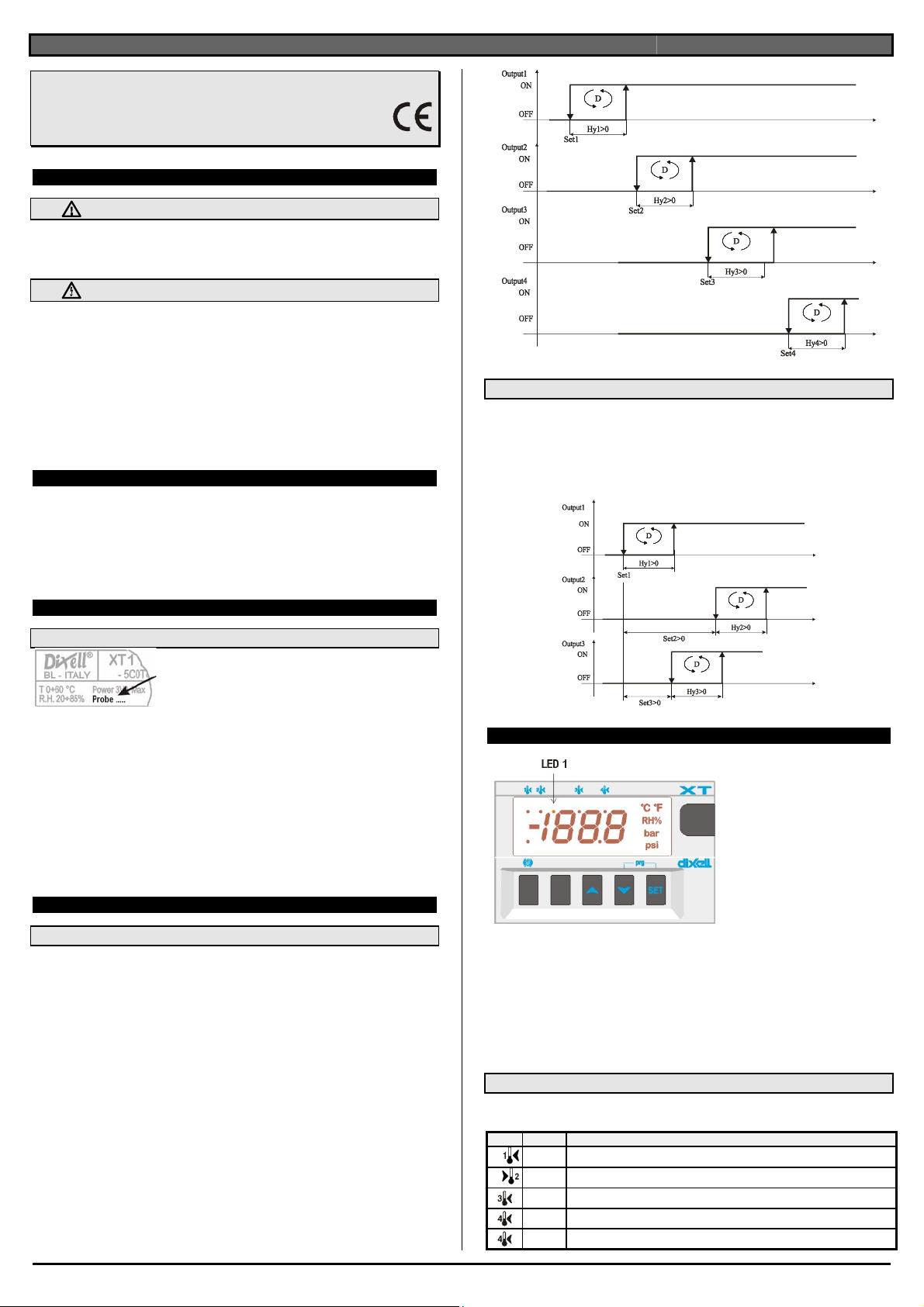
dIXEL
Installing and Operating Instructions
XT151D – XT160D
Three Four Stages Digital Controllers
with Multi Probe Input
1. GENERAL WARNING
1.1 PLEASE READ BEFORE USING THIS MANUAL
• This manual is part of the product and should be kept near the instrument for easy and quick reference.
