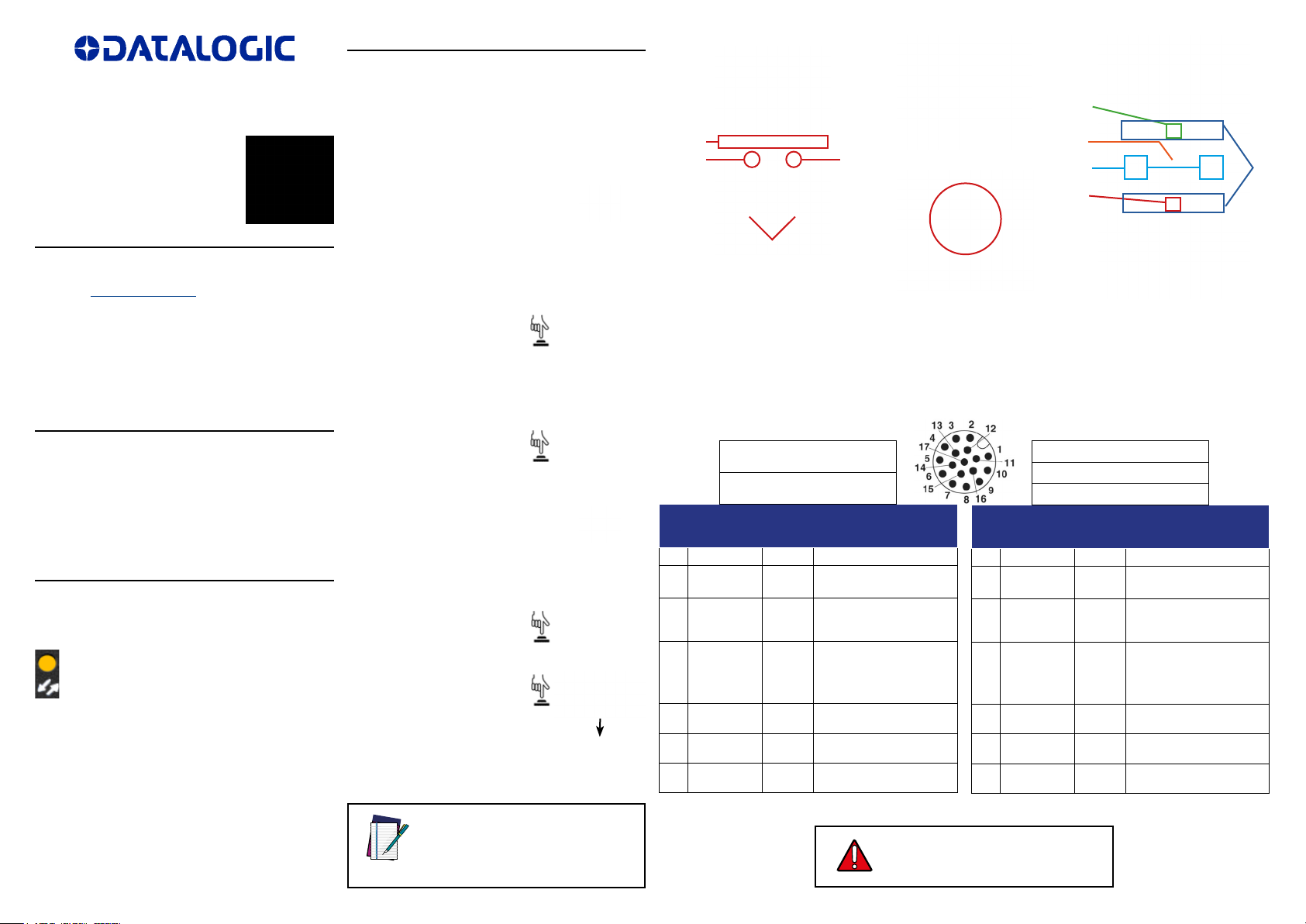
Smart-VS
QUICK REFERENCE GUIDE
Download the Smart-VS Product
Reference Guide by reading
the QR code here or see the
paragraph below.
BUTTON TEACHING PROCEDURE
The Run LED will blink until the Teaching procedure is
entered (e.g. device factory default).
Long press (> 4s, until the red LED on HMI lights up)
the HMI Button to enter the Teaching procedure.
1. GOOD objects required to be
taught (green LED and green
spot blink).
2. Place the GOOD object in
front of the Aiming System.
1
2 3
11
6
7
5
8
9
12
10
SUPPORT THROUGH THE WEBSITE
Datalogic provides several services as well as technical
support through its website.
Log on to www.datalogic.com.
