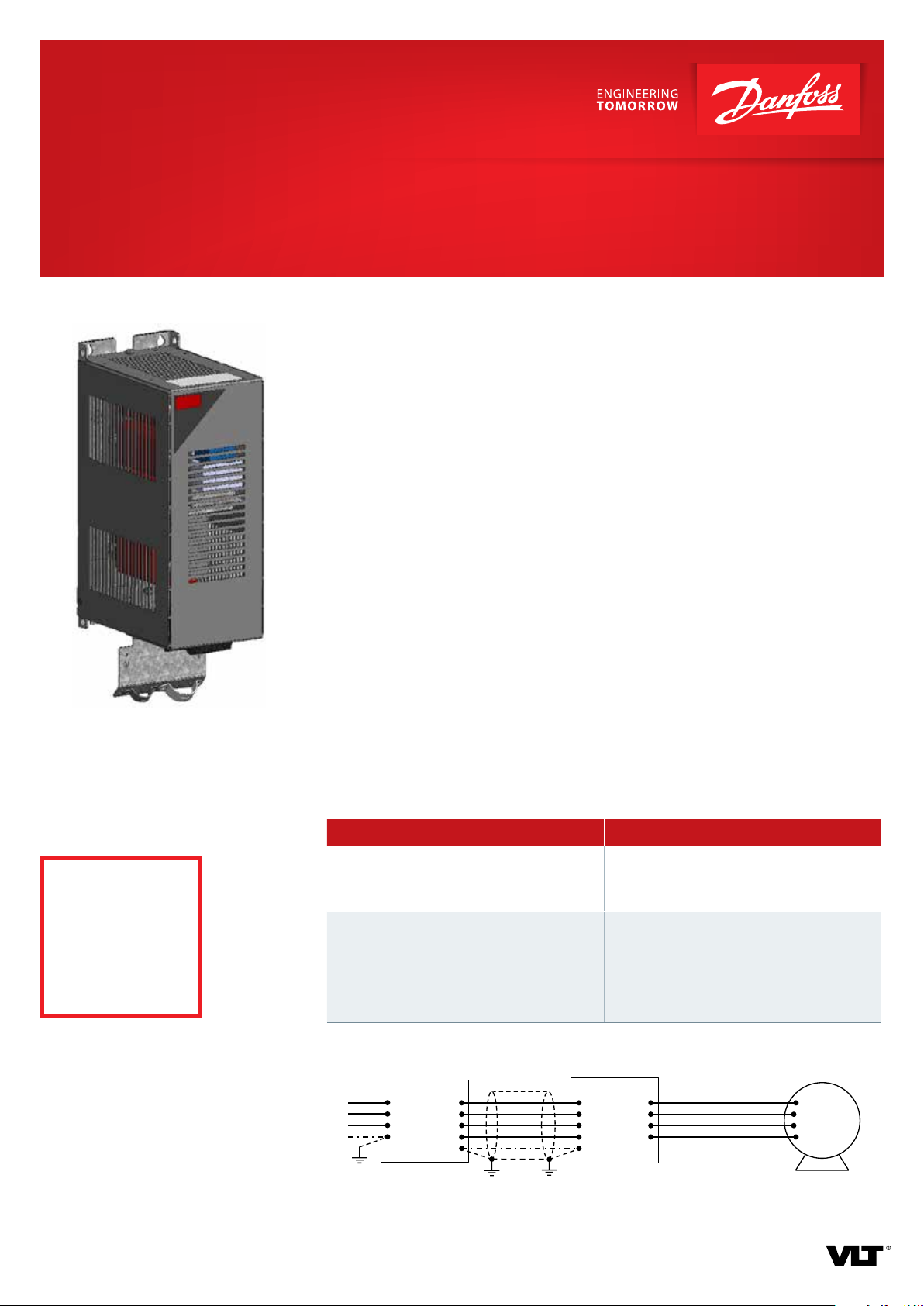
Fact sheet
VLT® All-mode Filter MCC 201
VLT® All-mode Filter MCC 201 output filters
are dual mode low-pass sine-wave filters
operating differential mode and common
mode. These filters suppress the switching
frequency component from the drive
and smooth out the phase-to-phase and
phase-to-ground output voltage of the
drive to become sinusoidal.
