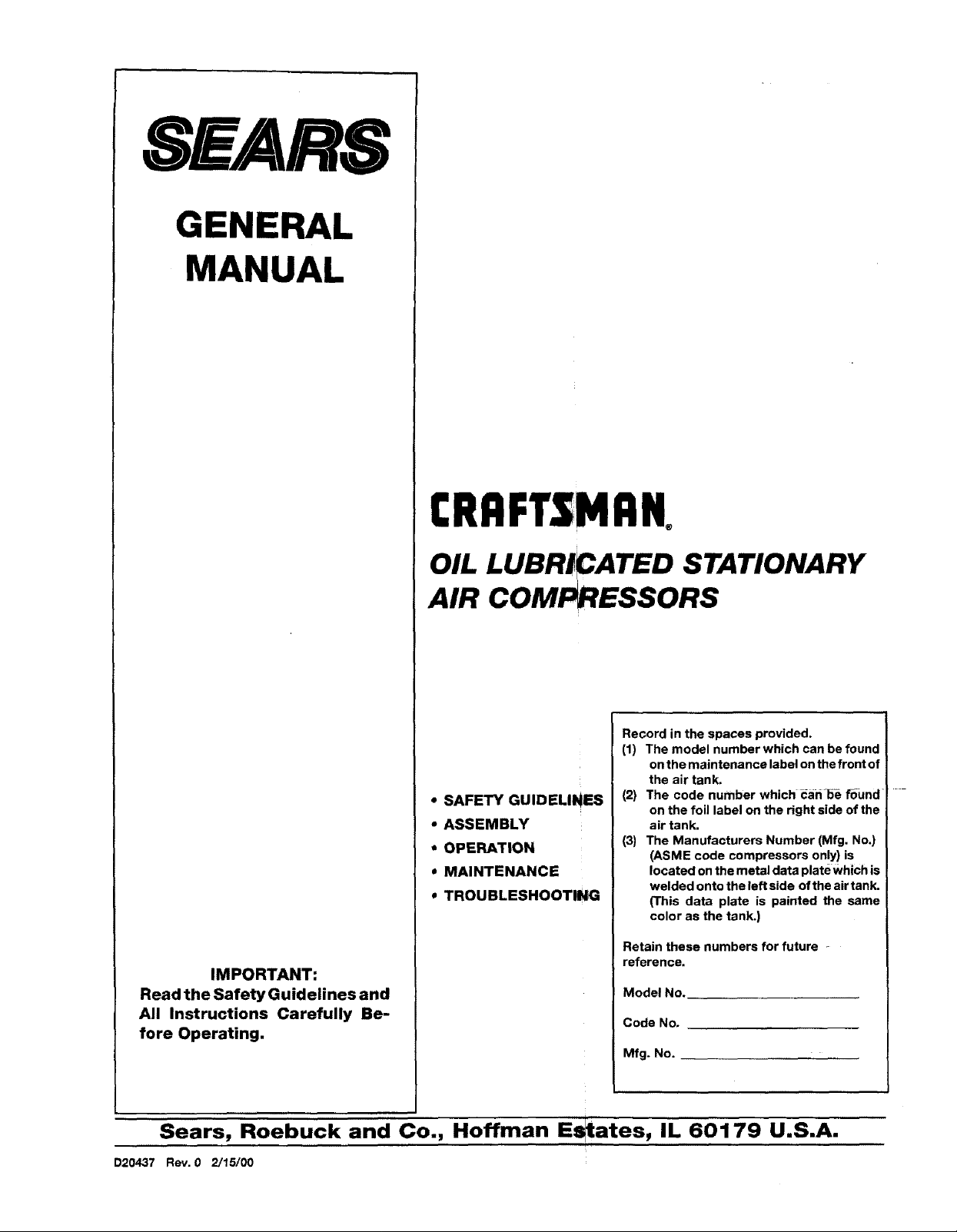
SEARS
GENERAL
MANUAL
CRRFTSHRH
OIL LUBRICATED STATIONARY
AIR COMPRESSORS
Record in the spaces provided.
(1) The model numberwhich can be found
on the maintenance label on the front of
the air tank,
° SAFETY GUIDELINES
• ASSEMBLY
° OPERATION
• MAINTENANCE
• TROUBLESHOOTING
IMPORTANT:
Read the Safety Guidelines and
All Instructions Carefully Be-
fore Operating.
(2) The code number which (:zin_Se t_und
on the foil label on the right side of the
air tank,
(3) The Manufacturers Number (Mfg. No.)
(ASME code compressors only) is
located on the metal data plate which is
welded onto the left side of the air tank.
(This data plate is painted the same
color as the tank.)
Retain these numbers for future
reference.
Model No.
Code No.
Mfg. No.
Sears, Roebuck and Co., Hoffman E_ates, IL 60179 U.S.A.
