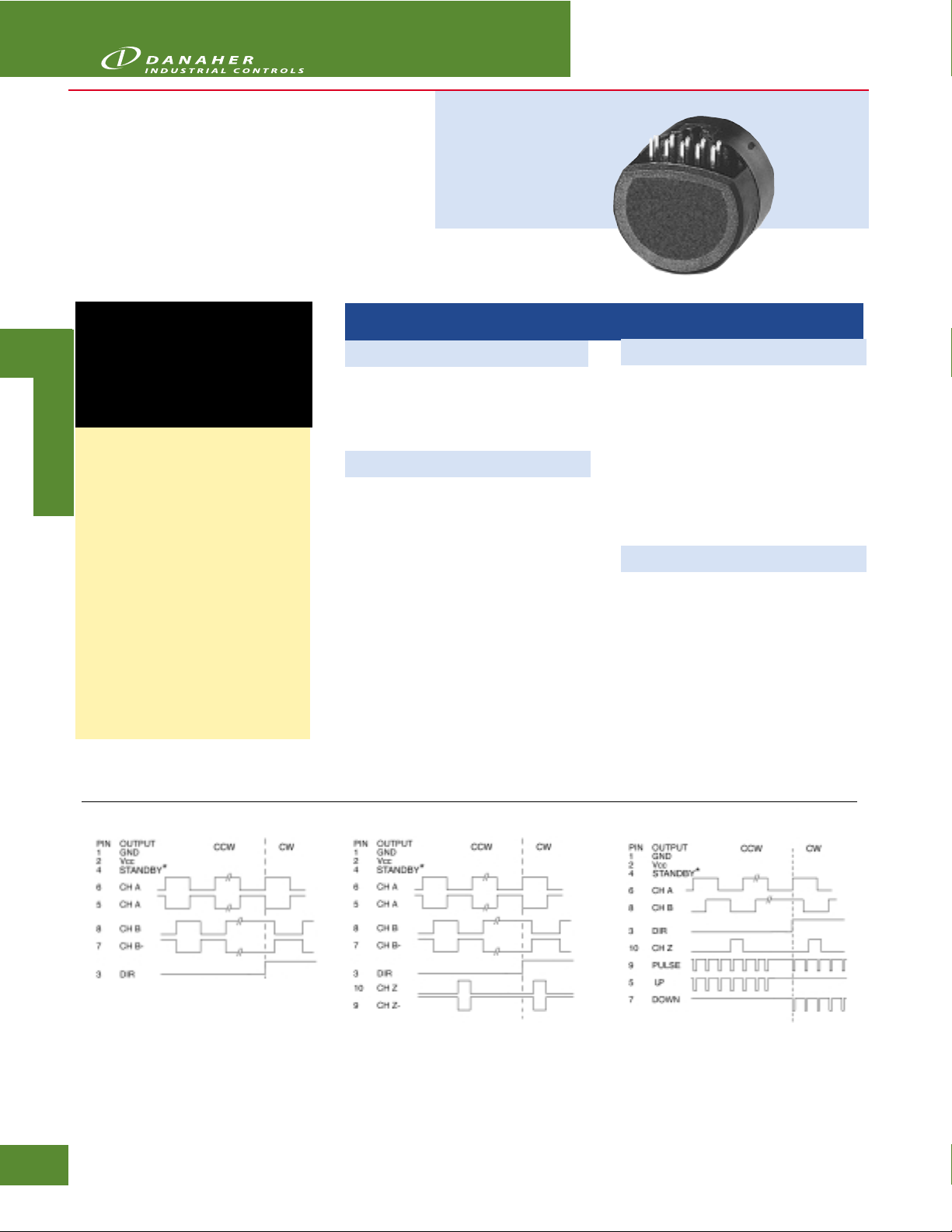
EncodersEncoders
Series E9 Miniature Encoder
• Ideal for position and speed sensing in small machines and
actuators
• Low power standby mode is ideal for battery powered
devices
• 200 kHz operating frequency
• Resolution to 512 lines/rev
• CE Qualified
Dynapar™ brand
APPLICATION/INDUSTRY
The E9 series incremental optical encoder
M
provides high performance feed-back for
O
precision motion control in a very small
T
package. Its small envelope makes it ideal for
O
instrument axes for position and speed
R
control in mechanisms too small to accept
standard encoders.
