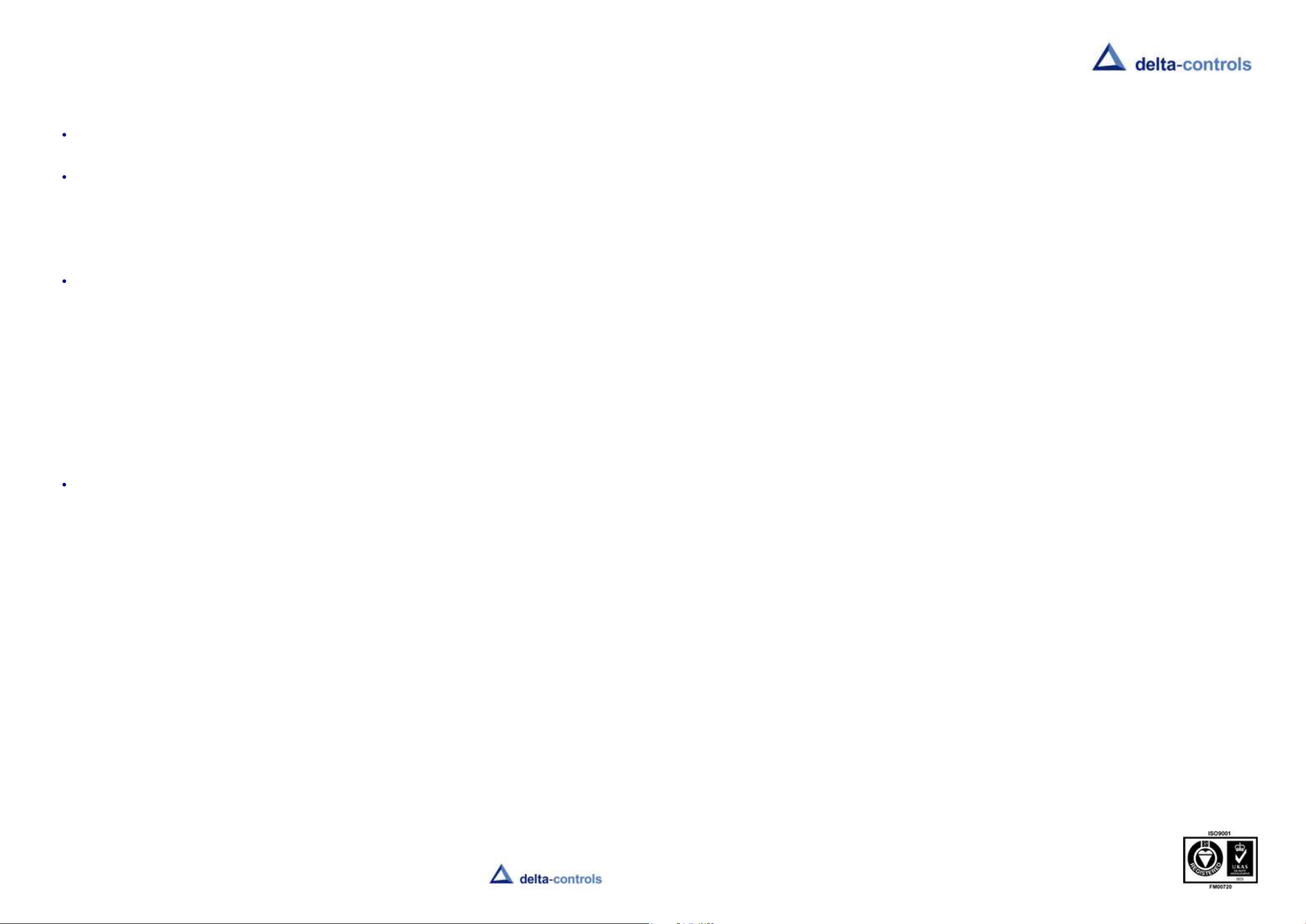
Your trusted partner in process instrumentation
Delta Controls Limited
Island Farm Avenue
West Molesey
Surrey KT8 2UZ, UK
T +44 (0) 20 8939 3500
F +44 (0) 20 8783 1163
E sales@delta-controls.com
W www.delta-controls.com
How can we help you?