For quick access, from the home page click on the
search icon, and type in the name of the product you’re
looking for. This allows you access to download Data
Sheets, Manuals, Software & Utilities, and Drawings.
Hover over the Support & Service menu for access to
Services and Technical Support.
INSTALLATION PROCEDURE
1. Physically mount the Smart-VS device.
2. Make the necessary electrical connections.
3. Congure the device using the embedded HMI or
the Smart-VS WebApp by connecting to the device
via Ethernet. The WebApp is accessible opening an
Internet browser (Google Chrome is recommended)
and entering the device IP address 192.168.3.100
in the address bar.
HMI INTERFACE
NO GOOD object
• in Teach phase: blinking, NO GOOD object
teaching
• in Run phase: NO GOOD object detected
• for future use
Trigger
• in Teach phase: trigger input status
• in Run phase: trigger received
GOOD object
• in Teach phase: blinking, GOOD object
teaching
• in Run phase: GOOD object detected
Run
• steady: device in Run phase
• blinking: Teaching required
3. Place the trigger sensor
properly. The Trigger LED
indicates object detection.
4. Short press (< 1s) the HMI
Button to acquire the image.
More than one GOOD
object can be acquired. It
is suggested to acquire one
image per GOOD object
instance. Camera parameters
are auto-adjusted on the rst
acquisition only.
5. Long press (> 4s, until the red
LED on HMI lights up) the
HMI Button to start acquiring
NO GOOD objects. Red LED
and red spot start blinking.
6. Place the NO GOOD object
in front of the Aiming System.
Check the Trigger LED.
7. Short press (< 1s) the HMI
Button to acquire the image.
More than one NO GOOD
object can be acquired.
8. Long press (> 4s, until the
red LED on HMI lights up)
the HMI Button to enter the
automatic learning procedure
(LEDs game). At the end,
the device will enter the Run
Phase.
The Teaching procedure can also be
entered when in Run phase: press the
HMI Button for 2s (yellow LED on HMI) for
incremental teaching or 4s (red LED on
NOTE
HMI) to cancel and re-teach. Refer to the
Product Reference Guide for more details.
4
1. Bracket Mounting Holes (2)
2. Power On LED
3. Ethernet Connection LED
4. 90° Rotating Connector Block
5. HMI Interface
6. Ethernet Connector
CAB-GD03 M12-17P 3M power and
I/O cable, isolated wires (95A900052)
CAB-GD05 M12-17P 5M power and
I/O cable, isolated wires (95A900053)
M12 17-pin Power, and I/O Connector Pinout
(9 stripped wires)
Pin Color Name Function
12Brown
Blue
Connector
case
6
Yellow
5
Pink
13
Green
3
White
Vdc
GND
Chassis Connector case provides
I1A *
I1B *
I2A *
I2B *
9 Red O1 **
8 Gray O2 **
