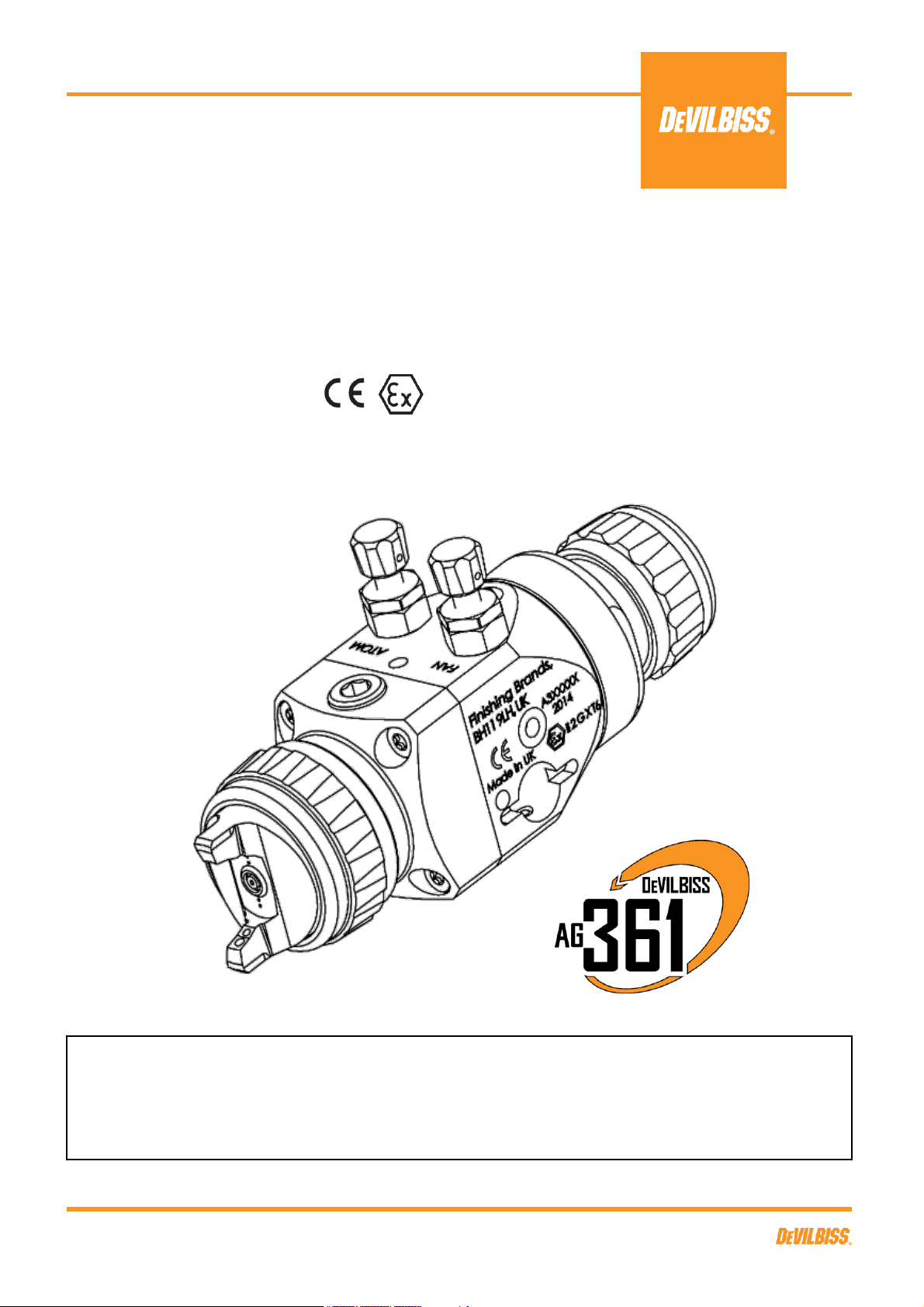
READ ALL INSTRUCTIONS BEFORE OPERATING THIS DEVILBISS PRODUCT.
Contact your local DeVilbiss representative for additional copies of this manual.
IMPORTANT! DO NOT DESTROY
It is the Customer's responsibility to have all operators and service personnel read and understand
this manual.
Low Pressure, Air Atomisation Automatic Spray
Guns.