Technical Datasheets and IOM Instructions for all Delta
Controls' pressure and temperature measurement
products are available from our website at www.deltacontrols.com.
For Service and Repair enquiries, please contact the
Switch, Transmitter or Temperature Sales Engineering
Teams on +44 (0)20 8939 3500 or visit www.deltaexpress.biz to buy selected Switch spares kits on-line.
DIRECTIVES
The following Directives are also relevant to this product:
EMC Directive 89/336 amended by 93/68/EEC
Not applicable to this product.
Pressure Equipment Directive (PED) 97/23/EC
This product is a 'Pressure Accessory' as defined by the
Pressure Equipment Directive 97/23/EC and the UK Pressure
Equipment Regulations 1999. The connection size <=DIN25
and is therefore manufactured to Sound Engineering Practice
(Art.3 (3)) and is not CE marked. The product, however, will
be CE marked for LVD or ATEX.
Low Voltage Directive (LVD) 2006/95/ECamended by
93/68/EEC
The product is in conformity with the following relevant
standards or parts thereof.
EN 60947-1:1992
Low Voltage Switchgear and Controlgear – General Rules
EN 60947- 5-1:1992
Low Voltage Switchgear and Controlgear – Devices and
Switching Elements
EN 60529:1991
Specification for Classification of Degrees of Protection
provided by Enclosures
BS 6134:1991
Specification for Pressure and Vacuum Switches
Intrinsic Safety
Pressure switches neither store nor generate energy and can
therefore be considered as ‘intrinsically safe’. When used
with a certified barrier
Installation, Operating and
Maintenance Instructions
Diaphragm Actuated
Pressure Switch
Series VM
IOM.VM-SERIES.V2-09/2010
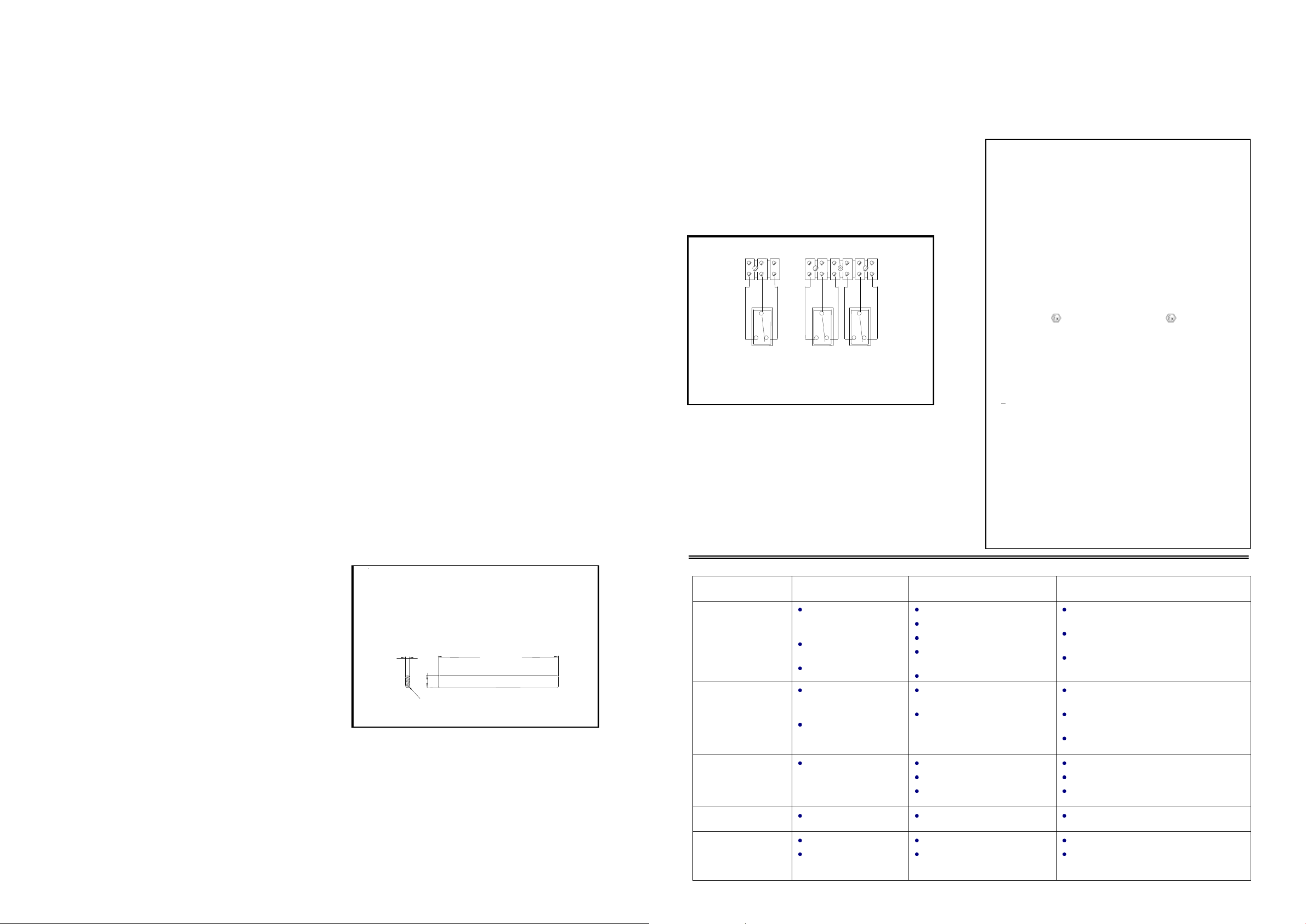
ALL Dimensions mm (inches)
To remove enclosure lid, loosen lid locking screw. Where lid is
tight, use a flat bar - refer to recommended sizes below. Material
needs to be hard chrome steel spanner grade.
