
Ser
Controller
PowerCommand® 3100
English
Original Instructions
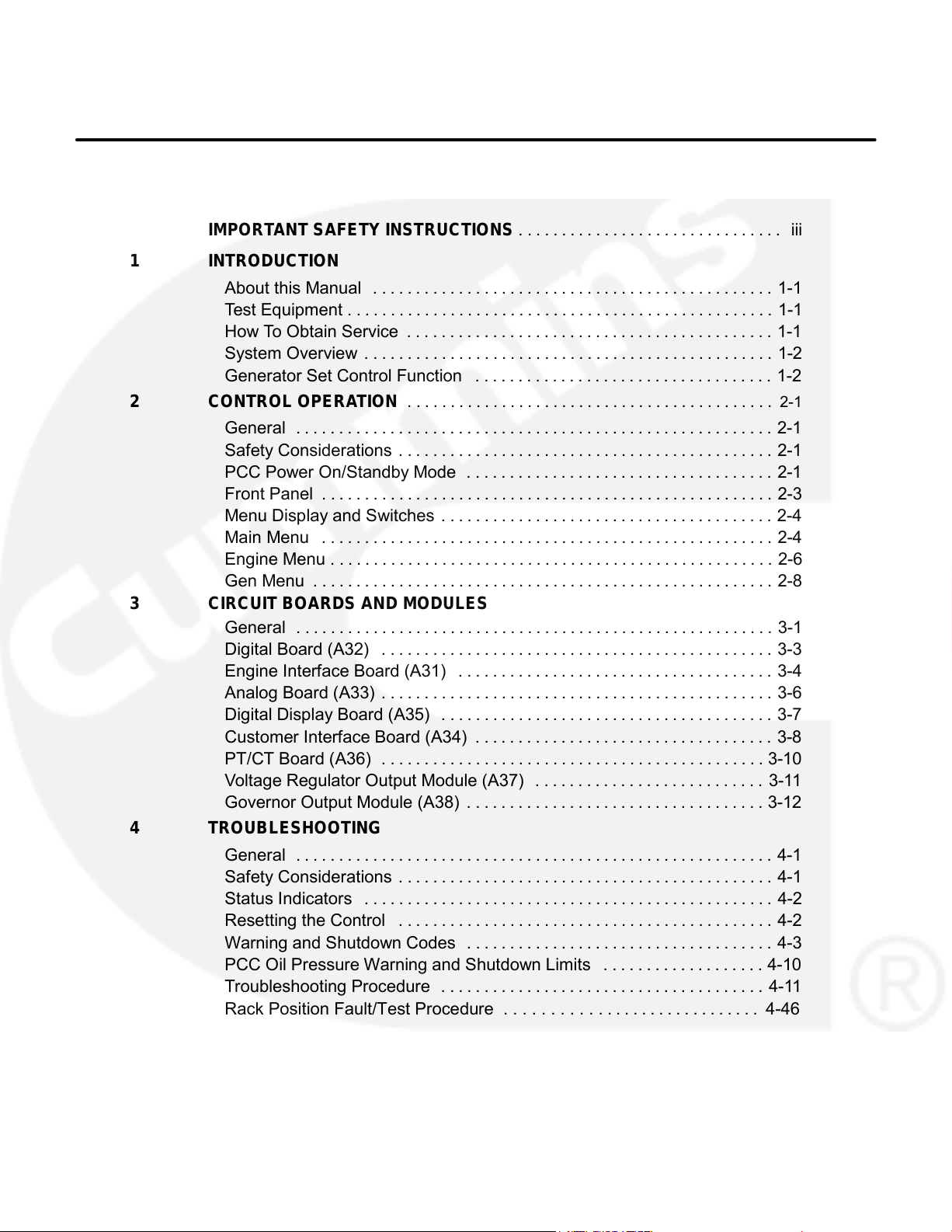
IMPORTANT SAFETY INSTRUCTIONS . . . . . . . . . . . . . . . . . . . . . . . . . . . . . . . iii
About this Manual . . . . . . . . . . . . . . . . . . . . . . . . . . . . . . . . . . . . . . . . . . . . . . . 1-1
Test Equipment . . . . . . . . . . . . . . . . . . . . . . . . . . . . . . . . . . . . . . . . . . . . . . . . . . 1-1
How To Obtain Service . . . . . . . . . . . . . . . . . . . . . . . . . . . . . . . . . . . . . . . . . . . 1-1
System Overview . . . . . . . . . . . . . . . . . . . . . . . . . . . . . . . . . . . . . . . . . . . . . . . . 1-2
Generator Set Control Function . . . . . . . . . . . . . . . . . . . . . . . . . . . . . . . . . . . 1-2
CONTROL OPERATION . . . . . . . . . . . . . . . . . . . . . . . . . . . . . . . . . . . . . . . . . . .
2-1
General . . . . . . . . . . . . . . . . . . . . . . . . . . . . . . . . . . . . . . . . . . . . . . . . . . . . . . . . 2-1
Safety Considerations . . . . . . . . . . . . . . . . . . . . . . . . . . . . . . . . . . . . . . . . . . . . 2-1
PCC Power On/Standby Mode . . . . . . . . . . . . . . . . . . . . . . . . . . . . . . . . . . . . 2-1
Front Panel . . . . . . . . . . . . . . . . . . . . . . . . . . . . . . . . . . . . . . . . . . . . . . . . . . . . . 2-3
Menu Display and Switches . . . . . . . . . . . . . . . . . . . . . . . . . . . . . . . . . . . . . . . 2-4
Main Menu . . . . . . . . . . . . . . . . . . . . . . . . . . . . . . . . . . . . . . . . . . . . . . . . . . . . . 2-4
Engine Menu . . . . . . . . . . . . . . . . . . . . . . . . . . . . . . . . . . . . . . . . . . . . . . . . . . . . 2-6
Gen Menu . . . . . . . . . . . . . . . . . . . . . . . . . . . . . . . . . . . . . . . . . . . . . . . . . . . . . . 2-8
CIRCUIT BOARDS AND MODULES
General . . . . . . . . . . . . . . . . . . . . . . . . . . . . . . . . . . . . . . . . . . . . . . . . . . . . . . . . 3-1
Digital Board (A32) . . . . . . . . . . . . . . . . . . . . . . . . . . . . . . . . . . . . . . . . . . . . . . 3-3
Engine Interface Board (A31) . . . . . . . . . . . . . . . . . . . . . . . . . . . . . . . . . . . . . 3-4
Analog Board (A33) . . . . . . . . . . . . . . . . . . . . . . . . . . . . . . . . . . . . . . . . . . . . . . 3-6
Digital Display Board (A35) . . . . . . . . . . . . . . . . . . . . . . . . . . . . . . . . . . . . . . . 3-7
Customer Interface Board (A34) . . . . . . . . . . . . . . . . . . . . . . . . . . . . . . . . . . . 3-8
PT/CT Board (A36) . . . . . . . . . . . . . . . . . . . . . . . . . . . . . . . . . . . . . . . . . . . . . 3-10
Voltage Regulator Output Module (A37) . . . . . . . . . . . . . . . . . . . . . . . . . . . 3-11
Governor Output Module (A38) . . . . . . . . . . . . . . . . . . . . . . . . . . . . . . . . . . . 3-12
General . . . . . . . . . . . . . . . . . . . . . . . . . . . . . . . . . . . . . . . . . . . . . . . . . . . . . . . . 4-1
Safety Considerations . . . . . . . . . . . . . . . . . . . . . . . . . . . . . . . . . . . . . . . . . . . . 4-1
Status Indicators . . . . . . . . . . . . . . . . . . . . . . . . . . . . . . . . . . . . . . . . . . . . . . . . 4-2
Resetting the Control . . . . . . . . . . . . . . . . . . . . . . . . . . . . . . . . . . . . . . . . . . . . 4-2
Warning and Shutdown Codes . . . . . . . . . . . . . . . . . . . . . . . . . . . . . . . . . . . . 4-3
PCC Oil Pressure Warning and Shutdown Limits . . . . . . . . . . . . . . . . . . . 4-10
Troubleshooting Procedure . . . . . . . . . . . . . . . . . . . . . . . . . . . . . . . . . . . . . . 4-11
Rack Position Fault/Test Procedure . . . . . . . . . . . . . . . . . . . . . . . . . . . . . 4-46
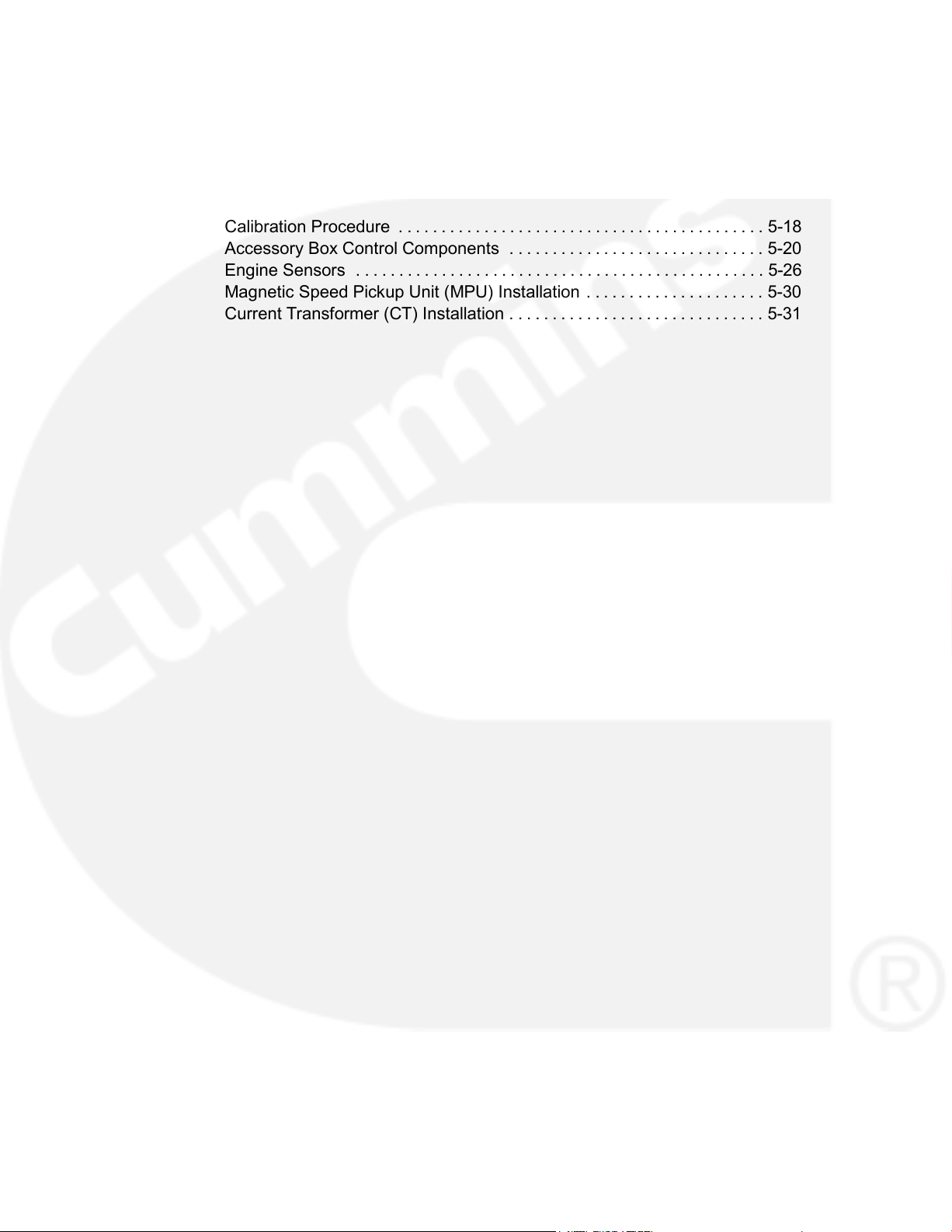
CONTROL SERVICE AND CALIBRATION
General . . . . . . . . . . . . . . . . . . . . . . . . . . . . . . . . . . . . . . . . . . . . . . . . . . . . . . . . 5-1
Circuit Board Removal/Replacement . . . . . . . . . . . . . . . . . . . . . . . . . . . . . . . 5-1
Initial Start Setup Menu . . . . . . . . . . . . . . . . . . . . . . . . . . . . . . . . . . . . . . . . . . 5-4
Adjust Menu . . . . . . . . . . . . . . . . . . . . . . . . . . . . . . . . . . . . . . . . . . . . . . . . . . . . 5-6
Setup and Calibration Menus . . . . . . . . . . . . . . . . . . . . . . . . . . . . . . . . . . . . . 5-8
Calibration Procedure . . . . . . . . . . . . . . . . . . . . . . . . . . . . . . . . . . . . . . . . . . . 5-18
Accessory Box Control Components . . . . . . . . . . . . . . . . . . . . . . . . . . . . . . 5-20
Engine Sensors . . . . . . . . . . . . . . . . . . . . . . . . . . . . . . . . . . . . . . . . . . . . . . . . 5-26
Magnetic Speed Pickup Unit (MPU) Installation . . . . . . . . . . . . . . . . . . . . . 5-30
Current Transformer (CT) Installation . . . . . . . . . . . . . . . . . . . . . . . . . . . . . . 5-31
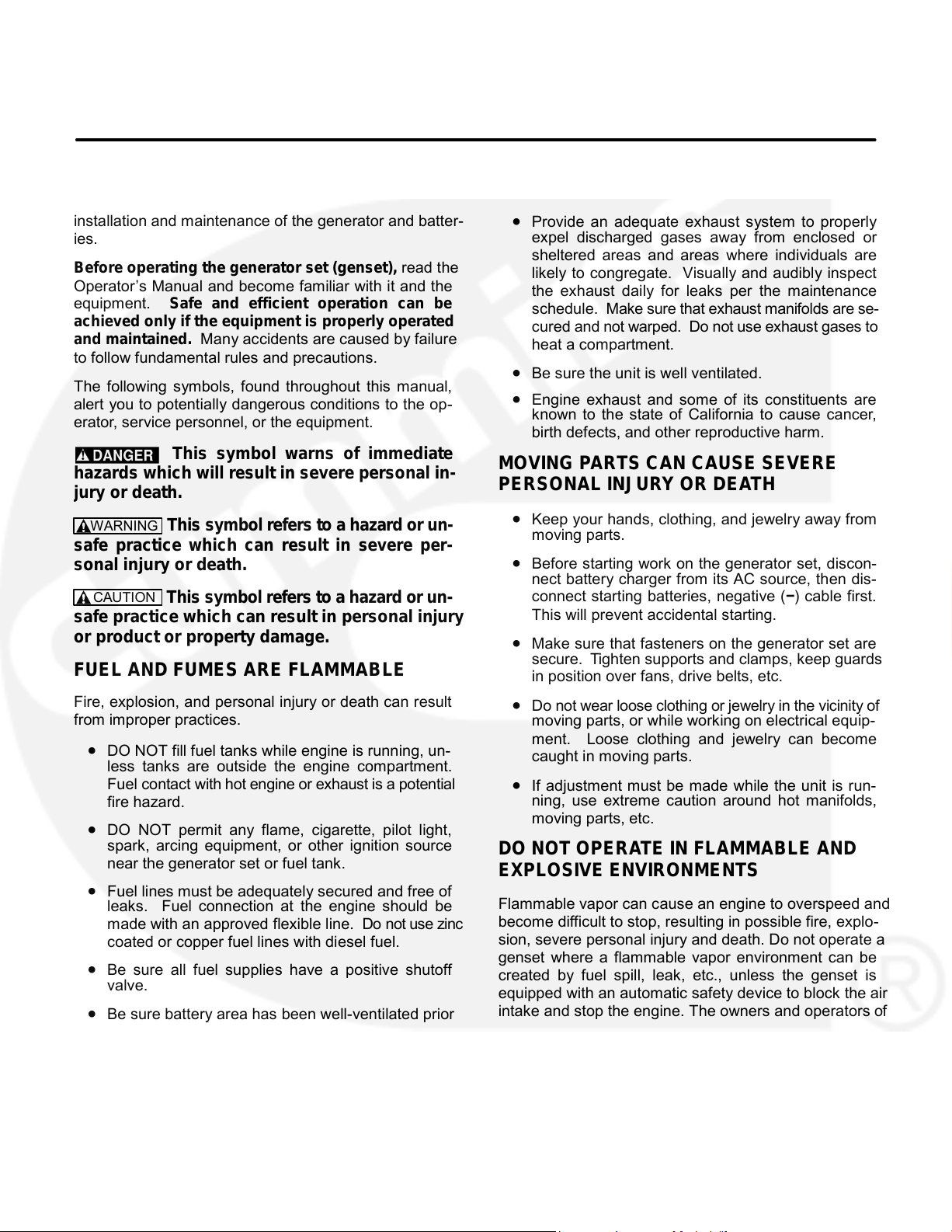
IMPORTANT SAFETY INSTRUCTIONS
SAVE THESE INSTRUCTIONS −
important instructions that should be followed during
• Provide an adequate exhaust system to properly
installation and maintenance of the generator and batter-
expel discharged gases away from enclosed or
sheltered areas and areas where individuals are
Before operating the generator set (genset), read the
likely to congregate. Visually and audibly inspect
Operator’s Manual and become familiar with it and the
the exhaust daily for leaks per the maintenance
equipment. Safe and efficient operation can be
schedule. Make sure that exhaust manifolds are se-
achieved only if the equipment is properly operated
cured and not warped. Do not use exhaust gases to
and maintained. Many accidents are caused by failure
to follow fundamental rules and precautions.