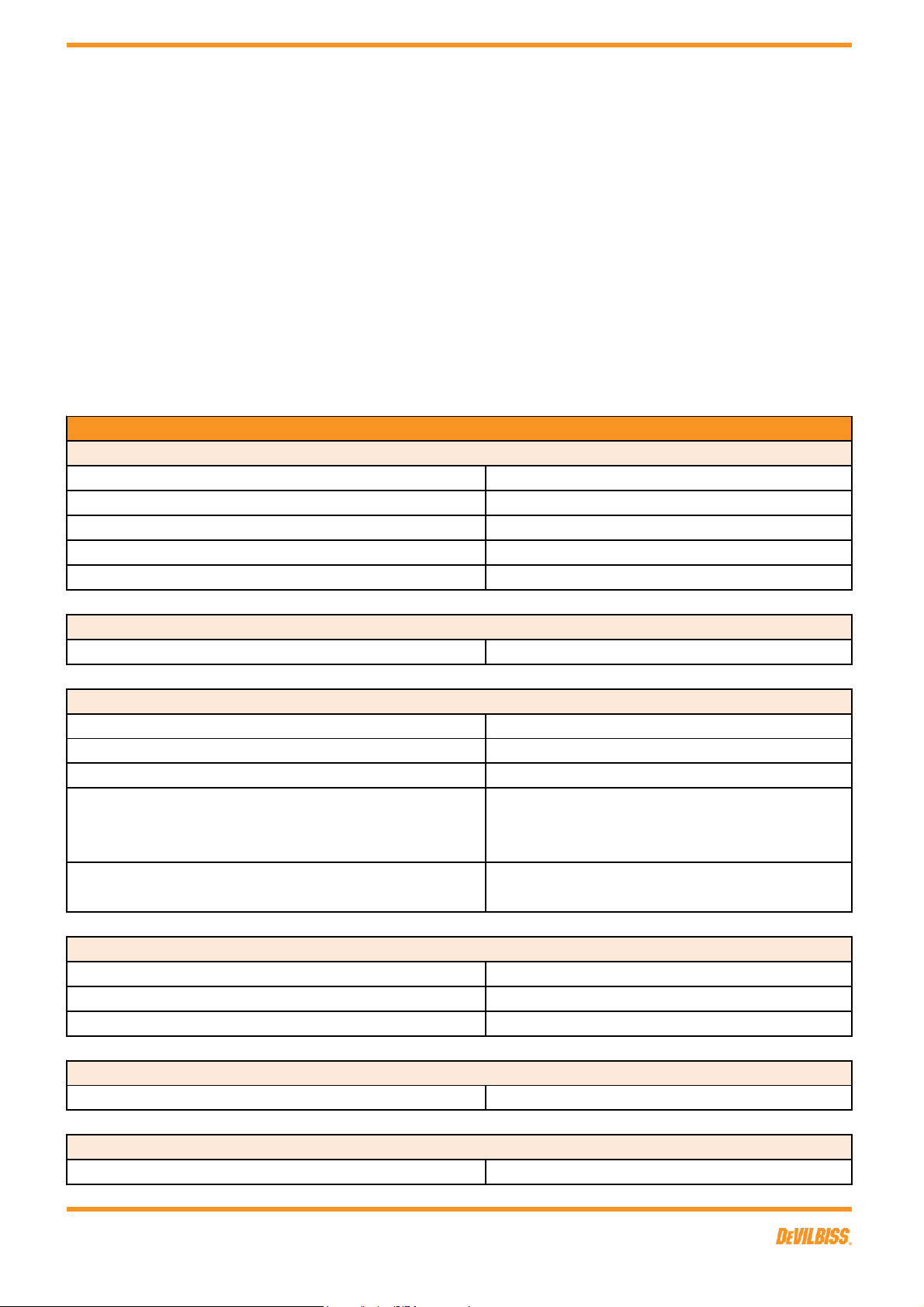
EN
P1 =
P2 =
P3 =
P1 =
P2 =
P3 =
670g
The AG361 and AG361E low pressure air atomising spray guns are designed to be cost effective guns
with maximum control and serviceability.
The AG361 is intended for most types of general industrial coating and fine finishing operations,
suitable for both waterbased and solventbased applications.
The AG361E is designed for the application of specialised waterbased ceramic and enamel coatings
for sanitaryware and vitreous markets.
Guns are available with a range of Conventional, Trans-Tech (High Efficiency) and HVLP atomisation
air caps, to give a choice of atomisation and Transfer Efficiency parameters. They are designed as a
flexible solution for the modern coating applicator with multiple accessories available, to futher
optimise the process.
