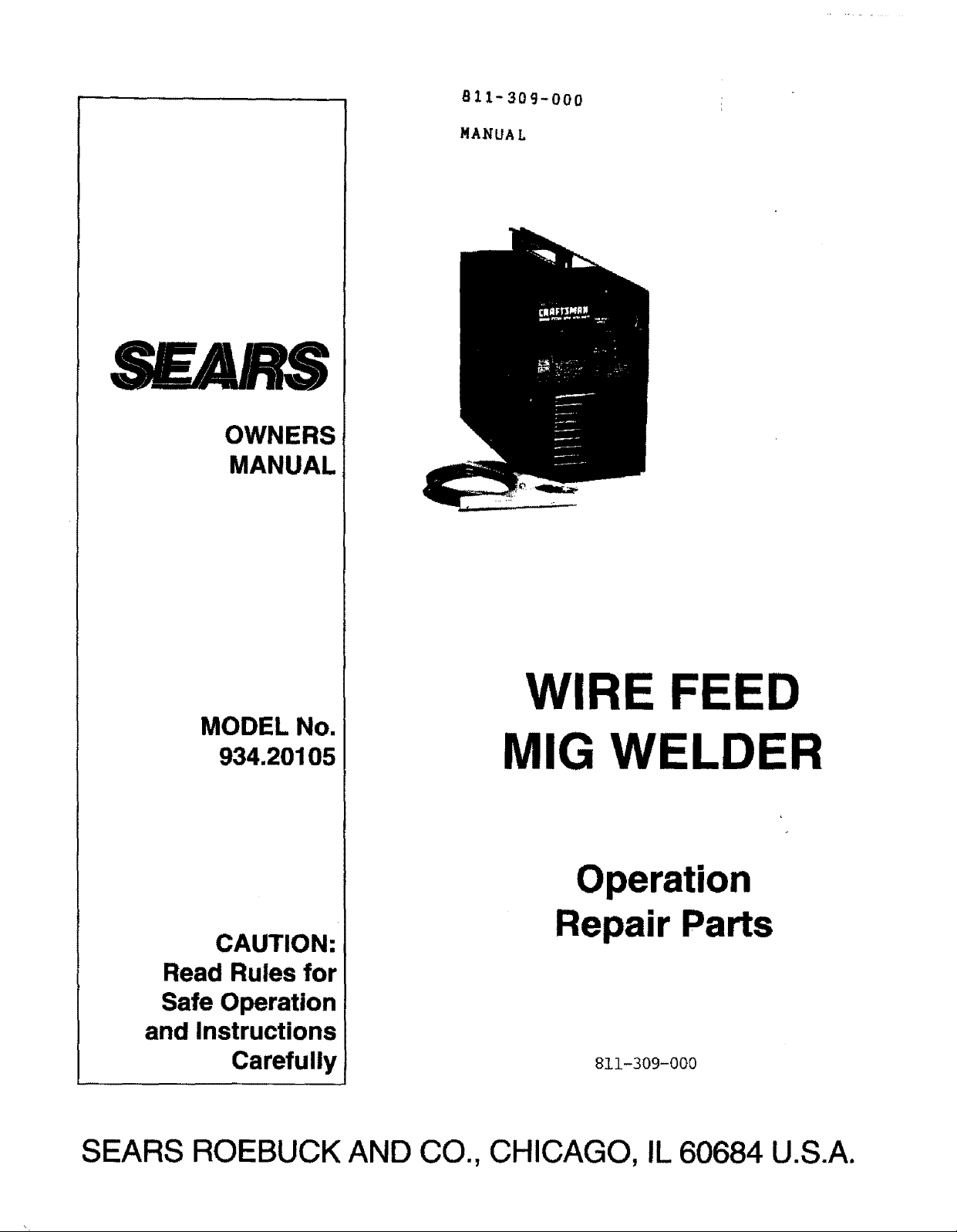
. EAR$
OWNERS
MANUAL
811-309-000
MANUAL
MODEL No.
934.20105
CAUTION:
Read Rules for
Safe Operation
and Instructions
Carefully
WIRE FEED
MIG WELDER
Operation
Repair Parts
811-309-000
SEARS ROEBUCK AND CO., CHICAGO, IL 60684 U.S.A.
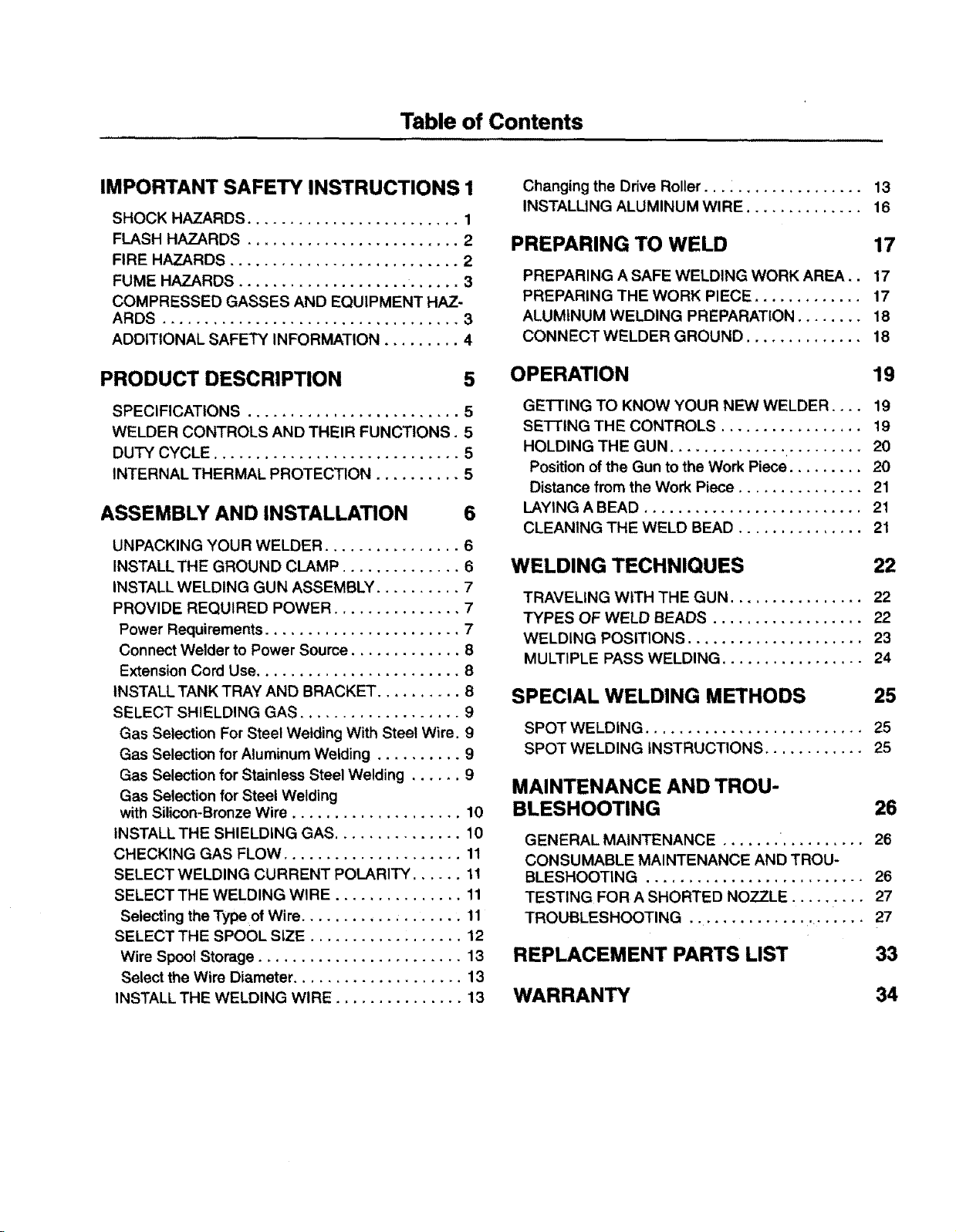
Table of Contents
IMPORTANT SAFETY INSTRUCTIONS 1
SHOCK HAZARDS ......................... 1
FLASH HAZARDS ......................... 2
FIRE HAZARDS ........................... 2
FUME HAZARDS .................... ...... 3
COMPRESSED GASSES AND EQUIPMENT HAZ-
ARDS ................................... 3
ADDITIONAL SAFETY INFORMATION ......... 4
PRODUCT DESCRIPTION 5
SPECIFICATIONS ......................... 5
WELDER CONTROLS AND THEIR FUNCTIONS. 5
DUTY CYCLE ............................. 5
INTERNAL THERMAL PROTECTION .......... 5
ASSEMBLY AND INSTALLATION 6
UNPACKING YOUR WELDER ................ 6
INSTALL THE GROUND CLAMP .............. 6
INSTALL WELDING GUN ASSEMBLY .......... 7
PROVIDE REQUIRED POWER ............... 7
Power Requirements ....................... 7
Connect Welder to Power Source ............. 8
Extension Cord Use ........................ 8
INSTALL TANK TRAY AND BRACKET .......... 8
SELECT SHIELDING GAS ................... 9
Gas Selection For Steel Welding With Steel Wire. 9
Gas Selection for Aluminum Welding .......... 9
Gas Selection for Stainless Steel Welding ...... 9
Gas Selection for Steel Welding
with Silicon-Bronze Wire .................... 10
INSTALL THE SHIELDING GAS ............... 10
CHECKING GAS FLOW ..................... 11
SELECT WELDING CURRENT POLARITY ...... 11
SELECT THE WELDING WIRE ............... 11
Selecting the Type of Wire ................... 11
SELECT THE SPOOL SIZE .................. 12
Wire Spool Storage ........................ 13