The edge of a spanner may be used.
SAFETY FACTORS THAT MAY AFFECT PRODUCT:
Potential Effect of
Failure
Potential Cause(s) of Failure
Switch does not
respond to pressure
change
Leakage of process
medium into housing
Blow-out vent operates
Over-pressured
Poor weld
Material defect
Incompatible process/wetted
parts materials
Metal fatigue
Ensure process pressure is within the
switches limits
Ensure the wetted part materials of the
switch are compatible with the process
Ensure the pressure switches rated lifespan
of 100,000 operations is not exceeded
Process connection
weld failure
Switch does not
respond to pressure
change
Leakage of process
medium into housing
Incompatible process/wetted
parts materials
Switch has been over-
pressurised
Ensure process pressure is within the
switches limits
Ensure the wetted part materials of the
switch are compatible with the process
Ensure the pressure switches rated lifespan
of 100,000 operations is not exceeded
Moisture ingress
Incorrect voltage applied
Mechanical failure
Check integrity of seals, glands etc
Check electrical ratings on switch label
Ensure the pressure switches rated lifespan
of 100,000 operations is not exceeded
Seizure of
mechanical assembly
Moisture ingress leading to
corrosion
Check integrity of seals, glands etc
Process connection
thread mismatched
Process medium leaks
Thread is visibly
damaged
Incorrect fittings used
Care not taken when
assembling process connection
thread
Take care to only use correctly sized fittings
Ensure thread is not crossed during
assembly
DECLARATION OF CONFORMITY
Description
Flameproof Pressure, comprising a housing in cast stainless
steel with an integral spring and venting chamber to which is
attached a process sensor. Process changes applied to the
sensor move a push rod, which passes through the enclosure
wall to actuate one or two microswitches.
