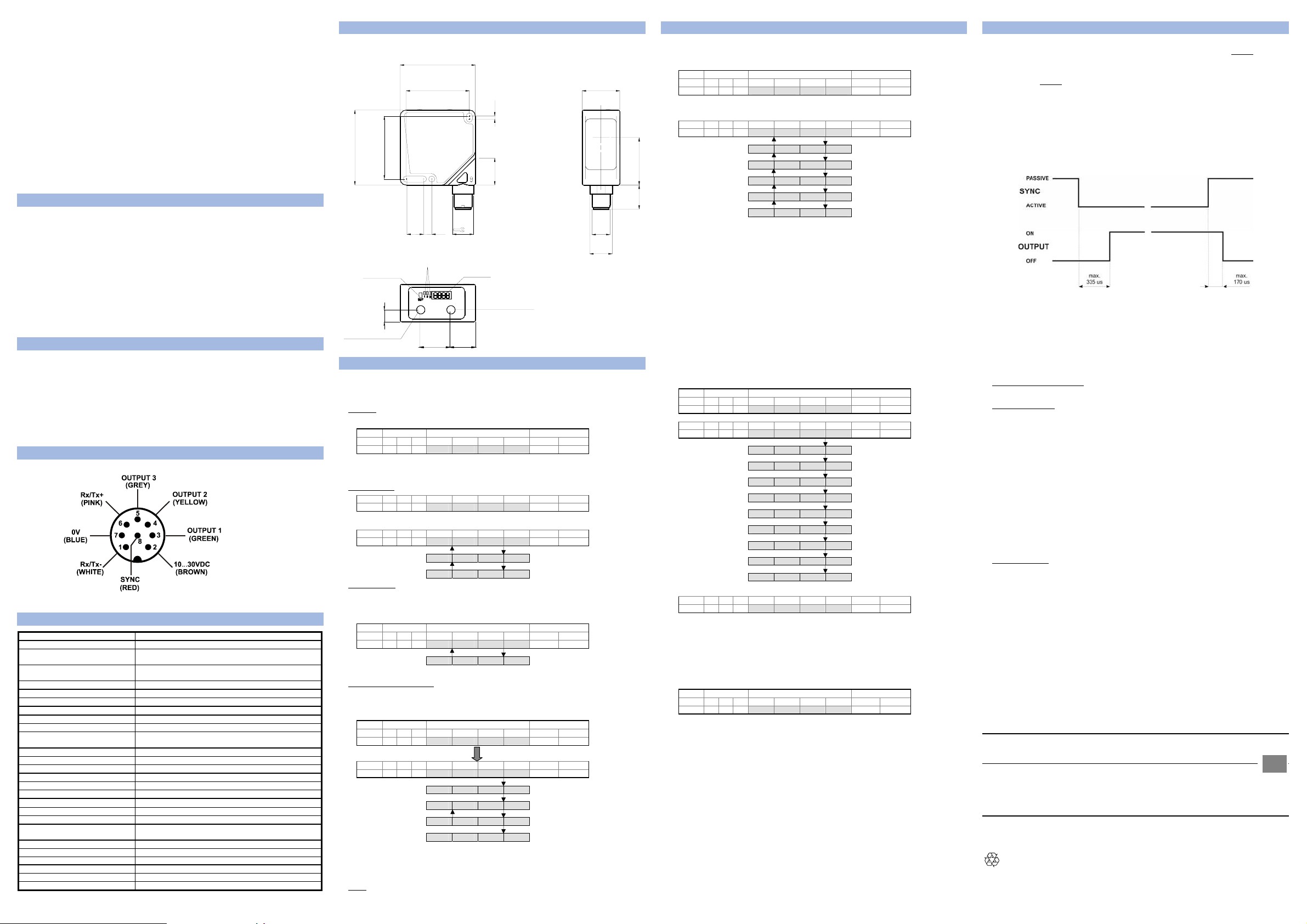
CTi Automation - Phone: 800.894.0412 - Fax: 208.368.0415 - Web: www.ctiautomation.net - Email: info@ctiautomation.net
S65-PA-5-V09
Colour sensor
OUPUT LED
The yellow LED ON indicates the OR function of the three OUT1, OUT2 and OUT3 outputs.
DISPLAY (green 4-digit display)
The display indicates the “run” or “rund” (run with delay) operating mode.
