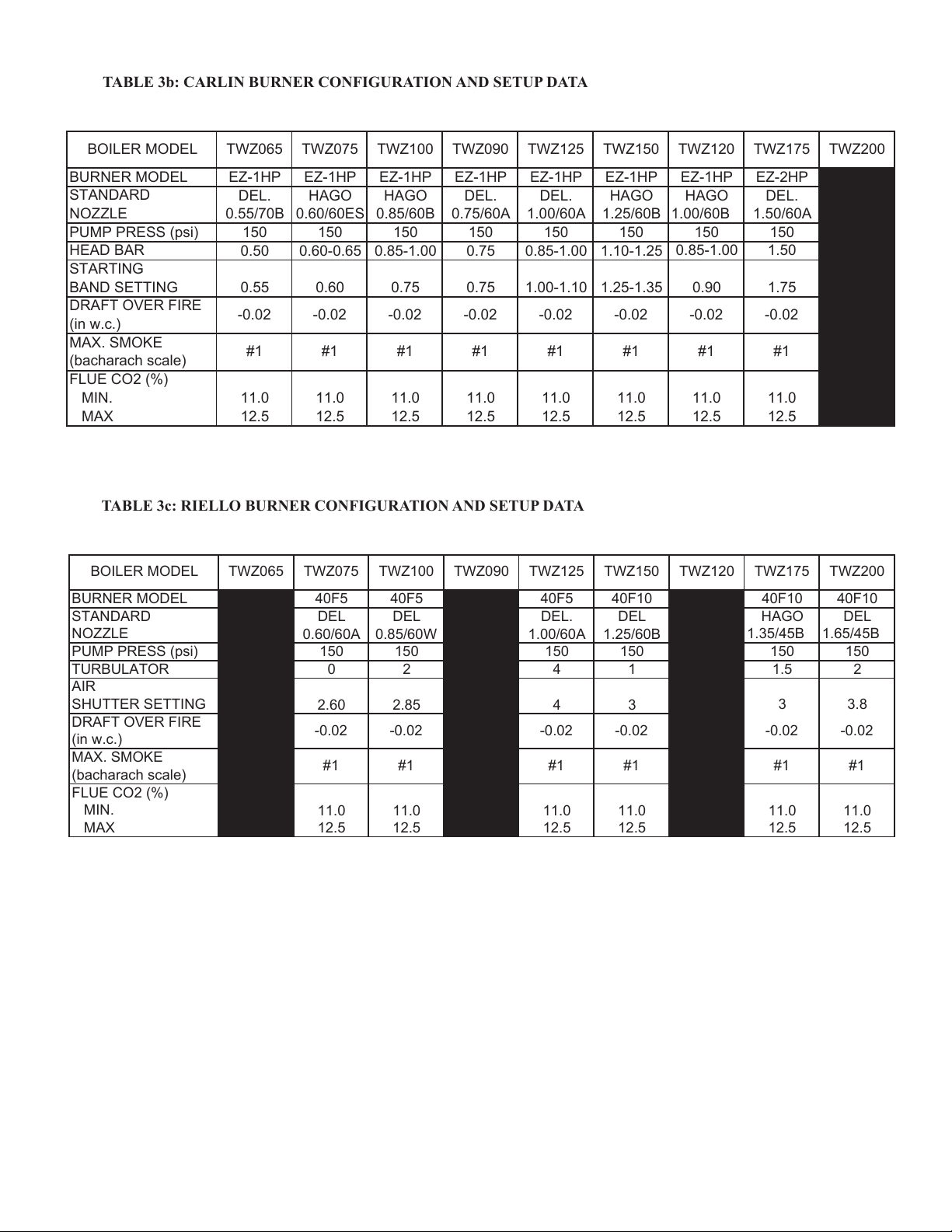
TABLE 3b: CARLIN BURNER CONFIGURATION AND SETUP DATA
BURNER MODEL
EZ-1HP EZ-1HP EZ-1HP EZ-1HP EZ-1HP EZ-1HP EZ-1HP EZ-2HP
STANDARD
DEL. HAGO HAGO DEL. DEL. HAGO HAGO DEL.
NOZZLE
0.55/70B 0.60/60ES 0.85/60B 0.75/60A 1.00/60A 1.25/60B
1.00/60B
1.50/60A
PUMP PRESS (psi)
150 150 150 150 150 150 150 150
HEAD BAR
0.50 0.60-0.65 0.85-1.00 0.75 0.85-1.00 1.10-1.25
0.85-1.00 1.50
STARTING
BAND SETTING
0.55 0.60 0.75 0.75 1.00-1.10 1.25-1.35
0.90 1.75
DRAFT OVER FIRE
(in w.c.)