• Be sure the unit is well ventilated.
The following symbols, found throughout this manual,
Engine exhaust and some of its constituents are
alert you to potentially dangerous conditions to the op-
known to the state of California to cause cancer,
erator, service personnel, or the equipment.
birth defects, and other reproductive harm.
This symbol warns of immediate
MOVING PARTS CAN CAUSE SEVERE
hazards which will result in severe personal in-
This symbol refers to a hazard or un-
safe practice which can result in severe per-
Before starting work on the generator set, discon-
nect battery charger from its AC source, then dis-
connect starting batteries, negative (−) cable first.
This symbol refers to a hazard or un-
This will prevent accidental starting.
safe practice which can result in personal injury
or product or property damage.
secure. Tighten supports and clamps, keep guards
FUEL AND FUMES ARE FLAMMABLE
in position over fans, drive belts, etc.
Do not wear loose clothing or jewelry in the vicinity of
Fire, explosion, and personal injury or death can result
moving parts, or while working on electrical equip-
ment. Loose clothing and jewelry can become
less tanks are outside the engine compartment.
Fuel contact with hot engine or exhaust is a potential
ning, use extreme caution around hot manifolds,
spark, arcing equipment, or other ignition source
DO NOT OPERATE IN FLAMMABLE AND
near the generator set or fuel tank.
Flammable vapor can cause an engine to overspeed and
leaks. Fuel connection at the engine should be
become difficult to stop, resulting in possible fire, explo-
made with an approved flexible line. Do not use zinc
sion, severe personal injury and death. Do not operate a
coated or copper fuel lines with diesel fuel.
genset where a flammable vapor environment can be
created by fuel spill, leak, etc., unless the genset is
equipped with an automatic safety device to block the air
intake and stop the engine. The owners and operators of
to servicing near it. Lead-acid batteries emit a highly
the genset are solely responsible for operating the gen-
explosive hydrogen gas that can be ignited by arc-
set safely. Contact your authorized Cummins Power
ing, sparking, smoking, etc.
Generation distributor for more information.
•
WARNING
CAUTION
• DO NOT fill fuel tanks while engine is running, un-
• DO NOT permit any flame, cigarette, pilot light,
• Fuel lines must be adequately secured and free of
• Keep your hands, clothing, and jewelry away from
•
• Make sure that fasteners on the generator set are
•
• If adjustment must be made while the unit is run-
• Be sure all fuel supplies have a positive shutoff
• Be sure battery area has been well-ventilated prior
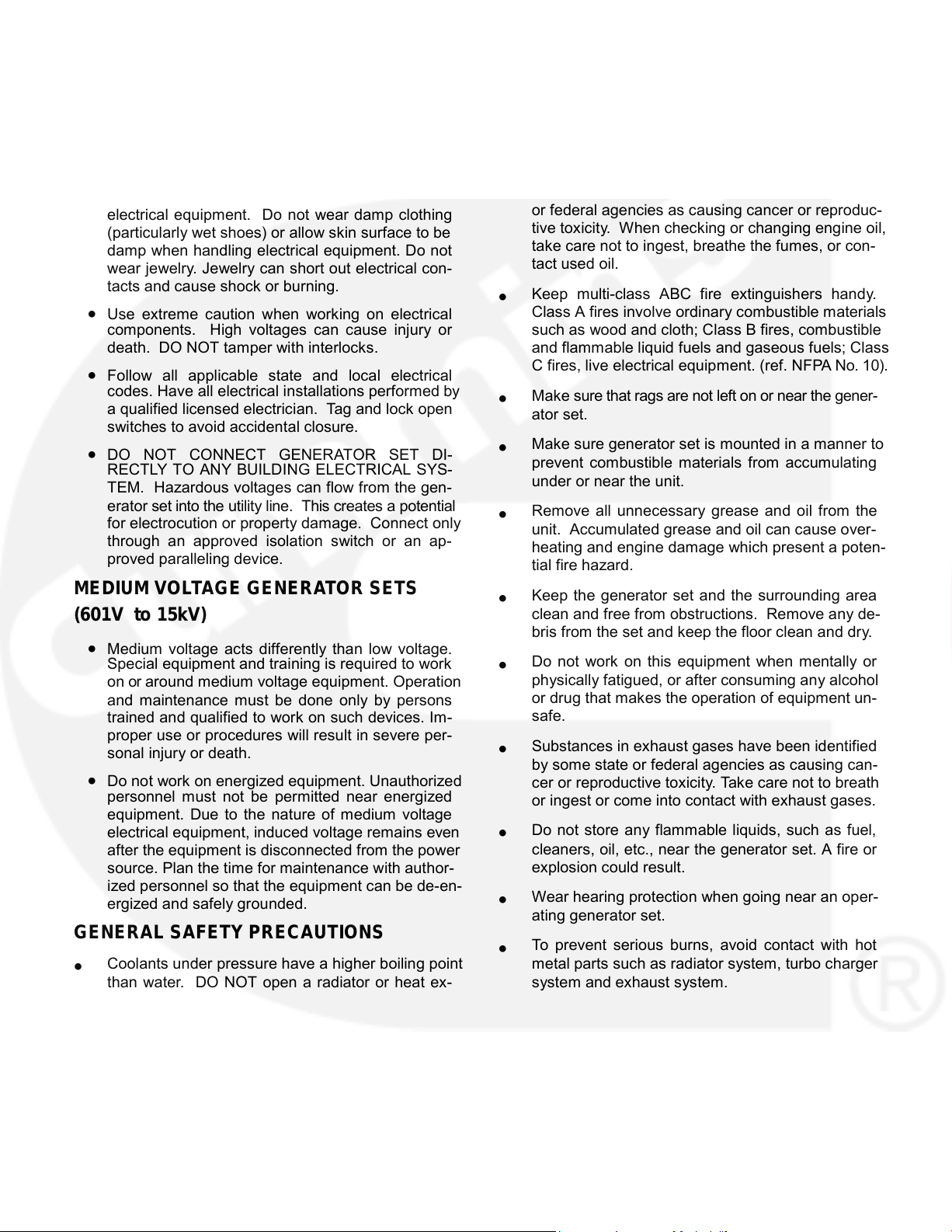
ELECTRICAL SHOCK CAN CAUSE
changer pressure cap while the engine is running.
To prevent severe scalding, let engine cool down
SEVERE PERSONAL INJURY OR DEATH
before removing coolant pressure cap. Turn cap
•
Remove electric power before removing protective
slowly, and do not open it fully until the pressure has
shields or touching electrical equipment. Use rub-
ber insulative mats placed on dry wood platforms
Used engine oils have been identified by some state
over floors that are metal or concrete when around
or federal agencies as causing cancer or reproduc-
electrical equipment. Do not wear damp clothing
tive toxicity. When checking or changing engine oil,
(particularly wet shoes) or allow skin surface to be
take care not to ingest, breathe the fumes, or con-
damp when handling electrical equipment. Do not
wear jewelry. Jewelry can short out electrical con-
tacts and cause shock or burning.
Keep multi-class ABC fire extinguishers handy.
Class A fires involve ordinary combustible materials
components. High voltages can cause injury or
such as wood and cloth; Class B fires, combustible
death. DO NOT tamper with interlocks.
and flammable liquid fuels and gaseous fuels; Class
C fires, live electrical equipment. (ref. NFPA No. 10).
Follow all applicable state and local electrical
codes. Have all electrical installations performed by
Make sure that rags are not left on or near the gener-
a qualified licensed electrician. Tag and lock open
switches to avoid accidental closure.
Make sure generator set is mounted in a manner to
DO NOT CONNECT GENERATOR SET DI-
prevent combustible materials from accumulating
RECTLY TO ANY BUILDING ELECTRICAL SYS-
TEM. Hazardous voltages can flow from the gen-
erator set into the utility line. This creates a potential
Remove all unnecessary grease and oil from the
for electrocution or property damage. Connect only
unit. Accumulated grease and oil can cause over-
through an approved isolation switch or an ap-
heating and engine damage which present a poten-
proved paralleling device.
MEDIUM VOLTAGE GENERATOR SETS
Keep the generator set and the surrounding area
clean and free from obstructions. Remove any de-
bris from the set and keep the floor clean and dry.
Do not work on this equipment when mentally or
Special equipment and training is required to work
physically fatigued, or after consuming any alcohol
on or around medium voltage equipment. Operation
or drug that makes the operation of equipment un-
and maintenance must be done only by persons
trained and qualified to work on such devices. Im-
proper use or procedures will result in severe per-
Substances in exhaust gases have been identified
by some state or federal agencies as causing can-
• Do not work on energized equipment. Unauthorized
cer or reproductive toxicity. Take care not to breath
personnel must not be permitted near energized
or ingest or come into contact with exhaust gases.
equipment. Due to the nature of medium voltage
Do not store any flammable liquids, such as fuel,
electrical equipment, induced voltage remains even
cleaners, oil, etc., near the generator set. A fire or
after the equipment is disconnected from the power
source. Plan the time for maintenance with author-
ized personnel so that the equipment can be de-en-
Wear hearing protection when going near an oper-
ergized and safely grounded.
GENERAL SAFETY PRECAUTIONS
To prevent serious burns, avoid contact with hot
Coolants under pressure have a higher boiling point
metal parts such as radiator system, turbo charger
than water. DO NOT open a radiator or heat ex-
system and exhaust system.
KEEP THIS MANUAL NEAR THE GENSET FOR EASY REFERENCE
• Use extreme caution when working on electrical
•
•
•
•
• Medium voltage acts differently than low voltage.
•
•
•
•
•
•
•
•
•
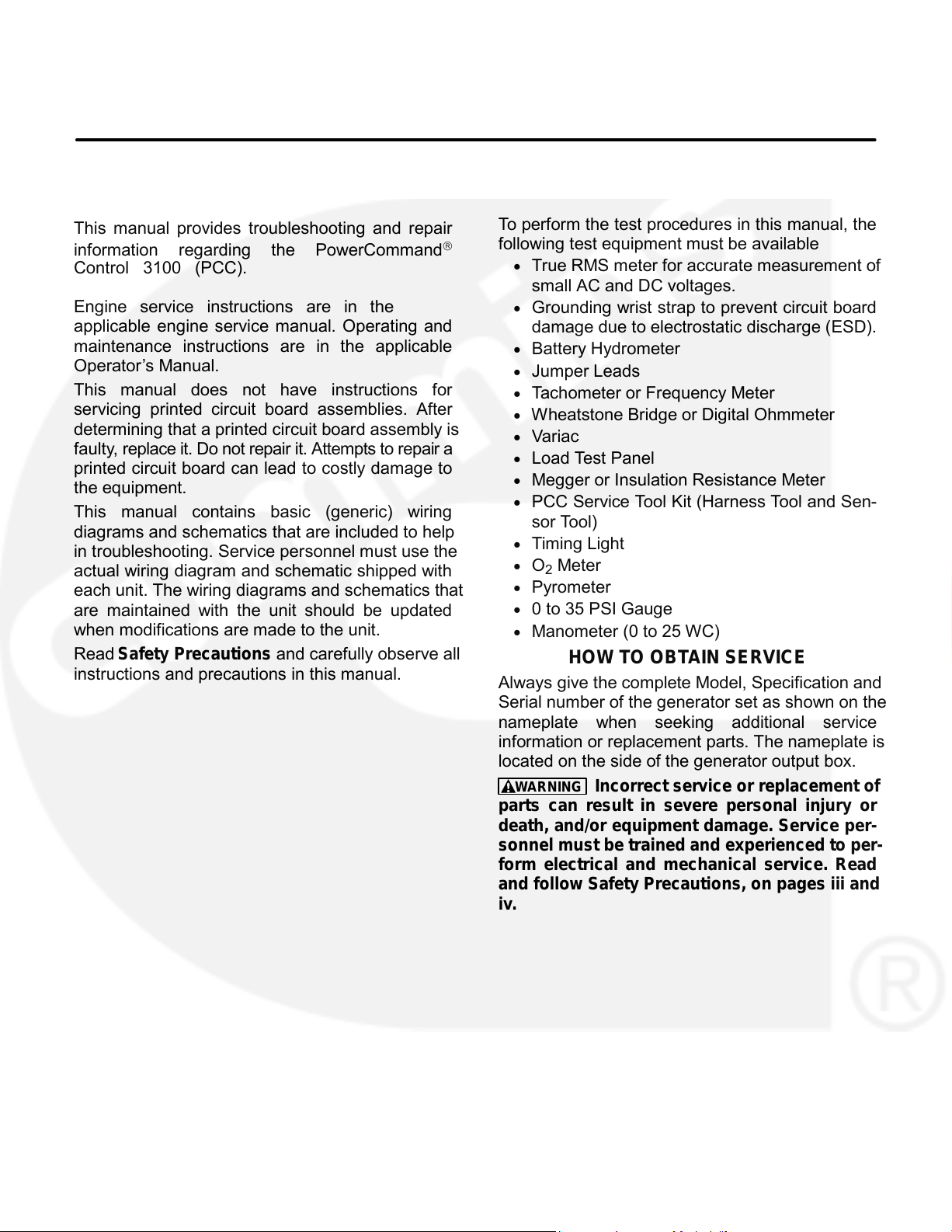
To perform the test procedures in this manual, the
This manual provides troubleshooting and repair
following test equipment must be available
information regarding the PowerCommand
True RMS meter for accurate measurement of
small AC and DC voltages.
Engine service instructions are in the
Grounding wrist strap to prevent circuit board
applicable engine service manual. Operating and
damage due to electrostatic discharge (ESD).
maintenance instructions are in the applicable
This manual does not have instructions for
Tachometer or Frequency Meter
servicing printed circuit board assemblies. After
Wheatstone Bridge or Digital Ohmmeter
determining that a printed circuit board assembly is
faulty, replace it. Do not repair it. Attempts to repair a
printed circuit board can lead to costly damage to
Megger or Insulation Resistance Meter
PCC Service Tool Kit (Harness Tool and Sen-
This manual contains basic (generic) wiring
diagrams and schematics that are included to help
in troubleshooting. Service personnel must use the
actual wiring diagram and schematic shipped with
each unit. The wiring diagrams and schematics that
are maintained with the unit should be updated
when modifications are made to the unit.
Read Safety Precautions and carefully observe all
instructions and precautions in this manual.
Always give the complete Model, Specification and
Serial number of the generator set as shown on the
nameplate when seeking additional service
information or replacement parts. The nameplate is
located on the side of the generator output box.
WARNING Incorrect service or replacement of
parts can result in severe personal injury or
death, and/or equipment damage. Service per-
sonnel must be trained and experienced to per-
form electrical and mechanical service. Read
and follow Safety Precautions, on pages iii and
Copyright 2001 Cummins Power Generation. All rights reserved.