Please refer to the “SETTING” paragraph for the correct setup procedure indications.
OUT1, OUT2, OUT 3 LEDs
The green LED ON indicates that the corresponding output is active.
SET PUSHBUTTON
The pressure on the pushbutton activates the self-setting procedure.
A long pressure on the pushbutton allows the access to the delay setting menu.
SEL PUSHBUTTON
The pressure allows to scroll through the sensor setting parameter menu.
Please refer to the “SETTING” paragraph for the correct setup procedure indications.
The sensor can be mounted by means of the three housing’s
holes using two screws (M4x25 or longer, 1 Nm maximum
tightening torque) with washers. The use of fixing brackets is
recommended if the supporting surface doesn't have a good
planarity. Various orientable fixing brackets to ease the sensor
positioning are available (please refer to the accessories listed in
the catalogue).
The operating distance is measured from the front surface of the
sensor optics.
The M12 connector can be oriented at two different positions
using the specific fastening spring and rotating the block of 180°.
M12 CONNECTOR
*
Available only for version with RS485 serial connection (S65-PA-5-V09-xxxZ).
Power supply: 10 … 30 Vdc limit values
Ripple: 2 Vpp max.
Consumption
(output current excluded):
Outputs: 3 PNP or NPN outputs
Tolerance level: 10 (toL0 - toL9) independent per each channel
Operating mode: C, C+I independent per each channel
Output current: 100 mA max.
Output saturation voltage:
Response time: 335us
Switching frequency: 1.5 KHz
Indicators: 4-digit display (GREEN), OUTPUT LED (YELLOW)
Setting: SET pushbutton, SEL pushbutton
Data retention: EEPROM non volatile memory
Operating temperature: -10 … 55 °C
Storage temperature: -20 … 70 °C
Electrical protection: Class 2
Operating distance (typical values): 20 mm
Minimum spot dimension:
Emission type: white light LED (400-700nm)
Ambient light rejection: according to EN 60947-5-2
Vibrations: 0.5 mm amplitude, 10 … 55 Hz frequency, for every axis
Shock resistance: 11 ms (30 G) 6 shock for every axis (EN60068-2-27)
Housing material: ABS
Lens material: window and lenses in glass
Mechanical protection: IP67
Connections: M12 8-pole connector
Weight: 100 g. max.
INSTRUCTION MANUAL
CONTROLS
INSTALLATION
CONNECTIONS
*
*
TECHNICAL DATA
60 mA max. @ 24Vdc
30 Vdc max. (short-circuit protection)
≤ 2 V
3 OUTPUT STATUS LEDs (GREEN)
∅ 4 mm
(EN60068-2-6)
DIMENSIONS
50
42
25
2
42
50
18x45°
5.5
OUTPUT LED
OUTPUT STATUS
LEDS
SELSET
1411
DISPLAY
SEL PUSHBUTTON
M12
15
mm
7.75
SET PUSHBUTTON
20 17.05
SETTING
The three-phase sensor setting allows the adjustment of the channel, operating mode and tolerance
values.
z pushbutton pressed { pushbutton not pressed
- Detection
Place object to detect inside the operating distance, in front of the sensor.
OUT Display Keyboard
OR 1 2 3 Dig1 Dig2 Dig3 Dig4 SET SEL
- Press the SET pushbutton for at least 2s.
- The “Set1” message is visualised.
- Channel setting
OR 1 2 3 Dig1 Dig2 Dig3 Dig4 SET SEL
- Use the SEL pushbutton to select the channel to detection.
OR 1 2 3 Dig1 Dig2 Dig3 Dig4 SET SEL
- Operating mode
- Press the SET pushbutton again to configure the operating mode.
- Select C (colour) or C+I (colour + intensity) using the SEL pushbutton *.
OUT Display Keyboard
OR 1 2 3 Dig1 Dig2 Dig3 Dig4 SET SEL
- TEACH and tolerance setting
- Press the SET pushbutton again, the “updt” text blinks for 2s.
The sensor then automatically passes into the tolerance selection.
Use the SEL pushbutton to select the required value.
OUT Display Keyboard
OR 1 2 3 Dig1 Dig2 Dig3 Dig4 SET SEL
OR 1 2 3 Dig1 Dig2 Dig3 Dig4 SET SEL
- The “FAIL” text alternated with “Hi” or “Lo” is visualised if the detection is not correct.