• The instrument shall not be used for purposes different from those described hereunder. It cannot be
used as a safety device.
• Check the application limits before proceeding.
1592002250
1.2
• Check the supply voltage is correct before connecting the instrument.
• Do not expose to water or moisture: use t he controller only withi n the operating limit s avoiding sudden
• Warning: disconnect all electrical connections before any kind of maintenance.
• The instrument must not be opened.
• In case of failure or faulty operation send the instrument back to the dist ributor or to “ DIXELL S.p.A”
• Consider the maximum current which can be applied to each relay (see Technical Data).
• Ensure that the wires for probes, loads and the power supply are separated and far enough from each
• In case of applications in industrial environments, the use of mains fil ters (our mod. FT1) in parallel with
SAFETY PRECAUTIONS
temperature changes with high atmospheric humidity to prevent formation of condensation
(see address) with a detailed description of the fault.
other, without crossing or intertwining.
inductive loads could be useful.
2. GENERAL DESCRIPTION
The XT151D and XT160D (DIN RAIL format) are three (XT151D) or four (XT160D) stage ON/OFF
controllers for temperature, humidity and pressure applications with direct or inverse action, userselectable. The analogue input type can be set by paramet er between the f ollowing, according to the
model:
- PTC, NTC;
- PTC, NTC, Pt100, Thermocouple J, K, S;
- 4÷20mA, 0÷1V, 0÷10V.
3. FIRST INSTALLATION
3.1 PROBE SETTING
The pre-set probe type is written on the label of the instrument,
see picture. If it is different from the probe that has be used, set
the probe following procedure below
3.1.1 How to set the probe.
1. Enter the programming menu by pressing the SET+ n for 3s.
2. Select the Pbc (Probe configuration) parameter and push the SET key.
3. Set the kind of probe:
a. Controller for temperature: Pt= Pt 100, J = J thermocouple, c = K thermocouple, S
= S thermocouple; Ptc = PTC; ntc = ntc.
b. Controller with current or voltage inputs: cur=4÷20mA, 0-1= 0÷1V, 10= 0÷10V
4. Push the SET key to confirm it.
5. Switch the controller off and on again.
NOTE: Before proceeding check and, if necessary; set with appropriate values the Minimum Set
Points (LS1 e LS2) and Maximum Set Points (US1 e US2). See also th e paragraphs concerning
the programming.
4. REGULATIONS
4.1 3 OR 4 INDEPENDENT OUTPUTS (OUC=IND)
3 or 4 independent control stages (ouC=ind): output #1 at direct (S1C=dir) or inverse (S1C=in)
action; output #2 at (S2C = dir) direct or inverse (S2C =in) act ion, output #3 at (S3C = dir) direct or
inverse (S3C =in) action, output #4 (only for XT160D) at (S4C = dir) direct or inverse (S4C =in)
action.
E.I. with OUC = ind, S1C = dir (cooling), S2C = dir (cooling), S3C = dir (cooling), S4C = dir
(cooling).
4.2 3 OR 4 DEPENDENT OUTPUTS (OUC=DIP)
With dependent control stages (ouC=diP) SET2 and SET3 are related to SET1:
therefore SET2 is: SET1+SET2, while SET3 = SET1 + SET3
output #1 with direct or inverse action according to the S1C parameter; output # 2 with direct or
inverse action according to the S2C, output #3 with direct or inverse action according to the S3C,
output #4 (only for XT160D) with direct or inverse action according to the S4C.
E.I. 3 outputs OUPUTS (XT151D) with ouC=diP (dependent), S1C = dir (cooling), S2C = dir
(cooling), S3C = dir (cooling).