D20437 Rev. 0 2/15/00
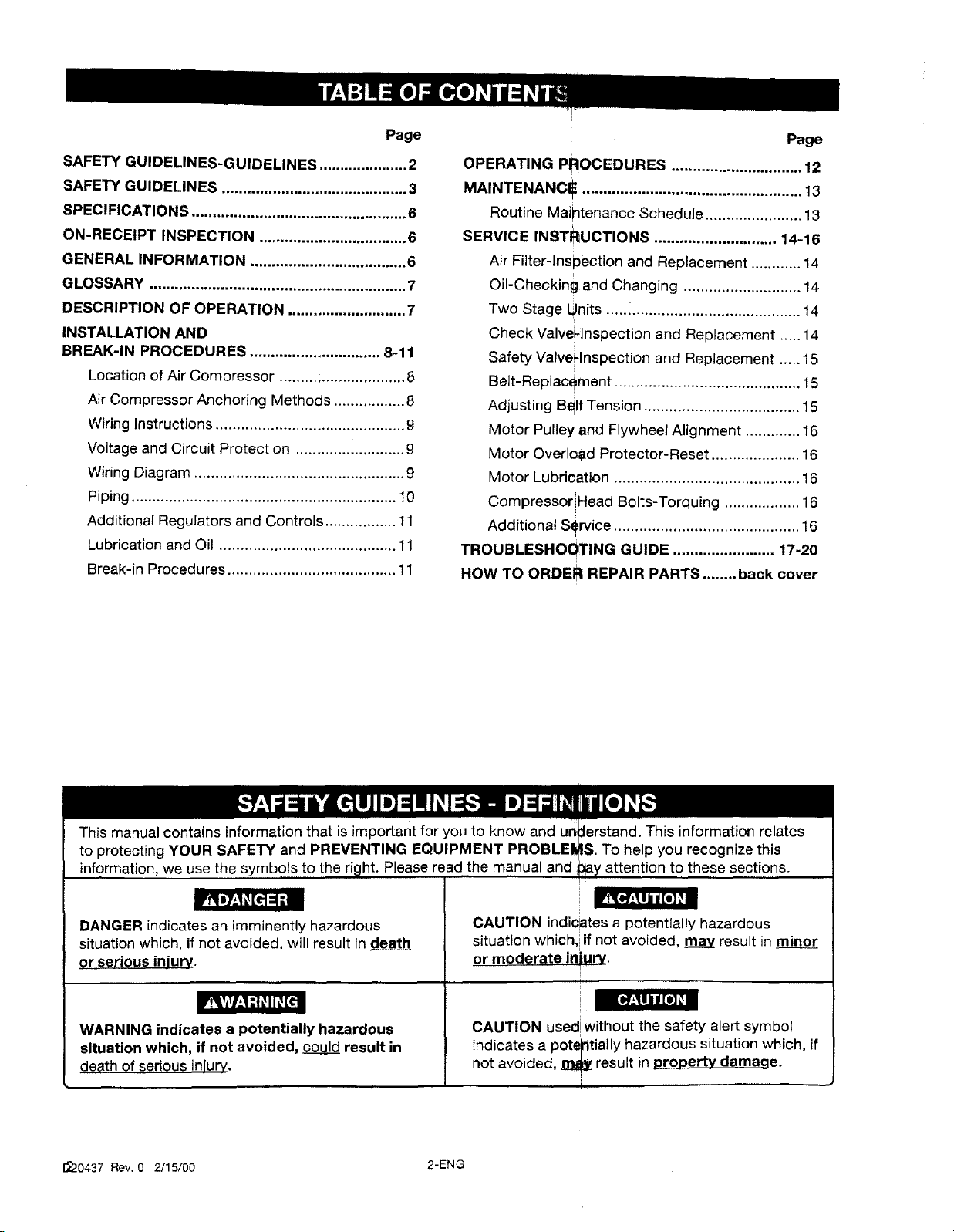
Page
SAFETY GUIDELINES-GUIDELINES ..................... 2
SAFETY GUIDELINES ............................................ 3
SPECIFICATIONS ................................................... 6
ON-RECEIPT INSPECTION ................................... 6
GENERAL INFORMATION ..................................... 6
GLOSSARY ............................................................. 7
DESCRIPTION OF OPERATION ............................ 7
INSTALLATION AND
BREAK-IN PROCEDURES ................ _.............. 8-11
Location of Air Compressor .............................. 8
Air Compressor Anchoring Methods ................. 8
Wiring Instructions ............................................. 9
Voltage and Circuit Protection .......................... 9
Wiring Diagram .................................................. 9
Piping ............................................................... 10
Additional Regulators and Controls ................. 11
Lubrication and Oil .......................................... 11
Break-in Procedures ........................................ 11
I
Page
OPERATING PROCEDURES ............................... 12
MAINTENANCE .................................................... 13
Routine Maintenance Schedule ....................... 13
SERVICE INSTRUCTIONS ............................. 14-16
Air Filter-Inspection and Replacement ............ 14
Oil-Checking and Changing ............................ 14
Two Stage Units .............................................. 14
=
Check Valve!- nspect on and Replacement ..... 14
Safety ValveHnspection and Replacement .....15
Belt-Replacement ............................................ 15
Adjusting Belt Tension ..................................... 15
Motor Pulleyi and Flywheel Alignment ............. 16
Motor Overlqad Protector-Reset ..................... 16
Motor Lubriqation ............................................ 16
Compressor jHead Bolts-Torquing .................. 16
Additional Service ............................................ 16
TROUBLESHOOTING GUIDE ........................ 17-20
=
HOW TO ORDER REPAIR PARTS ........ back cover
This manual contains information that is important for you to know and u
to protecting YOUR SAFETY and PREVENTING EQUIPMENT PROBLEI
information, we use the symbols to the right. Please read the manual
DANGER indicates an imminently hazardous
situation which, if not avoided, will result in death
or serious iniurv.