MAX. SMOKE
(bacharach scale)
FLUE CO2 (%)
MIN.
11.0 11.0 11.0 11.0 11.0 11.0 11.0 11.0
MAX
12.5 12.5 12.5 12.5 12.5 12.5 12.5 12.5
TWZ125 TWZ150 TWZ120 TWZ175 TWZ200
-0.02 -0.02 -0.02 -0.02
BOILER MODEL TWZ065 TWZ075 TWZ100 TWZ090
#1 #1 #1
-0.02 -0.02 -0.02 -0.02
#1 #1 #1 #1 #1
BURNER MODEL
40F5 40F5 40F5 40F10 40F10 40F10
STANDARD
DEL DEL DEL. DEL HAGO DEL
NOZZLE
0.60/60A 0.85/60W 1.00/60A 1.25/60B
1.35/45B 1.65/45B
PUMP PRESS (psi)
150 150 150 150 150 150
TURBULATOR
0 2 4 1
1.5 2
AIR
SHUTTER SETTING
2.60 2.85 4 3
3 3.8
DRAFT OVER FIRE
(in w.c.)
MAX. SMOKE
(bacharach scale)
FLUE CO2 (%)
MIN.
11.0 11.0 11.0 11.0 11.0 11.0
MAX
12.5 12.5 12.5 12.5 12.5 12.5
TWZ150 TWZ120 TWZ175 TWZ200BOILER MODEL TWZ065 TWZ075 TWZ100 TWZ090 TWZ125
-0.02
#1 #1 #1 #1 #1 #1
-0.02-0.02 -0.02 -0.02 -0.02
TABLE 3c: RIELLO BURNER CONFIGURATION AND SETUP DATA
XII Service and Maintenance
The following procedure should be performed on an annual basis:
1) Turn off electrical power and oil supply to the boiler.
2) Clean the boiler as follows:
a) Remove vent connector and piping.
b) Remove barometric draft regulator.
c) Remove top jacket panel to gain access to boiler ue collector.
d) Unscrew four wing nuts and remove canopy retaining carriage bolts, lift off the canopy and ceramic ber sealing
e) Unplug the burner, disconnect the oil lines (if the pump is hard piped), and remove the two 5/16” bolts securing the
strips.
burner door. Open the burner swing door.
25
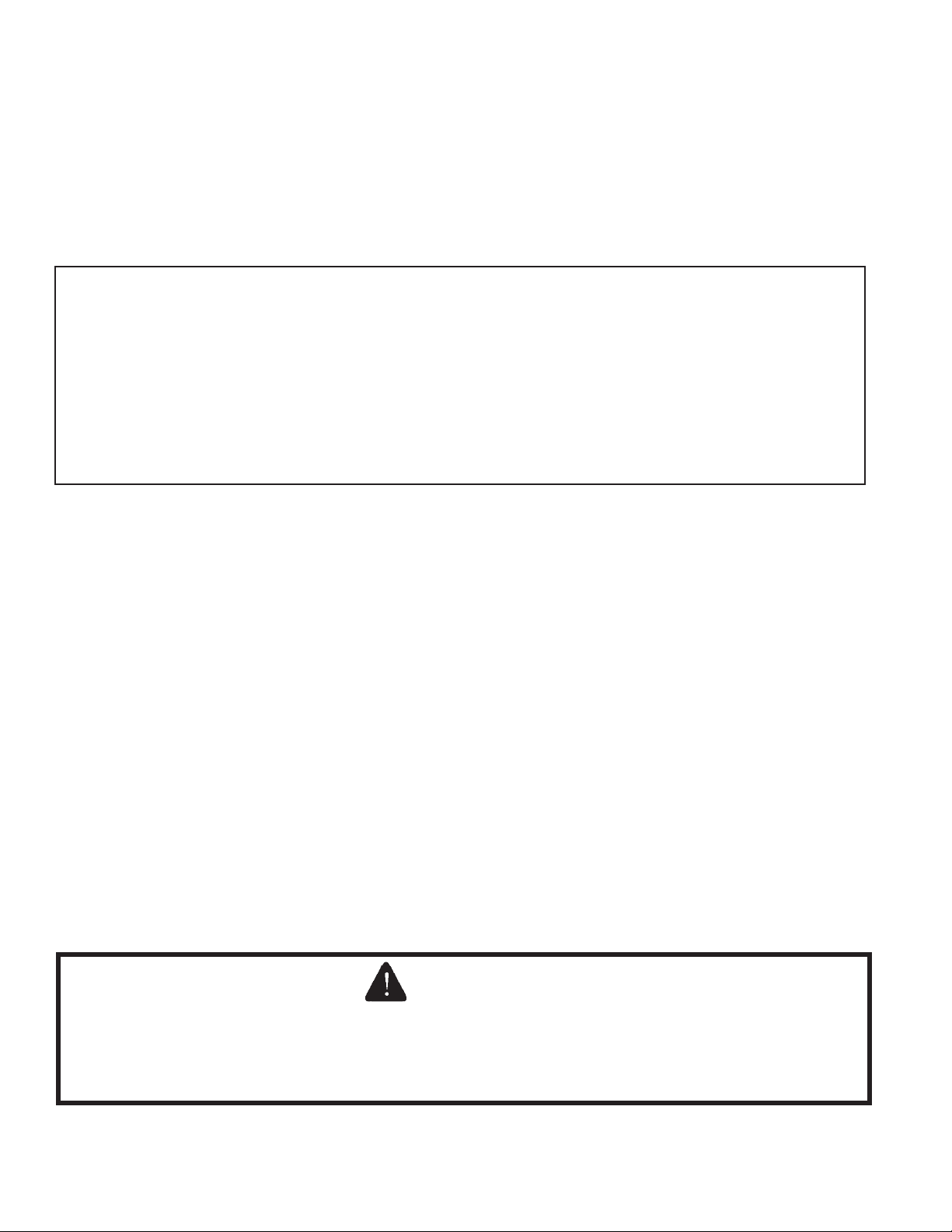
f) Thoroughly brush boiler ueways from the top and diagonally between casting pin rows. Be careful when brushing the
rear passage not to damage the rear target wall insulation.
g) Vacuum soot and debris from combustion chamber.
h) Check condition of rear target wall insulation, combustion chamber liner, and burner door insulation; replace if required.
i) Check burner head for signs of deterioration. Clean the head of any deposits.
j) Close burner door, reinstall 5/16” bolts, reconnect fuel oil and electrical lines.
k) Installation of boiler canopy, jacket top panel barometric draft regulator and breeching piping is done in reverse order
