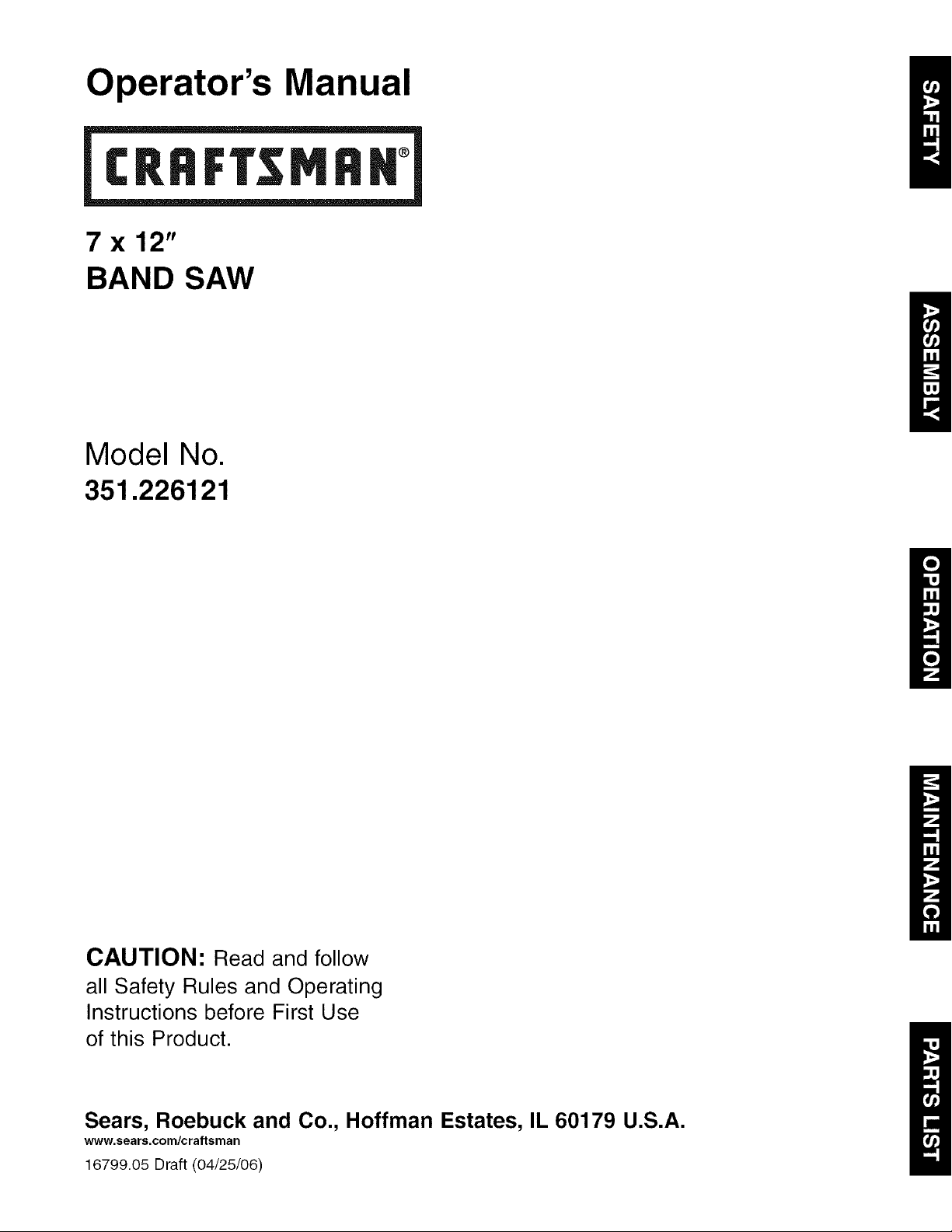
Operator's Manual
7 x 12"
BAND SAW
Model No.
351.226121
CAUTION: Read and follow
all Safety Rules and Operating
Instructions before First Use
of this Product.
