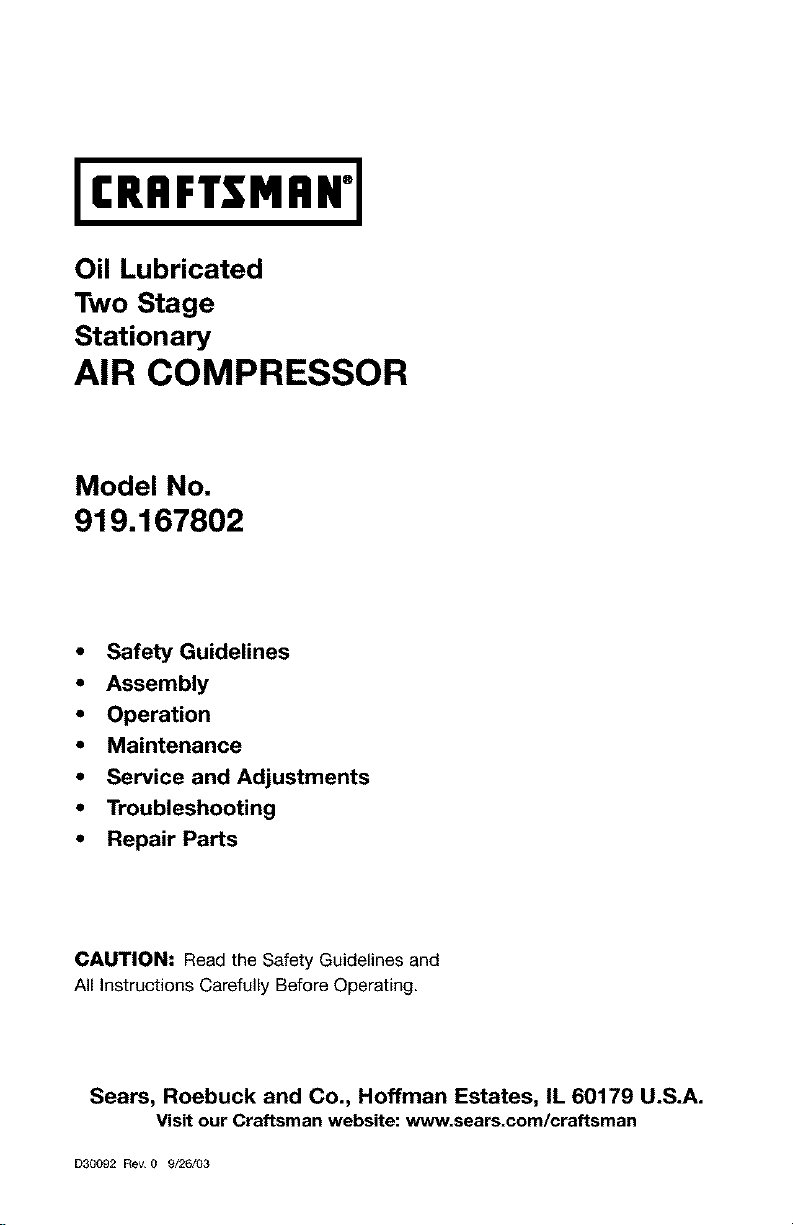
iCRRFTSMRNq
Oil Lubricated
Two Stage
Stationary
AIR COMPRESSOR
Model No.
919.167802
• Safety Guidelines
• Assembly
• Operation
• Maintenance
• Service and Adjustments
• Troubleshooting
• Repair Parts
CAUTION: Read the Safety Guidelines and
All Instructions Carefully Before Operating.
Sears, Roebuck and Co., Hoffman Estates, IL 60179 U.S.A.
Visit our Craftsman website: www.sears.com/craftsman
D30092 Rev0 9/26/03
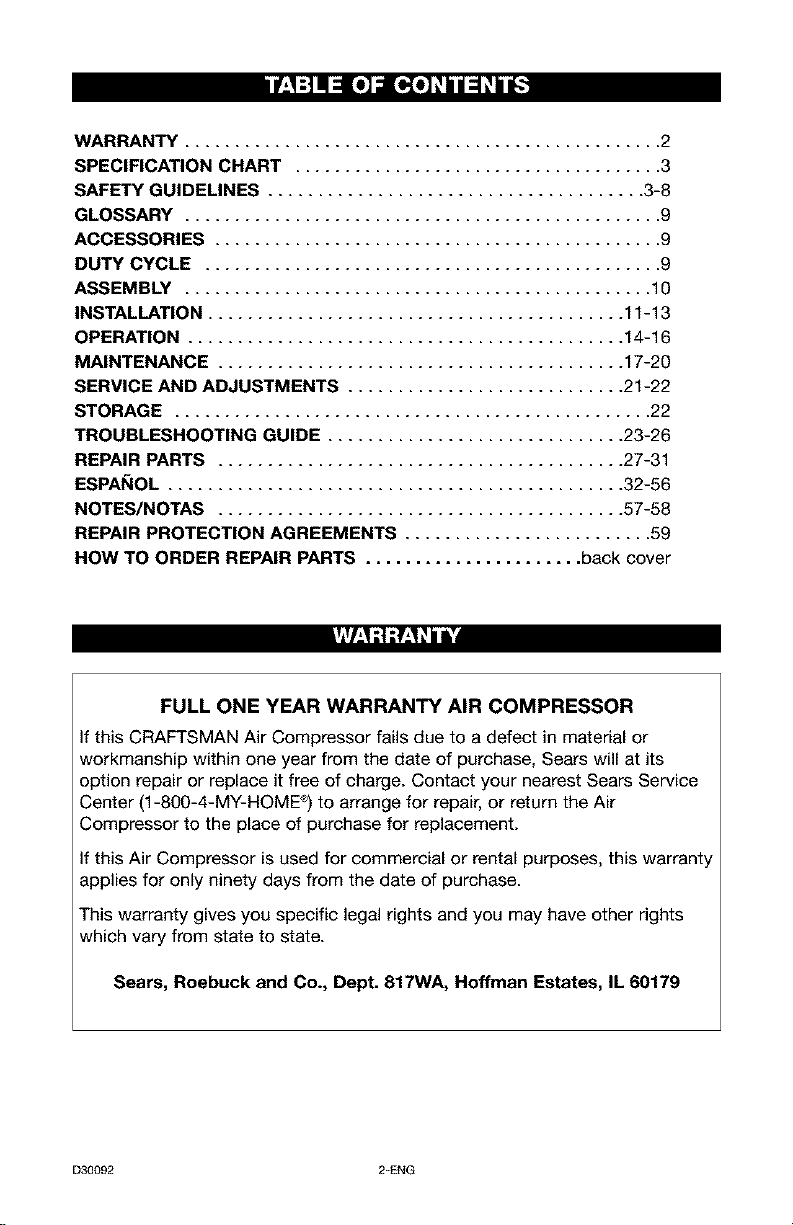
WARRANTY ................................................ 2
SPECIFICATION CHART ..................................... 3
SAFETY GUIDELINES ...................................... 3-8
GLOSSARY ................................................ 9
ACCESSORIES ............................................. 9
DUTY CYCLE .............................................. 9
ASSEMBLY ............................................... 10
INSTALLATION .......................................... 11-13
OPERATION ............................................ 14-16
MAINTENANCE ......................................... 17-20
SERVICE AND ADJUSTMENTS ............................ 21-22
STORAGE ................................................ 22
TROUBLESHOOTING GUIDE .............................. 23-26
REPAIR PARTS ......................................... 27-31
ESPAI_IOL .............................................. 32-56
NOTES/NOTAS ......................................... 57-58
REPAIR PROTECTION AGREEMENTS ......................... 59
HOW TO ORDER REPAIR PARTS ...................... back cover
ltl__1;| ;[_I_ hi"
FULL ONE YEAR WARRANTY AIR COMPRESSOR
If this CRAFTSMAN Air Compressor fails due to a defect in material or
workmanship within one year from the date of purchase, Sears will at its
option repair or replace it free of charge. Contact your nearest Sears Service
Center (1-800-4-MY-HOME ®)to arrange for repair, or return the Air
Compressor to the place of purchase for replacement.
If this Air Compressor is used for commercial or rental purposes, this warrant
applies for only ninety days from the date of purchase.
This warranty gives you specific legal rights and you may have other rights
which vary from state to state.
Sears, Roebuck and Co., Dept. 817WA, Hoffman Estates, IL 60179
D30092 2=ENG
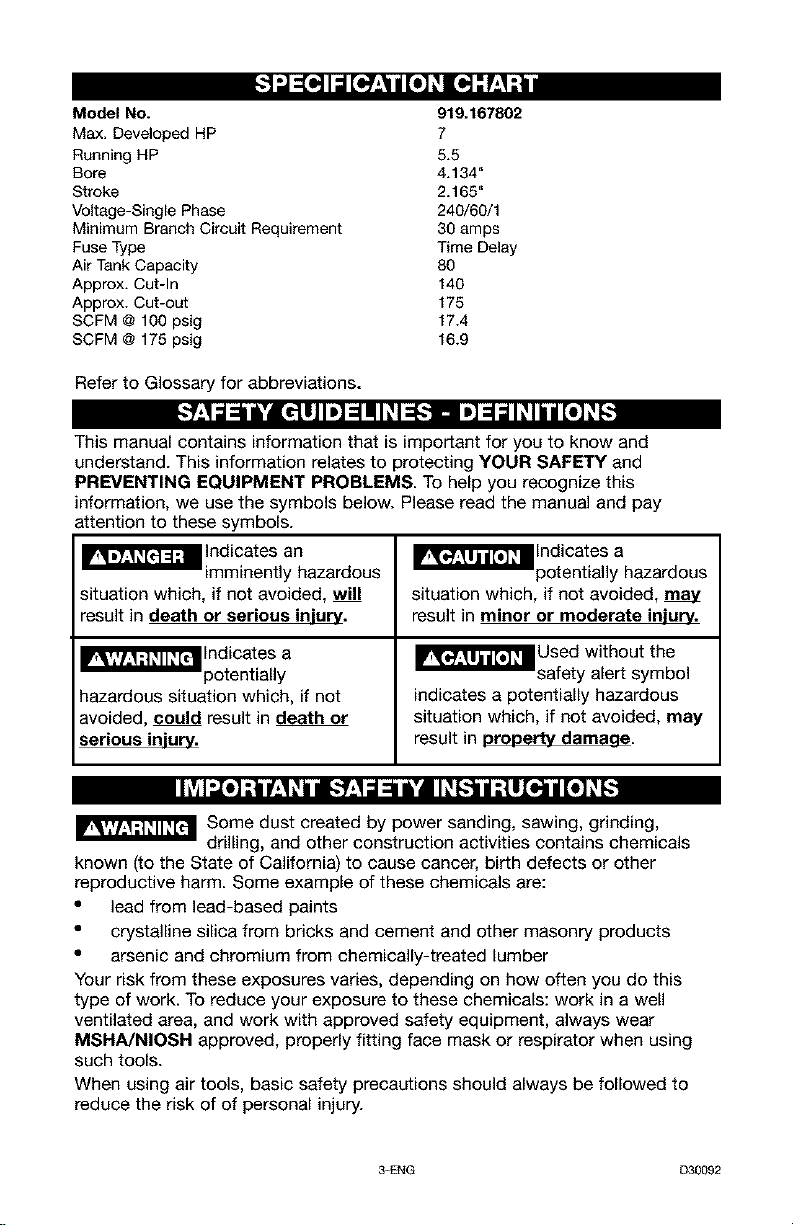
Model No. 919,167802
Max. Developed HP 7
Running HP 5.5
Sore 4.134"
Stroke 2.165"
Voltage-Single Phase 240/60/1
Minimum Branch Circuit Requirement 30 amps
Fuse Type Time Delay
Air Tank Capacity 80
Approx. Cut-In 140
Approx. Cut-out 175
SCFM @ 100 psig 17.4
SCFM @ 175 psig 16.9
Refer to Glossary for abbreviations.
