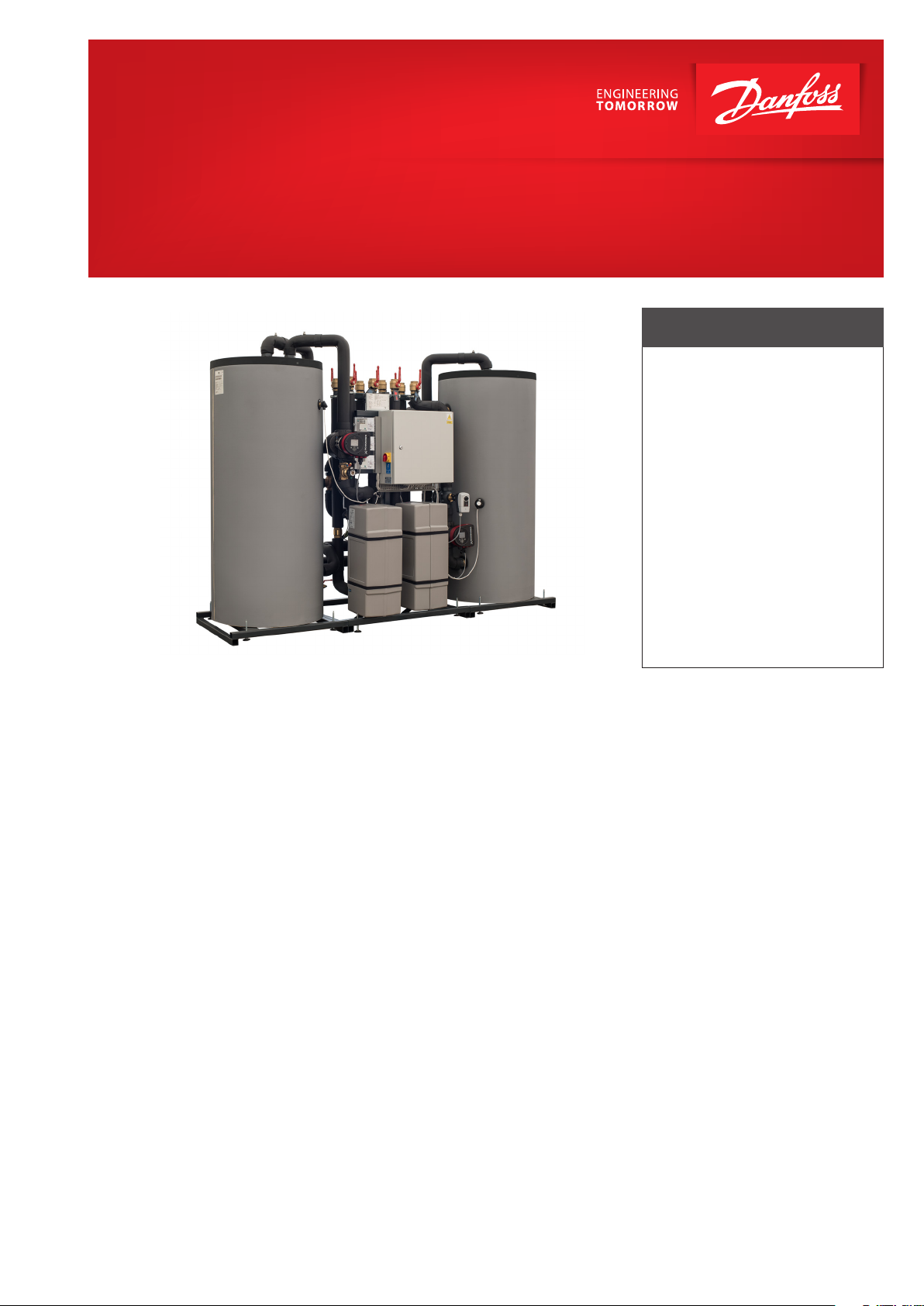
Fact sheet
HRU – Heat Recovery Unit
FEATURES AND BENEFITS
• Substations with high quality
components designed for heat recovery
applications fully customized by use
of 3D-tools to fit individual needs
• All control components in the substation
are high quality Danfoss components
like: heat exchanger, control valves,
shut-off valves, energy meter, shutoff valves and automatic controls
• Danfoss prefabricated substations
reduces space demand approximately
30% compared to build-on-site solutions
• Easy to install and use with remote
access via Danfoss free cloud based
ECL portal or via other communication
protocols like MODBUS
• All Danfoss products are manufactured
according PED 97/23/ EC European
Pressure Directive, and Danfoss is
compliant to ISO9001/ISO14001/
iATF 16949 automotive
Designed for heat recovery
The Heat Recovery Unit is designed to
recover the waste heat from refrigeration installations, where CO2 is used. Recovered heat can be used for own heating purposes or returned to District
Heating Utility network. It suits perfectly for supermarkets equipped with
refrigerators. System include heating
substation with accumulation tanks.
