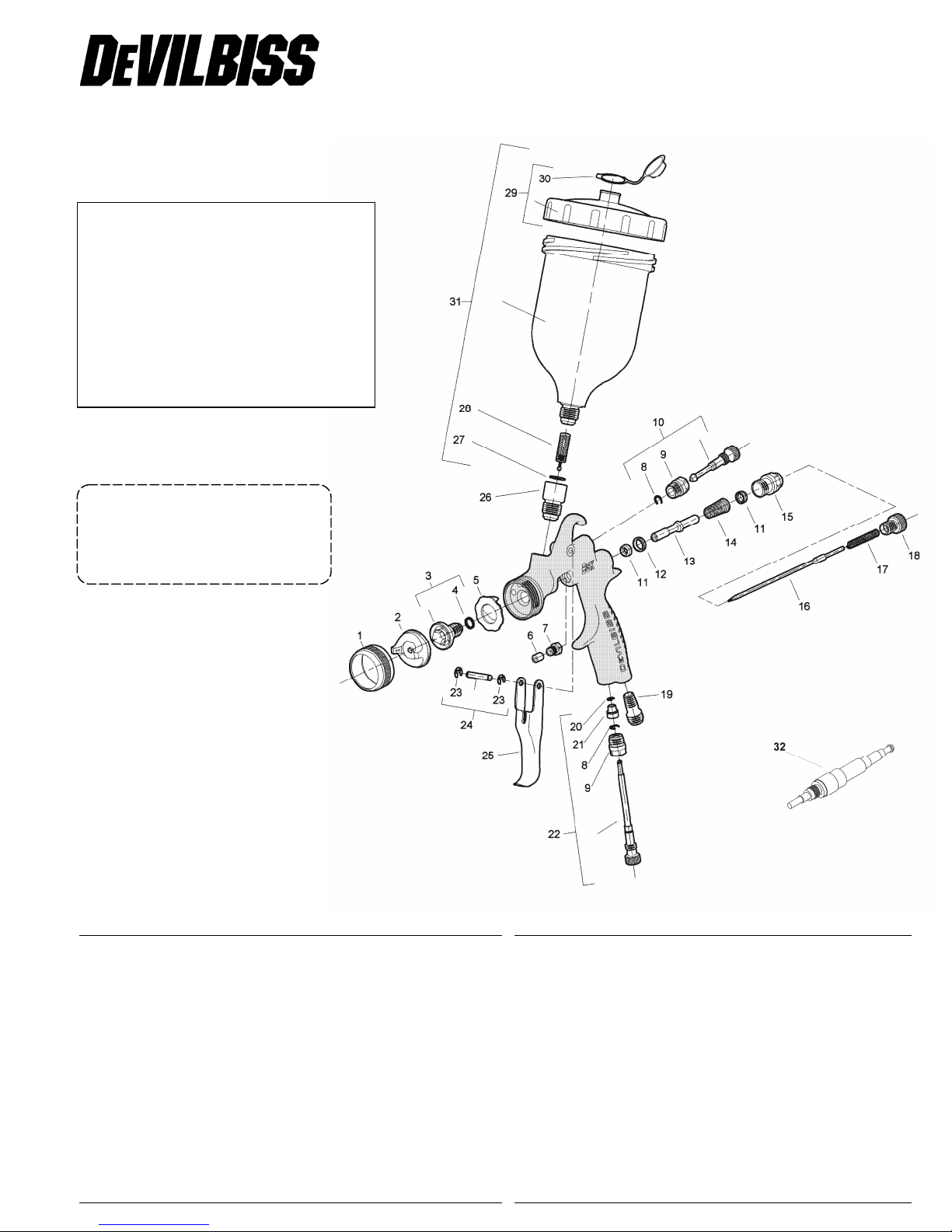
Service Instructions
BYC-069-A
HVLP Transtec
gravity feed spray gun
Model SGK - 600 - PR
Specifications:
• Pressure at spray gun inlet: up to 32 psi
• Paint flow rate: 270 ml/min
• Air consumption: 9,8 cfm
• Pattern size: 10" at 7" distance
ote: Figure obtained with metallic polyester base at
24 seconds viscosity #4 Ford cup.
Benefits:
• Less overspray
• Paint savings
• Cost reduction
Respect your work and protect
your equipment:
USE DEVILBISS ORIGINAL
SPARE PARTS.
Replacement kits
K-5026: Seal replacement kit, items 11(2x) and 12.
{
K-5027: Air valve replacement kit, items 11(2x), 12, 13 and 14.
K-5028-20: Tip, needle and gasket replacement kit, items 3, 4, 6, 16 and 17.
K-5029: Items 4, 11(2x), 12 and 32 replacement kit.
∇
K-5030: Baffle replacement kit, items 4 and 5.
