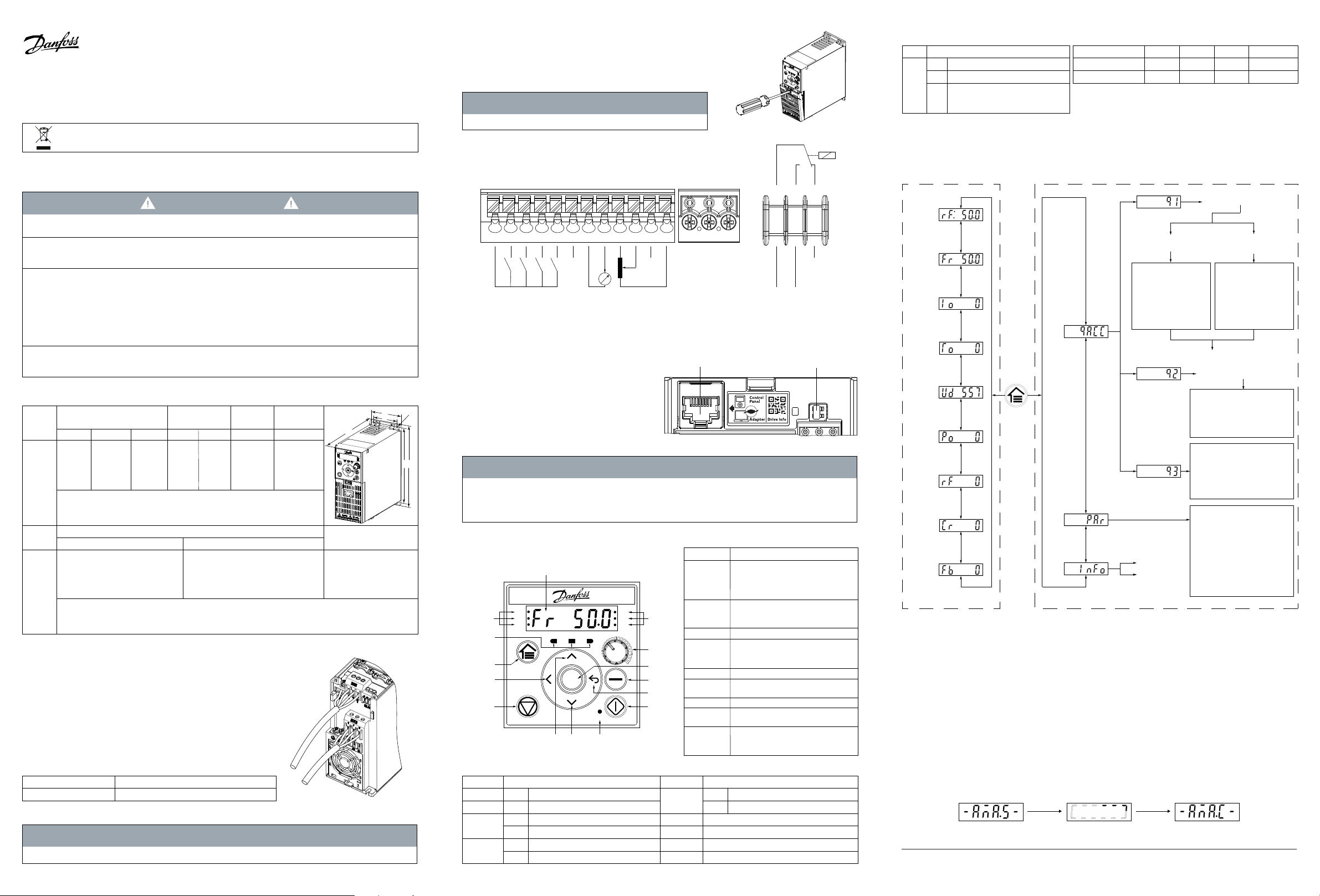
Operating Guide
iC2-Micro Frequency Converters
*M0033001*
130R1215
1 Introduction
This Operating Guide provides necessary information for qualified personnel to install and commission the
AC drive. Read and follow the instructions to use the drive safely and professionally.
Do not dispose of equipment containing electrical components together with domestic waste.
Collect it separately in accordance with local and currently valid legislation.