Select the Wire Diameter .................... 13
INSTALL THE WELDING WIRE ............... 13
Changing the Drive Roller ................... 13
INSTALLING ALUMINUM WIRE .............. 16
PREPARING TO WELD 17
PREPARING A SAFE WELDING WORK AREA.. 17
PREPARING THE WORK PIECE ............. 17
ALUMINUM WELDING PREPARATION ........ 18
CONNECT WELDER GROUND .............. 18
OPERATION 19
GETTING TO KNOW YOUR NEW WELDER .... 19
SETTING THE CONTROLS ................. 19
HOLDING THE GUN ....................... 20
Position of the Gun to the Work Piece ......... 20
Distance from the Work Piece ............... 21
LAYING A BEAD .......................... 21
CLEANING THE WELD BEAD ............... 21
WELDING TECHNIQUES 22
TRAVELING WITH THE GUN ................ 22
TYPES OF WELD BEADS .................. 22
WELDING POSITIONS ..................... 23
MULTIPLE PASS WELDING ................. 24
SPECIAL WELDING METHODS 25
SPOT WELDING .......................... 25
SPOT WELDING INSTRUCTIONS ............ 25
MAINTENANCE AND TROU-
BLESHOOTING 26
GENERAL MAINTENANCE ....... .......... 26
CONSUMABLE MAINTENANCE AND TROU-
BLESHOOTING .......................... 26
TESTING FOR A SHORTED NO72'LE ......... 27
TROUBLESHOOTING ...................... 27
REPLACEMENT PARTS LIST 33
WARRANTY 34
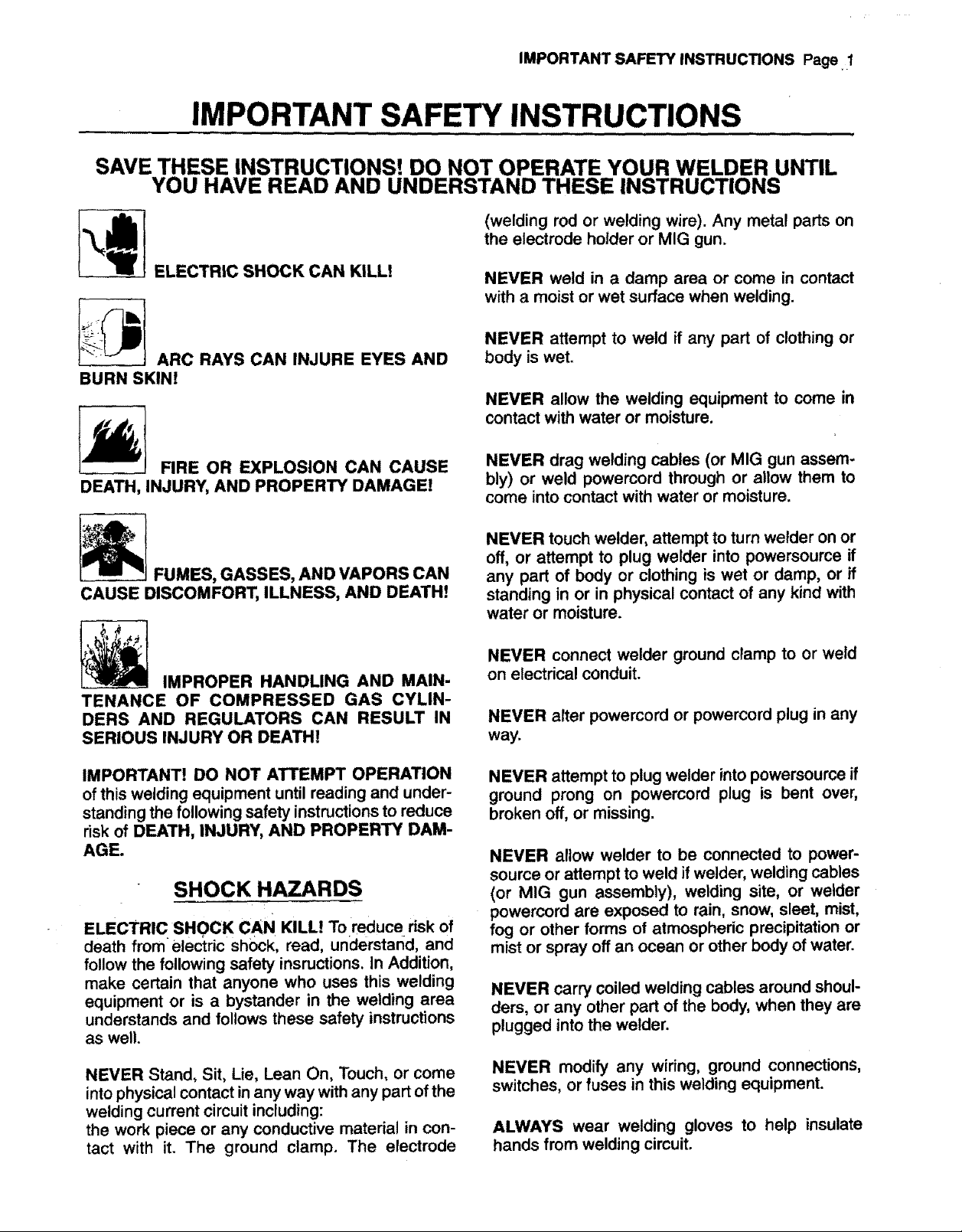
IMPORTANT SAFETY INSTRUCTIONS Page 1
IMPORTANT SAFETY INSTRUCTIONS
SAVE THESE INSTRUCTIONS! DO NOT OPERATE YOUR WELDER UNTIL
YOU HAVE READ AND UNDERSTAND THESE INSTRUCTIONS
(welding rod or welding wire). Any metal parts on
the electrode holder or MIG gun.
ELECTRIC SHOCK CAN KILL!
I_:_l ARC RAYS CAN INJURE EYES AND
BURN SKIN!
FIRE OR EXPLOSION CAN CAUSE
DEATH, INJURY, AND PROPERTY DAMAGE!
FUMES, GASSES, AND VAPORS CAN
CAUSE DISCOMFORT, ILLNESS, AND DEATH!
