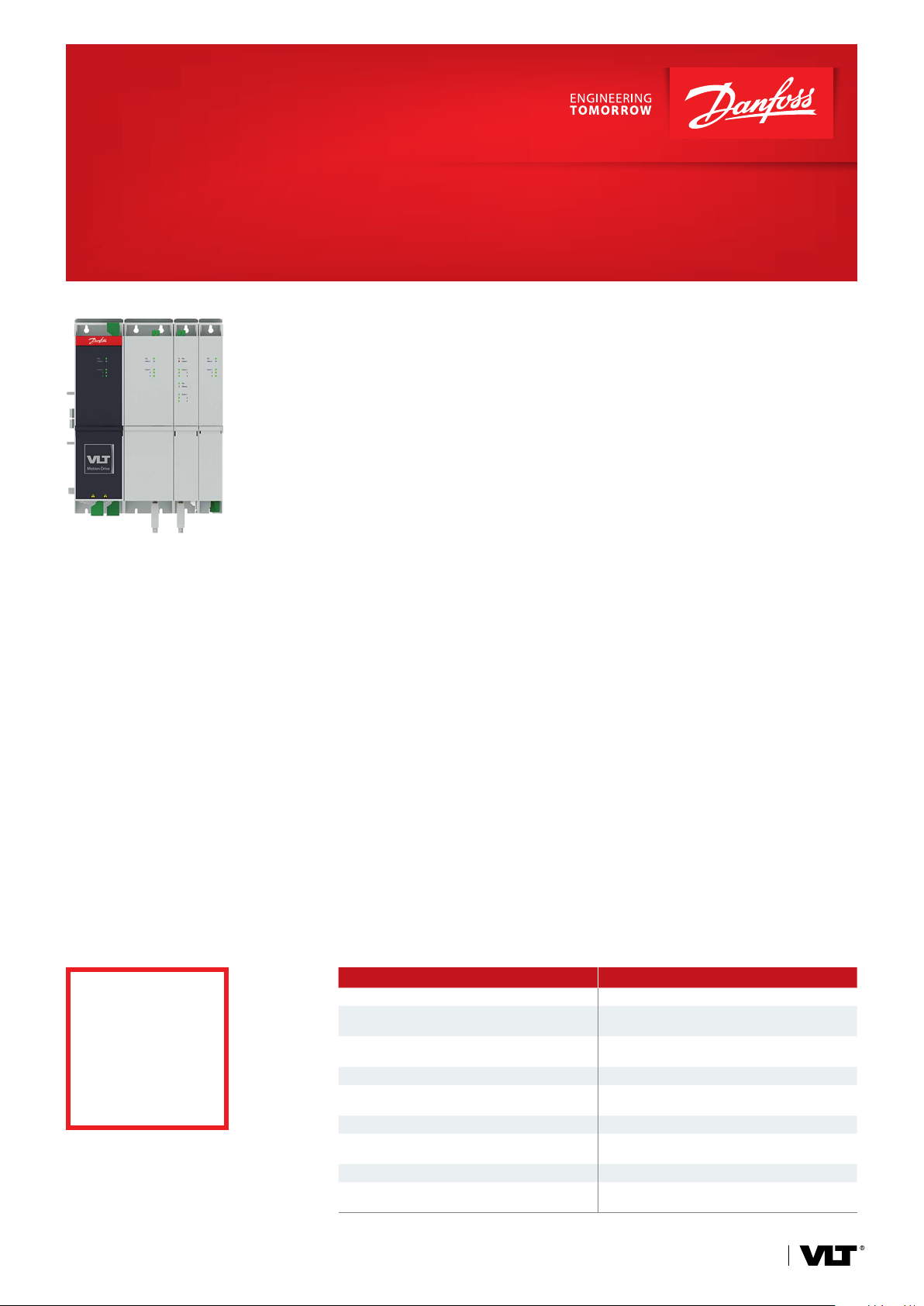
Fact Sheet
VLT® Multiaxis Servo Drive MSD 510
High-performance central servo motion solution
The VLT® Multiaxis Servo Drive MSD 510
system is a high-performance central
servo motion solution, developed
specifically for the Food & Beverage,
Packaging, Pharmaceutical and Material
Handling industries. The servo system
comprises a Power Supply Module
(PSM 510), Drive Modules (SDM 511,
SDM 512), Decentral Access Module
(DAM 510) and an Auxiliary Capacitors
Module (ACM 510). Modules are
available in 2 frame sizes with a width
of 50 and 100 mm.
