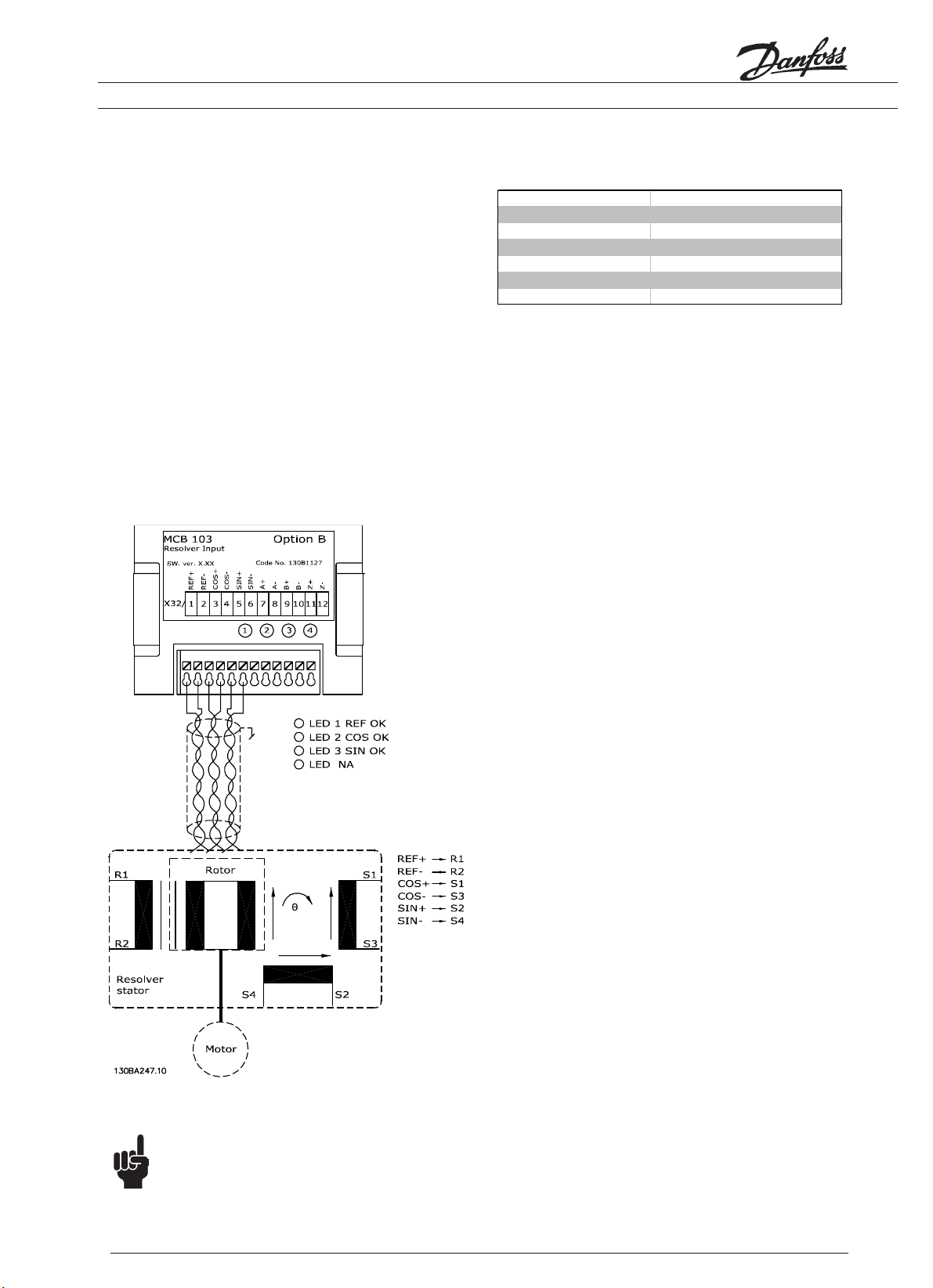
Resolver Option MCB 103
VLT® AutomationDrive FC 300
MCB 103 Resolver Option is used for interfacing resolver
motor feedback to FC 300 AutomationDrive. Resolvers
are used basically as motor feedback device for
Permanent Magnet brushless synchronous motors.
When the Resolver option is ordered separately the kitWhen the Resolver option is ordered separately the kit
When the Resolver option is ordered separately the kit
When the Resolver option is ordered separately the kitWhen the Resolver option is ordered separately the kit
includes:includes:
includes:
includes:includes:
••
• Resolver Option MCB 103
••
• Enlarged LCP fixture and enlarged terminal cover
Selection of parameters: 17-5x resolver Interface.
MCB 103 Resolver Option supports a various number of
resolver types.
Reso lver specifications:
Resolver poles
Resolver In put Voltage
Resolver Input Frequency
Transformation ratio
Secondary input voltage Max. 4 Vrms
Secondary load App. 10 k?
Par. 17-50: 2 *2
Par. 17-51: 2.0-8.0 Vrms *7.0 Vrms
Par. 17-52: 2-15 kHz *10.0 kHz
Par. 17-53: 0.1-1.1 *0.5
NB!NB!
NB!
NB!NB!
The resolver option MCB 103 can only be used with rotor-supplied resolver types.
Stator-supplied resolvers cannot be used.
