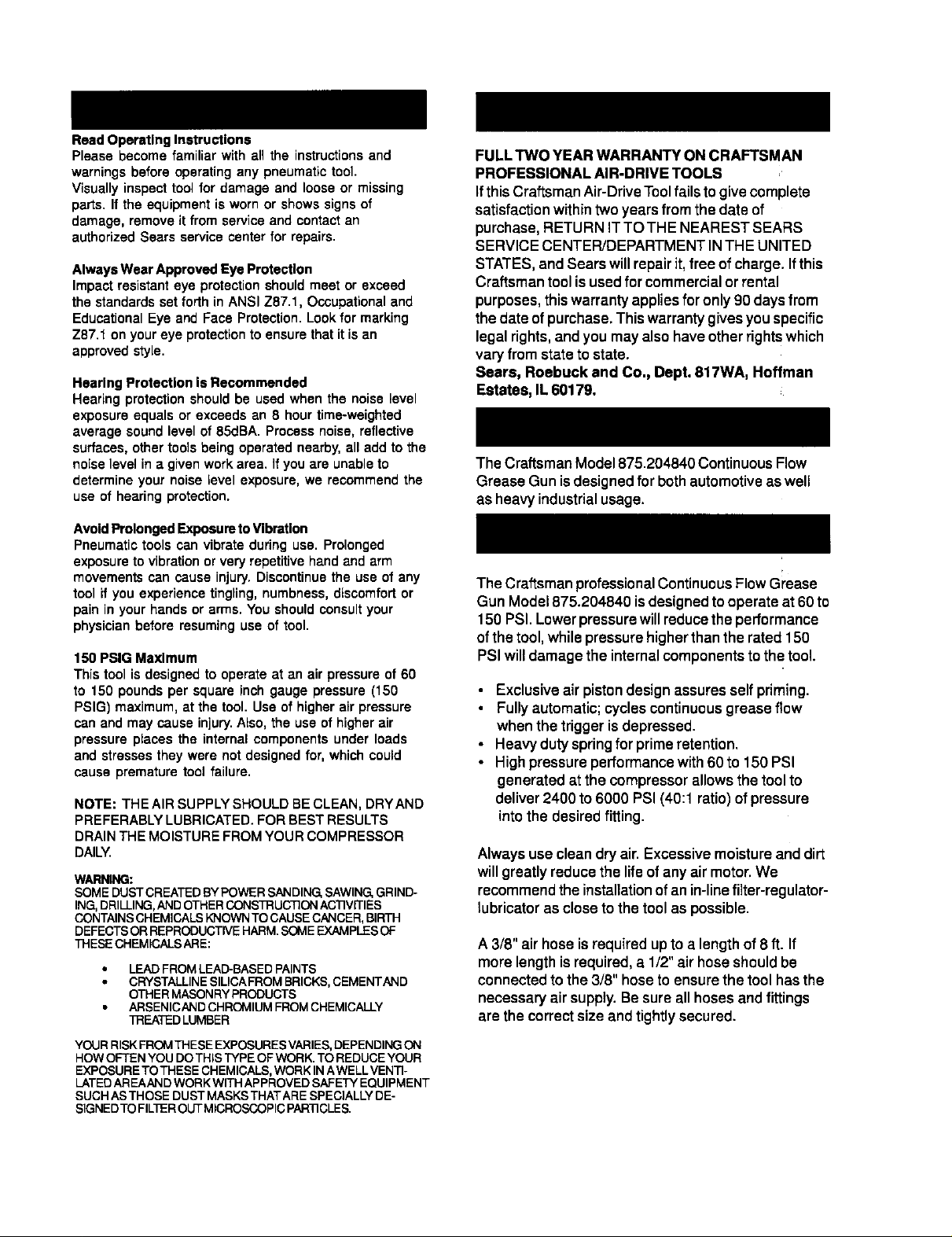
Read Operating Instructions
Please become familiar with all the instructions and
warnings before operating any pneumatic tool.
Visually inspect tool for damage and loose or missing
parts. If the equipment is worn or shows signs of
damage, remove it from service and contact an
authorized Sears service center for repairs.
Always Wear Approved Eye Protection
Impact resistant eye protection should meet or exceed
the standards set forth in ANSI Z87.1, Occupational and
Educational Eye and Face Protection. Look for marking
Z87.1 on youreye protectionto ensure that it is an
approved style.
Hearing Protection is Recommended
Hearing protection should be used when the noise level
exposure equals or exceeds an 8 hour time-weighted
average sound level of 85dBA. Process noise, reflective
surfaces, other tools being operated nearby, all add to the
noise level in a given work area. If you are unableto
determine your noise level exposure, we recommend the
use of hearing protection.
Avoid Prolonged ER3osuretoVibration
Pneumatic tools can vibrate during usa. Prolonged
exposure to vibration or very repetitive hand and arm
movements can cause injury. Discontinue the use of any
tool if you experience tingling, numbness, discomfortor
pain in your hands or arms. You should consultyour
physician before resuming use of tool.
