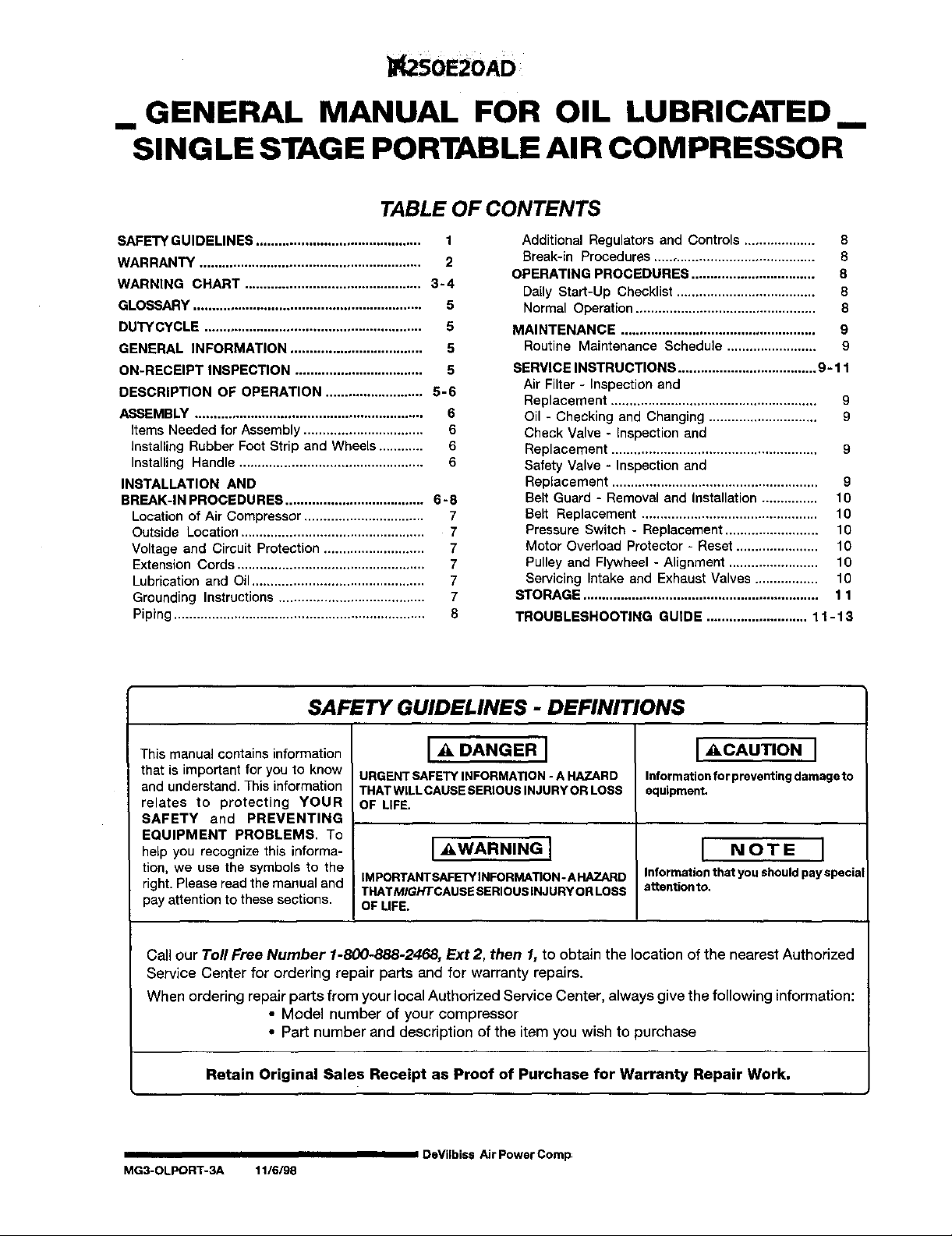
50E2OAD
GENERAL MANUAL FOR OIL LUBRICATED
SINGLE STAGE PORTABLE AIR COMPRESSOR
TABLE OF CONTENTS
SAFETY GUIDELINES ............................................ 1
WARRANTY ........................................................... 2
WARNING CHART ............................................... 3-4
GLOSSARY ............................................................. 5
DUTYCYCLE .......................................................... 5
GENERAL INFORMATION ................................... 5
ON-RECEIPT INSPECTION .................................. 5
DESCRIPTION OF OPERATION .......................... 5-6
ASSEMBLY ............................................................. 6
Items Needed for Assembly ................................ 6
Installing Rubber Foot Strip and Wheels ............ 6
Installing Handle ................................................. 6
INSTALLATION AND
BREAK-IN PROCEDURES ..................................... 6-8
Location of Air Compressor ................................ 7
Outside Location ................................................. 7
Voltage and Circuit Protection ........................... 7
Extension Cords .................................................. 7
Lubrication and Oil .............................................. 7
Grounding Instructions ....................................... 7
Piping ................................................................... 8
Additional Regulators and Controls ................... 8
Break-in Procedures ........................................... 8
OPERATING PROCEDURES ................................. 8
Daily Start-Up Checklist ..................................... 8
Normal Operation ................................................ 8
MAINTENANCE .................................................... 9
Routine Maintenance Schedule ........................ 9
SERVICE INSTRUCTIONS ..................................... 9-11
Air Filter - Inspection and
Replacement ....................................................... 9
Oil - Checking and Changing ............................. 9
Check Valve - Inspection and
Replacement ....................................................... 9
Safety Valve - Inspection and
Replacement ....................................................... 9
Belt Guard - Removal and Installation ............... 10
Belt Replacement ............................................... 10
Pressure Switch - Replacement ......................... 10
Motor Overload Protector - Reset ...................... 10
Pulley and Flywheel - Alignment ........................ 10
Servicing Intake and Exhaust Valves ................. 10
STORAGE ............................................................... 11
TROUBLESHOOTING GUIDE ........................... 11- 13
SAFETY GUIDELINES - DEFINITIONS
This manual contains information
that is important for you to know
and understand. This information
relates to protecting YOUR
SAFETY and PREVENTING
EQUIPMENT PROBLEMS. To
he_pyou recognize this informa-
tion, we use the symbols to the
right. Please read the manual and
pay attention to these sections.
