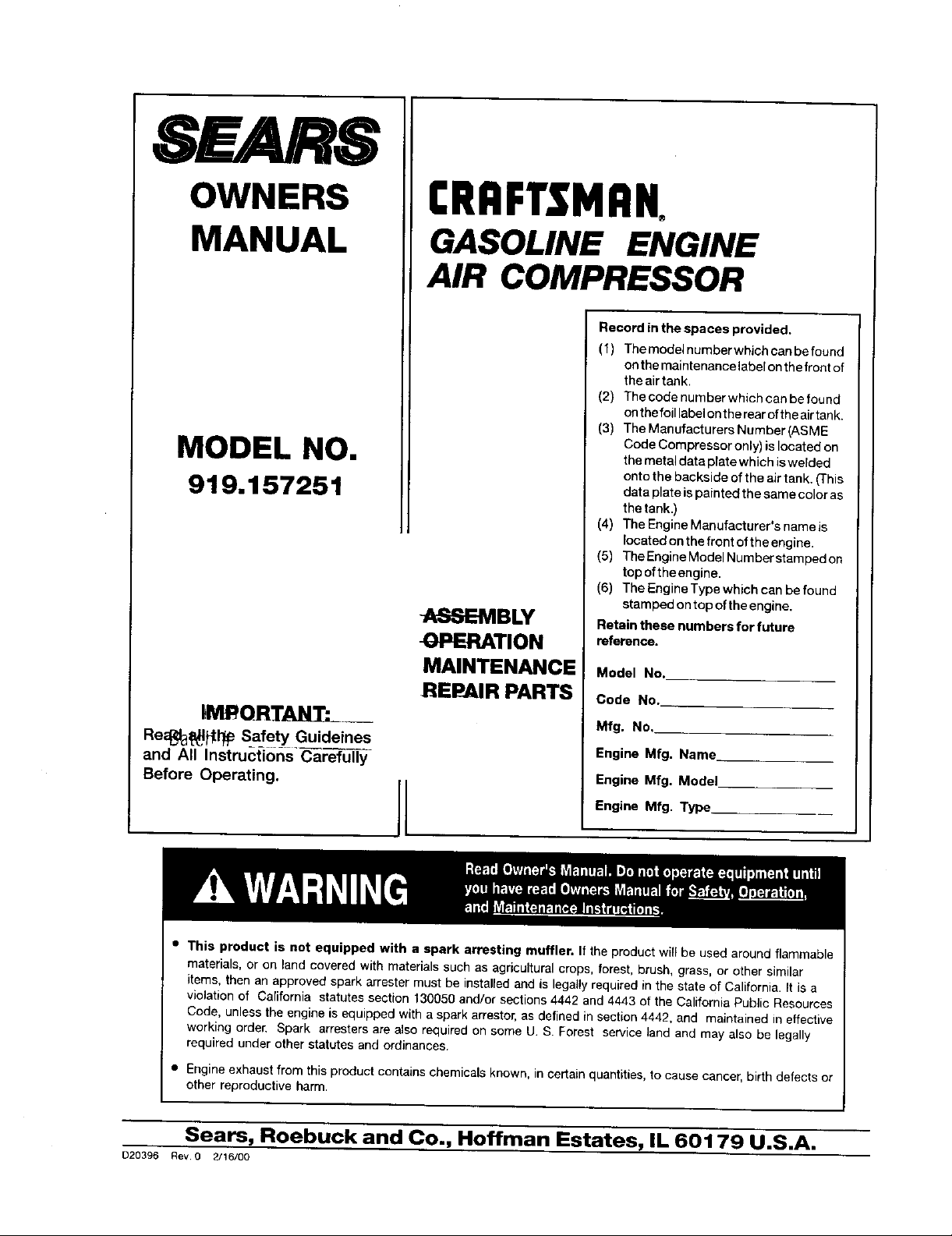
SEAR8
OWNERS
MANUAL
MODEL NO.
919.157251
|MI_ORTAN_:___
Re_l-_e Safety Guideines
and All Instructions Carefully
Before Operating.
CRRFTSMRN,
GASOLINE ENGINE
AIR COMPRESSOR
Record in the spaces provided.
(1) The model number which can be found
on the maintenance label onthe front of
the airtank.
(2) The cede number which can be found
onthefoil labelonthe rear of the airtank.
(3) The Manufacturers Number {ASME
Code Compressor only) is located on
the meta_data plate which iswelded
onto the backside of the air tank. (This
data plate ispainted the same color as
thetank.)
(4) The Engine Manufacturer's name is
located onthe frontofthe engine.
(5) The EngineModel Number stamped on
top oftheengine.
(6) The EngineType which can befound
ASSEMBLY
OPERATION
MAINTENANCE
REPAIR PARTS
stamped on top of the engine.
Retain these numbers for future
reference.
Model No.
Code No.
Mfg. No,
Engine Mfg. Name
Engine Mfg. Model
Engine Mfg, Type
II
• This product Is not equipped with a spark erresUlng muffler. If the product will be used around flammable
materials, or on land covered with materials such as agricultural crops, forest, brush, grass, or other similar
items, then an approved spark arrestor must be installed and is legally required in the state of California. It is a
violation of California statutes section 130050 and/or sections 4442 and 4443 of the California Public Resources
Code, unless the engine is equipped with a spark arrestor, as defined in section 4442, and maintained in effective
working order. Spark arrestors are also required on some U, S. Forest service land and may also be legally
required under other statutes and ordinances.
• Engine exhaust from this product contains chemicals known, in certain quantities, to cause cancer, birth defects or
other reproductive harm.
Sears, Roebuck and Co., Hoffman Estates, IL 60179 U.S.A.