Remote controlling and monitoring
Danfoss automatic controller ECL offers
more possibilities for external communication. Traditional SCADA solutions
can communicate with the controller via a Modbus protocol. Further
Danfoss offers a web-based SCADA
solution called ECL portal (ecl. portal.
danfoss.com), which enables remote
controlling, monitoring and alarming
functionalities from the sub- station.
Visualization of the ECL portal gives
you easiness of use, and access via PC
or Smartphone improves the level of
service and reduce costs due to 24/7
access.
Construction / installation
Heat Recovery Unit is designed as
floor station and it is delivered in one
piece, with possibility to be split into
3 parts, which allows to transport station thru narrow corridors. All heat
exchangers are produced in Micro
Plate technology develop by Danfoss,
which significantly increase substation
performance and lifetime. Standard
unit layout allows to prepare connection piping inside the builing before
station is delivered. Piping prepared
with automatic welding machines ensure highest possible welding quality.
Friendly solution for climate
Heat recovery unit is environmental
friendly as it saves globe from unnecessary CO2 emissions. Especially supermarkets can accumulate excess heat
from cooling systems to heat up shop
area. In some areas waste heat via
heating networks can be transferred
to household. System efficiency ensure short “return of investment” time
and allows to save money for heating
in longer term.
Prefabricated substations enable
top quality and shorten installation work on the building site
The Heat Recovery units are produced
based on a 3D models prepared by
our design department. All components like: heat exchangers, control
valves, pumps and measuring equipment are virtually connected with
piping. Based on 3D-drawings pipes
are bent, cut and welded with support of automated machines ensuring
supreme quality and short delivery
time. Units are designed as modular
constructions, which makes transportation and assembly easier. Heating
units includes an electrical wired panel, which is functionally tested and
