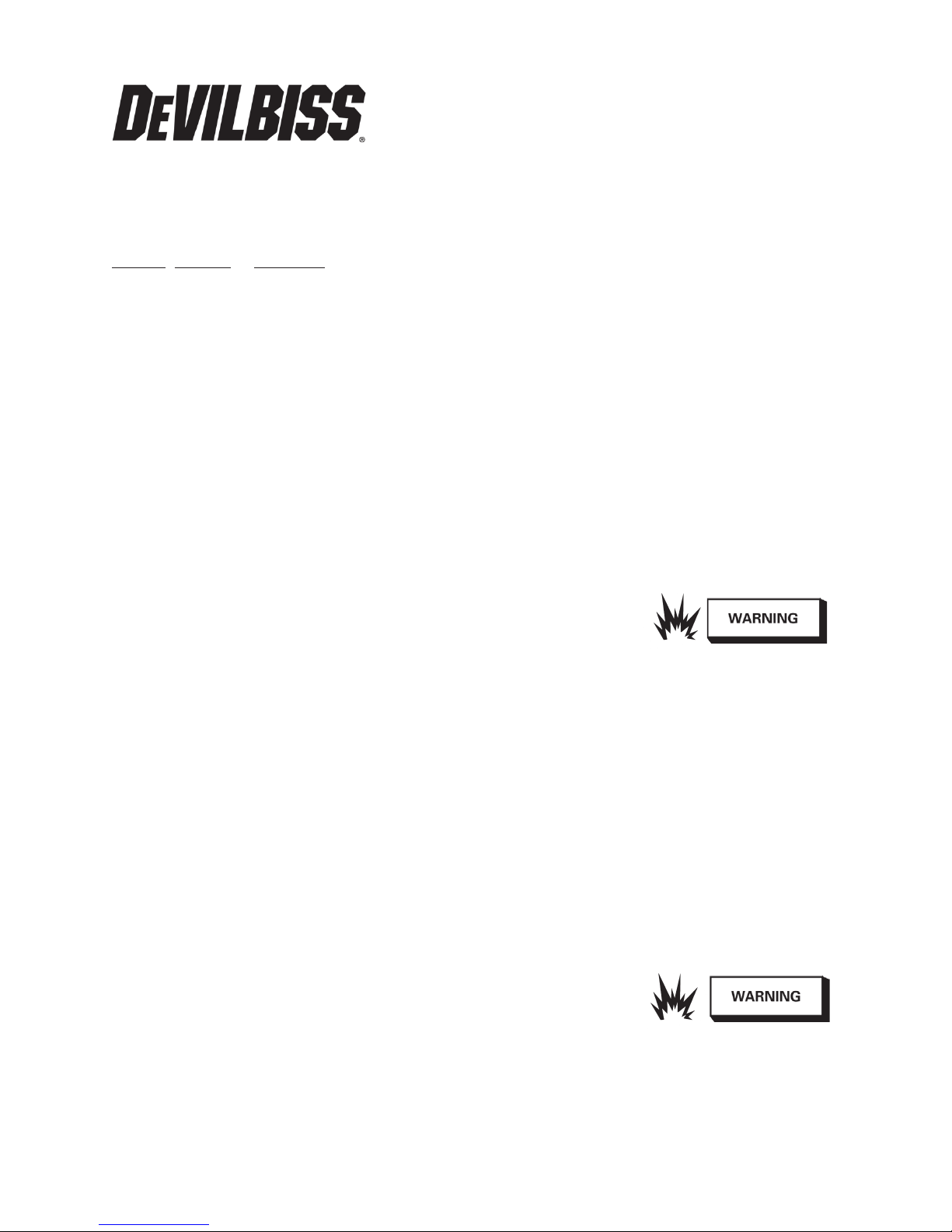
SERVICE BULLETIN
SB-6-159-H
Replaces SB-6-159-G
DAD-503 (130089) AIR STATION WITH DESICCANT
IMPORTANT: Read and follow all INSTRUC-
TIONS and SAFETY PRECAUTIONS before
installing, operating or maintaining this
equipment. Keep this manual for future
reference.