D20396 Rev, 0 2/16/00
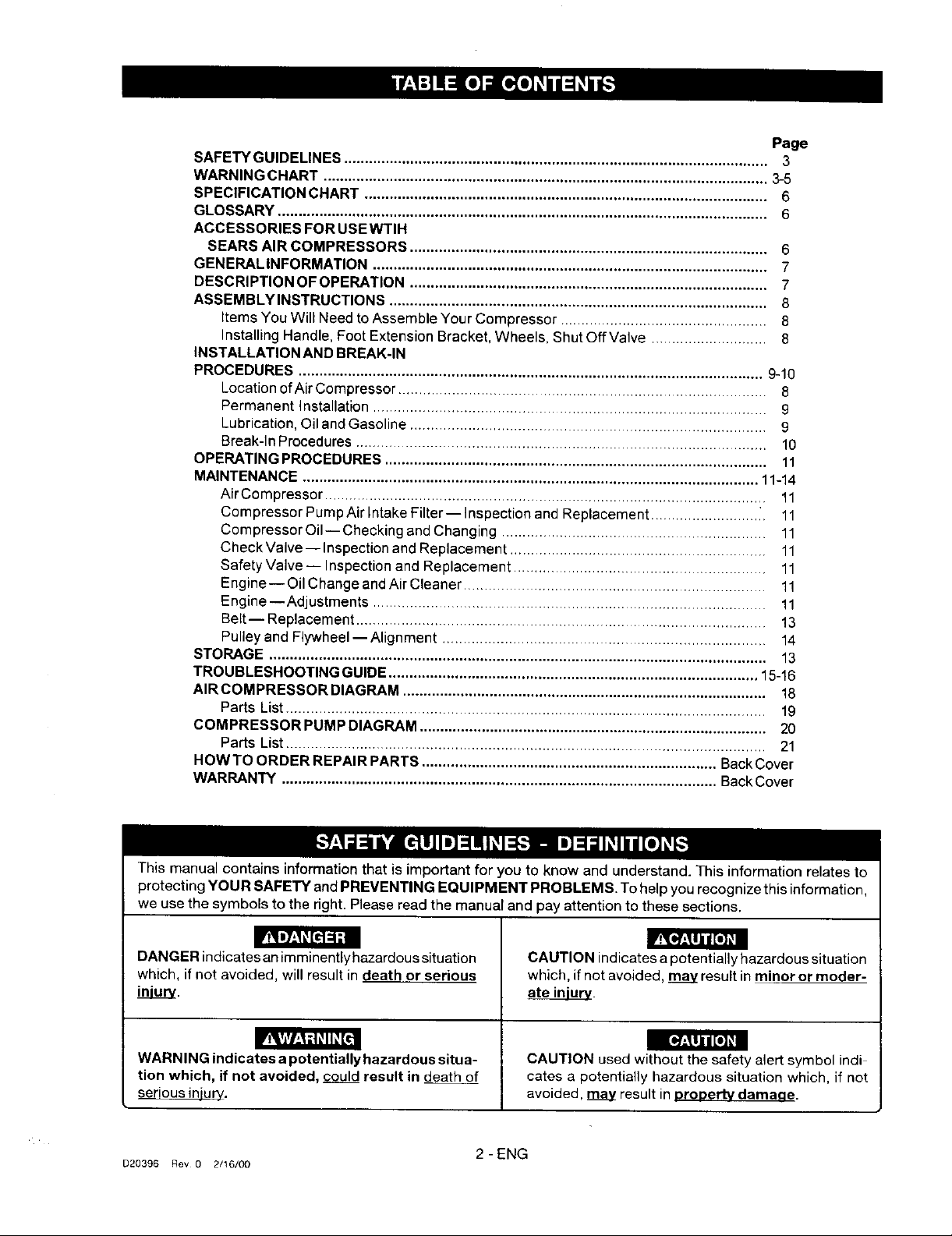
Page
SAFETY GUIDELINES ...................................................................................................... 3
WARNING CHART ........................................................................................................... 3-5
SPECIFICATION CHART ................................................................................................. 6
GLOSSARY ...................................................................................................................... 6
ACCESSORIES FOR USE WTIH
SEARS AIR COMPRESSORS ...................................................................................... 6
GENERALINFORMATION ............................................................................................... 7
DESCRIPTION OF OPERATION ...................................................................................... 7
ASSEMBLYINSTRUCTIONS ........................................................................................... 8
Items You Will Need to Assemble Your Compressor .................................................. 8
Installing Handle, Foot Extension Bracket, Wheels, Shut Off Valve ............................ 8
INSTALLATION AND BREAK-IN
PROCEDURES ................................................................................................................ 9-10
Location of Air Compressor ........................................................................................ 8
Permanent Installation
............................................................................................... g
Lubrication, Oil and Gasoline ...................................................................................... 9
Break-In Procedures ................................................................................................... 10
OPERATING PROCEDURES ............................................................................................ 11
MAINTENANCE .............................................................................................................. 11-14
AirCompressor ........................................................................................................... 11
Compressor Pump Air Intake Filter-- Inspection and Replacement .......................... i. 11
Compressor Oil-- Checking and Changing ................................................................ 11
Check Valve--Inspection and Replacement .............................................................. 11
Safety Valve -- Inspection and Replacement ............................................................. 11
Engine-- Oil Change and Air Cleaner ......................................................................... 11
Engine--Adjustments ............................................................................................... 11
Belt-- Replacement ................................................................................................... 13
Pulley and Flywheel -- Alignment .............................................................................. 14
STORAGE ........................................................................................................................ 13
TROUBLESHOOTING GUIDE ......................................................................................... 15-16
AIR COMPRESSOR DIAGRAM ........................................................................................ 18
Parts List .................................................................................................................... 19
COMPRESSOR PUMP DIAGRAM .................................................................................... 20
Parts List .................................................................................................................... 21
HOWTO ORDER REPAIR PARTS ....................................................................... Back Cover
WARRANTY ......................................................................................................... BackCover
This manual contains information that is important for you to know and understand. This information relates to
protecting YOUR SAFETY and PREVENTING EQUIPMENT PROBLEMS. To help you recognize this information,
we use the symbols to the right. Please read the manuar and pay attention to these sections.
DANGER indicates an imminently hazardous situation
which, if not avoided, will result in death or serious
iniurv.
WARNING indicates a potentially hazardous situa-
tion which, if not avoided, could result in death of
CAUTION indicates a potentially hazardous situation
which, if not avoided, _ result in minor or moder-
ate in'lUnt.