Cummins and PowerCommand are registered trademarks of Cummins Inc.
•
•
•
•
•
•
•
•
•
•
•
•
•
•
•
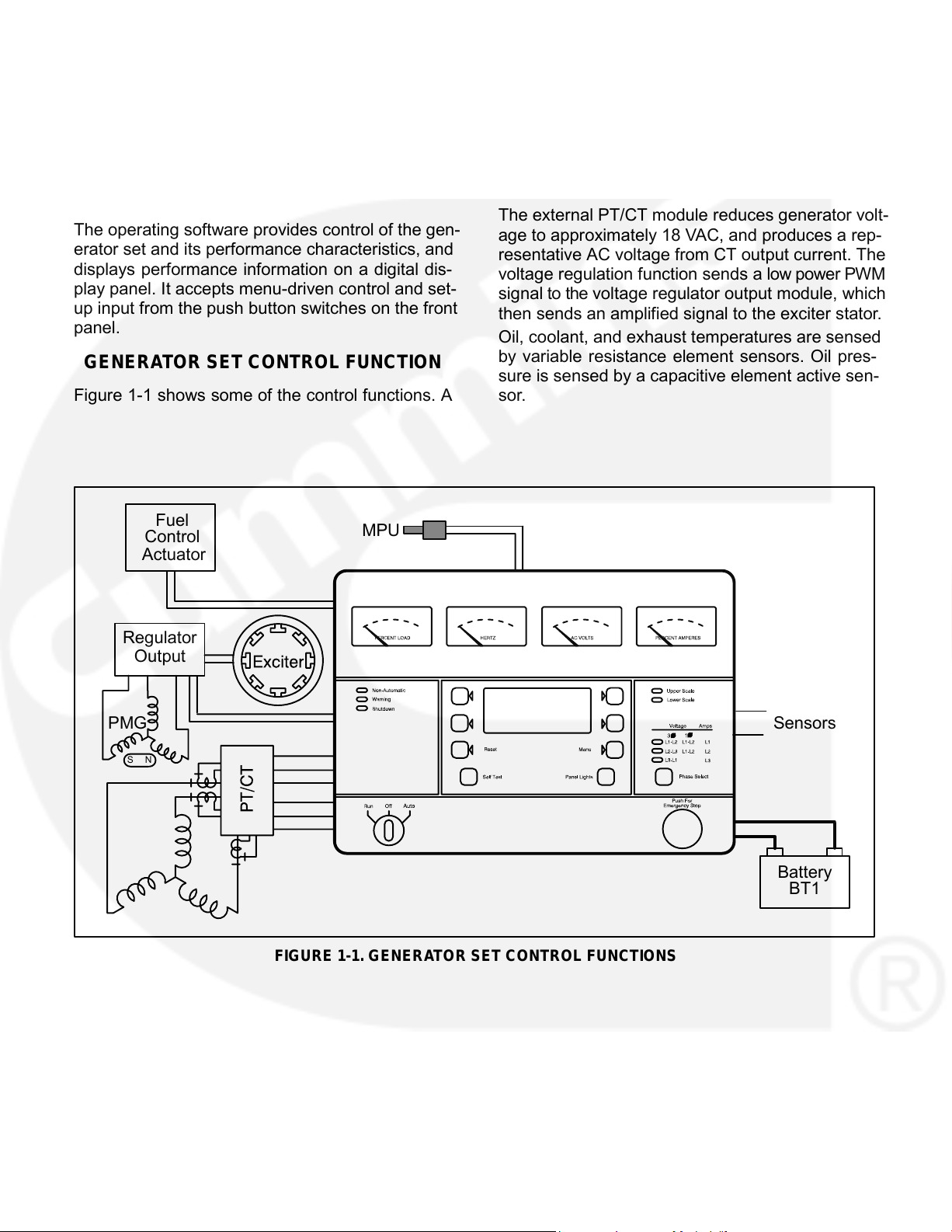
more complete block diagram is provided in Section
3. A system schematic is provided in Section 8.
The PCC is a microprocessor-based control for
The PCC monitors frequency from both the mag-
Cummins generator sets. It provides fuel control
netic pick-up (MPU) and the main stator inputs. The
and engine speed governing, main alternator volt-
control sends a low power pulse-width modulated
age output regulation, and complete generator set
(PWM) signal to the fuel control actuator.
The external PT/CT module reduces generator volt-
The operating software provides control of the gen-
age to approximately 18 VAC, and produces a rep-
erator set and its performance characteristics, and
resentative AC voltage from CT output current. The
displays performance information on a digital dis-
voltage regulation function sends a low power PWM
play panel. It accepts menu-driven control and set-
signal to the voltage regulator output module, which
up input from the push button switches on the front
then sends an amplified signal to the exciter stator.
Oil, coolant, and exhaust temperatures are sensed
by variable resistance element sensors. Oil pres-
GENERATOR SET CONTROL FUNCTION
sure is sensed by a capacitive element active sen-
Figure 1-1 shows some of the control functions. A
FIGURE 1-1. GENERATOR SET CONTROL FUNCTIONS
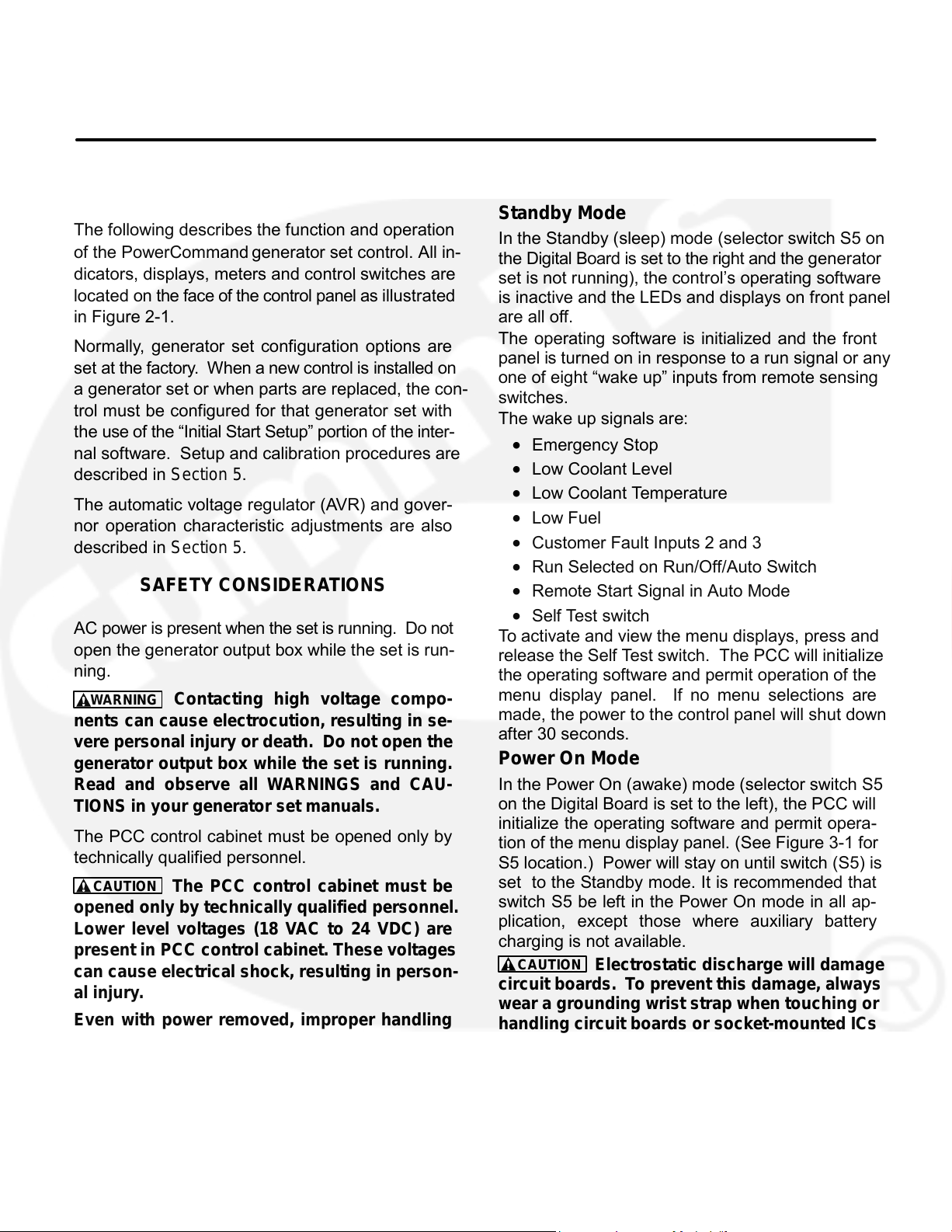
PCC POWER ON / STANDBY MODE
The following describes the function and operation
In the Standby (sleep) mode (selector switch S5 on
of the PowerCommand generator set control. All in-
the Digital Board is set to the right and the generator
dicators, displays, meters and control switches are
set is not running), the control’s operating software
located on the face of the control panel as illustrated
is inactive and the LEDs and displays on front panel
The operating software is initialized and the front
Normally, generator set configuration options are
panel is turned on in response to a run signal or any
set at the factory. When a new control is installed on
one of eight “wake up” inputs from remote sensing
a generator set or when parts are replaced, the con-
trol must be configured for that generator set with
the use of the “Initial Start Setup” portion of the inter-
nal software. Setup and calibration procedures are
The automatic voltage regulator (AVR) and gover-
nor operation characteristic adjustments are also
Customer Fault Inputs 2 and 3
Run Selected on Run/Off/Auto Switch
Remote Start Signal in Auto Mode
AC power is present when the set is running. Do not
To activate and view the menu displays, press and
open the generator output box while the set is run-
release the Self Test switch. The PCC will initialize
the operating software and permit operation of the
menu display panel. If no menu selections are
WARNING
Contacting high voltage compo-
made, the power to the control panel will shut down
nents can cause electrocution, resulting in se-
vere personal injury or death. Do not open the
generator output box while the set is running.
In the Power On (awake) mode (selector switch S5
Read and observe all WARNINGS and CAU-
on the Digital Board is set to the left), the PCC will
TIONS in your generator set manuals.
initialize the operating software and permit opera-
The PCC control cabinet must be opened only by
tion of the menu display panel. (See Figure 3-1 for
technically qualified personnel.
S5 location.) Power will stay on until switch (S5) is
set to the Standby mode. It is recommended that
The PCC control cabinet must be
switch S5 be left in the Power On mode in all ap-
opened only by technically qualified personnel.
plication, except those where auxiliary battery
Lower level voltages (18 VAC to 24 VDC) are
charging is not available.
present in PCC control cabinet. These voltages
CAUTION
Electrostatic discharge will damage
can cause electrical shock, resulting in person-
circuit boards. To prevent this damage, always
wear a grounding wrist strap when touching or
Even with power removed, improper handling
handling circuit boards or socket-mounted ICs
of components can cause electrostatic dis-
and when disconnecting or connecting harness
charge and damage to circuit components.
CAUTION
•
•
•
•
•
•
•
•
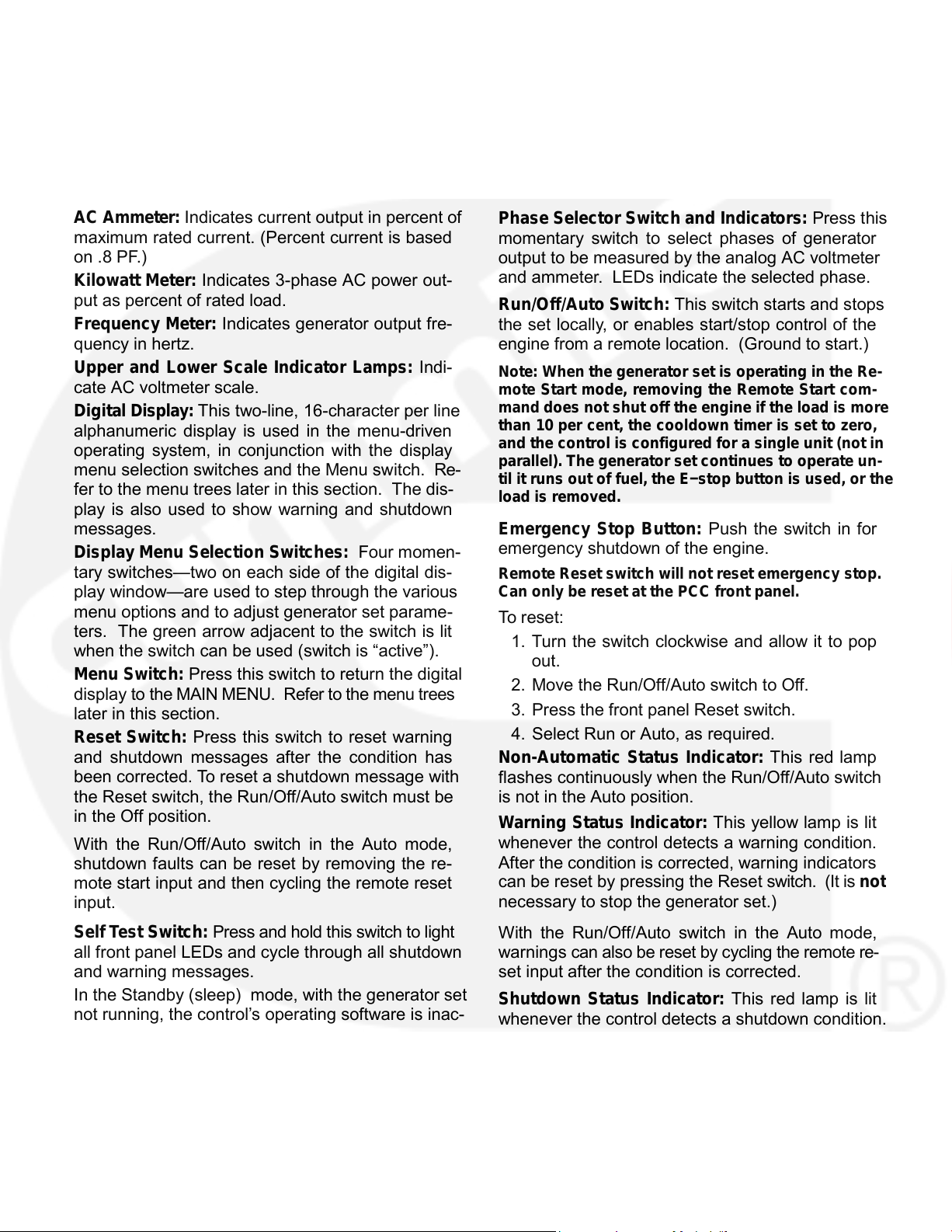
operation of the menu display panel. If no menu
selections are made, a software timer will shut
Figure 2-1 shows the features of the front panel.
down the power after 30 seconds.
Panel Lights Switch: Press this switch to turn con-
AC Voltmeter: Dual scale instrument indicates AC
trol panel illumination on and off. The illumination
voltage. Measurement scale in use is shown on
will shut off after about eight minutes.
AC Ammeter: Indicates current output in percent of
Phase Selector Switch and Indicators: Press this
maximum rated current. (Percent current is based
momentary switch to select phases of generator
output to be measured by the analog AC voltmeter
and ammeter. LEDs indicate the selected phase.
Kilowatt Meter: Indicates 3-phase AC power out-
put as percent of rated load.
Run/Off/Auto Switch: This switch starts and stops
Frequency Meter: Indicates generator output fre-
the set locally, or enables start/stop control of the
engine from a remote location. (Ground to start.)
Upper and Lower Scale Indicator Lamps: Indi-
Note: When the generator set is operating in the Re-
mote Start mode, removing the Remote Start com-
mand does not shut off the engine if the load is more
Digital Display: This two-line, 16-character per line
than 10 per cent, the cooldown timer is set to zero,
alphanumeric display is used in the menu-driven
and the control is configured for a si n g le unit (not in
operating system, in conjunction with the display
parallel). The generator set continues to operate un-
menu selection switches and the Menu switch. Re-
til it runs out of fuel, the E−stop button is used, or the
fer to the menu trees later in this section. The dis-
play is also used to show warning and shutdown
Emergency Stop Button: Push the switch in for
emergency shutdown of the engine.