This manual contains information that is important for you to know and
understand. This information relates to protecting YOUR SAFETY and
PREVENTING EQUIPMENT PROBLEMS. To help you recognize this
information, we use the symbols below. Please read the manual and pay
attention to these symbols.
I_'_J_ Indicates an
imminently hazardous
situation which, if not avoided, will
result in death or serious injury.
_'_1'_J_ Indicates a
potentially hazardous
situation which, if not avoided,
result in minor or moderate injury.
I_'_J_'_'_ Indicat es a
potentially
hazardous situation which, if not
avoided, could result in death or
serious injury.
_T_'_Used without the
safety alert symbol
indicates a potentially hazardous
situation which, if not avoided, may
result in property damaae.
Ih_l_o]-'tnq.+1+id_"Y.4_l_,_'d_[IP.[-:-]ljt,ttl_o,]njl[o_]P.[-.+
_Some dust created by power sanding, sawing, grinding,
known (to the State of California) to cause cancer, birth defects or other
reproductive harm. Some example of these chemicals are:
• lead from lead-based paints
• crystalline silica from bricks and cement and other masonry products
• arsenic and chromium from chemically-treated lumber
Your risk from these exposures varies, depending on how often you do this
type of work. To reduce your exposure to these chemicals: work in a well
ventilated area, and work with approved safety equipment, always wear
MSHA/NIOSR approved, properly fitting face mask or respirator when using
such tools.
When using air tools, basic safety precautions should always be followed to
reduce the risk of of personal injury.
drilling, and other construction activities contains chemicals
3-ENG [330092
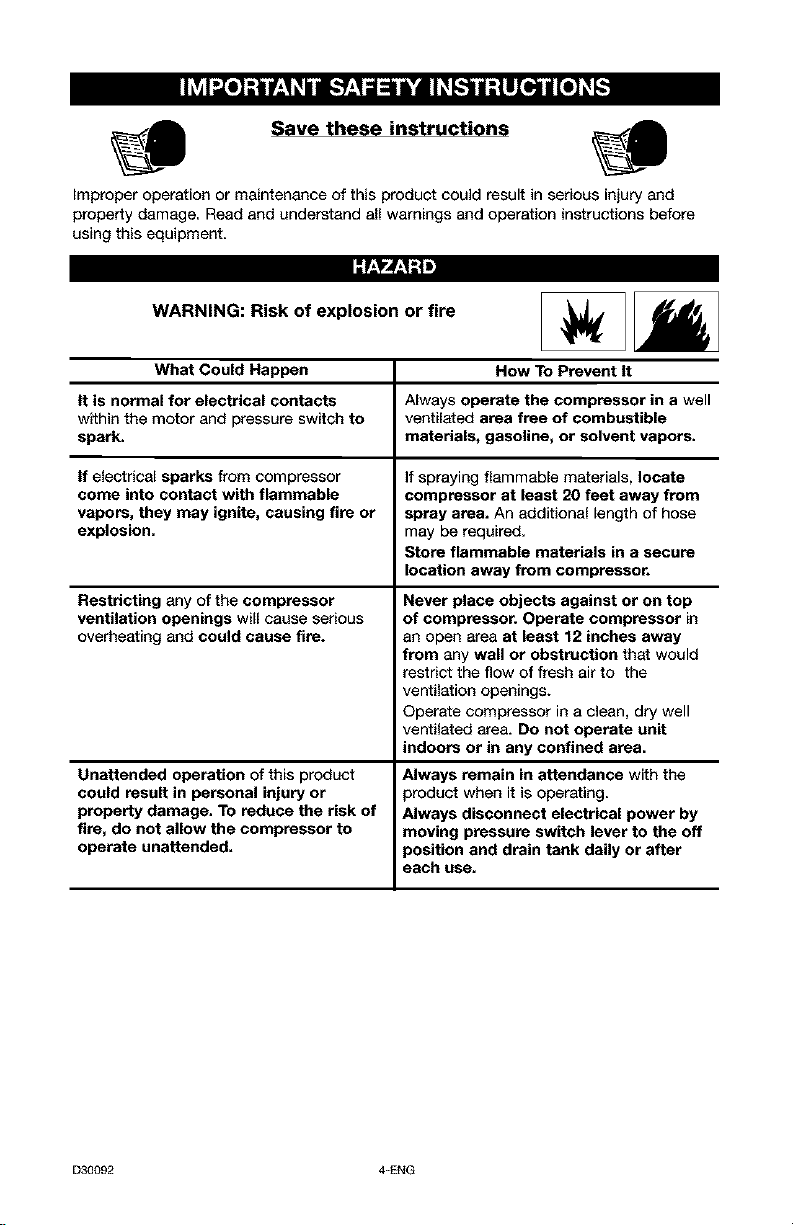
Save these instructions
improper operation or maintenance of this product could result in serious injury and
property damage. Read and understand all warnings and operation instructions before
using this equipment.
:r:_rJ:_;!m
WARNING: Risk of explosion or fire
What Could Happen How To Prevent It
tt is normal for electrical contacts Always operate the compressor in a well
within the motor and pressure switch to ventilated area free of combustible
spark, materials, gasoline, or solvent vapors.
tf electrical sparks from compressor if spraying flammable materials, locate
come into contact with flammable compressor at least 20 feet away from
vapors, they may ignite, causing fire or spray area. An additional length of hose
explosion, may be required.
Store flammable materials in a secure
location away from compressor.
Restricting any of the compressor
ventilation openings will cause serious
overheating and could cause fire.
Unattended operation of this product
could result in personal injury or
property damage. To reduce the risk of
fire, do not allow the compressor to
operate unattended.
Never place objects against or on top
of compressor. Operate compressor in
an open area at least 12 inches away
from any wall or obstruction that would
restrict the flow of fresh air to the
ventilation openings.
Operate compressor in a clean, dry well
ventilated area. Do not operate unit
indoors or in any confined area.
Always remain in attendance with the
product when it is operating.
Always disconnect electrical power by
moving pressure switch lever to the off
position and drain tank daily or after
each use.
D30092 4=ENG
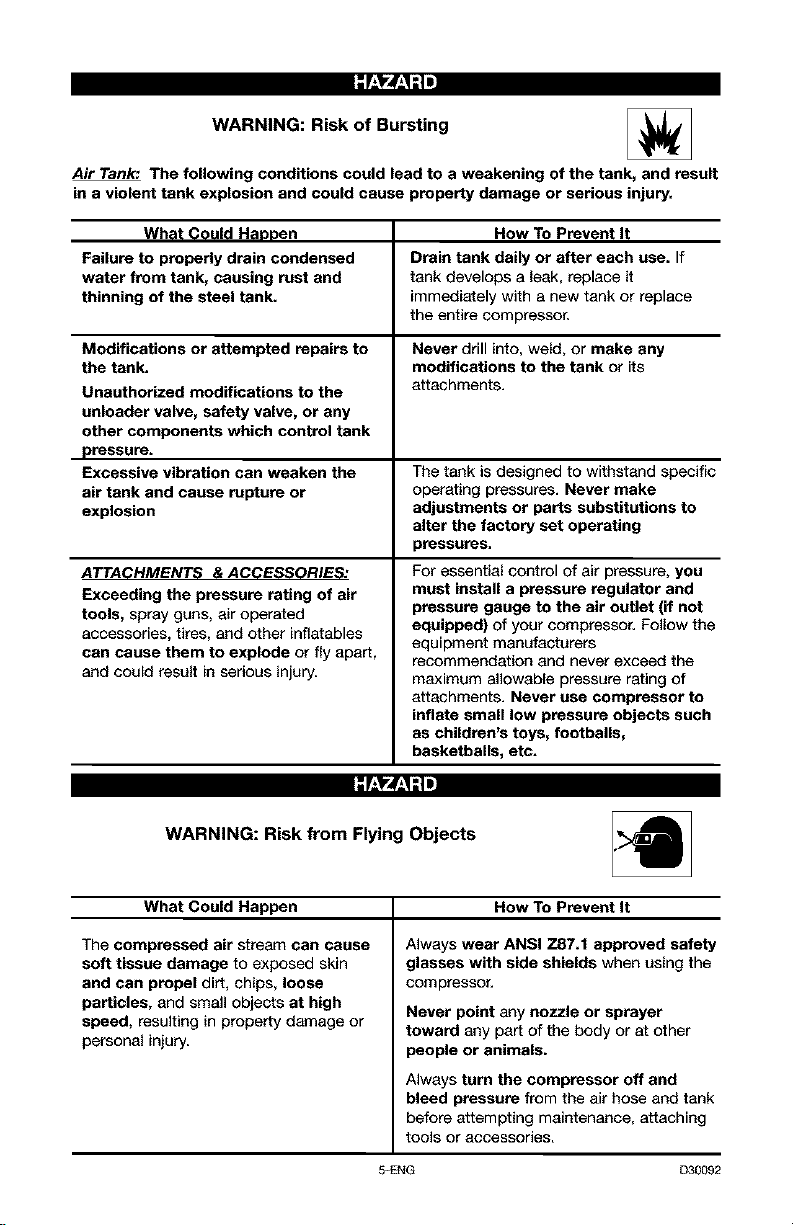
WARNING: Risk of Bursting
Air Tank', The following conditions could lead to a weakening of the tank, and result
in a violent tank explosion and could cause property damage or serious injury.
