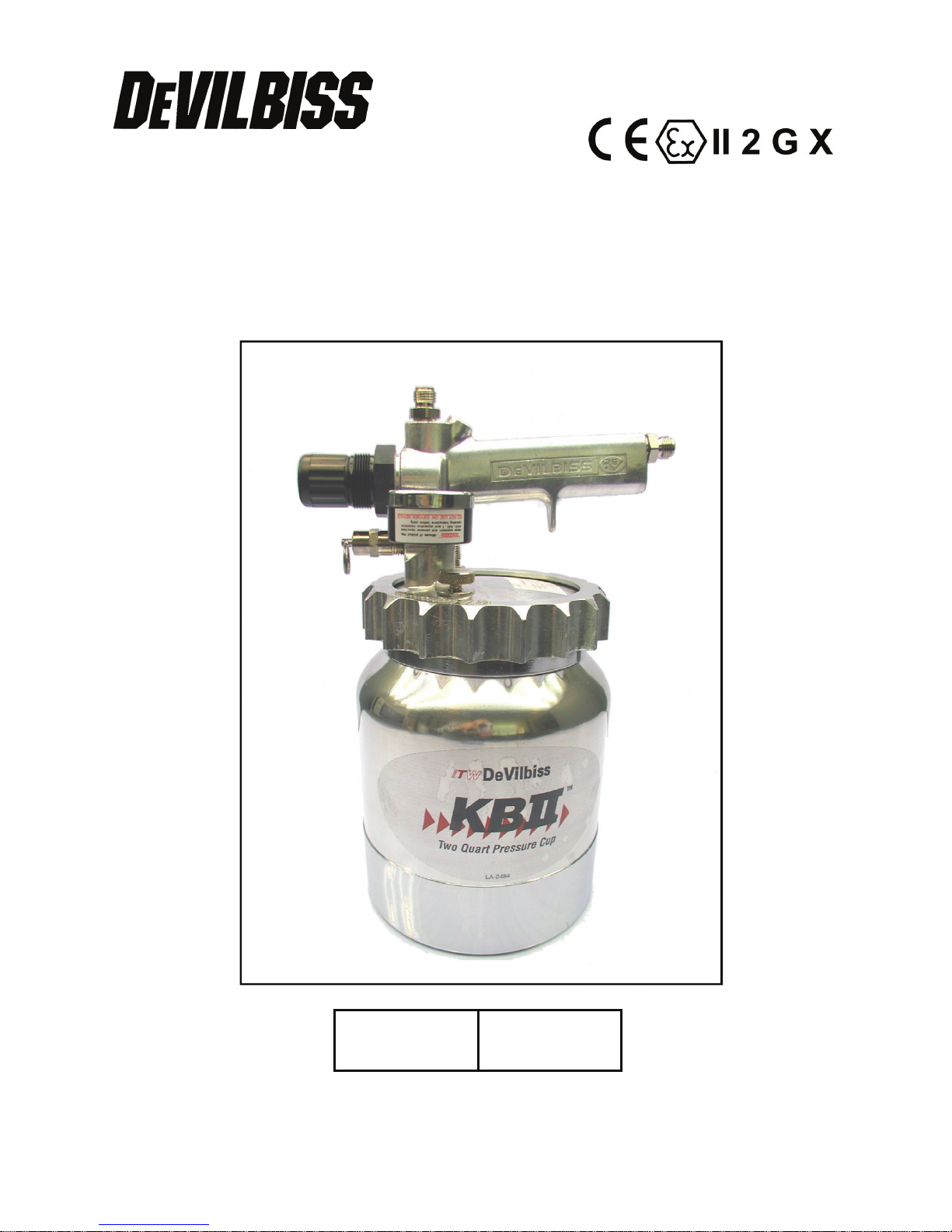
SB-E-4-205
Operation Manual:
KB-522 & KB-522-SS
Pressure Feed Cup
ISS.02
E
E
P 1 - 12
© 2010 ITW Finishing Systems and Products
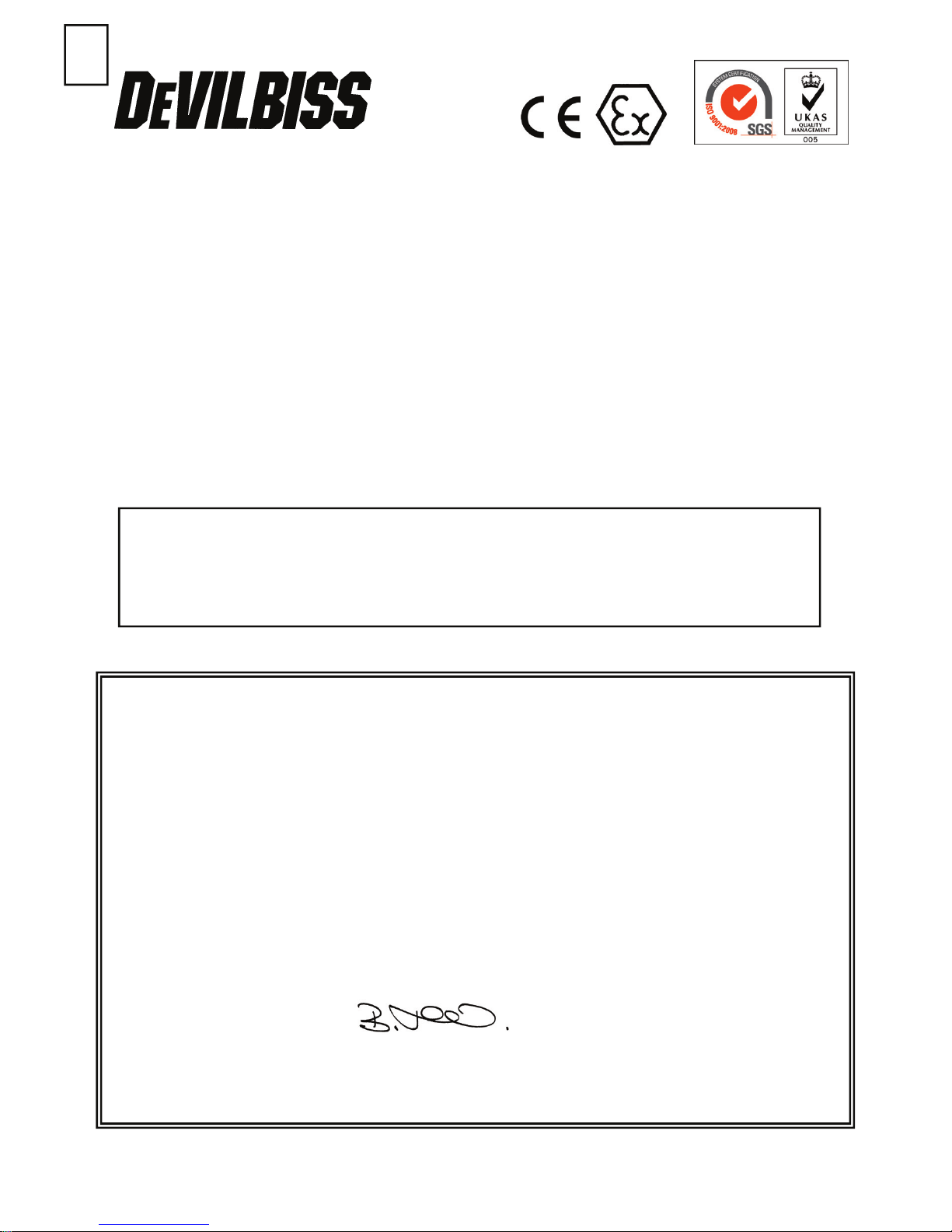
EE
Operation Manual:
KB-522 & KB-522-SS Pressure Feed Cups
Important: Read and follow all instructions and SAFETY PRECAUTIONS
before using this equipment.
The KB-522 pressure feed cup incorporates an air regulator, safety valve, pressure relief
valve, pressure gauge and a carrying handle. An additional bail handle is also supplied to
enable the user to suspend the cup from a belt or other device. Hose assemblies to
connect the spray gun to the cup are not included and should be ordered separately, see
‘Accessories’.
Corrosion resistant version also available with Stainless Steel Cup and plated Lid.
Order No.
