiiiiiiiii_
Ifyou use afireplaceor a kitchen or bathroom exhaustfan,
you should installan outside air intake. These deviceswill
rob theboiler and water heater of combustion air.
Sizing Air/Ventilation Openings
Airopenings must be sized to handle allappliances and
air movers(exhaust fans,etc.) usingthe air supply.For
air openingsinto spaces containing other appliancesin
addition to the boiler referto the NationalFuel GasCode,
ANSIZ223.1for sizing.
If NoOther GasAppliances InThe Same Space
Provide air openings intothe boiler spaceas describedin this sec-
tion and the National FuelGasCode,ANSI Z223.1.Direct exhaust
installationsrequire airfor combustion and ventilation. Directvent
installationsmay require air openings for ventilation(to prevent
overheatingof boiler controls and boiler space).
When Other GasAppliances Sharethe Same Space
For airopenings into spaces containing other appliancesin addition
to the boiler referto the NationalFuel GasCode,ANSI Z223.1for
sizing.
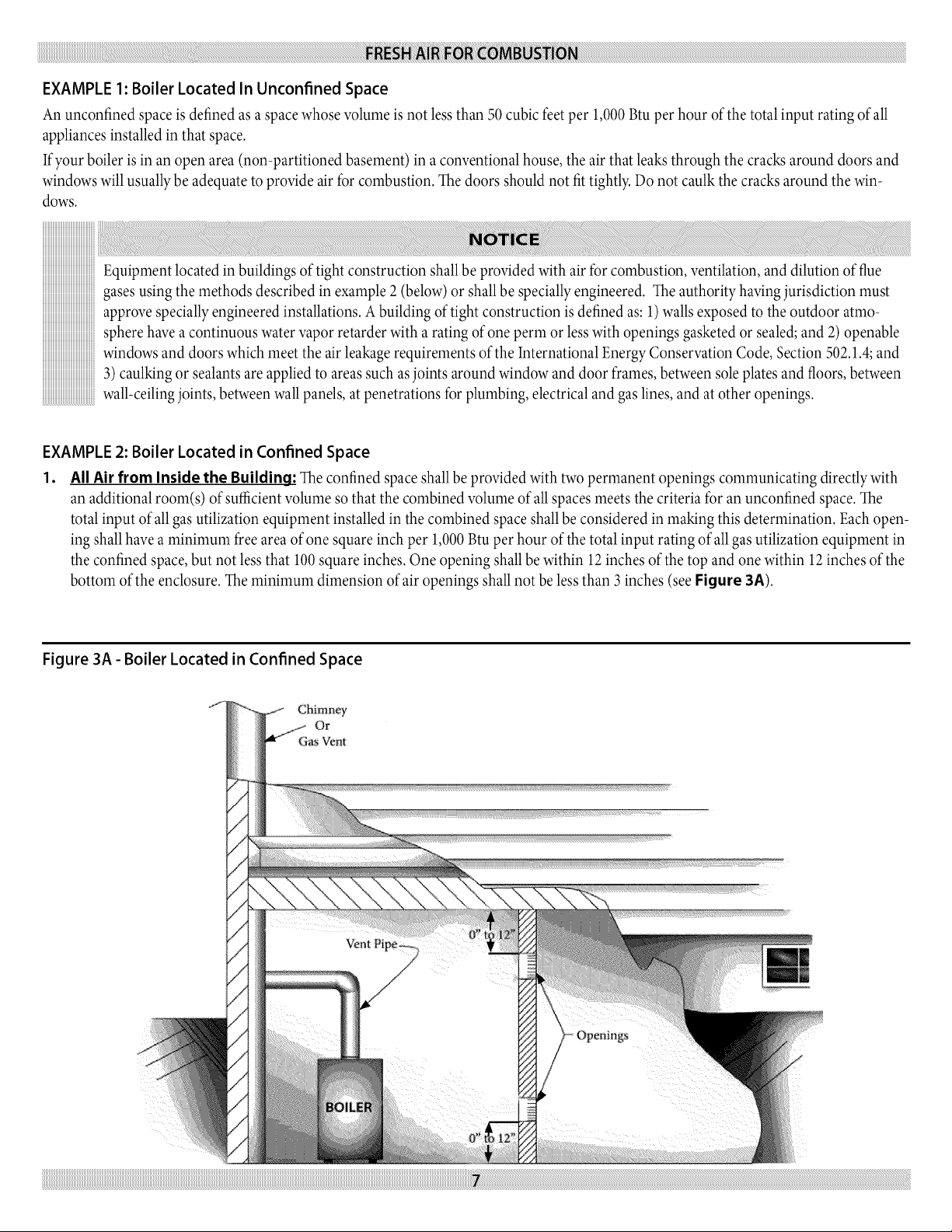
EXAMPLE 1: Boiler Located In Unconfined Space
An unconfined space is defined as a space whose volume is not less than 50 cubic feet per 1,000 Btu per hour of the total input rating of all
appliances installed in that space.