What Could Haopen How To Prevent It
Failure to properly drain condensed Drain tank daily or after each use. If
water from tank, causing rust and tank develops a leak, replace it
thinning of the steel tank. immediately with a new tank or replace
the entire compressor,
Modifications or attempted repairs to Never drill into, weld, or make any
the tank. modifications to the tank or its
Unauthorized modifications to the attachments.
unloader valve, safety valve, or any
other components which control tank
pressure.
Excessive vibration can weaken the The tank is designed to withstand specific
air tank and cause rupture or operating pressures. Never make
explosion adjustments or parts substitutions to
alter the factory set operating
pressures.
ATTACHMENTS & ACCESSORIES:
Exceeding the pressure rating of air
tools, spray guns, air operated
accessories, tires, and other inflatables
can cause them to explode or fly apart,
and could result in serious injury.
For essential control of air pressure, you
must install a pressure regulator and
pressure gauge to the air outlet (if not
equipped) of your compressor. Follow the
equipment manufacturers
recommendation and never exceed the
maximum allowable pressure rating of
attachments. Never use compressor to
inflate small low pressure objects such
as children's toys, footballs,
basketballs, etc.
-"f.,_'_f.,1"1=
WARNING: Risk from Flying Objects
What Could Happen How To Prevent It
The compressed air stream can cause
soft tissue damage to exposed skin
and can propel dirt, chips, loose
particles, and small objects at high
speed, resulting in property damage or
personal injury.
Always wear ANSI Z87.f approved safety
glasses with side shields when using the
compressor,
Never point any nozzle or sprayer
toward any part of the body or at other
people or animals.
Always turn the compressor off end
bleed pressure from the air hose and tank
before attempting maintenance, attaching
tOOlS or accessories,
5-ENG D30092
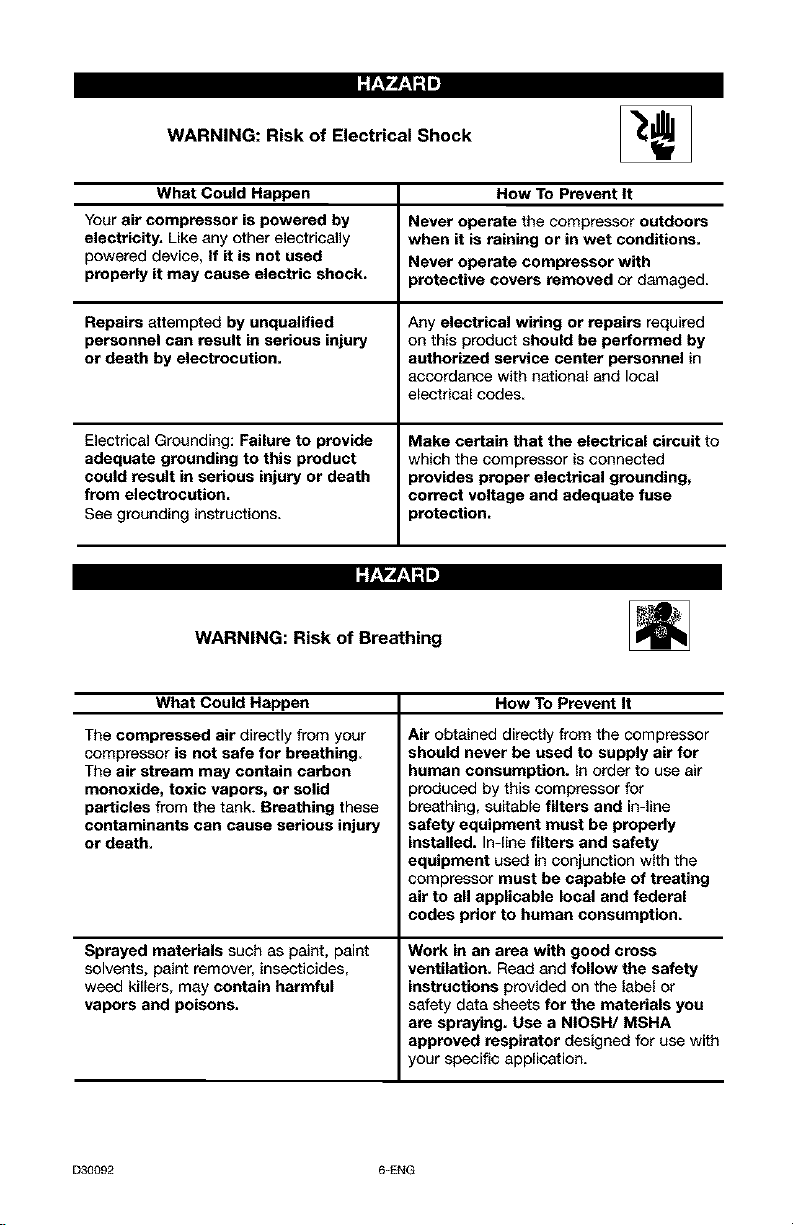
:f:1"4_;ll
WARNING: Risk of Electrical Shock _J
What Could Happen
Your air compressor is powered by
electricity. Like any other electrically
powered device, If it is not used
properly it may cause electric shock.
Repairs attempted by unqualified
personnel can result in serious injury
or death by electrocution.
Electrical Grounding: Failure to provide
adequate grounding to this product
could result in serious injury or death
from electrocution.
See grounding instructions,
WARNING: Risk of Breathing
What Could Happen How To Prevent It
The compressed air directly from your
compressor is not safe for breathing.
The air stream may contain carbon
monoxide, toxic vapors, or solid
particles from the tank. Breathing these
contaminants can cause serious injury
or death.
How To Prevent It
Never operate the compressor outdoors
when it is raining or in wet conditions.
Never operate compressor with
protective covers removed or damaged.
Any electrical wiring or repairs required
on this product should be performed by
authorized service center personnel in
accordance with national and local
electrical codes,
Make certain that the electrical circuit to
which the compressor is connected
provides proper electrical grounding,
correct voltage and adequate fuse
protection.
Air obtained directly from the compressor
should never be used to supply air for
human consumption, in order to use air
produced by this compressor for
breathing, suitable filters and in-line
safety equipment must be properly
installed. In-line filters and safety
equipment used in conjunction with the
compressor must be capable of treating
air to all applicable local and federal
codes prior to human consumption.
Sprayed materials such as paint, paint
solvents, paint remover, insecticides,
weed killers, may contain harmful
vapors and poisons,
D30092 6=ENG
Work in an area with good cross
ventilation. Read and follow the safety
instructions provided on the label or
safety data sheets for the materials you
are spraying. Use a NtOSH/MSHA
approved respirator designed for use with
your specific application.
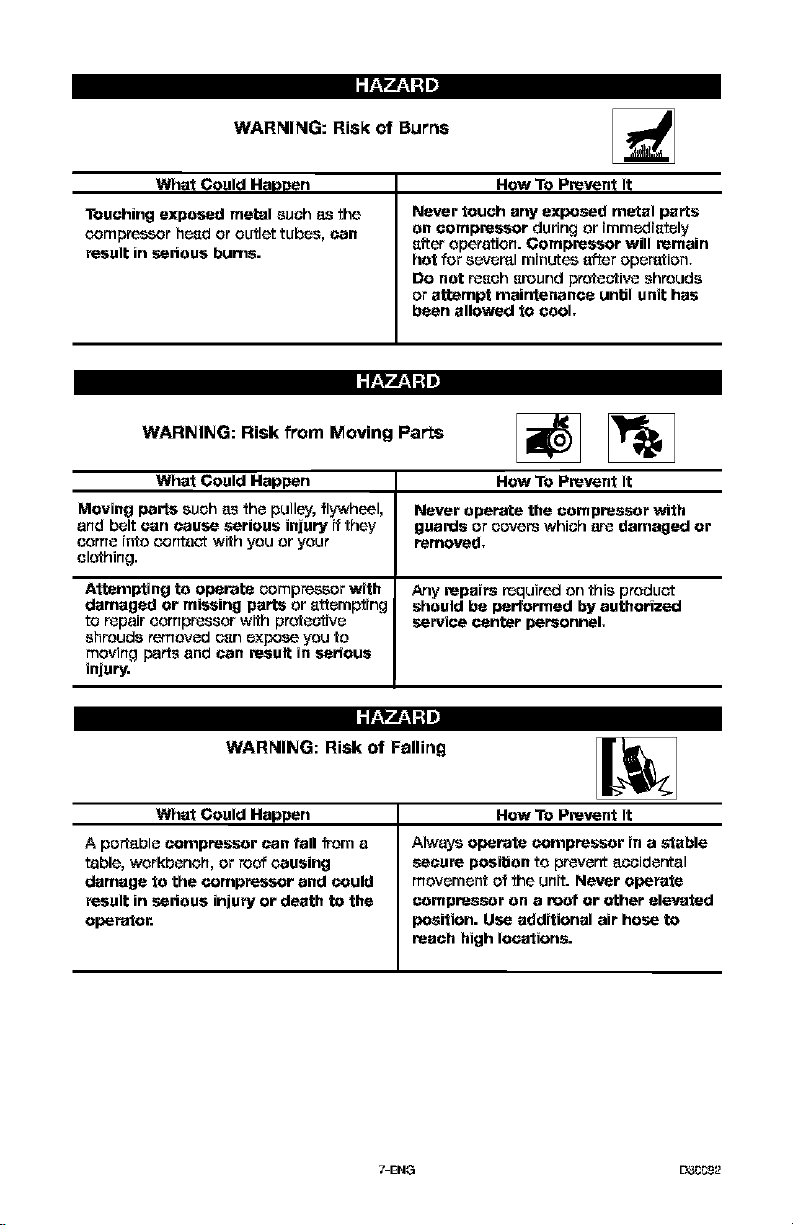
f-'_J-'1_ i
WARNING: Risk of Burns
What Gould Happen
Touching exposed metal such _ the
oompre_r hcsd or outlet tubes, _an
result in serious bums.
Never touch any exposed metal parts
on compressor during or immedistely
sft_r operation. Gompressor will remain
hot for scvcml minutes a_er operation,
Do net r_sch sreund protective shrouds
or attempt mairrtenance unbl unit has
been allowed to cool,
How To Prevent It
;F-'YJ-'I:,]J
WARNING: Risk from Moving Parts _T)
What Could Happen How To Prevent It
Moving parts such a_ the pulley, flywheel, Never operate the compressor with
and belt can cause serious injury if they guards or covers which a_ damaged or
come into _,ontact with you or your removed,
el_hing.