URGENTSAFETYINFORMATION-A HAZARD
THATWILLCAUSESERIOUSINJURYOR LOSS
OF LIFE.
IMPORTANTSAFETYINFORMATION-AHAZARD
THATMIGHTCAUSESERIOUSINJURYORLOSS
OF LIFE.
[ _, DANGER J
Informationforpreventingdamageto
equipmenL
a, WARNING ]
Informationthatyoushouldpayspecia
attentionto.
Call our Toll Free Number 1-800-888-2468, Ext 2, then 1,to obtain the location of the nearest Authorized
Service Center for ordering repair parts and for warranty repairs.
When ordering repair parts from your local Authorized Service Center, always give the following information:
• Model number of your compressor
• Part number and description of the item you wish to purchase
Retain Original Sales Receipt as Proof of Purchase for Warranty Repair Work.
DeVilbiss Air Power Comp;
MG3-OLPORT-3A 11/6/98
_CAUTION ]
NOTE I
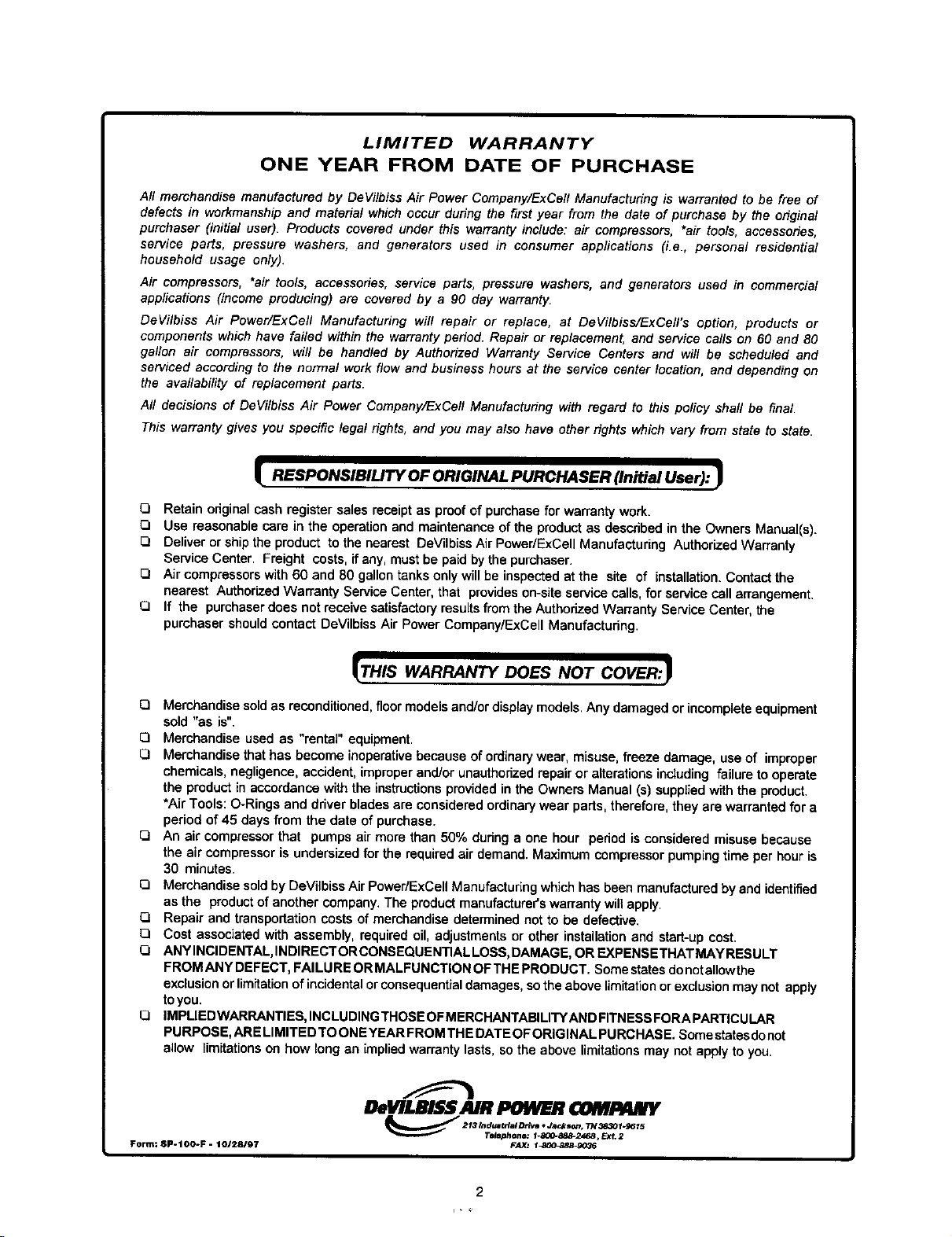
LIMITED WARRANTY
ONE YEAR FROM DATE OF PURCHASE
All merchandise manufactured by DeVilbiss Air Power Company/ExCell Manufacturing is warranted to be free of
defects in workmanship and material which occur during the first year from the date of purchase by the original
purchaser (initial user). Products covered under this warranty include: air compressors, *air tools, accessories,
service parts, pressure washers, and generators used in consumer appficafions (i.e., personal residential
household usage only).
Air compressors, *air tools, accessories, service parts, pressure washers, and generators used in commercial
applications (income producing) are covered by a 90 day warranty.
DeVilbiss Air Power/ExCell Manufacturing will repair or replace, at DeVilbiss/ExCell's option, products or
components which have failed within the warranty period. Repair or replacement, and service calls on 60 and 80
gallon air compressors, will be handled by Authorized Warranty Service Centers and will be scheduled and
serviced according to the normal work flow and business hours at the service center location, and depending on
the ava#ability of replacement parts.
All decisions of DeVilbiss Air Power Company/ExCell Manufactudng with regard to this policy shall be final.
This warranty gives you specific legal rights, and you may also have other rights which vary from state to state.
( RESPONSIBILITYOF ORIGINAL PURCHASER (Ini_al User): J
{3 Retain onginal cash register sales receipt as proof of purchase for warranty work.