Sears, Roebuck and Co., Hoffman Estates, IL 60179 U.S.A.
www.sears.com/craftsman
16799.05 Draft (04/25/06)
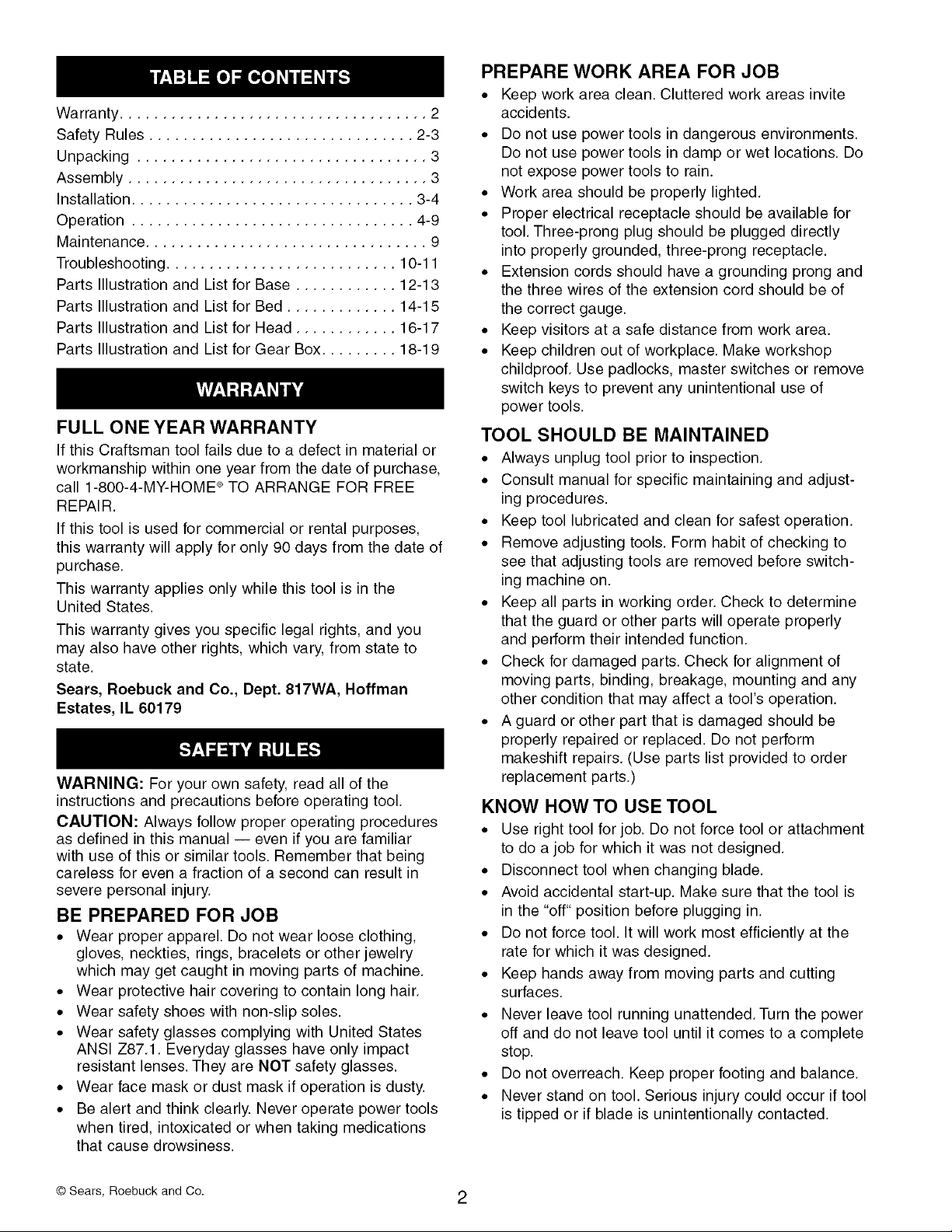
Warranty.................................... 2
SafetyRules............................... 2-3
Unpacking.................................. 3
Assembly................................... 3
Installation................................. 3-4
Operation................................. 4-9
Maintenance................................. 9
Troubleshooting........................... 10-11
PartsIllustrationandListforBase............ 12-13
PartsIllustrationandListforBed............. 14-15
PartsIllustrationandListforHead............ 16-17
PartsIllustrationandListforGearBox......... 18-19
FULL ONE YEAR WARRANTY
If this Craftsman tool fails due to a defect in material or
workmanship within one year from the date of purchase,
call 1-800-4-MY-HOME ®TO ARRANGE FOR FREE
REPAIR.
If this tool is used for commercial or rental purposes,
this warranty will apply for only 90 days from the date of
purchase.
This warranty applies only while this tool is in the
United States.
This warranty gives you specific legal rights, and you
may also have other rights, which vary, from state to
state.
Sears, Roebuck and Co., Dept. 817WA, Hoffman
Estates, IL 60179
WARNING: For your own safety, read all of the
instructions and precautions before operating tool.