16 Black O3 **
* Polarity insensitive
** Short-circuit protected and
software programmable
PWR supply input voltage +
PWR supply input voltage -
electrical connection to
chassis
Trigger Input A
Trigger Input B
Remote Teach A
Remote Teach B
Data Valid (default is PushPull)
GOOD Output (default is
Push-Pull)
NO-GOOD Output (default
is Push-Pull)
For proper installation, it is recommended
to trim out all unused wires.
WARNING
7. Power - I/O Connector
8. Lens
9. LED Aiming System
10. Red Spot (NO GOOD)
11. Green Spot (GOOD)
12. White Polarized Illuminators
CAB-GD03 M12 F/L 3M Free wires
CAB-GD05 M12 F/L 5M Free wires
CAB-GD10 M12 F/L 10M Free wires
M12 17-pin Power, and I/O Connector Pinout
(17 stripped wires)
Pin Color Name Function
12Brown
Blue
Connector
case
6
Yellow
5
Pink
13
White/Green
3
White
Vdc
GND
Chassis Connector case provides
I1A *
I1B *
I2A *
I2B *
9 Red O1 **
8 Gray O2 **
Yellow/Brown
16
O3 **
PWR supply input voltage +
PWR supply input voltage -
electrical connection to
chassis
Trigger Input A
Trigger Input B
Remote Teach A
Remote Teach B
Data Valid (default is PushPull)
GOOD Output (default is
Push-Pull)
NO-GOOD Output (default
is Push-Pull)
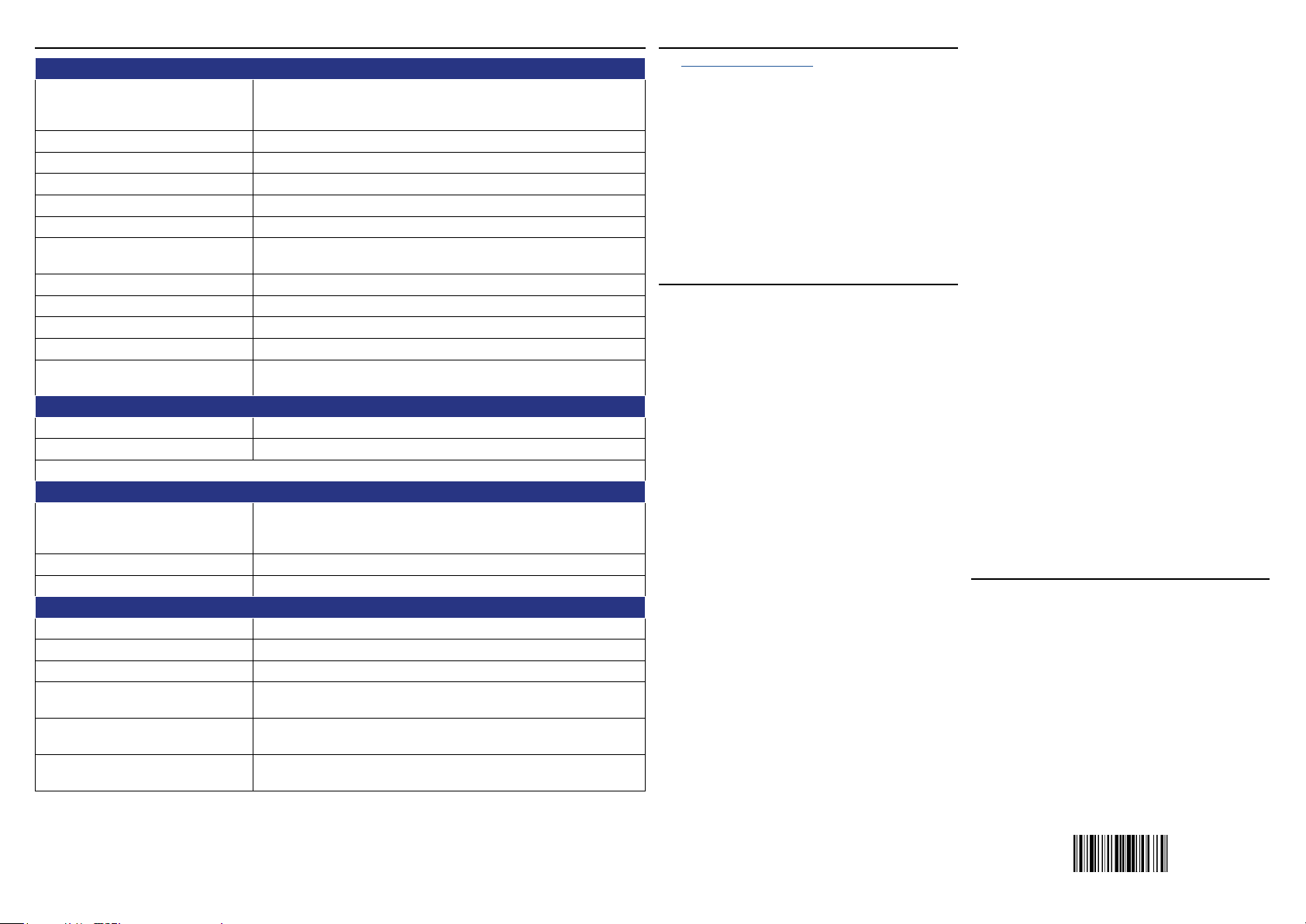
TECHNICAL FEATURES
Electrical Features
Power
Supply Voltage (Vdc)
Consumption (A) Max.
10 to 30 Vdc
0.40 - 0.14 A (4.2 W)
Communication Interfaces
Ethernet
1
10/100 Mbit/s
Inputs: Opto-coupled and polarity insensitive (see Product Reference Guide)
Max. Voltage 30 Vdc
Max. Input Current 10 mA
Outputs:
PP, NPN or PNP short circuit protected
(see Product Reference Guide)
Max. Output Voltage Drop 3V
V
HIGH (Max. / Min.) V
OUT
V
LOW (Max. / Min.) 3V / 0V
OUT
I
Max. 100 mA
LOAD
GOOD and NO GOOD output
response time
50 ms ± 1 ms from input trigger
supply
/ V
supply
- 3V
Optical Features
Operating Distance 50 - 150 mm
View Angle 19°
See Product Reference Guide for details
Physical Features
Dimensions
Std Smart-VS connector at 0°
Std Smart-VS connector at 90°
78 x 47 x 38 mm (3.1 x 1.9 x 1.5 in)
58 x 47 x 58 mm (2.3 x 1.9 x 2.3 in)
H x W x L
Weight 173 g (6.1 oz)
Material Aluminum with PMMA protective window cover
Environmental Features
Operating Temperature
2
-10 to 50 °C (14 to 122 °F)
Storage Temperature -20 to 70 °C (-4 to 148 °F)
Max. Humidity 90% non-condensing
Vibration Resistance
EN 60068-2-6
Shock Resistance
EN 60068-2-27
Protection Class
3
EN 60529
1
The embedded Ethernet interface is intended for conguration only through connection to the device IP
14 mm @ 2 to 10 Hz; 1.5 mm @ 13 to 55 Hz; 2 g @ 70 to 500 Hz; 2
hours on each axis
30 g; 11 ms; 3 shocks on each axis
IP65 and IP67
address 192.168.3.100.
