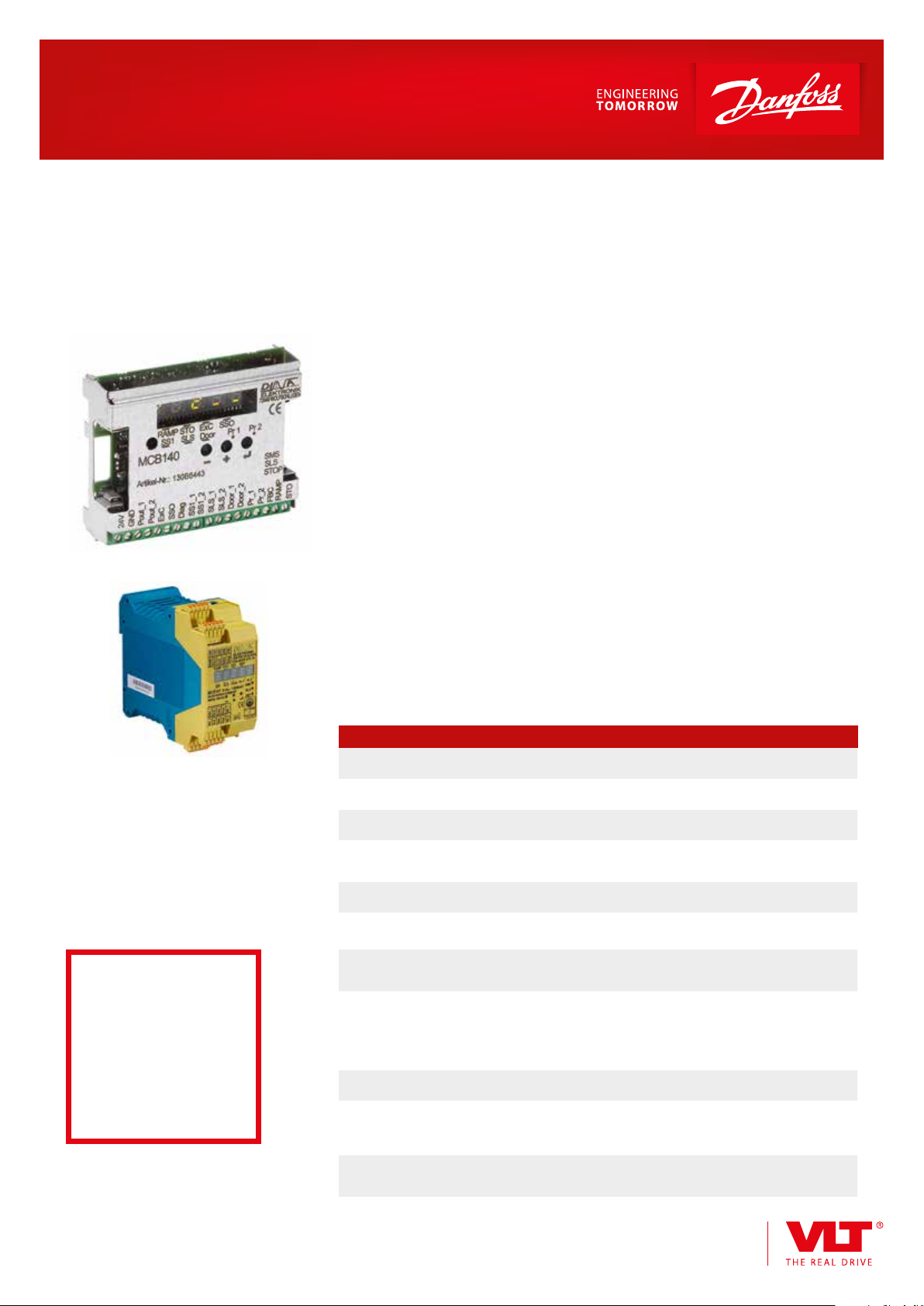
VLT® Safety Option MCB 140/141
Integrate the most important safety functions in a single, compact device that works with all drives.
MCB 141 – for external mounting outside the drive
enabling use of the MCB 140 functionality if another
B- option is installed.
Ordering no. MCB 140 130b6443
Ordering no. MCB 141 130b6447
50%
saving on wiring can be
achieved in low safetycritical applications,
compared to traditional
dual-channel solutions.
The VLT® Safety Option MCB 140/141
series expands the Safe Torque O
(STO) function that is integrated into
the drive, by adding a safe measurement of the ramp-down time, also
called SS1, Safe Stop 1.
The MCB 140/141 has been designed
to provide drive-integrated safety
without needing to change the
overall safety concept. This means
that the option can be commissioned
and used in a similar way as external
safety devices. By integrating the
Extensive speed monitoring features
have also been integrated into the
system.