WARNING indicates a potentially hazardous
situation which, if not avoided, could result in
death of serious injury.
r_0437 Rev. 0 2/15/00 2-ENG
CAUTION indicates a potentially hazardous
situation which,i if not avoided, may result in minor
or moderate in!urv.
CAUTION usedi without the safety alert symbol
indicates a potentially hazardous situation which, if
not avoided, g31tLYresult in property damage.
attention to these sections.
I
I
i
I

IMPROPER OPERATION OR MAINTENANCE OF THIS PRODUCT COULD I:
AGE. READ AND UNDERSTAND ALL WARNINGS AND OPERATING
RISK OF EXPLOSION OR FIRE
__J
IN SERIOUS INJURY AND PROPERTY DAM-
THJS EQUIPMENT.
• iiiiii lU ilUUl i
WHAT CAN HAPPEN
IT IS NORMAL FOR ELECTRICAL CONTACTS WITHIN THE
MOTOR AND PRESSURE SWITCH TO SPARK.
' ! HOW TO PREVENT IT
ALWAYS OPERATE THE COMPRESSOR IN A WELL VENTI-
LATED AREA FREE OF COMBUSTIBLE MATERIALS, GASO-
iii i
LINE OR SOLVENT VAPORS.
IF ELECTRICAL SPARKS FROM COMPRESSOR COME INTO
CONTACT WITH FLAMMABLE VAPORS, THEY MAY IGNITE,
CAUSING FIRE OR EXPLOSION.
IF SPRAYLNG FLAMMABLE MATERIALS, LOCATE COMPRES-
SOR AT LEAST 20 FEET AWAY FROM SPRAY AREA. AN
ADDITIONAL LENGTH OF HOSE MAY BE REQUIRED.
i
STORE FLAMMABLE MATERIALS IN A SECURE LOCATION
RESTRICTING ANY OF THE COMPRESSOR VENTILATION
OPENINGS WILL CAUSE SERIOUS OVERHEATING AND
COULD CAUSE FIRE.
AWAY FROM COMPRESSOR.
NEVER PLACE OBJECTS AGAINST OR ON TOP OF COM-
PRESSOR_ OPERATE COMPRESSOR IN AN OPEN AREA AT
LEAST 12 INCHES AWAY FROM ANY WALL OR OBSTRUC-
i I
TION THATIWOULD RESTRICT THE FLOW OF FRESH AIR TO
THE VENTILLATION OPENINGS.
OPERATE I_OMPRESSOR IN A CLEAN, DRY,WELL VENTILATED
AREA. DO NOT OPERATE UNIT INDOORS OR IN ANY
CONFINED AREA.
UNATTENDED OPERATION OF THIS PRODUCT COULD ALWAYS REMAIN IN ATTENDANCE WITH THE PRODUCT
RESULT IN PERSONAL INJURY OR PROPERTY DAMAGE. WHEN IT .1_OPERATING,
RISK OF BURSTING I_1
_: THE FOLLOWING CONDITIONS COULD LEAD TO A WEAKEiNING OF THE TANK, AND RESULT IN A ..........
VIOLENT TANK EXPLOSION AND COULD CAUSE PROPERTY DAMAGE OR SERIOUS INJURY.
WHAT CAN HAPPEN
f. FAILURE TO PROPERLY DRAIN CONDENSED WATER
FROM THE TANK, CAUSING RUST AND THINNING OF THE
STEEL TANK.
2. MODIFICATIONS OR ATTEMPTED REPAIRS TO THE TANK.
3. UNAUTHORIZED MODIFICATIONS TO THE UNLOADER
VALVE, SAFETY VALVE, OR ANY OTHER COMPONENTS
WHICH CONTROL TANK PRESSURE.
4. EXCESSIVE VIBRATION CAN WEAKEN THE AIR TANK AND
CAUSE RUPTURE OR EXPLOSION.
ATTACHME_NTS & ACCESSORIES;
EXCEEDING THE PRESSURE RATING OF AIR TOOLS, SPRAY
GUNS, AIR OPERATED ACCESSORtES, TtRES AND OTHER
INFLATABLES CAN CAUSE THEM TO EXPLODE OR FLY
APART, AND COULD RESULT IN SERIOUS INJURY.
I Ilil
DRAIN TANK DALLY OR AFTER EACH USE. IF TANK DEVELOPS
HOW TO PREVENT IT
i
A LEAK REPLACE IT IMMEDIATELY WITH A NEW TANK OR
REPLACE THE ENTIRE COMPRESSOR.
NEVER DRILL INTO, WELD, OR MAKE ANY MODIFICATIONS-TO
THE TANK OR ITS A]-FACHMENTS.