As the manufacturers of the apparatus, listed, we declare under
our sole responsibility that the products listed below: Pressure
switch series Volume to which this declaration relates are in
conformity with the following relevant harmonised standards:-
EN 50014:1997+Amds 1 & 2 EN 50018:2000
EEx d IIC T85 II 2 GD or EEx d IIC T100 II 2 GD
T85 Tamb -60 degC to +65 degC and T100 -60 degC to +80
degC
Certified by Notified Body ITS Ltd in accordance with Article 9
of the Council Directive 94/9/EC.
EC-TYPE EXAMINATION CERTIFICATE
No ITS03ATEX11510X
And thereby, conforms to the requirements of the ATEX Directive
94/9/EC.
Signed
………………………………………
R. Harrison
Managing Director 4/1/2005
GENERAL
The unit is manufactured, checked and supplied in accordance
with our published specification and, when installed and used in
normal or prescribed applications with the lid in place and within
the parameters set for mechanical and electrical performance, will
not cause danger or hazard to life or limb.
HEALTH AND SAFETY AT WORK ACT 1974
WARNINGS
1. THE USER'S ATTENTION IS DRAWN TO THE FACT THAT, WHEN
THE UNIT IS ‘LIVE’ WITH RESPECT TO ELECTRICAL OR
PRESSURE SUPPLIES, A HAZARD MAY EXIST IF THE UNIT IS
OPENED OR DISMANTLED.
2. UNITS MUST BE SELECTED AND INSTALLED BY SUITABLY
TRAINED AND QUALIFIED PERSONNEL IN ACCORDANCE WITH
APPROPRIATE CODES OF PRACTICE SO THAT THE POSSIBILITY
OF FAILURE RESULTING IN INJURY OR DAMAGE CAUSED BY
MISUSE OR MISAPPLICATION IS AVOIDED.
OPERATING PRINCIPLES
Process pressure is sensed by a diaphragm that generates a force
proportional to the applied pressure. This force is opposed by an
adjustable spring that, at the point of equilibrium, permits
movement of an operating rod which actuates a switch or switches.
Note: Should the diaphragm fail the process will vent to
atmosphere via a control orifice without pressurising the switch
enclosure.
INSTALLATION
The instrument is designed to be mounted vertically with the
process connection underneath. However, mounting up to 45°
from the vertical in any plane is acceptable, although a small
calibration shift may occur. The instrument can be mounted either
direct to process, or to a wall or panel, using the four mounting
holes provided. Select the mounting point so as to avoid excessive
shock, vibration or temperature fluctuation. Instruments should be
mounted to avoid excessive heat transfer from the process lines or
adjacent plant. To avoid undue stresses being imparted to the
instrument when wall or panel mounted, it is recommended that a
short length of flexible line be installed between the instrument and
process line.The terminal strip is designed to be pulled out to
Assist wiring up.
Take care to select and install adaptors to the electrical entry that
do not reduce the enclosure degree of protection.
Use a spanner to support the process connection when fitting the
instrument. When fitting the instrument lid, make sure the ‘O’ ring
is in good condition and fitted correctly.
References for Selection and Installation
BS EN 60079-14:1997
BS EN 60529:1992 IEC 529 IP RATING (Ingress Protection)
Standards Applied to Product (Enclosure Code R)
EN 50014:1997 + Amendments 1 and 2
EN 50018:2000 CENELEC.
Temperature Classification (Enclosure Code R)
T85 deg c T
-60oC to +65oC and T100 deg c -60oC to +80oC.
amb
Product Code
First Character: Enclosures
R - Stainless steel flameproof enclosure for use in Zone 1
A - Stainless steel ‘weatherproof’
Second and Third Characters: Type
VM - Type of Pressure Switch
Installation of Electrical Adaptors and Cable Glands to the
Electrical Entry
Take care to select and install adaptors to the electrical entry that
do not reduce the enclosure's degree of protection for use in Zone
1 Hazardous Areas. The product code at character 4 indicates the
size and type of thread. The most common thread supplied is ISO
M20 x 1.5. Other non-ISO and tapered threads will have the size
and type stamped next to the entry.