- Repeat the procedure starting from the operating mode.
NOTE: The 0, 1, 2 tolerance values are particularly suitable for critical applications.
r u n d
S E t 1
S E t 1
S E t 2
S E t 3
C
C _ I
u p d t
t o L 0
t o L 1
t o L 2
t o L …
t o L 9
z {
{ z
{ z
{ z
{ z
z {
{ z
z {
{ z
{ z
{ z
{ z
{ z
PARAMETER SETTING
Delay value visualisation and setting
OUT Display Keyboard
OR 1 2 3 Dig1 Dig2 Dig3 Dig4 SET SEL
Press the SET pushbutton for at least 6s to access to the delay setting mode.
OR 1 2 3 Dig1 Dig2 Dig3 Dig4 SET SEL
31.6516
At each pressure of the SEL pushbutton, the different delay levels in ms are visualised in a cyclical
manner at the output deactivation and moreover, the relative delay value will be stored.
When the “d-00” message is visualised the operating mode will be “run”, and “rund” in all other cases.
The delay value setting is in common for all three outputs.
When a delay value, differen t from zero, is set the outputs will be maintained active fo r a minimum time,
which is equal to the number of milliseconds visualised on the display.
Channel status visualisation
This function allows a rapid control of the three sensor channel adjustment.
Pressing the SEL pushbutton for at least 2 s the channel, operating mode and tolerance are visualised
in a sequential manner.
r u n d
d - 0 0
d - 0 5
d - 1 0
d - 2 0
d - 3 0
d - 4 0
d-00 = 0 ms
d-05 = 5 ms
d-10 = 10 ms
d-20 = 20 ms
d-30 = 30 ms
d-40 = 40 ms
z {
{ z
{ z
{ z
{ z
{ z
{ z
OUT Display Keyboard
OR 1 2 3 Dig1 Dig2 Dig3 Dig4 SET SEL
OR 1 2 3 Dig1 Dig2 Dig3 Dig4 SET SEL
OR 1 2 3 Dig1 Dig2 Dig3 Dig4 SET SEL
At the end of the sequence the display will indicate the “run” or “rund” operating mode again.
r u n d
C h _ 1
C _ I
t o L 2
C h _ 2
C
t o L 1
C h _ 3
C
t o L 8
d - 0 5
r u n d
z {
{ z
z {
Non-initialised E2PROM
If the display indicates “E2Pr” the sensor does not have any of the three channels initialised.
OUT Display Keyboard
OR 1 2 3 Dig1 Dig2 Dig3 Dig4 SET SEL
In this case it is sufficient to program one single channel to obtain the “run” or “rund” visualisation on the
display.
* The 'C' type algorithm is used to obtain a larger depth of field, or to detect colours on different
opaque, shiny or reflecting surfaces. Whereas the 'C+I' type algorithm offers a higher sensitivity
towards tone variations and is recommended for the detection of different colours on the same type
of material, with the possibility of distinguishing also the grey tones.
E 2 P r
{ {
REMOTE FUNCTIONS
KEYLOCK function (SET pushbutton block)
If at sensor powering the SYNC wire is connected to +Vdc for at least 1s, the keylock function is
activated and the pushbuttons are no longer active.
After the first second, the SYNC input is available for the normal operating modes; if SYNC is high the
outputs are deactivated.
To deactivate the keylock, the sensor has to be turned off and re-powered with the SYNC wire not
connected or ground connected (GND).
SYNC input
The SYNC signal can exactly determine the beginning and end of the colour identification.
The identification cycle begins after the SYNC signal changes from passive to active and the sensor
outputs have to updated after max. 335µs.
All the outputs are deactivated after max. 170µs from an active passage to a passive one.
The connection of the SYNC wire to Vdc corresponds to the passive logic status while SYNC not
connected or connected to 0V corresponds to the active logic status.
(SYNC passive = Vdc ; SYNC active = 0V)
A typical application is a multicoloured target where the colour to detect is in a determinate position,
while the other zones have to be faded out.
Moreover, incorrect detections can be avoided during transition from the target to the background.
RS485 serial connection only for version S65-PA-5-V09-xxxZ
The complete sensor remote control is possible using the RS485 line.
All the functions such as the channel selection, the tolerance selection and the operating mode can be
accessed by means of this serial line.
