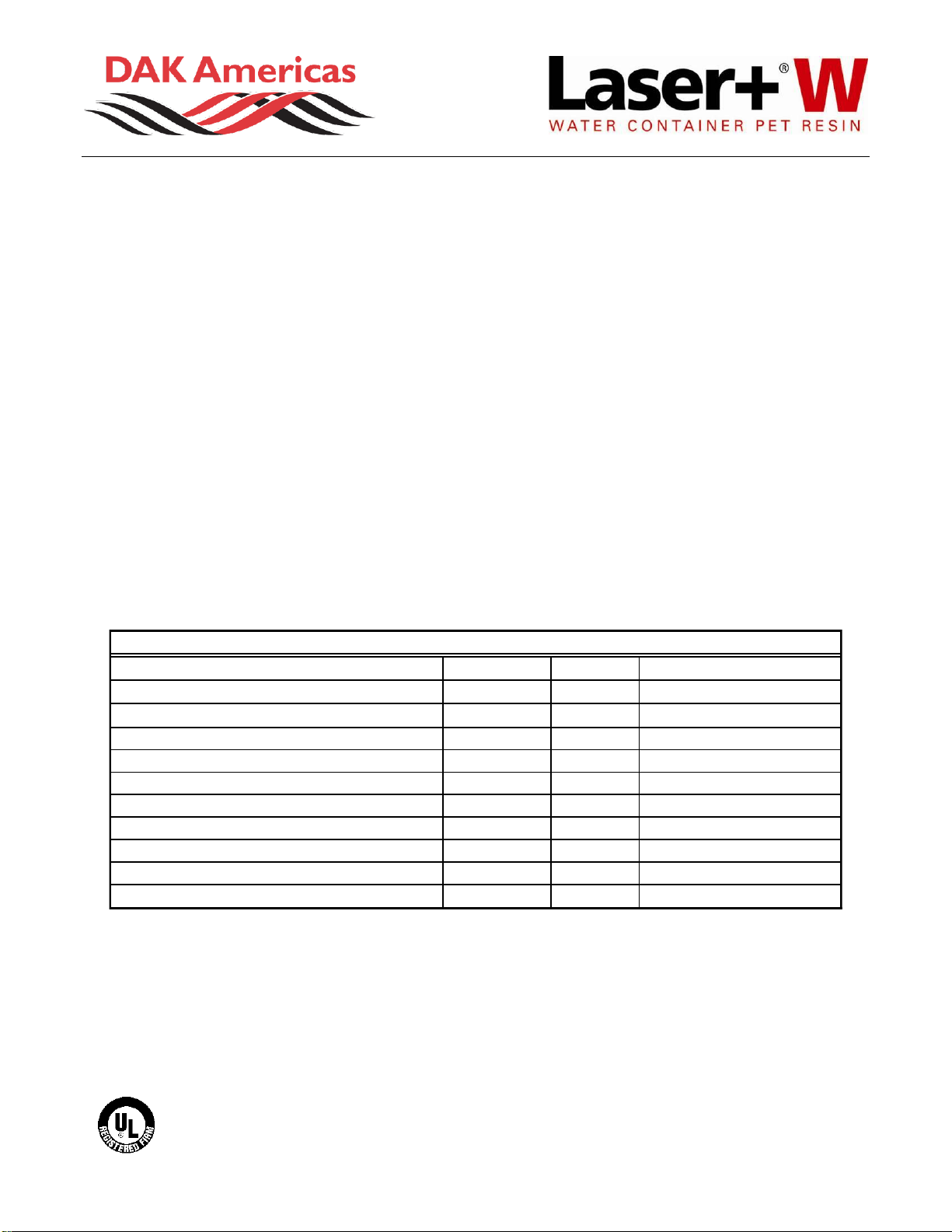
DAK Americas
ISO 9001:2008
#10004457
Property Value Unit Test Method
0.72 ± 0.02 dL/g DAK-QAR-SOP-0012
79.0 ± 2.0 CIE DAK-QAR-SOP-0011
-4.3 ± 2.0 CIE DAK-QAR-SOP-0011
Acetaldehyde 1 max ppm DAK-QAR-SOP-0010
Moisture Content (as packaged) 0.25 max weight % DAK-QAR-SOP-0013
Fines (as packaged, +24 Mesh Size) 0.10 max weight % DAK-QAR-SOP-0014
Chip Size, nominal 59 chips / g DAK-QAR-SOP-0015
Crystallinity > 45 % DAK-QAR-SOP-0016
Partical Size, Shape (Cylindrical) 3x2x2 mm DAK-QAR-SOP-0017
Melting Point, min 240 ºC DAK-QAR-SOP-0016
Bulk Density 56 lb / ft³ DAK-QAR-SOP-0018
Laser+® W Ti844 (P46A) Product Information
polyethylene terephthalate resin
Product Description
Laser+® W Ti844 (P46A) polyethylene terephthalate (PET) resin is a copolymer formulated for
conversion to PET bottles by conventional single or two-stage processing technology.
