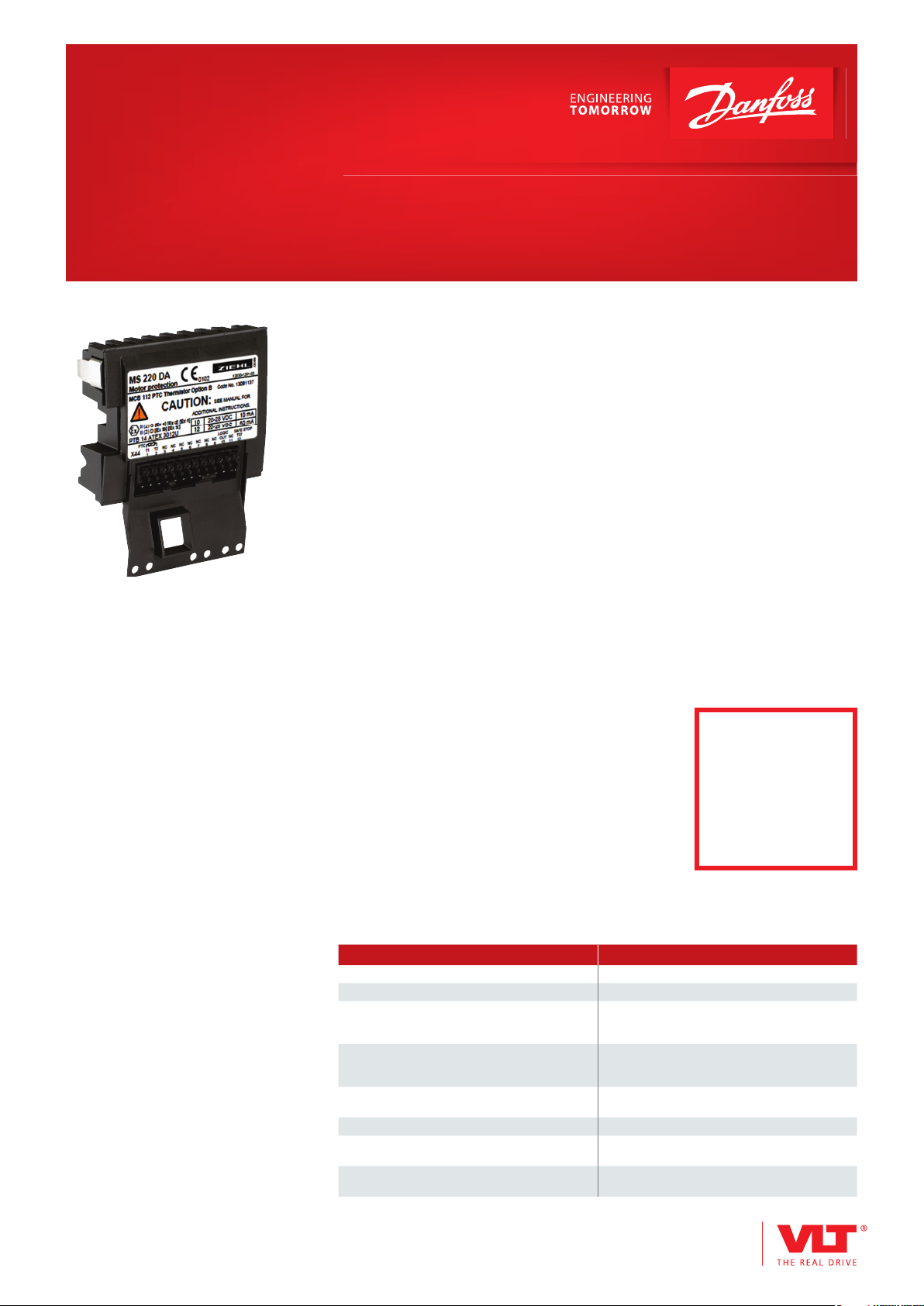
Fact Sheet
VLT® PTC Thermistor Card MCB 112
VLT® PTC Thermistor Card MCB 112
improves the motor condition
surveillance in the Danfoss VLT®
AutomationDrive, VLT® HVAC Drive
and VLT® AQUA Drive frequency converters, compared to the standard
built-in ETR function with thermistor
terminal.
The MCB 112 option enables VLT® drives
to be used in systems that require
control of motors located in potentially
explosive environments. When MCB 112
is used with a VLT® drive with integrated
Safe Torque Off, the drive is certified to
coast the motor when motor temperature becomes too high. This helps to
eliminate the risk of explosion due to
an over-temperature condition in the
ATEX-certified motor (Ex d, Ex e, Ex n,
Ex tb and Ex tc).
ATEX Directive 94/9/EC is an EU directive that describes equipment permitted in an environment with a potentially explosive atmosphere.
The option is ATEX certified for
protection of certified Ex proof
motors, regardless of supplier, in zones
1 and 2 (gas) and zones 21 and 22
(dust), in accordance with the
dedicated additional measures of the
Ex protection system of the motor.