CAUTION used without the safety alert symbol indi
cates a potentially hazardous situation which, if not
avoided, _ result in i_roDertv damaae.
D20396 Rev 0 2/16/00
2 - ENG
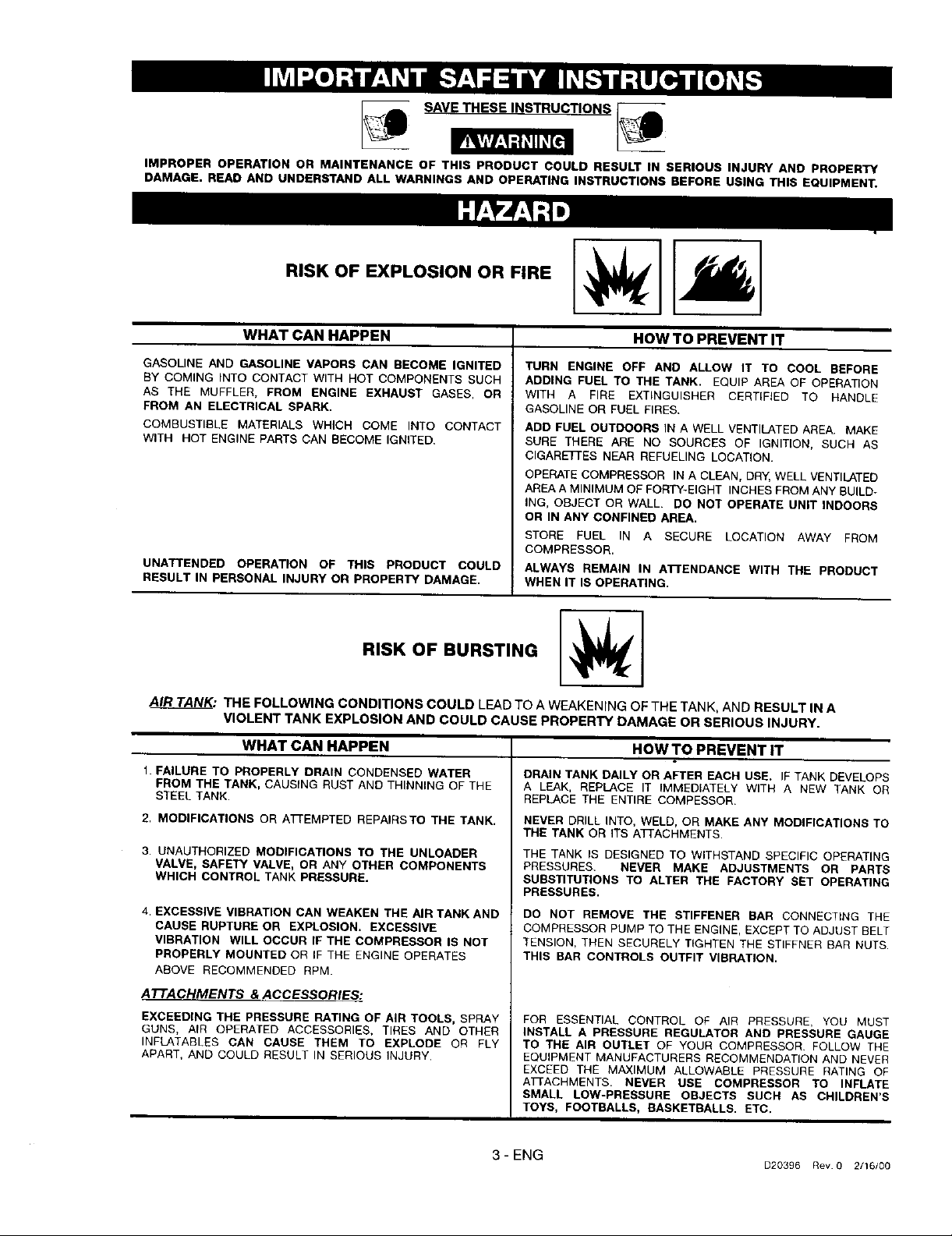
___ SAV_TIONS I_
IMPROPER OPERATION OR MAINTENANCE OF THIS PRODUCT COULD RESULT IN SERIOUS INJURY AND PROPERTY
DAMAGE. READ AND UNDERSTAND ALL WARNINGS AND OPERATING INSTRUCTIONS BEFORE USING THIS EQUIPMENT.
.so°xosoo [ li l
WHAT CAN HAPPEN
GASOLINE AND GASOLINE VAPORS CAN BECOME IGNITED
BY COMING INTO CONTACT WITH HOT COMPONENTS SUCH
AS THE MUFFLER, FROM ENGINE EXHAUST GASES, OR
FROM AN ELECTRICAL SPARK.
COMBUSTIBLE MATERIALS WHICH COME INTO CONTACT
WITH HOT ENGINE PARTS CAN BECOME IGNITED,
UNATTENDED OPERATION OF THIS PRODUCT COULD
RESULT IN PERSONAL iNJURY OR PROPERTY DAMAGE,
TURN ENGINE OFF AND ALLOW IT TO COOL BEFORE
ADDING FUEL TO THE TANK. EQUIP AREA OF OPERATION
WITH A FIRE EXTINGUISHER CERTIFIED TO HANDLE
GASOLINE OR FUEL FIRES,
ADD FUEL OUTDOORS IN A WELL VENTILATED AREA. MAKE
SURE THERE ARE NO SOURCES OF IGNIT[ON, SUCH AS
CIGARE-FrES NEAR REFUELING LOCATION.
OPERATE COMPRESSOR IN A CLEAN, DRY,WELL VENTILATED
AREA A MINIMUM OF FORTY-EIGHT INCHES FROM ANY BUILD-
ING, OBJECT OR WALL. DO NOT OPERATE UNIT INDOORS
OR IN ANY CONFINED AREA.
STORE FUEL IN A SECURE LOCATION AWAY FROM
COMPRESSOR.
ALWAYS REMAIN IN AI-FENDANCE WITH THE PRODUCT
WHEN IT iS OPERA'RNG.