5. FRONT PANEL COMMANDS
KEY COMBINATIONS:
o + n To lock & unlock the keyboard.
SET + n To enter in programming mode.
SET + o To return to the room temperature display.
SET: To display and modify target set
points; in programming mode it
selects a parameter or confirm an
operation.
TO SWITCH THE INSTRUMENT
ON/OFF: If the function is enabled
(par. onF=yES), by pressing the
SET key for more than 4s the
controller is switched OFF. To
switch the instrument on again
press the SET key.
o UP: in programming mode it browses
the parameter codes or increases
the displayed value. Hold it pressed
for a faster change
n DOWN: in programming mode it
browses the parameter codes or
decreases the displayed value. Hold
it pressed for a faster change
5.1 USE OF LEDS
A series of light points on the front panels is used to monitor the loads controlled by the instrument.
Each LED function is described in the following table.
LED MODE FUNCTION
ON Output 1 enabled
ON Output 2 enabled
ON Output 3 enabled
ON Output 4 enabled – Only for XT160D
Flashing - Programming Phase (flashing with LED1)
1592002250 XT151-160D GB R.1.08.03.2005 XT151D – XT160D 1/4
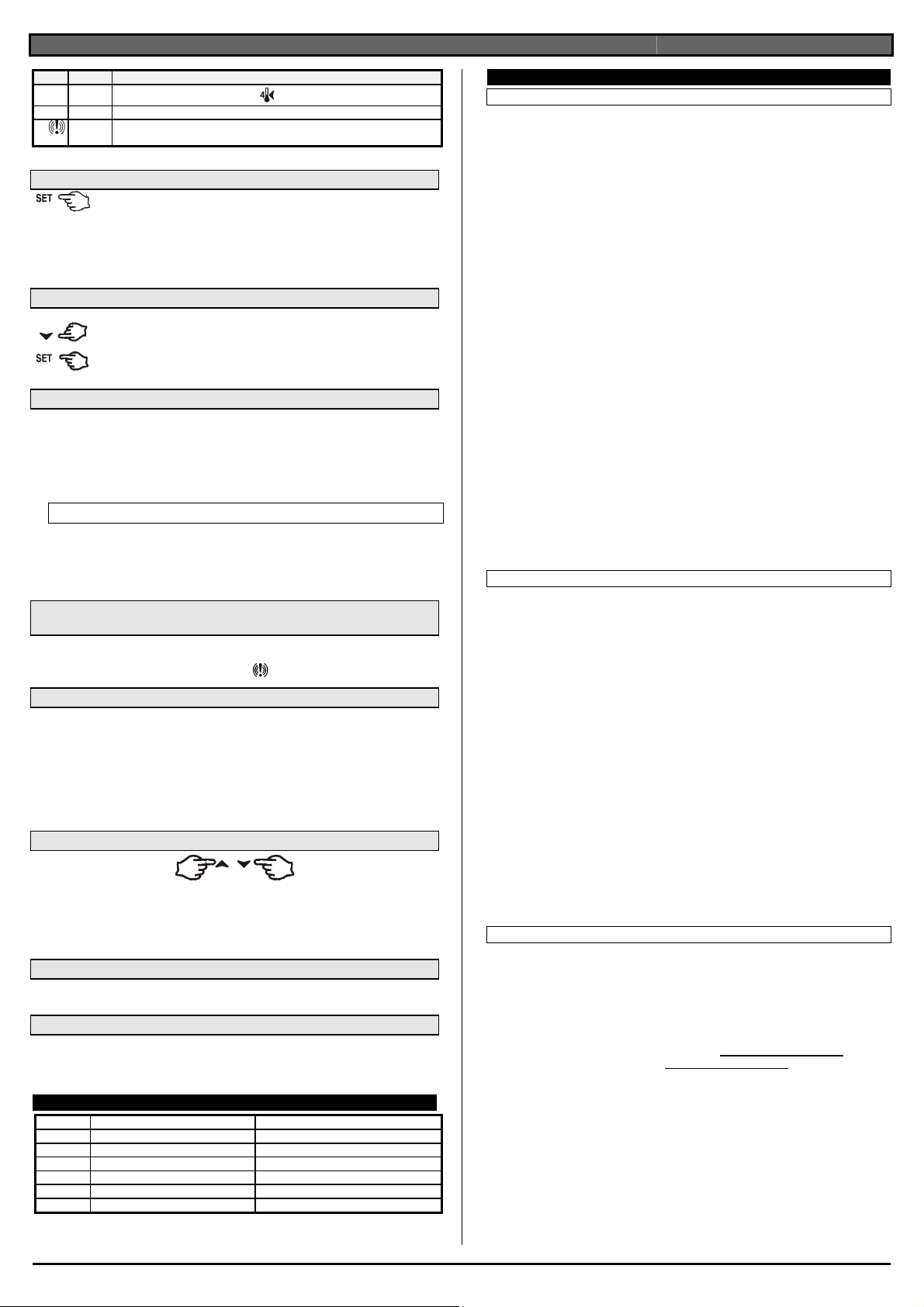
dIXEL
LED MODE FUNCTION
LED1
Flashing
LED1
- Programming Phase (flashing with
ON Energy saving activated by digital input
ON - ALARM signal
- In “Pr2” indicates the parameter is also present in “Pr1”
Installing and Operating Instructions
)
5.2 TO SEE AND CHANGE THE SETPOINTS
1. Push and release the SET key the St1 label will be displayed
3. To change the Set value push the o or n arrows within 10s.
4. To confirm the new value and pass to the next SET push the SET key.
5. Repeat the points 2, 3 and 4 to change the next set point.
TO EXIT: Press SET + UP or wait 15s without pressing a key.
2. Push again the SET key to see point value;
5.3 TO ENTER THE PARAMETERS LIST “PR1
To enter the parameter list “Pr1” (user accessible parameters) operate as follows:
1. Push for 3s the SET + DOWN keys (LED1 & 2 start blinking).