IMPROPER HANDLING AND MAIN-
TENANCE OF COMPRESSED GAS CYLIN-
DERS AND REGULATORS CAN RESULT IN
SERIOUS INJURY OR DEATH!
NEVER weld in a damp area or come in contact
with a moist or wet surface when welding.
NEVER attempt to weld if any part of clothing or
body is wet.
NEVER allow the welding equipment to come in
contact with water or moisture.
NEVER drag welding cables (or MIG gun assem-
bly) or weld powercord through or allow them to
come into contact with water or moisture.
NEVER touch welder, attempt to turn welder on or
off, or attempt to plug welder into powersource if
any part of body or clothing is wet or damp, or if
standing in or in physical contact of any kind with
water or moisture.
NEVER connect welder ground clamp to or weld
on electrical conduit.
NEVER alter powercord or powercord plug in any
way.
IMPORTANT! DO NOT ATTEMPT OPERATION
of this welding equipment until reading and under-
standing the following safety instructions to reduce
risk of DEATH, INJURY, AND PROPERTY DAM-
AGE.
SHOCK HAZARDS
ELECTRIC SHOCK CAN KILL! To reduce risk of
death from electric shock, read, understand, and
follow the following safety insructions. In Addition,
make certain that anyone who uses this welding
equipment or is a bystander in the welding area
understands and follows these safety instructions
as well.
NEVER Stand, Sit, Lie, Lean On, Touch, or come
into physical contact in any way with any part of the
welding current circuit including:
the work piece or any conductive material in con-
tact with it. The ground clamp. The electrode
NEVER attempt to plug welder into powersource if
ground prong on powercord plug is bent over,
broken off, or missing.
NEVER allow welder to be connected to power-
source or attempt to weld if welder, welding cables
(or MIG gun assembly), welding site, or welder
powercord are exposed to rain, snow, sleet, mist,
fog or other forms of atmospheric precipitation or
mist or spray off an ocean or other body of water.
NEVER carry coiled welding cables around shoul-
ders, or any other part of the body, when they are
plugged into the welder.
NEVER modify any wiring, ground connections,
switches, or fuses in this welding equipment.
ALWAYS wear welding gloves to help insulate
hands from welding circuit.
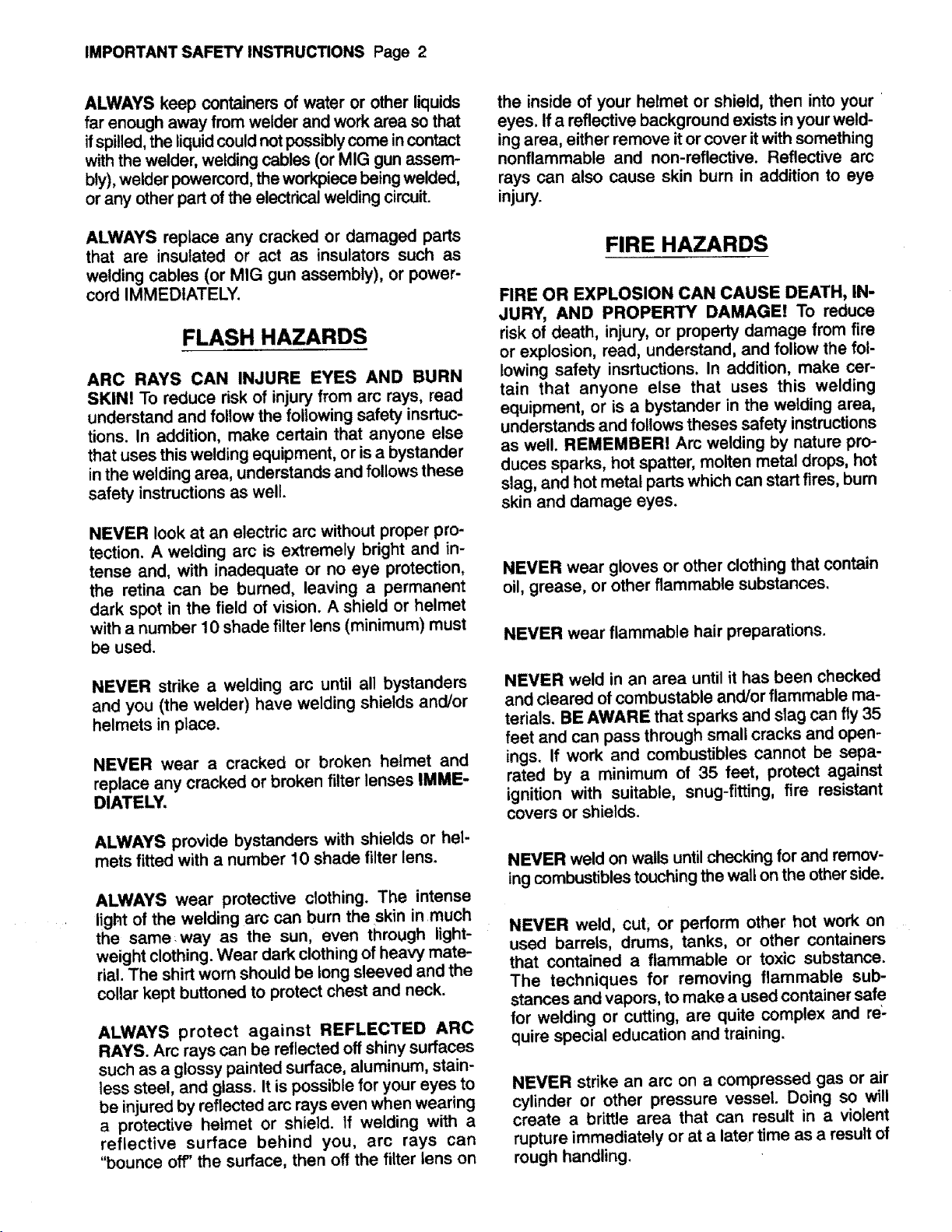
IMPORTANTSAFETYINSTRUCTIONSPage2
ALWAYSkeep containers of water or other liquids
far enough away from welder and work area so that
ifspilled, the liquid could not possibly come incontact
with the welder, welding cables (or MIG gun assem-
bly), welder powercord, the workpiece being welded,
or any other part of the electrical welding circuit.
ALWAYS replace any cracked or damaged parts
that are insulated or act as insulators such as
welding cables (or MIG gun assembly), or power-
cord IMMEDIATELY.
FLASH HAZARDS
ARC RAYS CAN INJURE EYES AND BURN
SKIN! To reduce risk of injury from arc rays, read
understand and follow the following safety insrtuc-
tions. In addition, make certain that anyone else
that uses this welding equipment, or is a bystander
in the welding area, understands and follows these
safety instructions as well
NEVER look at an electric arc without proper pro-
tection. A welding arc is extremely bright and in-
tense and, with inadequate or no eye protection,
the retina can be burned, leaving a permanent
dark spot in the field of vision. A shield or helmet
with a number 10 shade filter lens (minimum) must
be used.
the inside of your helmet or shield, then into your
eyes. If a reflective background exists in your weld-
ing area, either remove itor cover it with something
nonflammable and non-reflective. Reflective arc
rays can also cause skin burn in addition to eye
injury.
FIRE HAZARDS
FIRE OR EXPLOSION CAN CAUSE DEATH, IN-
JURY, AND PROPERTY DAMAGE! To reduce
risk of death, injury, or property damage from fire
or explosion, read, understand, and follow the fol-
lowing safety insrtuctions. In addition, make cer-
tain that anyone else that uses this welding
equipment, or is a bystander in the welding area,
understands and follows theses safety instructions
as well. REMEMBERI Arc welding by nature pro-
duces sparks, hot spatter, molten metal drops, hot
slag, and hot metal parts which can start fires, burn
skin and damage eyes.
NEVER wear gloves or other clothingthat contain
oil,grease, or other flammable substances.
NEVER wear flammable hair preparations.
NEVER strike a welding arc until all bystanders
and you (the welder) have welding shields and/or
helmets inplace.