FAILURE TO OBSERVE THESE REQUIREMENTS WILL
RENDER THE INSTALLATION UNSAFE!
Number of Entries
The electrical entry is normally on the right hand side. Optional
entry in the top may be supplied. On Enclosure Code R, cable
entry holes are provided for the accommodation of ATEX certified
flameproof cable entry devices, with or without interposition of a
suitably certified flameproof thread adapter.
Unused Entries (Enclosure Code R)
Unused entries must be fitted with ATEX certified flameproof
stopping plugs. Suitable flameproof cable entry devices, thread
adapters and stopping plugs certified as equipment (not a
component) under an EC type examination certificate to directive
94/9/EC may also be used in the manner specified above.
Alternative electrical entry threads that may be supplied to order: 1
electrical entry USAS B2.1 (1968) gauging to clauses 36 & 37 up
to 1/2" NPT.
WARNING FOR ENCLOSURE CODE R: IT IS A SAFETY
REQUIREMENT THAT AT LEAST 5 FULL THREADS ARE
ENGAGED BETWEEN THE ADAPTOR AND CONDUIT ENTRY
WHEN THE UNIT IS IN OPERATION. NEVER OPERATE THE
UNIT UNLESS THIS CONDITION IS MET. ONLY USE GREASES
OR LUBRICANTS WHICH ARE COMPATIBLE WITH THE
ENVIRONMENT AND ENCLOSURE MATERIAL.
Removing Cover/Lid
The enclosure contains potentially sparking contacts so the
cover/lid should never be removed while electrical power is
connected to the switch and/or when a flammable gas is present.
Remove the cover/lid using an appropriate tool if tight, eg: edge of
spanner or metal rod (Fig 1).
Replacing Cover/Lid
Thread, seal and contact surfaces may be lightly lubricated using a
non-setting, non-corrosive grease compatible with the lid seal.
Before connecting to electrical power, screw on cover/lid hand
tight, making sure that mating surfaces of the lid and enclosure are
in contact. Use the locking screw provided to prevent casual and
unauthorised removal of the cover/lid. The enclosure is rated IP66
End of Line Resistors (Enclosure Code R)
Never fit end of line resistors or modify the product without
reference to Delta Controls.
Only operation, maintenance or repair procedures, either contained
herein or approved by Delta Controls, may be used to avoid
rendering the equipment unsafe in operation and/or nullifying the
Certification. NO MODIFICATIONS ARE PERMITTED.
Wire in accordance with local and National codes. Use cables no
larger than 2.5 mm2 (14 AWG). Deliver the electrical connection
through a suitable cable gland which will maintain the IP rating of
the instrument. Insert bare wires fully into the terminal block and
tighten securely. Keep wiring tails to a minimum and check that
wires do not interfere with the operating mechanism. Use the
earthing/grounding points provided. See Fig 2 for wiring details.
OPERATION
Pressure switches are supplied calibrated against falling pressure
unless otherwise specified. Set Point adjustment refers to falling
pressure. Switching differential is the difference between the set
point and the operating value on rising pressure.
Set Point Adjustment: Models VM2
1. Isolate the instrument from the process and power.
2. Loosen lid lock screw and remove the lid.
3. Retain in a safe place to avoid damage to threads.
4. Rotate the set point adjuster screw as required. Rotate
clockwise to increase the set point and counter-clockwise to
decrease the set point.Raise/lower the pressure 2-3 times to
ensure stability of setting against a reference gauge.
5. Replace the instrument lid (see Maintenance).
Note: For accurate setting, a suitable pressure gauge must be used
in conjunction with the above procedure. Do not attempt to set the
switch outside the scale limits. Though the unit may be set
anywhere within its operating range, for optimum performance it is
good practice to have a set point value between 25% and 75% of
span.