The frequency converter itself is not
ATEX rated and must be situated outside the hazardous area.
The Safe Torque Off function can be
used with external safety devices (with
integrated “&” function) and is compatible with simultaneous use of the
MCB 112.
Collaboration and approval
The MCB 112 is a standard plug-in
option for VLT® AutomationDrive, VLT®
HVAC Drive and VLT® AQUA Drive with
integrated Safe Torque Off.
Alarm handling
The MCB 112 surveillance function
detects motor overheating, possible
short circuits, or open circuit due to
breaks in the sensor circuit. It also
provides alarm logging, diagnosis and
intelligent evaluation, thus facilitating
troubleshooting.
Integrated Safe Torque Off
The MCB 112 uses the Safe Torque Off
function of the drive which is approved
in accordance with SIL2 EN 61508.
A mains disconnect contactor is not
necessary.
Feature Benefit
Independent of motor supplier Flexible choice of motor type
No binding between the different components Easy service
Temperature surveillance is performed
directly in the frequency converter
Can assume sole protection of an Ex d, Ex e,
Ex n, Ex tb and Ex tc certified motor within the
installation/facility
Current limiting feature
(only VLT® AutomationDrive)
Integrated safety technology Reduced cabling and commissioning cost
Plug-and-play
Isolated solution (PELV)
The MCB 112 has been developed in
collaboration with the company ZIEHL
industrie-elektronik, an experienced
specialist in thermal motor protection
in potentially explosive atmospheres,
approved by the PTB (PhysikalischTechnische Bundesanstalt).
Ex
Suitable for
operation of Ex d,
Ex e & Ex n and Ex
tb & Ex tc certi ed
motors
– No external components needed
– Less space required
– Reduced system cost
External components saved
Less costly Ex-e motors can be applied
– Swift and cost-efficient upgrade on-site
– The drive automatically identifies the option
Digital outputs are galvanically isolated from
supply and high-voltage
www.vlt-drives.danfoss.com
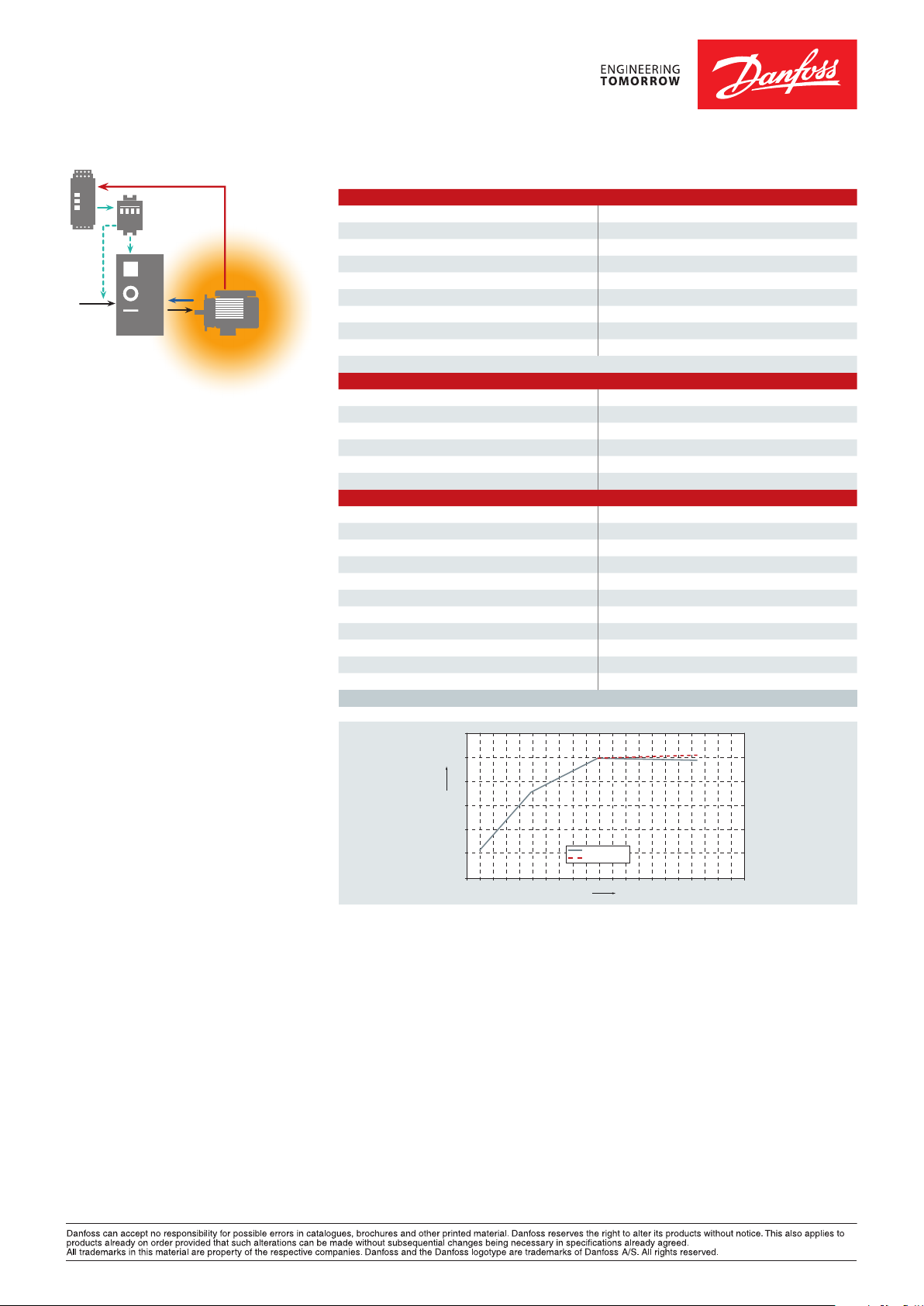
Thermistor relay
Contactor
Stop
Non-explosive hazard zone
ATEX
certified
motor
Explosive hazard zone
The integrated MCB 112 replaces external
components like thermistor relay, contactor and
wiring, since the drive communicates directly with
the motor.