The system offers easy mounting and
installation with its unique ‘click and
lock’ backlink concept. DC link and the
control voltage supply is integrated in
the backlink plate.
Depending on the application, the
system can be used exclusively in
a central system or together with
Danfoss Decentral Servo Drives (ISD
510 and DSD 510) in a mixed system.
The open system supports the RT
Ethernet systems EtherCAT®, Ethernet
POWERLINK® and PROFINET®.
VLT® Power Supply Module
(PSM 510)
The PSM 510 generates a 565-680 V DC
power supply and guarantees high
power density. The PSM 510 is available
in 3 power sizes and delivers an output
power of 10, 20 or 30 kW with 200%
overload capability. Furthermore, two
PSM can be used in parallel resulting in
an output power up to 60 kW.
Drive Modules
VLT® Servo Drive Module (SDM 511)
VLT® Servo Drive Module (SDM 512)
The SDM 511 is a single axis servo
drive available in 2 frame and 5 power
sizes. The SDM 512 is a double axis
servo drive available in the smallest
frame size and 3 power sizes. A wide
range of feedback options allows the
selection of the preferred PM motor.
Furthermore, the drive modules are
equipped with digital I/Os and Safe
Torque Off (STO).
The motion control is integrated
into each drive so that the
motion sequences can take place
independently. This releases the central
PLC and offers a highly flexible servo
drive concept. The master can be
programmed via IEC 61131-3.
VLT® Decentral Access Module
(DAM 510)
The DAM 510 is used to connect the
Danfoss Decentral Servo Drives ISD
510 and DSD 510 by a hybrid feed-in
cable to the MSD 510 system. This gives
the user the flexibility and freedom to
design the servo system according to
the application need.
VLT® Auxiliary Capacitors
Module (ACM 510)
Depending on the application the
ACM 510 can be added to the system
for controlled machine stop in certain
critical situations.
Click &
Lock
Backlink concept
enables easy installation and usage of the
MSD 510 system
Feature Benefit
