
1300 Henley Court
Pullman, WA 99163
509.334.6306
www.digilentinc.com
PmodHB5™ Reference Manual
Revised October 19, 2016
This manual applies to the PmodHB5 rev. E
Copyright Digilent, Inc. All rights reserved.
Other product and company names mentioned may be trademarks of their respective owners.
Overview
The Digilent PmodHB5 offers a 2A H-bridge circuit to drive small to medium sized DC motors. This module was
specifically designed to work with the Digilent gearbox motor, which incorporates quadrature encoder feedback.
1 Functional Description
The PmodHB5 utilizes a full H-Bridge circuit to allow users to drive DC motors from the system board. Two sensor
feedback pins are incorporated into the motor connection header and are specifically designed to work with
the Digilent motor/gearbox.
2 Interfacing with the Pmod
The PmodHB5 communicates with the host board via the GPIO protocol. Like all H-Bridges, care must be taken to
avoid causing a potential short within the circuitry. In terms of this Pmod, this means that the Direction pin must
not change state while the Enable pin is at a high voltage state. If this does occur, one set of switches that are
driving the motor will be closing while the other set is opening, allowing for the possibility for both sets of switches
to be open at the same time, creating a short.
2A H-bridge circuit
Drive a DC motor with operating voltage up
to 12V
6-pin JST connector for direct connection to
Digilent motor/gearboxes
Two screw terminals for external motor
power supply
Small PCB size for flexible designs 1.2 in ×
0.8 in (3.0 cm × 2.0 cm)
6-pin Pmod port with GPIO interface
Follows Digilent Pmod Interface
Specification Type 5
Libraries and example code available
in resource center
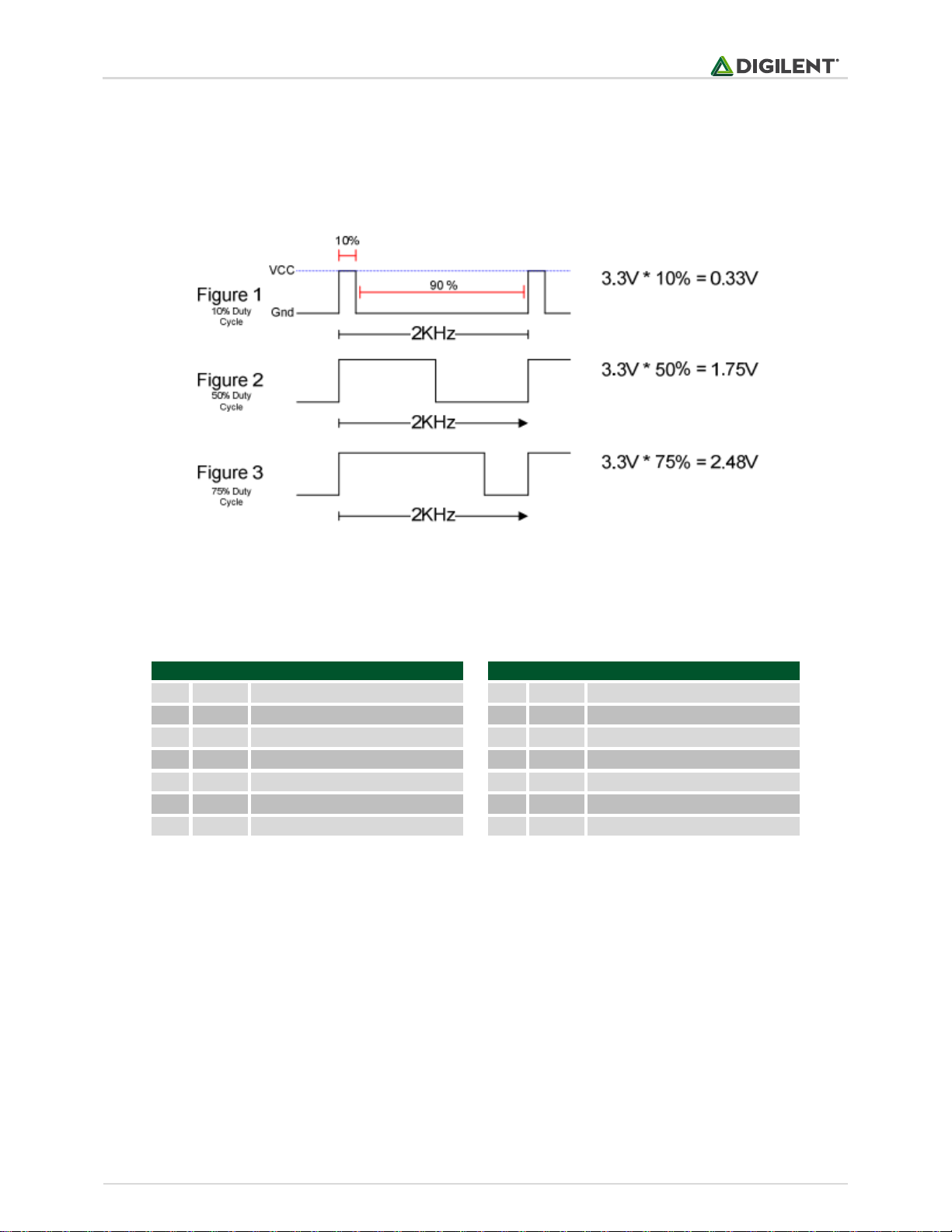
PmodHB5™ Reference Manual
Copyright Digilent, Inc. All rights reserved.
Other product and company names mentioned may be trademarks of their respective owners.
To drive the motor at a specific speed, users will need to choose a static direction (provide a low voltage to the
Direction pin to rotate the shaft in a clockwise direction or provide a high voltage on the Direction pin to rotate the
shaft in a counter-clockwise direction) on the Direction pin, and then perform pulse width modulation on the
Enable pin. The more often that an Enable pin is driven high within a set time frame, the faster the DC motor will
spin.
The way that this works is that when voltage is being applied, the motor is driven by the changing magnetic forces.
When voltage is stopped, momentum causes the motor to continue spinning a while. At a high enough frequency,
this process of powering and coasting enables the motor to achieve a smooth rotation that can easily be controlled
through digital logic.
Header J1 (pin 1 on the top)
Header J2 (pin 1 on the bottom)
Positive Power Supply (3.3/5V)
Positive Power Supply (3.3/5V)
Table 1. Pinout description table.

PmodHB5™ Reference Manual
Copyright Digilent, Inc. All rights reserved.
Other product and company names mentioned may be trademarks of their respective owners.
Any external power applied to the PmodHB5 must be within 2.7V and 5.25V; however, it is recommended that
Pmod is operated at 3.3V.
3 Physical Dimensions
The pins on the pin header are spaced 100 mil apart. The PCB is 1.2 inches long on the sides parallel to the pins on
the pin header and 0.8 inches long on the sides perpendicular to the pin header.