ready to use after connecting power
supply to the cooling substation on
site. Danfoss substation is a complete product: designed, produced
and tested – ready for use. Danfoss
has more than 40 years of experience
in production of substations, which
guarantees great functionality.
Need a design of substation?
Just send us:
• Heating demand
• CO2 heat capacity
www.danfoss.com
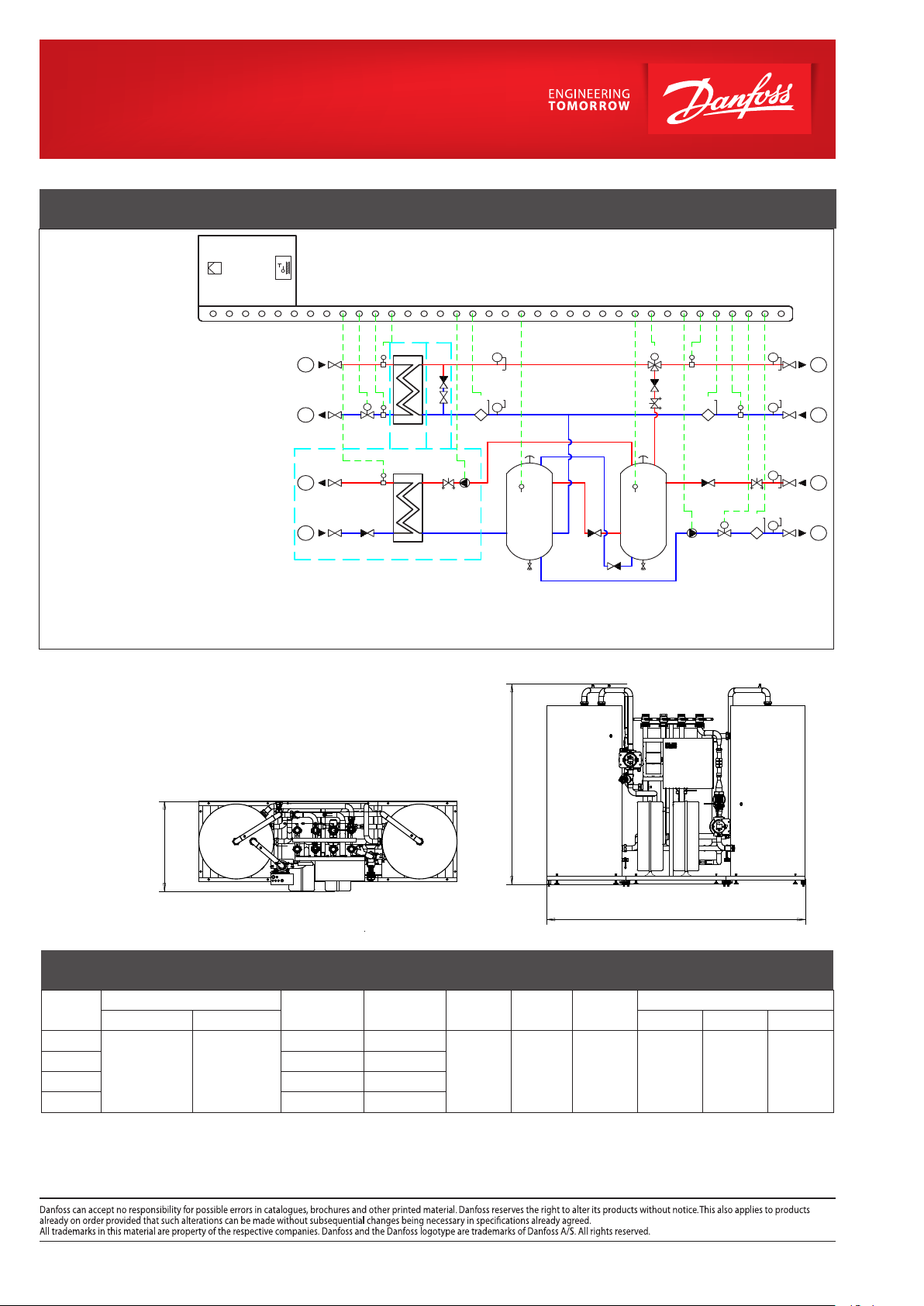
CIRCUIT DIAGRAM - EXAMPLECIRCUIT DIAGRAM
Danfoss Poland Sp. z o.o. · Tuchom, ul. Tęczowa 46 · 80-209 Chwaszczyno · POLAND
Tel.: +48 58 512 91 34 · Fax: +48 58 512 91 05 · serwis@danfoss.pl · www.danfoss.com
200
200
S1
200
200
M
S5M2
200
200
S14
200
200
M
M1
P4
S3
F1
E
S9
120
100
P3MM3 F2
G
300300
TE
E
TE
F
TE
G
ECL
S8
TE
F
TE
G
TE
E
100
100
T1 T2
V2
V1
400
500
400
500
S6
1
2
7
8
3
4
5
6
A1,A3
A1,A2
A3,A4
120
200
F3FS7
110310
100 Check valve
110 Check valve
120 Check valve
200 Ball valve
300 Balancing valve (ver. A1, A3)
310 Balancing valve
400 Air vent
500 Drain
F1, F2, F3 Heat meter
M1 Control valve HE (3-way)
M2 Control valve HE
M3 Control valve
P3 Pump
P4 Pump (ver. A1, A3)
S3, S7 Temperature sensor
S14, S5 Temperature sensor
S9 Temperature sensor (A1, A3)
S6, S8 Temperature sensor
T1, T2 Tanks
V1 Heat exchange r (ver. A1, A2)
120 Check valve (ver. A3, A4)
V2 Heat exchange r (ver. A1, A3)
S1 Outdoor temperature sensor
ECL Electronic controller
1 DH supply
2 DH return
3 Heating supply
4 Heating return
5 Cooling supply
6 Cooling return
7 DH supply
8 DH return
Technical paremeters
Primary side
Maximum temperature: 90 °C
Nominal pressure: PN 10
Diameter (threaded): DN 40
Secondary side
Maximum temperature (A1 / A2): 70 °C
Maximum temperature (A3 / A4): 90 °C
Nominal pressure (A1 / A2): PN 6
Nominal pressure (A3 / A4): PN 10
Diameter (threaded): DN 40
Electrical supply: 230 V AC
Controller: ECL 310
Height
Depth
CAPACITY, WEIGHT AND DIMENSIONS
Type
A1
A2 XB37/XB59 −
A3 DN 40 XB37/XB59
A4 DN 40 −
© Danfoss | DHS-SMCT/PL | 2017.08
Capacity [kW]
Heating CO
14 ÷ 540 50 ÷ 400
2
V1 V2 M1 M2/M3
XB37/XB59 XB37/XB59
VRB3
AMV
+
AHQM
AMV
Width
Weight
[kg]
+
up to
500
External dimensions [mm]
Height Width Depth
2000 2700 120 0
VL.MG.A1.02