HDPE, Viton Extreme
Max Air Input Pressure
Nitride Coated Stainless Steel
Fluid Tip and Needle Construction
Gun Head and Fluid Passageways
Quickclean™ Coated Aluminium
FLUID AND AIR INLET PRESSURES (See pages 8 & 9)
Max Ambient Operating Temperature
MATERIALS OF CONSTRUCTION
4 - 7 Bar [58 psi - 102psi]
Electroless Nickel Plated Brass
146 x 66 (Including Valves) x 44
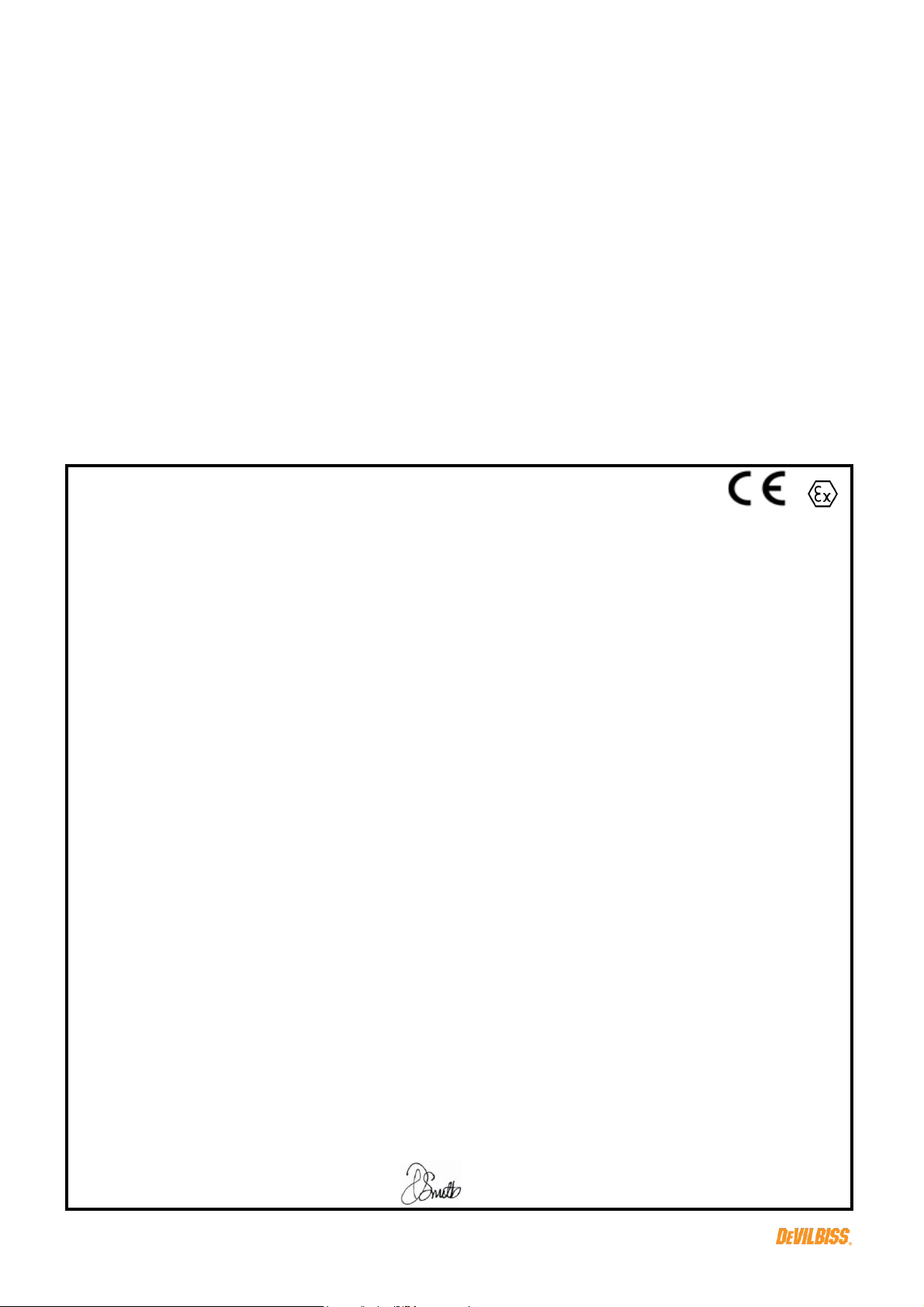
This Product is designed for use with:
Solvent and water based materials
Suitable for use in hazardous area:
Notified body details and role:
The object of the declaration described above is in conformity with the relevant Union
harmonisation legislation:
Providing all conditions of safe use / installation stated within the product manuals have been complied with and
also installed in accordance with any applicable local codes of practice.
Signed for and on behalf of Finishing Brands
UK Ltd:
Lodging of Technical file
This Declaration of conformity /
incorporation is issued under the sole
responsiblility of the manufacturer:
Finishing Brands UK Ltd,
Ringwood Road,
Bournemouth, BH11 9LH. UK
EU Declaration of Conformity
Machinery Directive 2006/42/EC
ATEX Directive 2014/34/EU
by complying with the following statutory documents and harmonised standards:
EN ISO 12100:2010 Safety of Machinery - General Principles for Design
BS EN 1953:2013 Atomising and spraying equipment for coating materials - Safety requirements
EN 14462:2005+A1:2009 Surface treatment equipment - Noise test code for surface treatment equipment
including its ancillary handling equipiment - Accuracy grades 2 and 3
EN 1127-1:2011 Explosive atmospheres - Explosion prevention - Basic concepts
EN 13463-1:2009 Non electrical equipment for use in potentially explosive atmospheres - Basic methods and
requirements
HVLP and High Efficiency products comply with the requirements of PG6 from the EPA guidelines and offer
greater than 65% transfer efficiency.