CAUTION: Always follow proper operating procedures
as defined in this manual -- even if you are familiar
with use of this or similar tools. Remember that being
careless for even a fraction of a second can result in
severe personal injury.
BE PREPARED FOR JOB
• Wear proper apparel. Do not wear loose clothing,
gloves, neckties, rings, bracelets or other jewelry
which may get caught in moving parts of machine.
• Wear protective hair covering to contain long hair.
• Wear safety shoes with non-slip soles.
• Wear safety glasses complying with United States
ANSI Z87.1. Everyday glasses have only impact
resistant lenses. They are NOT safety glasses.
• Wear face mask or dust mask if operation is dusty.
• Be alert and think clearly. Never operate power tools
when tired, intoxicated or when taking medications
that cause drowsiness.
PREPARE WORK AREA FOR JOB
• Keep work area clean. Cluttered work areas invite
accidents.
• Do not use power tools in dangerous environments.
Do not use power tools in damp or wet locations. Do
not expose power tools to rain.
• Work area should be properly lighted.
• Proper electrical receptacle should be available for
tool. Three-prong plug should be plugged directly
into properly grounded, three-prong receptacle.
• Extension cords should have a grounding prong and
the three wires of the extension cord should be of
the correct gauge.
• Keep visitors at a safe distance from work area.
• Keep children out of workplace. Make workshop
childproof. Use padlocks, master switches or remove
switch keys to prevent any unintentional use of
power tools.
TOOL SHOULD BE MAINTAINED
• Always unplug tool prior to inspection.
• Consult manual for specific maintaining and adjust-
ing procedures.
• Keep tool lubricated and clean for safest operation.
• Remove adjusting tools. Form habit of checking to
see that adjusting tools are removed before switch-
ing machine on.
• Keep all parts in working order. Check to determine
that the guard or other parts will operate properly
and perform their intended function.
• Check for damaged parts. Check for alignment of
moving parts, binding, breakage, mounting and any
other condition that may affect a tool's operation.
• A guard or other part that is damaged should be
properly repaired or replaced. Do not perform
makeshift repairs. (Use parts list provided to order
replacement parts.)
KNOW HOW TO USE TOOL
• Use right tool for job. Do not force tool or attachment
to do a job for which it was not designed.
• Disconnect tool when changing blade.
• Avoid accidental start-up. Make sure that the tool is
in the "off" position before plugging in.
• Do not force tool. It will work most efficiently at the
rate for which it was designed.
• Keep hands away from moving parts and cutting
surfaces.