M
DESCRIPTION
O
Its high performance, advanced features,
U
and competitive pricing make it the
N
encoder of choice for a broad range of
T
applications.
The E9 optical encoders utilize a patent-
pending ASIC that integrates all encoder
electronics, including the optoelectronic
sensors, which enhances reliability and
accuracy.
Outputs are quadrature A and B
channels with up to 512 lines per rev, an
index pulse, unique up/down and
rotation direction signals (version 2) or
complementary CMOS-compatible
(version 1). The E9 also has a low-power
standby mode to conserve power in
battery-operated applications.
SPECIFICATIONS
STANDARD OPERATING CHARACTERISTICS
Code: Incremental, Optical
Resolution: Incremental pulses per revolution;
100 to 512
Phasing: 90° ±18°
Symmetry: 180° ±18° electrical
Index Pulse Width: 90° ±36°
ELECTRICAL
Supply Voltage: 5 VDC ±10%
Supply Current: 10 mA, typ.
Standby Current: 50 µA, max.
Output Signals: 2.5 V min. high (V
0.5 V max. low (V
2 mA (100°C)
Frequency Response: 200 kHz
Termination: 10 pin header (accessory
connector/12" ribbon cable,
part no. CA0040012)
Reccomended Mating Connector:
Thomas & Betts part number 622-1030
electrical degrees
electrical
);
). 3 mA sink/source (25°C),
OL
OH
MECHANICAL
Weight: 0.18 oz (5.07 g)
Moment of Inertia: 0.28 x 10
(0.20 gm-cm2)
Hub Bore: 1.5, 2.0, 2.5, 3.0, 4.0 mm;
0.125, 0.156 inch
Hub Dia. Tolerance: +0.0004"/-0.0000" (+0.010
mm/-0.000 mm)
Mating Shaft Length: See table
Mating Shaft Runout: 0.001 TIR
Mating Shaft Endplay: >256 ppr: ±0.003"
(±0.076mm); 250, 256 ppr: +0.005/-0.003"
(+0.127/-0.076mm); <250 ppr: +0.007/-0.003"
(+0.178/-0.076mm)
-5
oz-in-sec
2
ENVIRONMENTAL