Product Description / Object of Declaration:
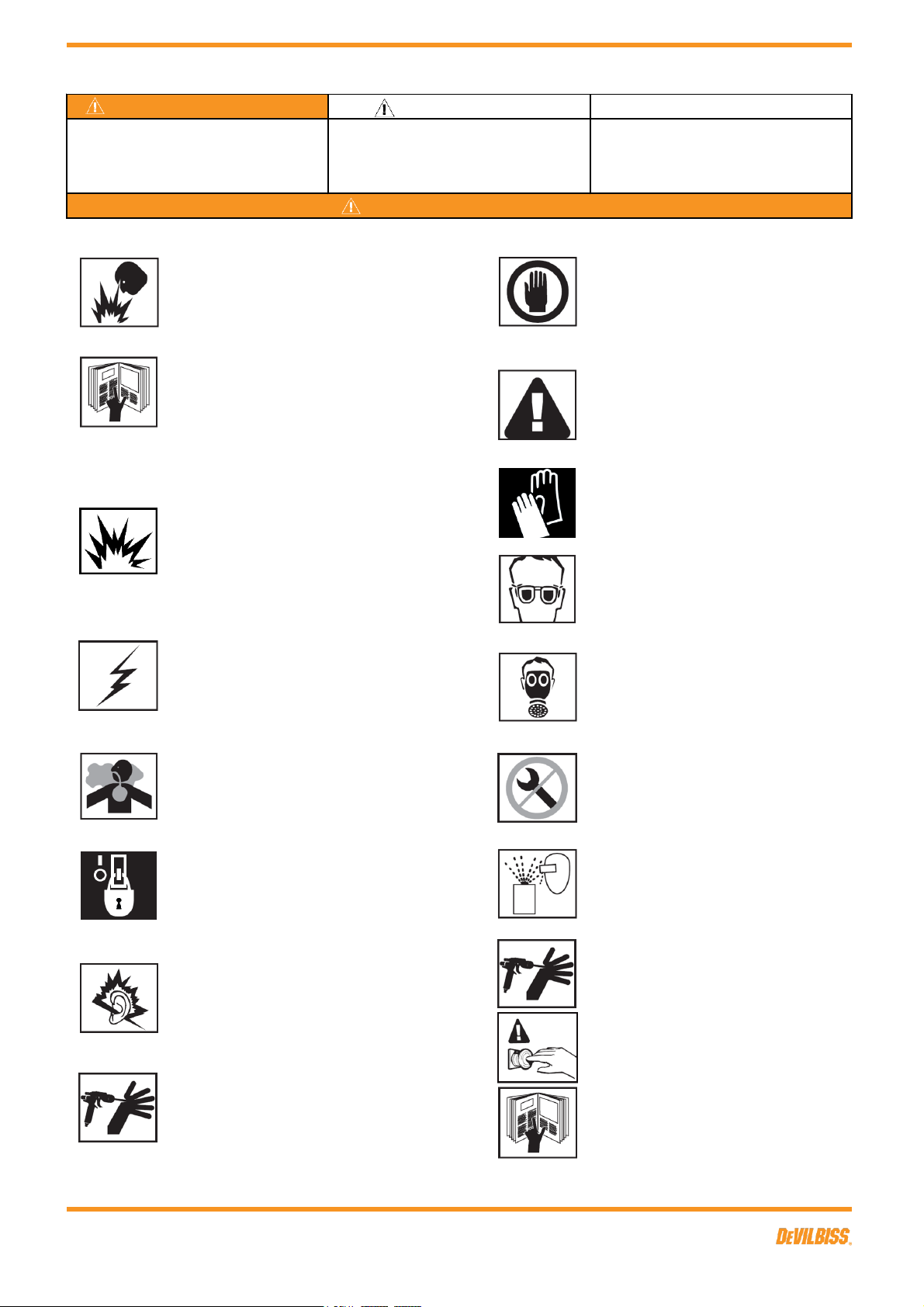
SOLVENTS AND COATING MATERIALS. Can be highly flammable or
combustible when sprayed. Always refer to the coating material supplier's
instructions and safety sheets before using this equipment.
READ THE MANUAL. Before operating finishing equipment, read and
understand all safety, operation and maintenance information provided in the
operation manual. Users must comply with all local and national codes of
practice and insurance company requirements governing ventilation, fire
precautions, operation and house-keeping of working areas.
In this part sheet, the words WARNING, CAUTION and NOTE are used to emphasise important safety information as
follows:
KNOW WHERE AND HOW TO SHUT OFF THE EQUIPMENT
IN CASE OF AN EMERGENCY.
WEAR SAFETY GLASSES. Failure to wear safety glasses with
side shields could result in serious eye injury or blindness.
WEAR RESPIRATOR. The use of respiratory protective
equipment is recommended at all times. The type of equipment
must be compatible with the material being sprayed.
FIRE AND EXPLOSION HAZARD. Never use 1,1,1-Trichloroethane,
Methylene Chloride, other Halogenated Hydrocarbon solvents or fluids
containing such solvents in equipment with aluminium wetted parts. Such use
could result in a serious chemical reaction, with the posibility of explosion.
Consult your fluid suppliers to ensure that the fluids being used are compatible
with aluminium parts.
LOCK OUT / TAG-OUT. Failure to de-energise, disconnect, lock out and tagout all power sources before performing equipment maintenance could cause
serious injury or death.
EQUIPMENT MISUSE HAZARD. Equipment misuse can cause
the equipment to rupture, malfunction or start unexpectedly and
result in serious injury.
GLOVES. Must be worn when spraying or cleaning the
equipment.