NEVER wear a cracked or broken helmet and
replace any cracked or broken filter lenses IMME-
DIATELY.
ALWAYS provide bystanders with shields or hel-
mets fitted with a number 10 shade filter lens.
ALWAYS wear protective clothing. The intense
light of the welding arc can bum the skin in much
the same way as the sun, even through light-
weight clothing. Wear dark clothing of heavy mate-
rial. The shirt worn should be long sleeved and the
collar kept buttoned to protect chest and neck.
ALWAYS protect against REFLECTED ARC
RAYS. Arc rays can be reflected off shiny surfaces
such as a glossy painted surface, aluminum, stain-
less steel, and glass. It is possible for your eyes to
be injured by reflected arc rays even when wearing
a protective helmet or shield. If welding with a
reflective surface behind you, arc rays can
"bounce off" the surface, then off the filter tens on
NEVER weld in an area until it has been checked
and cleared of combustable and/or flammable ma-
terials. BE AWARE that sparks and slag can fly 35
feet and can pass through small cracks and open-
ings. If work and combustibles cannot be sepa-
rated by a minimum of 35 feet, protect against
ignition with suitable, snug-fitting, fire resistant
covers or shields.
NEVER weld on walls until checking for and remov-
ing combustibles touching the wall on the other side.
NEVER weld, cut, or perform other hot work on
used barrels, drums, tanks, or other containers
that contained a flammable or toxic substance.
The techniques for removing flammable sub-
stances and vapors, to make a used container safe
for welding or cutting, are quite complex and re-
quire special education and training.
NEVER strike an arc on a compressed gas or air
cylinder or other pressure vessel. Doing so will
create a brittle area that can result in a violent
rupture immediately or at a later time as a result of
rough handling.
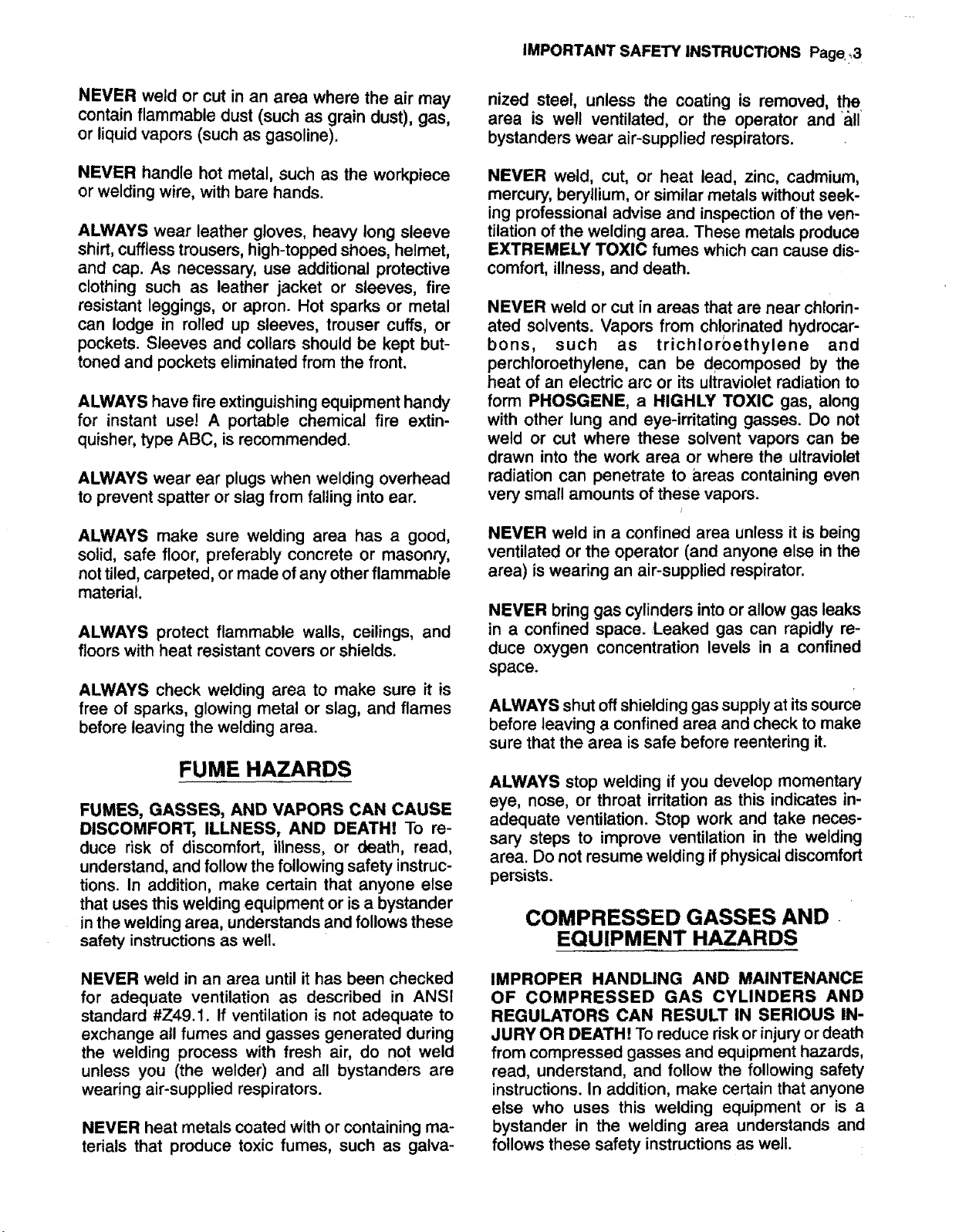
IMPORTANT SAFETY INSTRUCTIONS Page)3
NEVER weld or cut in an area where the air may
contain flammable dust (such as grain dust), gas,
or liquid vapors (such as gasoline).
NEVER handle hot metal, such as the workpiece
or welding wire, with bare hands.
ALWAYS wear leather gloves, heavy long sleeve
shirt, cuffless trousers, high-topped shoes, helmet,
and cap. As necessary, use additional protective
clothing such as leather jacket or sleeves, fire
resistant leggings, or apron. Hot sparks or metal
can lodge in rolled up sleeves, trouser cuffs, or
pockets. Sleeves and collars should be kept but-
toned and pockets eliminated from the front.
ALWAYS have fire extinguishing equipment handy
for instant use! A portable chemical fire extin-
quisher, type ABC, is recommended.
ALWAYS wear ear plugs when welding overhead
to prevent spatter or stag from falling into ear.
ALWAYS make sure welding area has a good,
solid, safe floor, preferably concrete or masonry,
not tiled, carpeted, or made of anyother flammable
material.
ALWAYS protect flammable walls, ceilings, and
floors with heat resistant covers or shields.
ALWAYS check welding area to make sure it is
free of sparks, glowing metal or slag, and flames
before leaving the welding area.
FUME HAZARDS
FUMES, GASSES, AND VAPORS CAN CAUSE
DISCOMFORT, ILLNESS, AND DEATH! To re-
duce risk of discomfort, illness, or death, read,
understand, and follow the following safety instruc-
tions. In addition, make certain that anyone else
that uses this welding equipment or is a bystander
in the welding area, understands and follows these
safety instructions as well.
nized steel, unless the coating is removed, the
area is well ventilated, or the operator and _all'
bystanders wear air-supplied respirators.
NEVER weld, cut, or heat lead, zinc, cadmium,
mercury, beryllium, or similar metals without seek-
ing professional advise and inspection of the ven-
tilation of the welding area. These metals produce
EXTREMELY TOXIC fumes which can cause dis-
comfort, illness, and death.
NEVER weld or cut in areas that are near chlorin-
ated solvents. Vapors from chlorinated hydrocar-
bons, such as trichlorbethylene and
perchloroethylene, can be decomposed by the
heat of an electric arc or its ultraviolet radiation to
form PHOSGENE, a HIGHLY TOXIC gas, along
with other lung and eye-irritating gasses. Do not
weld or cut where these solvent vapors can be
drawn into the work area or where the ultraviolet
radiation can penetrate to areas containing even
very small amounts of these vapors.