KB-522 STD CUP
KB-522-SS STAINLESS STEEL CUP
EC Declaration of Conformity
We: ITW Finishing UK, Ringwood Rd, Bournemouth, Dorset, BH11 9LH, UK, as the
manufacturer of the
Pressure Cup models KB-522 & KB-522-SS
declare, under our sole responsibility, that the equipment to which this document relates
is in conformity with the following standards or other normative documents:
EN 13463-1:2001; and thereby conform to the protection requirements of Council
Directive 94/9/EC relating to Equipment and Protective Systems intended for use in
Potentially Explosive Atmospheres protection level II 2 G X, suitable for use in ZONE
1 hazardous areas.
© 2010 ITW Finishing Systems and Products
B. Holt, General Manager
9th February 2004
2
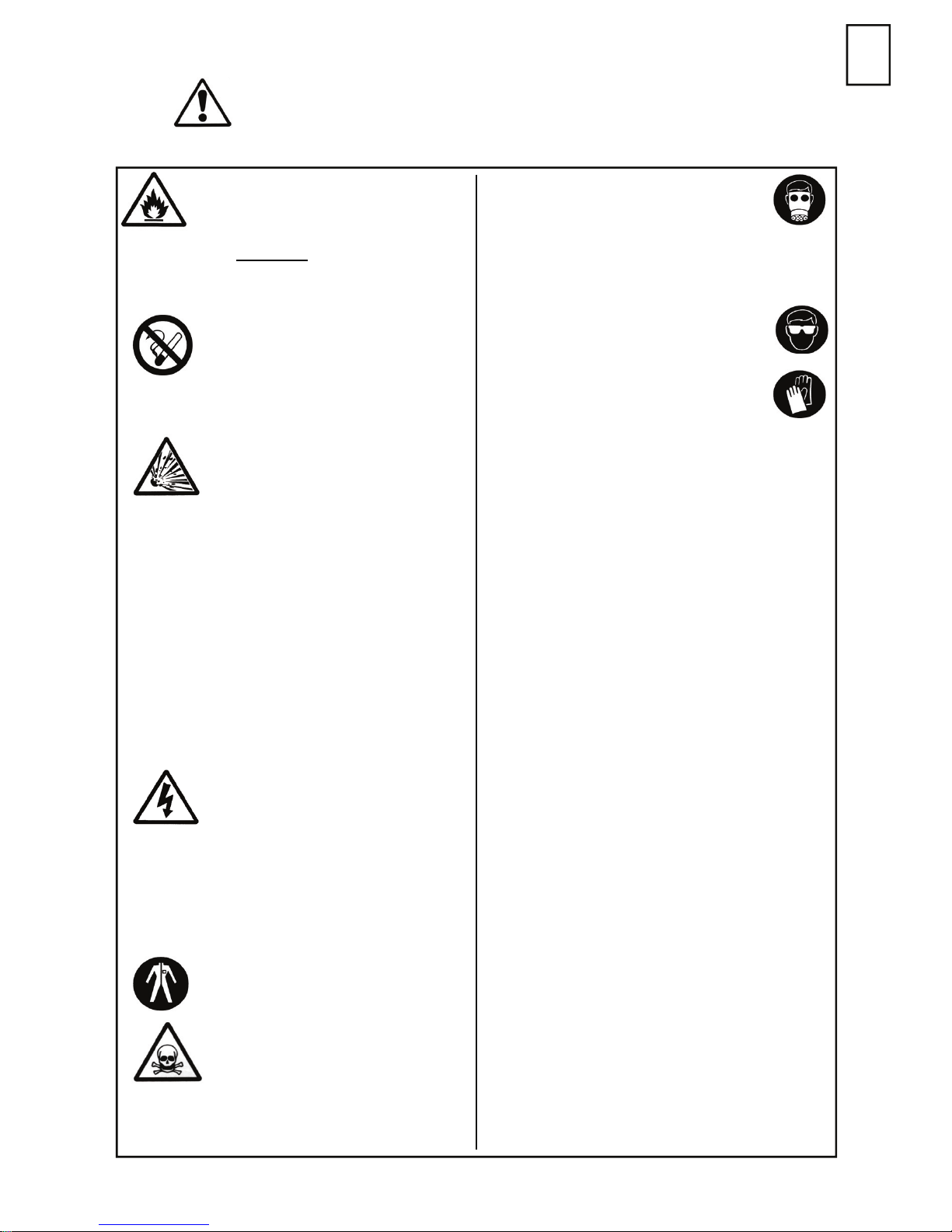
SAFETY WARNINGS
EE
Fire and explosion
Solvents and coating materials can
be highly flammable or combustible
when sprayed. ALWAYS
material suppliers instructions and COSHH
sheets before using this equipment
Users must comply with all local
and national codes of practice and
insurance company requirements
governing ventilation, fire
precautions, operation and house-keeping of
working areas
FOR KB-522 ONLY:
Do not use Solvents or coating
materials containing
HALOGENATED HYDROCARBONS with this
equipment.