Dynamic servo performance Fast, accurate, and energy-efficient
Standard servo drive variants in frame sizes
1 and 2
Real-time systems EtherCAT®,
Ethernet POWERLINK® and PROFINET®
Control via IEC 61131-3 Common standard, open system architecture
Local Control Panel (LCP)
LEDs on each module Fast and effective monitoring
Mixed systems
One user interface Same SW Tools for the whole servo drive platform
Openness to PM motors
Selection of most suitable servo drive for
the application’s power requirements
Fast process communication
Direct connection to the servo drives for fast
commissioning, diagnosis, and service
Perfect integration of Danfoss Decentral
Servo Drives
Use the servo motor and feedback type fitting
the application need
drives.danfoss.com
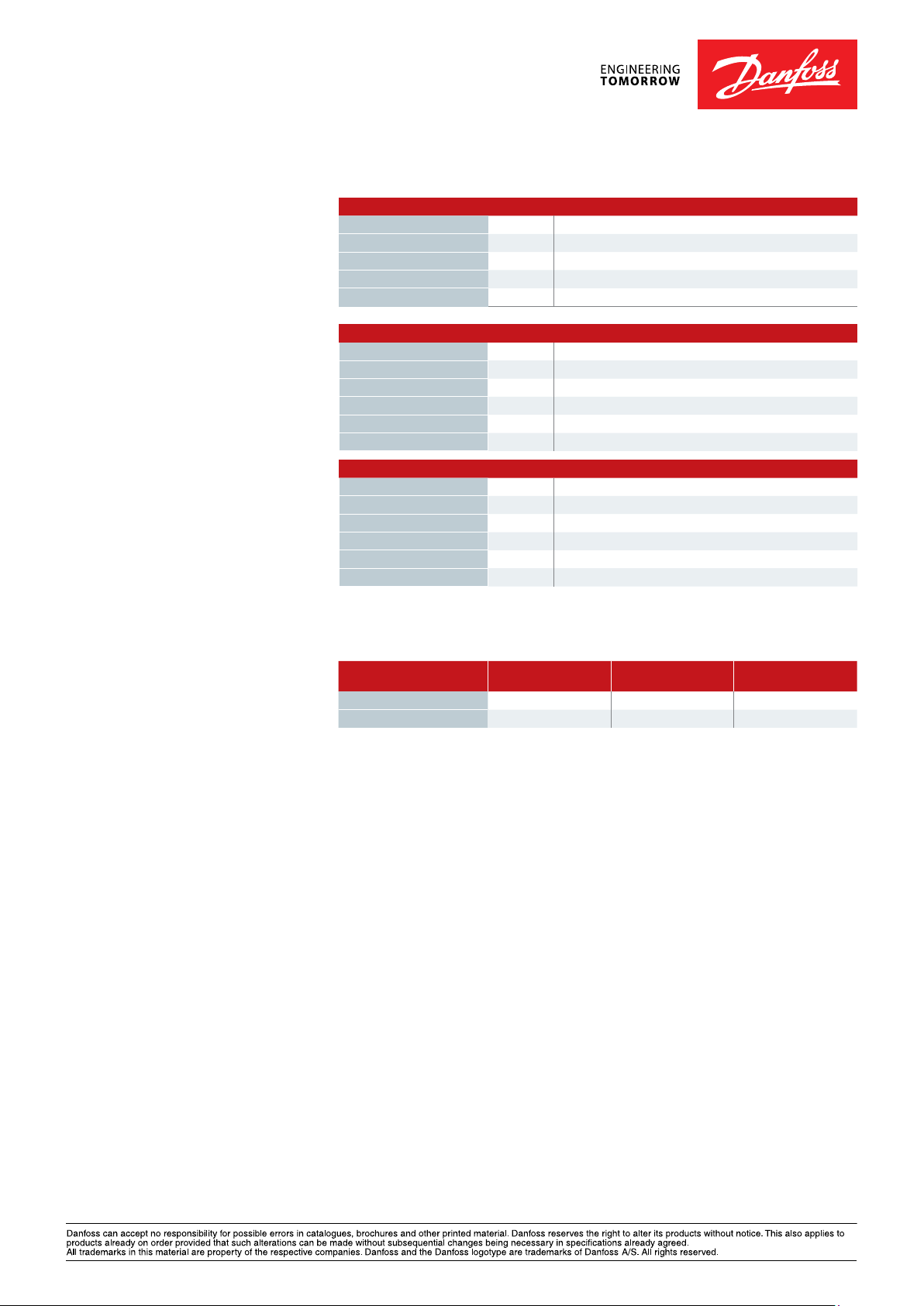
The perfect solution for:
Packaging machines
Food & Beverage machines
Pharmaceutical machines
Material Handling machines
Available options
Feedback
Resolver
BiSS single-turn
BiSS multi-turn
EnDat 2.1*
EnDat 2.2*
Hiperface*
Hiperface DSL*
Supported thermal sensors
KTY
PTC
NTC
Digital I/Os
4 digital inputs
4 digital outputs
* In preparation
Specifications
PSM 510
Input voltage U
Output voltage U
Rated current I
Rated power P
IN
OUT
N
N
400-480 V AC ±10%, 3-phase
565-680 V DC ±10%
20, 40, 60 A
10, 20, 30 kW
Enclosure IP20
Servo Drive Modules SDM 511
Rated voltage UDC
Rated current I
Maximum current I
Rated power P
N
max
N
Link
DC 565 V
2.5, 5, 10, 20, 40 A
10, 20, 30, 40, 80 A
1.4-22 kW
Functional Safety STO (Safe Torque Off )
Enclosure IP20
Servo Drive Modules SDM 512
Rated voltage UDC
Rated current I
Maximum current I
Rated power P
N
max
N
DC 565 V
Link
2 x 2.5, 2 x 5, 2 x 10 A
2 x 10, 2 x 15, 2 x 20 A
2.8-11.3 kW
Functional Safety STO (Safe Torque Off )
Enclosure IP20
Dimensions
Depth
mm
Frame size 1 270** 50 380**
Frame size 2 270** 100 380**
** Including backplate
Width
mm
Height
mm
DKDD.PFP.802.A2.02 © Copyright Danfoss Drives | 2018.04
EtherNet/IP™ and DeviceNet™ are trademarks of ODVA, Inc.