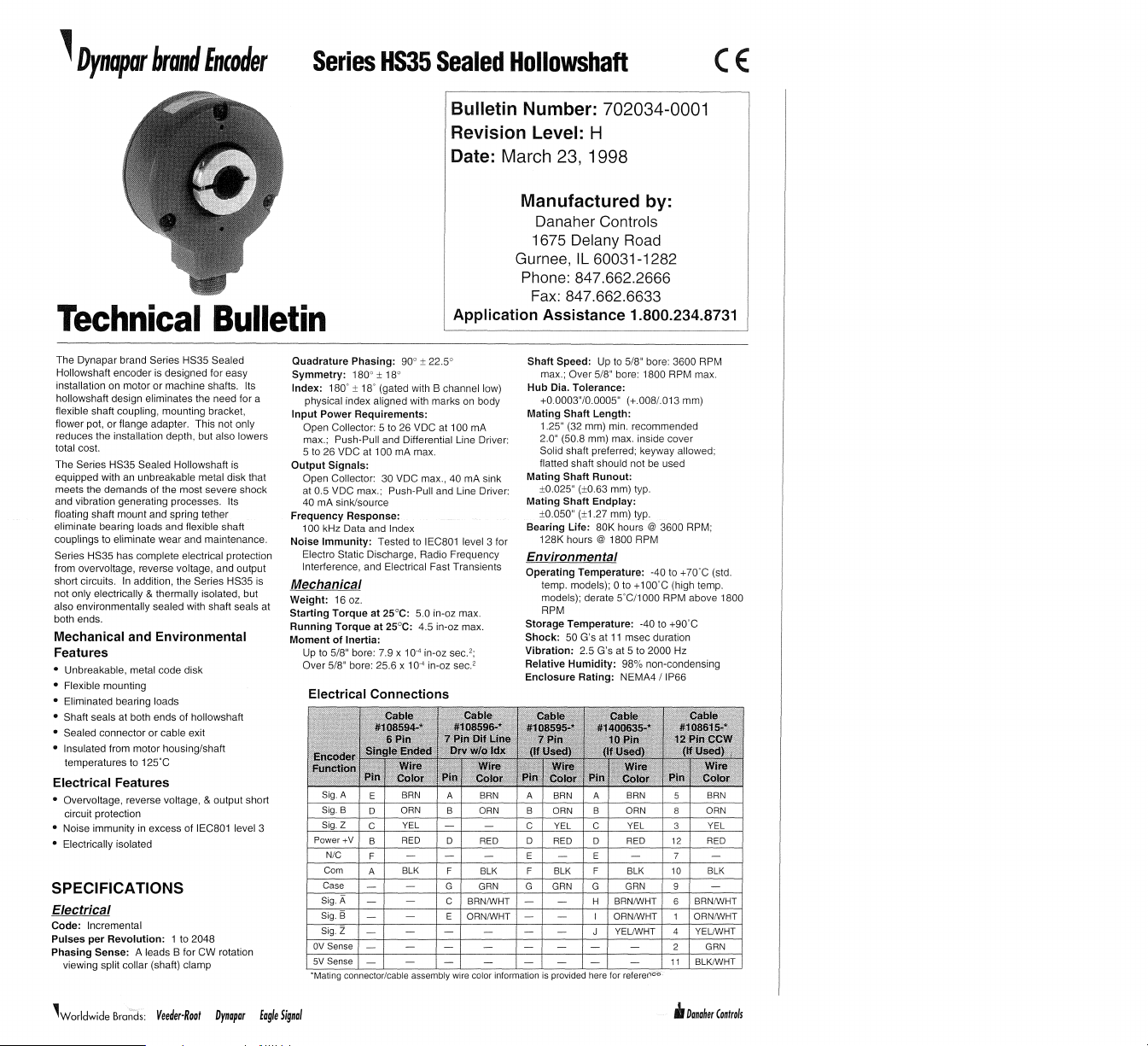
~
DynQpar
brand
Encoder
Technical
Series
Bulletin
HS35
Sealed
Hollowshaft
CE
Bulletin Number: 702034-0001
Revision Level: H
Date: March
23,
1998
Manufactured by:
Danaher Controls
1675 Delany Road
Gurnee,
Phone: 847.662.2666
Application Assistance 1.800.234.8731
IL 60031-1282
Fax: 847.662.6633
The Dynapar brand Series HS35 Sealed
Hollowshaft encoder is designed for easy
installation on motor or machine shafts. Its
hollowshaft
flexible shaft coupling, mounting bracket,
flower pot, or flange adapter. This not only
reduces the
total cost.
The Series
equipped with an unbreakable metal disk that
meets
and vibration generating processes. Its
floating shaft mount and spring teth.er
eliminate bearing loads and flexible shaft
couplings to eliminate wear and maintenance.