HOW TO PREVENT IT
RISK OF BURSTING I_
IRTA_: THE FOLLOWING CONDITIONS COULD LEADTO AWEAKENING OF THE TANK, AND RESULT IN A
1. FAILURE TO PROPERLY DRAIN CONDENSED WATER
FROM THE TANK, CAUSING RUST AND THINNING OF THE
STEEL TANK.
2. MODIFICATIONS OR A_EMPTED REPAIRSTO THE TANK.
3. UNAUTHORIZED MODIFICATIONS TO THE UNLOADER
VALVE, SAFETY VALVE, OR ANY OTHER COMPONENTS
WHICH CONTROL TANK PRESSURE.
4. EXCESSIVE VIBRATION CAN WEAKEN THE AIR TANK AND
CAUSE RUPTURE OR EXPLOSION. EXCESSIVE
VIBRATION WILL OCCUR IF THE COMPRESSOR IS NOT
PROPERLY MOUNTED OR IF THE ENGINE OPERATES
ABOVE RECOMMENDED RPM.
ATTACHMENTS & ACCESSORIES:
EXCEEDING THE PRESSURE RATING OF AIR TOOLS, SPRAY
GUNS, AIR OPERATED ACCESSORIES, TIRES AND OTHER
INFLATABLES CAN CAUSE THEM TO EXPLODE OR FLY
APART, AND COULD RESULT IN SERIOUS INJURY.
VIOLENT TANK EXPLOSION AND COULD CAUSE PROPERTY DAMAGE OR SERIOUS INJURY.
WHAT CAN HAPPEN
DRAIN TANK DAILY OR AFTER EACH USE, iF TANK DEVELOPS
A LEAK, REPLACE IT IMMEDIATELY WITH A NEW TANK OR
REPLACE THE ENTIRE COMPESSOR
NEVER DRILL INTO, WELD, OR MAKE ANY MODIFICATIONS TO
THE TANK OR ITS AT[AGHMENTS.
THE TANK IS DESIGNED TO WITHSTAND SPECIFIC OPERATING
PRESSURES. NEVER MAKE ADJUSTMENTS OR PARTS
SUBSTITUTIONS TO ALTER THE FACTORY SET OPERA_NG
PRESSURES.
DO NOT REMOVE THE STIFFENER BAR CONNECTING THE
COMPRESSOR PUMP TO THE ENGINE, EXCEPT TO ADJUST BELT
TENSION, THEN SECURELY TIGHTEN THE STIFFNER BAR NUTS.
THIS BAR CONTROLS OUTFIT VIBRATION.
FOR ESSENTIAL CONTROL OF AIR PRESSURE, YOU MUST
INSTALL A PRESSURE REGULATOR AND PRESSURE GAUGE
TO THE AIR OUTLET OF YOUR COMPRESSOR FOLLOW THE
EQUIPMENT MANUFACTURERS RECOMMENDATION AND NEVER
EXCEED THE MAXIMUM ALLOWABLE PRESSURE RATING OF
A_rACHMENTS. NEVER USE COMPRESSOR TO INFLATE
SMALL LOW-PRESSURE OBJECTS SUCH AS CHILDREN'S
TOYS, FOOTBALLS, BASKETBALLS. ETC.
HOW TO PREVENT IT
3 - ENG
D20396 Rev 0 2/16/00
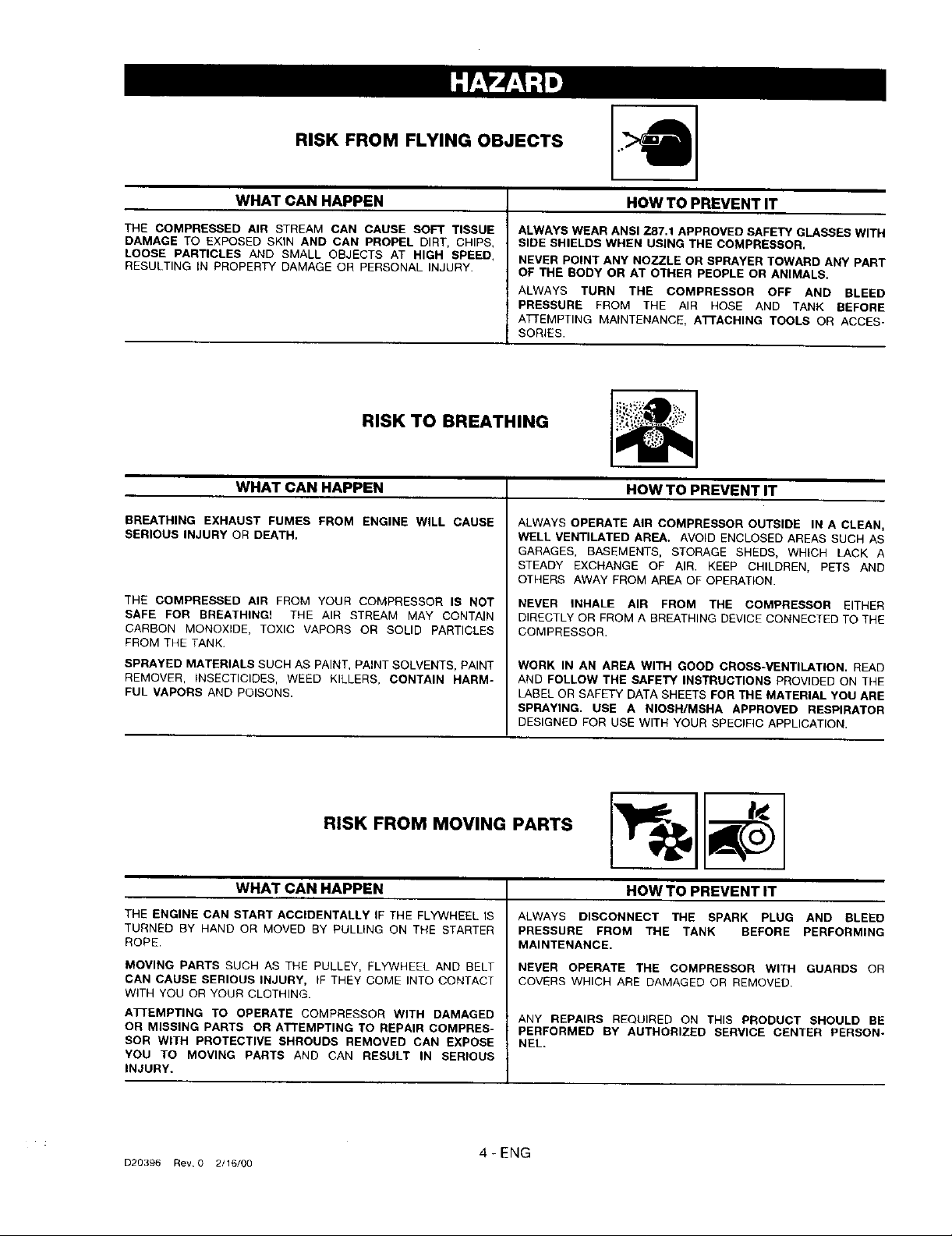
RISK FROM FLYING OBJECTS
WHAT CAN HAPPEN
THE COMPRESSED AIR STREAM CAN CAUSE SOFT TISSUE
DAMAGE TO EXPOSED SKIN AND CAN PROPEL DIRT, CHIPS,
LOOSE PARTICLES AND SMALL OBJECTS AT HIGH SPEED,
RESULTING IN PROPERTY DAMAGE OR PERSONAL INJURY.