2 Safety
Pay particular attention to the safety instructions and general warnings to avoid the risk of death, serious
injury, and equipment or property damage.
WARNING
HIGH VOLTAGE
AC drives contain high voltage when connected to AC mains input, DC supply, or load sharing.
UNINTENDED START
The motor may start from control panel, I/O inputs, fieldbus, or MyDrive® Insight at any time, when the drive is connected
to the AC mains, DC supply, or load sharing.
DISCHARGE TIME
The drive contains DC-link capacitors, which can remain charged even when the drive is not powered. High voltage can be
present even when the warning indicator lights are off.
- Stop the motor, and disconnect AC mains, permanent magnet type motors, and remove DC-link supplies, including
battery back-ups, UPS, and DC-link connections to other drives.
- Wait for the capacitors to discharge fully and measure it before performing any service or repair work.
- The minimum waiting time is 4 minutes for MA01c, MA02c, MA01a, and MA02a drives, and 15 minutes for MA03a, MA04a,
and MA05a drives.
LEAKAGE CURRENT
Leakage currents of the drive exceed 3.5 mA. Make sure that the minimum size of the ground conductor complies with the
local safety regulations for high touch current equipment.
3 Installation
3.1 Mechanical Dimensions
Enclosure
size
MA01c
MA02c
MA01a
MA02a
A A
150 (5.9)
176 (6.9)
150 (5.9)
186 (7.3)
Height
[mm (in)]
(1)
216 (8.5)
232.2 (9.1)
202.5 (8.0)
240 (9.4)
Width
[mm (in)]
a B b C
70 (2.8)
75 (3.0)
70 (2.8)
75 (3.0)
55 (2.2)
59 (2.3)
55 (2.2)
59 (2.3)
140.4 (5.5)
150.5 (5.9)
140.4 (5.5)
176.4 (6.9)
[mm (in)]
143 (5.6)
157 (6.2)
158 (6.2)
175 (6.9)
Depth
Mounting holes
(2)
[mm (in)]
4.5 (0.18)
4.5 (0.18)
4.5 (0.18)
4.5 (0.18)
D
C
MA03a
MA04a
Data for MA03a to MA05a will be available in next release.
MA05a
Enclosure
size
MA01c
MA02c
MA01a
MA02a
1x200–240 V 3x380–480 V
0.37–0.75 (0.5–1.0)
1.5 (2.0)
–
Power [kW (hp)]
–
–
0.37–1.5 (0.5–2.0)
2.2–4.0 (3.0–5.4)2.2 (3.0)
Maximum weight
[kg (lb)]
1.0 (2.4)
1.3 (2.9)
1.1 (2.4)
1.6 (3.5)
MA03a
MA04a
Data for MA03a to MA05a will be available in next release.
MA05a
Note:
(1) Including decoupling plate. (2) The potentiometer on the local control panel extends 6.5 mm (0.26 in) from the drive.
(3) Not including decoupling plate.
3.2 Connecting to Mains and Motor
• Mount the ground wires to the PE terminal.
• Connect motor to terminals U, V, and W.
• Mount mains supply to terminals L1/L, L2, and L3/N (3-phase) or L1/L
and L3/N (single-phase) and tighten.
• For required maximum screwing torque, see the back of terminal cover.
3.3 Load Sharing/Brake
Use 6.3 mm (0.25 in) insulated connectors designed for high voltage
for DC (load sharing and brake).
Contact Danfoss or refer to the drive's Design Guide.
Table 1: Connect Terminals
Load sharing
Brake
Recommended connector type (only for drives below 7.5 kW/10 hp): Ultra-Pod
Fully Insulated FASTON Receptacles and Tabs, 521366-2, TE connectivity.
-UDC and +UDC/+BR
-BR and +UDC/+BR
Illustration 1: Mounting of Ground
Cable, Mains, and Motor Wires
Ø D
B
b
a
A
(3)
NOTICE
Voltage levels of up to 850 V DC may occur between terminals +UDC/+BR and -UDC. Not short-circuit protected.
3.4 Control Terminals
• All control cable terminals are located underneath the terminal
cover in front of the drive.
• See the back of the terminal cover for outlines of control terminals
and switches.
NOTICE
Remove the terminal cover with a screwdriver, see illustration 2.