Display Menu Selection Switches: Four momen-
tary switches—two on each side of the digital dis-
Remote Reset switch will not reset emergency stop.
play window—are used to step through the various
Can only be reset at the PCC front panel.
menu options and to adjust generator set parame-
ters. The green arrow adjacent to the switch is lit
1. Turn the switch clockwise and allow it to pop
when the switch can be used (switch is “active”).
Menu Switch: Press this switch to return the digital
2. Move the Run/Off/Auto switch to Off.
display to the MAIN MENU. Refer to the menu trees
3. Press the front panel Reset switch.
4. Select Run or Auto, as required.
Reset Switch: Press this switch to reset warning
Non-Automatic Status Indicator: This red lamp
and shutdown messages after the condition has
been corrected. To reset a shutdown message with
flashes continuously when the Run/Off/Auto switch
the Reset switch, the Run/Off/Auto switch must be
is not in the Auto position.
Warning Status Indicator: This yellow lamp is lit
whenever the control detects a warning condition.
With the Run/Off/Auto switch in the Auto mode,
After the condition is corrected, warning indicators
shutdown faults can be reset by removing the re-
can be reset by pressing the Reset switch. (It is not
mote start input and then cycling the remote reset
necessary to stop the generator set.)
Self Test Switch: Press and hold this switch to light
With the Run/Off/Auto switch in the Auto mode,
all front panel LEDs and cycle through all shutdown
warnings can also be reset by cycling the remote re-
set input after the condition is corrected.
In the Standby (sleep) mode, with the generator set
Shutdown Status Indicator: This red lamp is lit
not running, the control’s operating software is inac-
whenever the control detects a shutdown condition.
tive and the LEDs and displays on front panel are all
After the condition is corrected, shutdown indica-
tors can be reset by turning the Run/Off/Auto switch
To activate and view the menu displays without
to the Off position, and pressing the Reset switch.
starting the generator set, press and hold the Self
In Auto mode, shutdowns can be reset by removing
Test switch until the front panel LEDs light. The
the remote start input and then cycling the remote
PCC will initialize the operating software and permit
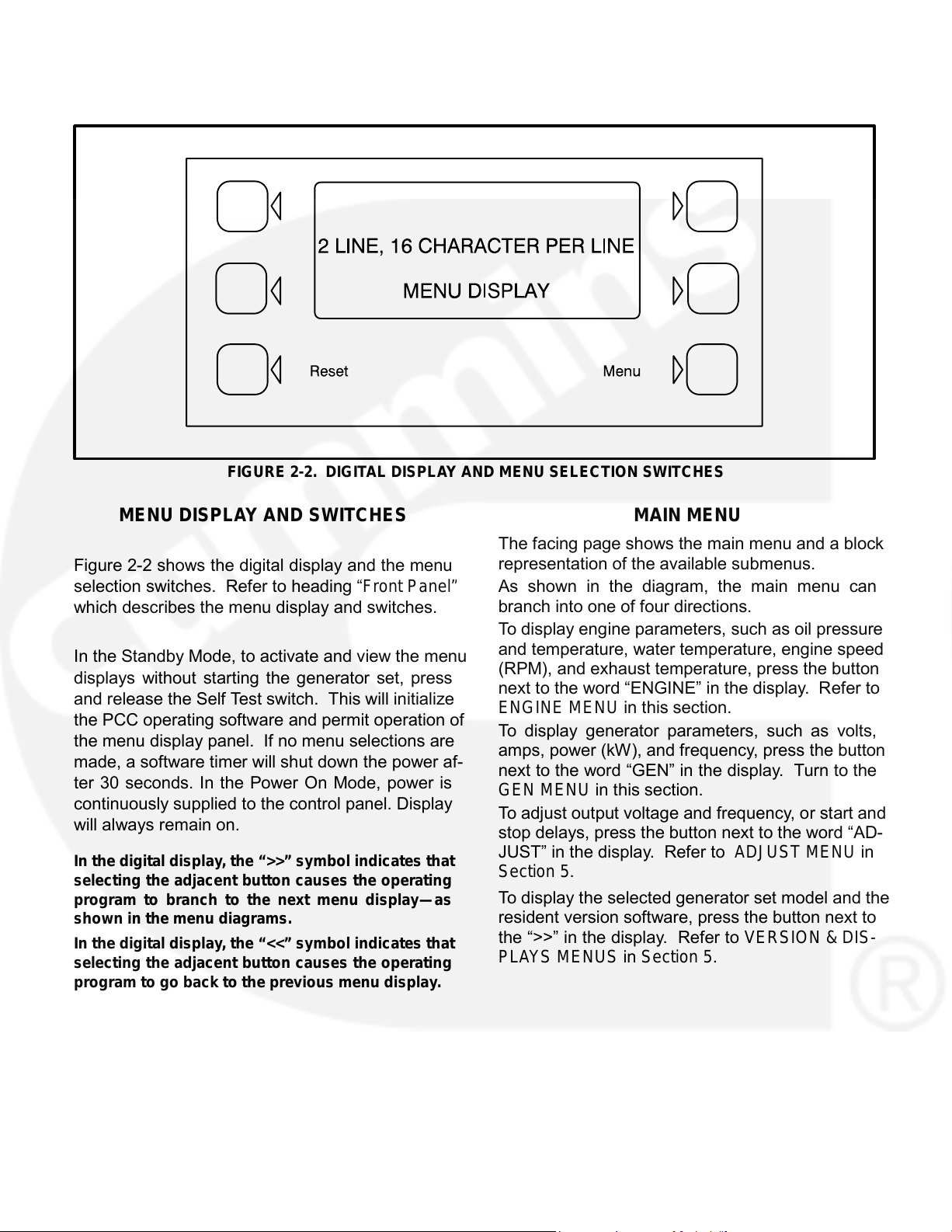
Stop shutdown status (Code 102 ) ca n be
reset only at the PCC front panel.
FIGURE 2-2. DIGITAL DISPLAY AND MENU SELECTION SWITCHES
MENU DISPLAY AND SWITCHES
The facing page shows the main menu and a block
representation of the available submenus.
Figure 2-2 shows the digital display and the menu
selection switches. Refer to heading “Front Panel”
As shown in the diagram, the main menu can
branch into one of four directions.
which describes the menu display and switches.
To display engine parameters, such as oil pressure
and temperature, water temperature, engine speed
In the Standby Mode, to activate and view the menu
(RPM), and exhaust temperature, press the button
displays without starting the generator set, press
next to the word “ENGINE” in the display. Refer to
and release the Self Test switch. This will initialize
ENGINE MENU in this section.
the PCC operating software and permit operation of
To display generator parameters, such as volts,
the menu display panel. If no menu selections are
amps, power (kW), and frequency, press the button
made, a software timer will shut down the power af-
next to the word “GEN” in the display. Turn to the
ter 30 seconds. In the Power On Mode, power is
GEN MENU in this section.
continuously supplied to the control panel. Display
To adjust output voltage and frequency, or start and
stop delays, press the button next to the word “AD-
JUST” in the display. Refer to ADJUST MENU in
In the digital display, the “>>” symbol indicates that
selecting the adjacent button causes the operating
To display the selected generator set model and the
program to branch to the next menu display—as
resident version software, press the button next to
shown in the menu diagrams.
the “>>” in the display. Refer to VERSIO N & DIS-
In the digital display, the “<<” symbol indicates that
PLAYS MENUS in Section 5.
selecting the adjacent button causes the operating
program to go back to the previous menu display.
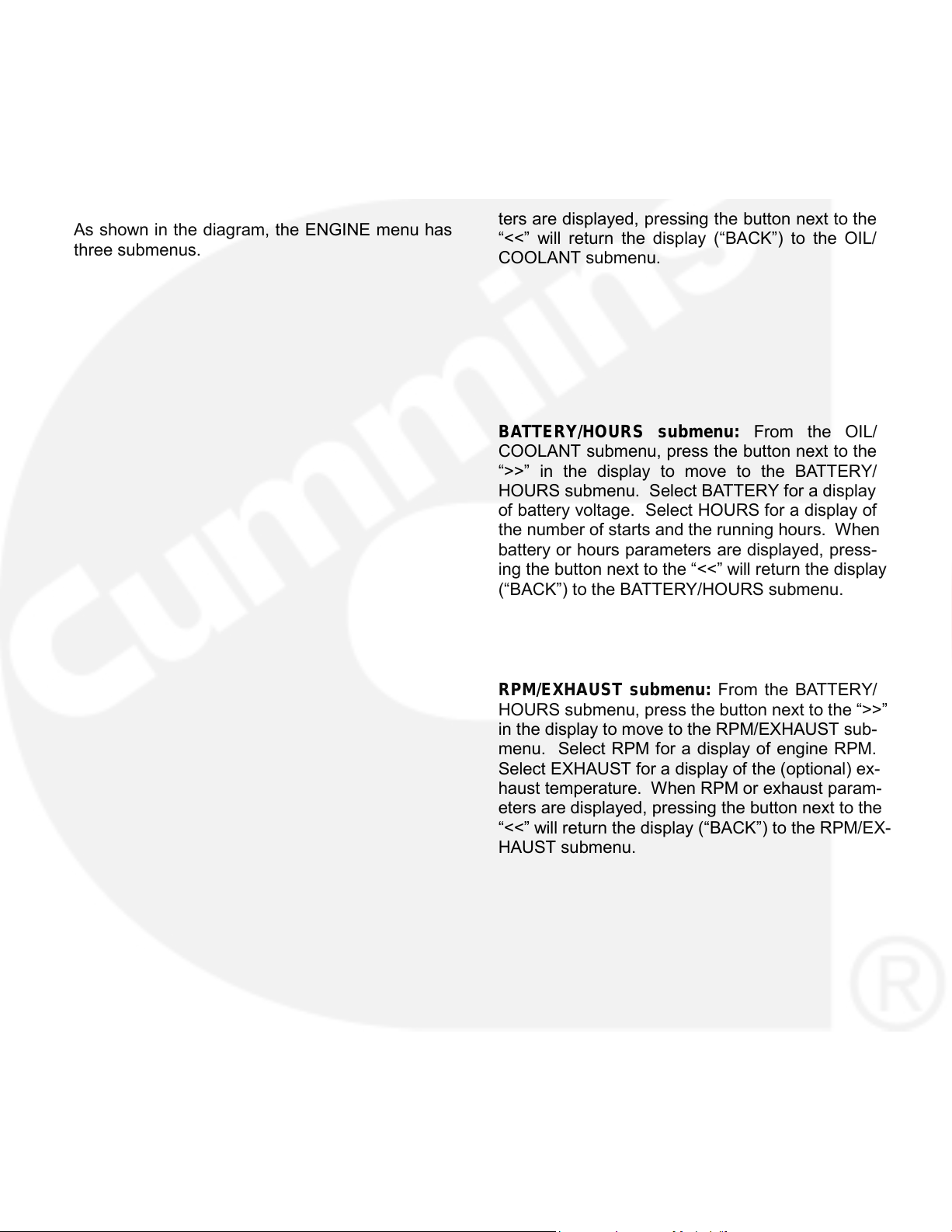
OIL/COOLANT submenu: This is the first subme-
The facing page shows a block representation of
the ENGINE menu. If you press the button next to
nu. Select OIL for a display of oil pressure and oil
the word “ENGINE” in the display, the first ENGINE
temperature. Select COOLANT for a display of
coolant temperature. When oil or coolant parame-
ters are displayed, pressing the button next to the
As shown in the diagram, the ENGINE menu has
“<<” will return the display (“BACK”) to the OIL/
BATTERY/HOURS submenu: From the OIL/
COOLANT submenu, press the button next to the
“>>” in the display to move to the BATTERY/
HOURS submenu. Select BATTERY for a display
of battery voltage. Select HOURS for a display of
the number of starts and the running hours. When
battery or hours parameters are displayed, press-
ing the button next to the “<<” will return the display
(“BACK”) to the BATTERY/HOURS submenu.
RPM/EXHAUST submenu: From the BATTERY/
HOURS submenu, press the button next to the “>>”
in the display to move to the RPM/EXHAUST sub-
menu. Select RPM for a display of engine RPM.
Select EXHAUST for a display of the (optional) ex-
haust temperature. When RPM or exhaust param-
eters are displayed, pressing the button next to the
“<<” will return the display (“BACK”) to the RPM/EX-
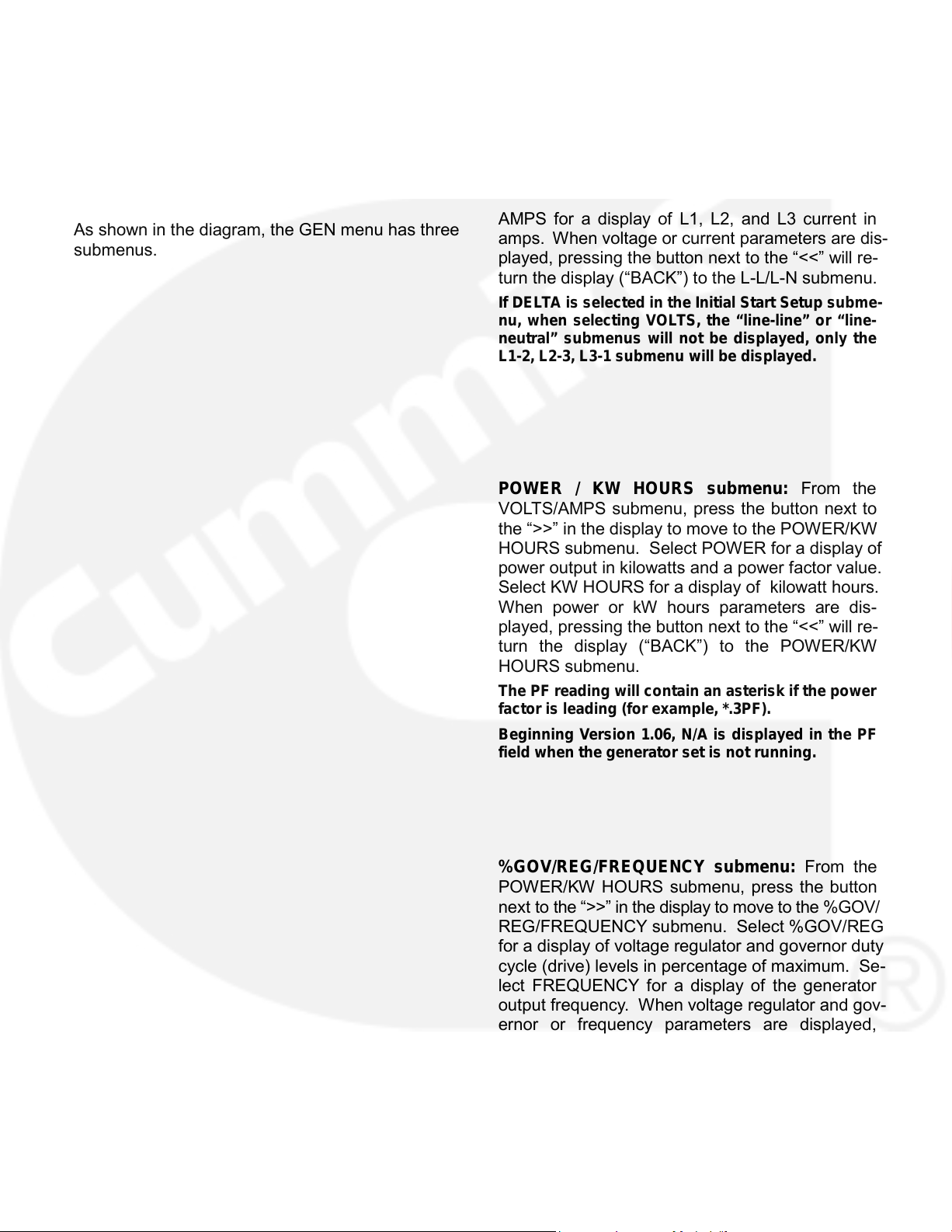
VOLTS/AMPS submenu: This is the first subme-
The facing page shows a block representation of
the GEN menu. If you press the button next to the
nu. Select VOLTS for a display of a line-line or line-
word “GEN” in the display, the first GEN submenu
neutral selection. Select line-line (L-L) or line-neu-
tral (L-N) for the desired voltage display. Select
AMPS for a display of L1, L2, and L3 current in
As shown in the diagram, the GEN menu has three
amps. When voltage or current parameters are dis-
played, pressing the button next to the “<<” will re-
turn the display (“BACK”) to the L-L/L-N submenu.