Hazards or unsafe practices which could result in
minor personal injury, product or property
damage.
Read the following warnings before using this equipment.
STATIC CHARGE. Fluid may develop a static charge that must be dissipated
through proper grounding of the equipment, objects to be sprayed and all other
electrically conductive objects in the dispensing area. Improper grounding or
sparks can cause a hazardous condition and result in fire, explosion or elecrtic
shock and other serious injury.
TOXIC VAPOURS. When sprayed, certain materials may be poisonous, create
irritation, or are otherwise harmful to health. Always read all labels, safety
sheets and follow any recommendations for the material before spraying. If in
doubt contact your material supplier.
IT IS THE RESPONSIBILITY OF THE EMPLOYER TO PROVIDE THIS INFORMATION TO THE OPERATOR OF THE EQUIPMENT.
NOISE LEVELS. The A-weighted sound level of pumping and spray equipment
may exceed 85 dB(A) depending on equipment settings. Actual noise levels
are available on request. It is recommended that ear protection is worn at all
times while equipment is in use.
PROJECTILE HAZARD. You may be injured by venting liquids or
gases that are released under pressure, or flying debris.
OPERATOR TRAINING. All personnel must be trained before
operating finishing equipment.
PRESSURE RELIEF PROCEDURE. Always follow the pressure
relief procedure in the equipment instruction manual.
NEVER MODIFY THE EQUIPMENT. Do not modify the
equipment unless the manufacturer provides written approval.
HIGH PRESSURE CONSIDERATION. High pressure can cause serious
injury. Relieve all pressure before servicing. Spray from the gun, hose leaks or
ruptured components can inject fluid into your body and cause extremely
serious injury.
Hazards or unsafe practices which could result in
severe personal injury, death or substantial
property damage.
Important installation, operation or maintenance
information.
INSPECT THE EQUIPMENT DAILY. Inspect the equipment for
worn or broken parts on a daily basis. Do not operate the
equipment if you are uncertain about its condition.
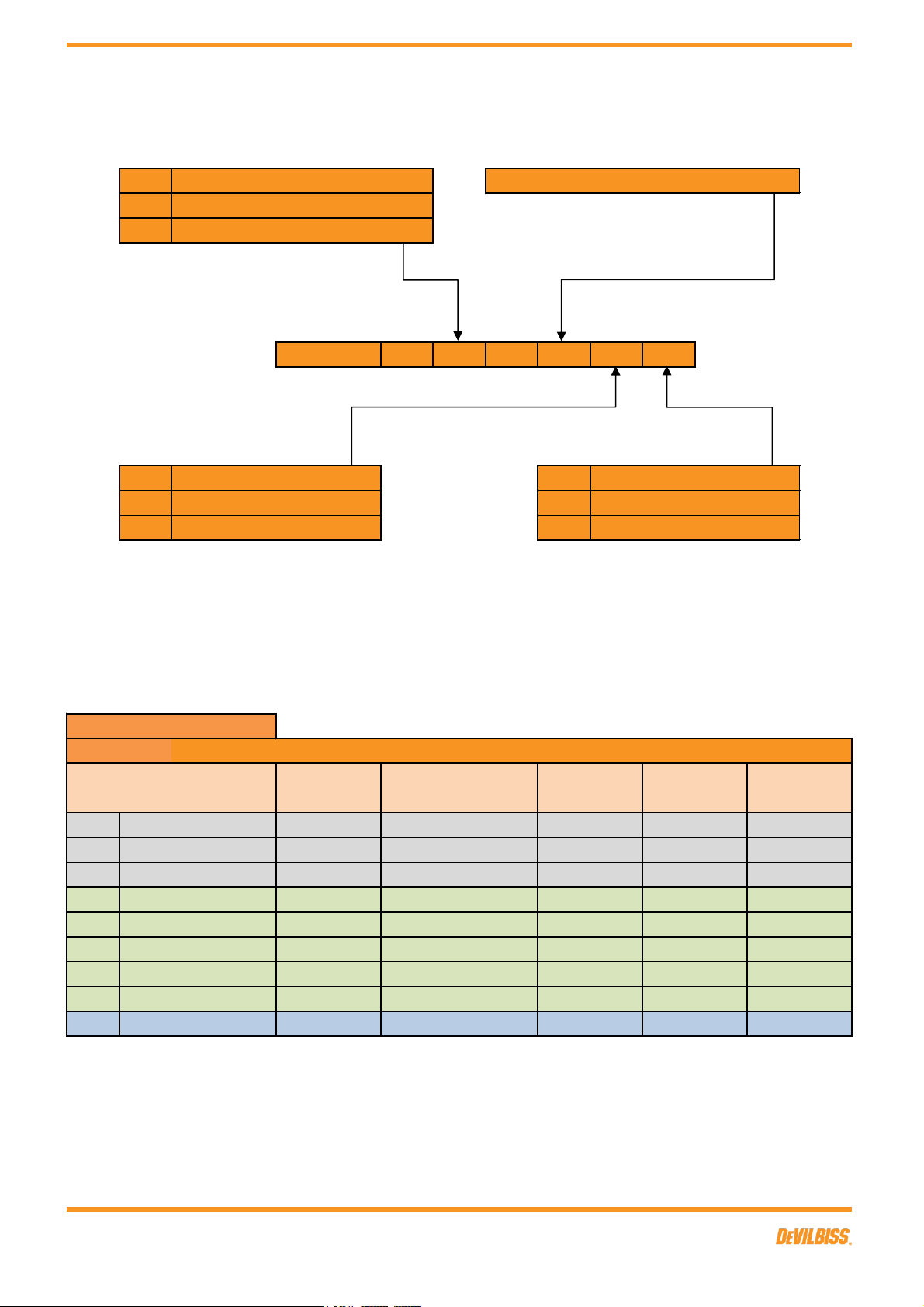
EN
C
TE
HV
- TE40 - 14N F P
F P
M R
C1
C2
C3
TE10
TE20
TE30
TE40
TE50
HV30***
Typical Fan Pattern
Size**
Flow rates may vary according to paint/material and pressure used.
