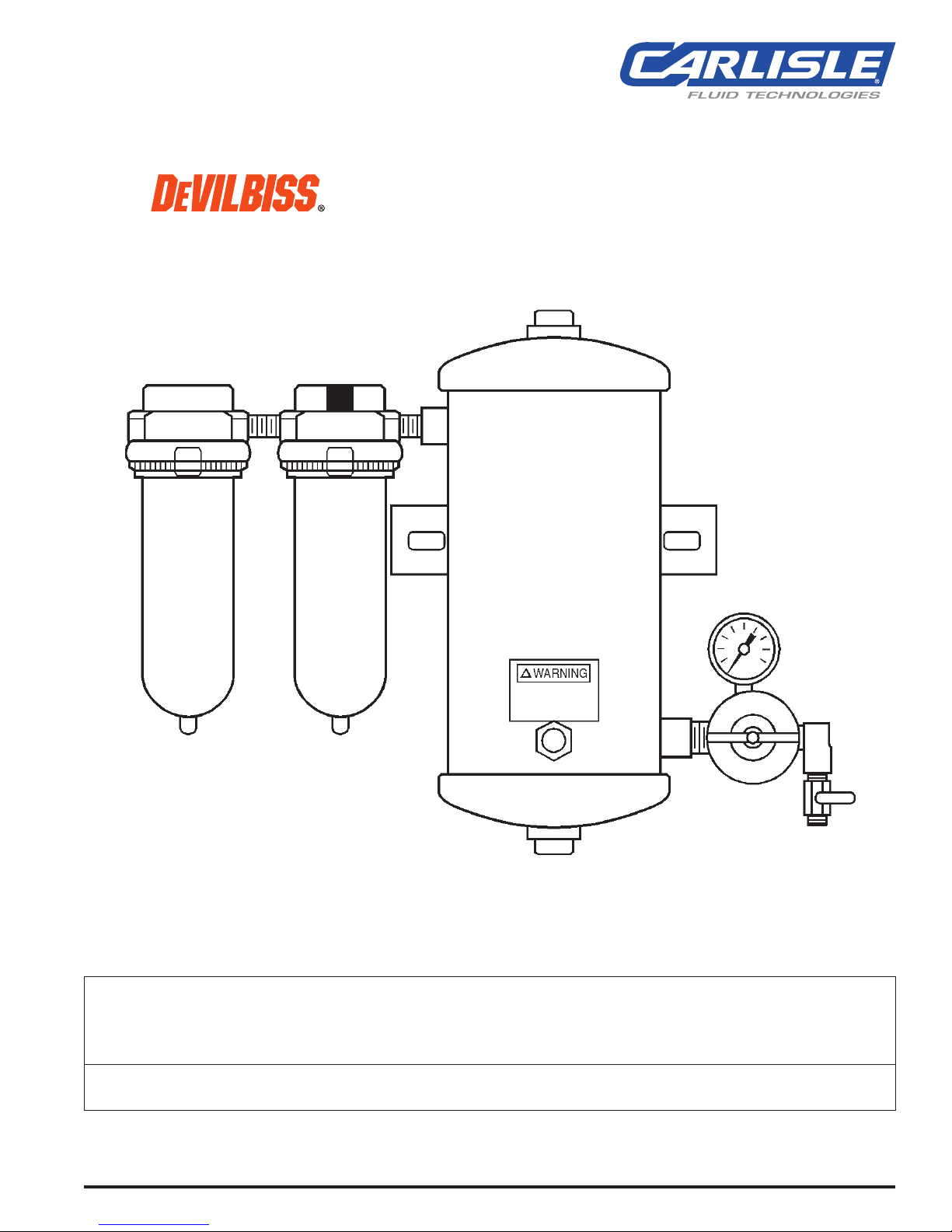
SERVICE MANUAL
EN
DAD-500 (130026)
DESICCANT AIR DRYING SYSTEM
IMPORTANT! DO NOT DESTROY
It is the Customer's responsibility to have all operators and service personnel read and understand this manual.
Contact your local DeVilbiss representative for additional copies of this manual.
READ ALL INSTRUCTIONS BEFORE OPERATING THIS DEVILBISS PRODUCT.