of removal. Make sure canopy is sealed tight to the casting; replace ceramic ber sealing strips as needed. All vent piping
joints must be ue gas leak free and secured with sheet metal screws.
IMPORTANT
• CLEAN THE BOILER EVEN IF THERE ARE NO SIGNIFICANT SOOT DEPOSITS. FAILURE TO
REMOVE ALL SULFUR AND ASH DEPOSITS ANNUALLY CAN CAUSE SEVERE CORROSION
DAMAGE.
• WHEN CLEANING THE REAR FLUE PASSAGE, BE CAREFUL NOT TO PUSH THE BRUSH TOO FAR
BEYOND THE BOTTOM OF THE PINS. DOING SO MAY DAMAGE THE TARGET WALL.
3) Inspect the vent system:
a) Make sure that the vent system is free of obstructions and soot.
b) Make sure that all vent system supports are intact.
c) Inspect joints for signs of condensate or ue gas leakage.
d) Inspect venting components for corrosion or other deterioration. Replace any defective vent system components.
4) Service the oil burner:
a) Replace oil nozzle with identical make and model (see Table 3).
b) Inspect the electrodes. Replace if they are deteriorated. Make sure that the electrode position is set according to the
burner manufacturer’s instructions.
c) Remove and clean fuel pump strainer.
d) Remove any accumulations of dust, hair, etc. from the air shutter, blower wheel, and other air handling parts of the
burner.
5) Replace the fuel oil line lter element and gaskets.
6) Inspect all oil piping and ttings for kinks and leaks. Repair any found.
7) Inspect the hydronic piping, tankless coil gasket, and boiler plugs for water leaks. Repair any leaks found immediately.
8) Verify operation of relief valve by manually lifting lever; replace relief valve immediately if valve fails to relieve pressure.
9) Open fuel line shut-off valve(s) and restore electrical power to the boiler.
10) Fire the boiler and check it out using the procedure outlined in “Start-up and Checkout” . This must include checking the
burner adjustments using instruments. Check for proper operation of all controls.
WARNING
WATER LEAKS CAN CAUSE SEVERE CORROSION DAMAGE TO THE BOILER OR
OTHER SYSTEM COMPONENTS. REPAIR ANY LEAKS FOUND IMMEDIATELY.
26