[3 Use reasonable care in the operation and maintenance of the product as described in the Owners Manual(s)•
Q Deliver or ship the product to the nearest DeVilbiss Air Power/ExCell Manufacturing Authorized Warranty
Service Center. Freight costs, if any, must be paid by the purchaser.
[3 Air compressors with 60 and 80 gallon tanks only will be inspected at the site of installation. Contact the
nearest Authorized Warranty Service Center, that provides on-site service calls, for service cell arrangement.
[3 If the purchaser does not receive satisfactory results from the Authorized Warranty Service Center. the
purchaser should contact DeVilbiss Air Power Company/ExCell Manufacturing.
(THIS WARRANTY DOES NOT COVER:J
[3 Merchandise sold as reconditioned,floormodels and/ordisplay models. Any damaged or incompleteequipment
sold"as is".
O Merchandise used as "rental" equipment.
Merchandisethat has become inoperativebecause ofordinarywear, misuse, freeze damage, use of improper
chemicals, negligence, accident, improperand/or unauthorizedrepair or alterationsincluding failure to operate
the product in accordance with the instructionsprovidedin the Owners Manual (s) supplled with the product.
*Air Tools: O-Rings and driver bladesare considered ordinarywear parts, therefore, they are warranted for a
period of45 days from the date of purchase.
[3 An air compressorthat pumps air more than 50% duringa one hour period is considered misuse because
the air compressoris undersized for the requiredair demand. Maximum compressorpumping time per hour is
30 minutes.
[3 Merchandisesold by DeVilbiss Air Power/ExCell Manufacturing whichhas been manufactured by and identified
as the productof another company. The productmanufacturers warranty will apply.
[3 Repair and transportationcosts of merchandise determinednot to be defective.
_1 Cost associated with assembly, required oil, adjustments or other installationand start-upcost.
[3 ANYINCIDENTAL, INDIRECTORCONSEQUENTIAL LOSS,DAMAGE, OR EXPENSETHATMAYRESULT
FROM ANY DEFECT, FAILURE OR MALFUNCTION OF THE PRODUCT. Some statesdonotallowthe
exclusion orlimitationof incidentalorconsequential damages, sothe above limitationorexclusion may not apply
toyou.
[3 IMPLIEDWARRANTIES, INCLUDING THOSE OFMERCHANTABILITYAND FITNESS FORA PARTICULAR
PURPOSE, ARE LIMITED TO ONEYEAR FROM THE DATEOF ORIGINAL PURCHASE. Somestatesdonot
allow limitations on how longan implied warranty lasts, sothe above limitationsmay not apply to you.
DeWLBISS AIR POWEB €_/IPAI_
Form: $P-IOO-F - 10/281@7
FAX: 14_O_8-9036
2
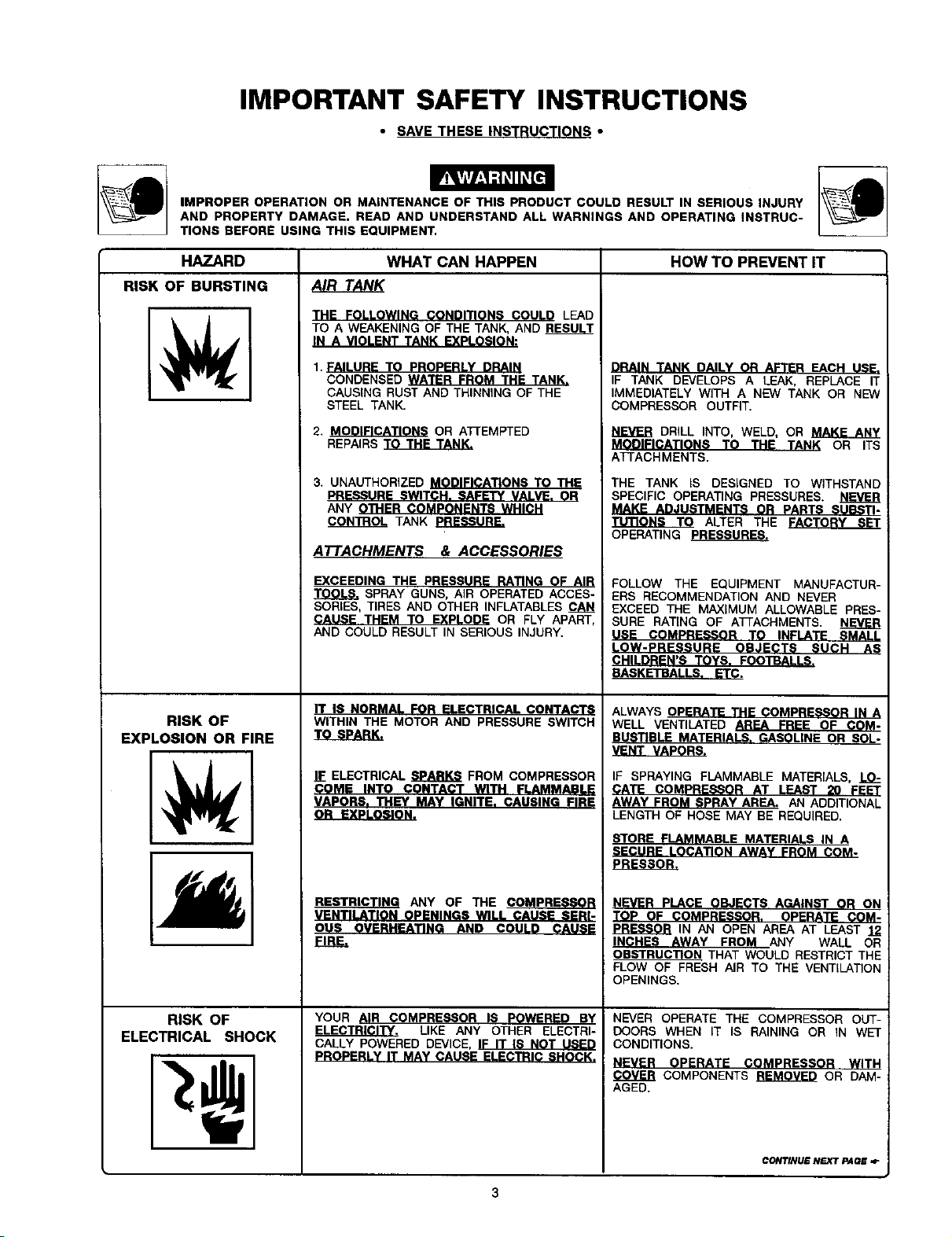
IMPORTANT SAFETY INSTRUCTIONS
• SAVE THESE INSTRUCTIONS •
¥I__
IMPROPER OPERATION OR MAINTENANCE OF THIS PRODUCT COULD RESULT IN SERIOUS INJURY
AND PROPERTY DAMAGE. READ AND UNDERSTAND ALL WARNINGS AND OPERATING INSTRUC-
TIONS BEFORE USING THIS EQUIPMENT.