RISK TO BREATHING
WHAT CAN HAPPEN
BREATHING EXHAUST FUMES FROM ENGINE WILL CAUSE
SERIOUS INJURY OR DEATH.
THE COMPRESSED AIR FROM YOUR COMPRESSOR IS NOT
SAFE FOR BREATHING! THE AIR STREAM MAY CONTAIN
CARBON MONOXIDE, TOXIC VAPORS OR SOLID PARTICLES
FROM THE TANK.
SPRAYED MATERIALS SUCH AS PAINT, PAINT SOLVENTS, PAINT
REMOVER, INSECTICIDES, WEED KILLERS, CONTAIN HARM-
FUL VAPORS AND POISONS.
HOW TO PREVENT IT
ALWAYS WEAR ANSI Z87.1 APPROVED SAFETY GLASSES WITH
SIDE SHIELDS WHEN USING THE COMPRESSOR.
NEVER POINT ANY NOZZLE OR SPRAYER TOWARD ANY PART
OF THE BODY OR AT OTHER PEOPLE OR ANIMALS.
ALWAYS TURN THE COMPRESSOR OFF AND BLEED
PRESSURE FROM THE AIR HOSE AND TANK BEFORE
ATTEMPTING MAINTENANCE, ATTACHING TOOLS OR ACCES-
SORIES.
HOW TO PREVENT IT
ALWAYS OPERATE AIR COMPRESSOR OUTSIDE IN A CLEAN,
WELL VENTILATED AREA. AVOID ENCLOSED AREAS SUCH AS
GARAGES, BASEMENTS, STORAGE SHEDS, WHICH LACK A
STEADY EXCHANGE OF AIR. KEEP CHILDREN, PETS AND
OTHERS AWAY FROM AREA OF OPERATION.
NEVER INHALE AIR FROM THE COMPRESSOR EITHER
DIRECTLY OR FROM A BREATHING DEVICE CONNECTED TO THE
COMPRESSOR.
WORK IN AN AREA WITH GOOD CROSS-VENTILATION. READ
AND FOLLOW THE SAFETY INSTRUCTIONS PROVIDED ON THE
LABEL OR SAFETY DATA SHEETS FOR THE MATERIAL YOU ARE
SPRAYING. USE A NIOSH/MSHA APPROVED RESPIRATOR
DESIGNED FOR USE WITH YOUR SPECIFIC APPLICATION.
RISK FROM MOVING PARTS
WHAT CAN HAPPEN
THE ENGINE CAN START ACCIDENTALLYIF THE FLYWHEELIS
TURNED BY HAND OR MOVED BY PULLING ON THE STARTER
ROPE.
MOVING PARTS SUCH AS THE PULLEY, FLYWHEEL AND BELT
CAN CAUSE SERIOUS INJURY, IF THEY COME INTO CONTACT
WITH YOU OR YOUR CLOTHING
ATTEMPTING TO OPERATE COMPRESSOR WITH DAMAGED
OR MISSING PARTS OR ATTEMPTING TO REPAIR COMPRES-
SOR WITH PROTECTIVE SHROUDS REMOVED CAN EXPOSE
YOU TO MOVING PARTS AND CAN RESULT IN SERIOUS
INJURY.
D203_ Rev 0 2/16/0Q
4-ENG
HOW TO PREVENT IT
ALWAYS DISCONNECT THE SPARK PLUG AND BLEED
PRESSURE FROM THE TANK BEFORE PERFORMING
MAINTENANCE.
NEVER OPERATE THE COMPRESSOR WITH GUARDS OR
COVERS WHICH ARE DAMAGED OR REMOVED
ANY REPAIRS REQUIRED ON THIS PRODUCT SHOULD BE
PERFORMED BY AUTHORIZED SERVICE CENTER PERSON-
NEL.