SB-6-156-R1 (3/2018) 1 / 8 www.carlisleft.com
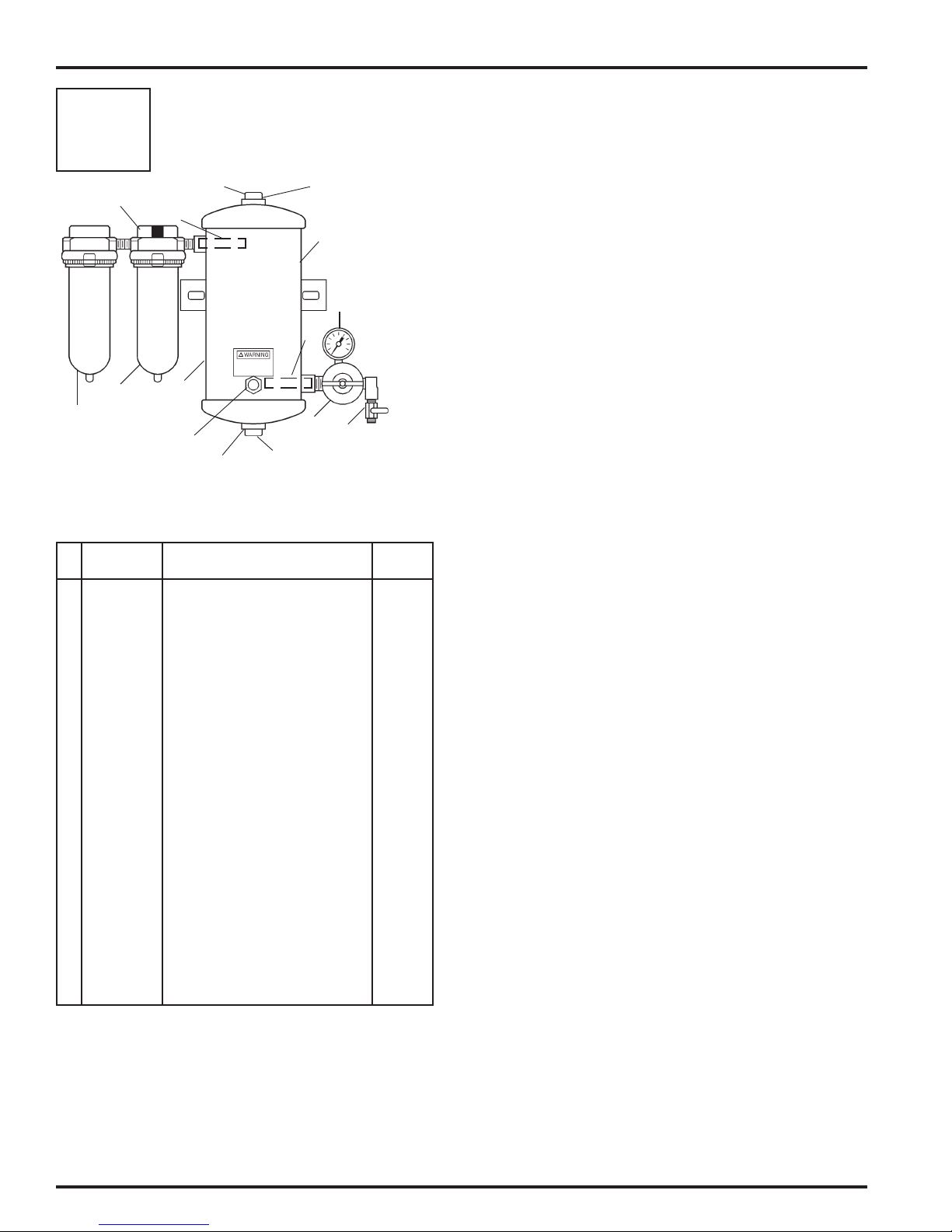
EN
CA PROP
65
Air In
11
PROP 65 WARNING
WARNING: This product contains chemicals known
to the State of California to cause cancer and birth
defects or other reproductive harm.
15
8
14
10
DESCRIPTION
The 25 CFM DAD-500 Desiccant Air Drying System
is designed to be a point of use system. It is capable
of removing dirt, water, oil and water vapor from
compresssed air. It consists of a filter separator,
coalescing filter, desiccant dryer, air regulator and main
air supply shut off valve.