HAZARD
RISK OF BURSTING
RISK OF
EXPLOSION OR FIRE
WHAT CAN HAPPEN
A/RTANK
THE FOLLOWING CONDITIONS COULD LEAD
TO A WEAKENING OF THE TANK, AND RESULT
IN A VIOLENT TANK EXPLOSION:
1.FAILURE TO PROPERLY DRAIN
CONDENSED]_
CAUSING RUST AND THINNING OF THE
STEEL TANK.
2. MODIFICATIONS OR ATTEMPTED
REPAIRS TO THE TANK.
3. UNAUTHORIZED MODIFICATIONS TO THE
PRESSURE SWITCH. SAFETY VALVE. OR
ANY OTHER COMPONENTS WHICH
CONTROL TANK
ATTACHMENTS & ACCESSORIES
EXCEEDING THE PRESSURE RATING OF AIR
SORIES, TIRES AND OTHER INFLATABLES CAN
AND COULD RESULT IN SERIOUS INJURY.
IT IS NORMAL FOR ELECTRICAL CONTACTS
WITHIN THE MOTOR AND PRESSURE SWITCH
IF ELECTRICALSPARKS FROM COMPRESSOR
COME INTO CONTACT WITH FLAMMABLE
VAPORS. THEY MAY IGNITE. CAUSING RRE
SPRAY GUNS, AIR OPERATED ACCES-
OR FLY APART,
HOW TO PREVENT IT
DRAIN TANK DALLY OR AFTER EACH USE.
IF TANK DEVELOPS A LEAK, REPLACE IT
IMMEDIATELY WITH A NEW TANK OR NEW
COMPRESSOR OUTFIT.
MODIFICATIONS TO THE TANK OR ITS
ATTACHMENTS.
THE TANK iS DESIGNED TO WITHSTAND
SPECIFIC OPERATING PRESSURES. NEVER
MAKE ADJUSTMENTS OR PARTS SUBST!-
TUTIONS TO ALTER THE FACTORY SET
OPERATING PRESSURES,
FOLLOW THE EQUIPMENT MANUFACTUR-
ERS RECOMMENDATION AND NEVER
EXCEED THE MAXIMUM ALLOWABLE PRES-
SURE RATING OF A1TACHMENTS.
USE COMPRESSOR TO INFLATE _MhLL
LOW-PRESSURE OBJECTS SUCH AS
CHILDREN'S TOYS. FOO11BALLS.
BASKETBALLS. ETC.
ALWAYS OPERATE THE COMPRESSOR IN A
WELL VENTILATED O -
BUSTIBLE MATERIALS. GASOLINE OR SOL-
VENT VAPORS.
IF SPRAYING FLAMMABLE MATERIALS, LO-
CATE COMPRESSOR AT LEAST 20 F!_l_T
AWAY FROM SPRAY AREA. AN ADDITIONAL
LENGTH OF HOSE MAY BE REQUIRED.
STORE FLAMMABLE MATERIALS IN A
SECURE LOCATION AWAY FROM COM-
DRILL INTO, WELD, OR
PRSSSOR.
RISK OF
ELECTRICAL SHOCK
RESTRICTING ANY OF THE COMPRESSOR
VENTILATION OPENINGS WILL CAUSE SERI-
OUS OVERHEATING AND COULD CAUSE
FIRE.
YOUR AIR COMPRESSOR IS POWERED BY
ELE_ LIKE ANY OTHER ELECTRI-
CALLY POWERED DEVICE, IF IT IS NOT USED
PROPERLY IT MAY CAUSE ELECTRIC SHOCK,
NEVER PLACE OBJECTS AGAINST OR ON
TOP OF COMPRESSOR, OPERATE COM-
PRESSOR IN AN OPEN AREA AT LEAST 12
INCHES AWAY FROM ANY WALL OR
OBSTRUCTION THAT WOULD RESTRICT THE
FLOW OF FRESH AIR TO THE VENTILATION
OPENINGS.
NEVER OPERATE THE COMPRESSOR OUT-
DOORS WHEN IT IS RAINING OR IN WET
CONDITIONS.
NEVER OPERATE COMPRESSOR WITH
COVER COMPONENTS BF.M_OR DAM-
AGED.
