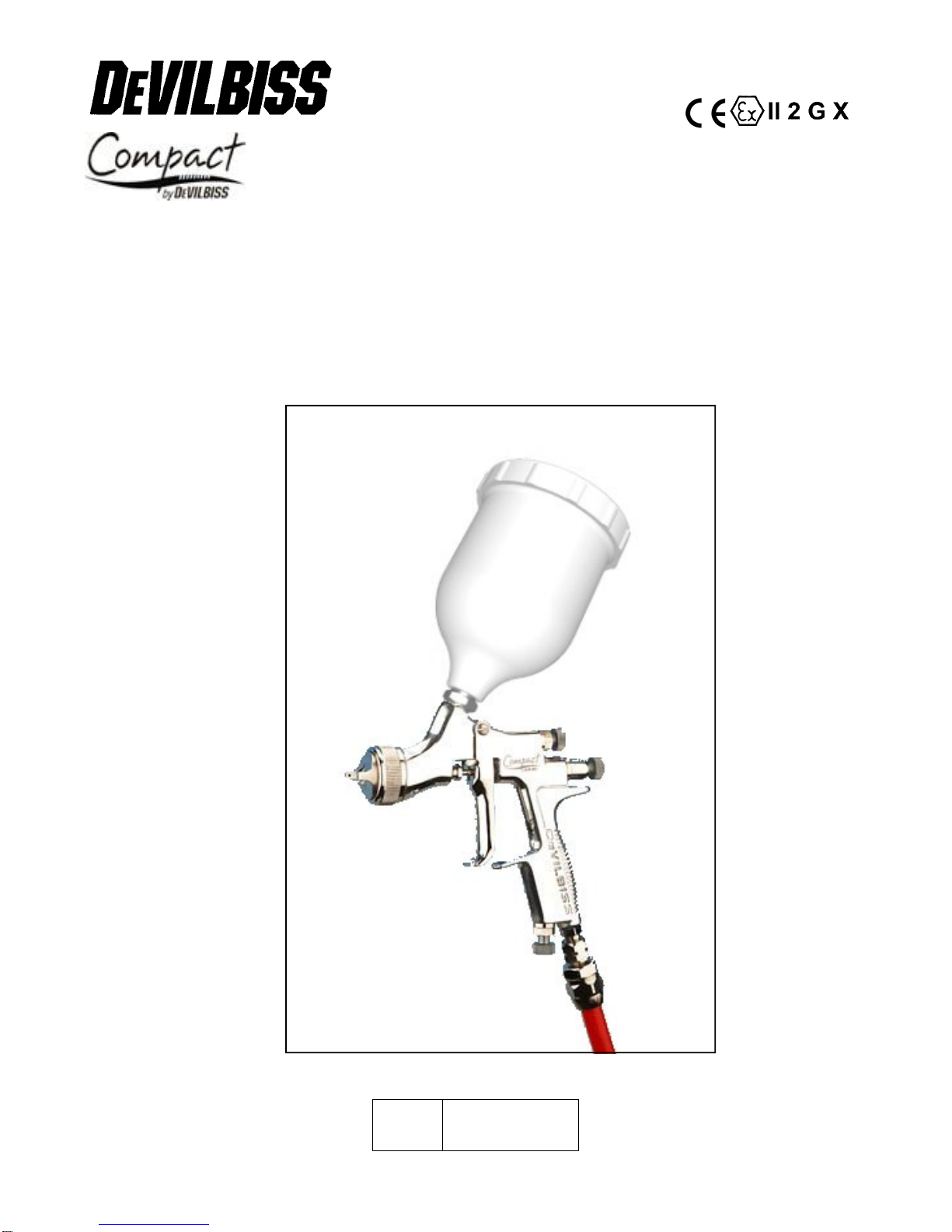
SB-E-2-534 ISS.06
Operation Manual
Advanced - Conventional Gravity
Feed Spraygun
E
P 1 – 12

E
Operation Manual
COMPACT – Gravity Feed S p r aygun
Important
Read and follow all instructions and Safety Precautions before using this equipment
Description
The Compact Gravity feed Spraygun Kit complies to ATEX regulations 94/9/EC, protection level;
II 2 G X, Suitable for use in Zones 1 and 2
Important: : These Sprayguns are suitable for use with solvent based materials. These guns are not
designed for use with highly corrosive and/or abrasive materials and if used with such materials it must
be expected that the need for cleaning and/or replacement of parts will be increased. If there is any
doubt regarding the suitability of a specific material contact your local Distributor or ITW Finishing direct.