Series
from overvoltage, reverse voltage, and output
short circuits.
not only
also environmentally sealed with shaft seals at
both ends.
design eliminates the need for a
installation depth, but also lowers
HS35 Sealed Hollowshaft is
the
demands
of
the
most
severe
shock
HS35 has complete electrical protection
In
addition, the Series HS35 is
electrically & thermally isolated, but
Mechanical and Environmental
Features
• Unbreakable, metal code disk
• Flexible mounting
• Eliminated bearing loads
• Shaft seals at both ends of hollows haft
• Sealed connector or cable exit
• Insulated from motor housing/shaft
temperatures to 125'C
Electrical Features
• Overvoltage, reverse voltage, & output short
circuit protection
• Noise immunity
• Electrically isolated
in
excess of IEC801 level 3
Quadrature
Symmetry:
Index:
Input
Output
Frequency
Noise
Phasing:
90' ± 22.5'
ISO' ±
ISO' ±
physical index aligned with marks on body
Power
Open Collector: 5 to 26 VDC at 100 mA
max.;
5 to 26 VDC at
Signals:
Open Collector: 30 VDC max., 40 mA sink
at
0.5 VDC max.; Push-Pull and Line Driver:
40 mA sink/source
100 kHz Data and Index
Immunity:
Electro Static Discharge, Radio Frequency
Interference, and Electrical Fast Transients
IS'
IS'
(gated with B channel low)
Requirements:
Push-Pull and Differential Line Driver:
100 mA max.
Response:
Tested to IECSOI level 3 for
Mechanical
Weight:
16 oz.
Starting
Torque
at
Torque
of
Inertia:
25°C: 5.0 in-oz max.
at
25°C: 4.5 in-oz max.
10.4 in-oz sec.'
Running
Moment
5/S" bore: 7.9 x 10.4 in-oz sec.';
Up to
Over 5/S" bore: 25.6 x
Electrical Connections
Shaft
Speed:
Up
Over
5/S"
Tolerance:
Shaft
Length:
Shaft
Runout:
Shaft
Endplay:
Life:
SOK
@
IS00
to 5/S" bore: 3600 RPM
bore:
IS00
RPM max.
typo
typo
hours @ 3600 RPM;
RPM
max.;
Hub
Dia.
+0.0003"/0.0005" (+.00SI.013 mm)
Mating
1.25" (32 mm) min. recommended
2.0" (50.S mm) max. inside cover
Solid shaft preferred; keyway allowed;
flatted shaft should not be used
Mating
±0.025" (±0.63 mm)
Mating
±0.050" (±1.27 mm)
Bearing
128K hours
Environmental
Operating
Storage
Shock:
Vibration:
Relative
Enclosure
Temperature:
temp. models);
models); derate
RPM
0 to +100'C (high temp.
5'C/l
Temperature: -40 to +90'C
50 G's at
11
msec duration
2.5 G's at 5 to 2000 Hz
Humidity:
Rating:
9S%
NEMA4/
-40 to +70'C (std.
000 RPM above
non-condensing
IP66
IS00
SPECIFICATIONS
Electrical
Code:
Incremental
Pulses
per
Phasing
~Worldwide
Revolution:
Sense:
viewing split
Bra;;cts:
1 to 2048
A leads B for
collar (shaft) clamp
CW
Veeder·Root
Dynapar
rotation
Eagle
Signal
•
Danaher