NEVER weld in a confined area unless it is being
ventilated or the operator (and anyone else in the
area) is wearing an air-supplied respirator.
NEVER bring gas cylindersinto or allow gas leaks
in a confined space. Leaked gas can rapidly re-
duce oxygen concentration levels in a confined
space.
ALWAYS shut off shielding gas supply at its source
before leaving a confined area and check to make
sure that the area is safe before reentering it.
ALWAYS stop welding if you develop momentary
eye, nose, or throat irritation as this indicates in-
adequate ventilation. Stop work and take neces-
sary steps to improve ventilation in the welding
area. Do not resume welding ifphysical discomfort
persists.
COMPRESSED GASSES AND
EQUIPMENT HAZARDS
NEVER weld in an area until it has been checked
for adequate ventilation as described in ANSI
standard #Z49.1. If ventilation is not adequate to
exchange all fumes and gasses generated during
the welding process with fresh air, do not weld
unless you (the welder) and all bystanders are
wearing air-supplied respirators.
NEVER heat metals coated with or containing ma-
terials that produce toxic fumes, such as galva-
IMPROPER HANDLING AND MAINTENANCE
OF COMPRESSED GAS CYLINDERS AND
REGULATORS CAN RESULT IN SERIOUS IN-
JURY OR DEATH! To reduce risk or injury or death
from compressed gasses and equipment hazards,
read, understand, and follow the following safety
instructions. In addition, make certain that anyone
else who uses this welding equipment or is a
bystander in the welding area understands and
follows these safety instructions as well.
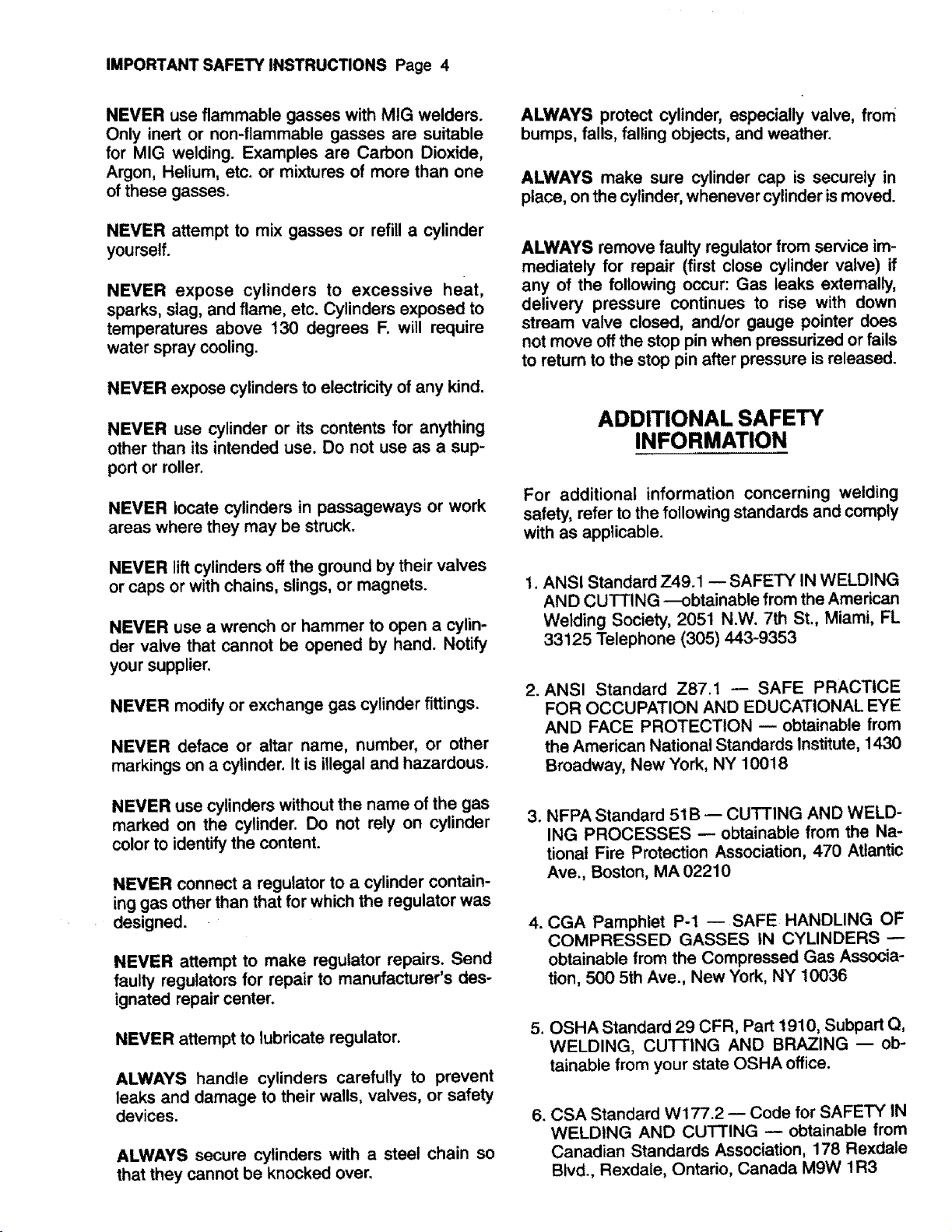
IMPORTANT SAFETY INSTRUCTIONS Page 4
NEVER use flammable gasses with MIG welders.
Only inert or non-flammable gasses are suitable
for MIG welding. Examples are Carbon Dioxide,
Argon, Helium, etc. or mixtures of more than one
of these gasses.
NEVER attempt to mix gasses or refill a cylinder
yourself.
NEVER expose cylinders to excessive heat,
sparks, slag, and flame, etc. Cylinders exposed to
temperatures above 130 degrees F. will require
water spray cooling.
NEVER expose cylinders to electricity of any kind.
NEVER use cylinder or its contents for anything
other than its intended use. Do not use as a sup-
port or roller.
NEVER locate cylinders in passageways or work
areas where they may be struck.
ALWAYS protect cylinder, especially valve, from
bumps, falls, falling objects, and weather.
ALWAYS make sure cylinder cap is securely in
place, on the cylinder, whenever cylinderis moved.
ALWAYS remove faulty regulator from service im-
mediately for repair (first close cylinder valve) if
any of the following occur: Gas leaks extemally,
delivery pressure continues to rise with down
stream valve closed, and/or gauge pointer does
not move off the stop pin when pressurized or fails
to return to the stop pin after pressure is released.
ADDITIONAL SAFETY
INFORMATION
For additional information concerning welding
safety, refer to the following standards and comply
with as applicable.
NEVER lift cylinders off the ground by their valves
or caps or with chains, slings, or magnets.
NEVER use a wrench or hammer to open a cylin-
der valve that cannot be opened by hand. Notify
your supplier.
NEVER modify or exchange gas cylinder fittings.
NEVER deface or altar name, number, or other
markings on a cylinder. It is illegal and hazardous.
NEVER use cylinders without the name of the gas
marked on the cylinder. Do not rely on cylinder
color to identify the content.
NEVER connect a regulator to a cylinder contain-
ing gas otherthan that for which the regulator was
designed.
NEVER attempt to make regulator repairs. Send
faulty regulators for repair to manufacturer's des-
ignated repair center.
1. ANSI Standard Z49.1 -- SAFETY IN WELDING
AND CUTTING ---obtainable from the American
Welding Society, 2051 N.W. 7th St., Miami, FL
33125 Telephone (305) 443-9353
2. ANSI Standard Z87.1 -- SAFE PRACTICE
FOR OCCUPATION AND EDUCATIONAL EYE
AND FACE PROTECTION -- obtainable from
the American National Standards Institute, 1430
Broadway, New York, NY 10018
3. NFPA Standard 51B -- CUTTING AND WELD-
ING PROCESSES -- obtainable from the Na-
tional Fire Protection Association, 470 Atlantic
Ave., Boston, MA 02210
4. CGA Pamphlet P-1 --SAFE HANDLING OF
COMPRESSED GASSES IN CYLINDERS
obtainable from the Compressed Gas Associa-
tion, 500 5th Ave., New York, NY 10036
NEVER attempt to lubricate regulator.