CONTINUE NEXT PAGE _"
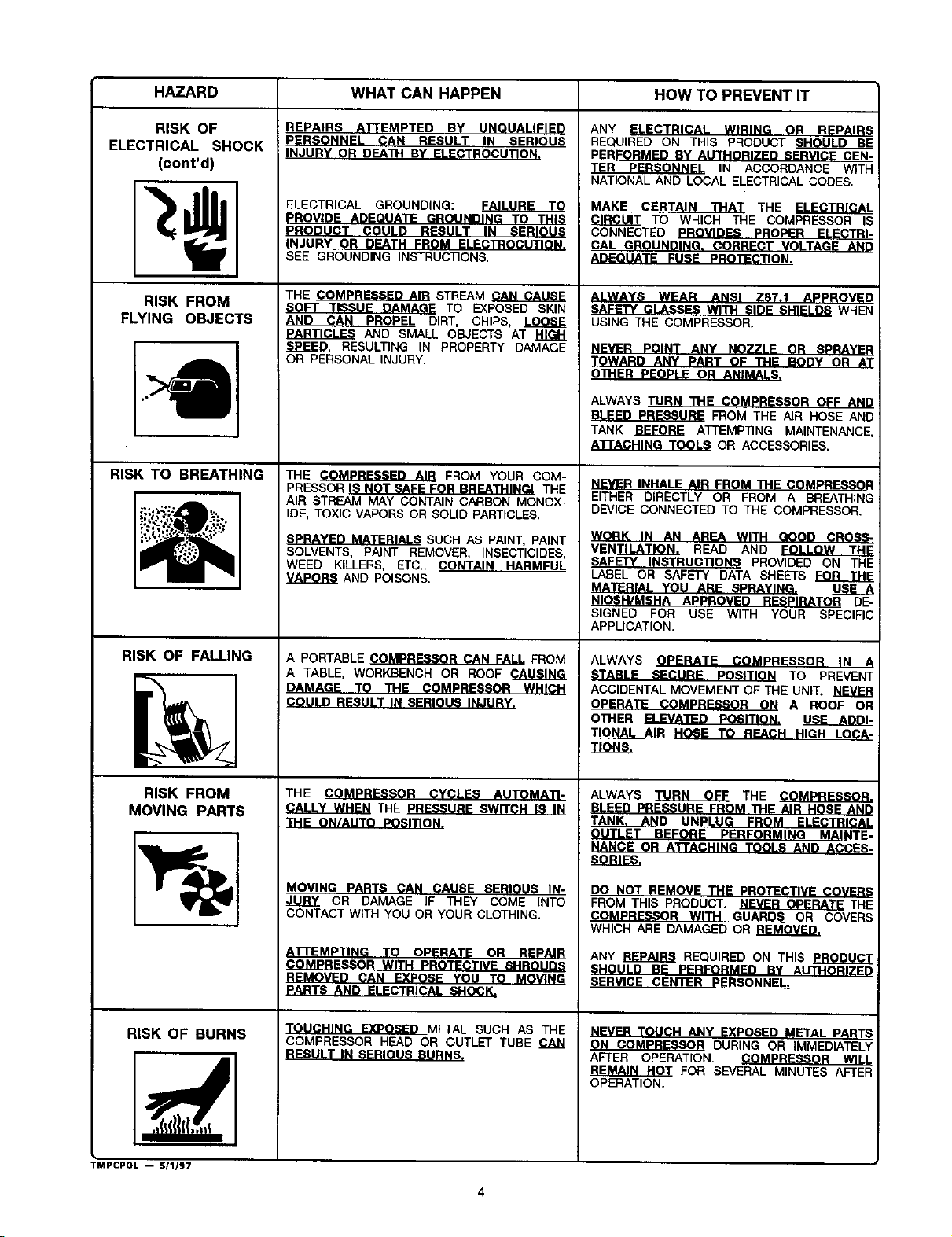
HAZARD WHAT CAN HAPPEN HOW TO PREVENT IT
RISK OF
ELECTRICAL SHOCK
(cont'd)
RISK FROM
FLYING OBJECTS
RISK TO BREATHING
_., t1
REPAIRS ATTEMPTED BY UNQUALIFIED
PERSONNEL CAN RESULT IN SERIOUS
INJURY OR DEATH BY ELECTROCU_ON.
ELECTRICAL GROUNDING:
PROVIDE ADEQUATE GROUNDING TO THIS
PRODUCT COULD RESULT IN SERIOUS
INJURY OR DEATH FROM ELECTROCUTION.
SEE GROUNDING INSTRUCTIONS,
THE COMPRESSED AIR STREAM _._
SOFT TISSUE DAMAGE TO EXPOSED SKIN
AND CAN PROPEL DIRT, CHIPS,
_O_F_, RESULTING IN PROPERTY DAMAGE
OR PERSONAL INJURY.
THE _ FROM YOUR COM-
PRESSOR_ THE
AIR STREAM MAY CONTAIN CARBON MONOX-
IDE, TOXIC VAPORS OR SOLID PARTICLES.
SPRAYED MATERIALS SUCH AS PAINT, PAINT
SOLVENTS, PAINT REMOVER, INSECTICIDES,
WEED KILLERS, ETC.. CONTAIN HARMFUL
Y_ AND POISONS.
AND SMALL OBJECTS AT HIGH
ANY ELECTRICAL WIRING OR REPAIRS
REQUIRED ON THIS PRODUCT SHU_
PERFORMED BY AUTHORIZED SERVICE CEN-
R_ IN ACCORDANCE WITH
NATIONAL AND LOCAL ELECTRICAL CODES.
MAKE CERTAIN THAT THE ELECTRIC__L
_._ TO WHICH THE COMPRESSOR IS
CONNECTED PROVIDES PROPER ELECTRI-
CAL GROUNDING. CORRECT VOLTAGE AND
ADEQUATE FUSE PROTECTION.
ALWAYS WEAR ANSI Z87.1 APpIROVED
SAFETY GLASSES WITH SIDE SHIELDS WHEN
USING THE COMPRESSOR.
NEVER POINT ANY NOZZLE OR SPRAYEF
TOWARD ANY PART OF THE BODY OR AT
OTHER PEOPLE OR ANIMALS,
ALWAYS TURN THE COMPRESSOR OFF AND
TANK BEFORE ATTEMPTING MAINTENANCE
A1-FACHING TOOLS OR ACCESSORIES.
NEVER INHALE AIR FROM THE COMPRESSOF
EITHER DIRECTLY OR FROM A BREATHING
DEVICE CONNECTED TO THE COMPRESSOR.
WORK IN AN AREA WITH GOOD CROSS-
VENTILATION, READ AND FOLLOW THE
SAFETY INSTRUCTIONS PROVIDED ON THE
LABEL OR SAFETY DATA SHEETS
MATERIAL YOU ARE SPRAYING. U_
NIOSH/MSHA APPROVED RESPIRATOR DE-
SIGNED FOR USE WITH YOUR SPECIFIC
APPLICATION.
FROM THE AIR HOSE AND
RISK OF FALLING
RISK FROM
MOVING PARTS
RISK OF BURNS
A PORTABLE COMPRESSOR CAN FALL FROM
A TABLE, WORKBENCH OR ROOF CAUSING
DAMAGE TO THE COMPRESSOR WHICH
COULD RESULT IN SERIOUS INJURy,
THE COMPRESSOR CYCLES AUTOMATI-
_._ THE PRESSURE SWITCH IS IN
MOVING PARTS CAN CAUSE SERIOUS IN-
_J_ OR DAMAGE JE THEY COME INTO
CONTACT WITH YOU OR YOUR CLOTHING.