+24 V OUT
DI1 (P 9.4.1.2)
DI2 (P 9.4.1.3)
DIO (P 9.4.1.4)
DI3 (P 9.4.1.5)
DI4 (P 9.4.1.6)
12 13 14 15 17 18 20 31 32 33 34 35 61 68 69
Jog
GND
Frequency
output
+24 V OUT
Start
Reverse
Reset (DI)
GND
+10 V OUT
AO1 (G 9.5.1)
AI1 (G 9.5.2)
AI2 (G 9.5.3)
0-10 V
1K Ohm
0-20 mA
Reference Function: Fault
GND
GND
COM RS 485
Illustration 3: Overview of Control Terminals in PNP-configuration with Factory Setting (Speed Control Mode)
3.5 RJ45 Port and RS485 Termination Switch
iC2-Micro drive has a RJ45 port which complies
with Modbus 485 protocol.
The RJ45 port is used for connecting:
• External control panel.
• PC tool (MyDrive® Insight) via an adapter.
• Offline configuration tool for parameter settings
when the drive is not powered on.
Note: (1) The tool is not available currently.
(1)
(1)
(1)
RJ45 port
Illustration 4: RJ45 Port and RS485 Termination Switch
Illustration 2: Removing Terminal Cover
P RS 485
N RS 485
Relay (P 9.4.3.1)
01 02 03
RS485 termination switch
(ON=RS485 terminated, OFF=Open)
1 2
O N
NOTICE
- The RJ45 port supports up to 3 m (9.8 ft) of shielded CAT5e cable which is NOT used to directly connect the drive to a PC.
Failure to follow this notice causes damage to the PC.
- RS485 termination switch should be set to ON if the drive is at the end of the fieldbus.
- Do not operate RS485 termination switch when the drive is powered on.
4 Programming
4.1 Control Panel
Main display
Status
indicators
Operating
indicators
Home/
Menu
Left
Stop/
Reset
Table 3: Status and Operating Indicator Lights
MON Shows the drive status.
PGM The drive is in programming status.
TOR
LOC
Up Down Run indicator
Illustration 5: Indicators and Operation Keys
FunctionName
On
On
The drive is in torque mode.
On
The drive is in speed mode.
Off
The drive is in local mode.
On
The drive is in remote mode.
Off
Status
indicators
Potentiometer
OK
Remote
/Local
Back
Start
Table 2: Operation Keys and Potentiometer
Name
Function
(1) Toggles between status display and
Home/Menu
main menu. (2) Long press to access
the shortcut menu for quickly reading
and editing parameters.
Up/Down
Switches status/parameter group/parameter numbers, and tunes the parameter values.
Moves the cursor 1 bit to the left.
Left
Navigates to the previous step in the
Back
menu structure or cancels the setting
during tuning parameter values.
Confirms the operation.
OK
Remote/Local
Stop/Reset
Potentiometer
Note: (1) The shortcut menu is not available currently.
Toggles between remote and local
mode.
Starts the drive in local mode.
Start
Stops the drive in local mode, or resets
the drive to clear a fault.
Changes the reference value when the
reference value is selected as potentiometer.
FunctionName
The drive is in reverse direction.
REV
ST2
WARN
READY
FAU LT
On
The drive is in forward direction.
Off
Refer to Table 5 Multiple Setups.
Steadily lit when a warning occurs.
Steadily lit when the drive is ready.
Flashes when a fault occurs.
(1)
Table 4: Run Indicator Lights
FunctionName
OnOffThe drive is in normal operation.
RUN
The drive has stopped.
In the motor-stopping process; or
Flash
the drive received a RUN command,
but no frequency output.
Table 5: Multiple Setups
ST2 Off On Flash Flash quickly
Active setup
Programming setup
Note:
(1) Select active setup in parameter P6.6.1 Active Setup.
(2) Select programming setup in parameter P6.6.2 Programming Setup.
(1)
(2)
Setup 1
Setup 1
Setup 2 Setup 2
Setup 2
Setup 1
Setup 2
Setup 1
4.2 Operation with Control Panel
After the drive is powered up, press the Home/Menu key to toggle between status display and main menu.
Use the Up/Down keys to select items, and press the OK key to confirm selection.