DESCRIPTION
The DAD-503 is designed to be a point
of use system. It is capable of removing
dirt, water, oil and water vapor hydrocarbons and odors from compresssed air. It
consists of a filter separator, coalescing
filter, charcoal filter, flow thru regulator,
desiccant dryer, air regulator, and main
air supply shut off valve.
A clean filtered supply of air must be
provided for use with a supplied air
respirator. In addition, air for spray
operations passes through the desiccant
filled tank that removes any remaining water vapor to a -40° F Dew Point,
providing the ultimate air supply for spray
finish applications.
SPECIFICATIONS
Air Filter (Separator):
Air Inlet 1/2" NPT(F)
Air Outlet 1/2" NPT(F)
Air Flow Capacity 100 CFM
Maximum Operating Press. 150 PSIG (10.3 Bar)
Maximum Temperature 150° F (65.6°C)
Automatic Mechanical Drain Supplied
Filter 5 micron
Coalescing Filter:
Air Inlet 1/2" NPT(F)
Air Outlet 1/2" NPT(F)
Air Flow Capacity 55 CFM
Maximum Operating Press. 150 PSIG (10.3 Bar)
Maximum Temperature 150° F (65.6°C)
Automatic Mechanical Drain Standard
Pressure Differential Ind. Standard
Filter 0.01 Micron
Charcoal Filter:
Air Inlet 1/2" NPT(F)
Air Outlet 1/2" NPT(F)
Air Flow Capacity 75 CFM
Maximum Operating Pressure 150 PSIG (10.3 Bar)
Maximum Temperature 150° F (65.6°C)
Manual Mechanical Drain Standard
Pressure Differential Indicator Standard
Aerosol Filter .003 ppm./wt.
Particulate Filter 3.0 micron
Flow Thru Regulator:
Flow Thru Ports 1/2" NPT(F)
Regulated Ports 1/4" NPT(F)
Air Flow Capacity(regulated) 28 CFM @ 60 PSI
with 100 PSI Inlet
Maximum Inlet Pressure 300 PSIG
Regulated Pressure 0-125 PSIG
Maximum Temperature 175° F (79.4°C)
Desiccant Dryer:
Air Inlet 1/2" NPT(F)
Air Outlet 1/2" NPT(F)
Air Flow Capacity 25 CFM
Maximum Operating Pressure 150 PSIG (10.3 Bar)
Maximum Temperature 150° F (65.6°C)
Humidity Indicator Standard
Water Vapor Removal -40° F Dew Point
Tool Air Regulator:
Air Inlet 3/8" NPT(F)
Air Outlet 1/4" NPT(F) (3 ea.)
Air Flow 60 CFM
Maximum Operating Pressure 150 PSIG (10.3 Bar)
Maximum Temperature 120° F (48.9°C)
VA-595 Main Air Supply Shut Off Valve:
Air Inlet and Air Outlet 1/2" NPT(M)
Maximum Operating Pressure 175 PSIG (12.0 Bar)
BREATHING AIR REQUIREMENTS
Supplied breathing air, as defined by
OSHA 29 CFR 1910.134i and NIOSH 42 CFR
84.141, MUST meet or exceed the following
requirements for Type 1-Grade D breathable air, as defined in Compressed Gas
Association (CGA-G7-1-1997):
Oxygen = 19.5-23.5% (Typical
atmospheric levels)
Oil (condensed) = 5 mg/m (milligrams per cubic meter) maximum
Carbon Monoxide (CO) = 10 ppm
(parts per million) max.
Carbon Dioxide (CO2) = 1OOO ppm
(parts per million) max. (Typical
atmospheric levels)
Odor = The presence of a pronounced odor should render the
air as unsatisfactory
It is up to the employer to assure that the
air compressor is properly maintained,
that the air compressor intake is located
in a clean contaminate free location
and that the air compressor is drawing
in typical atmospheric air, meeting all of
the national and local requirements for
breathing air.