THE TANK IS:DESIGNED TO WITHSTAND SPECIFIC OPEBATtNG
PRESSURe. NEVER MAKE ADJUSTMENTS OR PARTS
SUBSTITUT!ONS TO ALTER THE FACTORY SET OPERATING--
PRESSURES_
FOR ESSENTIAL CONTROL OF AIR PRESSURE, YOU MUST
LOW-PRI :H AS CHILDREN'S TOYS,
BASKETBALLS. ETC.
IEGULATOR AND PRESSURE GAUGE
YOUR COMPRESSOR. FOLLOW THE
_ECOMMENDATION AND NEVER
USE COMPRESSOR TO INFLATE SMALL
BLE PRESSURE RATING OF
J
3-ENG D20437 Rev. 0 2/15/00
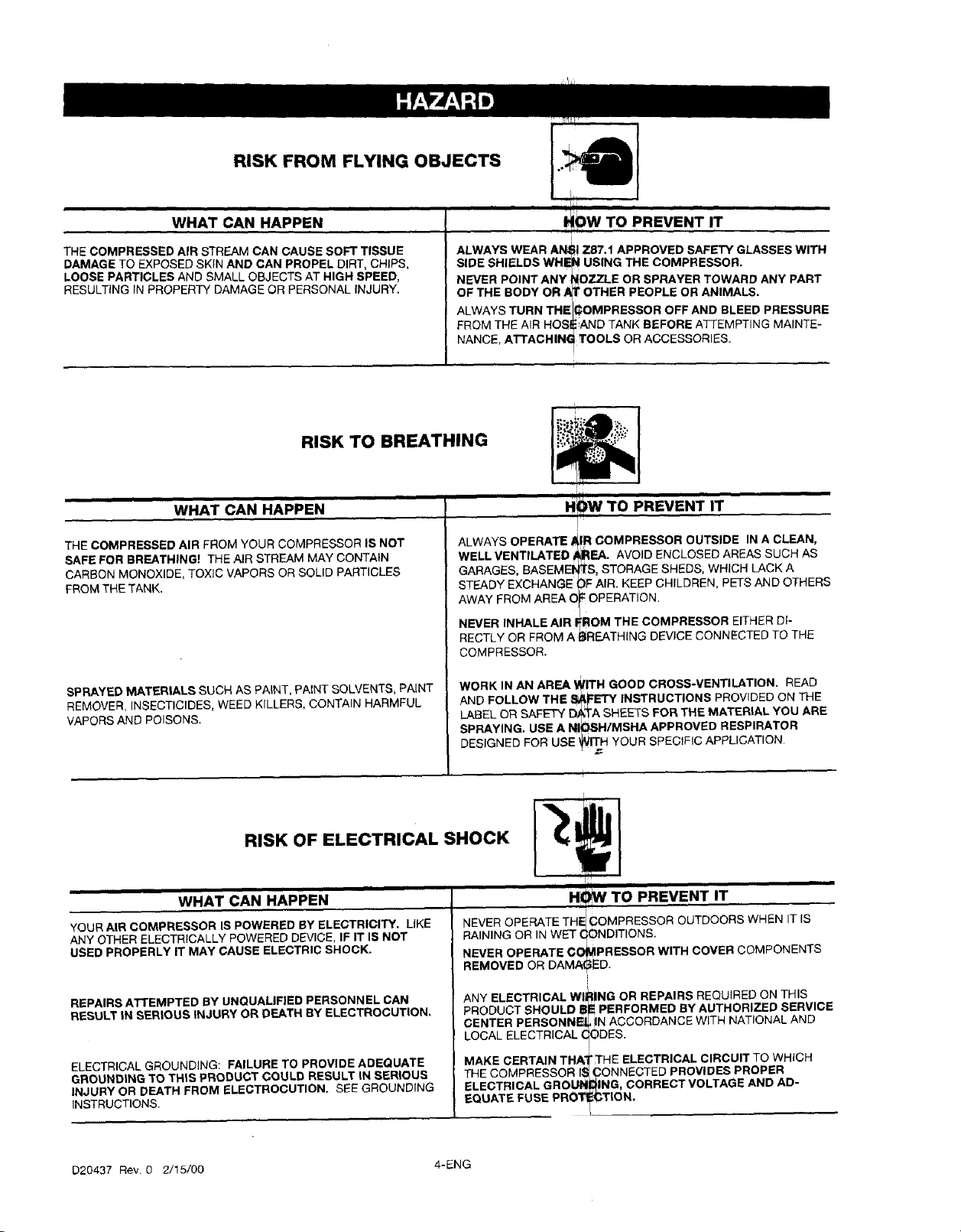
RISK FROM FLYING OBJECTS
llllllllU
WHAT CAN HAPPEN
THE COMPRESSED AIR STREAM CAN CAUSE SOFT TISSUE
DAMAGE TO EXPOSED SKIN AND CAN PROPEL DIRT, CHIPS,
LOOSE PARTICLES AND SMALL OBJECTS AT HIGH SPEED,
RESULTING IN PROPERTY DAMAGE OR PERSONAL INJURY.
RISK TO BREATHING
I..............
I
ALWAYS WEAR ANS! 7.87.1 APPROVED SAFETY GLASSES WITH
SIDE SHIELDS WHEN USING THE COMPRESSOR.