The serial communication parameters are: 9600 baud, no equity, 8 data bits, 1 stop bit.
All the commands have to be sent via terminal in an ASCII format as follows:
- Receiving of the channel status:
At any moment, the receipt of the ‘r <CR> <LF>’ command indicates the sensor configuration.
- Remote setting mode:
To access to the remote setting mode, the SYNC input has be remain passive for at least 300ms.
The commands available are given below:
@ <CR> <LF> beginning of the remote setting (together with passive SYNC)
cx <CR> <LF> channel selection, with x ∈ {1,2,3}
tx <CR> <LF> tolerance selection, with x ∈ {0,1,2,3,4,5,6,7,8,9}
mx <CR> <LF> operating mode selection, with x ∈ {1,2}
e <CR> <LF> configuration sequence activation.
q <CR> <LF> exit from the remote setting mode without saving configuration.
If the SYNC input is activated before the ‘e’ (execute) command is given, the sensor exits the remote
setting mode without saving the configuration, similarly to the receipt of the ‘q’ (quit) command.
If the SYNC input is active, at the receipt of the @ <CR> <LF> command, the sensor responds with: ??
<CR> <LF>. At the receipt of the q <CR> <LF> or e <CR> <LF> commands, the sensor transmits ok
<CR> <LF>.
The lo <CR> <LF> message is transmitted if the signal is too low and hi <CR> <LF> if the signal is too
high.
- Delay configuration
To access to the delay configuration, the SYNC input has be remain passive for at least 300 ms The
commands available are given below:
@ <CR> <LF> beginning of the delay configuration (together with passive SYNC)
dx <CR> <LF> delay selection, with x ∈ {0,1,2,3,4,5}
e <CR> <LF> memorisation of the new delay value
q <CR> <LF> exit from the delay configuration without saving the configuration.
If the SYNC input is activated before the ‘e’ (execute) command is given, the sensor exits the remote
setting mode without saving the configuration, similarly to the receipt of the ‘q’ (quit) command.
If the SYNC input is active, at the receipt of the @ <CR> <LF> command, the sensor responds with: ??
<CR> <LF>. At the receipt of the q <CR> <LF> or e <CR> <LF> commands, the sensor transmits ok
<CR> <LF>.
NOTE: during the command transmission, the single strings have to follow each other with a
delay of at least 1ms.
DECLARATION OF CONFORMITY
We DATASENSOR S.p.A. declare under our sole responsibility that these products are conform to the
89/336 CEE, 73/23 CEE Directives and successive amendments.
WARRANTY
DATASENSOR S.p.A. warrants its products to be free from defects.
DATASENSOR S.p.A. will repair or replace, free of charge, any product found to be defective during
the warranty period of 36 months from the manufacturing date.
This warranty does not cover damage or liability deriving from the improper application of
DATASENSOR products.
DATASENSOR S.p.A. Via Lavino 265
40050 Monte S. Pietro - Bologna - Italy
Tel: +39 051 6765611 Fax: +39 051 6759324
http://www.datasensor.com e-mail: info@datasensor.com
DATASENSOR S.p.A. cares for the environment: 100% recycled paper.
DATASENSOR S.p.A. reserves the right to make modifications and improvements without prior
notification.