If DELTA is selected in the Initial Start Setup subme-
nu, when selecting VOLTS, the “line-line” or “line-
neutral” submenus will not be displayed, only the
L1-2, L2-3, L3-1 submenu will be displayed.
POWER / KW HOURS submenu: From the
VOLTS/AMPS submenu, press the button next to
the “>>” in the display to move to the POWER/KW
HOURS submenu. Select POWER for a display of
power output in kilowatts and a power factor value.
Select KW HOURS for a display of kilowatt hours.
When power or kW hours parameters are dis-
played, pressing the button next to the “<<” will re-
turn the display (“BACK”) to the POWER/KW
The PF reading will contain an asteri sk if the power
factor is leading (for example, *.3PF).
Beginning Version 1.06, N/A is displayed in the PF
field when the generator set is n o t running.
%GOV/REG/FREQUENCY submenu: From the
POW ER/KW HOURS submenu, press the button
next to the “>>” in the display to move to the %GOV/
REG/FREQUENCY submenu. Select %GOV/REG
for a display of voltage regulator and governor duty
cycle (drive) levels in percentage of maximum. Se-
lect FREQUENCY for a display of the generator
output frequency. When voltage regulator and gov-
ernor or frequency parameters are displayed,
pressing the button next to the “<<” will return the
display (“BACK”) to the %GOV/REG/FREQUENCY
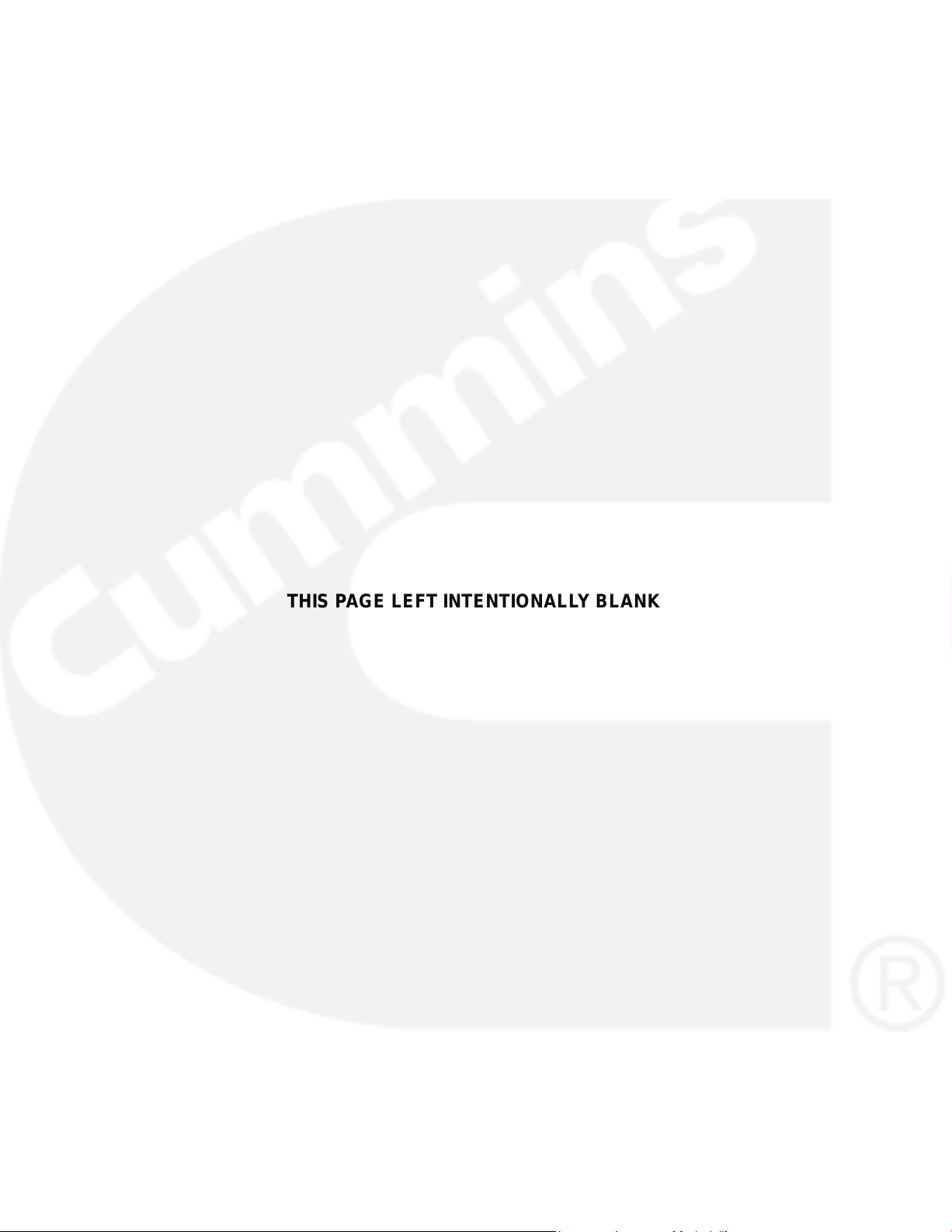
THIS PAGE LEFT INTENTIONALLY BLANK
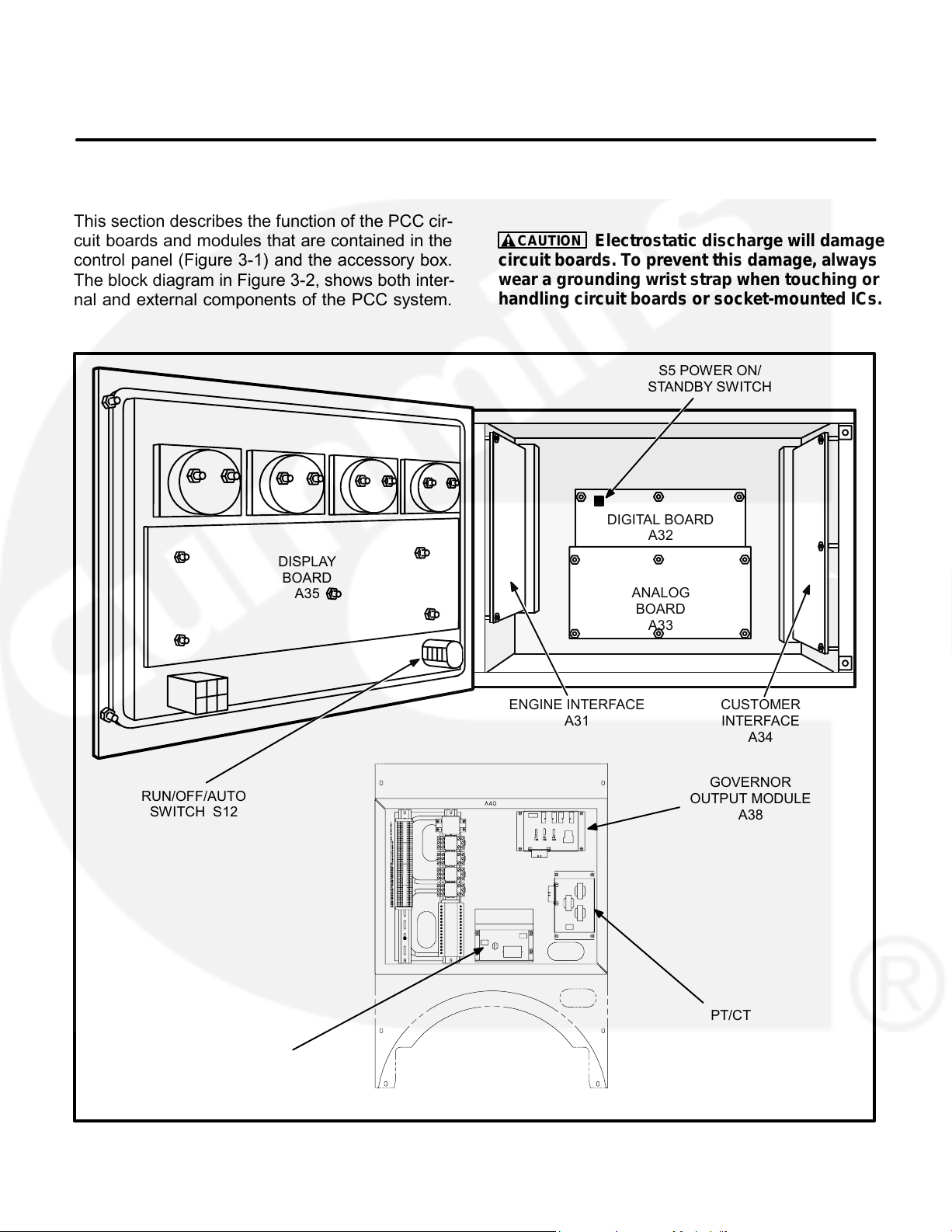
3. Circuit Boards and Modules
The system schematics are provided in Sect ion 9 of
This section describes the function of the PCC cir-
cuit boards and modules that are contained in the
CAUTION
Electrostatic discharge will damage
circuit boards. To prevent this damage, always
control panel (Figure 3-1) and the accessory box.
wear a grounding wrist strap when touching or
The block diagram in Figure 3-2, shows both inter-
handling circuit boards or socket-mounted ICs.
nal and external components of the PCC system.
FIGURE 3-1. CIRCUIT BOARD LOCATIONS
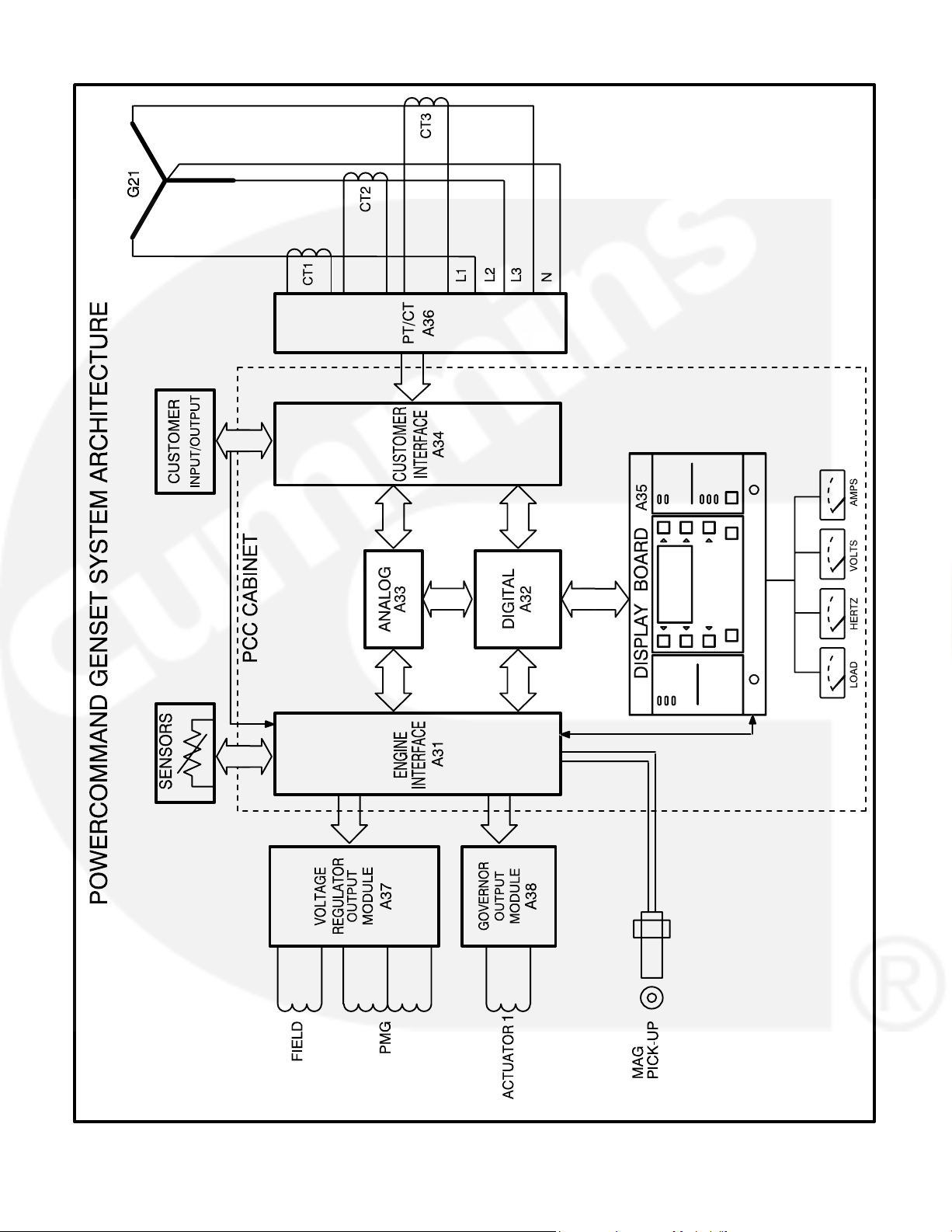
FIGURE 3-2. BLOCK DIAGRAM
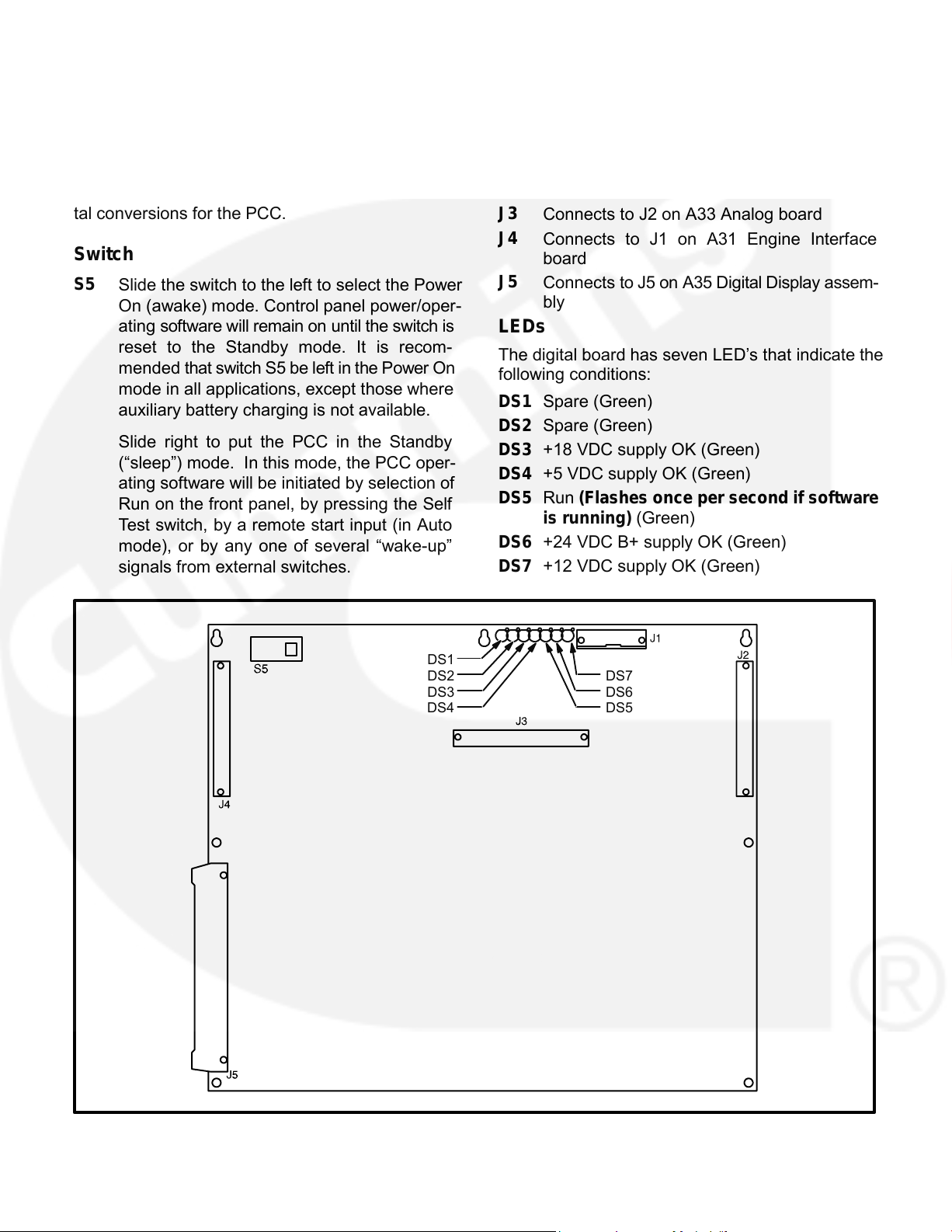
The digital board has five connectors. They are:
The digital circuit board (Figure 3-3) contains the
microprocessor and the operational software for the
Connects to J4 on A34 Customer Interface
control. It connects to all other boards inside the
control. This board also provides the analog-to-digi-
tal conversions for the PCC.