NEVER POINT ANY _OZZLE OR SPRAYER TOWARD ANY PART
OF THE BODY OR _ OTHER PEOPLE OR ANIMALS.
ALWAYS TURN THE COMPRESSOR OFF AND BLEED PRESSURE
FROM THE AIR HOSI_;AND TANK BEFORE ATTEMPTING MAINTE-
NANCE, ATI'ACHIN_TOOLS OR ACCESSORIES.
i,
WHAT CAN HAPPEN
THE COMPRESSED AIR FROM YOUR COMPRESSOR IS NOT
SAFE FOR BREATHING! THE _JR STREAM MAY CONTAIN
CARBON MONOXIDE, TOXIC VAPORS OR SOLID PARTICLES
FROM THE TANK.
SPRAYED MATERIALS SUCH AS PAINT, PAINT SOLVENTS, PAINT
REMOVER, INSECTICIDES, WEED KILLERS, CONTAIN HARMFUL
VAPORS AND POISONS.
RISK OF ELECTRICAL SHOCK
WHATCAN HAPPEN
YOUR AIR COMPRESSOR IS POWERED BY ELECTRICITY. LIKE
ANY OTHER ELECTRtCALLY POWERED DEVICE, IF IT IS NOT
USED PROPERLY IT MAY CAUSE ELECTRIC SHOCK.
REPAIRS ATTEMPTED BY UNQUALIFIED PERSONNEL CAN
RESULT IN SERIOUS INJURY OR DEATH BY ELECTROCUTION,
ELECTRICAL GROUNDING: FAILURE TO PROVIDE ADEQUATE
GROUNDING TO THIS PRODUCT COULD RESULT IN SERIOUS
INJURY OR DEATH FROM ELECTROCUTION, SEE GROUNDING
INSTRUCTIONS.
H T PREVENT IT
ALWAYS OPERATE J,IR COMPRESSOR OUTSIDE IN A CLEAN,
WELL VENTILATED i _EA. AVOID ENCLOSED AREAS SUCH AS
GARAGES, BASEMEr I_S, STORAGE SHEDS, WHICH LACK A
STEADY EXCHANGE :)F AIR. KEEP CHILDREN, PETS AND OTHERS
AWAY FROM AREA CF OPERATION.
NEVER INHALE AIR I_ROM THE COMPRESSOR EITHER DI-
RECTLY OR FROM A_REATHING DEVICE CONNECTED TO THE
COMPRESSOR.
WORK IN AN AREA WtTH GOOD CROSS-VENTILATION. READ
AND FOLLOW THE_FETY INSTRUCTIONS PROVIDED ON THE
LABEL OR SAFETY I:_TA SHEETS FOR THE MATERIAL YOU ARE
SPRAYING. USE A NI_OSH/MSHA APPROVED RESPIRATOR
DESIGNED FOR USE WIT=HYOUR SPECIFIC APPLICATION.
NEVER OPERATE THE]COMPRESSOR OUTDOORS WHEN IT IS
RAINING OR IN WET _ONDITIONS.
NEVER OPERATE COMPRESSOR WITH COVER COMPONENTS
REMOVED OR DAMA(_ED.
ANY ELECTRICAL WIRING OR REPAIRS REQUIRED ON THIS
PRODUCT SHOULD BE PERFORMED BY AUTHORIZED SERVICE
CENTER PERSONNE_ IN ACCORDANCE WITH NATIONAL AND
LOCAL ELECTRICAL qODES.
MAKE CERTAIN THAT THE ELECTRICAL CIRCUIT TO WHICH
THE COMPRESSOR IS[CONNECTED PROVIDES PROPER
ELECTRICAL GROUNDING, CORRECT VOLTAGE AND AD-
EQUATE FUSE PROTI_CTION.
