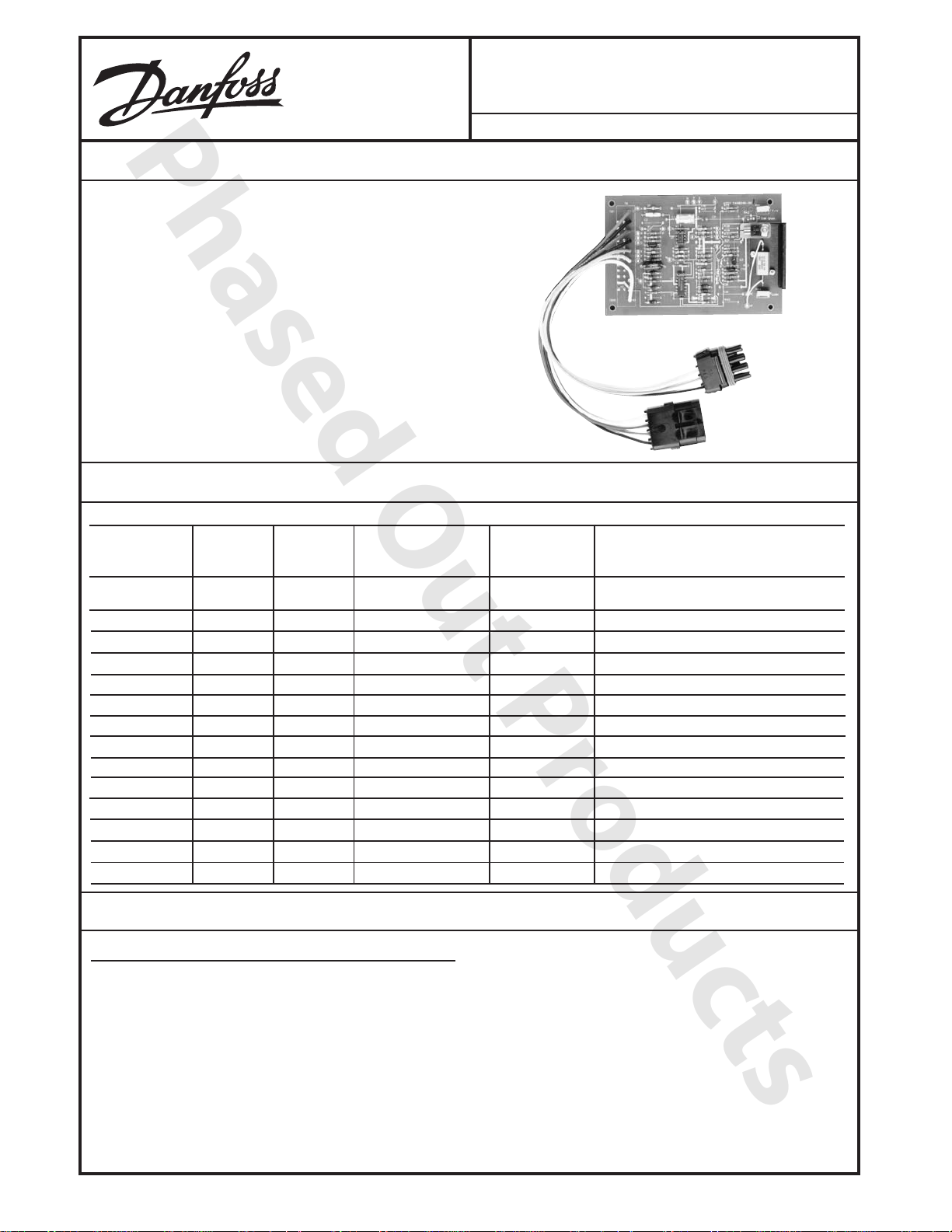
MCE102A
Automotive Controller
BLN-95-8993-3 Issued: May 1998
DESCRIPTION
The MCE102A automotive controller enables hydrostatically
powered vehicles to operate in a manner similar to a car’s
automatic transmission. The automotive control maintains a
definite relationship between the engine r.p.m. and the
swashplate angle (i.e, displacement) of the variable
displacement pump used in the hydrostatic transmission. The
transmission ratio (displacement of the pump/displacement of
the motor) increases with increasing engine r.p.m. Vehicle
speed is obtained by depressing the throttle pedal which
controls the vehicle engine r.p.m.