.
COM-G430-16
Model Part Number
Example:
Aircap
Fluid Nozzle size
(14 = 1.4 mm)
EC Declaration of Conformity
We, ITW Finishing UK, Ringwood Rd, Bournemouth, Dorset, BH11 9LH, UK, as the
manufacturer of the Spray gun model Compact, declare, under our sole responsibility, that the
equipment to which this document relates is in conformity with the following standards or other
normative documents:
BS EN 292-1 PARTS 1 & 2: 1991, BS EN 1953: 1999; and thereby conform to the
protection requirements of Council Directive 98/37/EEC relating to Machinery Safety Directive,
and: EN 13463-1:2001, council Directive 94/9/EC relating to Equipment and Protective
Systems intended for use in Potentially Explosive Atmospheres protection level II 2 G X.
For HVLP and Trans-Tech Aircaps these products comply with the requirements of the EPA
guidelines, PG6/34,PG6/20 and PG6/23 achieving transfer efficiency in excess of 65%.
B. Holt, General Manager
30th June 2003
ITW Finishing Systems and Products reserve the right to modify equipment specification without prior
notice.
2 © 2003 ITW Finishing Systems and Products
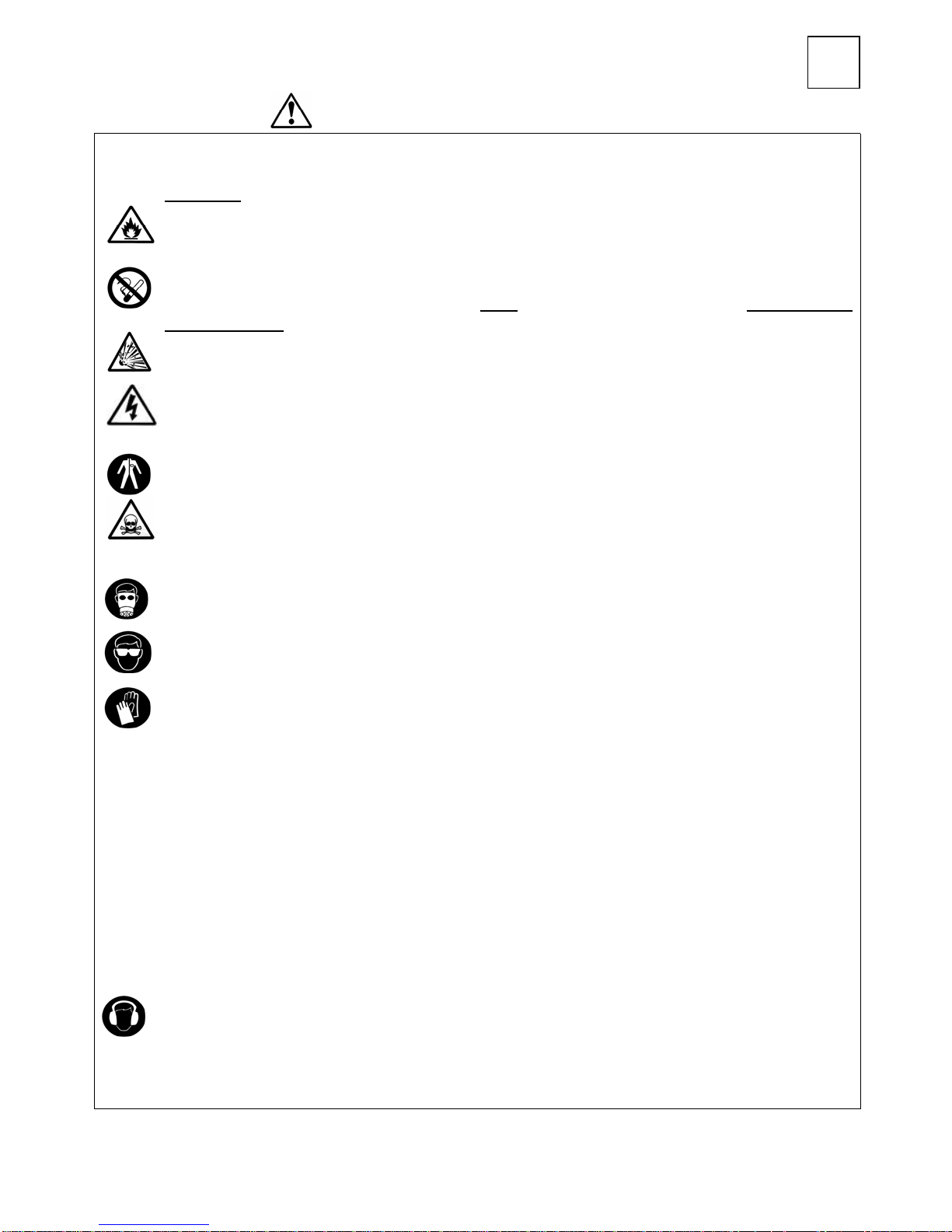
E
SAFETY WARNINGS
Fire and explosion
Solvents and coating materials can be highly flammable or combustible when sprayed.