Attempting to operate compressor with Any repairs r_quired on this product
damaged or missing parts or _cm_ing should be performed by authorized
to r_pair compressor with profeutivc service center personnel,
shrouds removed c_n expose you to
moving parts and can result in serious
injury.
;F_,yJ_,_!:,]J
WARNING: Risk of Falling
What Gould Happen
A portable compressor can fall _m a
table, workbench, or roof causing
damage to the compressor and could
result in serious injury or death to the
operator.
How To Prevent It
Always operate compressor in a stable
secure posibon to prevent accidental
movement of the unit. Never operate
compressor On a roof or ether elevated
position. Use additional air hose to
reach high locations.
7-ENG L33_92
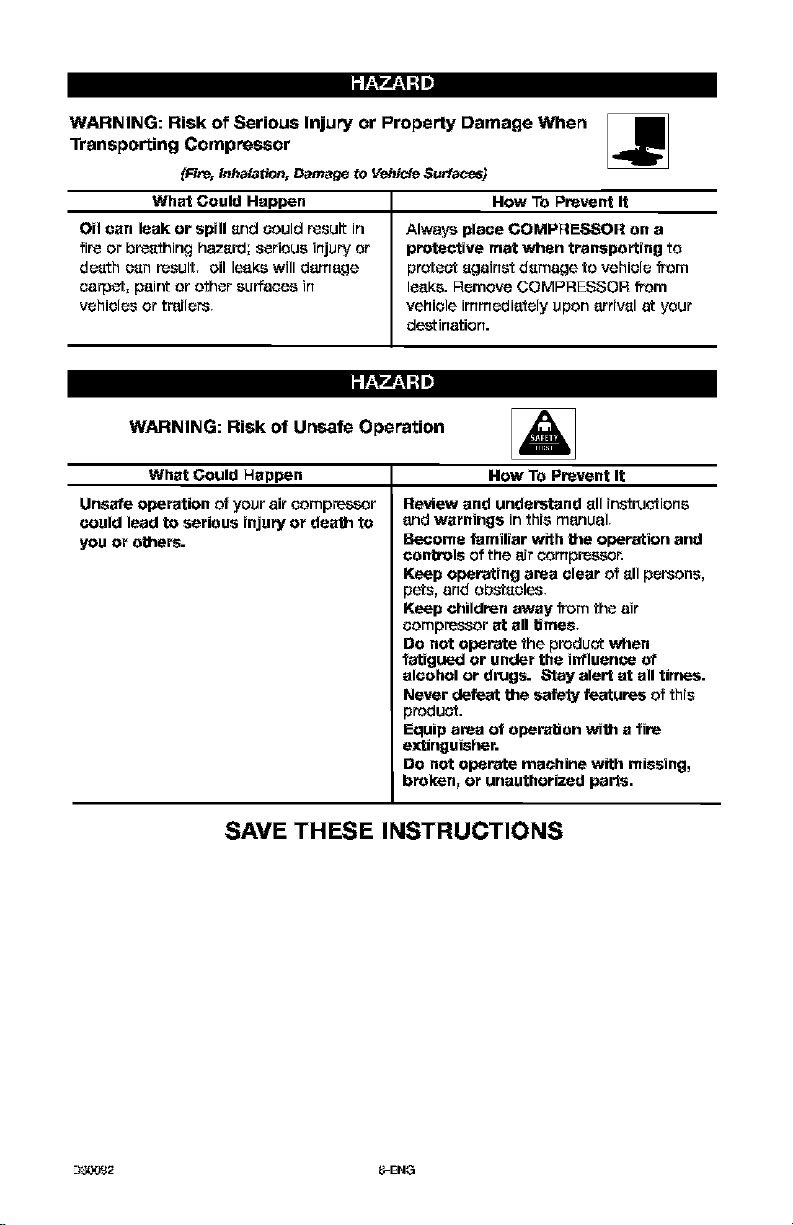
WARNING: Risk of Unsafe Operation
What Could Rappen How To Prevent It
Unsafe operation of your air compressor
could lead to serious injury or death to
you or others.
;7-'_rJ-q:t J
;7-'_r.L'_!:t J
Renew and understand all instructions
and warnings in this manual,
Become familiar with the operation and
controls of the air _mprsssor,
Keep operating area clear of all persons,
pets, and obstacles,
Keep children away _m the air
compressor at all itrnes,
Do not operate the product when
fatigued or under the influence of
alcohol or drugs. Stay alert at all times.
Never defeat the safely faatures of this
preduct.
Equip area of operation with a fire
extinguisher.
DO not operate machine with missing,
broken, or unauthorized parts.
SAVE THESE INSTRUCTIONS
:I_2 _ENG
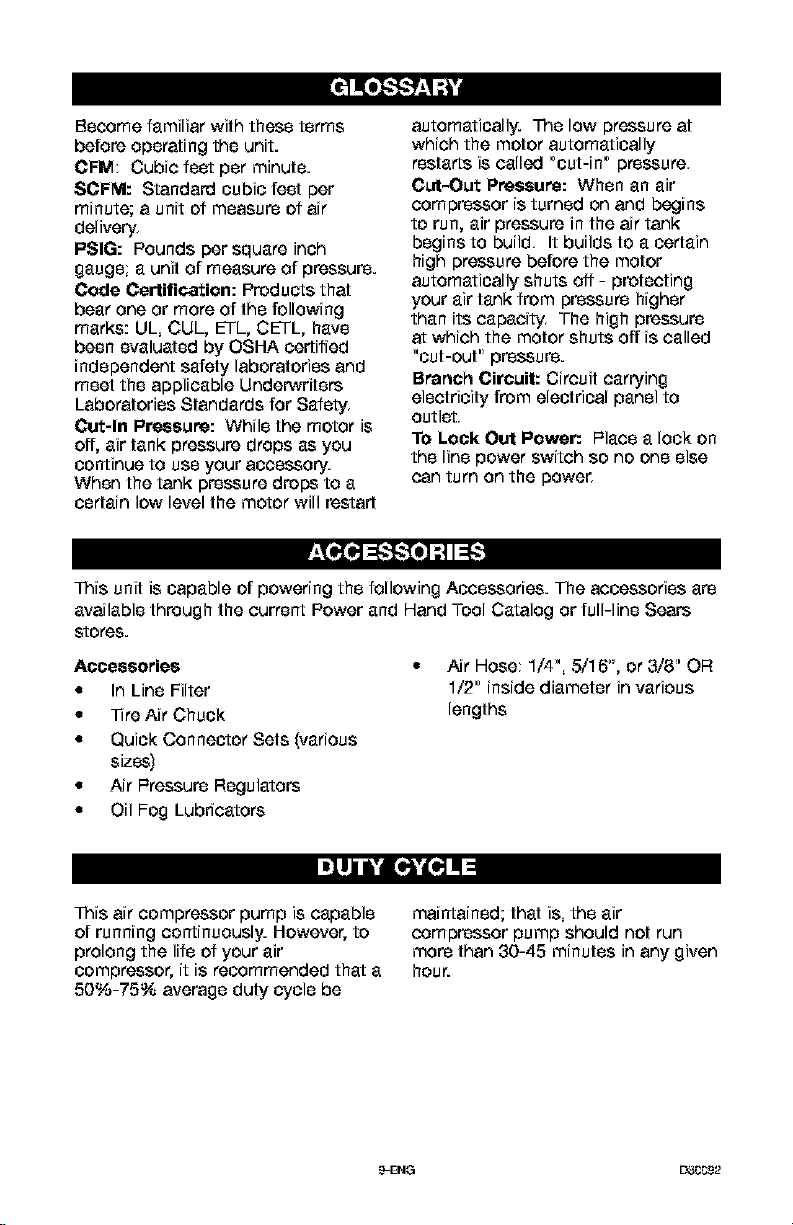
Become familiar with these terms
before operating the unit.
CFM Cubicfest per minute.
SCFM: Standard cubic feet per
minute; a unit of measure of air
delivery.
PSIG: Pounds per square inch
gauge; a unit of measure of pressure.
Code Certification: Products that
bear one or more of the following
marks: UL, CUL, ETL, CETL, have
been evaluated by OSHA certified
independent safety laboratories and
meet the applicable Underwriters
Laboratories Standards for Safety,
Cut*In Pressure: While the motor is
off, air tank pressure drops as you
continue to use your accessory.
When the tank pressure drops to a
automatically. Tr_e low pressure at
which the motor automatically
restarts is called "cut-in" pressure,
Cut-Out Pressure: When an air
compressor is turned on and begins
to run, air pressure in the air tank
begins to build, It builds to a certain
high pressure before the motor
automatically shuts off - protecting
your air tank from pressure higher
than its capacity. The high pressure
at which the motor shuts Off is called
"cut -out" preesure.
Branch Circuit: Circuit carrying
electricity from electrical panel to
outlet,
To Lock Out Power: Place a lock on
the line power switch SOno one else
can turn on the powe_
certain low level the motor will restart
Troisunit is capable of powering the following Accessories. The accessories are
available through the current Power and Hand Tool Catalog or full-line Sears
stores.
Accessories
• In Line Filter
• Tire Air Chuck
• Air Hose: 1/4", 5/16", or 3/8" OR
1/2" inside diameter in various
lengths
• Quick Connector Sets (various
sizes)
• Air Pressure Regulators
• Oil Fog Lubricators
Troisair compressor pump is capable
of running continuously. However, to
prolong the life of your air
compressor, it is recommended that a
50%-75% average duty cycle be
maintained; that is, the air
compressor pump should not run
more than 30-45 minutes in any given
hour.