Long or unshielded motor cables
The VLT® All-mode Filter MCC 201
technology with reduction of differential
mode and common mode interference
at the inverter output enables the use of
extremely long motor cable lengths. This
filter also supports the use of unshielded
motor cables.
Electrical interference
The VLT® All-mode Filter MCC 201 efficiently
filters differential and common mode
interferences. Through the connection to
the intermediate circuit of the VLT® drive,
the common mode currents returns to
the source of the drive. This configuration
is highly effective at preventing this
high-frequency interference current from
spreading across the electrical installation.
Bearing current
Inverter-based bearing currents in the
motor may be caused by the common
mode voltage from the drive IGBT output
stage. The VLT® All-mode Filter MCC 201
provides a real solution to those effects,
for all practical purposes completely
eliminating the common mode distortions,
which considerably extends motor lifetime.
Quality and operation
The VLT® AutomationDrive FC 302,
VLT® AQUA Drive FC 202, and the
VLT® HVAC Drive FC 102 have been
designed to operate the VLT® All-mode
Filter MCC 201 by an automated feature,
which will enable matching operating
conditions. The drive requires DC-link
connection for common mode feedback
from filter, R+ terminal (terminal 82). The
VLT® All-mode Filter MCC 201 is designed
to match the look and quality of the FC
series drives.
True
sinusoidal
power supply
Features Benefits
Terminals can accommodate larger
cable cross sections
Dual-mode operation
VLT®
L1
L2
L3
PE
U
V
W
R+
PE
- Reduces voltage drop for long cable operation
- Enables longer cables than limited by the drive
- Enables use of unshielded motor cables
- Reduces acoustical switching noise from motor