2. The controller will display the first parameter present in the Pr1 menu..
5.4 TO ENTER THE PARAMETERS LIST “PR2”
The “Pr2” parameter list contains the configuration parameters. A security code is required to enter it.
1. Enter the “Pr1” level, see above paragraph.
2. Select “Pr2” parameter and press the “SET” key.
3. The “PAS” flashing message is displayed, shortly followed by “0 - -” with a flashing zero.
4. Use o or n to input the security code in the flashing digit; confirm the f igure by pressing
“SET”.
The security code is “321”.
5. If the security code is correct the access to “Pr2” is enabled by pressing “SET” on the last digit.
Another possibility is the following:
After switching ON the instrument, within 30 seconds, push SET and DOWN keys together for 3s:
the Pr2 menu will be entered.
5.5 HOW TO MOVE A PARAMETER FROM THE “PR2” MENU TO “PR1” AND
VICEVERSA.
Each parameter present in “Pr2” MENU can be removed or put into “Pr1”, user level, by pressing
“SET + n”.
In “Pr2” when a parameter is present in “Pr1” the LED
is on.
5.6 HOW TO CHANGE A PARAMETER
To change a parameter value operates as follows:
1. Enter the Programming mode
2. Select the required parameter.
3. Press the “SET” key to display its value.
4. Use “UP” or “DOWN” to change its value.
5. Press “SET” to store the new value and move to the following parameter.
TO EXIT: Press SET + UP or wait 15s without pressing a key.
NOTE: the set value is stored even when the procedure is exited by waiting the time-out to expire.
5.7 HOW TO LOCK THE KEYBOARD
1. Keep pressed for more than 3 s the o and n keys.
2. The “POF” message will be displayed and the keyboard will be locked. At this point it will be
possible only to see the set point or the MAX o Min temperature stored
3. If a key is pressed more than 3s the “POF” message will be displayed.
5.8 HOW TO UNLOCK THE KEYBOARD
Keep pressed together for more than 3s the o and n keys, till the “Pon” message will be
displayed.