_-ENG L3_92
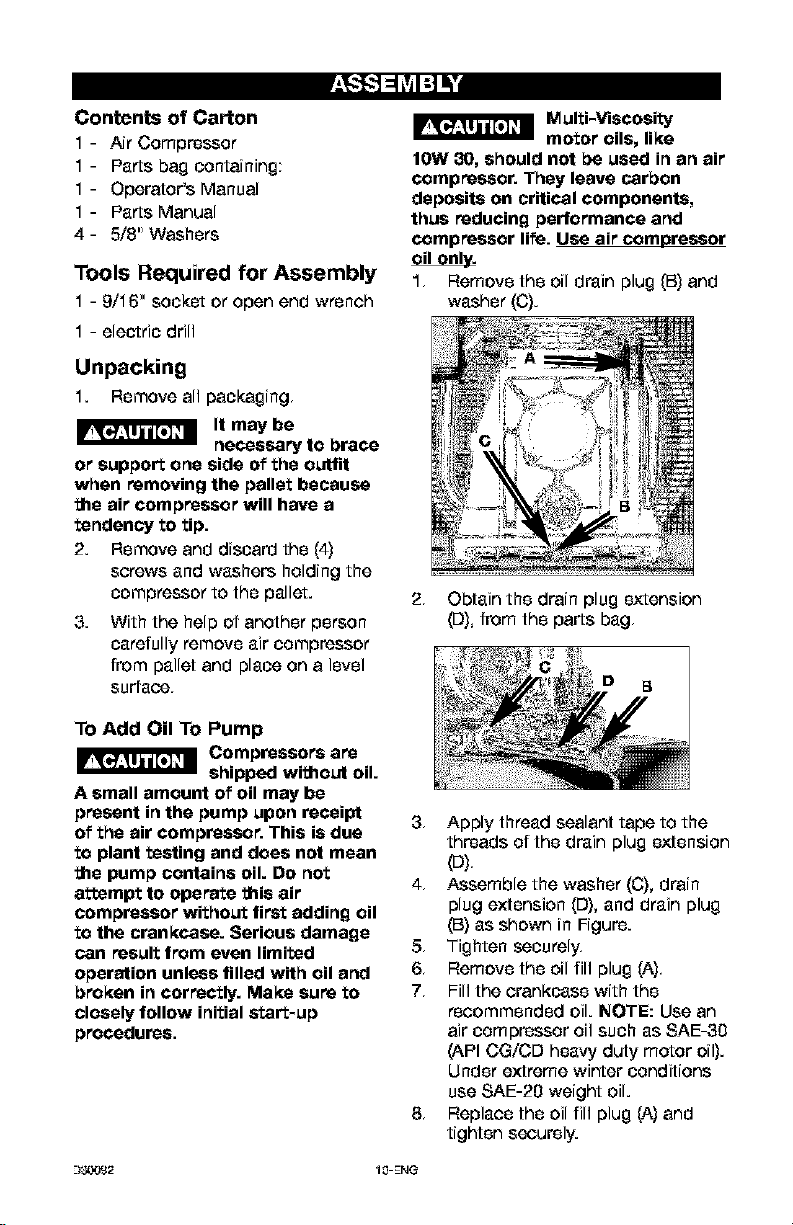
Contents of Carton
1 - Air Compressor
1 - Parts bag containing:
1 - Operator's Manual
1 - Parts Manual
4 - 5/8" Washers
Tools Required for Assembly
1 - g/16" socket or open end wrench
1 - electric drill
Unpacking
1. Remove all packaging,
It may be
necessary to brace
or support one side of the outfit
when removing the pallet because
the air compressor will have a
tendency to tip.
2. Remove and discard the (4)
screws and washers holding the
compressor to the pallet.
3. With the help of another person
carefully remove air compressor
from pallet and place on a level
surface,
iI=l,t'
Multi-Viscosity
motor oils, like
10W 80, should not be used in an air
compressor. They leave carbon
deposits on critical components,
thus reducing performance and
compressor life. Use air compressor
oil only..
1, Remove the oil drain plug (B) and
washer (C).
2, Obtain the drain plug extension
([3), from the parts bag,
To Add Oil To Pump
_ Compressore are
A small amount of oil may be
present in the pump upon receipt
of the air compressor. This is due
to plant testing and does not mean
the pump contains oil. Do not
attempt to operate this air
compressor without first adding oil
to the crankcase. Serious damage
can result from even limited
operation unless filled with oil and
broken in correctly. Make sure to
closely follow initial start*up
procedures.
--)_2 1,q-ENG
shipped without oil.
3, Apply thread sealant tape to the
threads of the drain plug extension
4, Assemble the washer (C), drain
plug extension (D), and drain plug
(B) as shown in Figure.
5, Tighten securely.
6, Remove the oil fill plug (A),
7, Fill the crankcase with the
recommended oil. NOTE: Use an
air compressor oil such as SAE-30
(API CG/CD heavy duty motor oil).
Under extreme winter conditions
use SAE-20 weight oil.
8, Replace the oil fill plug (A) and
tighten securely.
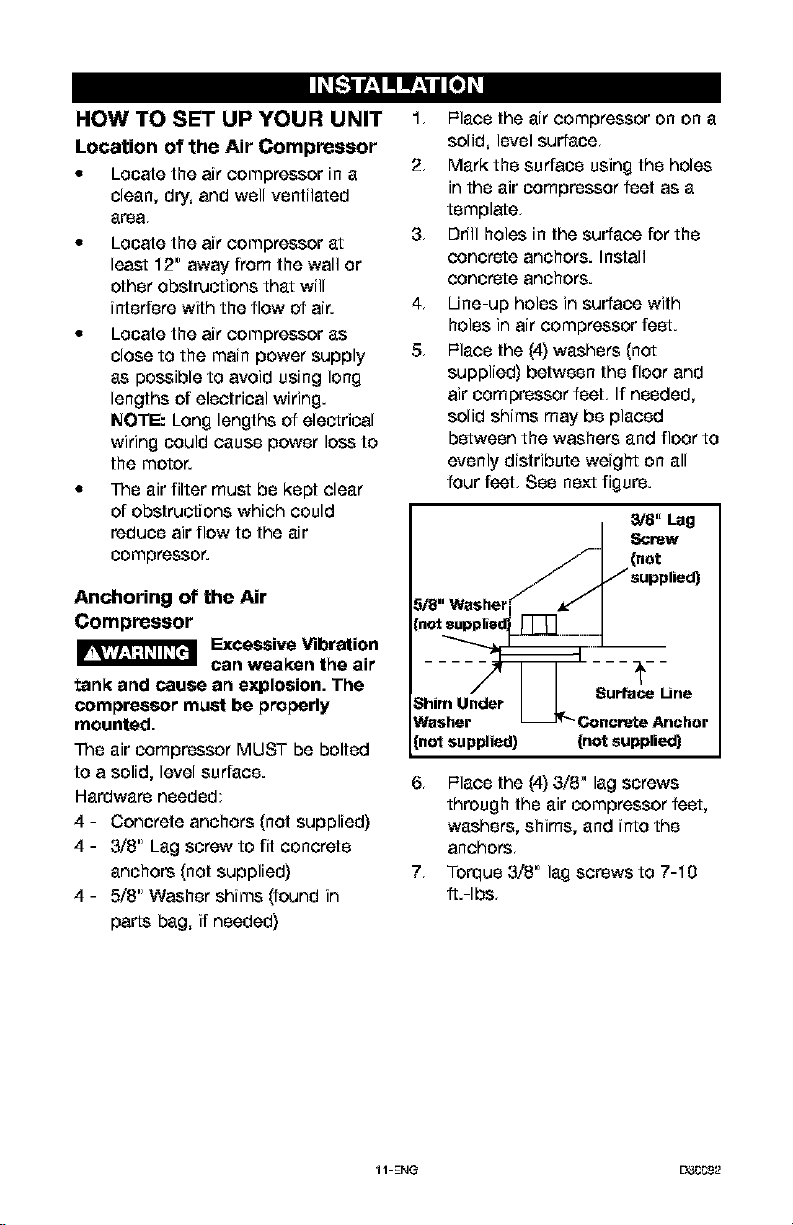
HOW TO SET UP YOUR UNIT
Location of the Air Compressor
• Locate the air compressor in a
clean, dry, and well ventilated
area,
• Locate the air compressor at
least 12" away from the wall or
other obetruc'tions that will
interfere with the flow of air.
• Locate the air compressor as
close to the main power supply
as possible to avoid using long
lengths of electrical wiring.
NOTE: Long lengths of electrical
wiring could cause power loss to
the motor.
• Tr_eair filter must be kept clear
of obetruc'tions which could
reduce air flow to the air
compressor.
Anchoring of the Air
Compressor
Excessive Vibration
can weaken the air
tank and cause an explosion. The
compressor must be properly
mounted.
Tr_eair compressor MUST be bolted
to a solid, level surface.
Hardware needed:
4 - Concrete anchors (not supplied)
4 - 3/8" Lag screw to fit concrete
anchors (not supplied)
4 - 5/8" Washer shims (found in
parts bag, if needed)
1, Place the air compressor on on a
solid, level surface,
2, Mark the surfaes using the holes
in the air compressor feet as a
template,
3, Drill holes in the surface for the
concrete anchors. Install
concrete anchors.
4, Une-up holes in surface with
holes in air compressor feet.
5, Place the (4)washers (not
supplied) between the floor and
air compressor feet, If needed,
solid shims may be placed
between the washers and floor to
evenly distribute weight on all
four feet, See next figure.
3/8' Lag
_rew
(net
--_--
ShimUnder
Surface Line
Washer Concrete Anchor
[notsupplied) (not supplied)
6, Place the (4)3/8" lag screws
through the air compressor feet,
washers, shims, and into the
anchors,
7, Torque 3/8" lag screws to 7-10
fL-Ibs,
11-ENG L33CC9_2
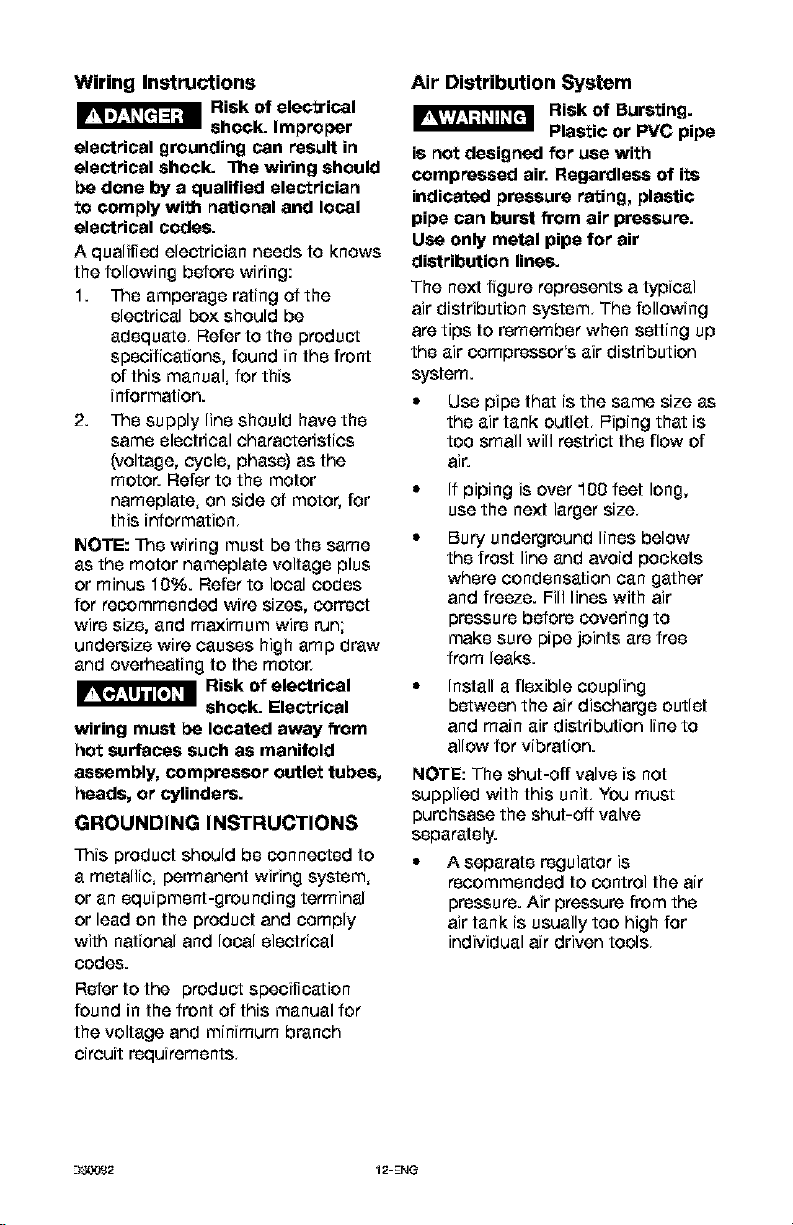
Wiring Instructions
_Risk of elec_ical
shock. Improper
electrical grounding can result in
electrical shock. The wiring should
be done by a qualified electrician
to comply with national and local
electrical codes.