ATTEMPTING TO OPERATE OR REPAIR
COMPRESSOR WITH PROTECTIVE SHROIInR
REMOVED CAN EXPOSE YOU TO MOVING
PARTS AND ELECTRICAL SHOCK,
_METAL SUCH AS THE
COMPRESSOR HEAD OR OUTLET TUBE CAN
ALWAYS OPERATE COMPRESSOR IN A
ACCIDENTAL MOVEMENT OF THE UNIT,
O _= A ROOF OR
OTHER _=EY_ U_-
TIO_P__NJ_=_AIRHOSE TO REACH HIGH LOC/_-
TIONS.
ALWAYS TURN OFF THE _O_
BLEED PRESSURE FROM THE AIR HOSE AMn
TANK. AND UNPLUG FROM ELECTRICAl
OUTLET BEFORE PERFORMING MAINTE-
NANCE OR ATTACHING TOOLS AND ACCES-
DO NOT REMOVE THE PROTECTIVE COVERS
FROM THIS PRODUCT. _ THE
COMPRESSOR WITH GUARDS OR COVERS
WHICH ARE DAMAGED OR BF,,MQ._ED=
ANY REPAIRS REQUIRED ON THIS PRODUCT
SHOULD BE PERFORMED BY AUTHORi7Fn
SERVICE CENTER PERSONNEL-
NEVER TOUCH ANY EXPOSED METAL PARTS
C_ DURING OR IMMEDIATELY
AFTER OPERATION. .._
EB_ FOR SEVERAL MINUTES AFTER
OPERATION.
TO PREVENT
TMPCPOL -- 5/1197
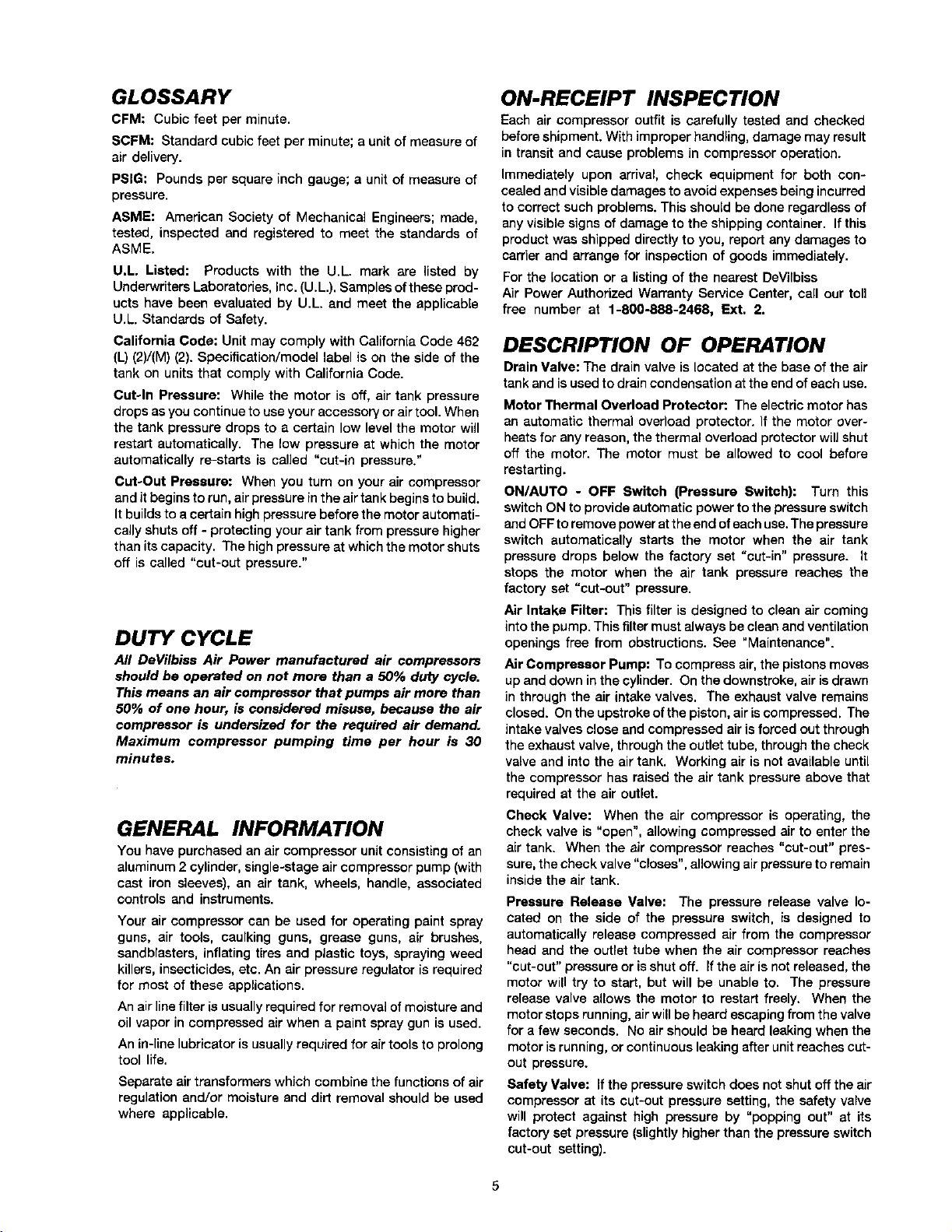
GLOSSARY
CFM: Cubic feet per minute.
SCFM: Standard cubic feet per minute; a unit of measure of
air delivery.
PSIG: Pounds per square inch gauge; a unit of measure of
pressure.
ASME: American Society of Mechanical Engineers; made,
tested, inspected and registered to meet the standards of
ASME.
U.L. Listed: Products with the U.L. mark are listed by
Underwriters Laboratories, Inc. (U.L.). Samples of these prod-
ucts have been evaluated by U.L. and meet the applicable
U.L Standards of Safety.
California Code: Unit may comply with California Code 462
(L) (2)/(M) (2). Specification/model label is on the side of the
tank on units that comply with California Code.