:
m1 = C
m2 = C+I
d0 = 0 ms d3 = 20 ms
d1 = 5 ms d4 = 30 ms
d2 = 10 ms d5 = 40 ms
826001693 Rev.C
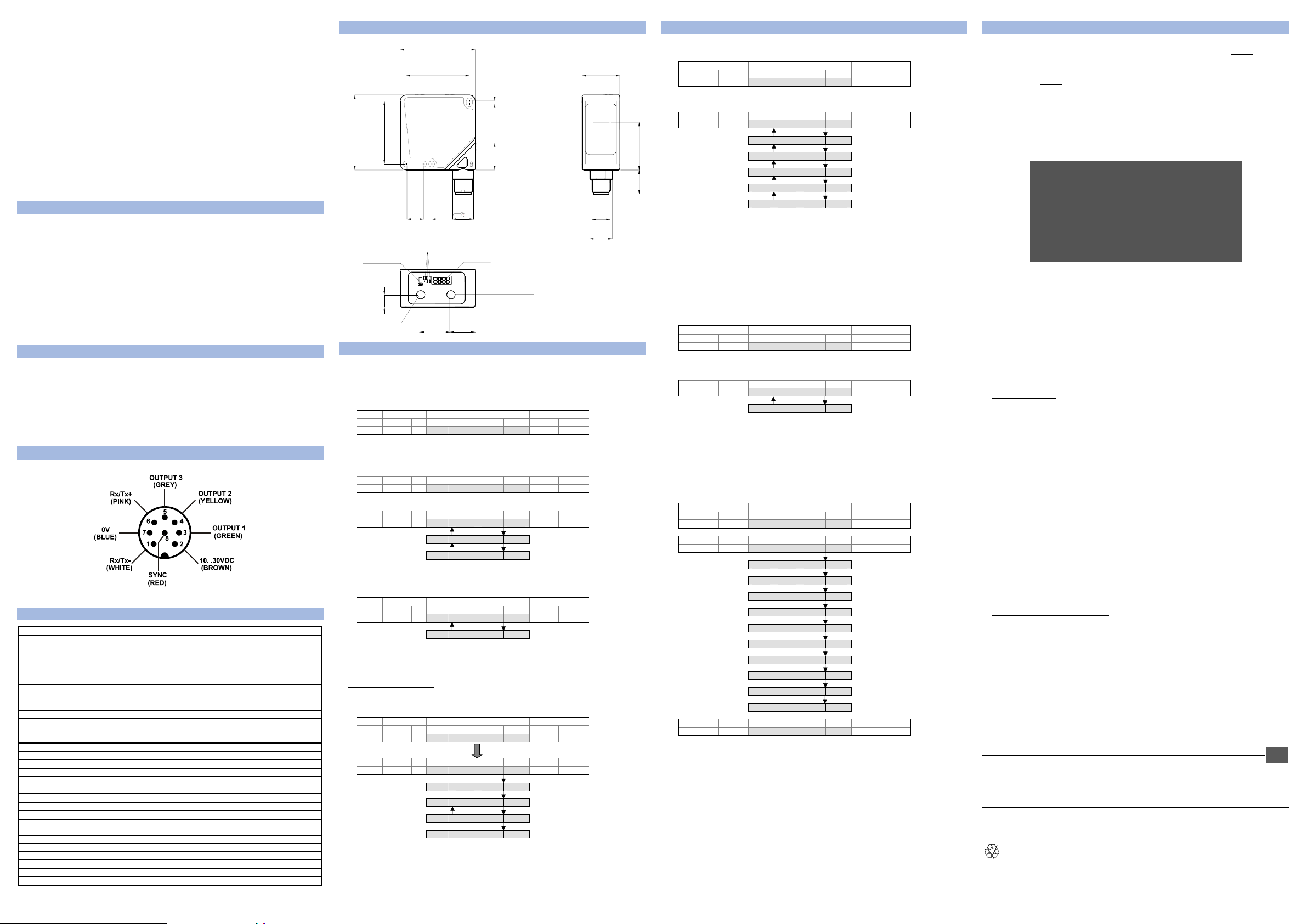
CTi Automation - Phone: 800.894.0412 - Fax: 208.368.0415 - Web: www.ctiautomation.net - Email: info@ctiautomation.net
S65-PA-5-V19
Colour sensor
OUPUT LED
The yellow LED ON indicates the OR function of the three OUT1, OUT2 and OUT3 outputs.
DISPLAY (green 4-digit display)
The display indicates the “run” or “rund” (run with delay) operating mode If the FAST commutating
speed is selected, the display visualizes every 40 sec (for 5 sec) the notice "FAST".
Please refer to the “SETTING” paragraph for the correct setup procedure indications.
OUT1, OUT2, OUT 3 LEDs
The green LED ON indicates that the corresponding output is active.
SET PUSHBUTTON
The pressure on the pushbutton activates the self-setting procedure.
A long pressure on the pushbutton allows the access to the delay setting menu.
SEL PUSHBUTTON
The pressure allows to scroll through the sensor setting parameter menu.
Please refer to the “SETTING” paragraph for the correct setup procedure indications.
The sensor can be positioned by means of the three housing’s
holes using screws (M4x35 or longer, 1 Nm maximum tightening
torque) with washers. The use of fixing brackets is recommended
if the supporting surface doesn't have a good planarity.