Status Display
(MON status indicator light is on)
Reference
Setting
(1)
(Hz)
Output
Frequency
(Hz)
Motor
Current
(A)
Quick
Access
Torque
(Nm)
Udc
Voltage
(V)
Power
(kW)
Reference
(2)
(%)
Full
Parameters
Customer
Readout
(3)
(Unit)
Events
Information
Feedback
(2)(3)
(Unit)
(1) Local mode only. (2) Remote mode only. (3) The status is only shown when the corresponding function is enabled.
Note:
(4) For AMA execution, refer to chapter Automatic Motor Adaptation (AMA). If parameter P5.4.3 Motor Control Principle is set as [0] U/f,
no need to execute AMA.
Illustration 6: Operation with Control Panel
Main Menu
(PGM status indicator light is on)
P4.2.1.1 Motor Type
Q1: Motor Data
*[0] IM Motor
P4.2.2.1 Nominal Power
P4.2.2.2 Nominal Voltage
P4.2.2.3 Nominal Current
P4.2.2.4 Nominal Frequ ency
P4.2.2.5 Nominal Speed
P4.2.1.2 Number of Poles
P4.2.2.3 Nominal Current
P4.2.2.5 Nominal Speed
P4.2.3.7 Motor Cont.
Rated Torque
P4.2.4.1 Back EMF
P4.2.1.2 Number of Poles
P4.2.1.3 AMA Mode
P5.4.1 Application Selection
Application
Q2:
Selection
Motor
Q3:
Control
Faults
Warnings
*[20] Speed Control Mode
[21] Process Control Mode
[22] Multi Speed Control Mode
[23] 3-wire Control Mode
[24] Torque Control Mode
P5.5.3.3 Reference Maximum
P5.5.3.4 Reference Minimum
P5.5.4.2 Ramp 1 Accel. Time
P5.5.4.3 Ramp 1 Decel. Time
P2.3.14 Max Output Frequency
P5.8.2 Motor Speed High Limit
Parameter group 1st level:
G1 Grid
G2 Power Conversion & DC-link
G3 Filters & Brake Chopper
G4 Motor
G5 Application
G6 Maintenance & Service
G8 Customization
G9 I/O
G10 Connectivity
PM Motor
[1] SPM or [3] IPM
(4)
4.3 Automatic Motor Adaptation (AMA)
+
• Via running AMA in VVC
bility between drive and motor, and thus enhances the motor control performance.
• Some motors may be unable to run the complete version of the test. In that case, select [2] Enable Reduced
AMA in parameter P4.2.1.3 AMA Mode.
• AMA completes within 5 minutes. For best results, run the following procedure on a cold motor.
Procedure:
1. Set motor data according to the motor nameplate.
2. If needed, set motor cable length in parameter P4.2.1.4 Motor Cable Length.
3. Set [1] Enable Complete AMA or [2] Enable Reduced AMA for parameter P4.2.1.3 AMA Mode, the main display
shows To start AMA, see illustration 7.