MI.33.I1.02 - VLT is a registered Danfoss trademark
1
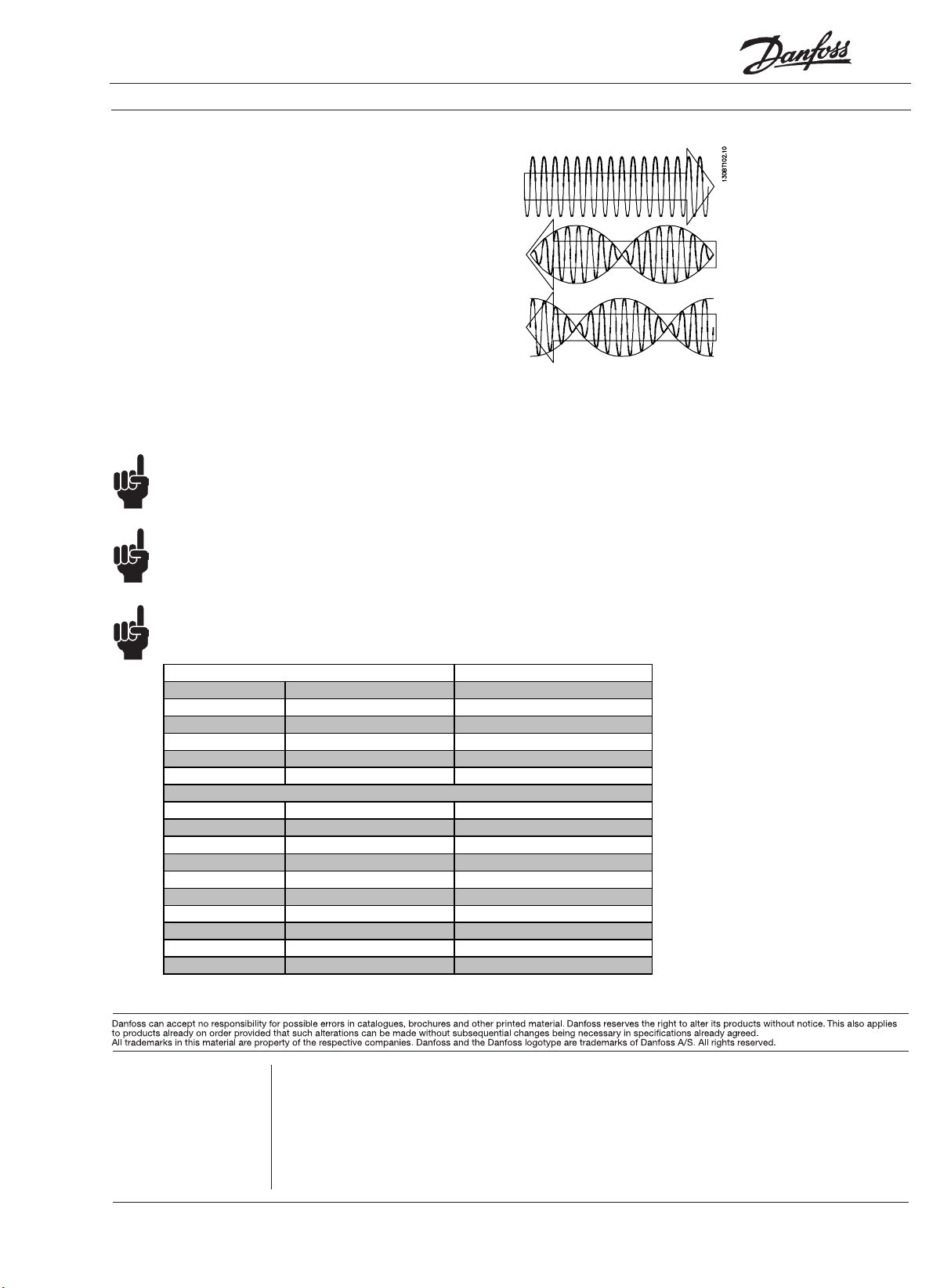
VLT® AutomationDrive FC 300
LED Indicators
LED 1 is on when the reference signal is OK to resolver
LED 2 is on when Cosinus signal is OK from resolver
LED 3 is on when Sinus signal is OK from resolver
The LEDs are active when par. 17-61 is set to Warning
or Trip.
Set-up example
In this example a Permanent Magnet (PM) Motor is used with the resolver as speed feedback. A PM motor
must usually operate in flux mode.
Wiring:Wiring:
Wiring:
Wiring:Wiring:
The max. cable length is 150 m when a twisted pair type of cable is used.
NB!NB!
NB!
NB!NB!
Resolver cables must be screened and separated from the motor cables.
NB!NB!
NB!
NB!NB!
The screen of the resolver cable must be correctly connected to the de-coupling
plate and connected to chassis (earth) on the motor side.
NB!NB!
NB!
NB!NB!
Always use screened motor cables and brake chopper cables.
Adjust following parameters:
Par. 1-00 Configuration Mode
Par. 1-01 Motor Control Principle Flux with feedback [3]
Par. 1-10 Motor Construction PM, non salient SPM [1]
Par. 1-24 Motor Current Nameplate
Par. 1-25 Motor Nominal Speed Nameplate
Par. 1-26 Motor Contr. Rated Torque Nameplate
MA is not possible on PM motors
Par. 1-30 Stator Resistance Motor data sheet
Par. 1-37 d-axis Inductance (Ld) Motor data shee t (mH)
Par. 1-39 Motor Poles Motor data sheet
Par. 1-40 Back EMF at 1000 RPM Motor data sheet
Par. 1-41 Motor Angle Offset Motor data sheet (Usually zero)
Par. 17-50 Poles Resolver data sheet
Par. 17-51 Input Voltage Resolver data sheet
Par. 17-52 Input Frequency Resolver data sheet
Par. 17-53 Transformation Ratio Resolver data sheet
Par. 17-59 Resolver Interface Enabled [1]
Speed closed loop [1]
130R0312
Rev. 2007-05-07
*MI33I102*