A qualified electrician needs to knows
the following before wiring:
1. Tr_e amperage rating of the
electrical box should be
adequate, Refer to the product
specifications, found in the front
of this manual, for this
information.
2. Tr_esupply line should have the
same electrical charac'tedsfice
(voltage, cycle, phase) as the
motor. Refer to the motor
nameplate, on side of motor, for
this information,
NOTE: Tr_ewiring must be the same
as the motor nameplate voltage plus
or minus 10%. Refer to local codes
for recommended wire sizes, correct
wire size, and maximum wire run;
undersize wire causes high amp draw
and overheafing to the moto_
Risk of electrical
shock. Electrical
wiring must be located away _om
hot surfaces such as manifold
assembly, compressor outlet tubes,
heads, or cylinders.
GROUNDING INSTRUCTIONS
Trois product should be connected to
a metallic, permanent wiring system,
or an equipment-grounding terminal
or lead on the product and comply
with national and local electrical
codes.
Refer to the product specification
found in the front of this manual for
the voltage and minimum branch
circuit requirements,
Air Distribution System
Risk of Bursting.
Plastic or PVC pipe
is not designed for use with
compressed air. Regardless of its
indicated pressure rating, plastic
pipe can burst _om air pressure.
Use only metal pipe for air
distribution lines.
The next figure represents a typical
air distribution system, The following
are tips to remember when setting up
the air eompressor's air distribution
system.
Use pipe that is the same size as
the air tank outlet, l=iping that is
too small will restrict the flow of
air.
• If piping is over 100 feet long,
use the next larger size,
Bury underground lines below
the frost line and avoid pockets
where condensation can gather
and freeze. Fill lines with air
pressure before covering to
make sure pipe joints are free
from leaks.
Install a flexible coupling
between the air discharge outlet
and main air distribution line to
allow for vibration.
NOTE: The shut-off valve is not
supplied with this unit, You must
purehsase the shut-off valve
separately.
A separate regulator is
recommended to control the air
pressure. Air pressure from the
air tank is usually too high for
individual air driven tools,
--I_2 12-ENG
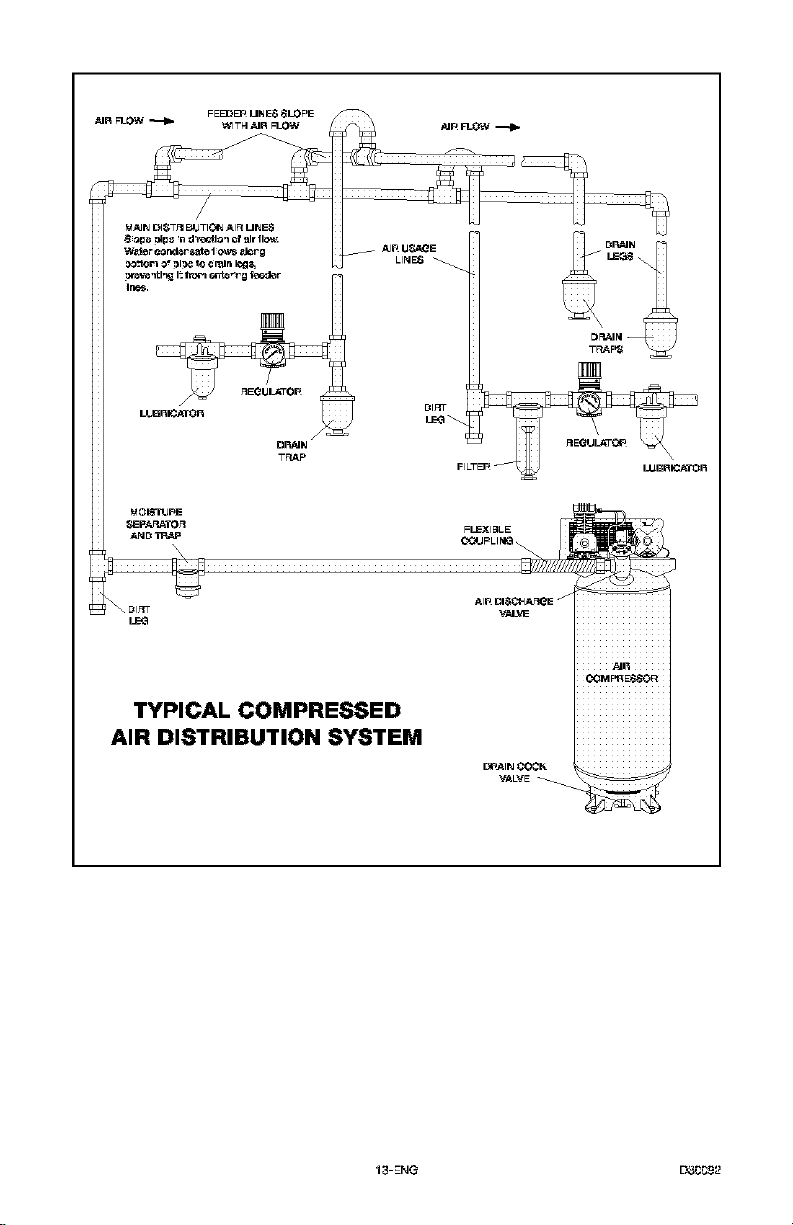
LEG
TYPICAL COMPRESSED
AIR DISTRIBUTION SYSTEM
13-ENG L33_92
VALVE _
I_Al_J _CK _
AIR
CCM PRE,_OR
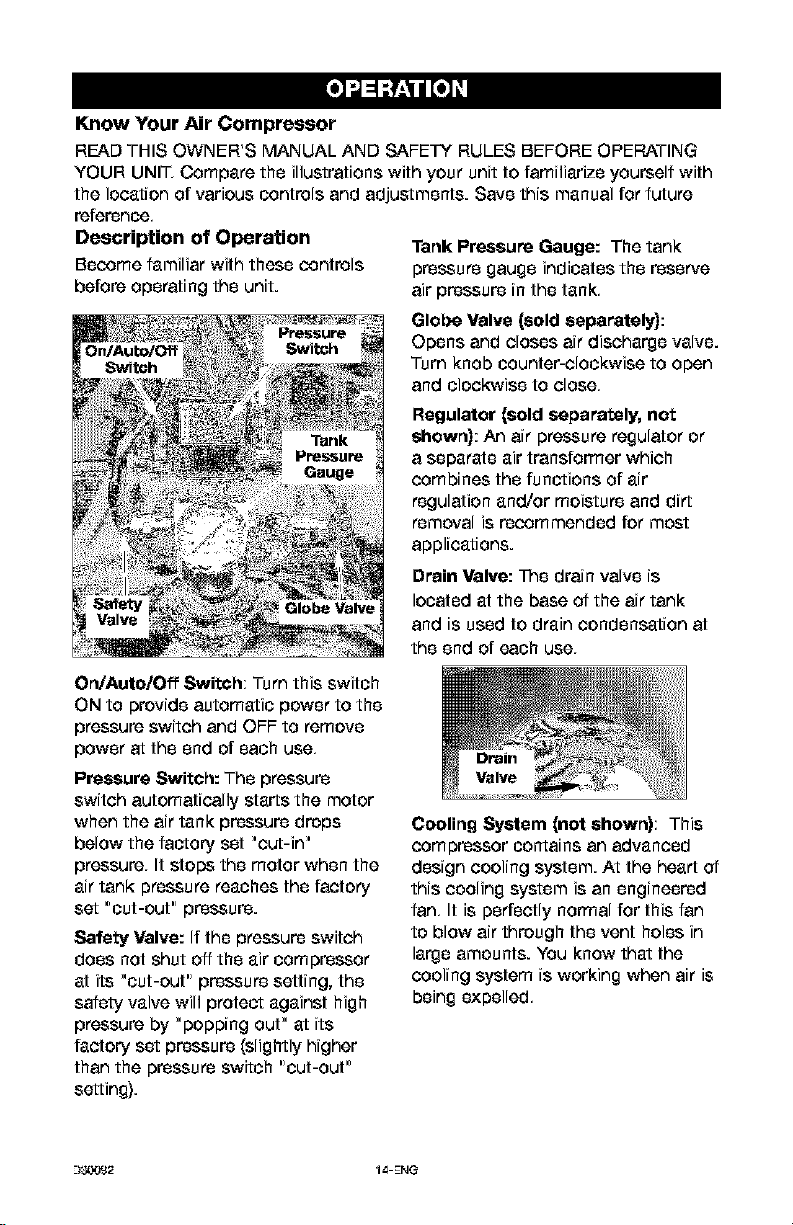
Know Your Air Compressor
READ THIS OWNER'S MANUAL AND SAFETY RULES BEFORE OPERATING
YOUR UNI_ Compare the illustrations with your unit to familiarize yourself with
the location of various controls and adjustments. Save this manual for future
reference,
Description Of Operation
Become familiar with these controls
before operating the unit.