5.9 ON/OFF FUNCTION
TO SWITCH THE INSTRUMENT ON/OFF: If the function is enabled (par. onF=yES), by pressing
the SET key for more than 4s the controller is swit ched OFF. To switch the instrument on again
press the SET key.
6. PROBES AND MEASURING RANGE
Probe Down Scale Full Scale
NTC -40°C/-40°F 110°C / 230 °F
PTC -50°C / -58°F 150°C / 302°F
Pt100 -200°C / -328°F 600°C / 1112°F
TcK 0°C / 32°F 1300°C / 1999°F
TcJ 0°C / 32°F 600°C / 1112°F
TcS 0°C / 32°F 1400°C / 1999°F
1592002250
7. LIST OF PARAMETERS
Hy1 Intervention differential for set point1 (-Full Sc. / Full Sc.). It can be set with positive value or
with negative value. The kind of action depends on the S1C parameter: dir = direct or in =
inverse.
Hy2 Intervention differential for set point2: (-Full Sc. / Full Sc.). It can be set with positive value
or with negative value. The kind of action depends on the S2C parameter: dir = direct or in =
inverse.
Hy3 Intervention differential for set point3: (-Full Sc. / Full Sc.). It can be set with positive value
or with negative value. The kind of action depends on the S3C parameter: dir = direct or in =
inverse.
Hy4 Intervention differential for set point4 (only fo r XT160D): (-Full Sc. / Full Sc.). It can be set
with positive value or with negative value. The kind of action depends on the S4C parameter:
dir = direct or in = inverse.
LS1 Minimum set point1: (Down Sc.÷ Set1) Sets the minimum acceptable value for the set point1.
LS2 Minimum set point2: (Down Sc.÷ Set2) Sets the minimum acceptable value for the set point2.
LS3 Minimum set point3: (Down Sc.÷ Set3) Sets the minimum acceptable value for the set point3.
LS4 Minimum set point4 (only for XT160D): (Down Sc.÷ Set4) Sets the minimum acceptable value
for the set point4.
US1 Maximum set point1: (Set1÷ Full Sc.) Sets the maximum acceptable value for set point1.
US2 Maximum set point2: (Set2÷ Full Sc.) Sets the maximum acceptable value for set point2.
US3 Maximum set point3: (Set3÷ Full Sc.) Sets the maximum acceptable value for set point3.
US4 Maximum set point4 (only for XT160D): (Set4÷ Full Sc.) Sets the maximum acceptable value
for set point4.
ouC Output connections (diP=dependent; ind=independent) select if SET2, SET3 and SET4
(only for XT160D) is independent from SET1 or if the SET2 and other sets depend on SET1 (so
Set2= SET1+SET2 etc).
S1C Action type output 1: S1C=in inverse action (heating/ humidifying /increase pressure);
S1C=dir direct action (cooling / dehumidifying /decrease pressure).
S2C Action type output 2: S2C=in inverse action (heating/ humidifying /increase pressure);
S2C=dir direct action (cooling / dehumidifying /decrease pressure).
S3C Action type output 3: S3C=in inverse action (heating/ humidifying /increase pressure);
S3C=dir direct action (cooling / dehumidifying /decrease pressure).
S4C Action type output 4 (only for XT160D): S4C=in inverse action (heating/ humidifying
/increase pressure); S4C=dir direct action (cooling / dehumidifying /decrease pressure).
AC Anti-short cycle delay: (0÷250 sec) Minimum time between the switching off and the following
switching on
on Minimum time a stage stays switched ON (0÷250 sec)
ono: Minimum time between 2 following switching ON of the same load (0÷120 min).