This filter unit does not remove or filter
Carbon Monoxide (CO). It is up to the
employer to ensure that the level of CO
does not exceed the maximum national
or local allowed level. The recommended
method to assure that the CO level is not
exceeded is to install a carbon monoxide
monitor and alarm.
This filter unit will only remove particulate
matter, water, oil and odor. This filter unit
will meet the particulate matter, oil and
odor requirements of Type 1-Grade D
Breathable Air and Compressed Breathing
Air, CSA-Z180.1 when:
• The lter unit is connected to a
compressed air source:
The compressor is properly
maintained
The air compressor intake is
located in a clean contaminate
free location
The air compressor is draw-
ing in typical atmospheric air,
meeting all of the national
and local requirements for
breathing air
• The lters are properly maintained
• A properly operating CO monitor
is installed
Risk of explosion or fire.
Improper use can cause
personal injury.
• This product is designed and
intended for use in industrial compressed air systems only. Do not use
for liquids or gasses other than air.
• Do not use where pressure or temperature can exceed rated operating
conditions (see specifications).
• Regulated outlet pressure must
never be set higher than the
maximum operating pressure of the
downstream air tool or equipment.
An outlet pressure gauge should
always be used.
Risk of illness or death. Carbon
monoxide can cause nausea,
fainting or death. Stop using if carbon monoxide is present. This unit
does not remove carbon monoxide.
A carbon monoxide monitor should
be incorporated into your air supply line to warn of the presence of
carbon monoxide.
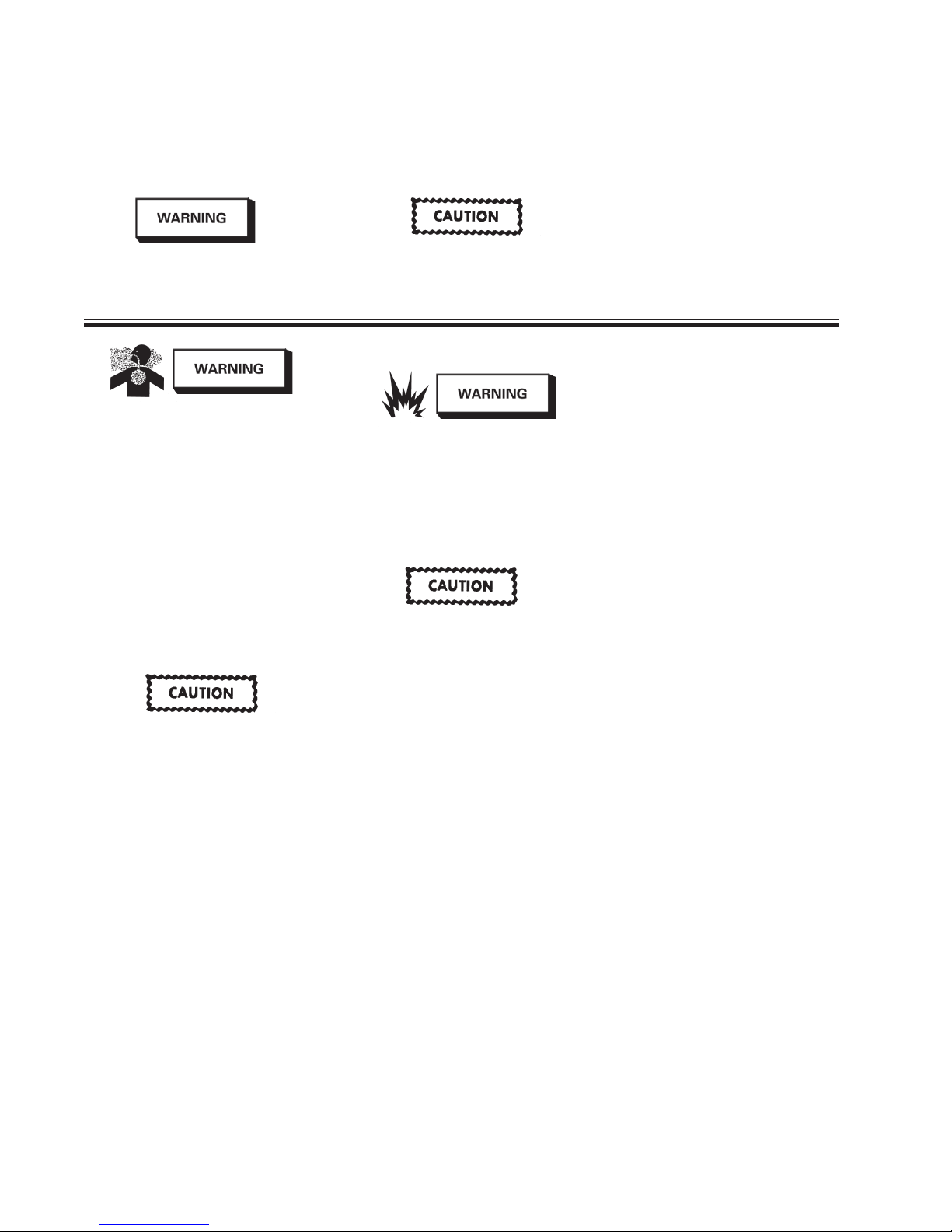
Page 2 SB-6-159-H
SAFETY PRECAUTIONS
This manual contains important information that all users must know and understand before using the equipment. This
information relates to USER SAFETY and PREVENTING EQUIPMENT PROBLEMS.
To help you recognize this information, we use the following terms to draw your attention to certain equipment labels and
portions of this manual. Please pay special attention to any label or information that is highlighted by one of these terms:
Note
Important information to alert you to a
situation that might cause serious injury
if instructions are not followed.
Risk of injury. Do not place unit in