Cut-In Pressure: While the motor is off, air tank pressure
drops as you continue to use your accessory or airtool. When
the tank pressure drops to a certain low level the motor will
restart automatically. The low pressure at which the motor
automatically re-starts is called "cut-in pressure."
Cut-Out Pressure: When you turn on your air compressor
and it begins to run, air pressure in the airtank begins to build.
It buildsto a certain high pressure before the motor automati-
cally shutsoff - protecting your air tank from pressure higher
than itscapacity. The highpressure at which the motor shuts
off is called "cut-out pressure."
DUTY CYCLE
All DeVilbiss Air Power manufactured air compressors
should be operated on not more than a 50% duty cycle.
This means an air compressor that pumps air more than
50% of one hour, is considered misuse, because the air
compressor is undersized for the required air demand.
Maximum compressor pumping time per hour is 30
minutes.
GENERAL INFORMATION
You have purchased an air compressor unit consisting of an
aluminum 2 cylinder, single-stage air compressor pump (with
cast iron sleeves), an air tank, wheels, handle, associated
controls and instruments.
Your air compressor can be used for operating paint spray
guns, air tools, caulking guns, grease guns, air brushes,
sandblasters, inflating tires and plastic toys, spraying weed
killers, insecticides, etc. An air pressure regulator isrequired
for most of these applications.
An airlinefilter is usually required for removal ofmoisture and
oil vapor in compressed air when a paint spray gun is used.
An in-line lubricator is usually required for air tools to prolong
tool life.
Separate air transformers which combine the functions of air
regulation and/or moisture end dirt removal should be used
where applicable.
ON-RECEIPT INSPECTION
Each air compressor outfit is carefully tested and checked
before shipment. With improper handling, damage may result
in transit and cause problems in compressor operation.
Immediately upon arrival, check equipment for both con-
cealed and visible damages to avoid expenses being incurred
to correct such problems. This should be done regardless of
any visible signs of damage to the shipping container. If this
product was shipped directly to you, report any damages to
carrier and arrange for inspection of goods immediately.
For the location or a listingof the nearest DeVilbiss
Air Power Authorized Warranty Service Center, call our toll
free number at 1-800-888-2468, Ext, 2.
DESCRIPTION OF OPERATION
Drain Valve: The drain valve is located at the base of the air
tankand is used to drain condensation at the end of each use.
Motor Thermal Overload Protector: The electric motor has
an automatic thermal overload protector. If the motor over-
heatsfor any reason, the thermal overload protector wilJshut
off the motor. The motor must be allowed to cool before
restarting.
ON/AUTO - OFF Switch (Pressure Switch): Turn this
switch ON to provide automatic power to the pressureswitch
andOFF toremove power at the end ofeach use.The pressure
switch automatically starts the motor when the air tank
pressure drops below the factory set "cut-in" pressure. It
stops the motor when the air tank pressure reaches the
factory set "cut-out" pressure.
Air Intake Filter: This filter is designed to clean air coming
intothe pump. Thistilter must always be clean and ventilation
openings free from obstructions. See "Maintenance".
Air Compressor Pump: To compress air, the pistons moves
up anddown in the cylinder. On the downstroke, airis drawn
in through the air intake valves. The exhaust valve remains
closed. On the upstroke ofthe piston, air iscompressed. The
intake valves close and compressed air is forced out through
the exhaust valve, through the outlet tube, through the check
valve and into the airtank. Working air is not available until
the compressor has raised the air tank pressure above that
required at the air outlet.
Check Valve: When the air compressor is operating, the
check valve is "open", allowing compressed air to enter the
air tank. When the air compressor reaches "cut-our' pres-
sure,the check valve "closes", allowing airpressureto remain
inside the air tank.
Pressure Release Valve: The pressure release valve lo-
cated on the side of the pressure switch, is designed to
automatically release compressed air from the compressor
head and the outlet tube when the air compressor reaches
"cut-out" pressure or isshut off. If the airis not released, the
motor will try to start, but will be unable to. The pressure
release valve allows the motor to restart freely. When the
motor stops running,air will be heard escapingfrom the valve