Connects to J2 on A33 Analog board
Connects to J1 on A31 Engine Interface
Connects to J5 on A35 Digital Display assem-
Slide the switch to the left to select the Power
On (awake) mode. Control panel power/oper-
ating software will remain on until the switch is
reset to the Standby mode. It is recom-
The digital board has seven LED’s that indicate the
mended that switch S5 be left in the Power On
mode in all applications, except those where
auxiliary battery charging is not available.
Slide right to put the PCC in the Standby
DS3 +18 VDC supply OK (Green)
(“sleep”) mode. In this mode, the PCC oper-
DS4 +5 VDC supply OK (Green)
ating software will be initiated by selection of
DS5 Run (Flashes once per second if software
Run on the front panel, by pressing the Self
Test switch, by a remote start input (in Auto
DS6 +24 VDC B+ supply OK (Green)
mode), or by any one of several “wake-up”
DS7 +12 VDC supply OK (Green)
signals from external switches.
FIGURE 3-3. DIGITAL BOARD
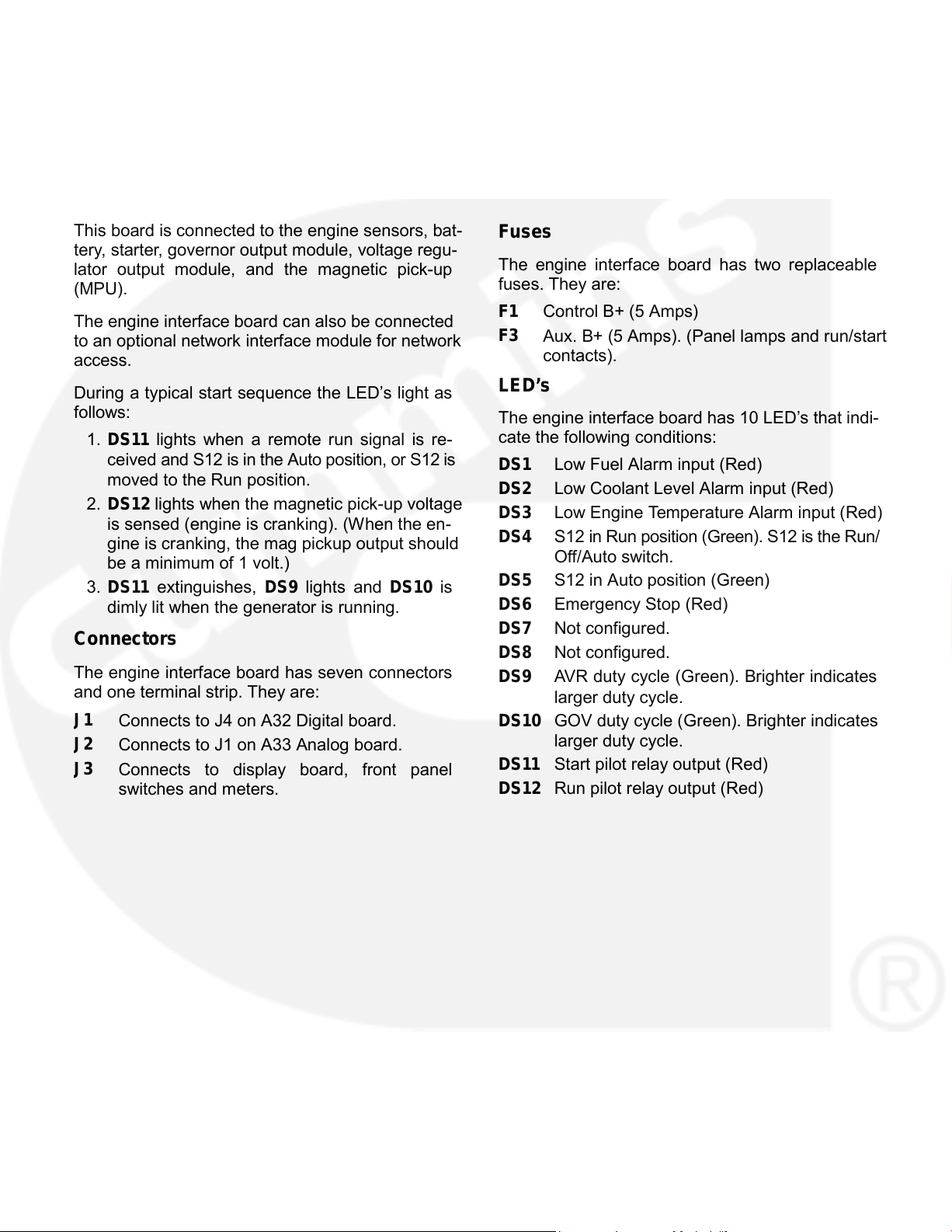
ENGINE INTERFACE BOARD (A31)
Connects to customer connections and to en-
gine harness which includes magnetic pick-
The engine interface board (Figure 3-4) reads user
control inputs, monitors engine, generator and sys-
Connects to engine sensors.
tem status, and initiates the appropriate action for
Connects to Genset Control module (GCM).
normal operating and fault conditions (warning or
Connects to Genset Control module (GCM).
This board is connected to the engine sensors, bat-
tery, starter, governor output module, voltage regu-
The engine interface board has two replaceable
lator output module, and the magnetic pick-up
The engine interface board can also be connected
Aux. B+ (5 Amps). (Panel lamps and run/start
to an optional network interface module for network
During a typical start sequence the LED’s light as
The engine interface board has 10 LED’s that indi-
cate the following conditions:
1. DS11 lights when a remote run signal is re-
ceived and S12 is in the Auto position, or S12 is
DS1 Low Fuel Alarm input (Red)
moved to the Run position.
DS2 Low Coolant Level Alarm input (Red)
2. DS12 lights when the magnetic pick-up voltage
DS3 Low Engine Temperature Alarm input (Red)
is sensed (engine is cranking). (When the en-
DS4 S12 in Run position (Green). S12 is the Run/
gine is cranking, the mag pickup output should
DS5 S12 in Auto position (Green)
3. DS11 extinguishes, DS9 lights and DS10 is
dimly lit when the generator is running.
The engine interface board has seven connectors
DS9 AVR duty cycle (Green). Brighter indicates
and one terminal strip. They are:
Connects to J4 on A32 Digital board.
DS10 GOV duty cycle (Green). Brighter indicates
Connects to J1 on A33 Analog board.
DS11 Start pilot relay output (Red)
Connects to display board, front panel
DS12 Run pilot relay output (Red)
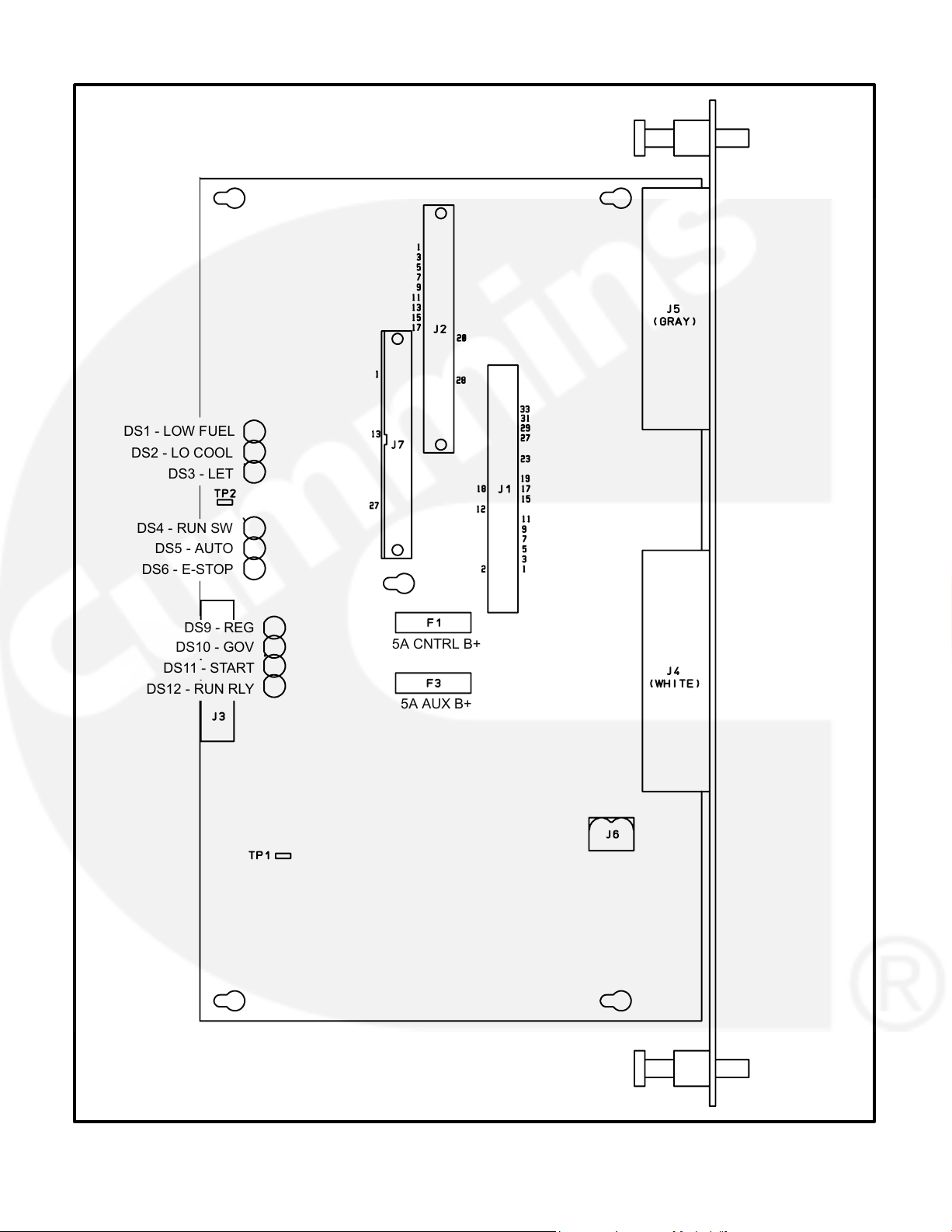
FIGURE 3-4. ENGINE INTERFACE BOARD
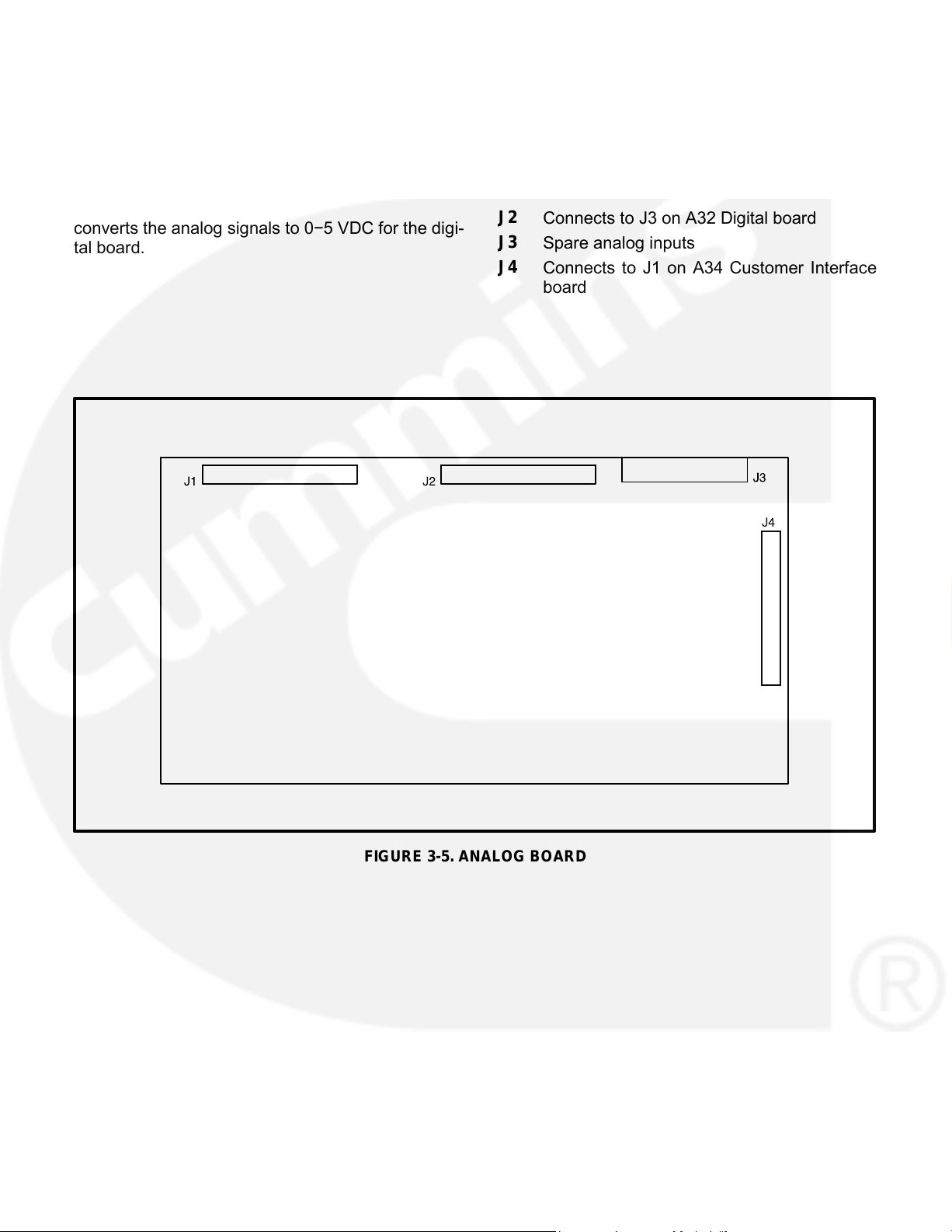
The analog board (Figure 3-5) is the only circuit
The analog board has four connectors with ribbon
board inside the control that has no LED’s. There
cables permanently soldered to them. They are:
are two versions of the analog board that are used
Connects to J2 on A31 Engine Interface
for paralleling and non-paralleling systems.