• Never leave tool running unattended. Turn the power
off and do not leave tool until it comes to a complete
stop.
• Do not overreach. Keep proper footing and balance.
• Never stand on tool. Serious injury could occur if tool
is tipped or if blade is unintentionally contacted.
© Sears, Roebuck and Co. 2
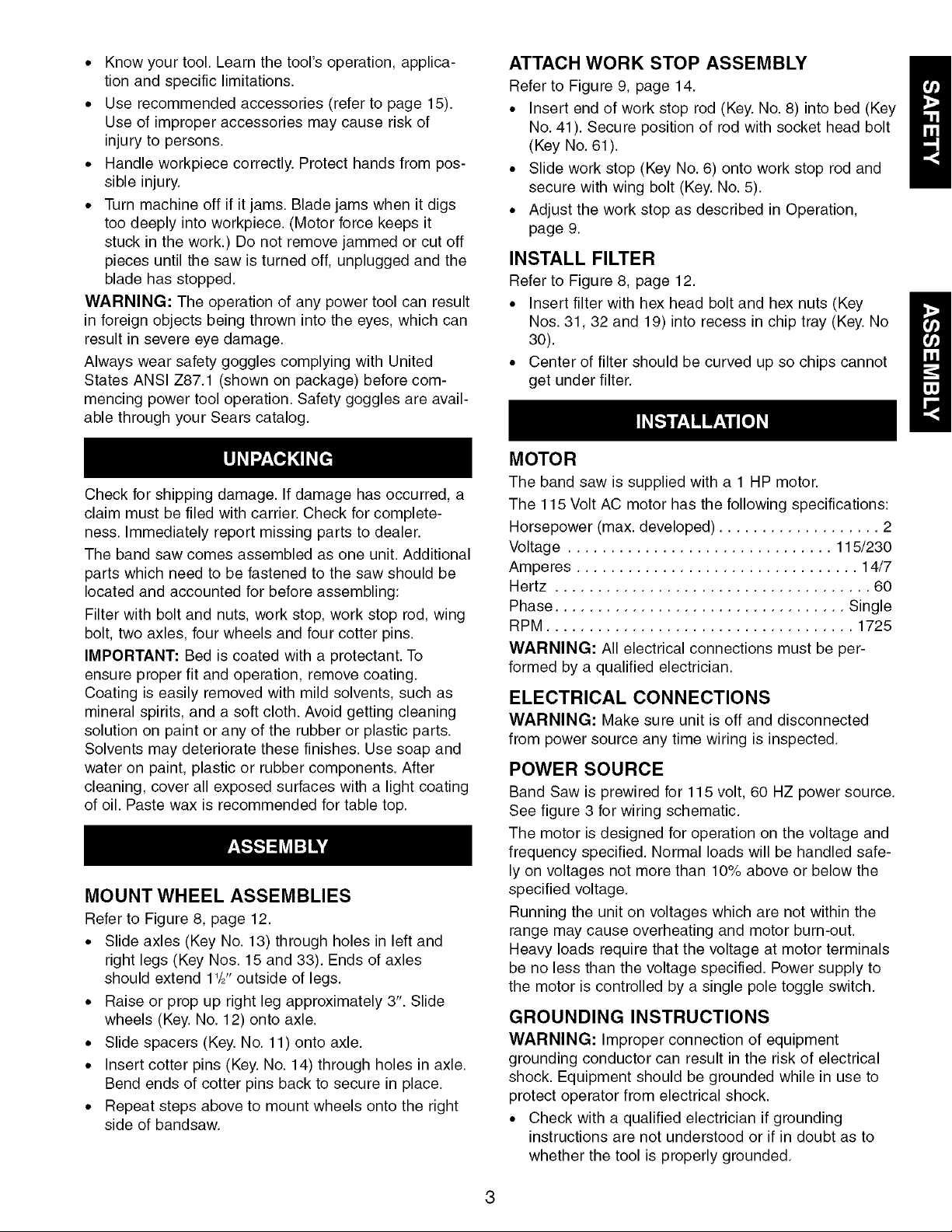
• Know your tool. Learn the tool's operation, applica-
tion and specific limitations.
• Use recommended accessories (refer to page 15).
Use of improper accessories may cause risk of
injury to persons.
• Handle workpiece correctly. Protect hands from pos-
sible injury.
• Turn machine off if it jams. Blade jams when it digs
too deeply into workpiece. (Motor force keeps it
stuck in the work.) Do not remove jammed or cut off
pieces until the saw is turned off, unplugged and the
blade has stopped.
WARNING: The operation of any power tool can result
in foreign objects being thrown into the eyes, which can
result in severe eye damage.
Always wear safety goggles complying with United
States ANSI Z87.1 (shown on package) before com-
mencing power tool operation. Safety goggles are avail-
able through your Sears catalog.
Check for shipping damage. If damage has occurred, a
claim must be filed with carrier. Check for complete-
ness. Immediately report missing parts to dealer.
The band saw comes assembled as one unit. Additional
parts which need to be fastened to the saw should be
located and accounted for before assembling:
Filter with bolt and nuts, work stop, work stop rod, wing
bolt, two axles, four wheels and four cotter pins.
IMPORTANT: Bed is coated with a protectant. To
ensure proper fit and operation, remove coating.
Coating is easily removed with mild solvents, such as
mineral spirits, and a soft cloth. Avoid getting cleaning
solution on paint or any of the rubber or plastic parts.
Solvents may deteriorate these finishes. Use soap and
water on paint, plastic or rubber components. After
cleaning, cover all exposed surfaces with a light coating
of oil. Paste wax is recommended for table top.
MOUNT WHEEL ASSEMBLIES
Refer to Figure 8, page 12.
• Slide axles (Key No. 13) through holes in left and
right legs (Key Nos. 15 and 33). Ends of axles
should extend 11/2"outside of legs.
• Raise or prop up right leg approximately 3". Slide
wheels (Key. No. 12) onto axle.
• Slide spacers (Key. No. 11) onto axle.
• Insert cotter pins (Key. No. 14) through holes in axle.
Bend ends of cotter pins back to secure in place.
• Repeat steps above to mount wheels onto the right
side of bandsaw.
ATTACH WORK STOP ASSEMBLY
Refer to Figure 9, page 14.
• Insert end of work stop rod (Key. No. 8) into bed (Key
No. 41 ). Secure position of rod with socket head bolt
(Key No. 61 ).
• Slide work stop (Key No. 6) onto work stop rod and
secure with wing bolt (Key. No. 5).