Fan pattern size @ 200mm distance.
HV30 (HVLP) operates at 0.7 Bar [10 psi] atomisation air pressure at the cap.
Recommended
Air Inlet Pressure
GUN PART NUMBER FORMAT & PART SELECTION GUIDE
AIR CAP PERFORMANCE GUIDE
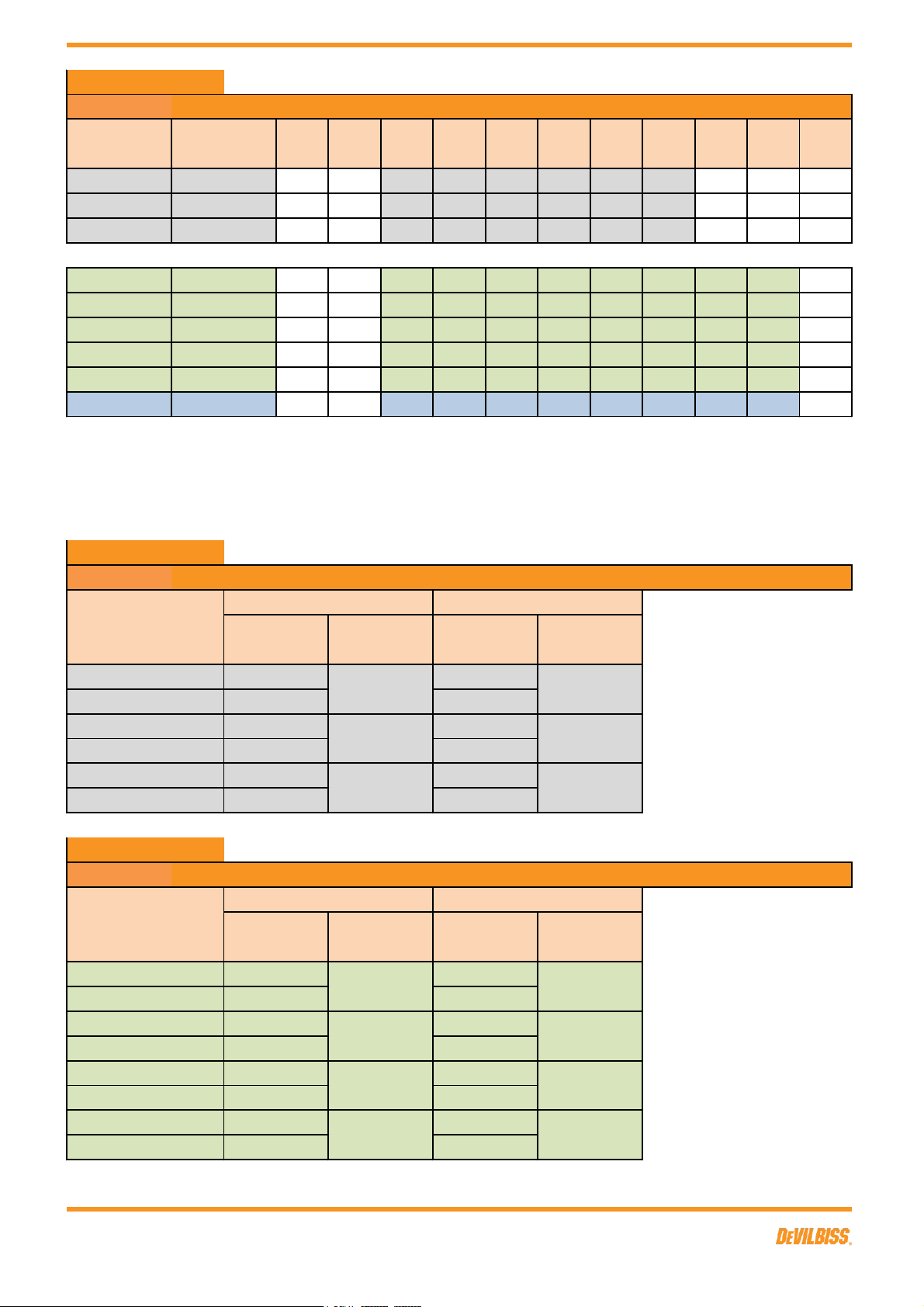
EN
- - SN SN SN SN SN SN - - -
- - SN SN SN SN SN SN - - -
- - SN SN SN SN SN SN - - -
- - SN SN SN SN SN SN SN SN -
- - SN SN SN SN SN SN SN SN -
- - SN SN SN SN SN SN SN SN -
- - SN SN SN SN SN SN SN SN -
- - SN SN SN SN SN SN SN SN -
- - SN SN SN SN SN SN SN SN -
S =
N =
For Conventional tip & needle part numbers, see table 3.