ORDERING INFORMATION
DEVICE
NUMBER
MCE102A1007 12 Vdc .14 amp 200 to 900 Hz Packard External Inch Pot
MCE102A1014 12 Vdc .14 amp 200 to 900 Hz Packard External Foot Break
MCE102A1022 12 Vdc .14 amp 50 to 225 Hz Terminal Strip External F/V Turn Down
MCE102A1030 24 Vdc .7 amp 4 to 20 mA Packard Reverse Acting
MCE102A1049 12 Vdc 1.0 amp 10 to 50 Hz Terminal Strip Lead/Lag Filter
MCE102A1055 12 Vdc .7 amp 90 to 500 Hz Packard Pressure Transducer Turn Down
MCE102A1063 12 Vdc 1.0 amp 200 to 650 Hz Terminal Strip Lead/Lag Filter, 2 Speed
MCE102A1071 24 Vdc .7 amp 4 to 20 mA Terminal Strip Reverse Acting
MCE102A1097 12 Vdc 1.0 amp 200 to 650 Hz Terminal Strip Lead/Lag Filter, 2 Speed
MCE102A1105 12 Vdc .14 amp 1000 to 3000 Hz Terminal Strip Lead/Lag Filter
MCE102A1113 12 Vdc .14 amp 200 to 650 Hz Terminal Strip Lead/Lag Filter
MCE102A1121 12 Vdc 1.0 amp 600 to 1950 Hz Terminal Strip Lead/Lag Filter, 2 Speed
MCE102A1139 24 Vdc .14 amp 1000 to 3000 Hz Terminal Strip Lead/Lag Filter
MCE102A1147 12 Vdc .14 amp 200 to 650 Hz Packard Lead/Lag Filter
SUPPLY
VOLTAGE
OUTPUT
CURRENT
INTERNAL
SETPOINT RANGE
CONNECTOR
TYPE
MISCELLANNEOUS
TECHNICAL DATA
ELECTRICAL
SUPPLY VOLTAGE
12 Vdc nominal (11 to 15 Vdc range)
24 Vdc nominal (22 to 30 Vdc range)
OUTPUT CURRENT
1.0 amps maximum in auto mode (12 Vdc models)
0.7 amps maximum in auto mode (24 Vdc models)
OUTPUT VOLTAGE
System supply voltage less 3 volts, maximum (limited by
a series resistor on some models).
REVERSE VOLTAGE PROTECTION
A series diode protects against reverse voltage up to
50 Vdc
SHORT CIRCUIT PROTECTION
1.4 to 2.0 amps (12 Vdc models)
0.8 to 1.2 amps (24 Vdc models)
Shorted load of more than 2 minutes may degrade
device at elevated temperature. Output limited by a
series resistor on some models.
© Danfoss, 2013-09 BLN-95-8993-3 1
.
.