Tank Pressure Gauge: The tank
pressure gauge indicates the reserve
air pressure in the tank,
Glebe Valve (sold separately):
Opens and closes air discharge valve.
Turn knob counter-clockwise to open
and clockwise to close,
Regulator (sold separe_ely, not
shown):/_ air pressure regulator or
a separate air transformer which
combines the functions of air
regulation and/or moisture and dirt
removal is recommended for most
applications.
Drain Valve: Tr_e drain valve is
located at the base of the air tank
and is used to drain condensation at
the end of each use,
On/Auto/Off Switch; Turn this switch
ON to provide automatic power to the
pressure switch and OFF to remove
power at the end of each use,
Pressure Switch: The pressure
switch automatically starts the motor
when the air tank pressure drops
below the factory set "cut-in"
pressure, It stops the motor when the
air tank pressure reaches the factory
set "cut-out" pressure.
Safety Valve: If the pressure switch
does not shut off the air compressor
at its "cut-out" pressure setting, the
safety valve will protect against high
Cooling System (not shown); This
compressor contains an advanced
design cooling system. At the head 04
this cooling system is an engineered
fan, It is perfectly normal for this fan
to blow air through the vent holes in
large amounts. You know that the
cooling system is working when air is
being expelled,
pressure by "popping out" at its
factory set pressure (slightly higher
than the pressure switch "cut-out"
setting).
--)_,YJ£2 14-ENG
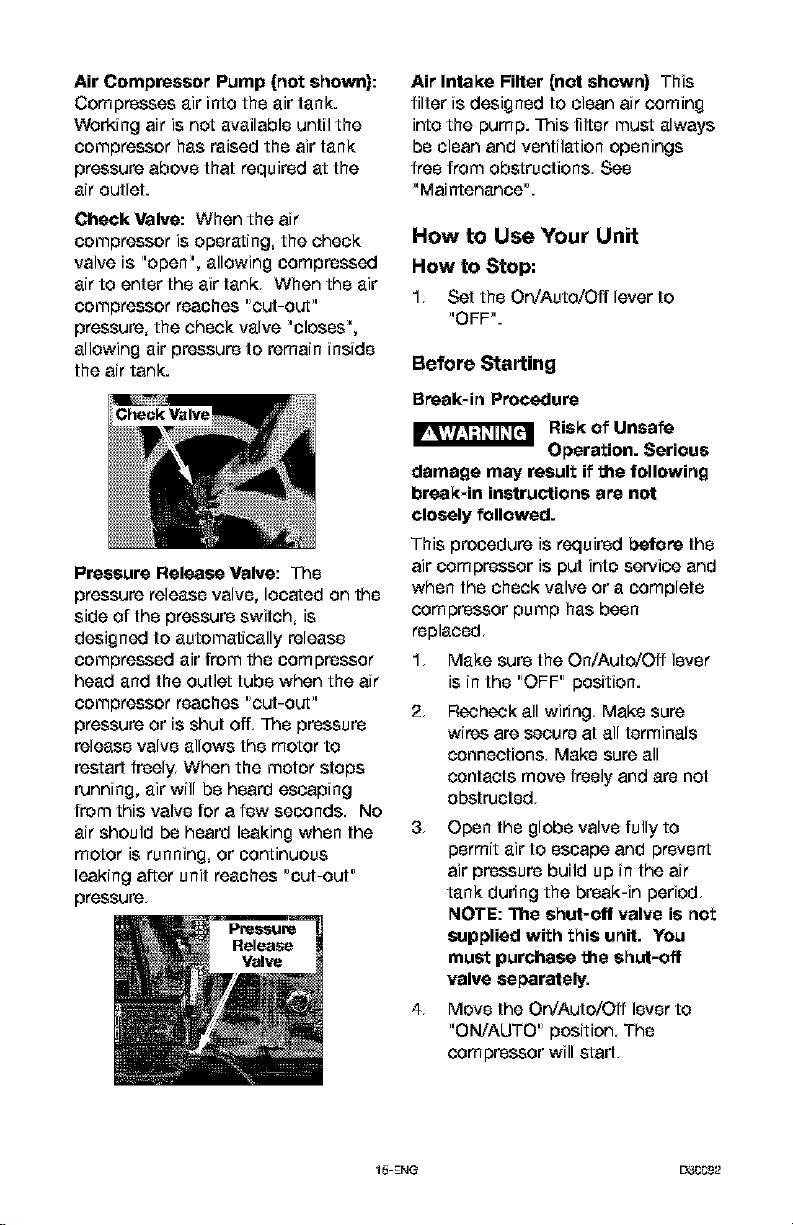
Air Compressor Pump (not shown):
Compresses air into the air tank.
Working air is not available until the
compressor has raised the air tank
pressure above that required at the
air outlet.
Check Valve: When the air
compressor is operating, the check
valve is "open", allowing compressed
air to enter the air tank, When the air
compressor reaches "cut-out"
pressure, the check valve "closes",
allowing air pressure to remain inside
the air tank.
Pressure Release Valve: The
pressure release valve, located on the
side of the pressure switch, is
designed to automatically release
compressed air from the compressor
head and the outlet tube when the air
compressor reaches "out-out"
pressure or is shut off, Tr_epressure
release valve allows the motor to
restart freely. When the motor stops
running, air will be heard escaping
from this valve for a few seconds, No
air should be heard leaking when the
motor is running, or continuous
leaking after unit reaches "out-out"
pressure,
Air Intake Filter (not shown) This
filter is designed to clean air coming
into the pump. Troisfilter must always
be clean and ventilation openings
free from obstructions, See
"Maintenance'.
How to Use Your Unit
How to Stop:
1, Set the 0n/Auto/0ff lever to
_,OFF_,.
Before Starting
Break*in Procedure
Risk of Unsafe
Operation. Serious
damage may result if the following
break*in instructions are not
closely followed.
This procedure is required before the
air compressor is put into service and
when the check valve or a complete
compressor pump has been
replaced,
1, Make sure the On/Auto/Off lever
is in the "OFF" position.
2, Recheck all wiring, Make sure
wires are secure at all terminals
connections, Make sure all
contacts move freely and are not
obstructed,
3, Open the globe valve fully to
permit air to escape and prevent
air pressure build up in the air
tank during the braak-in period,
NOTE: The shut*off valve is net
supplied with this unit. You
must purchase the shut-off
valve separately.
4, Move the 0n/Auto/Off lever to
"0N/AUT0" position, The
compressor will start,
15-ENG D_CC9_2
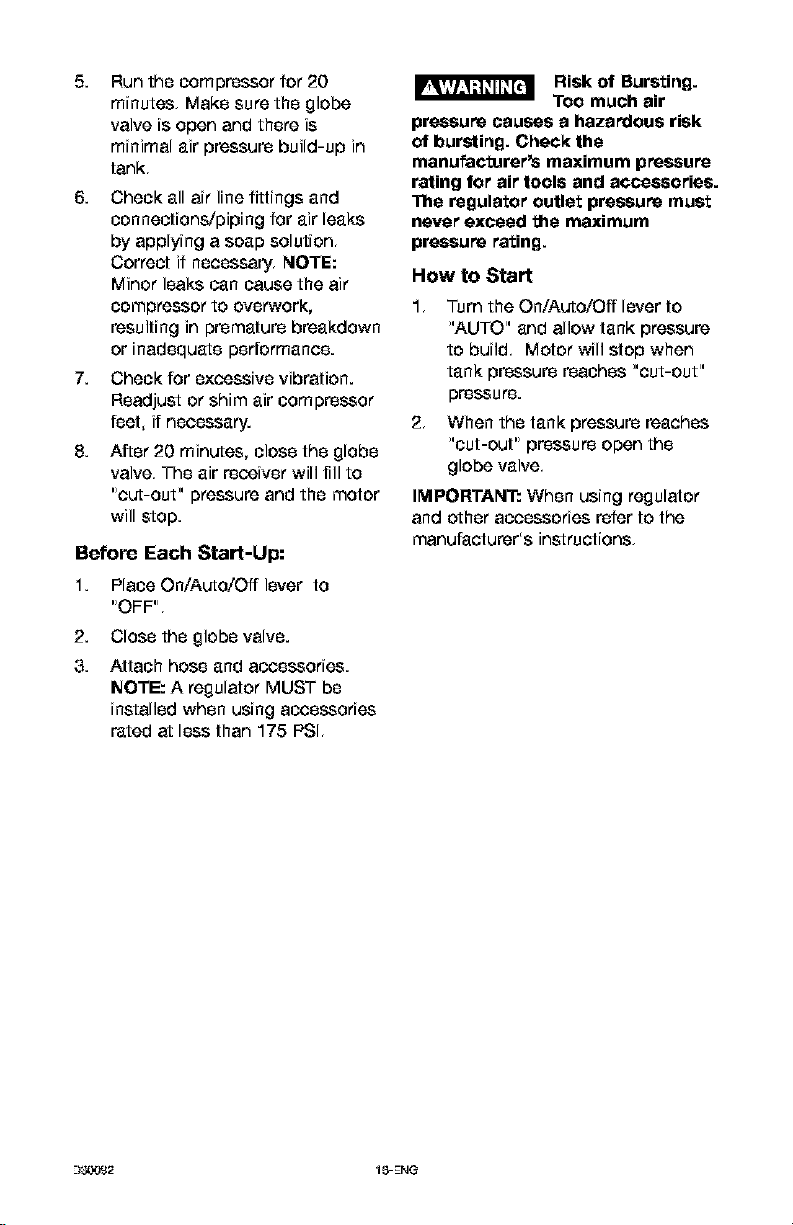
5. Run the cornpressor for 20
minutes, Make sure the globe
valve is open and there is
minimal air pressure build-up in
tank,
6. Check all air line fittings and
connections/piping for air leaks
by applying a soap solution,
Correct if necessary. NOTE:
Minor leaks can cause the air
compressor to overwork,
resulting in premature breakdown
or inadequate performance.
7. Check for excessive vibration.
Readjust or shim air compressor
feet, if necessary.
8. After 20 minutes, close the globe
valve, The air receiver will fill to
"cut-out" pressure and the motor
will stop.
Before Each Start-Up:
1. Place On/Auto/Off lever to
._OFF,_"
2. Close the globe valve.
3. Attach hose and accessories.
NOTE: A regulator MUST be
installed when using accessories
reted at less than 175 PSI,
Risk of Bursting.
Too much air
pressure causes a hazardous risk
of bursting. Cheek the
manufacturer's maximum pressure
rating for air tools and accessories.