• Adjust the work stop as described in Operation,
page 9.
INSTALL FILTER
Refer to Figure 8, page 12.
• Insert filter with hex head bolt and hex nuts (Key
Nos. 31,32 and 19) into recess in chip tray (Key. No
30).
• Center of filter should be curved up so chips cannot
get under filter.
MOTOR
The band saw is supplied with a 1 HP motor.
The 115 Volt AC motor has the following specifications:
Horsepower (max. developed) ................... 2
Voltage ............................... 115/230
Amperes ................................. 14/7
Hertz ..................................... 60
Phase .................................. Single
RPM .................................... 1725
WARNING: All electrical connections must be per-
formed by a qualified electrician.
ELECTRICAL CONNECTIONS
WARNING: Make sure unit is off and disconnected
from power source any time wiring is inspected.
POWER SOURCE
Band Saw is prewired for 115 volt, 60 HZ power source.
See figure 3 for wiring schematic.
The motor is designed for operation on the voltage and
frequency specified. Normal loads will be handled safe-
ly on voltages not more than 10% above or below the
specified voltage.
Running the unit on voltages which are not within the
range may cause overheating and motor burn-out.
Heavy loads require that the voltage at motor terminals
be no less than the voltage specified. Power supply to
the motor is controlled by a single pole toggle switch.
GROUNDING INSTRUCTIONS
WARNING: Improper connection of equipment
grounding conductor can result in the risk of electrical
shock. Equipment should be grounded while in use to
protect operator from electrical shock.
• Check with a qualified electrician if grounding
instructions are not understood or if in doubt as to
whether the tool is properly grounded.
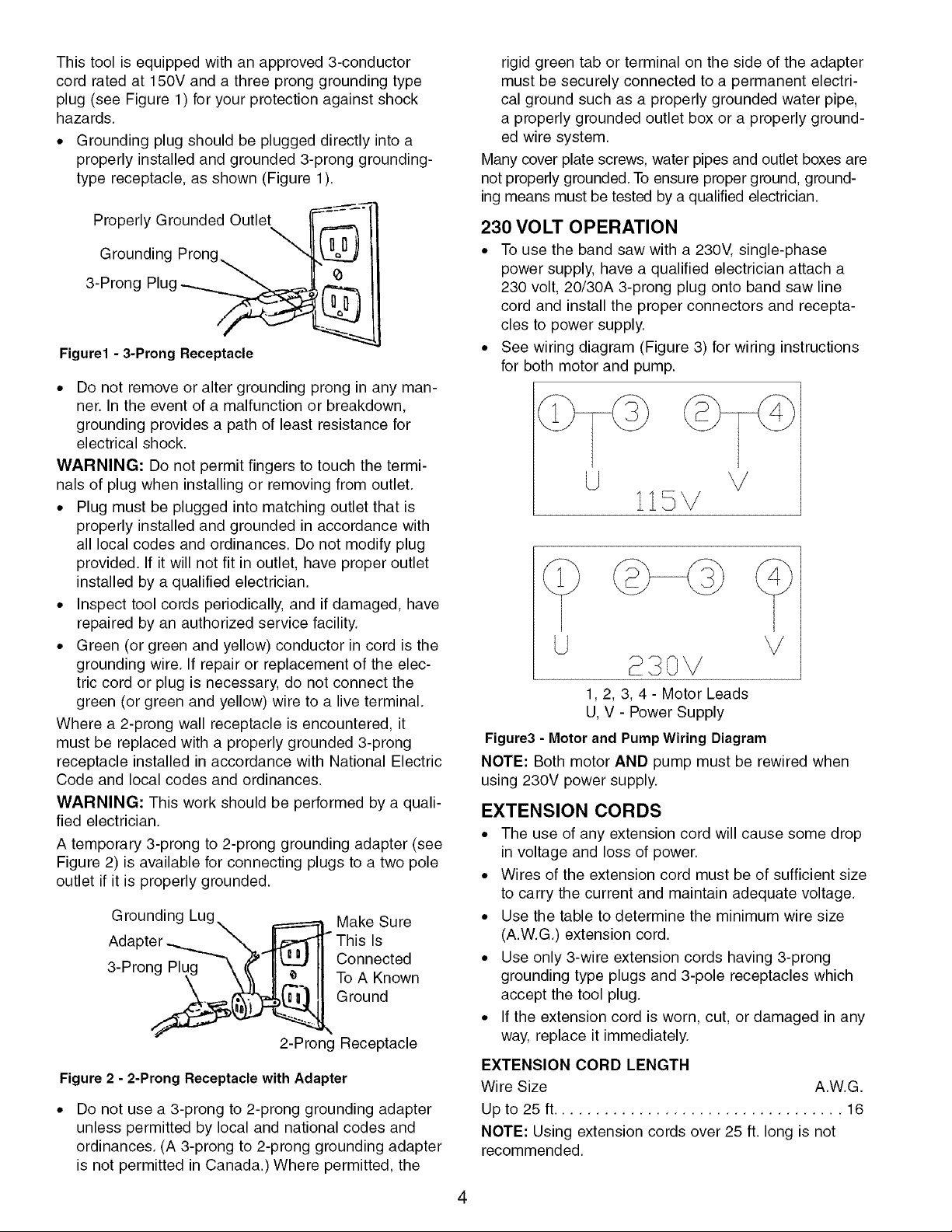
Thistoolisequippedwithanapproved3-conductor
cordratedat150Vanda threepronggroundingtype
plug(seeFigure1)foryourprotectionagainstshock
hazards.