Typical Properties
Bi-orientation of Laser+® W Ti844 (P46A) by injection/stretch blow molding provides optimal barrier and
mechanical properties, including superior stress crack resistance. It performs exceptionally well in the
manufacture of water bottles where heat up rate and temperature profile through the wall are important.
Laser+® W Ti844 (P46A) is an antimony free polymer designed for water bottles using a slightly lower
intrinsic viscosity (IV), allowing for a gentle injection molding process, and improved acetaldehyde (AA)
performance. Laser+® W Ti844 (P46A) offers superior heat absorption and processing control, even at
higher blow molding speeds. A relatively slow crystallization rate enables high injection molding output.
Certification
Laser+® W Ti844 (P46A) is ideally suited for food packaging applications and is considered in
compliance with the Food and Drug Administration (FDA) Food Contact Notification (FCN) 000085,
covering PET polymers.
Sales Specifications
These values represent the anticipated performance data for these polyester resins and intermediates; they are not intended to
be used as design data. We believe this information is the best currently available on the subject. It is offered as a possible
helpful suggestion in the experimentation you may care to undertake along these lines. It is subject to revision as additional
knowledge and experience is gained. DAK Resins makes no guarantee of results and assumes no obligation or liability
whatsoever in connection with this information. This publication is not a license to operate under, or intended to suggest
infringement of, any existing patents.
CAUTION: Do not use in medical applications involving permanent implantation in the human body. For other medical
applications, see “DAK Medical Caution Statement”.
DAK Americas LLC
Gateway Corporate Center, Suite 210
223 Wilmington W Chester Pike• Chadds Ford, PA 19317
1-888-738-2002 • fax: 610-558-7385 • www.dakamericas.com
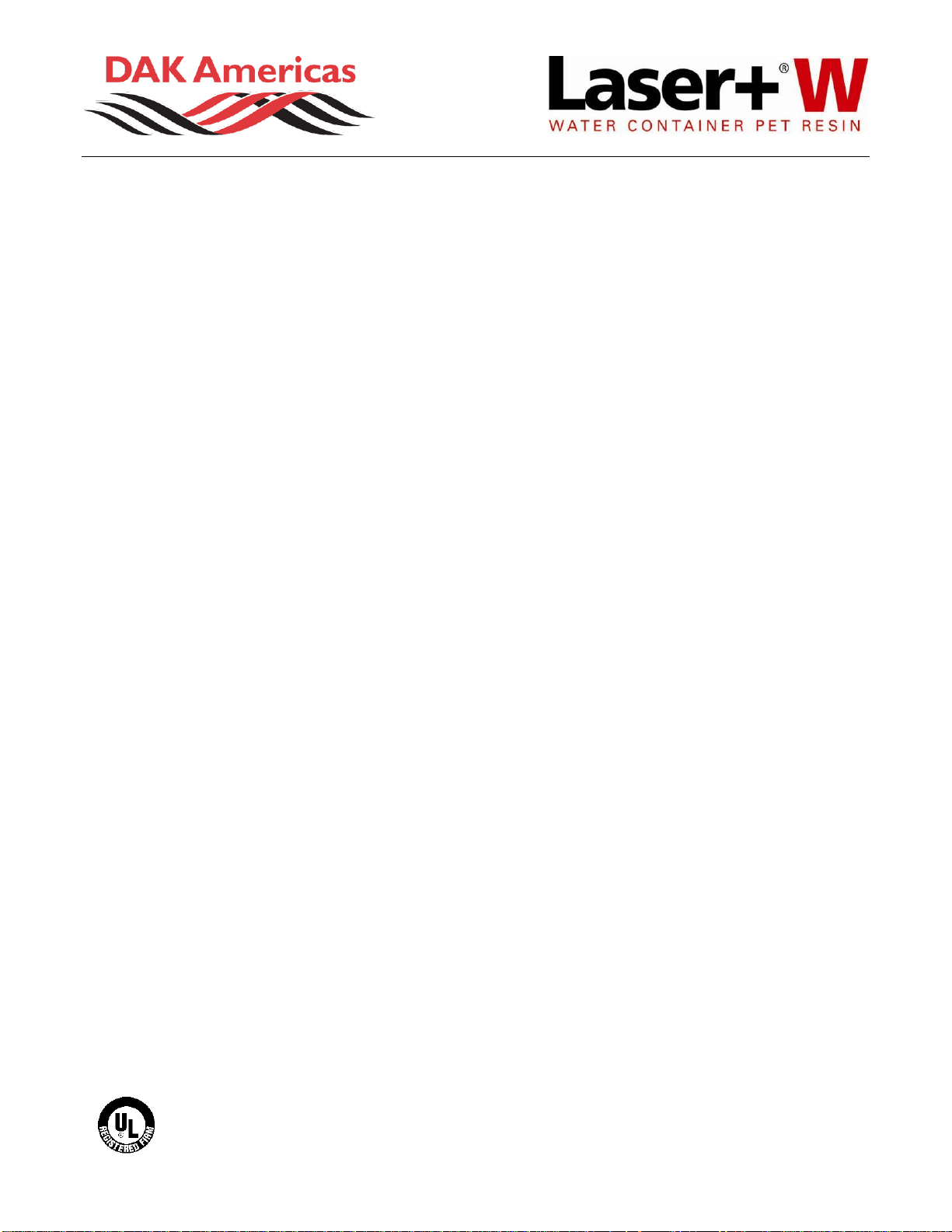
DAK Americas
ISO 9001:2008
#10004457
Laser+® W Ti844 (P46A) Product Information
polyethylene terephthalate resin
Material Drying
Proper drying of polyethylene terephthalate (PET) is essential to produce a high quality part (container,
film, etc.) with optimum physical properties. PET is hygroscopic, meaning that when it is exposed to
humid atmospheres, it will absorb moisture. In PET the moisture is not only on the surface but diffuses
slowly through the whole pellet and is firmly held by molecular attraction. Before processing the PET,