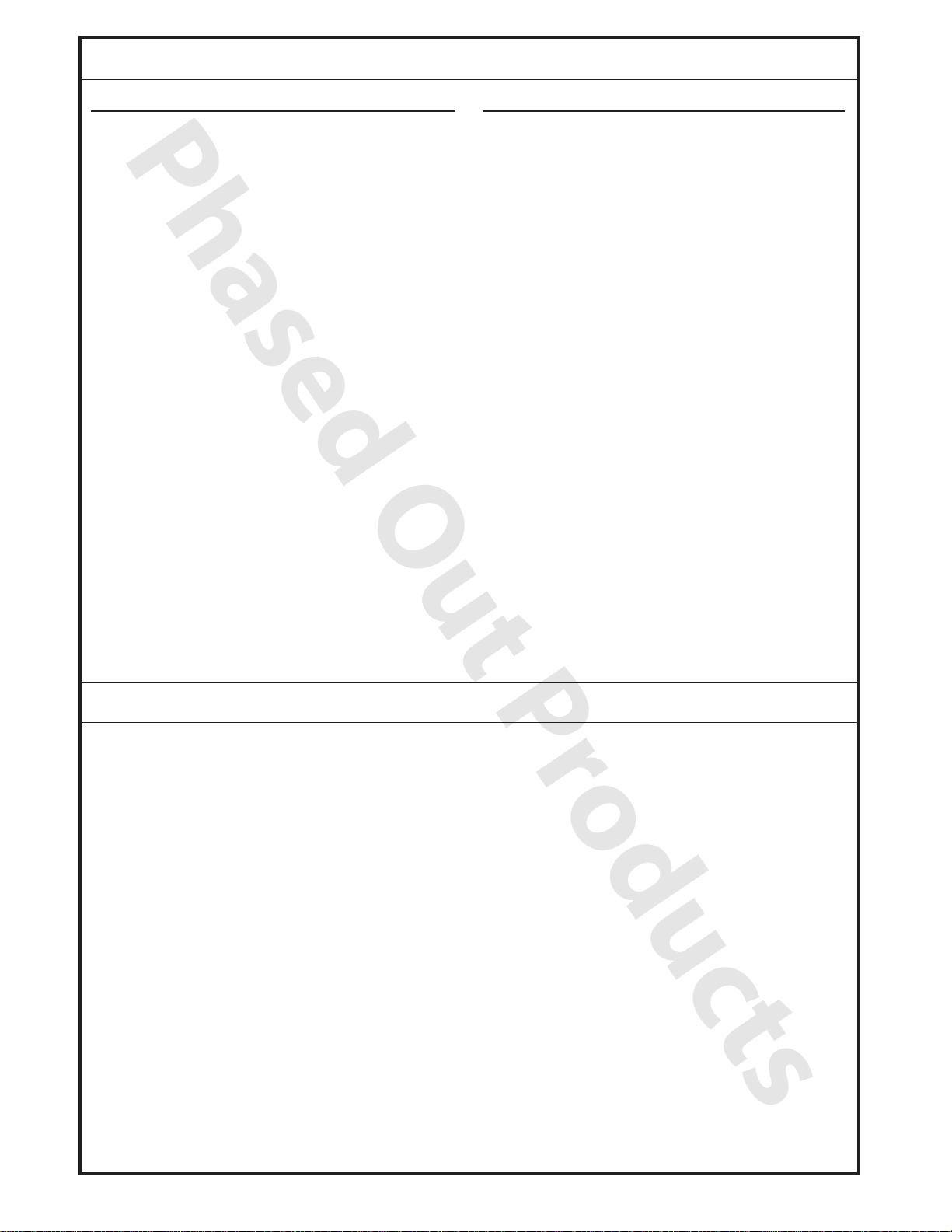
TECHNICAL DATA
(continued)
ENVIRONMENTAL
VIBRATION
Withstands a vibration test designed for mobile
equipment controls consisting of two parts:
1. Cycling from 5 to 2000 Hz in each of the three axes
2. Resonance dwell for one million cycles in each of
the three axes
Run from 1 to 10 Gs. Acceleration level varies with
frequency.
HUMIDITY
After being placed in a controlled atmosphere of 95%
humidity at 38° C (100° F) for 10 days, the controller will
perform within specification limits.
RAIN
After being showered from all directions by a high
pressure hose down, the controller will perform within
specification limits.