Various orientable fixing brackets to ease the sensor positioning
are available (please refer to the accessories listed in the
catalogue). The operating distance is measured from the front
surface of the sensor optics.
The M12 connector can be oriented at tree different positions
using the specific fastening spring and rotating the block of 90°.
M12 CONNECTOR
*
Available only for version with RS485 serial connection (S65-PA-5-V19-xxxZ).
Power supply: 10 … 30 Vdc limit values
Ripple: 2 Vpp max.
Consumption
(output current excluded):
Outputs: 3 PNP or NPN outputs
Tolerance level: 10 (toL0 - toL9) independent per each channel
Operating mode: C, C+I independent per each channel
Output current: 100 mA max.
Output saturation voltage:
Response time: 5ms (NORM) ; 1ms (FAST)
Switching frequency: 100 Hz (NORM) ; 500 Hz (FAST)
Indicators: 4-digit display (GREEN), OUTPUT LED (YELLOW)
Setting: SET pushbutton, SEL pushbutton
Data retention: EEPROM non volatile memory
Operating temperature: -10 … 55 °C
Storage temperature: -20 … 70 °C
Electrical protection: Class 2
Operating distance (typical values): 20 mm
Minimum spot dimension:
Emission type: white light LED (400-700nm)
Ambient light rejection: according to EN 60947-5-2
Vibrations: 0.5 mm amplitude, 10 … 55 Hz frequency, for every axis
Shock resistance: 11 ms (30 G) 6 shock for every axis (EN60068-2-27)
Housing material: ABS
Lens material: window and lenses in glass
Mechanical protection: IP67
Connections: M12 8-pole connector
Weight: 100 g. max.
INSTRUCTION MANUAL
CONTROLS
INSTALLATION
CONNECTIONS
*
*
TECHNICAL DATA
60 mA max. @ 24Vdc
30 Vdc max. (short-circuit protection)
≤ 2 V
3 OUTPUT STATUS LEDs (GREEN)
∅ 4 mm
(EN60068-2-6)
DIMENSIONS
50
42
2
42
50
18x45°
5.5
1411
OUTPUT STATUS
LEDS
OUTPUT LED
SELSET
DISPLAY
SEL PUSHBUTTON
mm
7.75
SET PUSHBUTTON
20 17.05
SETTING
The three-phase sensor setting allows the adjustment of the channel, operating mode and tolerance
values.
z pushbutton pressed { pushbutton not pressed
- Detection
Place object to detect inside the operating distance, in front of the sensor spot.
Display Keyboard
OUT 1 2 3 Dig1 Dig2 Dig3 Dig4 SET SEL
- Press the SET pushbutton for at least 2s.
- The “Set1” message is visualised.
- Channel setting
OUT 1 2 3 Dig1 Dig2 Dig3 Dig4 SET SEL
- Use the SEL pushbutton to select the channel.
OUT 1 2 3 Dig1 Dig2 Dig3 Dig4 SET SEL
- Operating mode
- Press the SET pushbutton again to configure the operating mode.
- Select C (colour) or C+I (colour + intensity) using the SEL pushbutton *.
Display Keyboard
OUT 1 2 3 Dig1 Dig2 Dig3 Dig4 SET SEL
* The 'C' type algorithm is used to obtain a larger depth of field, or to detect colours on different
opaque, shiny or reflecting surfaces. Whereas the 'C+I' type algorithm offers a higher sensitivity
towards tone variations and is recommended for the detection of different colours on the same type
of surface, with the possibility of distinguishing also the grey tones.
- TEACH and tolerance setting
- Press the SET pushbutton again, the “updt” text blinks for 2s.
The sensor then automatically passes into the tolerance selection.
Use the SEL pushbutton to select the required value.
Display Keyboard
OUT 1 2 3 Dig1 Dig2 Dig3 Dig4 SET SEL
OUT 1 2 3 Dig1 Dig2 Dig3 Dig4 SET SEL
- The “FAIL” text alternated with “Hi” or “Lo” is visualised if the detection is not correct.
- Repeat the procedure starting from the operating mode.