4. Press the Start key, the test runs automatically and the main display indicates when it is completed.
5. When AMA is completed, press any key to exit and return to normal operation mode.
mode, the drive builds a mathematical model of the motor to optimize compati-
To start AMA
AMA is running
Illustration 7: AMA Status Indications
AMA is completed
AQ379331704297en-000101 / 130R1215 | 1Danfoss A/S © 2022.02
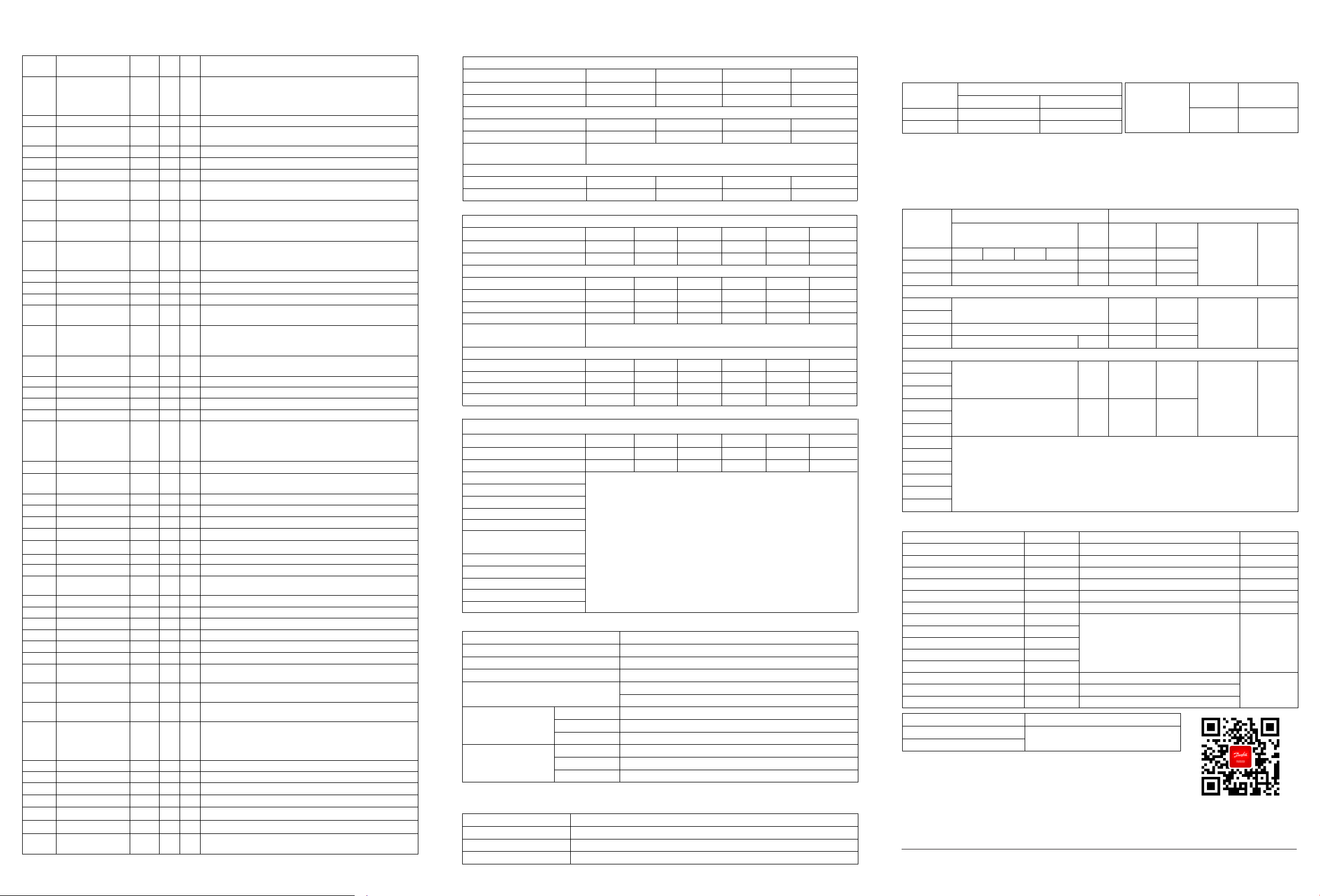
5 Troubleshooting
Table 6: Warning and Fault Events Summary
Number Description Warning Fault
Live zero error2
No motor3 No motor has been connected to the output of the drive.X – –
Mains phase loss
4
7 DC-link voltage exceeds the limit.X X –
DC overvoltage
DC undervoltage
8 DC-link voltage drops below the voltage warning low limit.X X –
Inverter overloaded9 More than 100% load for too long.X X –
Motor ETR overtemp-
10 Motor is too hot due to more than 100% load for too long.X X –
erature
Motor thermistor
11
overtemperature
Torque limit12
Overcurrent13
Ground fault14 Discharge from output phases to ground.– X X
Short circuit16 Short circuit in motor or on motor terminals.– X X
Control word timeout17 No communication to the drive.X X –
Brake resistor short-
25
circuited
Brake overload26
Brake IGBT/Brake
27
chopper short-circuited
Brake check28 Brake resistor is not connected/working.– X –
U phase loss30 Motor phase U is missing. Check the phase.– X X
V phase loss31 Motor phase V is missing. Check the phase.– X X
W phase loss32 Motor phase W is missing. Check the phase.– X X
Mains failure36
Internal fault38 Contact the local supplier.– X X
Overload T1540
Gate drive voltage fault46 –– X –
24 V supply low47 24 V DC may be overloaded.X X X
AMA calibration failed50 A calibration error has occurred.– X –
AMA check U
51 Wrong setting for motor voltage and/or motor current.– X –
52 Motor current is too low. Check the settings.– X –
AMA low I
AMA big motor53 The power size of the motor is too large for the AMA to operate.– X –
AMA small motor54 The power size of the motor is too small for the AMA to operate.– X –
AMA parameter range55
AMA interrupt56 The AMA is interrupted.– X –
AMA timeout57 –– X –
AMA internal58 Contact the local supplier.– X –
Current limit59 The drive is overloaded.X X –
External Interlock60 External interlock has been activated.– X –
Feedback error61 –X X –
Mechanical brake low63
Power card temp69
Drive initialized to
80 All parameter settings are initialized to default settings.– X –
default value