SHOCK
50 Gs for 11 milliseconds. Three shocks in both
directions of the three mutually perpendicular axes for a
total of 18 shocks.
OPERATING TEMPERATURE
-20 to 65° C (-4 to 149° F)
STORAGE TEMPERATURE
-30 to 65° C (-22 to 149° F)
PERFORMANCE
MAXIMUM OUTPUT VOLTAGE
The maximum output voltage to the load shall be the
supply voltage less three volts up to rated load current.
MAXIMUM OUTPUT CURRENT
With the output terminal shorted to ground, the
maximum output current shall be from 1.4 to 2.0 amps
(12 Vdc models) or 0.8 to 1.2 amps (24 Vdc models),
depending on temperature.
OPERATING SUPPLY VOLTAGE
11 to 15 Vdc, or 24 to 30 Vdc optional with added
components
SUPPLY CURRENT
1.1 amps maximum (except for shorted loads) (12 Vdc
models)
0.8 amps maximum (except for shorted loads) (24 Vdc
models)
VOLTAGE RANGE
The controlled voltage decreases from supply minus 3
volts down to zero.
SENSITIVITY
The sensitivity control changes the proportioning band
from 4% (turned clockwise) to 75% (turned counter
clockwise) of calibrated r.p.m. The proportioning band is
defined as the change necessary to reduce output
voltage from 100% to 20% of rated output. Sensitivity
control may be removed and replaced with a fixed
resistance in some models.
THEORY OF OPERATION
The automotive controller monitors engine r.p.m. as a
variable frequency through the alternator or pulse pickup.
The controller’s calibration (point of maximum displacement)
is at or near the r.p.m. at which the engine is capable of
maximum horsepower. The output is directed to the pump
displacement control through a double-pole double-throw
center off switch. For vehicle forward, neutral and reverse,
see Automotive Control System Diagram.
Between low idle and low r.p.m., the engine is well below
setpoint (see Controller Output Vs. Engine RP M and Reverse
Acting Controller), which the controller interprets as a lugged
condition; consequently there is no propel. As engine r.p.m.
increases, the controller output increases, the rate of
increase being determined by the gain setting of the
controller. The engine r.p.m. that corresponds to maximum
ratio is determined by the engine r.p.m. calibration
potentiometer. Vehicle speed will continue to increase with
increasing engine r.p.m. even though the transmission ratio
remains unchanged above the high r.p.m. calibration point.
The transmission ratio is proportional to engine r.p.m., an d
overhauling loads resulting in high engine r.p.m. will keep the
pump at full angle, resulting in dynamic braking limited by the
engine horsepower absorption. Therefore, to guarantee
adequate braking, the vehicle mechanical brake must be
applied.
The automotive controller is adaptable to applications with
either medium or heavy duty transmissions. Additional
features such as HI/LOW range, reverse acting, pressure
transducer turn down, lead/lag and inching may also be
incorporated into the system.
The feedback circuit may be modified to accept a dc signal.
4 to 20 mA from a pressure transducer or 0 to 6 Vdc from a
tachometer are two types of dc signals acceptable for
feedback.
The unit may be modified to provide decreasing output for
increasing r.p.m. (reverse acting).