Ref. Part N.° Description Ref. Part N.° Description
1 SGK-0023 Retaining ring
2 BSK-0158-510 Air cap 18 SGK-0035 Fluid adjustment knob
- Fluid tip 19 PTGA-0029 Nipple
3
∇ 4
{∇11
{∇12
- Gasket 20 BSS-240104 Retaining ring
- Baffle 21 SGK-0041 Air adjusting valve head
5
SGK-0037 Packing 22 SGK-0502 Air adjusting valve assembly
6
7 SGK-0036 Packing gland nut 23 BSS-240106 Retaining ring
8 SST-8416 Retaining ring 24 K-5025 Trigger pin assembly
9 SGK-0500 Spray pattern adjustment valve bushing 25 SGK-0020 Trigger
10 SGK-0501 Spray pattern valve 26 SGK-0021 Fluid nipple
- U-cup seal 27 KGP-0012 Gasket
- Air valve seat 28 KGP-0005 Filter
{13 - Air valve stem 29 GFC-0402 Lid assembly
{14 SGK-0032 Air valve spring 30 GFC-0002 Drip free vent lid
15 SGK-0034 Air valve bushing 31 GFC-0501 Cup assembly
- Fluid needle
16
17
∇ 32
SGK-0400 Fluid needle spring
- Assembly tool
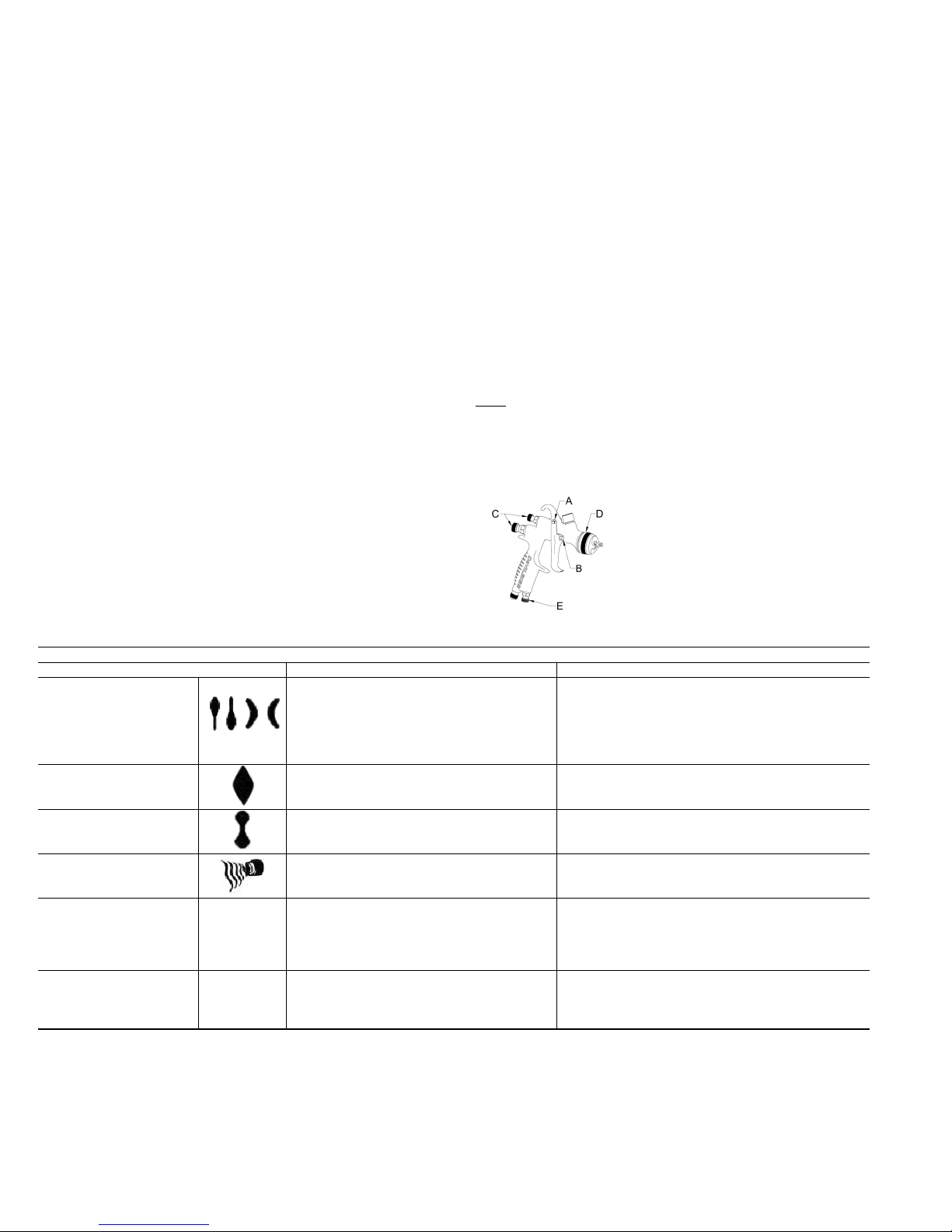
Service Instructions
BYC-069-A
Description
The SGK-600PR spray gun has Transtec HVLP technology and is gravity fed.