Auto DC brake87
Broken belt95 –X X –
Locked rotor99 Rotor is blocked.– X –
Motor rotating126 PM motor is rotating when AMA is performed.– X –
Back EMF too high127 The back EMF of PM motor is too high before starting.X – –
Parameter read onlyErr. 89 Parameters cannot be changed.– – –
Not while runningErr. 95 Parameters can only be changed when the motor is stopped.– – –
A wrong password
Err. 96
Note: (1) These faults may be caused by mains distortions. Installing a Danfoss line filter may rectify this problem.
was entered
(1)
and I
nom
nom
(1)
(1)
nom
X X –
X X X
X X –
X X –
X X X
– X X
X X –
– X X
X X –
X – –
– X –
– X –
X X X
X – –
– – –
Trip
lock
Signal on terminal 33 or 34 is less than 50% of the value set in parameter P9.5.2.3 T33 Low Voltage, parameter P9.5.2.5 T33 Low Current,
parameter P9.5.3.3 T34 Low Voltage, and parameter P9.5.3.5 T34 Low
Current.
Missing phase on the supply side, or the voltage imbalance is too
high. Check the supply voltage.
Thermistor or thermistor connection is disconnected, or the motor
is too hot.
Torque exceeds the value set in either parameter P5.10.1 Motor Tor-
que Limit or parameter P5.10.2 Regenerative Torque Limit.
Inverter peak current limit is exceeded. If this fault occurs on
power-up, check whether power cables are mistakenly connected
to the motor terminals.
Brake resistor is short-circuited, thus the brake function is disconnected.
The power transmitted to the brake resistor over the last 120 s
exceeds the limit. Possible corrections: Decrease brake energy via
lower speed or longer ramp time.
Brake transistor is short-circuited, thus brake function is disconnected.
This warning/fault is only active if the supply voltage to the drive is
less than the value set in parameter P2.3.7 Power Loss Controller
Limit, and parameter P2.3.6 Power Loss Action is NOT set to [0] No
Function.
Check the load connected to terminal 15 or remove short-circuit
connection.
The parameter values of the motor are outside of the acceptable
range. AMA does not run.
Actual motor current has not exceeded release brake current
within start delay time window.
The cutout temperature of the power card has exceeded the upper
limit.
Occurs in IT mains when the drive coasts, and the DC voltage is
higher than 830 V for 400 V units and 425 V for 200 V units. The
motor consumes energy on the DC link. This function can be enabled/disabled in parameter P2.3.13 Auto DC Braking.
Occurs when using a wrong password for changing a passwordprotected parameter.