If your boiler is in an open area (non-partitioned basement) in a conventional house, the air that leaks through the cracks around doors and
windows will usually be adequate to provide air for combustion. The doors should not fit tightly. Do not caulk the cracks around the win-
dows.
iiiiiiiiiiiiiiiiiiiiiiiiiiiiiiiiiiiiiiiiiiiiii_
Equipment located in buildings of tight construction shall be provided with air for combustion, ventilation, and dilution of flue
gases using the methods described in example 2 (below) or shall be specially engineered. The authority having jurisdiction must
approve specially engineered installations, a building of tight construction is defined as: 1)walls exposed to the outdoor atmo-
sphere have a continuous water vapor retarder with a rating of one perm or less with openings gasketed or sealed; and 2) openable
windows and doors which meet the air leakage requirements of the International Energy Conservation Code, Section 502.1.4; and
3) caulking or sealants are applied to areas such as joints around window and door frames, between sole plates and floors, between
wall-ceiling joints, between wall panels, at penetrations for plumbing, electrical and gas lines, and at other openings.
EXAMPLE 2: Boiler Located in Confined Space
1. All Air from Inside the Building: The confined space shall be provided with two permanent openings communicating directly with
an additional room(s) of sufficient volume so that the combined volume of all spaces meets the criteria for an unconfined space. The
total input of all gas utilization equipment installed in the combined space shall be considered in making this determination. Eachopen-
ing shall have a minimum free area of one square inch per 1,000 Btu per hour of the total input rating of all gas utilization equipment in