- The tolerance level increases from “toL0” to “toL9”. To detect small chromatic differences select
lower tolerance levels.
r u n d
S E t 1
S E t 1
S E t 2
S E t 3
C
C _ I
u p d t
t o L 0
t o L 1
t o L 2
t o L …
t o L 9
z {
{ z
{ z
{ z
{ z
z {
{ z
z {
{ z
{ z
{ z
{ z
{ z
25
M12
15
PARAMETER SETTING
Delay value visualisation and setting
Display Keyboard
OUT 1 2 3 Dig1 Dig2 Dig3 Dig4 SET SEL
Press the SET pushbutton for at least 6s to access to the delay setting mode.
OUT 1 2 3 Dig1 Dig2 Dig3 Dig4 SET SEL
31.6516
At each pressure of the SEL pushbutton, the different delay levels in ms are visualised in a cyclical
manner at the output deactivation and moreover, the relative delay value will be stored.
When the “d-00” message is visualised the operating mode will be “run”, and “rund” in all other cases.
The delay value setting is in common for all three outputs.
When a delay value, differen t from zero, is set the outputs will be maintained active fo r a minimum time,
which is equal to the number of milliseconds visualised on the display.
Visualization and set up of the FAST commutating speed
Display Keyboard
OUT 1 2 3 Dig1 Dig2 Dig3 Dig4 SET SEL
By pressing of SET and SEL buttons at the same time for 2 seconds at least, you enter in the set up
mode of the commutating speed.
OUT 1 2 3 Dig1 Dig2 Dig3 Dig4 SET SEL
At each pressure of the SEL push-button, the different commutating speed are displayed in cyclical
mode and the correspondant speed value is saved.
When message "norn" is displayed, the commutating speed is NORMAL, when message "FAST" is
displayed the commutating speed is FAST.
The set up of the commutating speed value is common at all three outputs.
r u n d
d - 0 0
d - 0 5
d - 1 0
d - 2 0
d - 3 0
d - 4 0
d-00 = 0 ms d-20 = 20 ms
d-05 = 5 ms d-30 = 30 ms
d-10 = 10 ms d-40 = 40 ms
r u n d
n o r n
F A S t
Channel status visualisation
This function allows a rapid control of the three sensor channel adjustment.
Pressing the SEL pushbutton for at least 2 s the channel, operating mode and tolerance are visualised
in a sequential manner.
Display Keyboard
OUT 1 2 3 Dig1 Dig2 Dig3 Dig4 SET SEL
OUT 1 2 3 Dig1 Dig2 Dig3 Dig4 SET SEL
OUT 1 2 3 Dig1 Dig2 Dig3 Dig4 SET SEL
At the end of the sequence the display will indicate the “run” or “rund” operating mode again.
r u n d
C h _ 1
C _ I
t o L 2
C h _ 2
C
t o L 1
C h _ 3
C
t o L 8
d - 0 5
F A S t
r u n d
z {
{ z
{ z
{ z
{ z
{ z
{ z
z {
{ z
z {
{ z
z {
REMOTE FUNCTIONS
KEYLOCK function (SET pushbutton block)
If at sensor powering the SYNC wire is connected to +Vdc for at least 1s, the keylock function is
activated and the pushbuttons are no longer active.
After the first second, the SYNC input is available for the normal operating modes; if SYNC is high the
outputs are deactivated.
To deactivate the keylock, the sensor has to be turned off and re-powered with the SYNC wire not
connected or ground connected (GND).
SYNC input
The SYNC signal can exactly determine the beginning and end of the colour identification.
The identification cycle begins after the SYNC signal changes from passive to active and the sensor
outputs have to updated after max. 700µs.
All the outputs are deactivated after max. 400µs from an active passage to a passive one.
The connection of the SYNC wire to Vdc corresponds to the passive logic status while SYNC not
connected or connected to 0V corresponds to the active logic status.
(SYNC passive = Vdc ; SYNC active = 0V)
A typical application of the SYNC function is the necessity to detect a particular position in a multicoloured target while the other area must not be detected. This function can also be used to avoid
erroneous detection during target-background transitions.
RS485 serial connection only for version S65-PA-5-V19-xxxZ
The complete sensor remote control is possible using the RS485 line.
All the functions such as the channel selection, the tolerance selection and the operating mode can be
accessed by means of this serial line.
The serial communication parameters are: 9600 baud, no equity, 8 data bits, 1 stop bit.
All the commands have to be sent via terminal in an ASCII format as follows:
- Receiving of the channel status:
At any moment, the receipt of the ‘r <CR> <LF>’ command indicates the sensor configuration.