ALWAYS
before using this equipment.
Users must comply with all local and national codes of practice and insurance company
requirements governing ventilation, fire precautions, operation and house-keeping of
working areas.
This equipment, as supplied, is NOT
Hydrocarbons.
Static electricity can be generated by fluid and/or air passing through hoses, by the
spraying process and by cleaning non-conductive parts with cloths. To prevent ignition
sources from static discharges, earth continuity must be maintained to the spray gun
and other metallic equipment used. It is essential to use conductive air and/or fluid
hoses.
Toxic vapours – When sprayed, certain materials may be poisonous, create irritation or
be otherwise harmful to health. Always read all labels, safety data sheets and follow any
recommendations for the material before spraying. If in doubt, contact your material
supplier.
The use of respiratory protective equipment is recommended at all times. The type of
equipment must be compatible with the material being sprayed.
Always wear eye protection when spraying or cleaning the spray gun.
Gloves must be worn when spraying or cleaning the equipment.
Training – Personnel should be given adequate training in the safe use of spraying equipment.
refer to the coating material suppliers instructions and COSHH sheets
suitable for use with Halogenated
Personal Protective Equipment
Misuse
Never aim a spray gun at any part of the body.
Never exceed the max. recommended safe working pressure for th e equipment.
The fitting of non-recommended or non-original spares may create hazards.
Before cleaning or maintenance, all pressure must be isolated and relieved from the equip ment.
The product should be cleaned using a gun-washing machine. However, this equipment should
not be left inside gun-washing machines for prolonged periods of time.
Noise Levels
The A-weighted sound level of spray guns may exceed 85 dB (A) depending on the setup being used. Details of actual noise levels are available on request. It is
recommended that ear protection is worn at all times when spraying.
Operating
Spray equipment using high pressures may be subject to recoil forces. Under certain
circumstances, such forces could result in repetitive strain injury to the operator.