Controls
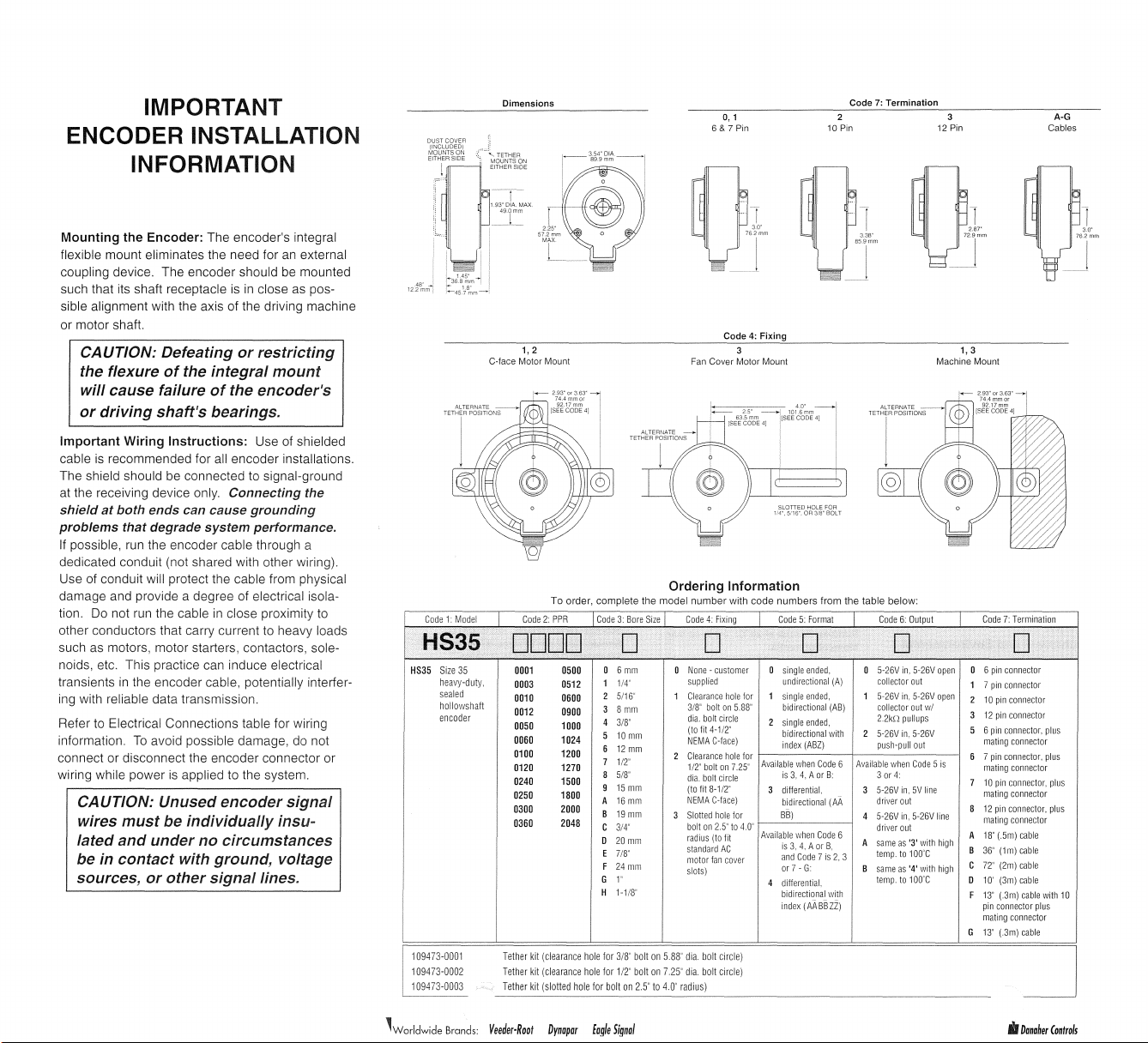
IMPORTANT
ENCODER INSTALLATION
INFORMATION
Mounting
flexible mount eliminates the need for
coupling device. The encoder should
such that its shaft receptacle
sible alignment with the axis of the driving machine
or motor
Important
cable
The shield should
at the receiving device only.
shield
problems
If
possible,
dedicated conduit (not shared with other wiring).
Use of conduit
damage and provide a degree of electrical isolation.
other conductors tllat carry current to heavy loads
such as motors, motor starters, contactors,
noids, etc.
transients
ing with reliable data transmission.
Refer to Electrical Connections table for wiring
information.
connect or disconnect the encoder connector or
wiring while power is applied to the system.
the
Encoder:
shaft.
CAUTION: Defeating
the flexure
will
cause failure
or
driving
Wiring
is
recommended for all encoder installations.
The encoder's integral
is
in
close as pos-
or
restricting
of
the integral
of
shaft's
bearings.
Instructions:
be
connected to signal-ground
mount
the encoder's
Use of shielded
Connecting
at
both
ends
can
cause
grounding
that
degrade
run
the encoder cable through a
will protect the cable from physical
Do
not
run
ThiS
practice can induce electrical
in
the encoder cable. potentially interfer-
To
avoid possible damage, do not
CAUTION: Unused
wires
must
lated
and
under
be in
contact
sources,
or
the cable
be
individually
no
with
other
system
pertormance.
in
close proximity
encoder
insu-
circumstances
ground,
voltage
signa/lines.
an
external
be
mounted
the
sole-
signal
to
hollowshatt
encoder
Dimensions
C-face
Matm
0003 0512
0010 0600
0012 0900
0050
0060
0100
0120
0240
0250
0300
0360
0,1
G & 7 Pin
--~1~~~,1~
!
.
...
i JO
'_'I,m,
~
Code 4:
Information
circle
circle
hole
for
25""
10
4.0'
fall
cO\jer
f
!
IFiLt
~
1,2
Mount
Fan Cover Motor Mount
Ordering
To order, complete the model number with code numbers from the table below:
1;4'
5/16'
8
1000
1024
1200
1270
1500
1800
2000
2048
mm
31S'
10mm
12mm
1/2"
5/8"
15
mOl
16mm
19
mm
lIia.
bolt
lIia.
bolt
3
Siotteu
I
boll
011
motor
slots)
bidirectional
clifferential,
10 Pin
witl1
Code 7:
I 2
Termination
5-26V
ill.
(
12
Pin
2ii7'
r
f-
."1"'''
1,3
Machine Mount
A-G
Cables
109473-0001
109473-0002
109473-0003
-_._---
~Worldwide
Bronds
Teliler
kil
(clearallce
Tether
kil
(clearance
Tether
kit
(slotted
Veeder·Root
Dynapar
hole
110Ie
hole
for
Eagle
for
for
bolt
Signal
3/3"
1/2'
bolt
DC
5.88"
dia.
boll
dia.
radius)
boll
errcle)
circle)
",
Danaher
Controls
bolt
on
725"
on
2.5""
to
4.0"