- R B G component detection:
At the receipt of the ‘V <CR> <LF>’ comand (at any moment), the 3 components are transmitted in
the Rxxxx<CR><LF>Bxxxx<CR><LF>Gxxxx<CR><LF> forma t where the Rxxxx, Bxxxx and Gxxxx
are ASCII strings and one digit identifies the colour (R, B or G) and 4 digits represent the value.
- Remote setting mode:
To access to the remote setting mode, the SYNC input has be remain passive for at least 300ms.
The commands available are given below:
@ <CR> <LF> beginning of the remote setting, passive SYNC
cx <CR> <LF> channel selection, with x ∈ {1,2,3}
tx <CR> <LF> tolerance selection, with x ∈ {0,1,2,3,4,5,6,7,8,9}
mx <CR> <LF> operating mode selection, with x ∈ {1=C, 2=C+1}
e <CR> <LF> configuration sequence activation and configuration saving.
q <CR> <LF> exit from the remote setting mode without saving configuration.
If the SYNC input is activated before the ‘e’ (execute) command is given, the sensor exits the remote
setting mode without saving the configuration, similarly to the receipt of the ‘q’ (quit) command.
If the SYNC input is active, at the receipt of the @ <CR> <LF> command, the sensor responds with: ??
<CR> <LF>. At the receipt of the q <CR> <LF> commands the sensor transmits ok <CR> <LF>.
At the receipt of the e <CR> <LF> commands the sensor transmits ok <CR> <LF> in case of correct
acquisition, lo <CR> <LF> if the signal is too low, hi <CR> <LF> if the signal is too high.
- Delay configuration:
To access to the delay configuration, the SYNC input has be remain passive for at least 300 ms.
The commands available are given below:
@ <CR> <LF> beginning of the delay configuration, passive SYNC
dx <CR> <LF> delay selection, with x ∈ {0,1,2,3,4,5}, 0=0ms, 1=5ms
e <CR> <LF> memorisation of the new delay value
q <CR> <LF> exit from the delay configuration without saving the configuration.
If the SYNC input is activated before the ‘e’ (execute) command is given, the sensor exits the remote
setting mode without saving the configuration, similarly to the receipt of the ‘q’ (quit) command.
If the SYNC input is active, at the receipt of the @ <CR> <LF> command, the sensor responds with: ??
<CR> <LF>. At the receipt of the q <CR> <LF> or e <CR> <LF> commands, the sensor transmits ok
<CR> <LF>.
- Configuration of the commutating speed:
To enter the configuration of the commutating speed the SYNC input has be remain passive for at
least 300 ms. The available commands are:
@ <CR> <LF> start of the speed configuration (together with passive SYNC)
sx <CR> <LF> speed selection, with x ∈ {0=FAST, 1=NORMAL}
e <CR> <LF> saving of the new speed value
q <CR> <LF> exit from the delay configuration without saving configuration.
If the SYNC input becomes active before the ‘e’ (execute) command is given, the sensor exits from the
configuration without saving, likewise what happens when the ‘q’ (quit) command is given.
If the SYNC input is active, at the receipt of the @ <CR> <LF> command, the sensor responds with: ??
<CR> <LF>. At the receipt of the q <CR> <LF> or e <CR> <LF> commands, the sensor transmits ok
<CR> <LF>.
NOTE: during the command transmission, the single strings have to follow each other with a
delay of at least 1ms.
DECLARATION OF CONFORMITY
We DATASENSOR S.p.A. declare under our sole responsibility that these products are conform to the
2004/108 CEE, 73/23 CEE Directives and successive amendments.
WARRANTY
DATASENSOR S.p.A. warrants its products to be free from defects.
DATASENSOR S.p.A. will repair or replace, free of charge, any product found to be defective during
the warranty period of 36 months from the manufacturing date.
This warranty does not cover damage or liability deriving from the improper application of
DATASENSOR products.
DATASENSOR S.p.A. Via Lavino 265
40050 Monte S. Pietro - Bologna - Italy
Tel: +39 051 6765611 Fax: +39 051 6759324
http://www.datasensor.com e-mail: info@datasensor.com
DATASENSOR S.p.A. cares for the environment: 100% recycled paper.
DATASENSOR S.p.A. reserves the right to make modifications and improvements without prior
notification.
826002151 Rev.B