/
lU
H
,,,WTO PREVENT IT
D20437 Rev. 0 2/15/00 4-ENG
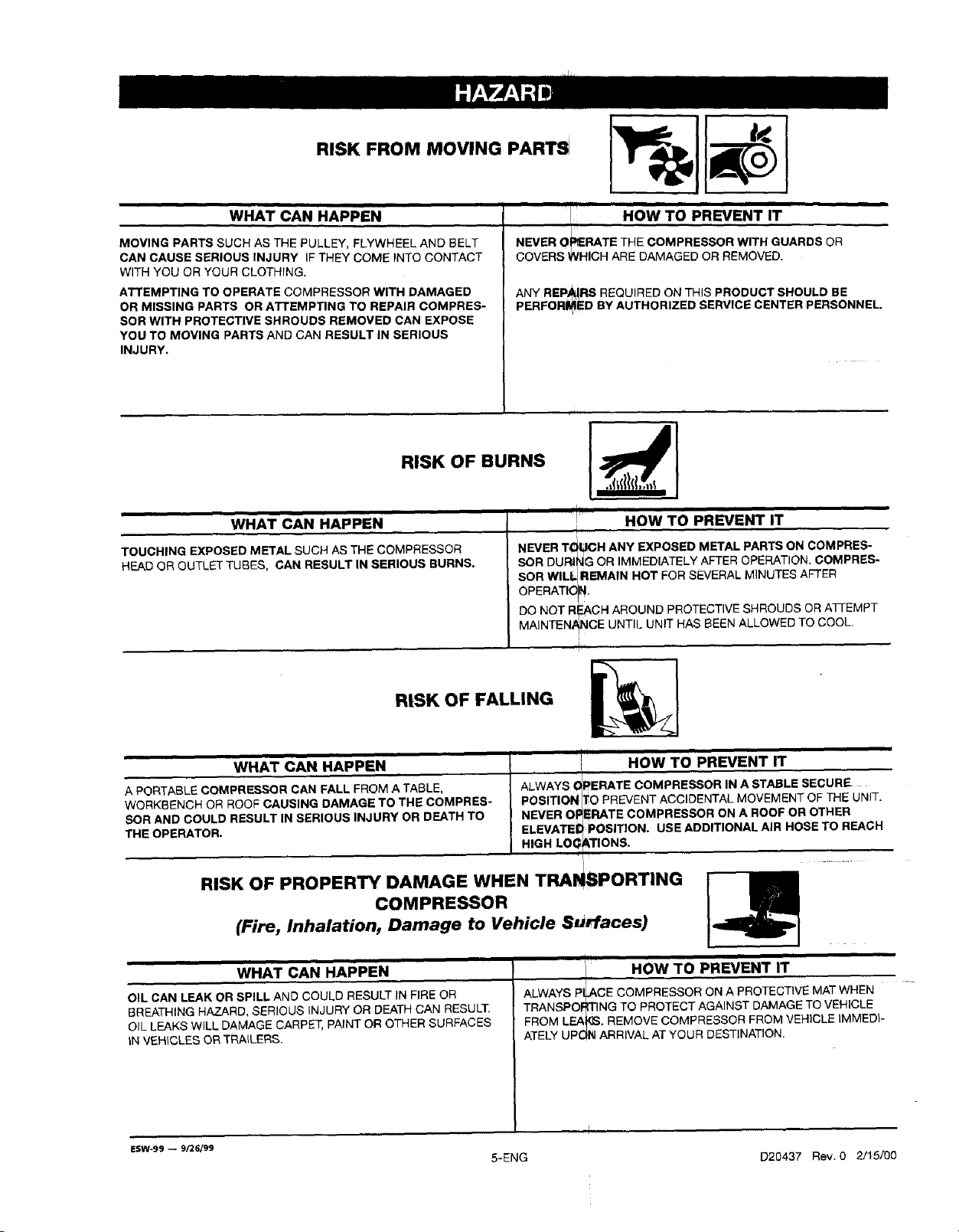
RISK FROM MOVING PARTSi
WHAT CAN HAPPEN
MOVING PARTS SUCH AS THE PULLEY, FLYWHEEL AND BELT
CAN CAUSE SERIOUS INJURY IF THEY COME INTO CONTACT
WITH YOU OR YOUR CLOTHING.
ATTEMPTING TO OPERATE COMPRESSOR WITH DAMAGED
OR MISSING PARTS OR ATTEMPTING TO REPAIR COMPRES-
SOR WITH PROTECTIVE SHROUDS REMOVED CAN EXPOSE
YOU TO MOVING PARTS AND CAN RESULT IN SERIOUS
INJURY.
RISK OF BURNS
WHAT CAN HAPPEN
TOUCHING EXPOSED METAL SUCH AS THE COMPRESSOR
HEAD OR OUTLET TUBES, CAN RESULT IN SERIOUS BURNS.
"1' HOW TO PREVENT IT
NEVER O_ERATE THE COMPRESSOR WITH GUARDS OR
COVERS WHICH ARE DAMAGED OR REMOVED.
ANY REPineRS REQUIRED ON THIS PRODUCT SHOULD BE
PERFORMED BY AUTHORIZED SERVICE CENTER PERSONNEL.
i Jill i illllll I
NEVER T_UCH ANY EXPOSED METAL PARTS ON COMPRES-
SOR DURING OR IMMEDIATELY AFTER OPERATION. COMPRES-
SOR WILLIREMAIN HOT FOR SEVERAL MINUTES AFTER
OPERATIO_I.
DO NOT R_ACH AROUND PROTECTIVE SHROUDS OR ATi'EMPT
MAINTEN/_NCE UNTIL UNIT HAS BEEN ALLOWED TO COOL.
,I
HOW TO PREVENT IT
RiSK OF FALLING
WHAT ....
A PORTABLE COMPRESSOR CAN FALL FROM A TABLE,
WORKBENCH OR ROOF CAUSING DAMAGE TO THE COMPRES-
SOR AND COULD RESULT IN SERIOUS INJURY OR DEATH TO
THE OPERATOR.
RISK OF PROPERTY DAMAGE WHEN TRANSPORTING
(Fire, Inhalation, Damage to Vehicle Surfaces)
WHAT CAN HAPPEN
OIL CAN LEAK OR SPILL AND COULD RESULT IN FIRE OR
BREATHING HAZARD, SERIOUS INJURY OR DEATH CAN RESULT.
OIL LEAKS WILL DAMAGE CARPET, PAINT OR OTHER SURFACES
iN VEHICLES OR TRAILERS.