SPECIFICATIONS
5
8
2
1
3
4
6
9
14
15
Air Out
Figure 1
DAD-500 25 CFM Desiccant Air Dryer
PARTS LIST
Ref. Replacement Individual
No. Part No. Description Parts Req.
1 13-0041 Water Separator Filter 1
(HAF-502)
2 HAF-505 Oil Coalescing Filter 1
3 --- Desiccant Dryer 1
4 HAR-507 Air Regulator 1
5 GA-288 Gauge 1
6 VA-542 Ball Valve 1
*7 DAD-1 Replacement Desiccant
(1 Humidity Indicator Paper
Included)
8 DAD-8 Air Filter, (inside of tank) 2
9 DAD-400 Humidity Indicator (1 Humidity 1
Indicator Paper Included)
10 PT-417 Desiccant Tank (without desiccant) 1
(Includes Ref. No. 8)
11 HAF-404 Filter Change Indicator 1
12 DAD-600 Dessicant Tune-Up Kit
Includes 1 each: DAD-1 and HAF-6.
13 DAD-600-1 Complete Tune-Up Kit
Includes 1 each: DAD-1, HAF-28,
and HAF-6.
14
SSG-8217-K2
15 PT-96 Pipe Plug, Special, 1-1/2 NPT 2
16 VA-595 Main Air Supply Shut Off Valve 1
O-Ring Kit (2) 1
(Not shown)
(Not shown)
(Not shown)
(Not shown)
1
1
1
13-0041 (HAF-502) Water Separator Filter - See page 4:
Air Inlet 1/2" NPT(F)
Air Outlet 1/2" NPT(F)
Air Flow Capacity 100 CFM
Maximum Operating Pressure 150 PSIG (10.3 Bar)
Maximum Temperature 150° F (65.6°C)
Automatic Drain Standard
Filter 5 micron
HAF-505 Oil Coalescing Filter - See page 5:
Air Inlet 1/2" NPT(F)
Air Outlet 1/2" NPT(F)
Air Flow Capacity 55 CFM
Maximum Operating Pressure 150 PSIG (10.3 Bar)
Maximum Temperature 150° F (65.6°C)
Automatic Mechanical Drain Standard
Pressure Differential Indicator Standard
Filter 0.01 Micron
Desiccant Dryer - See page 3:
Air Inlet 1/2" NPT(F)
Air Outlet 1/2" NPT(F)
Air Flow Capacity 25 CFM
Maximum Operating Pressure 150 PSIG (10.3 Bar)
Maximum Temperature 150° F (65.6°C)
Humidity Indicator Standard
Water Vapor Removal -40° F Dew Point
HAR-507 Air Regulator - See page 5:
Air Inlet 3/8" NPT(F)
Air Outlet 1/4" NPT(F) (3 ea.)
Air Flow 60 CFM
Maximum Operating Pressure 150 PSIG (10.3 Bar)
Maximum Temperature 120° F (65.6°C)
VA-595 Main Air Supply Shut Off Valve - Not Shown:
Air Inlet and Air Outlet 1/2" NPT(M)
Maximum Operating Pressure 175 PSIG (12.0 Bar)
*The Safety Data Sheet (SDS) is available upon request.
Shipping Weight: DAD-500 = 35 lbs.
