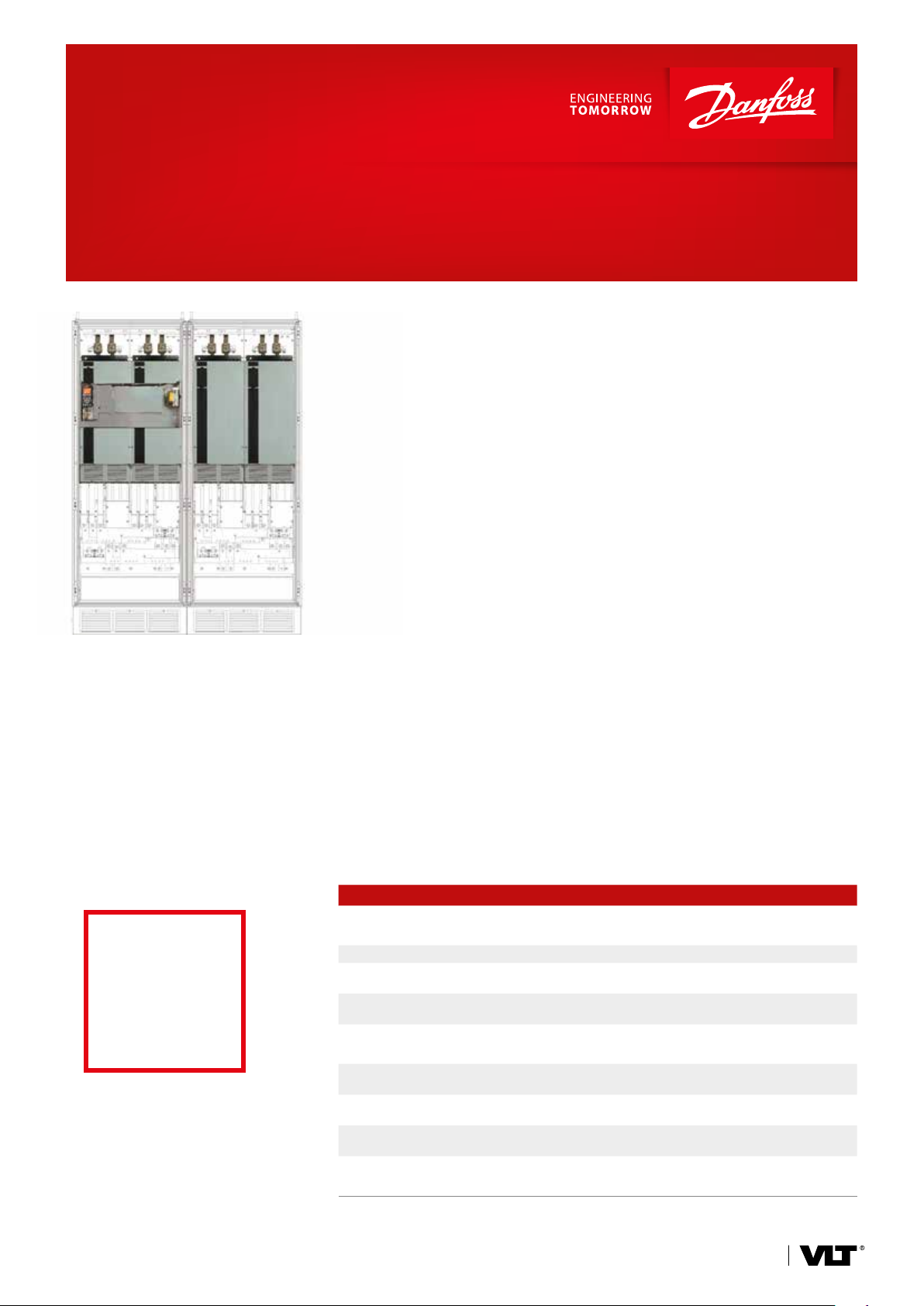
Fact Sheet
VLT® Common AC Drive Modules
Build cabinets exactly how you need them, using VLT® common AC drive modules. By using multiple
high power drives connected in parallel, you can achieve greater power sizes in a modular solution.
VLT® common AC drive modules
comprise sets of two to four VLT® high
power drives connected in parallel,
with 6-pulse and 12-pulse variants.
A reference design for the cabinet of
the drives has been made using the
Rittal TS8 enclosure. This reference
design makes it easy for panel builders
and machine builders to build their
own cabinets, worldwide.
Reliability
Enjoy long drive lifetime and save on
extra components, with integrated
fuses and DC coils. The high-power
drive modules are delivered with these
components built-in as standard.