ESW-99 _ 9/26/99
CAN HAPPEN
COMPRESSOR
,,,,,,,,,,,,,,,, ,IIIlU
'" JI ! '
ALWAYS (_PERATE COMPRESSOR IN A STABLE SECURE .....
POSITION _ro PREVENT ACCIDENTAL MOVEMENT OF THE UNIT.
NEVER OI_ERATE COMPRESSOR ON A ROOF OR OTHER
ELEVATEI_ POSITION. USE ADDITIONAL AIR HOSE TO REACH
HIGH LOC_TIONS.
' HOW TO PREVENT IT
I ..........
I' HOW TO PREVENT IT
ALWAYS PI_ACE COMPRESSOR ON A PROTECTIVE MAT WHEN ....
TRANSPOF_TING TO PROTECT AGAINST DAMAGE TO VEHICLE
FROM LEA_S. REMOVE COMPRESSOR FROM VEHICLE IMMEDi-
ATELY UPON ARRIVAL AT YOUR DESTINATION.
,,I,p
5-ENG D20437 Rev. 0 2/15/00

Refer to Outfit Parts Bulletin for the specifications of your compressor, a fuse or circuit breaker that is
the same rating as the branch circuit the air compressor is operated on. If e compressor is connected to a
circuit protected by fuses, use dual element time delay fuses, as noted bulletin.
Note
Each air compressor outfit is carefully checked before shipment. With imprc_perhandling, damage may result in
transit and cause problems in compressor operation.
Immediately upon arrival, check equipment for both 2.
concealed and visible damages to avoid expenses
being incurred to correct such problems. This should
be done regardless of any visible signs of damage to
the shipping container. Report any damages to carrier
and arrange for inspection of goods immediately. 3.
1. Check for damaged belt guard. 4.
You have purchased a complete compressor outfit
consisting of an air compressor, air tank, electric
motor, and associated controls and instruments. The
outfit you have selected is a stationary model and
contains either a single stage or two stage air com-
pressor pump.
Your new compressor outfit can be used for operating
paint sprayers, air tools, grease guns, air brushes,
caulking guns, sandblasters, inflating tires, etc.
An air pressure regulator is usually necessary for most
applications. An air line filter is normally required for
removal of moisture and oil vapor in compressed air
when a paint spray gun is used.
If belt guardior drive shows damage, remove
guard and tqrn the flywheel by hand to ensure
crankshaft h_s not been bent in shipping and that
the belt driv4_is properly aligned and free of any
distortion.
Check for d_maged air tank and attached legs.
Inspect compressor outfit for possible damaged
or missing c_mponents.
An in-line lubric_ Jris often required for air tools to
prolong tool life.
Separate air transformers which combine the func-
tions of air regulaJttonand/or moisture and dirt removal
should be used --_hereapplicable.
A regularly sched
nance will help pl
designed into yot
ing or performing
sor, refer to this r
To keep your co_
to these publicati
maintenance ste
Jled program of preventive mainte-
_vide the long life that has been
I_rcompressor outfit. Before operat-
any maintenance on your compres-
lanual and your Outfit Parts Bulletin.
_pressor in good working order, refer
3ns often and perform preventive
_$as recommended.
D20437 Rev. 0 2/15/00 6-ENG

CFM: Cubic feet per minute.
SGFM: Standard cubic feet per minute; a unit of
measure of air delivery.
PSIG: Pounds per square inch gauge; a unit of
measure of pressure.
ASME: American Society of Mechanical Engineers;
made, tested, inspected and registered to meet the
standards of the ASME.
Cut-In Pressure: While the motor is off, air tank
pressure drops as you continue to use your acces-
sory.
When pressure drops to a certain low level
will restart automatically. The low pressure
at 1the motor automatically re-starts is called
"cut- i pressure."
Cut-O_ Pressure: When you turn on your air com-
presso iand itbegins to run, air pressure in the air
tank be
sure be
tecting
capac_
off is
To Lo<
switch
ginsto build, it builds to a certain high pres-"
fore the motor automatically shuts off - pro-
your air tank from pressure higher than its
y. The high pressure at which the motor shuts
died "cut-out pressure."
k Out Power: Place a lock on the line power
no no one else can turn on the power.
Drain Valve: At the base of the air tank to drain
condensation at the end of each u_e.
Motor Thermal Overload Protector: The electric
motor has an automatic thermal overload protector. If
the motor overheats for any reason, the thermal
overload protector will shut off the motor. The motor
must be allowed to cool down before restarting.
ON/AUTO-OFF Switch: Turn this switch ON to
provide automatic power to the pressure switch and
OFF to remove power.
Air Intake Filter: This filter is designed to clean air
coming into the pump. This filter must always be clean
and ventilation openings free from obstructions. See
"Maintenance".
Air Compressor Pump: To compress air, the piston
moves up and down in the cylinder. On the down-
stroke, air is drawn in through the air intake valves.
The exhaust valve remains closed. On the upstroke of
the piston, air iscompressed. The intake valves close
and compressed air is forced out through the exhaust
valve, through the outlet tube, through the check valve
and into the air tank. Working air is not available until
the compressor has raised the air tank pressure above
that required at the air outlet.