FOR KB-522-SS ONLY:
This equipment, as supplied, is suitable for
use with Halogenated Hydrocarbons and the
user must ensure that all other equipment in
the system is also suitable for use with these
materials. DO NOT SPRAY MATERIALS
CONTAINING THESE SOLVENTS EXCEPT
WITH EQUIPMENT SPECIFICALLY
DESIGNATED BY THE MANUFACTURER
AS BEING SUITABLE FOR SUCH USE.
Static Electricity can be generated
by fluid and/or air passing through
hoses, by the spraying process
and by cleaning non- conductive
parts with cloths. To prevent ignition sources
from static discharges, earth continuity must
be maintained to the spraygun and other
metallic equipment used. It is essential to use
conductive air and/or fluid hoses.
refer to the coating
Personal Protective
Equipment
Toxic vapours – When sprayed,
certain materials may be
poisonous, create irritation or be
otherwise harmful to health.
Always read all labels and safety
data sheets for the material before
spraying and follow any recommendations. If
In Doubt, Contact Your Material Supplier
The use of respiratory protective
equipment is recommended at all
times. The type of equipment must be
compatible with the material being sprayed.
Always wear eye protection when
spraying or cleaning the spraygun
Gloves must be worn when spraying
or cleaning the equipment
Training
Personnel should be given adequate training
in the safe use of spraying equipment.
Misuse
Never aim a spraygun at any part of the
body. Never exceed the max. recommended
safe working pressure for the equipment.
The fitting of non-recommended or non-
original spares may create hazards.
Before cleaning or maintenance, all
pressure must be isolated and relieved from
the equipment.
Never exceed the recommended safe
working pressures for any of the equipment
used.
Never drill into or modify the pressure feed
cup in any way.
Do not adjust, remove or tamper with the
safety valve. If a replacement is necessary,
only use DeVilbiss supplied spare Valves.
The materials used in the construction of the
cup are (bearing in mind the warning on
Halogenated Hydrocarbons) solvent
resistant enabling the cup to be cleaned
using gun washing machines. However, the
lid assembly must not be cleaned in a gun
washing machine as it contains parts that
will be damaged.