the confined space, but not less that 100 square inches. One opening shall be within 12 inches of the top and one within 12 inches of the
bottom of the enclosure. The minimum dimension of air openings shall not be less than 3 inches (see Figure 3A).
Figure 3A - Boiler Located in Confined Space
f
Chimney
Or
GasVent
Vent Pipe_
) Openings
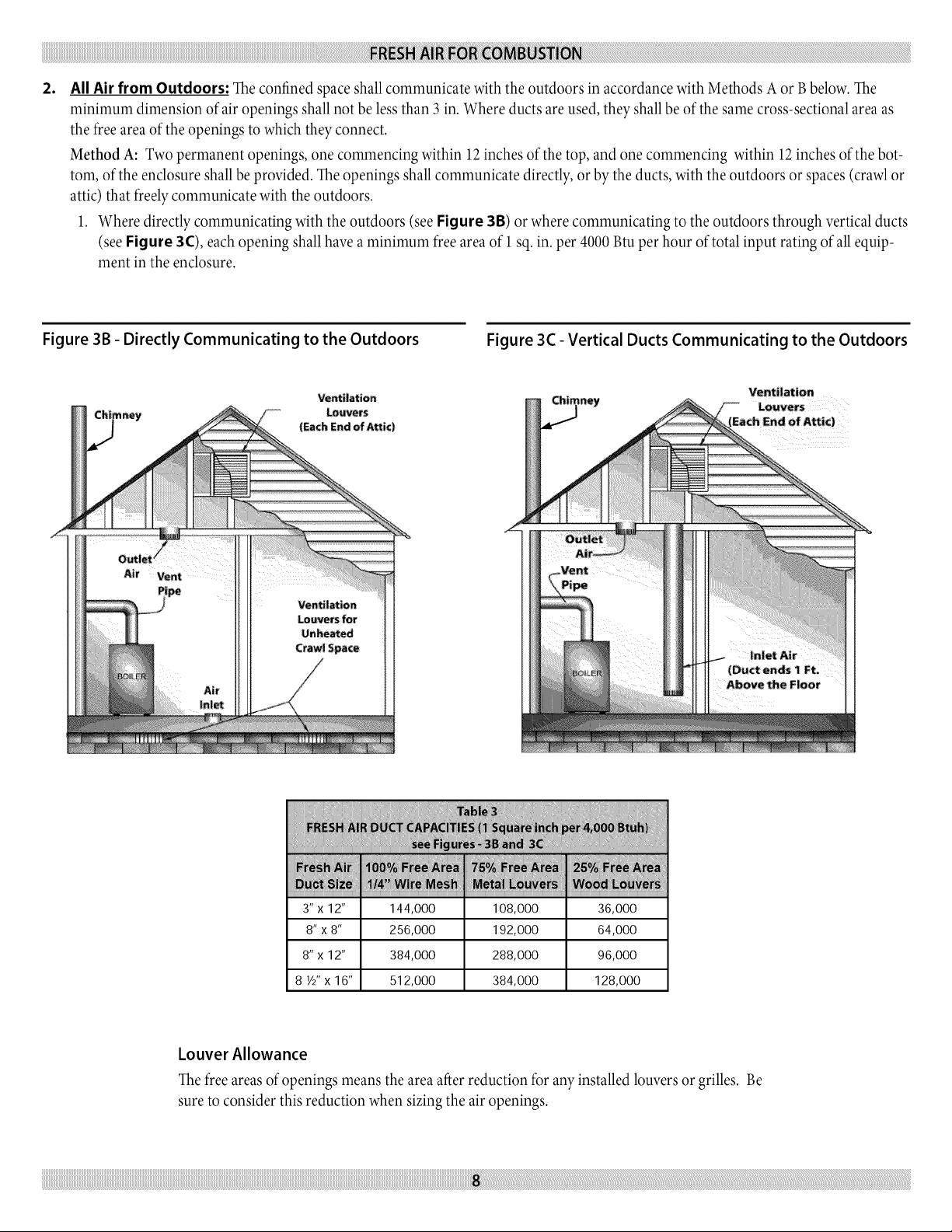
o
All Air from Outdoors: The confined space shall communicate with the outdoors in accordance with Methods A or Bbelow. The
minimum dimension of air openings shall not be less than 3 in. Where ducts are used, they shall be of the same cross-sectional area as
the free area of the openings to which they connect.
Method A: Two permanent openings, one commencing within 12 inches of the top, and one commencing within 12inches of the bot-
tom, of the enclosure shall be provided. The openings shall communicate directly, or by the ducts, with the outdoors or spaces (crawl or
attic) that freely communicate with the outdoors.
1. Where directly communicating with the outdoors (see Figure 3B) or where communicating to the outdoors through vertical ducts
(see Figure 3C), each opening shall have aminimum free area of 1 sq. in. per 4000 Btu per hour of total input rating of all equip-
ment in the enclosure.
Figure 3B - Directly Communicating to the Outdoors Figure 3C - Vertical Ducts Communicating to the Outdoors
Air
Pipe
3"x 12" 144,000 108,000 36,000
8"x 8" 256,000 192,000 64,000
8"x 12" 384,000 288,000 96,000
8 ½"x16" 512,000 384,000 128,000
Louver Allowance
The free areas of openings means the area after reduction for any installed louvers or grilles. Be
sure to consider this reduction when sizing the air openings.