ALWAYS handle cylinders carefully to prevent
leaks and damage to their wails, valves, or safety
devices.
ALWAYS secure cylinders with a steel chain so
that they cannot be knocked over.
5. OSHA Standard 29 CFR, Part 1910, Subpart Q,
WELDING, CU'I-I'ING AND BRAZING -- ob-
tainable from your state OSHA office.
6. CSA Standard W177.2 -- Code for SAFETY IN
WELDING AND CUTTING -- obtainable from
Canadian Standards Association, 178 Rexdale
Blvd., Rexdate, Ontario, Canada M9W 1R3

PRODUCT DESCRIPTION Page. 5
PRODUCT DESCRIPTION
Your new Metal Inert Gas (MIG) wire feed welder
is designed for maintenance, and sheetmetal fab-
rication. The welder consists of a single-phase
power transformer, stabilizer, rectifier, and a
unique built-in control/feeder. This MIG welder is
capable of welding with .024" and .030" solid steel,
or stainless steel wires and .030" aluminum (spec
#5356 alloy) wire on DC positive polarity and with
.030", self-shielding flux-core wire on DC negative
polarity.
NOTE; When using .035 Flux Core wire your duty
cycle may be shorter than 20%.
Now you can weld 20 gauge sheet metal up to
3/16" with a single pass. Welds 114" steel with
beveling and multiple pass.
SPECIFICATIONS
Primary (input) volts .............................. 120 VAC
Primary (input) Amps ....................................... 18
Phase ....................................................... Single
Frequency ................................................ 60 Hz
Kilovolt Amps ................................................ 2.2
Secendary (output) volts ............................... 18
Secondary (output) amps ............................. 75
Duty Cycle Rating: ..................................... 20%
Open Circuit Volts (Max.) ...................... 31 VDC
WIRE SPEED - This control adjusts the speed at
which the wire is fed out of the gun. The wire speed
needs to be closely matched ("tuned-in") to the
rate at which it is being melted off. Some things
that affect wire speed selection are the type and
diameter of the wire being used, the heat setting
selected, and the welding position to be used.
DUTY CYCLE
The duty cycle rating of a welder tells the operator
how long he or she can weld and how long the
welder must rest-to cool. tt is expressed as a
percentage of 10 minutes (the industry recognized
cycle time) and represents the maximum welding
time allowed, with the balance of the 10-minute
cycle required for cooling (see chart below).
Your new welder has a duty cycle rating of 20%.
You can weld for 2 minutes out of 10, with the
remaining 8 minutes required for cooling.
Duty Cycle
Rating
Maximum Required
Welding Time Resting Time
WELDER CONTROLS AND THEIR
FUNCTIONS
POWER SWITCH- Has three settings: LOW, OFF,
and HIGH. Setting the switch to OFF shuts the
welder off. When set to LOW, the welder can
produce up to 45 amps of welding current. When
set on HIGH, up to 75 amps of welding current will
be available. NOTE: The actual amperage will
vary depending on wire speed, length of the arc
held when welding, the type of wire being used,
and the ACTUAL voltage available at the wall
receptacle.
ELECTRIC SHOCK CAN KILL! To reduce risk of
electric shock, be aware that having the POWER
SWITCH in the OFF position does not remove
power from all intemal circuitry of the welder.
20% 2 Minutes 8 Minutes
40% 4 Minutes 6 Minutes
60% 6 Minutes 4 Minutes
80% 8 Minutes 2 Minutes
100% 10 Minutes 0 Minutes
INTERNAL THERMAL PROTECTION
If you exceed the duty cycle of your welder, and
internal thermal protector will open and shut off ai!
welder functions. After cooling, the thermal protec-
tor will automatically reset and the welder wilt func-
tion normally again.
DO NOT CONSTANTLY EXCEED THE DUTY
CYCLE OR DAMAGE TO THIS WELDER CAN
RESULT!
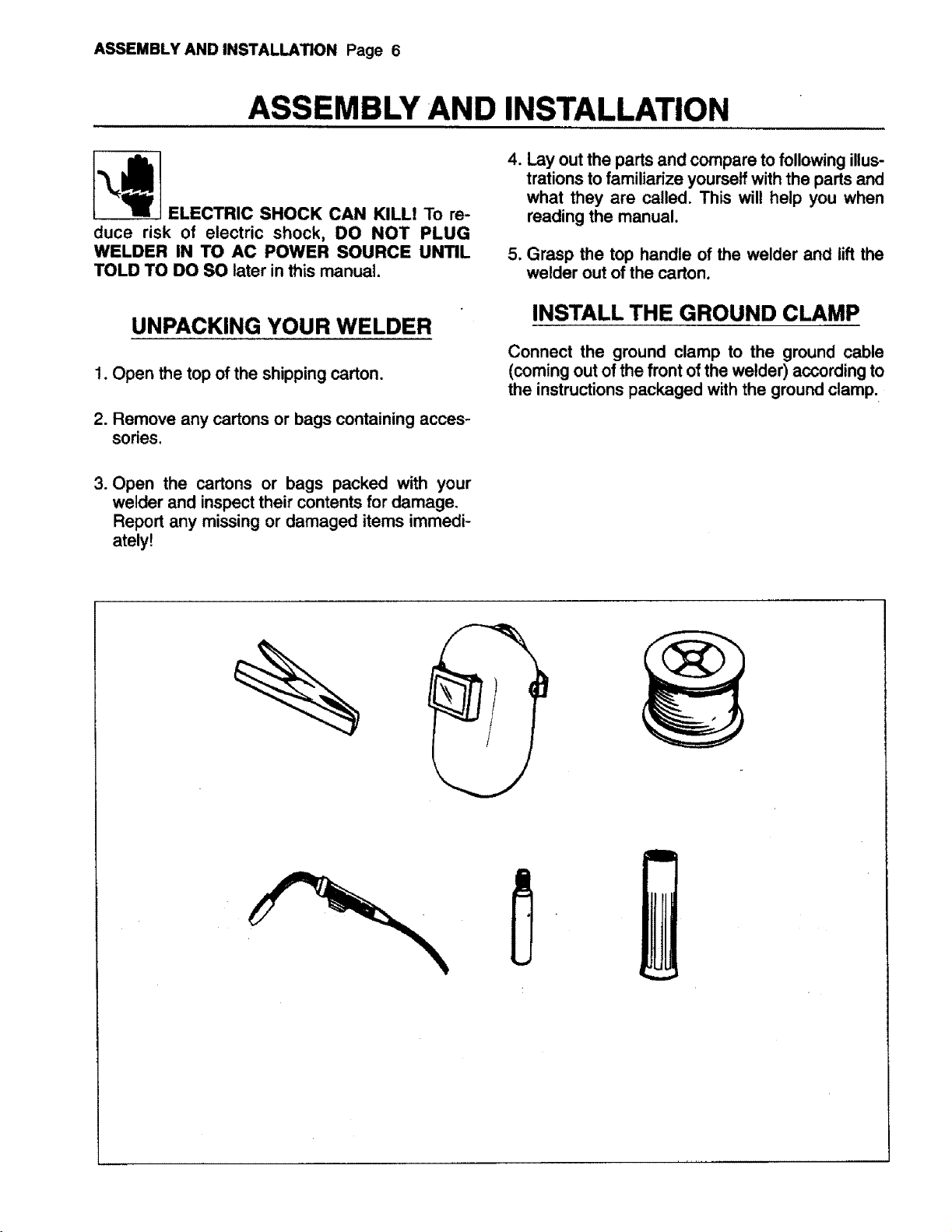
ASSEMBLYANDINSTALLATIONPage6
ASSEMBLY AND INSTALLATION
ELECTRIC SHOCK CAN KILL! To re-
duce risk of electric shock, DO NOT PLUG
WELDER IN TO AC POWER SOURCE UNTIL
TOLD TO DO SO later in this manual.