This board interprets all analog input signals and
Connects to J3 on A32 Digital board
converts the analog signals to 0−5 VDC for the digi-
Connects to J1 on A34 Customer Interface
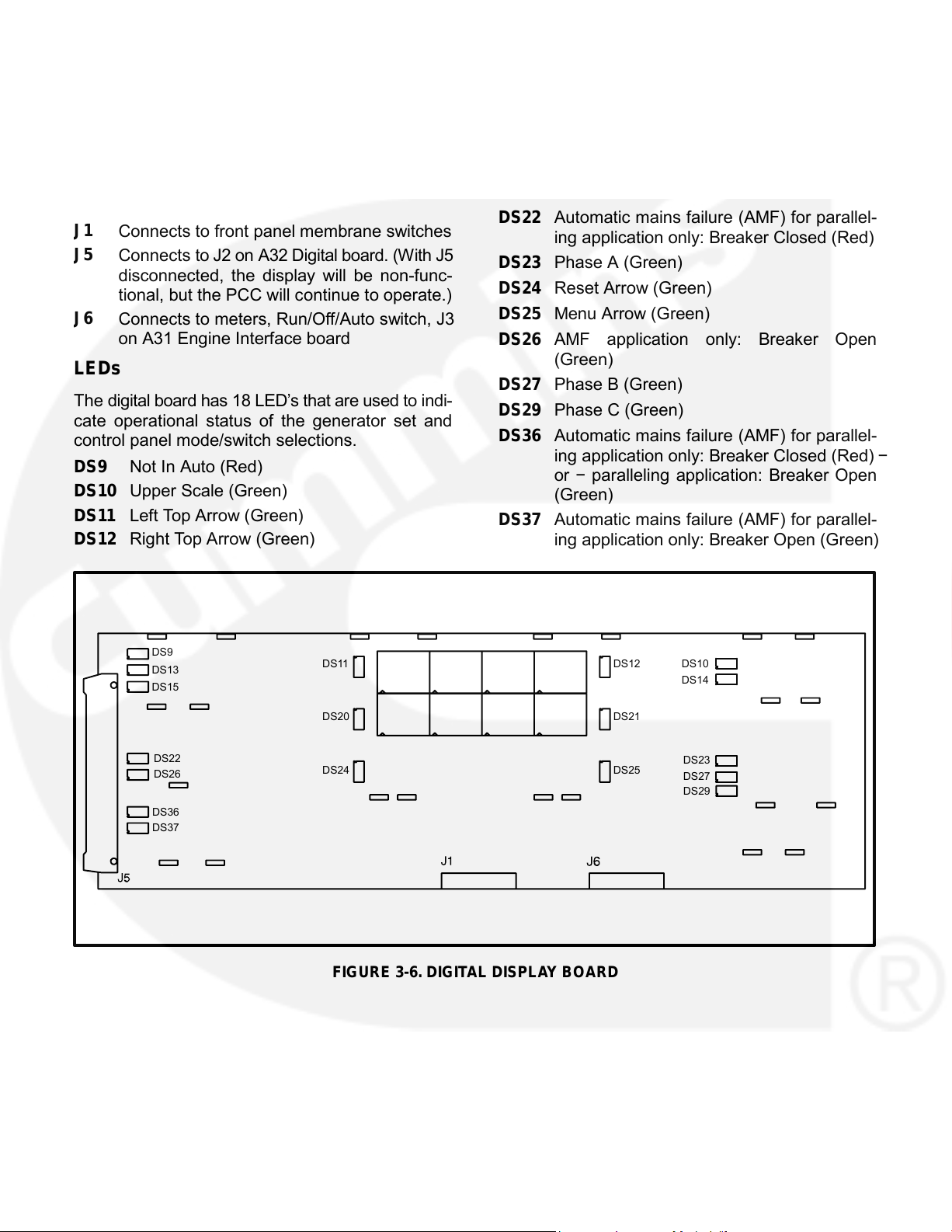
DIGITAL DISPLAY BOARD (A35)
The digital board (Figure 3-6) connects to all meters
DS20 Left Bottom Arrow (Green)
DS21 Right Bottom Arrow (Green)
The digital board has three connectors. They are:
DS22 Automatic mains failure (AMF) for parallel-
Connects to front panel membrane switches
ing application only: Breaker Closed (Red)
Connects to J2 on A32 Digital board. (With J5
disconnected, the display will be non-func-
tional, but the PCC will continue to operate.)
Connects to meters, Run/Off/Auto switch, J3
on A31 Engine Interface board
DS26 AMF application only: Breaker Open
The digital board has 18 LED’s that are used to indi-
cate operational status of the generator set and
DS36 Automatic mains failure (AMF) for parallel-
control panel mode/switch selections.
ing application only: Breaker Closed (Red) −
or − paralleling application: Breaker Open
DS11 Left Top Arrow (Green)
DS37 Automatic mains failure (AMF) for parallel-
DS12 Right Top Arrow (Green)
ing application only: Breaker Open (Green)
FIGURE 3-6. DIGITAL DISPLAY BOARD
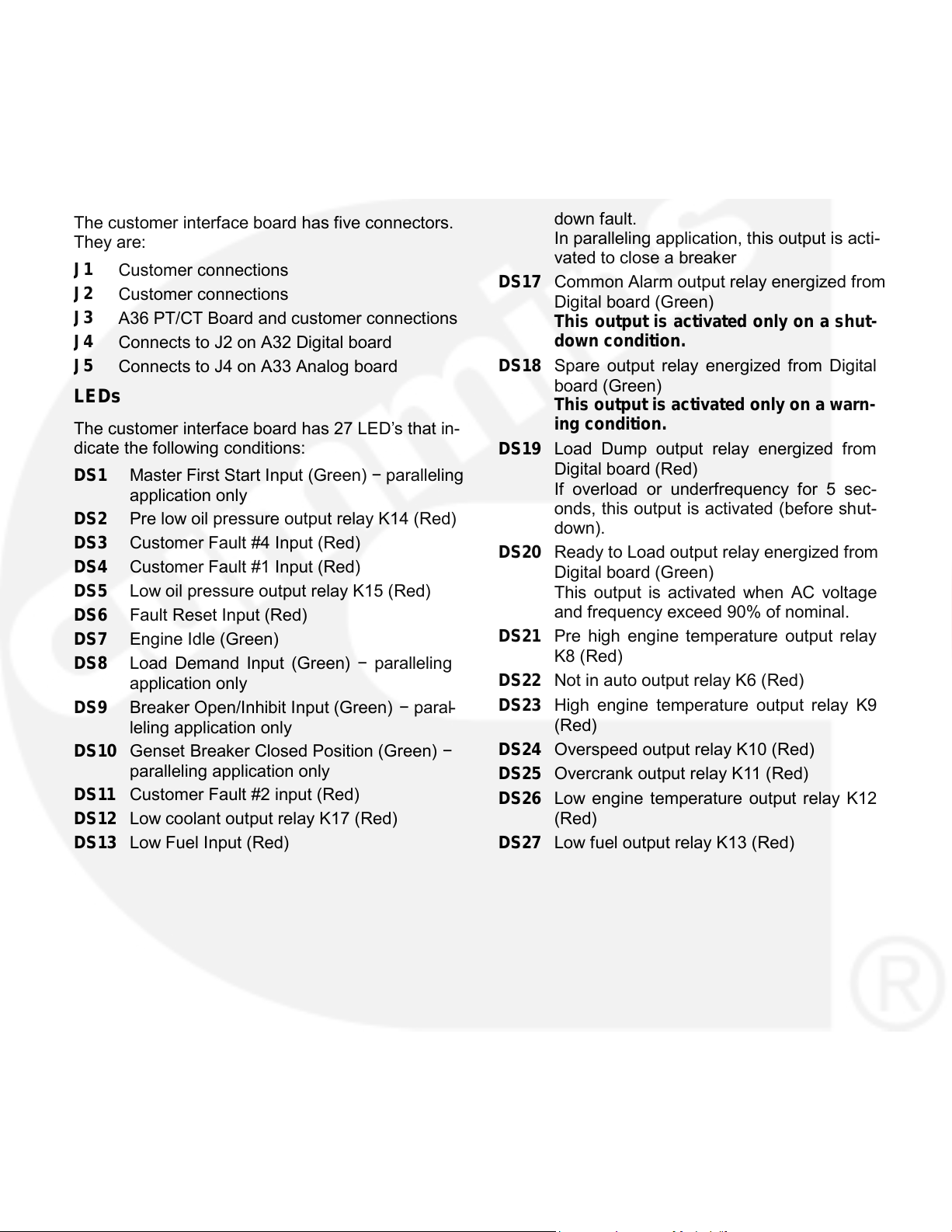
CUSTOMER INTERFACE BOAR D ( A34)
DS14 Remote Start input (Green)
DS15 Customer Fault #3 input (Red)
The customer interface board (Figure 3-7) connects
to the PT/CT board to bring in voltage and current. It
DS16 Breaker Control input relay energized from
also connects to customer inputs and outputs.
In single set application, this output is acti-
vated for a breaker trip when there is a shut-
The customer interface board has five connectors.
In paralleling application, this output is acti-
DS17 Common Alarm output relay energized from
A36 PT/CT Board and customer connections
This output is activated only on a shut-
Connects to J2 on A32 Digital board
DS18 Spare output relay energized from Digital
Connects to J4 on A33 Analog board
This output is activated only on a warn-
The customer interface board has 27 LED’s that in-
dicate the following conditions:
DS19 Load Dump output relay energized from
DS1 Master First Start Input (Green) − paralleling
If overload or underfrequency for 5 sec-
onds, this output is activated (before shut-
DS2 Pre low oil pressure output relay K14 (Red)
DS3 Customer Fault #4 Input (Red)
DS20 Ready to Load output relay energized from
DS4 Customer Fault #1 Input (Red)
DS5 Low oil pressure output relay K15 (Red)
This output is activated when AC voltage
and frequency exceed 90% of nominal.
DS6 Fault Reset Input (Red)
DS21 Pre high engine temperature output relay
DS8 Load Demand Input (Green) − paralleling
DS22 Not in auto output relay K6 (Red)
DS23 High engine temperature output relay K9
DS9 Breaker Open/Inhibit Input (Green) − paral-
DS24 Overspeed output relay K10 (Red)
DS10 Genset Breaker Closed Position (Green) −
paralleling application only
DS25 Overcrank output relay K11 (Red)
DS11 Customer Fault #2 input (Red)
DS26 Low engine temperature output relay K12
DS12 Low coolant output relay K17 (Red)
DS27 Low fuel output relay K13 (Red)
DS13 Low Fuel Input (Red)
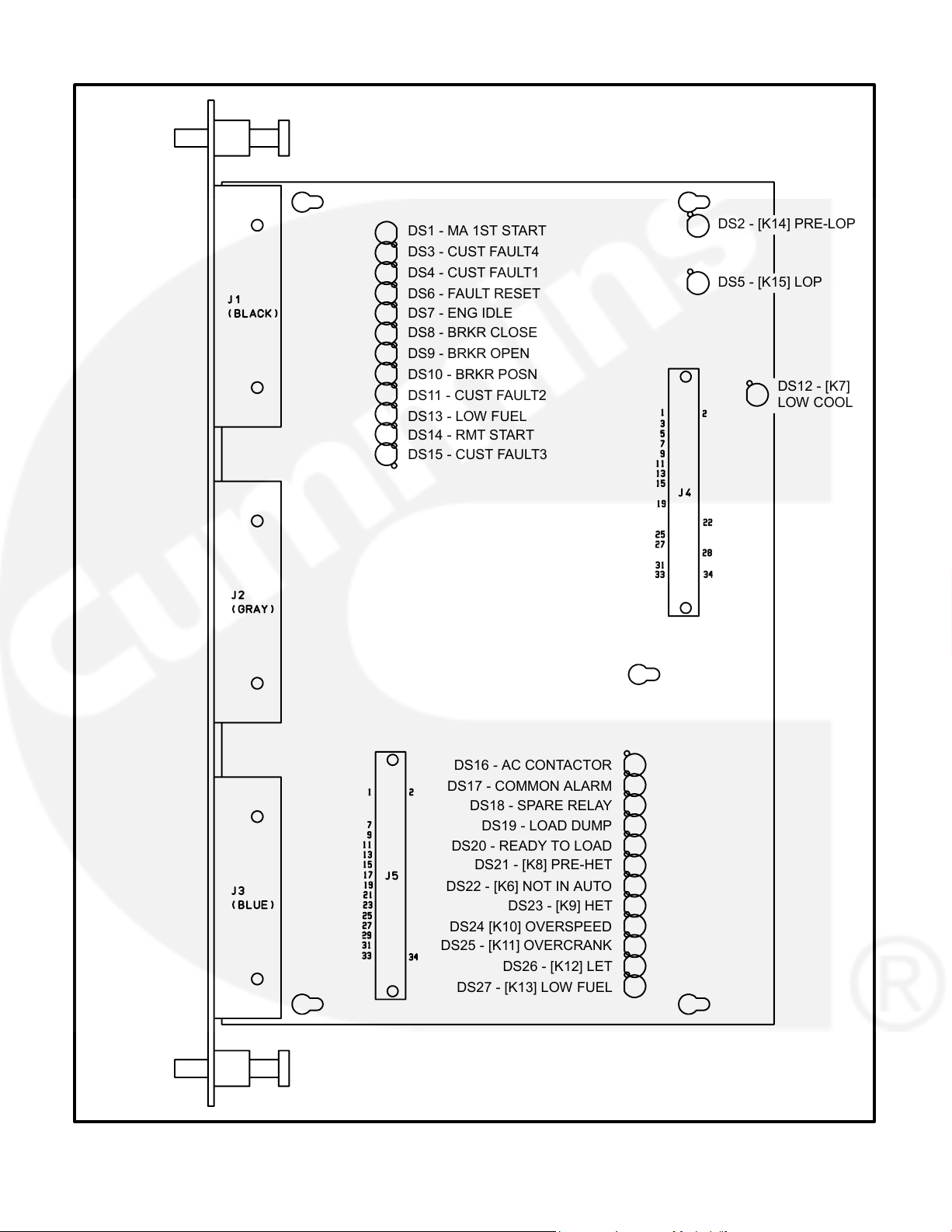
FIGURE 3-7. CUSTOMER INTERFACE BOARD
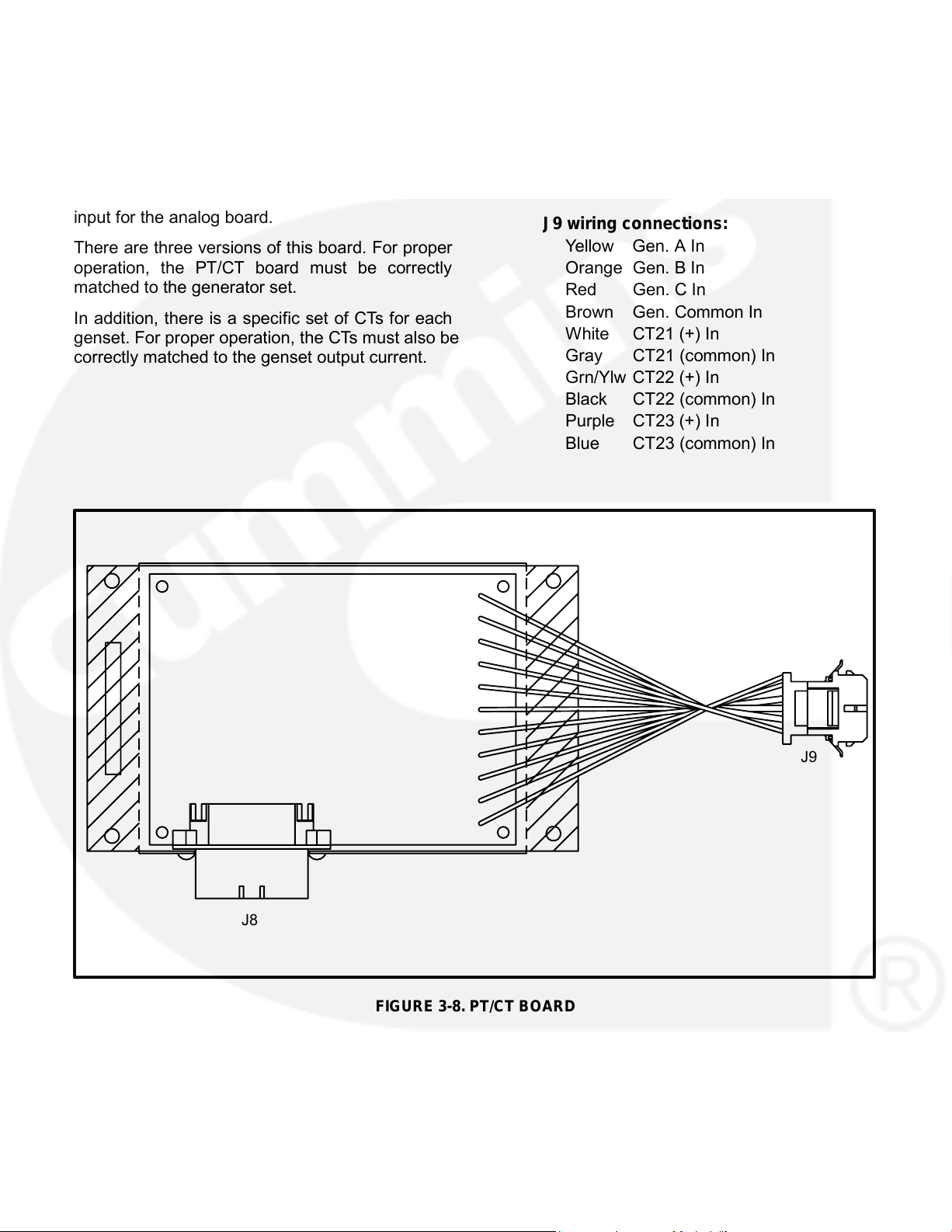
The PT/CT board has two connectors. They are:
The PT/CT board (Figure 3-8) is mounted inside the
accessory box. This board converts generator out-
Connects to J3 on A34 Customer Interface
put voltage to approximately 18 VAC levels for the
analog board. It also converts CT .55 amp (at full
Connects to AC harness (generator output
load) output to approximately 1.65 VAC (at full load)
input for the analog board.