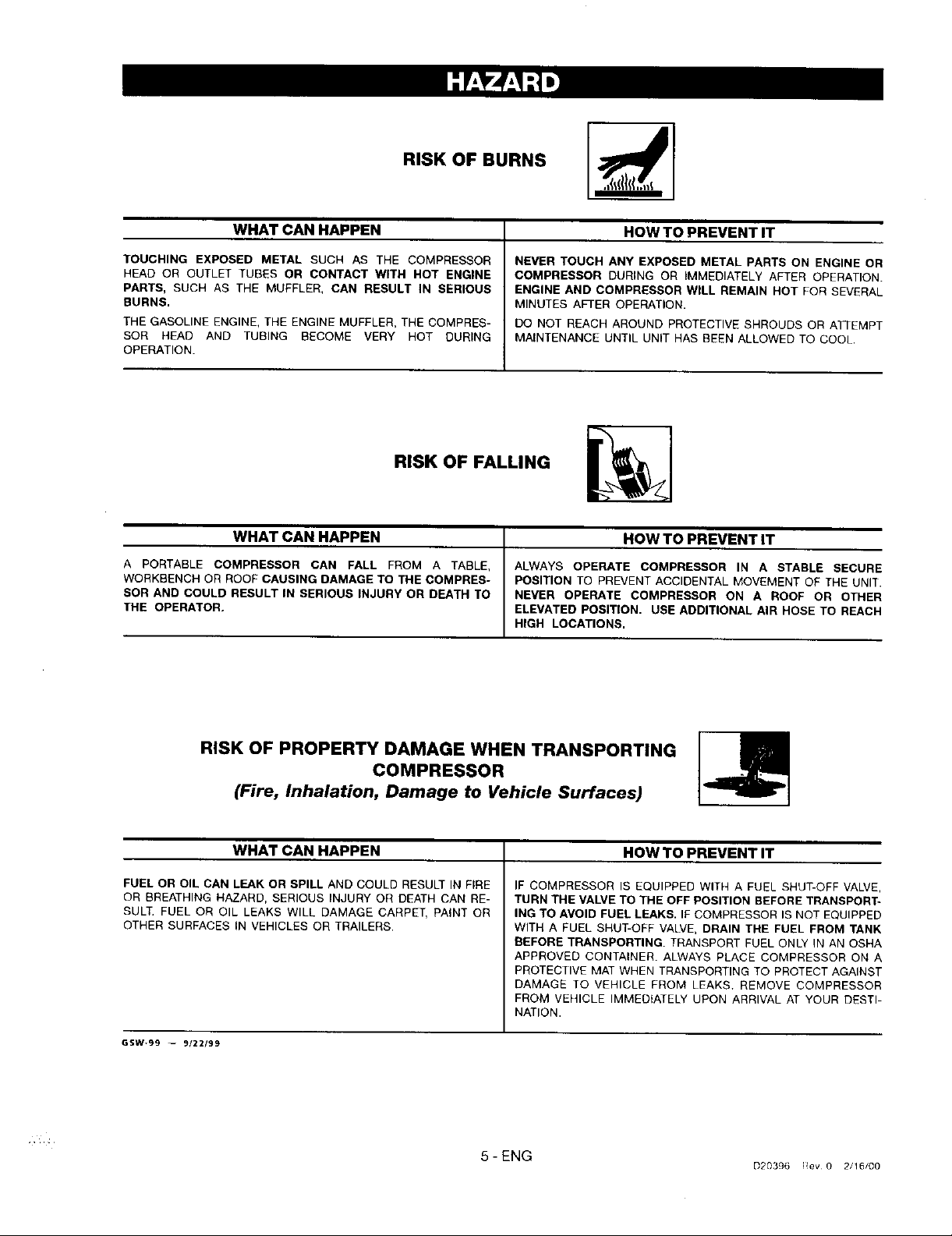
RISK OF BURNS
WHAT CAN HAPPEN
TOUCHING EXPOSED METAL SUCH AS THE COMPRESSOR
HEAD OR OUTLET TUBES OR CONTACT WITH HOT ENGINE
PARTS, SUCH AS THE MUFFLER, CAN RESULT IN SERIOUS
BURNS.
THE GASOLINE ENGINE, THE ENGINE MUFFLER, THE COMPRES-
SOR HEAD AND TUBING BECOME VERY HOT DURING
OPERATION.
RISK OF FALLING
WHAT CAN HAPPEN
A PORTABLE COMPRESSOR CAN FALL FROM A TABLE,
WORKBENCH OR ROOF CAUSING DAMAGE TO THE COMPRES-
SOR AND COULD RESULT IN SERIOUS INJURY OR DEATH TO
THE OPERATOR.
HOW TO PREVENT IT
NEVER TOUCH ANY EXPOSED METAL PARTS ON ENGINE OR
COMPRESSOR DURING OR IMMEDIATELY AFTER OPERATION.
ENGINE AND COMPRESSOR WILL REMAIN HOT FOR SEVERAL
MINUTES AFTER OPERATION.
DO NOT REACH AROUND PROTECTIVE SHROUDS OR ATTEMPT
MAINTENANCE UNTIL UNIT HAS BEEN ALLOWED TO COOL.
HOW TO PREVENT IT
ALWAYS OPERATE COMPRESSOR IN A STABLE SECURE
POSITION TO PREVENT ACCIDENTAL MOVEMENT OF THE UNIT.
NEVER OPERATE COMPRESSOR ON A ROOF OR OTHER
ELEVATED POSITION. USE ADDITIONAL AIR HOSE TO REACH
HIGH LOCATIONS.
RISK OF PROPERTY DAMAGE WHEN TRANSPORTING I n
COMPRESSOR
(Fire, Inhalation, Damage to Vehicle Surfaces)
WHAT CAN HAPPEN
FUEL OR OIL CAN LEAK OR SPILL AND COULD RESULT IN FIRE
OR BREATHING HAZARD, SERIOUS INJURY OR DEATH CAN RE-
SULT. FUEL OR OIL LEAKS WILL DAMAGE CARPET, PAINT OR
OTHER SURFACES IN VEHICLES OR TRAILERS.
GSW.99 -- 9122199
HOWTO PREVENT IT
IF COMPRESSOR IS EQUIPPED WITH A FUEL SHUT-OFF VALVE,
TURN THE VALVE TO THE OFF POSITION BEFORE TRANSPORT-
ING TO AVOID FUEL LEAKS. IF COMPRESSOR IS NOT EQUIPPED
WITH A FUEL SHUT-OFF VALVE, DRAIN THE FUEL FROM TANK
BEFORE TRANSPORTING. TRANSPORT FUEL ONLY IN AN OSHA
APPROVED CONTAINER. ALWAYS PLACE COMPRESSOR ON A
PROTECTIVE MAT WHEN TRANSPORTING TO PROTECT AGAINST
DAMAGE TO VEHICLE FROM LEAKS. REMOVE COMPRESSOR
FROM VEHICLE IMMEDIATELY UPON ARRIVAL AT YOUR DESTI-
NATION.