SB-6-156-R1 (3/2018)2 / 8www.carlisleft.com
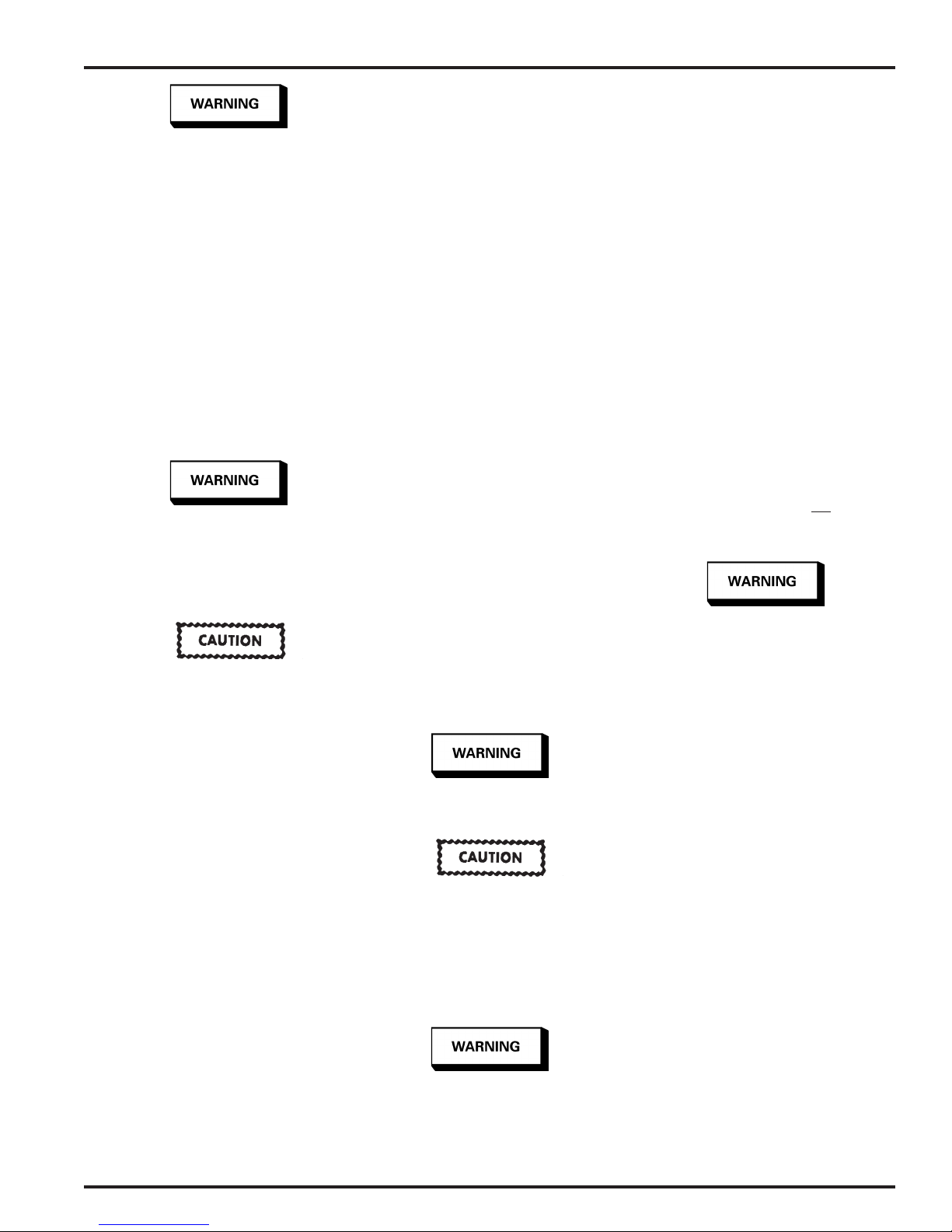
EN
Risk of personal injury.
Risk of property damage.
Except as otherwise specified by
the manufacturer, this product
is specifically designed for compressed air service and use with
any other fluid (liquid or gas) is a
misapplication. For example, use
with or injection of certain hazardous gases in the system (such as
oxygen or liquid petroleum gas)
could be harmful to the unit or
result in a combustible condition
that may cause fire or explosion.
Manufacturer's warranties are
void in the event of misapplication
and manufacturer assumes no responsibility for any resulting loss.
INSTALLATION
Risk of injury. Release all air pressure from system before servicing system. Be sure to read and
understand all Service Bulletins on
the separate components before
using the system. Use only specified DeVilbiss parts.
Certain solvents, paints and
chemicals may attack plastic
filter bowl and can cause bowl
failure. Do not use near these
materials.
NOTE
Risk of equipment damage! Do
not install your DAD unit where
it is subjected to sudden depressurization cycles exceedling
20 PSIG. Quick relieving air
solenoid valves, typical in some
spray booths, will eventually fail
pressure gauges and filters, and
produce desiccant "dusting".
To minimize sudden depressurization effect, replace the
existing solenoid with a "slow
closing solenoid valve". (One
source: Automatic Switch Co.)
Or, install an air adjusting valve
at the existing solenoids outlet.