BLN-95-8993-3
2
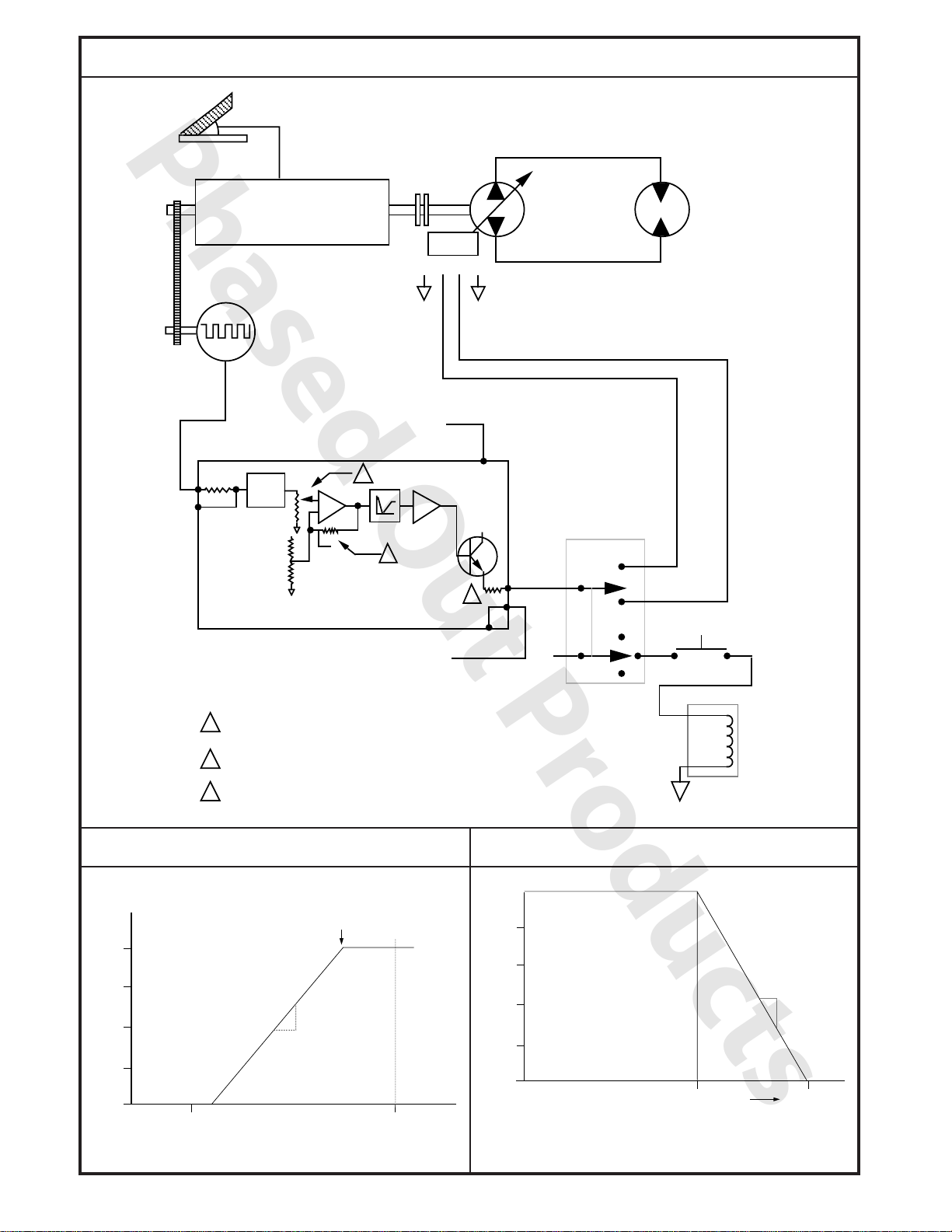
AUTOMOTIVE CONTROL SYSTEM DIAGRAM
ENGINE
B A D C
+12 V
+
-
GRD
EDC
RED
C
3
BLACK
A
D
WHITE
+12 V
FORWARD
NEUTRAL
REVERSE
GREEN
F/V
B
+2 VOLT REF
PROPORTIONAL TRANSMISSION
CONTROL BOARD
1
+
-
2
ENGINE CALIBRATION POTENTIOMETER
1
SLOPE ADJUST POTENTIOMETER
2
SERIES RESISTOR IN SOME MODELS TO LIMIT CURRENT IF
3
DIRECT DRIVING AN ELECTRICAL DISPLACEMENT CONTROL (EDC).