5 - ENG
D20396 F!ev 0 2/16/00
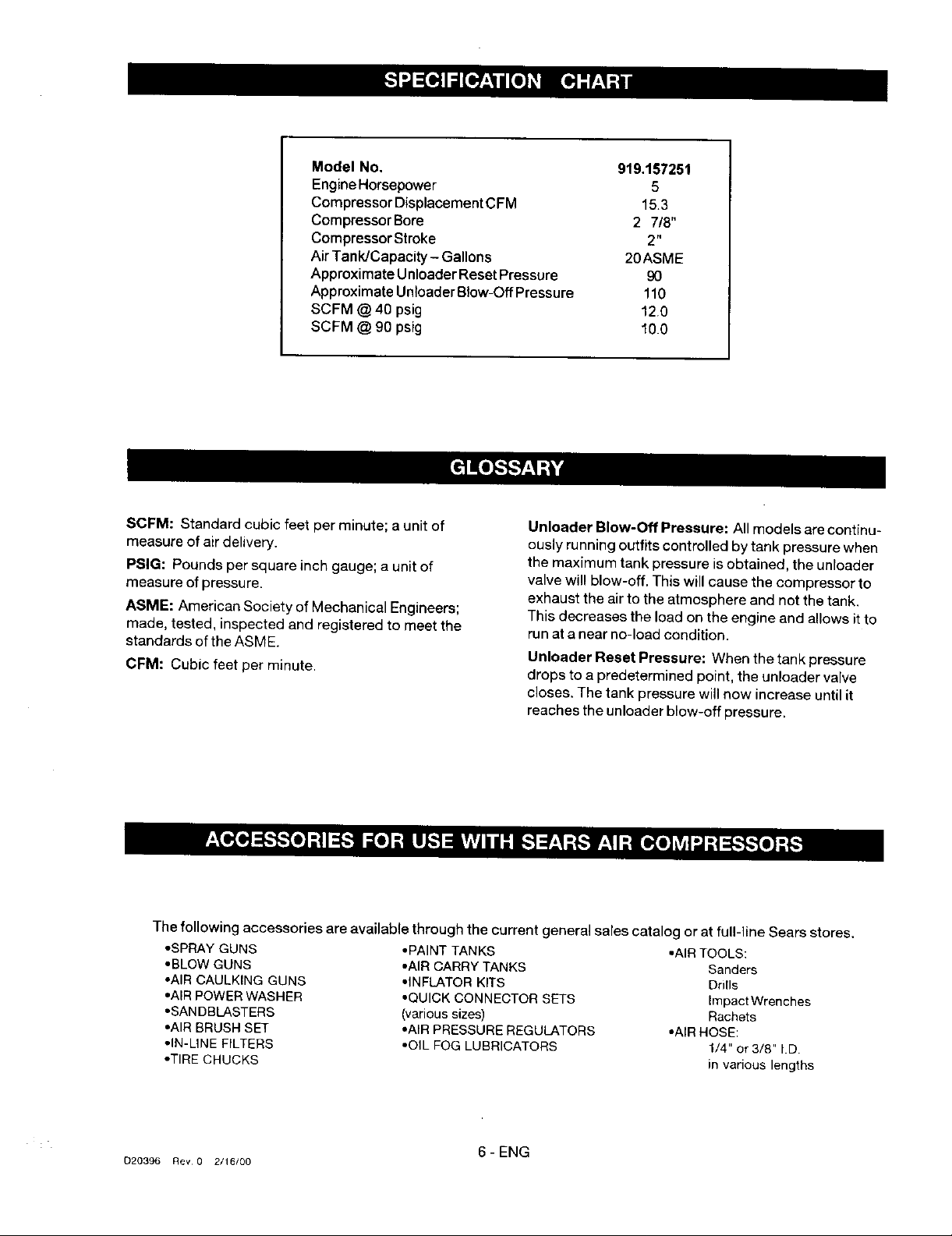
Model No.
Engine Horsepower
Compressor DisplacementCFM
CompressorBore
Compressor Stroke
Air Tank/Capacity- Gallons
Approximate UnloaderReset Pressure
Approximate UnloaderBlow-OffPressure
SCFM @ 40 psig
SCFM @ 90 psig
919.157251
5
15.3
2 7/8"
2"
20ASME
90
110
12.0
10.0
SCFM: Standard cubic feet per minute; aunit of
measure of air delivery.
PSIG: Pounds per square inch gauge; a unitof
measure of pressure.
ASME: American Society of Mechanical Engineers;
made, tested, inspected and registeredto meet the
standardsof theASME.
CFM: Cubic feet per minute.
Unloader Blow-Off Pressure: All models are continu-
ously running outfits controlled by tank pressure when
the maximum tank pressure is obtained, the unloader
valve will blow-off. This will cause the compressor to
exhaust the air to the atmosphere and not the tank.
This decreases the load on the engine and allows it to
run at a near no-load condition.
Unloader Reset Pressure: When the tank pressure
drops to a predetermined point, the unloader valve
closes. The tank pressure will now increase until it
reaches the unloader blow-off pressure.
The following accessories are available through the current general sales catalog or at full-line Sears stores,
• SPRAY GUNS
• BLOW GUNS
• AIR CAULKING GUNS
eAIR POWER WASHER
"SANDBLASTERS
• AIR BRUSH SET
oIN-LINE FILTERS
• TIRE CHUCKS
•PAINT TANKS
•AIR CARRY TANKS
•INFLATOR KITS
•QUICK CONNECTOR SETS
(various sizes)
•AIR PRESSURE REGULATORS
•OIL FOG LUBRICATORS
•AIR TOOLS:
Sanders
Drills
Impact Wrenches
Rachets
=AIR HOSE:
1/4" or 3/8" I.D.