It is a high production spray gun, ideal for spraying finishing materials, with
exception of corrosive and abrasive ones. It renders paint economy, less
overspray and ,consequently, reduces costs.
Installation
Connect the spray gun to a clean air source, free of humidity and oil, by using
at least a 5/16” internal diameter hose. Depending on the length of the hose, a
bigger internal diameter may be necessary. Press the spray gun trigger and
adjust the inlet air pressure at the handle of the gun to approximately 25 psi.
Operation
Prepare the material to be sprayed according to the manufacturer’s
instructions. Filter the material through a 100 mesh screen.
Regulate the air pressure at the DeVilbiss filter regulator
Make a spray test.
Regulate the spray pattern by opening or closing the spray pattern valve
knob (10)
Spray a small area to adjust the work speed and desired finishing. If
finishing is too dry or rough, the amount of material is too small in relation
to the air pressure. Turn the fluid adjustment knob (18) counter clockwise,
or decrease the air pressure at the filter regulator.
Keep the spray gun always perpendicular to the surface being painted.
Do not move your hand in an arch. The arch movement produces a non-
uniform paint layer.
We recommend the spray gun be kept at a distance of 6 to 8 inches from
the surface.
The position of the air cap determines the position of the pattern. Turn the
air cap according to requirements.
Maintenance and Cleaning
We recommend cleaning be done after using equipment:
1. Disconnect the spray gun from the air line.
2. Clean the cup and put clean solvent in same.
3. Open totally the fluid adjustment knob, press the trigger and let the solvent
flow through the fluid passage until it comes out completely clean.
4. Clean the gun body with a cloth wet with solvent, avoid waste of cotton
5. Remove the air cap and wash it in solvent using a brush or soft bristle
brush. Then dry it with an air jet.
6. If necessary, clean the air cap hole with a bristle or toothpick. NEVER
USE steel wire or hard instrument for this may damage the hole causing a
distorted spray pattern.
7. To avoid damaging the needle, make sure to pull the trigger and keep it
pulled while you are tightening or releasing the fluid tip, or remove the
fluid adjustment knob (18) to release the spring pressure.
8. Only remove the fluid tip when changing same or when there is internal
clogging.
For routine cleaning it is not necessary to remove the cup.
9.
10. The recommended tightening of the tip is 150-180 lbf/inch.
Note: To replace both U-cup seal (11) and air valve seat (12) see the procedure
described in Service Instructions of the K-5029 kit.
Lubrication
For best results, oil the indicated points daily
We recommend the use of the SSL-10 DeVilbiss oil.
A. Trigger areas
B. Needle gasket
C. Adjustment valves
D. Retaining ring
E. Air valve
Defect Causes Correcting
Service Check
Heavier spray on top or
below.
Defective configuration in
curve shape.
a. Material buildup at air cap. a. Remove air cap and wash it with solvent.
b. Partial obstruction of air cap horn holes or
central holes.
c. Material buildup at the fluid tip or partial
b. Remove air cap and wash it with solvent (see
maintenance and cleaning).
c. Remove the tip and wash it with solvent.
obstruction of same.
d. Damaged fluid tip. d. Replace the tip and needle assembly.
a. Excess material. a. Reduce the material flow by closing the fluid
Heavy spray in the center
adjustment knob.
b. Very thick material. b. Dilute the material.
a. Air pressure too high. a. Reduce air pressure at DeVilbiss filter regulator.
Split spray.
b. Lack of material. b. Increase material flow opening fluid.
a. Lack of material. a. Refill paint recipient.
Jerky or fluttering spray.
b. Obstructed fluid passage. b. Clean fluid passage.
c. False entrance of air in paint line. c. Check paint line.
a. Low air pressure at spray gun. a. Check air line or increase pressure.
b. Fluid regulating knob closed. b. Open fluid adjustment knob (see Operation).
Will not spray.
c. Material is too thick. c. Dilute material.
d. Air cap is loose. d. Tighten air cap.
e. Material buildup in between tip and air cap. e. Clean tip externally and the central air cap hole.
a. Fluid tip or needle worn or damaged. a. Change the tip and needle assembly (see item 7 in
Dripping or material leakage
through the tip.
b. Gasket holding the needle. b. Lubricate the gasket (item 6) when new, or change it,
Maintenance and Cleaning).
lubricate and adjust.
With 14 psi at spray gun inlet air cap pressure is 10 psi.
DeVilbiss maintains the right to modify the characteristics of its products without previous notice.
Warranty
DeVilbiss equipment has a six month warranty from the date of purchase. This warranty will be limited to material, manufacturing and workmanship defects; bad use or repairs effected by non authorized people imply
in automatic loss of the warranty;
When repairs are necessary, take your equipment to a DeVilbiss Authorized Distributor where the repair will be effected by specialized technical people and only charged if equipment it outside warranty.