4. Lay out the parts and compare tofollowing illus-
trations to familiarize yourself with the parts and
what they are called. This will help you when
reading the manual.
5. Grasp the top handle of the welder and lift the
welder out of the carton.
UNPACKING YOUR WELDER
1. Open the top of the shipping carton.
2. Remove any cartons or bags containing acces-
sories.
3. Open the cartons or bags packed with your
welder and inspecttheir contents for damage.
Report any missing or damaged items immedi-
ately!
INSTALL THE GROUND CLAMP
Connect the ground clamp to the ground cable
(coming out of the front of the welder) according to
the instructions packaged with the ground clamp.
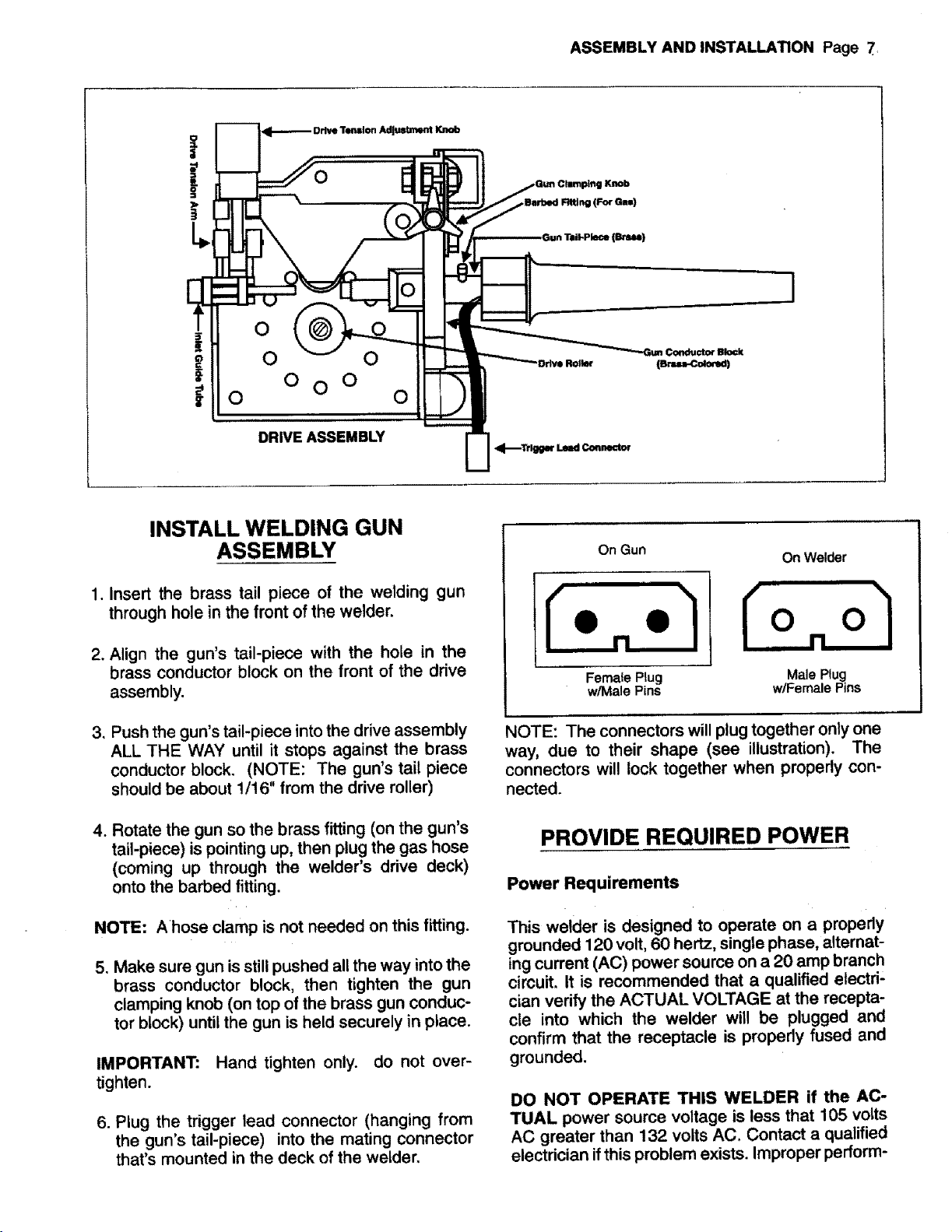
O
O O
000
0 0
DRIVE ASSEMBLY
ASSEMBLY AND INSTALLATION Page 7
Knob
INSTALL WELDING GUN
ASSEMBLY
1. Insert the brass tail piece of the welding gun
through hole in the frontof the welder.
2. Align the gun's tail-piece with the hole in the
brass conductor block on the front of the drive
assembly.
3, Push the gun's tail-piece into the drive assembly
ALL THE WAY until it stops against the brass
conductor block. (NOTE: The gun's tail piece
should be about 1/16" from the drive roller)
4. Rotate the gun so the brass fitting (on the gun's
tail-piece) is pointing up, then plug the gas hose
(coming up through the welder's drive deck)
onto the barbed fitting.
NOTE: Ahose clamp is not needed on this fitting.
5. Make sure gun is still pushed all the way into the
brass conductor block, then tighten the gun
clamping knob (on top of the brass gun conduc-
tor block) until the gun is held securely in place.
IMPORTANT: Hand tighten only. do not over-
tighten.
6. Plug the trigger lead connector (hanging from
the gun's tail-piece) into the mating connector
that's mounted in the deck of the welder.
On Gun
Female Plug
w/Male Pins
NOTE: The connectors will plug together only one
way, due to their shape (see illustration). The
connectors will lock together when properly con-
nected.
On Welder
PROVIDE REQUIRED POWER
Power Requirements
This welder is designed to operate on a properly
grounded 120 volt, 60 hertz, single phase, alternat-
ing current (AC) power source on a 20 amp branch
circuit. It is recommended that a qualified electri-
cian verify the ACTUAL VOLTAGE at the recepta-
cle into which the welder will be plugged and
confirm that the receptacle is properly fused and
grounded.