The regulator outlet pressure must
never exceed the maximum
pressure rating.
How to Start
1, Turn the On/Auto/Off lever to
"AUTO" and allow tank pressure
to build, Motor will stop when
tank pressure reaches "cut-out"
pressure.
2, When the tank pressure reaches
"cut-out" pressure open the
globe valve,
IMPORTANT: When using regulator
and other accessories refer to the
manufacturer's instructions,
_-)_,.v3£2 I_ENG
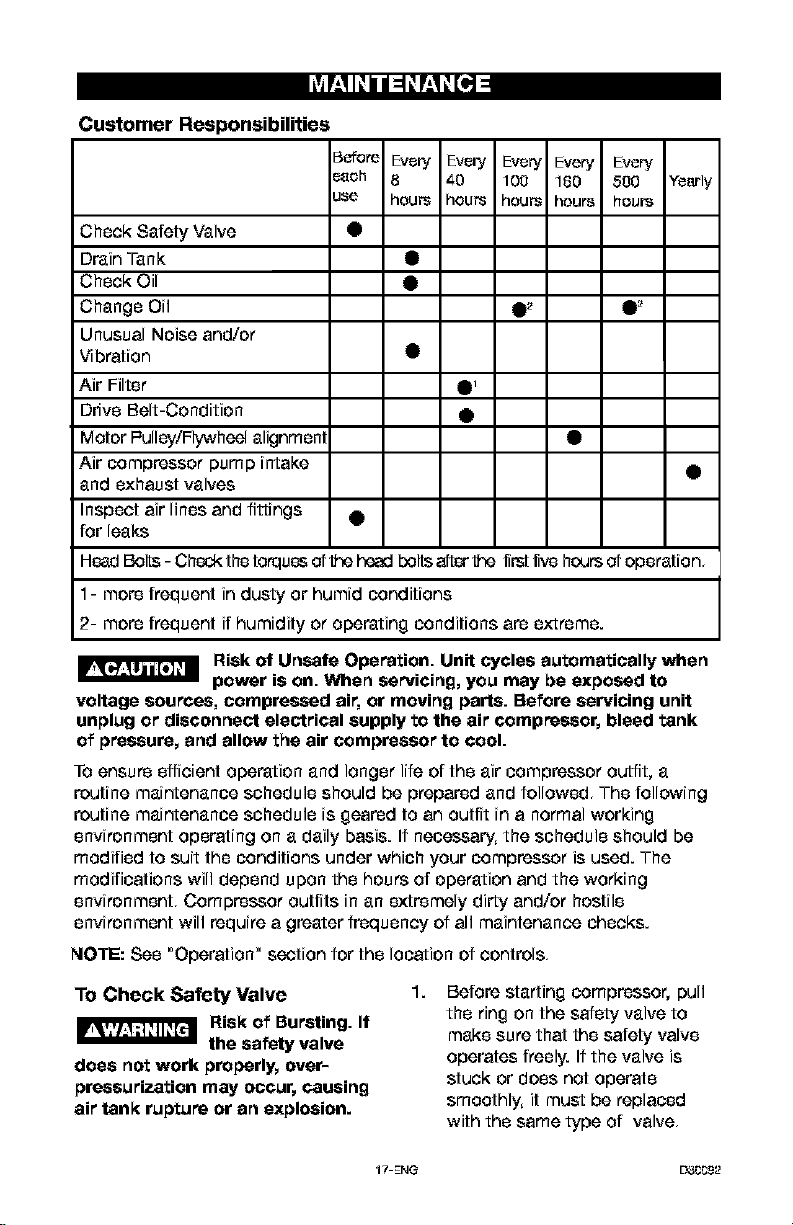
kVAr='llI_/ II =1_V=al_[_
Customer Responsibilities
5_ore Every Every Every Every Every,
_eh 8 _-0 100 180 500 Yearly
JSe hOUP3 hours houP3 hours houi_
Check Safety Valve •
Drain Tank •
Check Oil •
Change Oil •_ •_
Unusual Noise and/or
Vibration •
Air Filter •_
Drive Belt-Condition •
Motor l=ulley/Flywheel alignrnen •
Air compressor pump intake •
and exhaust valves
Inspect air lines and fittings •
for leaks
HeadBolts - Check the torques of tie headbolts after tie first five hours of operation,
1- more frequent in dusty or humid conditions
2- more frequent if humidity or operating conditions are extreme.
Risk of Unsafe Operation. Unit cycles automatically when
power is on. When sarvioing, you may be exposed to
voltage sources, compressed air, or moving parts. Before servicing unit
unplug or disconnect electrical supply to the air compressor, bleed tank
of pressure, and allow the air compressor to cool.
To ensure efficient operation and longer life of the air compressor outfit, a
routine maintenance schedule should be prepared and followed, The following
routine maintenance schedule is geared to an outfit in a normal working
environment operating on a daily basis. If necessary, the schedule should be
modified to suit the conditions under which your compressor is used. The
modifications will depend upon the hours of operation and the working
environment, Compressor outfits in an extremely dirty and/or hostile
environment will require a greater frequency of all maintenance checks.
NOTE: See "Operation" section for the location of controls,
1.
To Check Safety Valve
Before starting compressor, pull
the ring on the safety valve to
Risk of Bursting. If
the safety valve
does not work properly, over-
pressurization may occur, causing
air tank rupture or an explosion.
make sure that the safety valve
operates freely. Ifthe valve is
stuck or does not operate
smoothly, it must be replaced
with the same type of valve,
17-ENG D_CC9_2
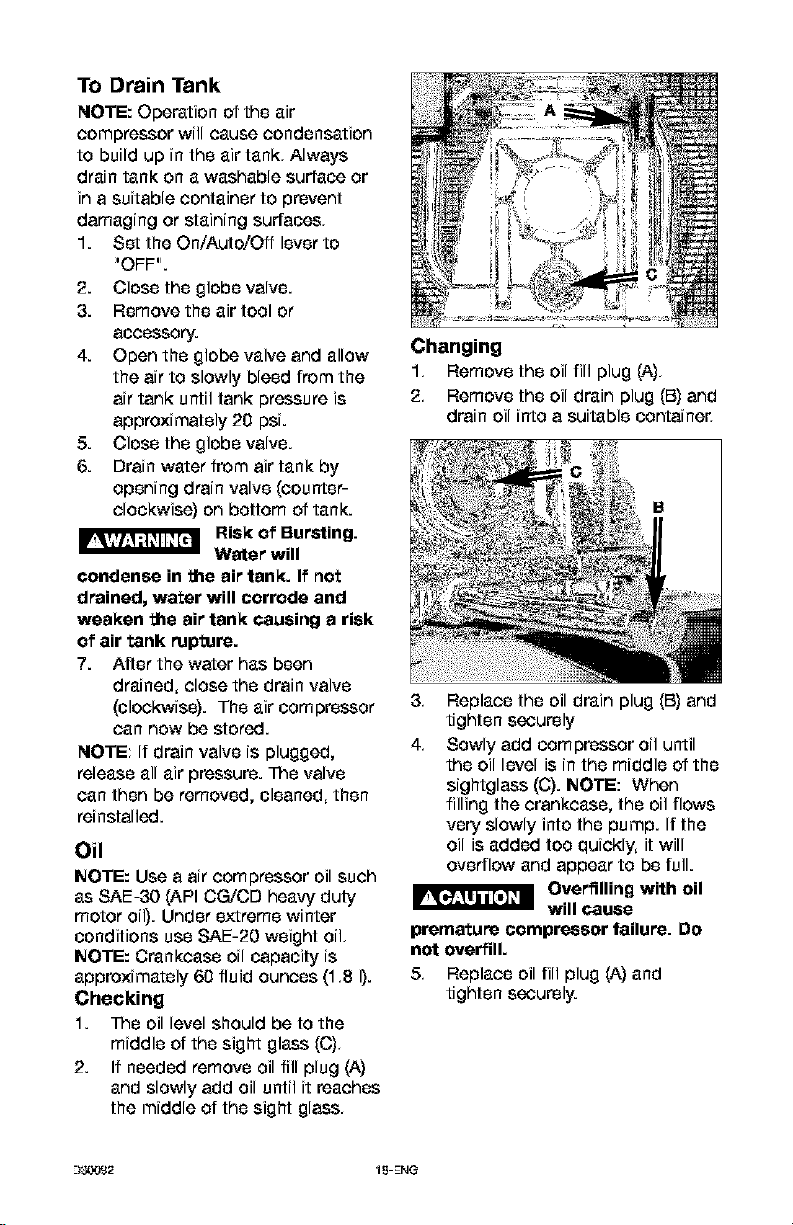
To Drain Tank
NOTE: Operation of the air
compressor will cause condensation
to build up in the air tank. Always
drain tank on a washable surface or
in a suitable container to prevent
damaging or staining surfaces.
1. Set the On/Auto/Off lever to
_,OFF,_.
2. Close the globe valve.
3. Remove the air tool or
accessory.
4. Open the globe valve and allow
the air to slowly bleed from the
air tank until tank pressure is
approximately 20 psi.
5. Close the globe valve.
6. Drain water from air tank by
opening drain valve (counter-
clockwise) on bottom of tank.
I_ Risk of Bursting.
Water will
condense in the air tank. If not
drained, water will corrode and
weaken the air tank causing a risk
of air tank rapture.
7. After the water has been
drained, close the drain valve
(clockwise). The air compressor
can now be stored.
NOTE: If drain valve is plugged,
release all air pressure. The valve
can then be removed, cleaned, then
reinstalled.
Oil
NOTE: Use a air compressor oil such
as SAE-30 (API CG/CD heavy duty
motor oil). Under extreme winter
conditions use SAE-20 weight oil.
NOTE: Crankcase oil capacity is
approximately 60 fluid ounces (1.8 l).
Checking
1. The oil level should be to the
middle of the sight glass (C).
2. If needed remove oil fill plug (A)
and slowly add oil until it reaches
the middle of the sight glass.
Changing
1. Remove the oil fill plug (A).
2. Remove the oil drain plug (B) and
drain oil into a suitable oontaine_
3. Replace the oil drain plug (B) and
tighten securely
4. Sowly add compressor oil until
the oil level is in the middle of the
sightglass (C). NOTE: When
filling the crankcase, the oil flows
very slowly into the pump. If the
oil is added too quickly, it will
overflow and appear to be full.
I_ Overfilling with oil
will cause
premature compressor failure. Do
not overfill.
5, Replace oil fill plug (A) and
tighten securely.
_-)_,.vJ£2 15-ENG