- Improves conducted emissions
- Eliminates motor bearing currents
- Eliminates motor insulation stress
- Extends motor service life
MCC 201
U1
U2
V1
V2
W1
W2
UDC
PE
PE
Schematic diagram showing the cabling of VLT® drive, MCC 201 filter and motor
drives.danfoss.com
U
M
V
W
3~
PE
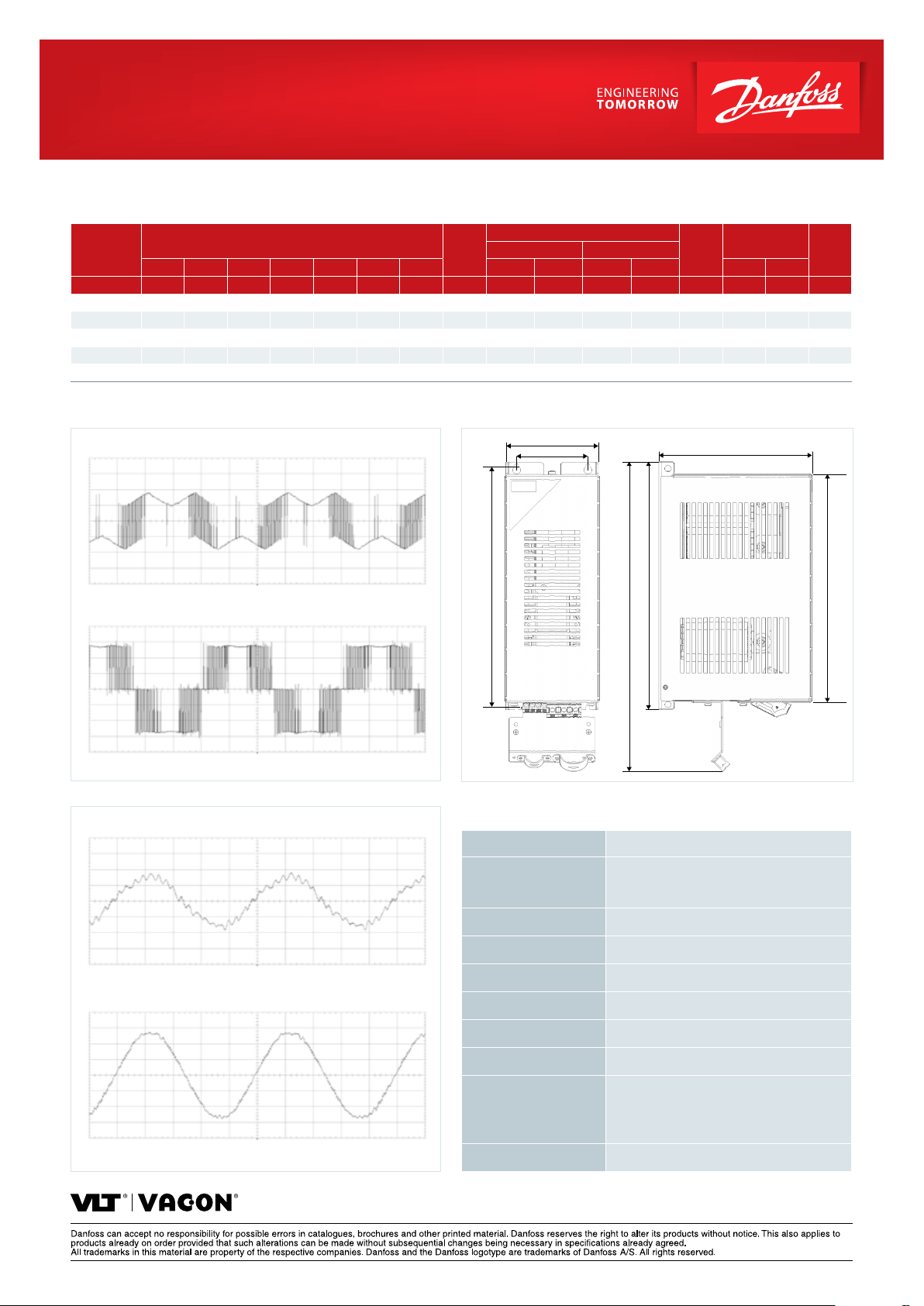
Dimensions and electrical ratings*
Ordering
number
Mechanical dimensions
A B C D E F G <5Hz 5-150 Hz <5Hz 5 -150H z Drive Motor
Current rating @voltage/frequency
Weight
380- 440V 441-500V
[P/N] [mm] [mm] [mm] [mm] [mm] [mm] [mm] [Kg] [A] [A] [A] [A] [W] [mm
175U6006 110 205 238 268 343 78 257 8 5.6 6 4.2 5.5 80 10 16 M6
175U6013 131 210 311 338 425 97 327 16 12.1 13 9.2 12 120 10 35 M6
175U6024 165 292 351 399 545 125 380 28 22.3 24 17. 7 23 200 16 50 M6
175U6046 201 314 461 518 690 14 8 501 43 42.8 46 33.5 43.5 350 35 95 M6
175U6065 231 366 488 550 746 175 529 69 60.5 65 47.7 62 650 50 120 M6
*The values are preliminary.
Max.
power
loss
Max. wire
cross section
2
] [mm2] [Bolt]
PE
Motor Voltage Phase-Ground
Voltage [v]Voltage [v]
Motor Voltage Phase-Phase
Without filter
Motor Voltage Phase-Ground
t [ms]
t [ms]
A
F
D
G
E
Preliminary Specifications
Voltage rating 3 x 380 - 500 V
Nominal current
6.0 - 65 A @400 V
5.5 - 62 A @500 V
B
C
Voltage [v]Voltage [v]
Motor frequency < 150 Hz without derating
Switching frequency 4 – 16 kHz
t [ms]
Motor Voltage Phase-Phase
Overload capacity 160% for 60 sec at 10-minute intervals
Ambient temperature -10 – 45 °C without derating
Cooling method Natural convection
Protection rating IP20
Book-st yle wall-mounting side by side
Mounting
with the drive
Cable terminations at the b ase of the filter, with EMC
decoupling plate
With filter
DKDD.PFO.623.A1.02 © Copyright Danfoss Drives | 2019.11
t [ms]
Approvals CE, UL 508 pending