ALC Alarms configuration: it determines if alarms are relative to set point1 or referred to absolute
values.
rE relative to set point1; Ab absolute temperature
ALL Minimum alarm:
with ALC=rE: relative to set point1, (0÷|Down Sc.-Set1|) this value is subtracted from the set
point1. The alarm signal is enabled when the temperature goes below the “SET1-ALL” value.
with ALC=Ab absolute temperature, (Down Scale ÷ ALu) minimum alarm is enabled when the
temperature goes below the “ALL” value.
ALU Maximum alarm:
with ALC=rE: alarm relative to set point1, (0÷|Full Sc.-Set1|) Maximum alarm is enabled when
the temperature exceeds the “SET1+ALU” value.
with ALC=Ab: absolute alarm, (ALL÷Full Sc.) Maximum alarm is enabled when the
temperature exceeds the “ALU” value.
ALH Temperature alarm for alarm recovery: (0,1÷Full scale) Differential for alarm reset, always
positive.
ALd Alarm delay:(0÷999 min) time interval between the detection of an alarm condition and alarm
signalling.
dAo Delay of alarm at start-up: (0÷23.5h) time interval between the detection of t he alarm condition
after instrument power on and alarm signalling.
tbA Status of alarm relay after pushing a key. (XT151D only): oFF = relay disabled; on = relay
enabled.
AS Alarm relay configuration (XT151D only): cL = 5-6 terminals open with alarm; oP = 5-6
terminals closed with alarm.
So1 Output 1 status with faulty probe: So1=oFF open; So1=on closed.
So2 Output 2 status with faulty probe: So2=oFF open; So2=on closed.
So3 Output 3 status with faulty probe: So3=oFF open; So3=on closed.
So4 Output 4 status with faulty prob e (o n ly for XT160D): So4=oFF open; So4=on closed.
LCI Start of scale, only with current or voltage input: (with rES = in, dE, cE: -99.00÷199.00, with
rES=irE -999÷1999) Adjustment of read out corresponding to 4mA or 0V input signal.
UCI End of scale, only with current or voltage input (with rES = in, dE, cE: -99.00÷199.00, with
rES=irE -999÷1999) Adjustment of read out corresponding to 20mA or 1V or 10V input signal.
oPb Probe calibration: (-999÷999) allows to adjust possible offset of the probe.
rES Resolution: select the resolution of the controller.
in= integer (-99÷199);
dEC= 1 decimal point (-99.0÷199.0),
cE = 2 digits after the decimal point (-99.00÷199.00) only for current or voltage input
irE = integer, large scale (–999÷1999) only for current or voltage input
WARNING: if rES is changed from “irE” to another value, all the parameters values expressed
in degrees: SET1, SET2, SET3, SET4 (XT160D), Hy1, Hy2, HY3, HY4 (XT160D), LS1,Ls2,
Ls3, Ls4 (XT160D), uS1, uS2, uS3, uS4 (XT160D), ALL. ALu, ALH, LCi, uCi, LAo, uAo, HES,
have to be checked and set.
NOTE: the decimal point selection is not available on models with thermocouple input.
UdM Measurement unit: it depends on models:
for temperature:°C = Celsius; °F = Fahrenheit.
with 4÷20mA, 0÷1V, 0÷10V input : 0= °C; 1= °F, 2= %RH, 3=bar, 4=PSI, 5=no measurement
unit.
PbC Probe selection: it sets the kind of probe. It depends on models
for temperature NTC/PTC: Ptc = PTC; ntc = ntc.
for temperature standard: Pt= Pt100, J = J thermocouple, c = K thermocouple, S = S
thermocouple; Ptc = PTC; ntc = ntc.
with 4÷20mA, 0÷1V, 0÷10V input : cur=4÷20mA, 0-1= 0÷1V, 10= 0÷10V.
REGULATION
ALARMS
PROBES AND DISPLAY
,
.
1592002250 XT151-160D GB R.1.08.03.2005 XT151D – XT160D 2/4