DO NOT OPERATE THIS WELDER if the AC-
TUAL power source voltage is less that 105 volts
AC greater than 132 volts AC. Contact a qualified
electrician ifthis problem exists. Improper perform-
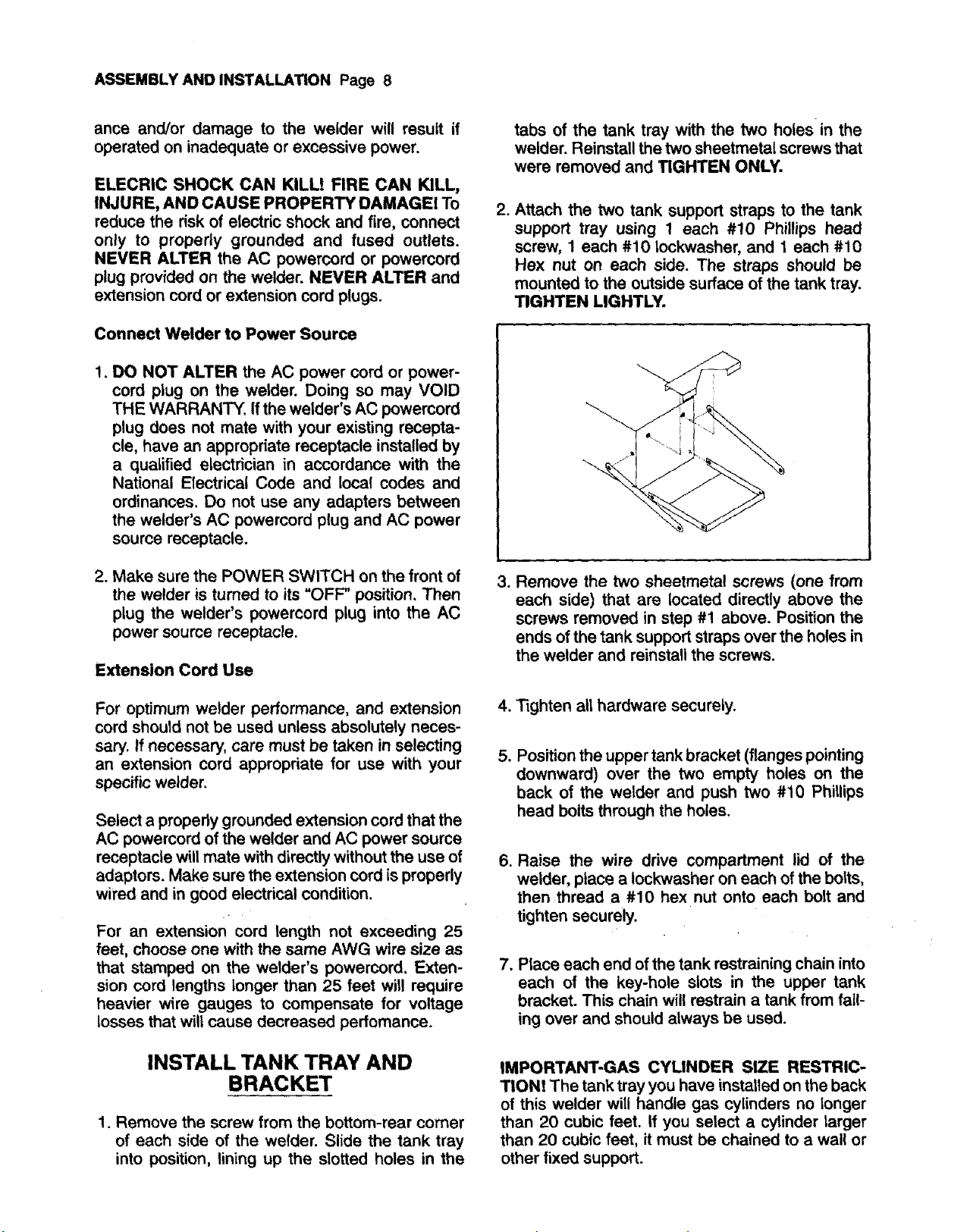
ASSEMBLY AND INSTALLATION Page 8
ance and/or damage to the welder will result if
operated on inadequate orexcessive power.
ELECRIC SHOCK CAN KILL! FIRE CAN KILL,
INJURE, AND CAUSE PROPERTY DAMAGE! To
reduce the risk of electric shock and fire, connect
only to properly grounded and fused outlets.
NEVER ALTER the AC powercord or powercord
plug provided on the welder. NEVER ALTER and
extension cord or extension cord plugs.
Connect Welder to Power Source
1, DO NOT ALTER the AC power cord or power-
cord plug on the welder. Doing so may VOID
THE WARRANTY. If the welder's AC powercord
plug does not mate with your existing recepta-
cle, have an appropriate receptacle installed by
a qualified electrician in accordance with the
National Electrical Code and local codes and
ordinances. Do not use any adapters between
the welder's AC powercord plug and AC power
source receptacle.
tabs of the tank tray with the two holes in the
welder. Reinstall the two sheetmetal screws that
were removed and TIGHTEN ONLY.
.
Attach the two tank support straps to the tank
support tray using 1 each #10 Phillips head
screw, 1 each #10 Iockwasher, and 1 each #10
Hex nut on each side. The straps should be
mounted to the outside surface of the tank tray.
TIGHTEN LIGHTLY.
2. Make sure the POWER SWITCH on the front of
the welder is turned to its "OFF" position. Then
plug the welder's powercord plug into the AC
power source receptacle.
Extension Cord Use
For optimum welder performance, and extension
cord should not be used unless absolutely neces-
san/. If necessary, care must be taken in selecting
an extension cord appropriate for use with your
specific welder.
Select a property grounded extension cord that the
AC powercord of the welder and AC power source
receptacle will mate with directly without the use of
adaptors. Make sure the extension cord is properly
wired and in good electrical condition.
For an extension cord length not exceeding 25
feet, choose one with the same AWG wire size as
that stamped on the welder's powercord, Exten-
sion cord lengths longer than 25 feet will require
heavier wire gauges to compensate for voltage
losses that will cause decreased perfomance.
3,
Remove the two sheetmetal screws (one from
each side) that are located directly above the
screws removed in step #1 above. Position the
ends of the tank support straps over the holes in
the welder and reinstall the screws.
4. Tighten all hardware securely.
.
Position the upper tank bracket (flanges pointing
downward) over the two empty holes on the
back of the welder and push two #10 Phillips
head bolts through the holes.
6. Raise the wire drive compartment lid of the
welder, place a Iockwasher on each of the bolts,
then thread a #10 hex nut onto each bolt and
tighten securely.
7,
Place each end of the tank restraining chain into
each of the key-hole slots in the upper tank
bracket. This chain will restrain a tank from fall-
ing over and should always be used.
INSTALL TANK TRAY AND
BRACKET
1. Remove the screw from the bottom-rear comer
of each side of the welder. Slide the tank tray
into position, lining up the slotted holes in the
IMPORTANT-GAS CYUNDER SIZE RESTRIC-
TION! The tank tray you have installed on the back
of this welder will handle gas cylinders no longer
than 20 cubic feet. If you select a cylinder larger
than 20 cubic feet, it must be chained to a wall or
other fixed support.

SELECT SHIELDING GAS
ASSEMBLYANDINSTALLATIONPage9
The shielding gas plays an extremely important
role in the MIG welding process. As with most
welding processes, itis critical that the molten weld
puddle be "shielded" from the atmosphere. Inade-
quate shielding will result in porous, brittle welds.
Notonly isshieldingthe weld important, butselect-
ing the proper gas to shield with isof equal impor-
tance. Generally, the shielding gas selected is
dependent upon the type and thickness of metal
being welded. Selecting the wrong gas for the
metal to be welded can result in porosity, brittle-
ness, and/or undesirable penetration of the weld.
Although there are many gasses and mixtures
available for MIG welding, the following recom-
mendations are based on the electrical output
characteristicsand metal-thickness welding capa-
bilitiesof this specific MIG welder.
GAS SELECTION FOR STEEL WELDING WITH
STEEL WIRE
Gas Selection For Aluminum Gas Welding
100% ARGON
Our only recommendation for shielding an alumP
num weld is pure Argon. Do not attempt to use the
Argon/Carbon Dioxide mixture (recommended for
steel) when welding aluminum.
Gas Selection For Stainless Steel Welding
75% ARGON
25% CO=
_J
For either mild or low carbon (High Strength Struc-
tural) steel, in the thicknesses that can be welded
with this welder, our primary recommendation is a
gas mixture of 75% Argon and 25% Carbon Diox-
ide. This gas mixture helps to prevent burn
through and distortion on very thin steel, yet pro-
vides food penetration on thicker steel. Its ability
to minimize spatter results in clean, smooth weld
appearances. In addition, it provides food puddle
control when welding vertically or overhead. This
gas mixture is available pre-mixed in a single cyl-
inder from your local gas distributor.
_o/o BEST
HELIUM
F "_"_''%ARGON
_% c(:f
The best shielding gas for stainless steel welding
is a mixture of 90% helium, 7.5% Argon, and 2.5%
Carbon Dioxide. However, the 75% argon 25%
Carbon Dioxide mixture (recommended for steel)
can also be used, but an increase in the area being
heated by the arc will be experienced causing
slightly greater distortion of the base metal. Also
this mixture can cause a decrease in the ability of
the stainless steel weld to resist corrosion. Either
mixture can be obtained in a single cylinder from
your local gas distributor.
_o/, ° ACCEPTABLE
ARGON
r - -2_% co 2
Note: Potential Shielding Gas Problems