this moisture must be removed. Carefully controlled drying of all PET is an essential requirement for
optimum processing performance and final product properties. If drying is not carried out properly, to
the known requirements of the type of PET in use, then deficiencies in process and product will results.
The deficiencies will be impossible to remedy by later process changes. These defects arise in the
injection molding or extrusion processes because at PET melt temperature (250°-280° C) any water
present causes hydrolytic degradation of the PET, almost instantaneously, with the resultant loss in
intrinsic viscosity (IV). Significant drops in IV cause loss of process control and reductions in end
product properties.
Drying of PET polymer involves the diffusion of absorbed moisture from the interior of the polymer chip
to its surroundings and, subsequently the removal of moisture from the bulk of polymer chips. Moisture
removal can be achieved by heating the polymer chip under dry air or vacuum. In an air drying system,
heated dehumidified air flows up through a chip bed and returns to the dehumidifier. The key
requirements for a reliable drying process are:
Drying temperature: The ACTUAL chip temperature should achieve between 300° and 340° F
measured at the dryer exit.
Dehumidified air temperature: Correctly designed equipment should operate at temperatures up to
340° F measured on entry to the dryer hopper, with an absolute maximum of 350° F to prevent possible
discoloration.
Dehumidified air dew point: This should not be allowed to rise above –34° F and should preferably be
–40° F or lower, measure after the desiccant bed. Always check the correct regeneration temperatures
are being used.
Dehumidified air flow through the chip bed: Most dryers operate at around l cfm of airflow per 1lb/hr of
PET chip as a minimum requirement, with the airflow at the correct temperature and dew point.
Chip residence time (drying time): DAK recommends a chip residence time for Laser+® PET of not less
than four hours and preferably six hours. This is the theoretical drying time, which is calculated by
dividing dryer capacity in lbs. by throughput in lb./hr. Extended periods of high temperature can
adversely affect the polymer processing conditions. In the event of a stoppage for an extended period,
dry polymer can be stored in the dryer-hopper by reducing the air temperature to 240° F (or even
lower).
DAK Americas LLC
Gateway Corporate Center, Suite 210
223 Wilmington W Chester Pike• Chadds Ford, PA 19317
1-888-738-2002 • fax: 610-558-7385 • www.dakamericas.com