150 PSlG Maximum
This tool is designed to operate at an air pressure of 60
to 150 pounds per square inch gauge pressure (150
PSIG) maximum, at the tool. Use of higher air pressure
can and may cause injury.Also, the use of higherair
pressure placas the internal components under loads
and stresses they were not designed for, which could
cause premature tool failure.
NOTE: THE AIR SUPPLY SHOULD BE CLEAN, DRYAND
PREFERABLY LUBRICATED. FOR BEST RESULTS
DRAIN THE MOISTURE FROM YOUR COMPRESSOR
DAILY.
WARNING:
SOME DUST CREATED BY POWER SANDING, SAWING, GRIND-
ING, DRILUNG, AND OTHER CONSTRUCTION ACTIVFFIES
CONTAINS CHEMICALS KNOWN TO CAUSE CANCER, BIRTH
DEFECTS OR REPRODUCTIVE HARM. SOME EXAMPLES OF
THESE CHEMICALS ARE:
LEAD FROM LEAD-BASED PAINTS
CRYSTALLINE SILICAFROM BRICKS, CEMENTAND
OTHER MASONRY PRODUCTS
ARSENICAND CHROMIUM FROM CHEMICALLY
TREATEDLUMBER
YOUR RISK FROM THESE EXPOSURES VARIES,DEPENDING ON
HOW OFTEN YOU DO THIS TYPE OF WORK. TO REDUCE YOUR
EXPOSURE TOTHESE CHEMICALS, WORK IN AWELLVENTI-
LATEDAREAAN DWORK WITH APPROVED SAFETY EQUIPMENT
SUCH AS THOSE DUST MASKS THATARE SPECIALLY DE-
SIGNED TO FILTER OUT MICROSCOPIC PARTICLES.
FULL't'WO YEAR WARRANTY ON CRAFTSMAN
PROFESSIONAL AIR-DRIVE TOOLS
IfthisCraftsmanAir-DriveToolfailstogivecomplete
satisfactionwithintwoyearsfromthe date of
purchase,RETURN IT TO THE NEAREST SEARS
SERVICE CENTER/DEPARTMENT INTHE UNITED
STATES, and Sears willrepair it, freeof charge. Ifthis
Craftsmantoolis used forcommercialor rental
purposes,thiswarrantyappliesforonly 90 days from
the date ofpurchase,Thiswarrantygivesyouspecific
legal rights,andyou may also have other rightswhich
varyfrom stateto state.
Sears, Roebuck and Co., Dept. 817WA, Hoffman
Estates, IL 60179.
The Craftsman Model 875.204840 Continuous Flow
Grease Gun isdesignedfor both automotiveaswell
as heavy industrial usage.
The Craftsman professionalContinuous Flow Grease
Gun Model 875.204840 is designed to operate at 60 to
150 PSI. Lower pressure will reduce the performance
ofthe tool, while pressure higher than the rated 150
PSI will damage the internal components to the tool.
• Exclusive air piston design assures selfpriming.
• Fully automatic; cycles continuous grease flow
when the trigger is depressed.
• Heavy duty spring for prime retention.
• High pressure performance with 60 to 150PSI
generated at the compressor allows the tool to
deliver 2400 to 6000 PSI (40:1 ratio) of pressure
into the desired fitting.
Always use clean dry air. Excessive moistureand dirt
willgreatlyreduce the lifeof anyair motor.We
recommendtheinstallationofanin-linefilter-regulator-
lubricator as close to the toolas possible.
A 3/8" air hose isrequired upto a lengthof 8 ft. If
morelength is required,a 1/2"air hose shouldbe
connectedto the 3/8" hoseto ensure the toolhasthe
necessaryair supply.Be sure all hoses and fittings
are the correctsize and tightlysecured.