STARTER
RELAY
CONTROLLER OUTPUT Vs. ENGINE RPM REVERSE ACTING CONTROLLER
AUTOMOTIVE CONTROL BOARD
% OF FULL DRIVE
CONTROLLER OUTPUT VOLTAGE
LOW
LOW
RPM
IDLE
HIGH RPM
CALIBRATION
GAIN
ENGINE RPM
HIGH
IDLE
100
% OF FULL DRIVE
CONTROLLER OUTPUT
CALIBRATE
POINT
1417
GAIN
PRESSURE
0-6 Vdc
or CURRENT
(4-20 mA)
14191418
3
BLN-95-8993-3

MCE102A1007 (1014) (1147*) AUTOMOTIVE
+12 V
0 - 2.5 V
200 - 900 Hz
R
NEUT
START
BRAKE
SWITCH
(1014)
F
R
F
N
D
C
A
B
INCH
ALT.
(200 - 650 Hz*)
1K
N.C
A - WHT
B - GRN
C - RED
D - BLK
A - N/C
B - YEL
C - ORG
D - BLK
A - 10
60 W
B - 3
C - 1
D - 2
B - 6
C - 5
D - 4
MCE102A1022 SLAVE RATIO
50 - 225 Hz ALT
2063
MCE102A
EDC
B
A
0 - 2.5 V
10
9
60 W
8
7
6
5
SLAVE
RATIO
1K
4
3
2
BLN-95-8993-3
+12 V
1
TERM
STRIP
4
1421

MCE102A1113 LEAD/LAG FILTER
MCE102A
EDC
B
A
0 - 2.5 V
10
9
60 W
8
7
6
5
4
200 - 650 Hz ALT
3
2
+12 V
1
TERM
STRIP
2064
MCE102A1105 (1139) LEAD/LAG FILTER
MCE102A
60 W
EDC
B
A
0 - 2.5 V
(120 W)
10
9
KPP
1600 - 3000 Hz
+12 V
(+24 V)
8
7
8.2 V
6
5
4
3
2
1
TERM
STRIP
2065
5
BLN-95-8993-3

MCE102A1030 REVERSE ACTING, 24 VOLT, 4 - 20 mA INPUT
CONTROL
HANDLE
20 V
ZERO
EDC
+24 V
A
B
+
-
4 - 20 mA
A - WHT
B - GRN
C - RED
D - BLK
A - 10
B - 3
C - 1
D - 2
1422A
MCE102A1097 (1121) WITH LEAD/LAG FILTER
EDC
200 - 650 HZ
(600 - 1950 Hz)
IGNITION
CONTROL
HANDLE
+12V
SLOW
0 - 10 V
NORM
MCE102A
10
9
8
7
6
5
4
3
2
1
BLN-95-8993-3
TERMINAL
STRIP
6
1423

MCE102A1071 REVERSE ACTING, 24 VOLT, 4 - 20 mA INPUT (TERMINALS)
Control
Handle
20 V
A
EDC
B
+
-
ZERO
10
9
8
7
6
5
4
3
4 - 20 mA
2
1
+24 VOLTS
TERMINAL
STRIP
1424
CUSTOMER SERVICE
NORTH AMERICA
ORDER FROM
Danfoss (US) Company
Customer Service Department
3500 Annapolis Lane North
Minneapolis, Minnesota 55447
Phone: (763) 509-2084
Fax: (763) 559-0108
DEVICE REPAIR
For devices in need of repair or evaluation, include a
description of the problem and what work you believe
needs to be done, along with your name, address and
telephone number.
RETURN TO
Danfoss (US) Company
Return Goods Department
3500 Annapolis Lane North
Minneapolis, Minnesota 55447
EUROPE
ORDER FROM
Danfoss (Neumünster) GmbH & Co.
Order Entry Department
Krokamp 35
Postfach 2460
D-24531 Neumünster
Germany
Phone: 49-4321-8710
Fax: 49-4321-871355
7
BLN-95-8993-3