Point-to-Point connection is recommended.
2
High ambient temperature applications should use metal mounting bracket for heat dissipation.
3
When correctly connected (fully tightened) to IP67 cables with seals.
PATENTS
See www.patents.datalogic.com for patent list.
Smart-VS is covered by one or more of the following patents:
Design patents: EP004735694
Utility patents: EP0996284B1, EP0999514B1, EP1014292B1,
EP1128315B1, EP1396811B1, EP1413971B1, EP2517148B1,
EP2649555B1, JP4435343B2, JP4571258B2, US6512218,
US6616039, US6808114, US6997385, US7053954,
US7387246, US7433590, US8058600, US8368000,
US8888003, US8915443, US9268982, US9430689,
US9798948, ZL200980163411.X
COMPLIANCE
In order to meet the EMC requirements, connect device
chassis to the plant earth ground by means of a at copper
braid shorter than 100 mm.
CE COMPLIANCE
CE marking states the compliance of the product with essential
requirements listed in the applicable European directive.
Since the directives and applicable standards are subject to
continuous updates, and since Datalogic promptly adopts
these updates, therefore the EU declaration of conformity is a
living document. The EU declaration of conformity is available
for competent authorities and customers through Datalogic
commercial reference contacts. Since April 20th, 2016 the
main European directives applicable to Datalogic products
require inclusion of an adequate analysis and assessment of
the risk(s). This evaluation was carried out in relation to the
applicable points of the standards listed in the Declaration
of Conformity. Datalogic products are mainly designed for
integration purposes into more complex systems. For this
reason, it is under the responsibility of the system integrator
to do a new risk assessment regarding the nal installation.
Warning
This is a Class A product. In a domestic environment this
product may cause radio interference in which case the user
may be required to take adequate measures.
FCC COMPLIANCE
Modications or changes to this equipment without the
expressed written approval of Datalogic could void the authority
to use the equipment.
This device complies with PART 15 of the FCC Rules.
Operation is subject to the following two conditions: (1) This
device may not cause harmful interference, and (2) this device
must accept any interference received, including interference
which may cause undesired operation.
This equipment has been tested and found to comply with
the limits for a Class A digital device, pursuant to part 15
of the FCC Rules. These limits are designed to provide
reasonable protection against harmful interference when the
equipment is operated in a commercial environment. This
equipment generates, uses, and can radiate radio frequency
energy and, if not installed and used in accordance with the
instruction manual, may cause harmful interference to radio
communications. Operation of this equipment in a residential
area is likely to cause harmful interference in which case the
user will be required to correct the interference at his own
expense.
EAC COMPLIANCE
Customs Union:
The CU Conformity certication has been achieved; this allows
the Product to bear the Eurasian mark of conformity.
LED SAFETY
LED emission according to EN 62471.
POWER SUPPLY
This product is intended to be installed by Qualied Personnel
only.
This product is intended to be connected to a UL Listed Direct
Plug-in Power Unit marked LPS or “Class 2”.
LEGAL NOTICES
© 2020-2021 Datalogic S.p.A. and/or its aliates * ALL RIGHTS
RESERVED. * Without limiting the rights under copyright, no
part of this documentation may be reproduced, stored in or
introduced into a retrieval system, or transmitted in any form or
by any means, or for any purpose, without the express written
permission of Datalogic S.p.A. and/or its aliates.
Datalogic and the Datalogic logo are registered trademarks of
Datalogic S.p.A. in many countries, including the U.S. and the
E.U.
Smart-VS is a trademark of Datalogic S.p.A. and/or its
aliates. All other trademarks and brands are property of their
respective owners.
Datalogic shall not be liable for technical or editorial errors or
omissions contained herein, nor for incidental or consequential
damages resulting from the use of this material.
821006913 (Rev. D)