• SMS (Safe Maximum Speed)
safety option into the drive owners
save both space and wiring, without
loosing the ability to commission the
safety system without using a PC.
protects both operators and
equipment from dangerous
overspeed.
• SLS (Safely Limited Speed) is
activated by a dedicated input that
allows operators to carry out work
at the machine without interrupting
Setup is fast and user-friendly. The
integrated display guides users
through a limited number of easy to
understand parameters, enabling
them to set up the safety system in a
matter of minutes.
the production process.
• SSM (Safe Speed Monitor)
Feature Benet
Scalable from single channel PL c to dual channel PL e
Internal and external version available
No need to power cycle the drive after a demand on the
safety system
Three logic safe inputs
Maintenance can be performed while the machine is still
in motion
Safe Torque O (STO)
Safe Stop 1 (SS1)
Monitors ramp down time and shuts o the torque
Safely Limited Speed (SLS)
Monitors whether a specied velocity is exceeded
Safe Maximum Speed (SMS)
Protection of over speed during automatic production
Standstill output
Pulsed voltage supply
Less wiring, fewer external components, only pay for
what you need.
Use the same safety concept no matter which drive is
used.
Minimized wear on the drive, longer lifetime
expectancy and reliability.
A dedicated input for each safety function, easy to
connect without needing an additional safety
component.
Minimize time and eort required for service
and installation work.
Prevention of unexpected startup without
power contactors. No maintenance needed.
Controlled ramp-down results in faster standstill
compared to STO, without losing all benets of the
STO.
Makes it possible to work safely with the guards
open.
Reduce set-up times thanks to a better view into the
set-up area.
Greater operational safety by means of safely limited
set-up speed.
Protect your machine from destruction due to
over-speed.
Use this output to control movable guard
interlocking devices. Enables the user to enter the
machine only if it is in standstill.
Show the user that it is safe to enter the machine.
Check wiring, connectors and switches for
correct function. Higher ecient failure
nding resulting in less downtime.
Facts about our products

frequency
time
Safe Torque Off (STO)
Activation
of STO
actual
frequency
frequency
time
Safe Stop 1 (SS1)
Activation of
SS1
Activation
of STO
SS1 time
actual
frequency
SS
1 time
supervision
frequency
time
Safely Limited Speed (SLS)
SLS activated
actual
frequency
SLS max
speed limit
frequency
time
Safe Maximum Speed (SMS)
actual
frequency
SMS max
speed limit
SMS always active
frequency
time
Safe Speed Monitor (SMS)
Standstill output
active
actual
frequency
speed
monitor limit
The safety Option oers the
following safety functions as per
IE C 6180 0-5-2:
Specications
General
Supply voltage 24V, PELV required
Supply current 80 mA + load current
Reaction time of safety functions 20 ms
Category according to ISO13849-1 4 (2 if single channel is used)
Performance Level (PL) according to
ISO13849-1
Digital inputs
Number of digital inputs
Input voltage range 0 V up to supply voltage
Input voltage Low: < 1 V / High: > 21,6 V
Input current 2,5 mA at 24 V/ -2,75 mA at 0 V
Galvanic isolation No
Short circuit proof Yes
Digital outputs
Number of outputs
Output voltage low 0 V (high side switch with pull down)
Output voltage high Supply voltage
Nominal output current 0,5 A
Short circuit proof Yes
Pulsed Outputs
Number of outputs 2 (1 for each safety channel)
Output voltage low 0 V (high side switch with pull down)
Output voltage high Supply voltage
Nominal output current 100 mA
Short circuit proof Yes
Proximity switch inputs
Number of inputs 2
Suitable output types PNP
Input voltage range 0 V – Supply voltage
Input frequency Max. 12,5 kHz
Galvanic isolation No
Short circuit proof Yes
Certications
Certied according to ISO 13849-1 cat. 4 and PL e
e (c if single channel is used)
6 (3x2–channel Digital Safety Input)
1 input for feedback circuit
3 safe outputs (1 x 2-channel Digital Safety
Output, 1 x 1-channel Digital Safety Output)
2 additional outputs
Danfoss VLT Drives, Ulsnaes 1, DK-6300 Graasten, Denmark, Tel. +45 74 88 22 22, Fax +45 74 65 25 80
www.danfoss.com/drives • info@danfoss.com
DKDD.PFO.608.A3.02 VLT® is a trademark of Danfoss A/S PE-MMSC 2015.04
Highly scalable, the VLT® Safety
Option MCB 140/141 can adapt to
your exact needs. In less critical
applications the option can be
congured as a single channel
system, which saves wiring and costs.
In more critical applications it can be
congured as a two-channel system.
Extensive built-in diagnostics help
nd failures quickly and reduce downtime. To enable diagnostics by using
dynamic signals, the MCB 140
features two pulsed outputs, making
it possible to nd wiring faults.