Nitride hardened tips & needles also available in this type & size.
RECOMMENDED FLUID TIP / AIR CAP COMBINATIONS
For Trans-Tech / HVLP tip & needle part numbers, see table 4.
High quality stainless steel tips & needles available in this type & size.
CONVENTIONAL FLUID TIPS & NEEDLES
TRANS-TECH / HVLP FLUID TIPS & NEEDLES
SPA-361-16-18-K
PROC-215N-12-K
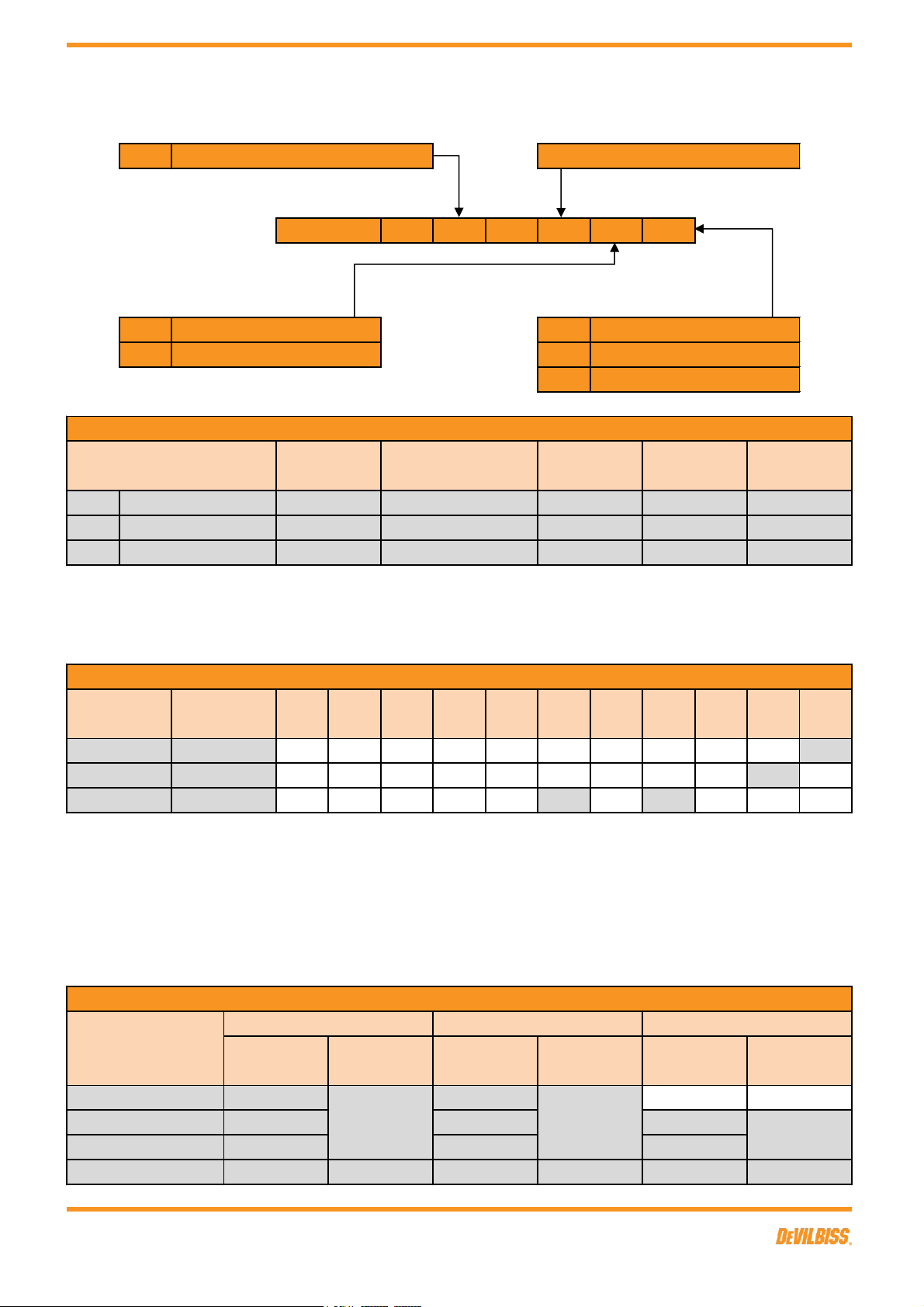
EN
C
- C62 - 28C F P
F P
R
C62
C64
C67
*
**
For Ceramic tip & needle part numbers, see table 7.