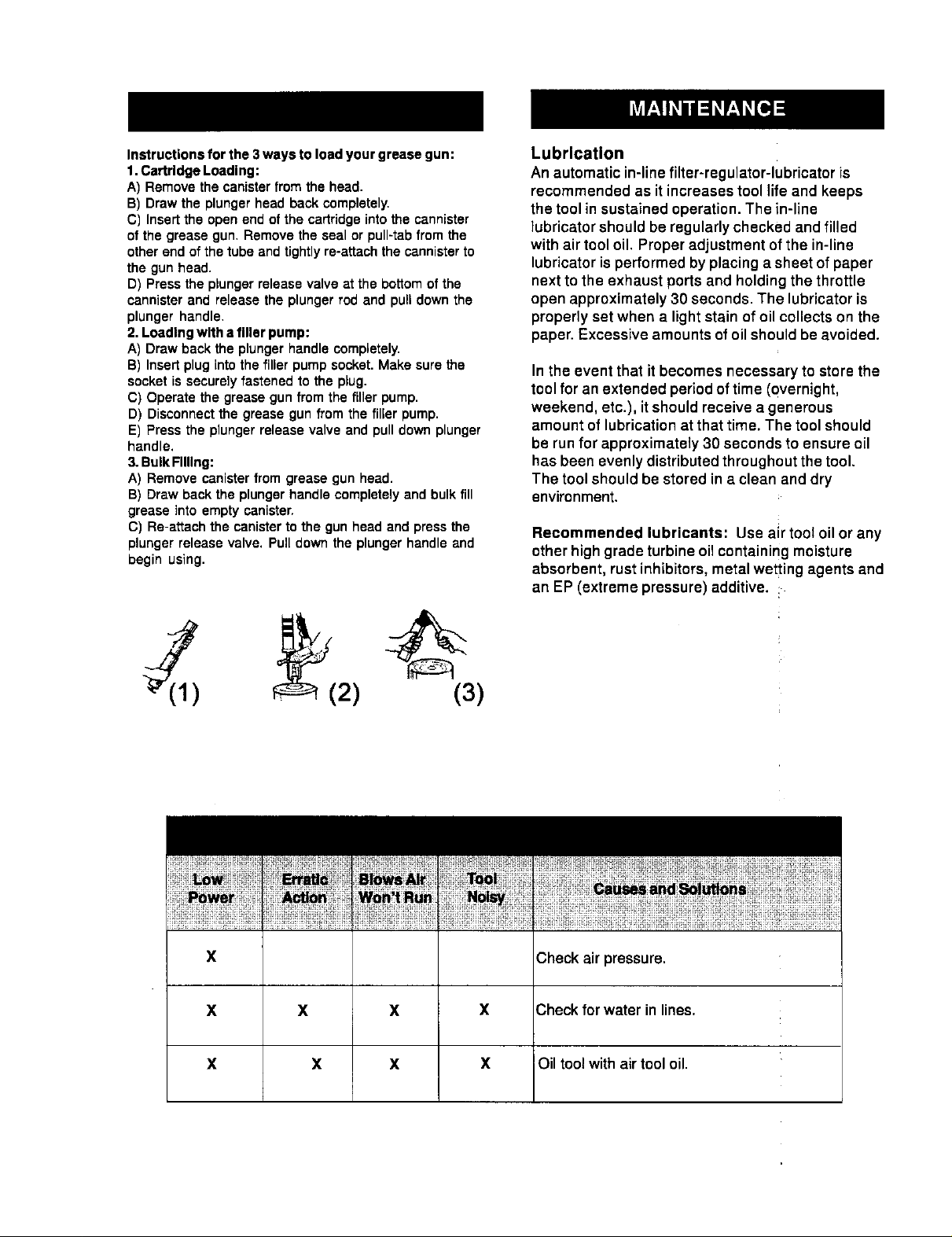
Instructions for the 3 ways to load your grease gun:
1,Cartridge Loading:
A) Remove the canister from the head,
B) Draw the plunger head back completely,
C) Insert the open end of the cartridge into the cannister
of the grease gun. Remove the seal or pull-tab from the
other end of the tube and tightly re-attach the cannister to
the gun head.
D) Press the plunger release valve at the bottom of the
cannister and release the plunger rod and pull down the
plunger handle.
2. Loading with a filler pump:
A) Draw back the plunger handle completely,
B) Insert plug intothe filler pump socket, Make sure the
socket is securely fastened to the plug,
C) Operate the grease gun from the filler pump,
D) Disconnect the grease gun from the filler pump,
E) Press the plunger release valve and pull down plunger
handle,
3. BulkFilling:
A) Remove canister from grease gun head.
B) Draw back the plunger handle completely and bulk fill
grease into empty canister.
C) Re-attach the canister to the gun head and press the
plunger release valve. Pull down the plunger handle and
begin using.
Lubrication
An automatic in-line filter-regulator-lubricator is
recommended as it increases tool life and keeps
the tool in sustained operation. The in-line
lubricator should be regularly checked and filled
with air tooloil. Proper adjustment of the in-line
lubricatorisperformed by placing a sheet ofpaper
nextto the exhaust portsand holdingthe throttle
open approximately 30 seconds. The lubricatoris
properly set when a light stain of oil collects on the
paper. Excessive amounts of oilshould be avoided.
In the event that it becomes necessary to store the
tool for an extended period of time (overnight,
weekend, etc.), itshould receive a generous
amount of lubricationat that time. The tool should
be runfor approximately 30 seconds to ensure oil
has been evenly distributed throughout the tool.
The tool should be stored in a clean and dry
environment.
Recommended lubricants: Use air tool oil or any
other high grade turbine oilcontaining moisture
absorbent, rust inhibitors,metal wetting agents and
an EP (extreme pressure) additive.
X Check air pressure.
X X X X Check for water in lines.
X X X X Oil tool with air tooloil.