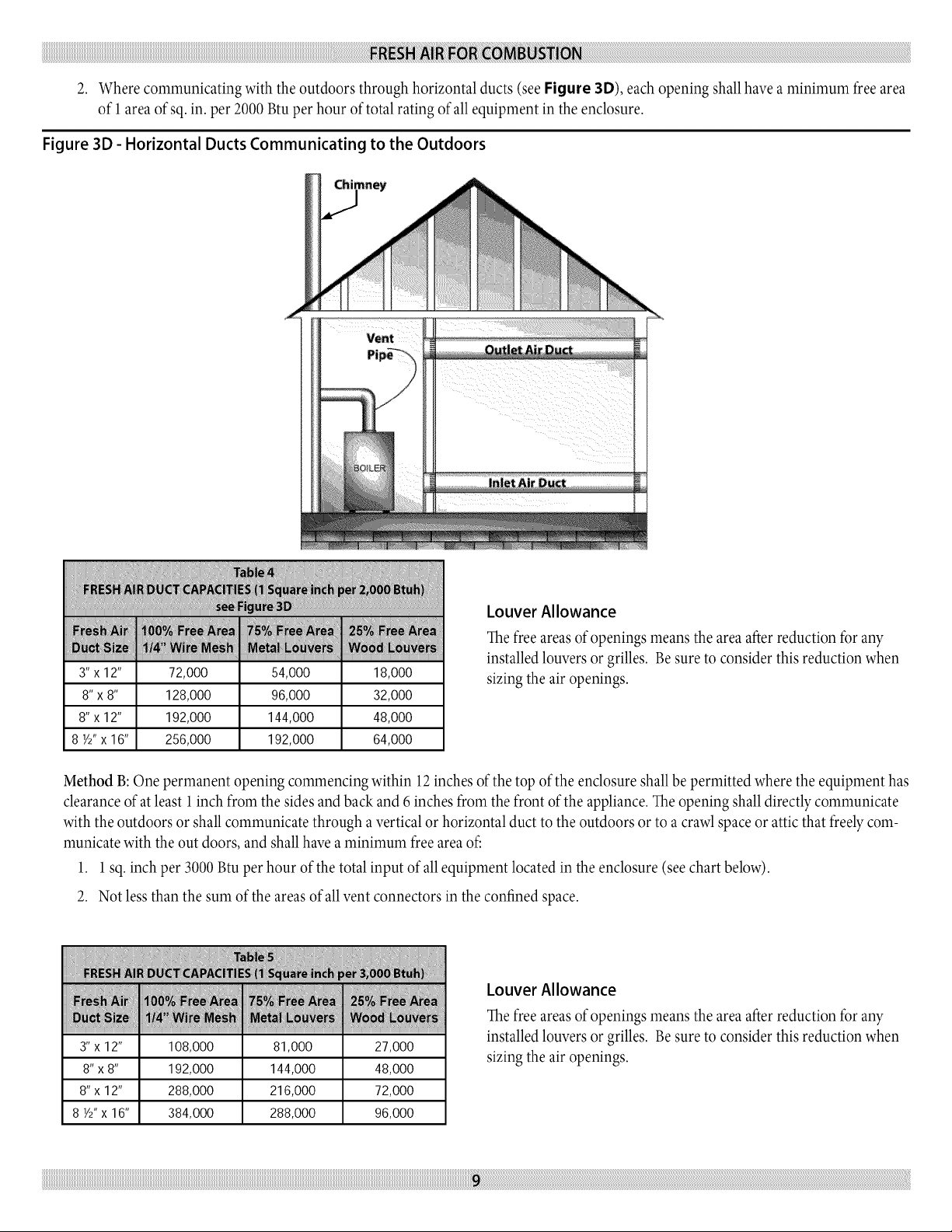
2. Wherecommunicatingwiththeoutdoorsthroughhorizontalducts(seeFigure 3D), each opening shall have a minimum free area
of 1area ofsq. in. per 2000 Btu per hour of total rating of all equipment in the enclosure.