service without metal bowl guard
installed. Filter units are sold only
with metal bowl guards. To minimize
the danger of flying fragments in the
event of plastic bowl failure, guard
must not be removed. If the unit is
in service without the metal bowl
guard installed, manufacturer’s warranties are void and the manufacturer
assumes no responsibility for any
resulting loss. If unit has been in
service and does not have a metal
bowl guard, order one and install
before placing back in service.
Certain compressor oils, cleaning agents and solvents may
attack the plastic and rubber
components used in the construction of this product. This
product should not be used in
conjunciton with or in the vicinity of these materials. Read and
follow material labels carefully.
Please consult DeVilbiss if in
doubt.
Important information that tells how to
prevent damage to equipment, or how
to avoid a situation that might cause
minor injury.
INSTALLATION - AIR STATION
Risk of explosion and injury.
Release all air pressure from
system before servicing system.
Be sure to read and understand
all Service Bulletins on the
separate components before
using the system. Use only
specified DeVilbiss parts.
Risk of equipment damage!
Do not install your air station
where it is subjected to sudden
depressurization cycles exceeding 20 PSIG. Quick relieving air
solenoid valves, typical in some
spray booths, will eventually
fail pressure gauges and filters.
To minimize sudden depressurization effect, replace the existing solenoid with a
"slow closing solenoid valve". (One source:
Automatic Switch Co). Or, install an air
adjusting valve at the existing solenoid
valve outlet.
For ease of installation and maintenance,
attach the assembled air station to the main
air line using a pipe union, (not included).
Information that you should pay special
attention to.
1. Be sure to read all "Warnings" and
"Cautions" in this manual and compo nent manuals on the unit before instal lation or using this equipment.
2. Install air station system as close as
possible to the point where the air is
being used. Use enclosed mounting
bracket to support Air Station.
3. Install main air supply shut off valve
upstream of air drying system to
allow maintenance to the unit.
4. Install unit with air flow through filter
in direction of arrow on top of filters.