In two stage compressors, air is first compressed to
an intermediate pressure in the large bore cylinder,
and after passing through an inter-cooler, the air is
further compressed to a higher pressure in the smaller
bore cylinder. This process continues until the air tank
pressure reaches the factory set cutoff pressure. At
that point the pressure switch shuts the electric motor
off.
Check Valve: When the air compressor is operating,
the check valve is "open", allowing compressed air to
enter the air tank. When the air compressor reaches
"cut-out" pressure, the check valve "closes", allowing
air pressure to remain inside the air tank.
iRelease Valve: The pressure release valve
located
to
COrn
comprel
If the air
will be
the mot_
runningi
few sec(
the mote
Pressur
starts th,
below th
motor w
set "cut-
Shut-off
the side of the pressure switch, is designed
' release compressed air from the
sor head and the outlet tube when the air
isor reaches "cut-out" pressure or is shut off.
is not released, the motor will try to start, but
rlable to. The pressure release valve allows
r to restart freely. When the motor stops
air will be heard escaping from the valve for a
nds. No air should be heard leaking when
r is running.
Switch: The pressure switch automatically
i motor when the air tank pressure drops
factory set "cut-in" pressure, It stops the
_n the air tank pressure reaches the factory
_ut" pressure.
Valve: Turn the knob counterclockwise to
open the valve and clockwise to close.
Air Tanl_ Safety Valve: If the pressure switch does
not shut Joffthe air compressor at its cut-out pressure
setting, t_le safety valve will protect against high
pressure by "popping off" at its factory set pressure
(slightly I_igher than the pressure switch cut-out
setting)_
Aftercoctler Safety Valve: On two stage compressor
units, safety valve is provided to prevent over-pres-
surization1of the aftercoole_; The valve will protect the
affercool_r by popping off at its factory set pressure.
Regulalx ur. An air pressure regulator or a separate air
transforn ler which combines the functions of air
regulatio 1and/or moisture and dirt removal is required
for most _pplications.
Tank Prl_$sure Gauge: The tank pressure gauge
indicate= the reserve air pressure in the tank. On
outfits w I_hno pressure regulator, this isalso the
pressure available at the air outlet.
7qENG D20437 Rev. 0 2/15/00

Location of the Air Compressor
Air Compr_
_sor Anchoring Methods
THE MANIFOLD ASSEMBLY DOES NOT
PROVIDE ADEQUATE STABILITY OR
SUPPORT FOR LIFTING THE UNIT. IF THE
OUTFIT MUST BE MOVED, USE THE TANK
FOR LIFTING.
This compressor should be permanently mounted in
place on a level floor. Operate the air compressor in a
clean, dry and well ventilated area. The air intake filter
must be kept clear of obstructions which could
reduce air delivery of the air compressor. The air
compressor should be located at least 12" away from
walls or other obstructions that could interfere with
the flow of air through the fan bladed flywheel. The air
compressor crankcase and head are designed with
fins to provide proper cooling.
The flywheel side of the outfit should be placed
toward the wall and protected with a totally enclosed
belt guard. In no case should the flywheel be closer
than 12 to 18 inches from the.wall or other obstruction
that will interfere with the flow of air through the fan
bladed flywheel. The area should allow space on all
sides for air circulation and for ease of normal mainte-
nance. Keep the outfit away from areas which have
dirt, vapor and volatile fumes in the atmosphere which
may clog and gum the intake filter and valves, causing
inefficient operation. Where this is not practical a
remote air intake is recommended.
Note
Where a remote air intake is used, enlarge the
size of the air intake piping by one pipe size
for each 10 feet of length.
If humidity is high, an air filter can be installed to remove
excessive moisture. Closely follow instructions pack-
aged with the filter for proper installation. It must be
installedas close as possible to the accessory.
VIBRATIC
TANK ANI
COMPRE_
MOUNTEI
Vertical Units
CAN WEAKEN THE AIR
3AUSE AN EXPLOSION. THE
OR MUST BE PROPERLY
kS ILLUSTRATED BELOW.
i
Vertical air com_essors must be bolted to the
floor. Bolting hollies are provided in the base feet.
Mount the air cqmpressor on a solid, level founda-
tion. Support c4mpressor weight evenly on a four
feet. Solid shims may be used if necessary.
• Lig $cralw
{nol sullied)
Torque to S-7 FLLb,
j Lag Scrow Ancho_ for ¢oncmtl
i (not =upplied)
Anchoring of Vertical Unit
Horizontal Un_
Some tank mour'ted compressor outfits are
shipped with (4) _bber isolator pads. When install-
ing compressor I
pad is to be pla¢
be smooth and li
square on all fou
supporL compre_
The horizontal ty
be bolted or lag{
'1Ltsworking location, one isolator
dunder each foot. The floor must
1el.The compressor should sit
feet. Install shims as needed to
;Sorweight evenly on all four feet.
_e compressor is not required to
ed to the floor.
The air compressor should be as near to air outlets as
possible in order to avoid long pipe lines. Do not place the
air compressor where heat is excessive.
D20437 Rev. 0 2/15/00 8-ENG
(not supplied)
To_'que',o_T FLLa.