Fan pattern size @ 300mm distance.
See table 6
Recommended
Air Inlet Pressure
TABLE 7 - AG361E CERAMIC FLUID TIPS & NEEDLES
High quality stainless steel tips & needles available in this type & size.
Nitride hardened tips & needles also available in this type & size.
CERAMIC & ENAMEL INDUSTRY GUN PART NUMBER FORMAT & PART SELECTION GUIDE
Flow rates may vary according to paint/material and pressure used.
Typical Fan Pattern
Size**
Tungsten carbide tips & needles also available in this type & size.
TABLE 6 - AG361E FLUID TIP / AIR CAP COMBINATIONS
TABLE 5 - AG361E AIR CAP PERFORMANCE GUIDE
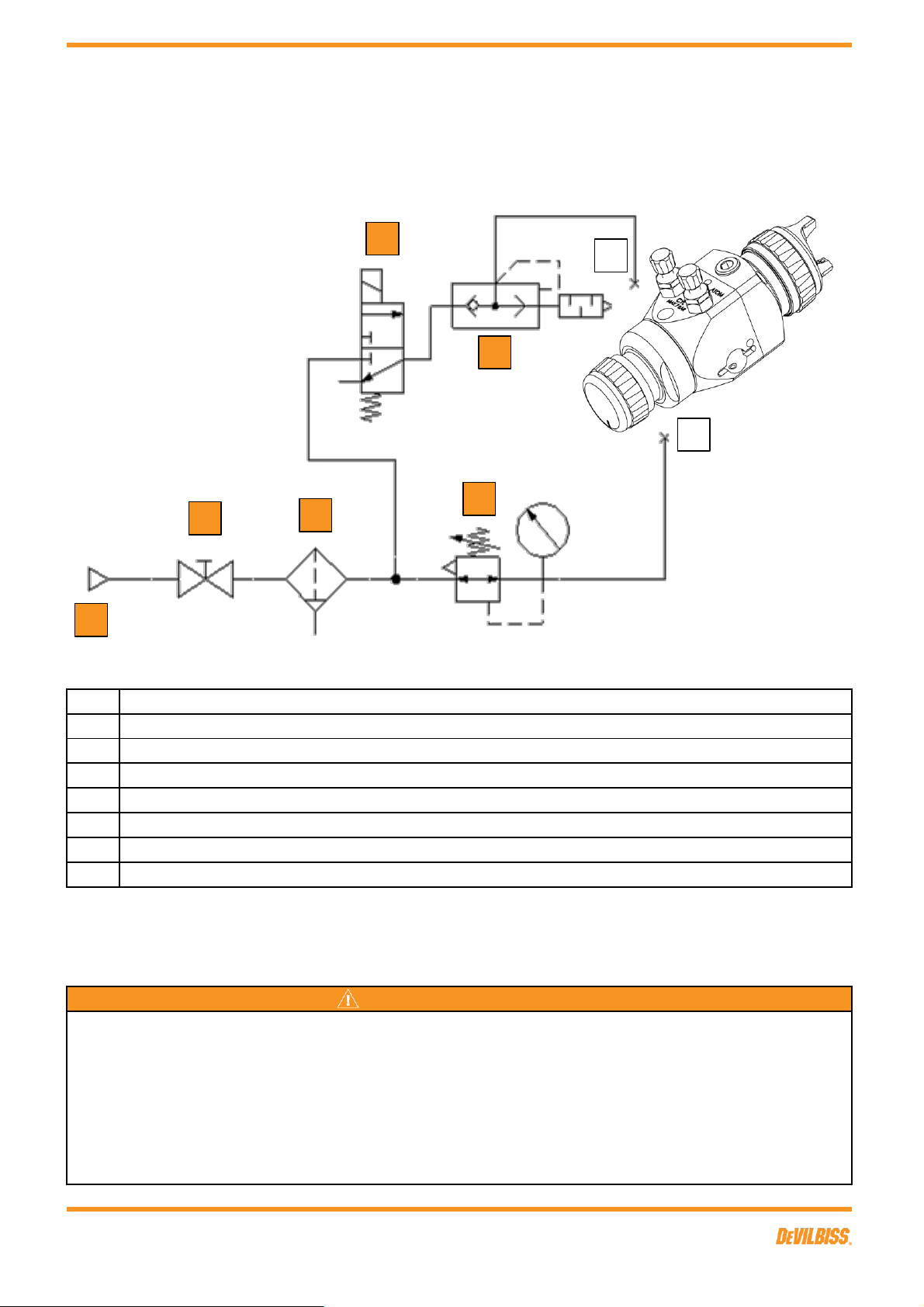
TYPICAL AIR CONNECTION SCHEMATIC
3/2 solenoid valve, normally closed
The spray gun must be earthed to dissipate any electrostatic charges which may be created by fluid
or air flows. This can be achieved through the spray gun mounting, or conductive air/fluid hoses.
Electrical bond from the spray gun to earth should be checked and a resistance of less than 10⁶ Ohms
is required.
Quick exhaust valve & silencer