Cause
6 Specifications
Table 7: Mains Supply 1x200–240 V AC
Normal overload 150% for 1 minute
Drive
Typical shaft output [kW (hp)]
Enclosure protection rating IP20 MA01c MA01c MA02c MA02a
Output current
Continuous (3x200–240 V) [A] 2.2 4.2 6.8 9.6
Intermittent (3x200–240 V) [A] 3.3 6.3 10.2 14.4
Maximum cable size
(Mains, motor) [mm ⁄AWG]
Maximum input current
Continuous (1x200–240 V) [A] 6.1 11.6 18.7 26.4
Intermittent (1x200–240 V) [A] 8.3 15.6 26.4 37
Table 8: Mains Supply 3x380–480 V AC MA01a–MA02a
Normal overload 150% for 1 minute
Drive
Typical shaft output [kW (hp)]
Enclosure protection rating IP20 MA01a MA01a MA01a MA02a MA02a MA02a
Output current
Continuous (3x380–440 V) [A] 1.2 2.2 3.7 5.3 7.2 9.0
Intermittent (3x380–440 V) [A] 1.8 3.3 5.6 8.0 10.8 13.7
Continuous (3x440–480 V) [A] 1.1 2.1 3.4 4.8 6.3 8.2
Intermittent (3x440–480 V) [A] 1.7 3.2 5.1 7.2 9.5 12.3
Maximum cable size
(Mains, motor) [mm ⁄AWG]
Maximum input current
Continuous (3x380–440 V) [A] 1.9 3.5 5.9 8.5 11.5 14.4
Intermittent (3x380–440 V) [A] 2.6 4.7 8.7 12.6 16.8 20.2
Continuous (3x440–480 V) [A]
Intermittent (3x440–480 V) [A] 2.3 4.0 7.5 10.8 14.4 17.5
Table 9: Mains Supply 3x380–480 V AC MA03a–MA05a
Normal overload 150% for 1 minute
Drive
Typical shaft output [kW (hp)]
Enclosure protection rating IP20 MA03a MA03a MA04a MA04a MA05a MA05a
Output current
Continuous (3x380–440 V) [A]
Intermittent (3x380–440 V) [A]
Continuous (3x440–480 V) [A]
Intermittent (3x440–480 V) [A]
Maximum cable size
(Mains, motor) [mm ⁄AWG]
Maximum input current
Continuous (3x380–440 V) [A]
Intermittent (3x380–440 V) [A]
Continuous (3x440–480 V) [A]
Intermittent (3x440–480 V) [A]
02A2 04A2 06A8 09A6
0.37 (0.5) 0.75 (1.0) 1.5 (2.0) 2.2 (3.0)
4/10
01A2 02A2 03A7 05A3 07A2 09A0
0.37 (0.5) 0.75 (1.0) 1.5 (2.0) 2.2 (3.0) 3.0 (4.0) 4.0 (5.5)
4/10
1.7 3.0 5.1 7.3 9.9 12.4
12A0 15A5 23A0 31A0 37A0 43A0
5.5 (7.5) 7.5 (10) 11 (15) 15 (20) 18.5 (25) 22 (30)
Data for MA03a to MA05a will be available in next release.
7 Ambient Conditions
Protection rating IP20 (IP21/Type 1 conversion kit as option).
Temperature during operation
Temperature during storage/transport
Relative humidity 5–95%, non-condensing during operation.
Altitude
Storage
Contamination level
Mechanical conditions
Transportation
Operation
Storage
Transportation
Operation
-10 °C to 50 °C (14 °F to 122 °F), up to 55 °C (131 °F) with derating.
-25 °C to 65/70 °C (-13 °F to 149/158 °F).
0–1000 m (3280 ft) without derating.
1000–3000 m (3280–9243 ft) with derating of 1%/100 m (328 ft).
IEC 60721-3-1, Class 1C2 (aggressive gases), Class 1S11 (dust/sand).
IEC 60721-3-2, Class 2C2 (aggressive gases), Class 2S5 (dust/sand).
IEC 60721-3-3, Class C4 (aggressive gases), Class 3S6 (dust/sand).
IEC 60721-3-1, Class 1M11.
IEC 60721-3-2, Class 2M5.
IEC 60721-3-3, Class 3M11.
8 Mounting Clearance
Table 10: Minimum Mounting Clearance
Enclosure size Minimun mounting clearance [maximum temperature 50 °C (122 °F)]
All enclosure sizes Above and below: 100 mm (3.9 in).
MA01a–MA05a, MA02c Sides: 0 mm (0 in).
MA01c (natural cooling) Sides: 0 mm (0 in) for 40 °C (104 °F), 10 mm (0.39 in) and above for 50 °C (122 °F).
9 EMC Compatibility and Motor Cable Length
iC2-Micro drive has 2 versions based on different EMC filter types:
(1) Drive with built-in EMC filter. (2) Drive with non built-in EMC filter.