Current limiting feature
VLT® AutomationDrive has a feature
that makes it possible to apply “Ex-e”
certified motors instead of the more
expensive “Ex-d” certified motors for
ignition protection. The combination of
the parameter setup and the MCB 112
ensures that the VLT® AutomationDrive
will never provide sufficient current to
cause the motor to overheat.
The feature is easy to use
Enter relevant data from the motor
name plate via variable speed current
limit parameters in the frequency
converter. From this data, the drive
creates an upper limit that limits the
current provided dependent upon the
motor speed.
Uncomplicated
Flexible use of speed control with
motors certified with increased safety
“e” ignition protection.
Compact
With increased safety “e” certification,
distinctly smaller frame size, lower
weight and lower costs compared
to speed control of motors with
flameproof enclosure “d” certification.
Flexible
Easy mix and match, resulting in
smaller stocks of motors and frequency
converters.
Specifications
PTC-thermistor connection
Monitoring function Temperature monitoring by means of PTC sensors
PTC compliant with DIN 44081, DIN 44082
Number of sensors in series Set with 3 -...6 resistors
Cut-out-point 3.3 kΩ .... 3.65 kΩ ... 3.85 kΩ
Reclosing point 1.7 kΩ .... 1.8 kΩ ... 1.95 kΩ
Collective resistance cold sensors < 1.65 kΩ
Terminal voltage (sensors) ≤ 2.5 V for R ≤ 3.65 kΩ, ≤ 9 V for R = ∞
Terminal current (sensors) ≤ 1 mA
Short circuit 20 Ω ≤ R ≤ 40 Ω
Max. sensor cable length for short-circuit detection 2 × 250 m with 0.5 mm
Testing conditions
EN 60 947-8
Rated impulse voltage 6000 V
Over voltage category III
Contamination level 2
EMC – Immunity industry standard EN61000-6-2
EMC – Emission industry standard EN61000-6-4
Safety-related parameters
EN 61508 for Ta = 40° C ongoing
SIL 2
HFT Type A
PFD (test interval one year) 3,37E-04
SFF 78%
λ
SD
λ
SU
λ
DU
2,35E-07
3,73E-08
7,69E-08
MTBF 179 years
Operating mode Low demand mode
Hardware architecture 1oo1
Ordering number: 130B1137
1.1
1
0.9
0.8
I/In
0.7
0.6
0.5
0 5 10 15 20 25 30 35 40 45 50 55 60 65 70 75 80 85 90 95 100 105
Incorrect area
Correct area
Star connection
Delta connection
f/Hz
Variable speed current limitation, from the EC type-e xamination certifi cate of the Ex e motor. Enter the relevant
information from the motor nameplate into the control panel of the drive. Then the drive will calculate max.
current in relation to the motor speed. The curve represents the limit under which the current must be kept to
prevent overheating of the motor. The nodes for the curves are determined by measurement from the Ex
notifi ed body. With a second protective device like the MCB 112, direct temperature monitoring is possible via a
triple PTC thermistor circuit. Direct temperature monitoring also detects malfunctions such as blocked
ventilation or inadmissibly high ambient temperatures.
Economical
Lower investment costs enable faster
payback when speed control is used to
achieve energy savings.
No need for matched pairs
Suitable for operation of Ex d, Ex e, Ex n,
Ex tb and Ex tc certified motors without
the need for matched pair motor-drive.
Universal
Universal solution for the entire power
range of 0.25 to 630 kW.
2
, 2 × 800 m with 1.5 mm
2
Danfoss VLT Drives, Ulsnaes 1, DK-6300 Graasten, Denmark, Tel. +45 74 88 22 22, Fax +45 74 65 25 80, www.danfoss.com/drives, E-mail: info@danfoss.com
DKDD.PFO.614.A1.02 © Copyright Danfoss Power Electronics | Danfoss VLT Drives PE-MSMBM | October 2014