for a few seconds. No air should be heard leakingwhen the
motoris running, or continuous leaking after unitreaches cut-
out pressure.
Safety Valve: If the pressure switch does not shut off the air
compressor at its cut-out pressure setting, the safety valve
will protect against high pressure by "popping out" at its
factory set pressure (slightly higher than the pressure switch
cut-out setting).
5
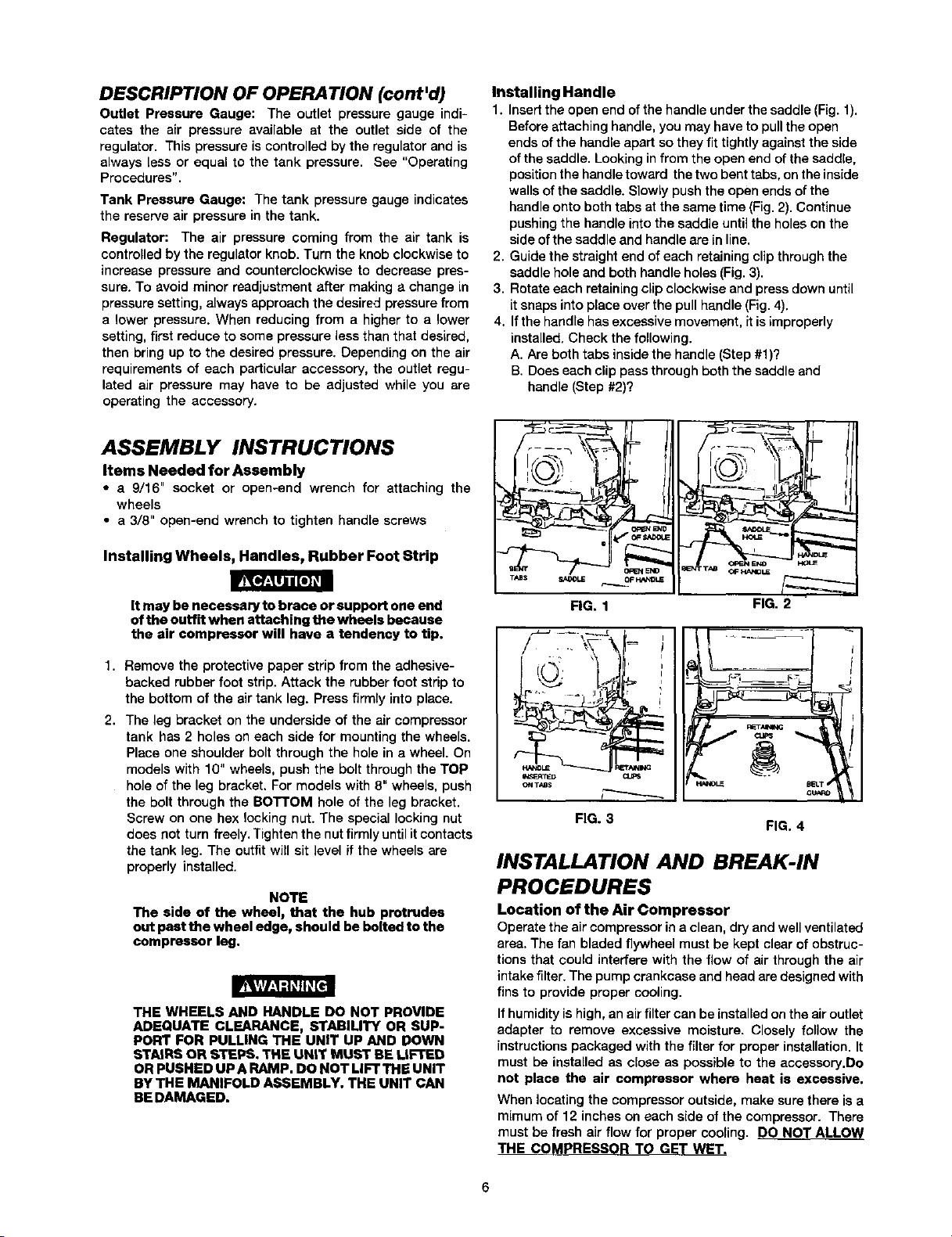
DESCRIPTION OF OPERATION (cont'd)
Outlet Pressure Gauge: The outlet pressure gauge indi-
cates the air pressure available at the outlet side of the
regulator. This pressure is controlled by the regulator and is
always less or equal to the tank pressure. See "Operating
Procedures".
Tank Pressure Gauge: The tank pressure gauge indicates
the reserve air pressure in the tank.
Regulator: The air pressure coming from the air tank is
controlled by the regulator knob. Turn the knob clockwise to
increase pressure and counterclockwise to decrease pres-
sure. To avoid minor readjustment after making a change in
pressuresetting, always approach the desired pressure from
a lower pressure. When reducing from a higher to a lower
setting, first reduce to some pressure less than that desired,
then bring up to the desired pressure. Depending on the air
requirements of each particular accessory, the cutlet regu-
lated air pressure may have to be adjusted while you are
operating the accessory.
ASSEMBLY INSTRUCTIONS
Items Needed for Assembly
• a 9/16" socket or open-end wrench for attaching the
wheels
• a 3/8" open-end wrench to tighten handle screws
Installing Handle
1. Insert the open end of the handle under the saddle (Fig. 1).
Before attaching handle, you may have to pullthe open
ends of the handle apart so they fit tightly against the side
ofthe saddle. Lookingin from the open end of the saddle,
positionthe handle toward the two bent tabs, onthe inside
wallsof the saddle. Slowly push the open ends of the
handle onto both tabs at the same time (Fig.2). Continue
pushing the handle into the saddle untilthe holes on the
side of the saddle and handle are inline.
2. Guide the straight end ofeach retaining clip through the
saddle hole and both handle holes (Fig.3).
3. Rotate each retainingc_ipclockwise and press down until
it snaps intoplace overthe pullhandle (Fig. 4).
4. If the handle hasexcessive movement, it isimproperly
installed,Check the following.
A. Are both tabs insidethe handle (Step #1)?
B. Does each clip passthrough both the saddle and
handle (Step #2)?
Installing Wheels, Handles, Rubber Foot Strip
It may be necessary to brace or support one end
of the outfit when attaching the wheels because
the air compressor will have a tendency to tip.
1. Remove the protective paper strip from the adhesive-
backed rubber foot strip. Attack the rubber foot strip to
the bottom of the air tank leg. Press firmly into place.
2. The leg bracket on the underside of the air compressor
tank has 2 holes on each side for mounting the wheels.
Place one shoulder bolt through the hole in a wheel. On
models with 10" wheels, push the bolt through the TOP
hole of the leg bracket. For models with 8" wheels, push
the bolt through the BOTTOM hole of the leg bracket.
Screw on one hex locking nut. The special locking nut
does not turn freely. Tighten the nut firmly until it contacts
the tank leg. The outfit will sit level if the wheels are
properly installed.
NOTE
The side of the wheel, that the hub protrudes
out past the wheel edge, should be bolted to the
compressor leg.
THE WHEELS AND HANDLE DO NOT PROVIDE
ADEQUATE CLEARANCE, STABILITY OR SUP-
PORT FOR PULLING THE UNIT UP AND DOWN
STAIRS OR STEPS. THE UNIT MUST BE UFTED
OR PUSHED UP A RAMP. DO NOT LIFT THE UNIT
BY THE MANIFOLD ASSEMBLY. THE UNIT CAN
BE DAMAGED.
FIG. 1 FIG. 2
L_ ÷
_ IJ_N_
K_NO_ BaTS
FIG. 3
G_
FIG. 4
INSTALLATION AND BREAK-IN
PROCEDURES
Location of the Air Compressor
Operate the air compressor in a clean, dry and well ventilated
area. The fan bladed flywheel must be kept clear of obstruc-
tions that could interfere with the flow of air through the air
intake filter. The pump crankcase and head are designed with
fins to provide proper cooling.
Ifhumidity is high, an air filter can be installed on the airoutlet
adapter to remove excessive moisture. Closely follow the
instructions packaged with the filter for proper installation. It
must be installed as close as possible to the accessory.Do
not place the air compressor where heat is excessive.
When locating the compressor outside, make sure there isa
mimum of 12 inches on each side of the compressor. There
must be fresh air flow for proper cooling. DO NOT ALLOW
THE COMPRESSOR TO GET WET.
6