5. Minimum 3/4" NPT piping is recom mended. Avoid using fittings, cou plings, etc. that restrict air flow.
6. Maximum inlet pressure and operat-
ing temperature is: 150 PSIG and
120° F (48.9 C)
7. Three 6' lengths of vinyl tubing are
shipped loose with the system. Slide
over drains which protrude from bot tom of the filters. Place the other end of
vinyl tubing into appropriate re ceptacle. Prevent vinyl tubing from
becoming kinked which would prevent
free movement of liquids discharged
from the automatic or manual drain.
8. An optional manual drain HAF-11) can
be installed in place of the auto matic drains.

PARTS LIST
Replace Ref.
No. Part No. Description Req.
1 13-0041 Air Filter/Separator 1
2 HAF-505 Coalescing Filter 1
3 HAF-517 Charcoal Filter 1
4 HAR-508 Flow-Thru Regulator 1
5 MPV-424 Breathable Air Quick 1
Release Socket
6 DAD-8 Screen (Not Shown) 2
7 GA-316 Gauge 1
8 PT-417 Desiccant Tank 1
( without desiccant,
Includes Ref. No. 6)
9 DAD-400 Humidity Indicator 1
(1 Humidity Indicator
Paper Included)
10 GA-288 Gauge 1
11 HAR-507 Air Regulator 1
12 VA-542 Ball Valve 1
13 DAD-1
(Not Shown)
(1 Humidity Indicator
Paper Included)
14 DAD-600 Desiccant Tune-Up Kit 1
(Not Shown) Includes
1 ea: DAD-1, DAD-3,
and HAF-6.
15 VA-595 Main Air Supply Shut 1
Off Valve (Not Shown)
OPERATION
After the system is installed and ready
to use;
1. Attach breathable air hose to Q.D.
on flow-thru regulator.
2. Attach air hose(s) to outlet valve.
3. Open main shut-off valve upstream
of system.
4. Attach breathable air hose to sup plied air respirator.
5. Adjust regulator (4) to read 60 PSIG
(flowing air to the visor). The pressure
should never be allowed to drop be low 50 PSI in a flowing condition.
6. Adjust regulator (11) to desired set ting by turning "T" handle in or out.
7. Open ball valve (12) to supply air to
spray gun or tool being used. With air
flowing, readjust air pressure at
regulator if necessary
8. After use, shut off ball valve and
bleed off residual air in hose.
I
ment
Parts
Replacement Desiccant
nd.
1
Figure 2 DAD-503 Air Station
4
1 2 3
MAINTENANCE
Risk of injury. Components
under pressure. Relieve air
pressure before performing any
maintenance.
1. Check system at least once per shift
to insure proper drainage. Look for
water in the drain tubing.
2. Before performing maintenance on
system, close main shut-off valve
located upstream. Bleed off residual
air in system.
MAINTENANCE - WATER SEPARATOR
FILTER 13-0041
1. Before performing maintenance on
unit, close any main shut-off valve
located upstream of filter. Bleed off
residual air in unit.
2. To open filter, press button located on
clamp ring and rotate ring either clock
wise or counterclockwise while pull ing down on ring. The metal bowl guard
and plastic bowl can then be removed
from the filter body.
3. Remove the filter element by loosen ing counterclockwise. Clean or replace
the filter element. Frequency of ele ment replacement will depend upon
air quality, air usage and condition of
the air piping. It is recommended to
change the element every six months.
4. Inspect o-ring for damage. Replace if
necessary.
SB-6-159-H Page 3
7
6
5
8
9
Figure 3 -13-0041
Body
(Not
Available)
HAF-6
Filter Kit
(Includes Bowl
O-Ring
HAF-18
Automatic Drain
(Available sepa-
rately)
HAF-8
Transparent
Plastic Bowl
HAF-19
Metal
Bowl
Guard
HAF-409
Clamp Ring
10
11
6
12
Gasket
(Included
with
HAF-26)
Baffle
(Included
with
HAF-26)
HAF-17
Bowl
O-Ring
HAF-26
Element
Retainer
HAF-11
Flexible Drain
(supplied with
13-0041)
5. Inspect plastic bowl for signs of dam age such as cracks, crazing or deterio ration. Replace if necessary.