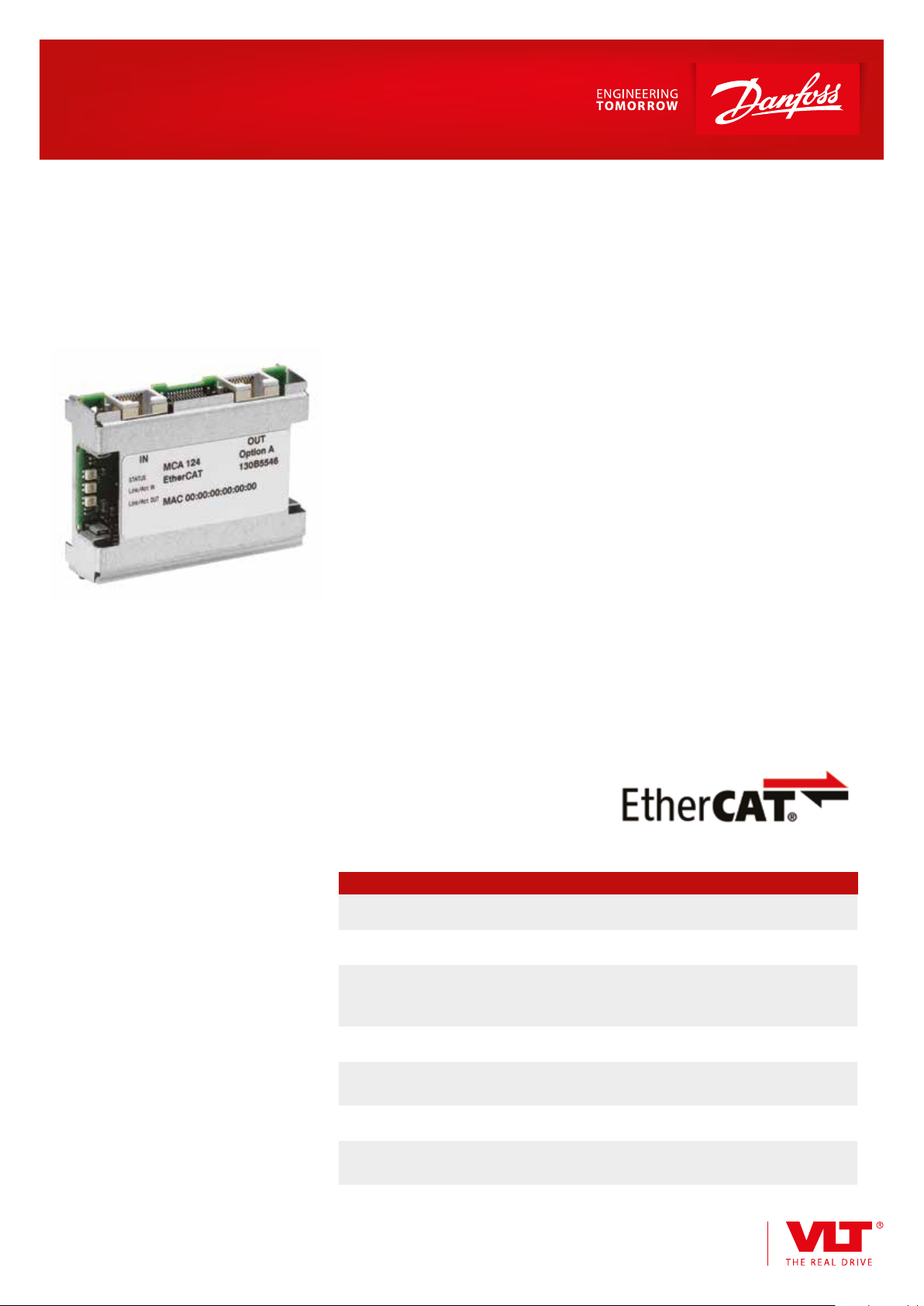
VLT® EtherCAT MCA 124
Cost-ecient connectivity to EtherCAT based networks
Ordering number
Uncoated 130B5545
Coated 130B5646
The VLT® EtherCAT MCA 124 interface
allows the VLT® AutomationDrive to
participate in EtherCAT networks for
high performance applications. The
interface utilizes the newest developments from the EtherCAT Technology
Group and gives the user full functionality, the highest degree of
exibility and outstanding performance.
The MCA 124 option supports full
control of the drive, access to I/O
modules and control of the advanced
synchronising and position option
(VLT® Motion Control MCO 305).
Ease of use
The Cyclical I/O size (PDO) is fully
exible and can be adjusted to t the
application.
This removes the transportation of
empty data, and so improves the
performance of both the network and
the PLC.
The conguration of the drive can be
read or written via the PC based VLT®
Motion Control Tool MCT 10 over the
EtherCAT bus. This enables cost
eective handling for backup and
restoring of drive conguration, with
no need for separate cabling.
The built-in web server provides
remote diagnosis and reading of basic
drive parameters. This cost-reducing
feature eliminates the need to install a
separate computer to monitor the
system.
Features Benets
Uses standard Ethernet cable
EoE, Ethernet over EtherCAT
E-mail notier
Two Ethernet ports with built-in switch
Support of DCP (discovery and conguration
protocol)
Variable PDO size
PDOs fullly congurable from master system
Cost eective cabling with standard, o the
shelf cables
Uses standard Ethernet TCP/IP communication protocols
Higher system performance as no computer
is needed to monitor alarms. The VLT®
EtherCAT 124 noties if warnings or alarms
occur.