1. See Plumbing Guide on page 6.
Be sure to read all "Warnings" and
"Cautions" in this manual and component manuals on the unit before
installation or using this equipment.
2. Install air drying system as close as
possible to the point where the air is
being used. Use template to position
location of system.
3. Install main air supply shut off valve
and piping union fitting (supplied by
user) upstream of air drying system
to allow maintenance to the unit.
4. Install unit with air flow through filter
in direction of arrow on top of filters.
5. Minimum 1/2" NPT piping is recommended. Avoid using fittings, couplings, etc. that restrict air flow.
6. Maximum inlet pressure and operating
temperature is: 150 PSIG (10.3 bar) and
a150° F (65.6°C)
7. Fill tank with desiccant materials (see
paragraphs 4, 5, 6 under "MAINTENANCE".
8. Two 6' lengths of vinyl tubing are
shipped loose with the system. Slide
over automatic drains which protrude
from bottom of the water/separator
and the oil coalescing filters. Place the
other end of vinyl tubing into appropriate receptacle. Prevent vinyl tubing
from becoming kinked which would
prevent free movement of liquids
discharged from the automatic drain.
9. An optional manual drain (HAF-11) can
be installed in place of the automatic
drains.
OPERATION
After the system is installed and ready to use:
1. Attach air hose(s) to outlet valve.
2. Open main shut-off valve upstream of
system.
3. Adjust regulator to desired setting by
turning "T" handle in or out.
4. Open ball valve to supply air to spray
guns or tool being used. With air
flowing, readjust air pressure at regulator if necessary.
5. After use, shut off ball valve and bleed
off residual air in hose.
MAINTENANCE
Risk of injury. Components under
pressure. Relieve air pressure before
performing any maintenance.
Certain solvents, paints and chemicals may attack plastic bowl and
can cause bowl failure. Do not use
near these materials. When bowl
becomes dirty, wipe only with
a clean, dry cloth. Immediately
replace any crazed, cracked, damaged or deteriorated plastic bowl
with a new plastic bowl. Reinstall
metal bowl guard.
Risk of injury. Do not place unit
in service without metal bowl
guard installed.
1. Check system at least once per shift to
insure proper drainage. Look for water
in the drain tubing.
2. Before performing maintenance on
system, close main shut-off valve
located upstream. Bleed off residual
air in system.
MAINTENANCE - DESICCANT DAD-1
NOTE
The desiccant tank contains an internal filter (DAD-8) at the inlet and
outlet. Be careful not to damage
them when changing desiccant.
1. Replace the desiccant when the hu-
midity indicator changes to a pink or
white color. Remove the pipe plug at the
bottom of the tank. Allow the material
to drain into a two (2) gallon or larger
container.
2. Once all the material has been removed,
replace the pipe plug (see "Note" following) and tighten (do not over tighten)
securely (air tight).
NOTE
Use PTFE tape on pipe plug threads
and all threaded fittings to facilitate
removal in the future. Do not use
loctite or any material that may
bond and make removal difficult.
Risk of injury. Only use a socket
wrench to remove the DAD-400
humidity indicator from the desiccant tank. Immediately replace
the DAD-400 humidity indicator
if damaged.
3. Replace the humidity indicator paper
(supplied with DAD-1 Dessiccant) by
removing the DAD-400 humidity indicator. Pry out the old paper and push
in the new paper (printed side facing
away from the glass).
4. Remove the pipe plug on top of the
unit.
5. Replace desiccant material, DAD-1
(19-0831). Two bags are supplied.
Hold bag pointed upward and cut bag
on dotted line. Grasp and hold bag
where cut and rotate over opening on
top of tank. Empty both bags into tank.
("Note" tank must be filled completely
to prevent damage to desiccant.)
6. Wrap pipe plug with 2 wraps of PTFE
tape. Replace the pipe plug and tighten
until air tight (do not over tighten).
7. The humidity indicator will return to a
blue color within five minutes.
8. The desiccant material should be disposed of properly.
9. Refer to the appropriate service bulletin
for checking the filters and components.
NOTE
A desiccant Tune-Up Kit Part No.
DAD-600, is available. Contains the
following parts to completely recondition a desiccant air station:
SB-6-156-R1 (3/2018) 3 / 8 www.carlisleft.com