Figure 3D - Horizontal Ducts Communicating to the Outdoors
Louver Allowance
The free areas of openings means the area after reduction for any
installed louvers or grilles. Be sure to consider this reduction when
3"x 12" 72,000 54,000 18,000
8"x 8" 128,000 96,000 32,000
8"x 12" 192,000 144,000 48,000
8 ½"x16" 256,000 192,000 64,000
sizing the air openings.
Method B:One permanent opening commencing within 12 inches of the top of the enclosure shall be permitted where the equipment has
clearance of at least 1inch from the sides and back and 6 inches from the front of the appliance. The opening shall directly communicate
with the outdoors or shall communicate through a vertical or horizontal duct to the outdoors or to a crawl space or attic that freely com-
municate with the out doors, and shall have a minimum free area off
1. 1 sq. inch per 3000 Btu per hour of the total input of all equipment located in the enclosure (see chart below).
2. Not less than the sum of the areas of all vent connectors in the confined space.
Louver Allowance
The free areas of openings means the area after reduction for any
3"x12" 108,000 81,000 27,000
8"x 8" 192,000 144,000 48,000
8"x12" 288,000 216,000 72,000
8 ½"x 16" 384,000 288,000 96,000
installed louvers or grilles. Be sure to consider this reduction when
sizing the air openings.
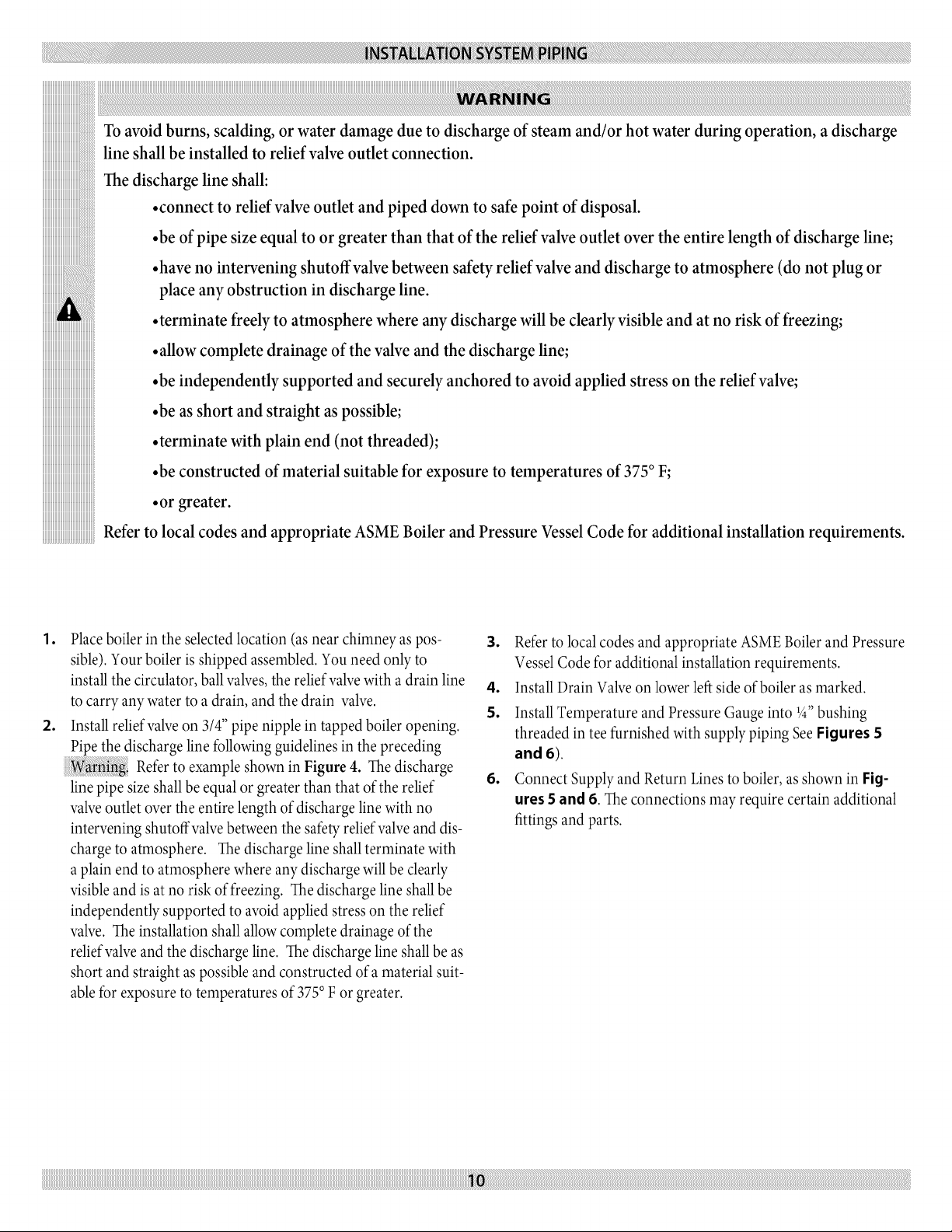
To avoid burns, scalding, or water damage due to discharge of steam and/or hot water during operation, a discharge
line shall be installed to relief valve outlet connection.