Operating Temperature: -40° to 100°C
Storage Temperature: -50° to 125°C
Relative Humidity: 90% non-condensing
Output Waveforms & Connections (Direction viewing encoder cover)
Code 4= 00 Code 4= 01 Code 4= 02
Figure 1 Figure 2 Figure 3
2.
108
* For operation, connect STANDBY (4) to Vcc (2)
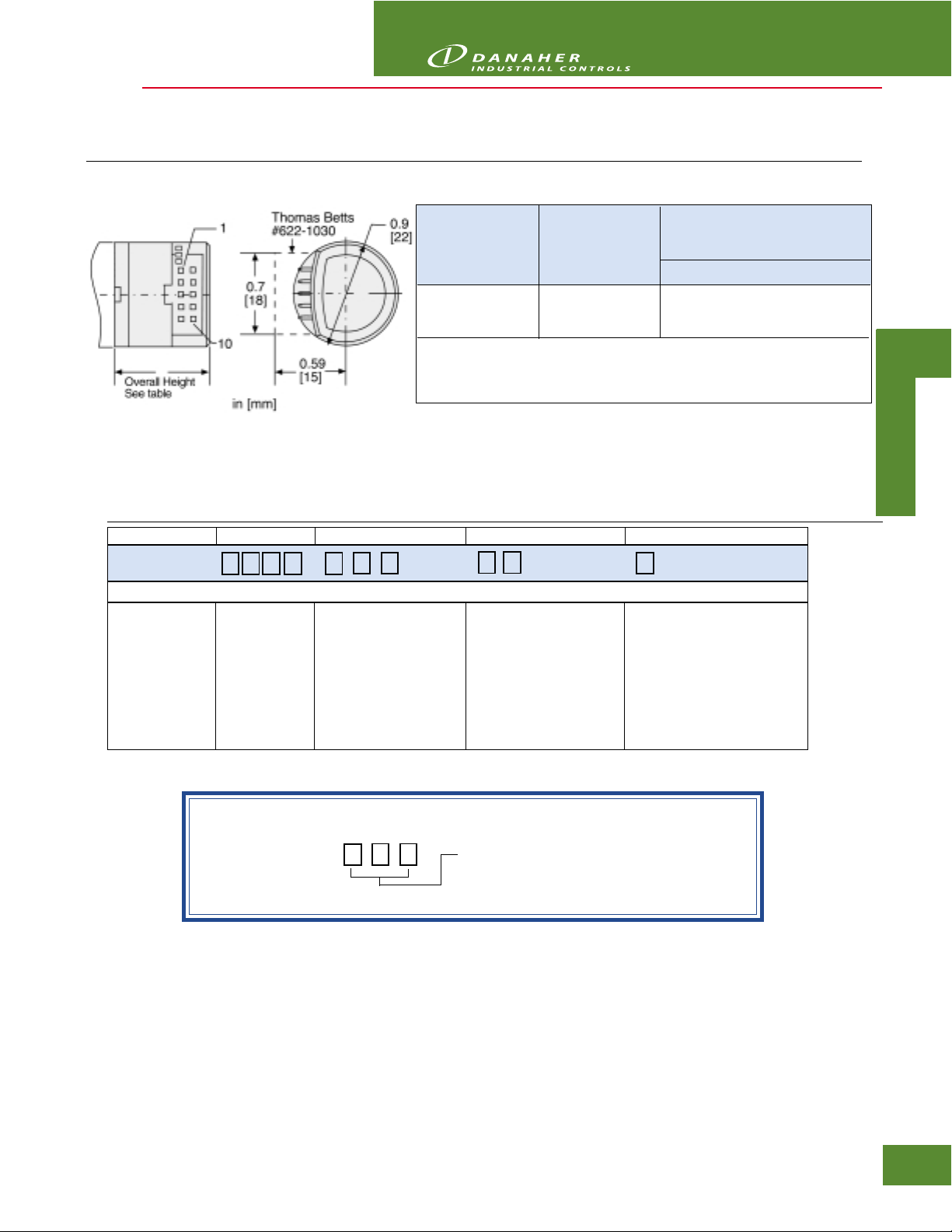
Dimensions/Installation
EncodersEncoders
Series E9 Miniature Encoder
Overall Height Motor Shaft Length
inch (MM) inch (MM)
Base (Code 3) Max. Min
A 0.795 (20.20) 0.479 (12.16) 0.467 (11.86)
C, D, E 0.929 (23.60) 0.613 (15.56) 0.581 (14.76)
Code 1: Model
E9
E9 0.9" Diameter
Incremental
Modular
Encoder
Bases C and D provide clearance for motor-bosses with maximum dimensions of 0.5 in,
Dia. x 0.15 in. high. Base E provides clearance for motor-bosses with maximum
dimensions of 1.0 in. x 0.15 in. high
Ordering Information
To order, complete the model number with code numbers from the table below:
Code 2: PPR
0100
0144
0200
0256
0300
0360
0500
0512
Code 3: Hub Bore Description
Ordering Information
1.5 1.5 mm
2.0 2.0 mm
2.5 2.5 mm
3.0 3.0 mm
4.0 4.0 mm
125 0.125 in
156 0.156 in
Code 4: Output Description
00 See Figure 1
01 See Figure 2
02 See Figure 3
M
O
T
O
R
M
O
U
N
T
Code 5: Mounting Description
0 No mounting base
A 4x M1.6 on 0.728" BC
C 2x #2-56 on 0.75" BC
D 3x #0-80 on 0.823" BC
E 2x #2-56 0n 1.812" BC
IMPORTANT: To properly install Series E9, a specialized mounting kit must be purchased. Only
one kit is required to install any number of encoders with the same hub bore size.
Kit Part Number: MK E9
Example: Kit for installing encoders with 3.0 mm hub Bore=
Code 3 (from Models Table, above) designating
Hub Bore requirement.
MK E9 3.0
2.
109