3
© 2010 ITW Finishing Systems and Products
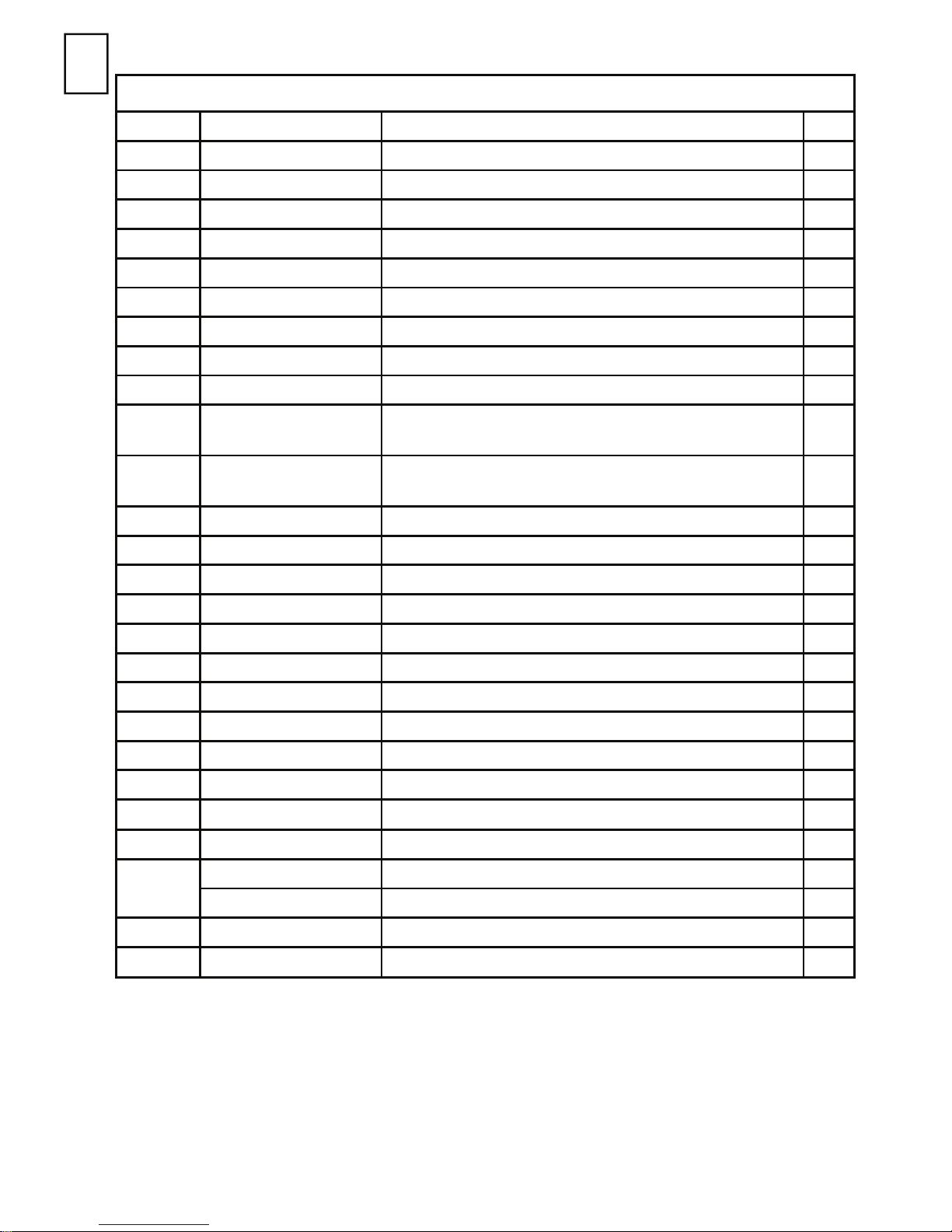
EE
Parts List
Ref. Order No. Description Qty.
1 KB-64 Retaining Ring 1
2 KB-81-K5 Slip Rings 1
3 KB-74 Handle 1
4 SS-656-CD CD Nut 1
5 JGA-158 Connector 1/4" BSP 2
6 KB-66 Pressure Relief Valve 1
7 - Lid 1
8 GA-355 Gauge 1
9 KB-80-K5 Seal 1
10 MBD-11-K5
KB-97-K2
11 KB-422
KB-442
12 KB-432-K3 Check Valve kit of 3 1
13 KB-85-K5 Seal kit of 5 1
14 TIA-4355 Safety Valve 1
15 KB-428-1 Regulator Assembly 1
*16
*17
*18
*19
*20
21 - Spring 1
*22
23 KB-60-K6 Seal kit of 6 1
- Spring 1
- Valve 1
- Valve Seat and Seal
- Diaphragm 1
- Slip Ring 1
- Bonnet 1
Locknut (KB-522) kit of 5
Locknut -Stainless Steel (KB-522-SS) kit of 2
Cup – Aluminium (KB-522)
Cup – Stainless Steel (KB-522-SS)
1
1
1
24
KK-4997 Tube Assembly (KB-522) 1
KK-4996 Tube Assembly (KB-522-SS) 1
25 KB-444 Check Valve and Seal Assembly 1
26 KB-101-K5 Seal kit of 5 1
Note: Ref No.s marked * are supplied in repair kit Order No. KK-4887-2.
© 2010 ITW Finishing Systems and Products
4