There are three versions of this board. For proper
operation, the PT/CT board must be correctly
matched to the generator set.
In addition, there is a specific set of CTs for each
genset. For proper operation, the CTs must also be
correctly matched to the genset output current.
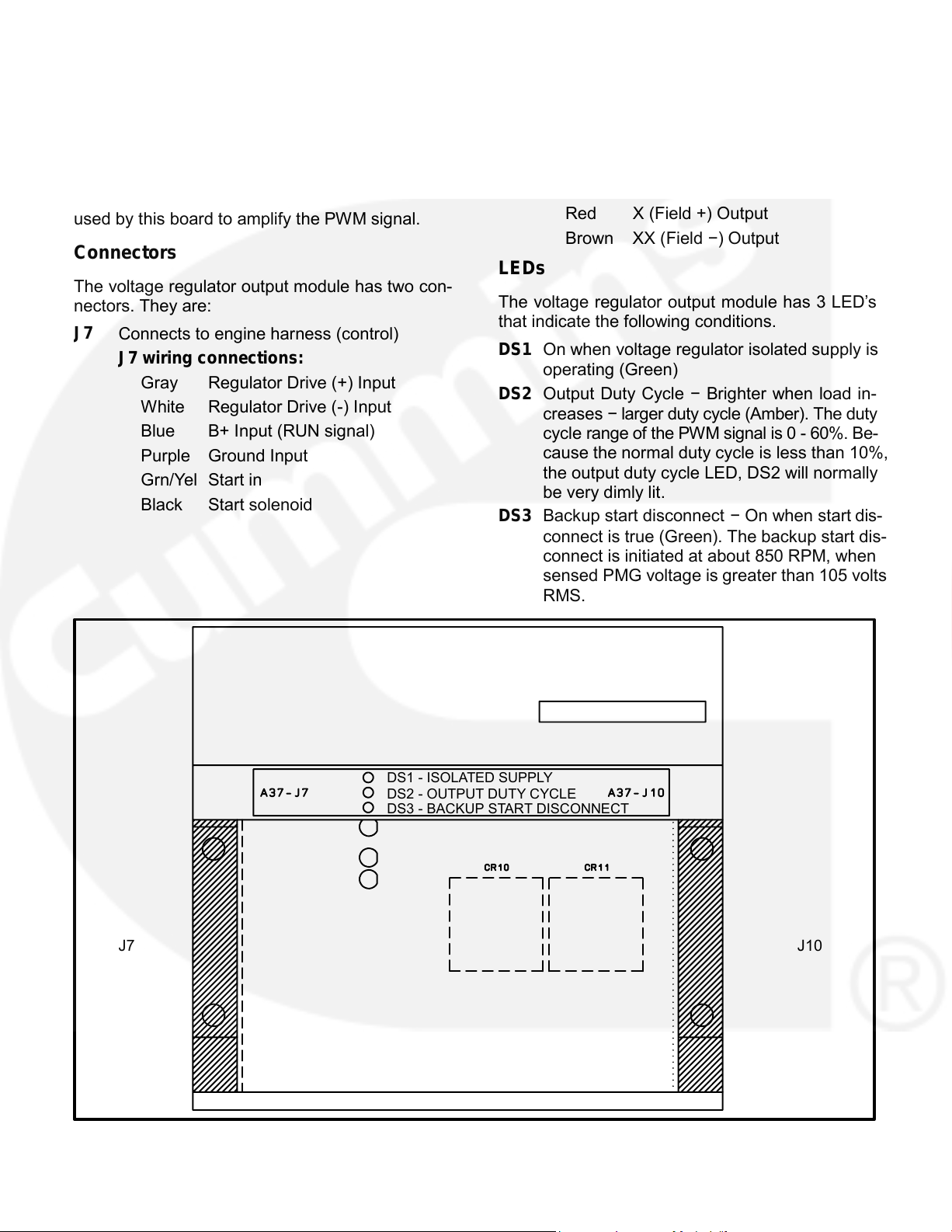
VOLTAGE REGULATOR OUTPUT MODULE
J10 Connects to engine harness (power)
The voltage regulator output module (Figure 3-9) is
a power amplifier. This board is used to amplify the
pulse-width modulated (PWM) signal from the PCC
to drive the exciter windings. Power from the PMG is
used by this board to amplify the PWM signal.
Brown XX (Field −) Output
The voltage regulator output module has two con-
The voltage regulator output module has 3 LED’s
that indicate the following conditions.
Connects to engine harness (control)
DS1 On when voltage regulator isolated supply is
Regulator Drive (+) Input
DS2 Output Duty Cycle − Brighter when load in-
White Regulator Drive (-) Input
creases − larger duty cycle (Amber). The duty
cycle range of the PWM signal is 0 - 60%. Be-
cause the normal duty cycle is less than 10%,
the output duty cycle LED, DS2 will normally
DS3 Backup start disconnect − On when start dis-
connect is true (Green). The backup start dis-
connect is initiated at about 850 RPM, when
sensed PMG voltage is greater than 105 volts
DS3 - BACKUP START DISCONNECT
FIGURE 3-9. VOLTAGE REGULATOR OUTPUT MODULE (A37)
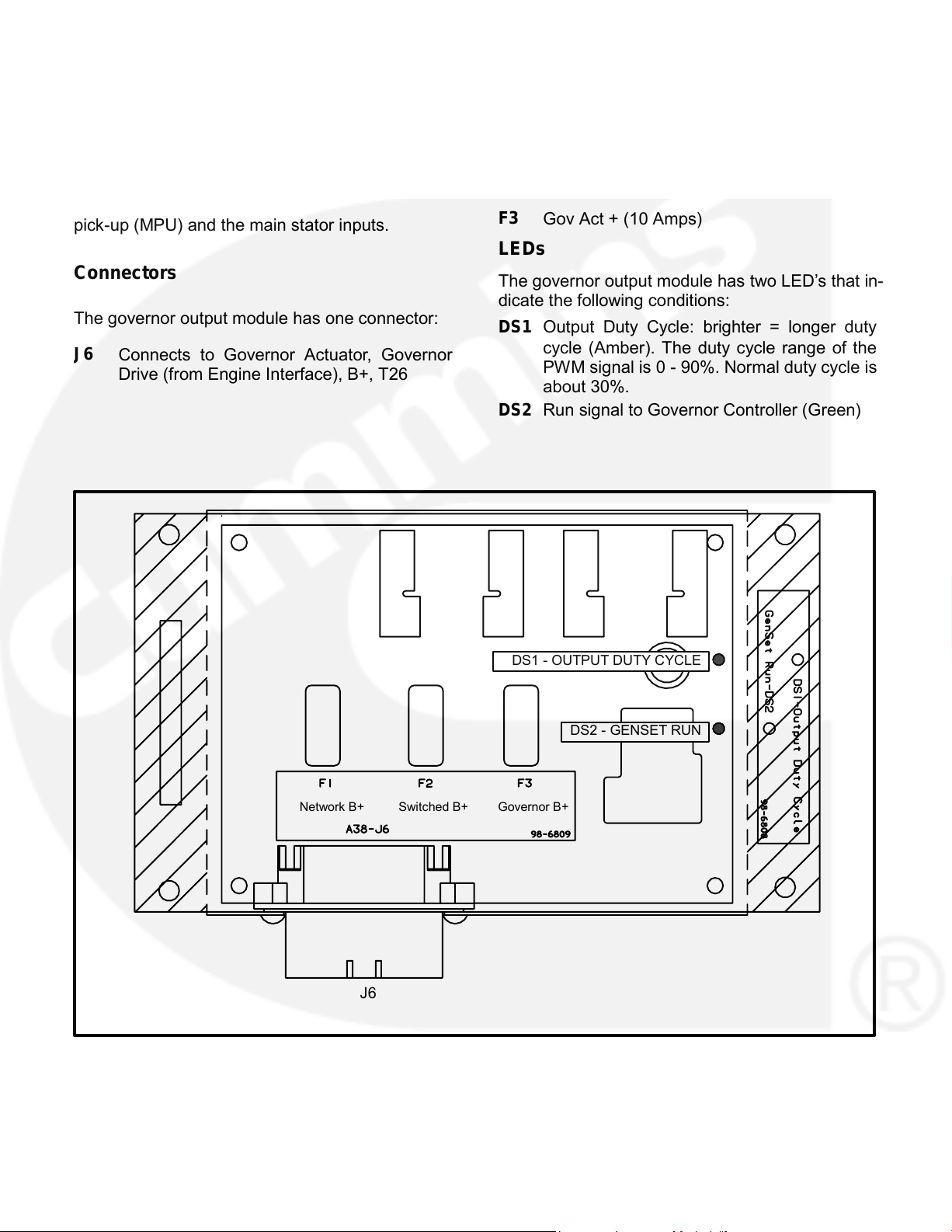
GOVERNOR OUTPUT MODULE (A38)
The governor output module has three fuses to pro-
The governor output module (Figure 3-10) receives
tect it from overloads and groundfaults. They are:
a low power pulse−width modulated (PWM) signal
from the engine interface board and then sends an
amplified signal to drive the governor actuator. The
Switched B+ (10 Amps) — T26
PCC monitors frequency from both the magnetic
pick-up (MPU) and the main stator inputs.
The governor output module has two LED’s that in-
dicate the following conditions:
The governor output module has one connector:
DS1 Output Duty Cycle: brighter = longer duty
cycle (Amber). The duty cycle range of the
Connects to Governor Actuator, Governor
PWM signal is 0 - 90%. Normal duty cycle is
Drive (from Engine Interface), B+, T26
DS2 Run signal to Governor Controller (Green)
Network B+
FIGURE 3-10. GOVERNOR OUTPUT MODULE (A38)
Switched B+ Governor B+
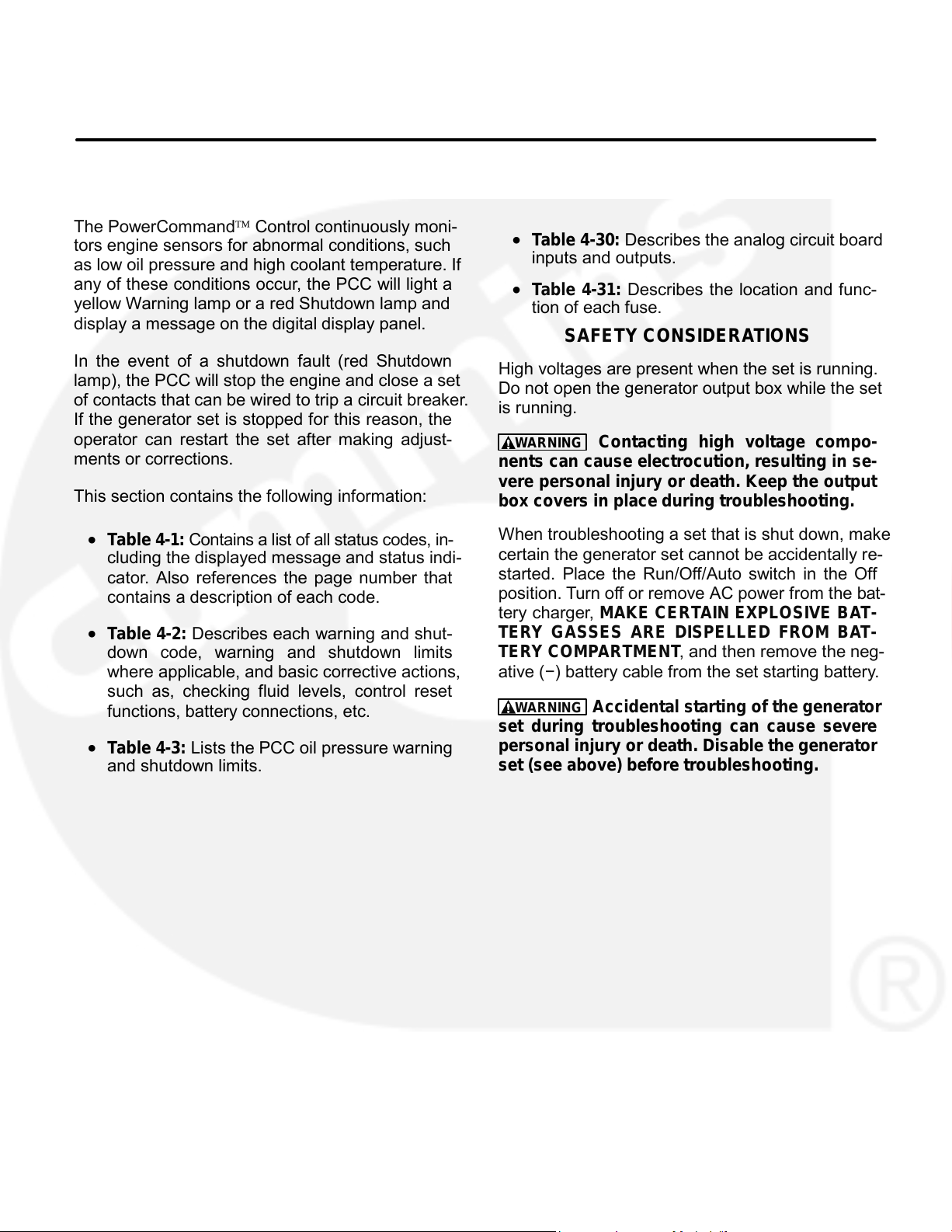
•
Tables 4-4 through 4-29: Provide detailed
troubleshooting procedures.
The PowerCommand Control continuously moni-
Table 4-30: Describes the analog circuit board
tors engine sensors for abnormal conditions, such
as low oil pressure and high coolant temperature. If
any of these conditions occur, the PCC will light a
Table 4-31: Describes the location and func-
yellow Warning lamp or a red Shutdown lamp and
display a message on the digital display panel.
In the event of a shutdown fault (red Shutdown
High voltages are present when the set is running.
lamp), the PCC will stop the engine and close a set
Do not open the generator output box while the set
of contacts that can be wired to trip a circuit breaker.
If the generator set is stopped for this reason, the
operator can restart the set after making adjust-
WARNING Contacting high voltage compo-
nents can cause electrocution, resulting in se-
vere personal injury or death. Keep the output
This section contains the following information:
box covers in place during troubleshooting.
When troubleshooting a set that is shut down, make
• Table 4-1: Contains a list of all status codes, in-
certain the generator set cannot be accidentally re-
cluding the displayed message and status indi-
started. Place the Run/Off/Auto switch in the Off
cator. Also references the page number that
position. Turn off or remove AC power from the bat-
contains a description of each code.
tery charger, MAKE CERTAIN EXPLOSIVE BAT-
TERY GASSES ARE DISPELLED FROM BAT-
Table 4-2: Describes each warning and shut-
TERY COMPARTMENT, and then remove the neg-
down code, warning and shutdown limits
where applicable, and basic corrective actions,
ative (−) battery cable from the set starting battery.
such as, checking fluid levels, control reset
WARNING Accidental starting of the generator
functions, battery connections, etc.
set during troubleshooting can cause severe
personal injury or death. Disable the generator
• Table 4-3: Lists the PCC oil pressure warning
set (see above) before troubleshooting.
•
•
•