The discharge line shall:
•connect to relief valve outlet and piped down to safe point of disposal.
•be of pipe size equal to or greater than that of the relief valve outlet over the entire length of discharge line;
•have no intervening shutoffvalve between safety relief valve and discharge to atmosphere (do not plug or
place any obstruction in discharge line.
iiiiiiiiiiii_iiiiiiiiiii_
•terminate freely to atmosphere where any discharge will be clearly visible and at no risk of freezing;
•allow complete drainage of the valve and the discharge line;
iiiiiiiiiiiiiiiiiiiiiiiiiiiiiiiiiiiiiiiiiiiiiii
•be independently supported and securely anchored to avoid applied stress on the relief valve;
iiiiiiiiiiiiiiiiiiiiiiiiiiiiiiiiiiiiiiiiiiiiiii
iiiiiiiiiiiiiiiiiiiiiiiiiiiiiiiiiiiiiiiiiiiiiii
iiiiiiiiiiii
Refer to local codes and appropriate ASME Boiler and Pressure Vessel Code for additional installation requirements.
1. Place boiler in the selected location (as near chimney as pos- 3.
sible). Your boiler is shipped assembled. You need only to
install the circulator, ball valves, the relief valve with a drain line
to carry any water to a drain, and the drain valve.
o
Install relief valve on 3/4" pipe nipple in tapped boiler opening.
Pipe the discharge line following guidelines in the preceding
line pipe size shall be equal or greater than that of the relief
valve outlet over the entire length of discharge line with no
intervening shutoffvalve between the safety relief valve and dis-
charge to atmosphere. Thedischarge line shall terminate with
a plain end to atmosphere where any discharge will be clearly
visible and is at no risk of freezing. The discharge line shall be
independently supported to avoid applied stress on the relief
valve. The installation shall allow complete drainage of the
relief valve and the discharge line. The discharge line shall be as
short and straight as possible and constructed of a material suit-
able for exposure to temperatures of 375° F or greater.
•be as short and straight as possible;
•terminate with plain end (not threaded);
•be constructed of material suitable for exposure to temperatures of 375° F;
•or greater.
Referto localcodes and appropriate ASMEBoilerand Pressure
VesselCode for additional installation requirements.
o
Install Drain Valveon lowerleftside ofboiler as marked.
5.
Install Temperature and Pressure Gauge into 1A,,bushing
threaded in tee furnished with supply piping See Figures 5
Refer to example shown in Figure 4. The discharge
and 6).
6,
Connect Supply and Return Lines to boiler, as shown in Fig-
ures 5 and 6. The connections may require certain additional
fittings and parts.

Figure 4 - Relief Valve Discharge Piping
RELIEFVALVE
DISCHARGE
PIPING
Check local code_
for maximum
distance from
floor or other al-
lowable safe point
of discharge
Figure 6 - Forced Hot Water Typical Piping With Zone
Control Valve
ZONE VALVE o,
Figure 5 - Forced Hot Water Typical Piping
MAiN
T_K