Increase uptime with the Reduce Run
functionality. This function enables the
system to run at part load even if one of
the drive units fails.
Back-channel cooling
A unique design uses a ducted back
channel to pass cooling air over heat
sinks with minimal air passing through
the electronics area. This design allows
90% of the heat losses to be exhausted
directly outside of the enclosure. Backchannel cooling improves reliability and
prolongs life by dramatically reducing
temperature rise and contamination
of the electronic components. There is
an IP54 seal between the back-channel
cooling duct and the electronics area of
the VLT® drive.
Product families
n VLT® AutomationDrive FC 302
n VLT® AQUA Drive FC 202
n VLT® HVAC Drive FC 102
Power range
6-pulse
n 450–1200 kW
n 600–1350 hp
12-pulse
n 250–1200 kW
n 350–1350 hp
Voltage range
n 380-480/500 V
n 525-690 V
Enclosure rating
n IP00
Up to 1.2 MW
output power,
in compact
modular design
with 98%
eciency
Feature Benet
VLT® family – one platform, one user interface,
common graphical LCP
Compact size – high power density Savings in space and cost, in cabinet design.
O
Runs at 100% load up to 45
Coated PCBs as standard
Built-in DC link reactors
Built-in AC fuses Savings on cost and space, for extra components.
Reduce Run function
98% efficiency Low lifetime operating cost.
Back-channel cooling
C
Know one drive, know them all.
Savings in time and cost for training, service,
ordering and spare parts logistics.
Full and reliable performance at high ambient
temperatures.
Extended lifetime, with high environmental
resistance.
Reduced harmonics distortion level and:
– No need for external AC chokes
– No additional panel space required
Allows the system to run at part load, even if one
of the drives fails.
Reduces the scale of air conditioning required for
the room, reducing up-front cost and operating
expenses.
www.danfoss.com/drives
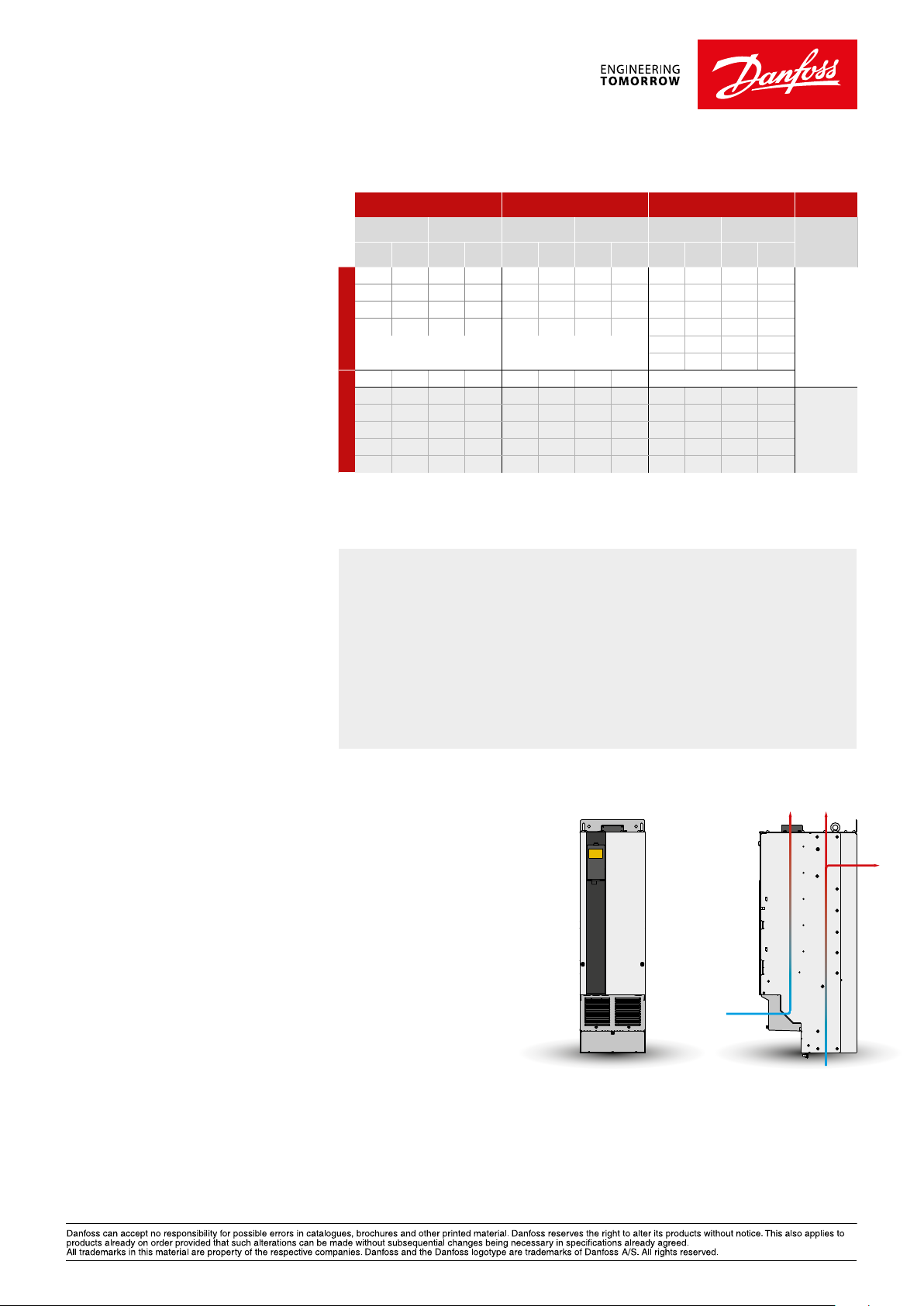
Options
n Stainless steel back channel
n RFI filter
n Brake chopper
n Heat sink access panel
n Fieldbus options
n Application options
n Control power back-up input
Busbar kit
Factory designed kit, including:
n Flexible busbars
n Common AC terminals
n DC busbars
n Ground busbars
n EMC screens
Cooling Duct kits
Pre-fabricated kits in
four different versions:
n Bottom-in/top-out
n Back-in/back-out
n Bottom-in/back-out
n Back-in/top-out
For more details, refer to
www.danfoss.com/drives.
PC Software
VLT® Motion Control Tool MCT 10
set-up software
MCT 10 offers advanced programming functionality for all VLT® products,
greatly reducing programming and
set-up time.
Nominal ratings
400 V AC 460 V AC 690 V AC
Normal
overload
Power
Current
[kW]
[A]
315 600 250 480 450 540 350 443 315 344 250 290
355 658 315 600 500 590 450 540 400 400 315 344
400 745 355 658 600 678 500 590 450 450 355 380
450 800 400 695 600 730 550 678 500 500 400 410
12-pulse
500 880 450 800 650 780 600 730
560 990 500 880 750 890 650 780 710 730 630 630
630 1120 560 990 900 1050 750 890 800 850 710 730
710 1260 630 1120 1000 1160 900 1050 900 945 800 850
800 1460 710 1260 1200 1380 1000 1160 1000 1060 900 945
6-pulse/12-pulse
1000 1720 800 1460 1350 1530 1200 1380 1200 1260 1000 1060
overload
Power
[kW]
High
Current
[A]
Normal
overload
Power
[hp]
Current
[A]
overload
Power
[hp]
High
Normal
Current
overload
Power
[A]
[kW]
560 570 500 500
630 630 560 570
Current
[A]
overload
Power
[kW]
Normal overload: 110% of nominal current can be applied for intermittent duty (60 sec).
High overload: 150% of nominal current can be applied for intermittent duty (60 sec).
Compliance
n CE & UL Listed for common AC drive module design
n EMC compliance:
– EN 55011, Class A2/IEC 61800-3 Category C3 (standard)
– EN 55011, Class A1/IEC 61800-3 Category C2 (optional)
n Safety category 3, PL d (ISO 13849-1)
n Stop category 0 (EN 60204-1)
n STO: Safe Torque Off (IEC 61800-5-2) SIL 2 (IEC 61508)
n SILCL 2 (IEC 62061)
High
Current
[A]
Module
dimensions
(number of
modules)
H x W x D
(2x)
1122 x 350 x
375 mm
44 x 14 x
15 in.
(4x)
1122 x 350 x
375 mm
44 x 14 x
15 in.
VLT® Motion Control Tool MCT 31
Harmonics Calculation Software
MCT 31 calculates the system harmonic
distortion due to AC drives, and determines the most cost-effective method
to mitigate harmonics.
n Calculate system harmonic
distortion
n Estimate the benefits of adding vari-
ous harmonic mitigation solutions
from the VLT® product portfolio
Danfoss Drives, Ulsnaes 1, DK-6300 Graasten, Denmark, Tel. +45 74 88 22 22, Fax +45 74 65 25 80, www.danfoss.com/drives, E-mail: info@danfoss.com
DKDD.PFP.404.A1.02 © Copyright Danfoss Drives | 2016.02