Table 11: EMC Compatibility Motor Cable Length
Drive with builtin EMC filter
1x200–240 V
3x400–480 V
Maximum motor cable length (shielded), @4kHz
C1 (Conducted) C2 (Conducted)
5 m (16.4 ft)
–
15 m (49.2 ft)–
Table 12: Maximum Motor Cable Length
Maximum motor
cable length
Shielded
Unshielded
50 m (164 ft)
75 m (246 ft)
• Drive with built-in EMC filter fulfills radiated emission C2 limits.
• Drive with non built-in EMC filter fulfills conducted/radiated emission C4 requirements, and shielded
motor cable is recommended.
• The drive is designed to operate with optimum performance within the maximum motor cable lengths
defined in Table 12 Maximum Motor Cable Length.
10 Fuses and Circuit Breakers
Non cabinet Cabinet
iC2-Micro
kW (hp)
Standard fault
High fault
1x200-240 V
0.37 (0.5)
0.75 (1.0)
1.5 (2.0)
2.2 (3.0)
3x380-480 V
0.37 (0.5)
0.75 (1.0)
1.5 (2.0)
2.2 (3.0)
3.0 (4.0)
4.0 (5.5)
5.5 (7.5)
7.5 (10)
11 (15)
15 (20)
18.5 (25)
22 (30)
UL fuse CE fuse
T
RK1
Standard fault current rating 5 kA
J
– –
25 A
35 A
40 A 50 A
Data for MA03a to MA05a will be available in next release.
gG
CC
– –
UL circuit
breaker
ABB
5 kA
65 kA
CE circuit
breaker
EATON
–
PKZM4-25MS165-25
PKZM4-32MS165-32
PKZM4-50MS165-42
PKZM0-16MS165-1615 A 16 A
PKZM4-32MS165-3230 A 40 A
Test cabinet size
[Height x Width x
Depth] [mm (in)]
500 x 400 x 260
(19.7 x 15.7 x 10.2)
500 x 400 x 260
(19.7 x 15.7 x 10.2)
Minimum
cabinet
volume [L]
11 Accessories and Spare Parts
Accessories AccessoriesCode number
IP21/Type 1 conversion kit, MA01c
IP21/Type 1 conversion kit, MA02c
IP21/Type 1 conversion kit, MA01a
IP21/Type 1 conversion kit, MA02a
IP21/Type 1 conversion kit, MA03a
IP21/Type 1 conversion kit, MA04a
IP21/Type 1 conversion kit, MA05a
NEMA 1 conversion kit, MA01c
NEMA 1 conversion kit, MA02c
NEMA 1 conversion kit, MA01a
NEMA 1 conversion kit, MA02a
NEMA 1 conversion kit, MA03a
NEMA 1 conversion kit, MA04a
NEMA 1 conversion kit, MA05a
Spare parts Code number
Cooling fan
Spare parts kit
132G0188
132G0189 132G0203
132G0190 132G0204
132G0191 132G0205
132G0192 132G0206
132G0193 132G0207
132G0194
132G0195
132G0196
132G0197
132G0198
132G0199
132G0200
132G0201
Decoupling plate mounting kit, MA01c
Decoupling plate mounting kit, MA02c
Decoupling plate mounting kit, MA01a
Decoupling plate mounting kit, MA02/03a
Decoupling plate mounting kit, MA04/05a
Connector for common DC/brake resistor
HMI and related accessories
Harmonic and EMC filter
Brake resistors
dU/dt filter
Refer to the Design Guide.
Code number
132G0202
Not available
currently.
Refer to the
Design Guide.
12 Technical Documentation
Scan the QR code (or, after scanning the QR code, click Global English to
select your local region's website), and search iC2 to access more technical
documents.
Danfoss A/S
Ulsnaes 1
DK-6300 Graasten
drives.danfoss.com
Danfoss can accept no responsibility for possible errors in catalogs, brochures, and other printed material.
Danfoss reserves the right to alter its products without notice. This also applies to products already on
order provided that such alterations can be made without subsequential changes being necessary in
specifications already agreed. All trademarks in this material are property of the respective companies.
Danfoss and the Danfoss logotype are trademarks of Danfoss A/S. All rights reserved.
AQ379331704297en-000101 / 130R1215 | 2Danfoss A/S © 2022.02
52
52