in various lengths
020396 Rev 0 2/16/00
6 - ENG
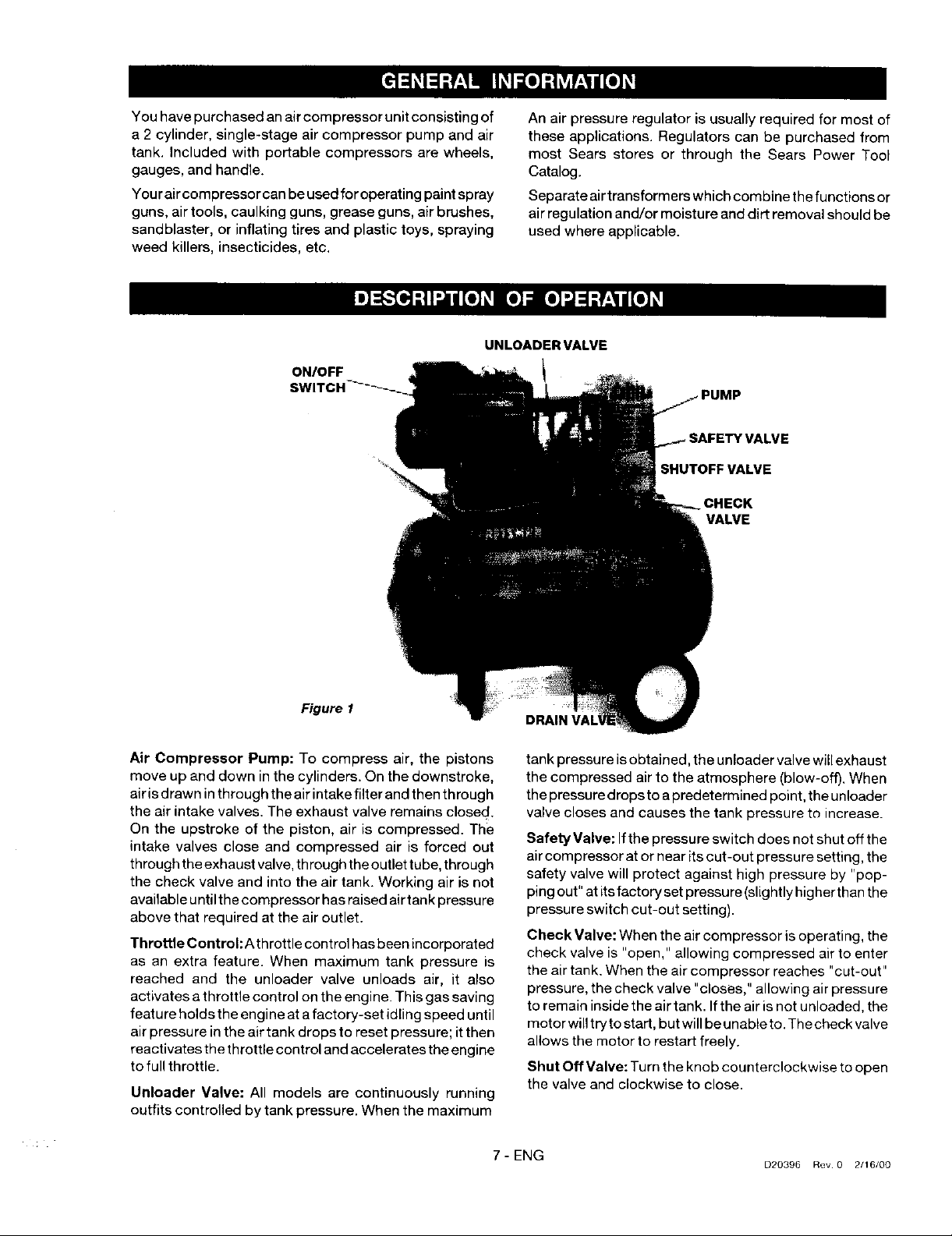
You have purchased an air compressor unit consisting of
a 2 cylinder, single-stage air compressor pump and air
tank. Included with portable compressors are wheels,
gauges, and handle.
Your air compressor can be used for operating paint spray
guns, air tools, caulking guns, grease guns, air brushes,
sandblaster, or inflating tires and plastic toys, spraying
weed killers, insecticides, etc.
ON/OFF
SWITCH-_-_
An air pressure regulator is usually required for most of
these applications. Regulators can be purchased from
most Sears stores or through the Sears Power Tool
Catalog.
Separate air transformers which combine the functions or
air regulation and/or moisture and dirt removal should be
used where applicable.
UNLOADER VALVE
VALVE
SHUTOFF VALVE
CHECK
VALVE
Figure 1
Air Compressor Pump: To compress air, the pistons
move up and down in the cylinders. On the downstroke,
air is drawn in through the air intake filter and then through
the air intake valves. The exhaust valve remains closed.
On the upstroke of the piston, air is compressed. The
intake valves close and compressed air is forced out
through the exhaust valve, through the outlet tube, through
the check valve and into the air tank. Working air is not
available until the compressor has raised airtank pressure
above that required at the air outlet.
Throttle Control: Athrottle control has been incorporated
as an extra feature. When maximum tank pressure is
reached and the unloader valve unloads air, it also
activates a throttle control on the engine. This gas saving
featu reholds the engine at a factory-set idling speed until
air pressure in the air tank drops to reset pressure; it then
reactivates the throttle control and accelerates the engine
to full throttle.
Unloader Valve: All models are continuously running
outfits controlled by tank pressure. When the maximum
tank pressure is obtained, the unloader valve will exhaust
the compressed air to the atmosphere (blow-off). When
the pressure drops to a predetermined point, the unloader
valve closes and causes the tank pressure to increase.
Safety Valve: If the pressure switch does not shut off the
air compressor at or near its cut-out pressure setting, the
safety valve will protect against high pressure by "pop-
ping out" at its factory set pressure (slightly higherthan the
pressure switch cut-out setting).
Check Valve: When the air compressor is operating, the
check valve is "open," allowing compressed air to enter
the air tank. When the air compressor reaches "cut-out"
pressure, the check valve "closes," allowing air pressure
to remain inside the air tank. Ifthe air is not unloaded, the
motor will try to start, but will be unable to. The check valve
allows the motor to restart freely.
Shut Off Valve: Turn the knob counterclockwise to open
the valve and clockwise to close.
7 - ENG
D20396 Rev 0 2/16/00