• Simple cabling
• No need for expensive switches or hubs
Makes topology and neighbourhood
recognition and an IP-address assertion from
PLC possible
Better use of the EtherCAT bandwidth and
the PLC I/O memory
Reduced conguration time when exchanging the drive, communication parameters are
set from central location
Facts about our products
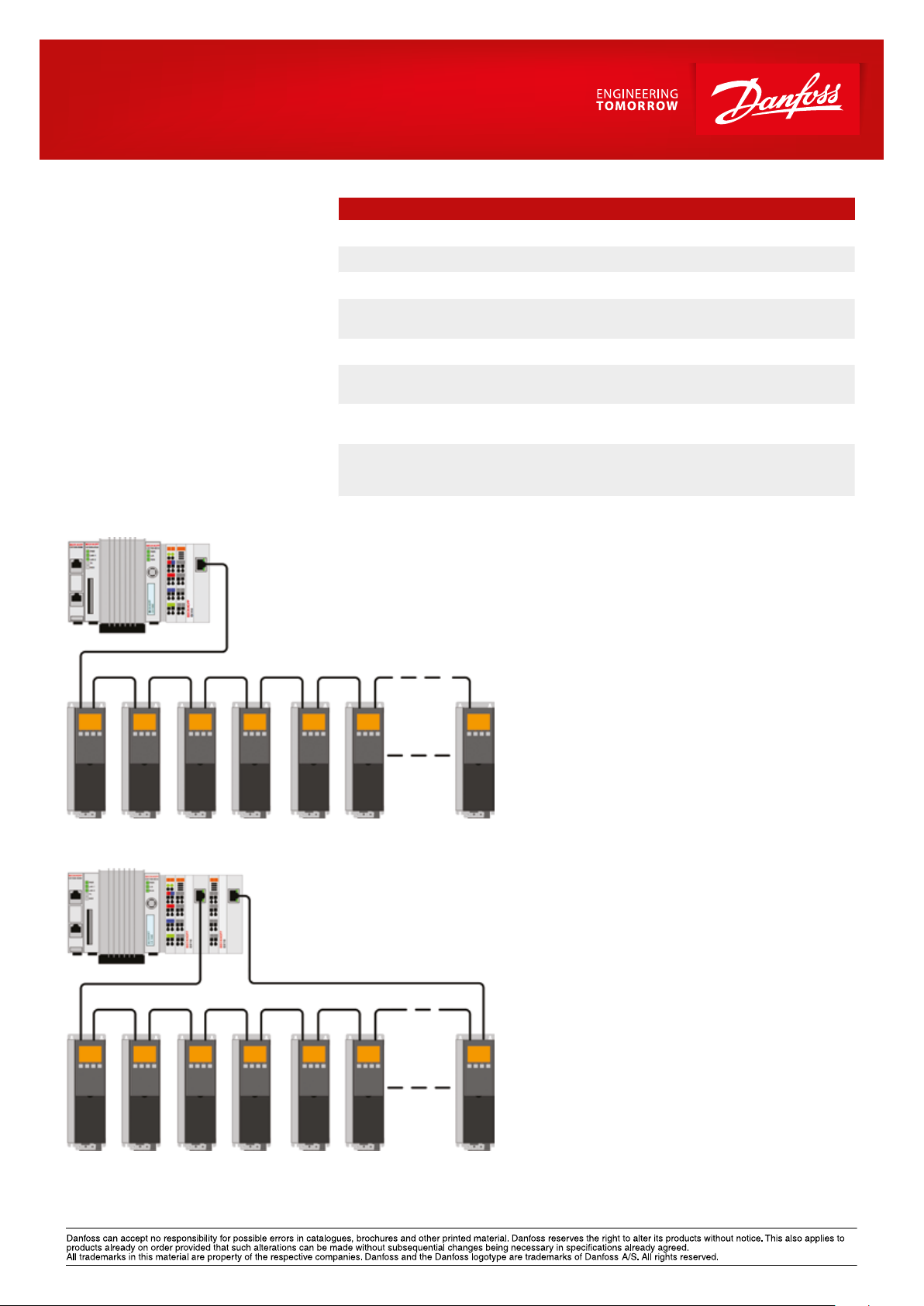
Thanks to its easy handling, EtherCAT
is a cost-eective solution that is easy
to implement from simple I/O up to
high-speed servo applications with
synchronizing capabilities.
Application protocols
CoE: CAN over EtherCAT Support
EoE: Ethernet-over-EtherCAT-support
FoE: File over EtherCAT, for update of the option rmware
Topology
Line Topology:
HTTP
SMTP (Simple Mail Transfer Protocol) for e-mail notication
DHCP
FTP (File Transfer Protocol) Server for le up and download
TCP/I PSocketPort
(Hypertext Transfer Protocol)
for diagnosis via built-in web server
(Dynamic Host Conguration Protocol)
for automatic IP address conguration
for easy access to drive conguration data from MCT 10
Ring Topology:
Danfoss VLT Drives, Ulsnaes 1, DK-6300 Graasten, Denmark, Tel. +45 74 88 22 22, Fax +45 74 65 25 80
www.danfoss.com/drives • info@danfoss.com
DKDD.PFO.600.A2.02 VLT® is a trademark of Danfoss A/S PE-MMSC 2014.09