© 2003 ITW Finishing Systems and Products 3
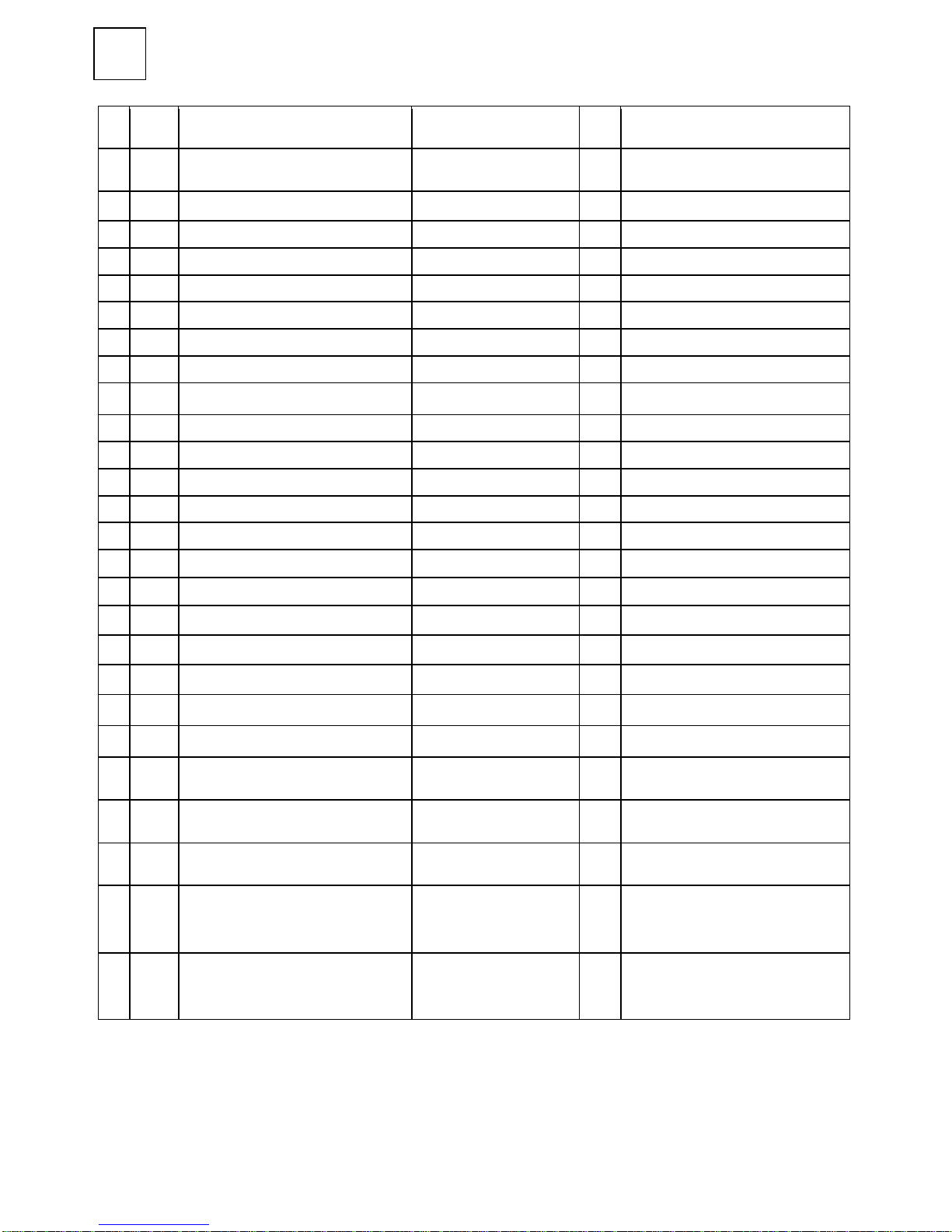
E
Parts List
Ref.
No
1 Air Cap/Retaining ring
2 Nozzle See Selection Chart
*+ 3 Separator SP-626-K5 5
*+ 4 Packing GTI-445-K2 2
5 Spreader Valve SP-403-K 1
6 Stud and Screw GTI-408-K5 5
7 Needle Adjusting Screw SP-614-K 1
*+ 8 Spring SP-622-K5 1
+ 9 Needle See Selection Chart
10 Airvalve housing + seal SP-612-K 1
*+ 11 Spindle 1
12 Trigger SP-617-K 1
13 Connector SP-611-K 1
Description Part Number Qty Options
See Selection Chart
14 Airflow Valve SP-402-K 1
15 Drip Check Lid kit of 5 GFC-2-K5 1
+ 16 Air Valve Service Kit SPK-101-K 1
17 Retaining Ring and Seals SPK-102-K 1
*+ 18 Spreader/ Cheater Service Kit GTI-428-K5 5
19 Circlip 25746-007-K5 5
+ 20 Cup Lid GFC-501 1
21 Filter KGP-5 1
22 1/2 Ltr Gravity Cup Kit GFC-501
* 23 Air Valve assembly Tool
24 Spanner SPN-5
Spraygun Service Kit
(parts included marked + )
Spraygun Service Kit
(parts included marked * )
SPK-401-** 1 ,13,14, 16,18,20,22
SPK-402-** 1 ,13,14, 16,18,20,22
e.g ** =14 =1.4 mm
e.g ** =14 =1.4 mm
4 © 2003 ITW Finishing Systems and Products