• Groundingplugshouldbepluggeddirectlyintoa
properlyinstalledandgrounded3-pronggrounding-
typereceptacle,asshown(Figure1).
rigid green tab or terminal on the side of the adapter
must be securely connected to a permanent electri-
cal ground such as a properly grounded water pipe,
a properly grounded outlet box or a properly ground-
ed wire system.
Many cover plate screws, water pipes and outlet boxes are
not properly grounded. To ensure proper ground, ground-
ing means must be tested by a qualified electrician.
ProperlyGroundedOutlet..,,,.K_'il
3__rroO_d_lnuggProng _._.._"4_L_.J II
Figure1 - 3-Prong Receptacle
• Do not remove or alter grounding prong in any man-
ner. In the event of a malfunction or breakdown,
grounding provides a path of least resistance for
electrical shock.
WARNING: Do not permit fingers to touch the termi-
nals of plug when installing or removing from outlet.
• Plug must be plugged into matching outlet that is
properly installed and grounded in accordance with
all local codes and ordinances. Do not modify plug
provided. If it will not fit in outlet, have proper outlet
installed by a qualified electrician.
• Inspect tool cords periodically, and if damaged, have
repaired by an authorized service facility.
• Green (or green and yellow) conductor in cord is the
grounding wire. If repair or replacement of the elec-
tric cord or plug is necessary, do not connect the
green (or green and yellow) wire to a live terminal.
Where a 2-prong wall receptacle is encountered, it
must be replaced with a properly grounded 3-prong
receptacle installed in accordance with National Electric
Code and local codes and ordinances.
WARNING: This work should be performed by a quali-
fied electrician.
A temporary 3-prong to 2-prong grounding adapter (see
Figure 2) is available for connecting plugs to a two pole
outlet if it is properly grounded.
Grounding Lug_ _" ThisMakelsSure
Adapter _ _ Connected
3-Pronu,,_u __D,,_ _ ¢ _'-----, H ToAKnown
Ground
2-Prong Receptacle
Figure 2 - 2-Prong Receptacle with Adapter
Do not use a 3-prong to 2-prong grounding adapter
unless permitted by local and national codes and
ordinances. (A 3-prong to 2-prong grounding adapter
is not permitted in Canada.) Where permitted, the
230 VOLT OPERATION
• To use the band saw with a 230V, single-phase
power supply, have a qualified electrician attach a
230 volt, 20/30A 3-prong plug onto band saw line
cord and install the proper connectors and recepta-
cles to power supply.
• See wiring diagram (Figure 3) for wiring instructions
for both motor and pump.
U
llS\J
U V
230V
1,2, 3, 4 - Motor Leads
U, V - Power Supply
Figure3 - Motor and Pump Wiring Diagram
NOTE: Both motor AND pump must be rewired when
using 230V power supply.
EXTENSION CORDS
• The use of any extension cord will cause some drop
in voltage and loss of power.
• Wires of the extension cord must be of sufficient size
to carry the current and maintain adequate voltage.
• Use the table to determine the minimum wire size
(A.W.G.) extension cord.
• Use only 3-wire extension cords having 3-prong
grounding type plugs and 3-pole receptacles which
accept the tool plug.
• If the extension cord is worn, cut, or damaged in any
way, replace it immediately.
EXTENSION CORD LENGTH
Wire Size A.W.G.
Up to 25 ft.................................. 16
NOTE: Using extension cords over 25 ft. long is not
recommended.
4
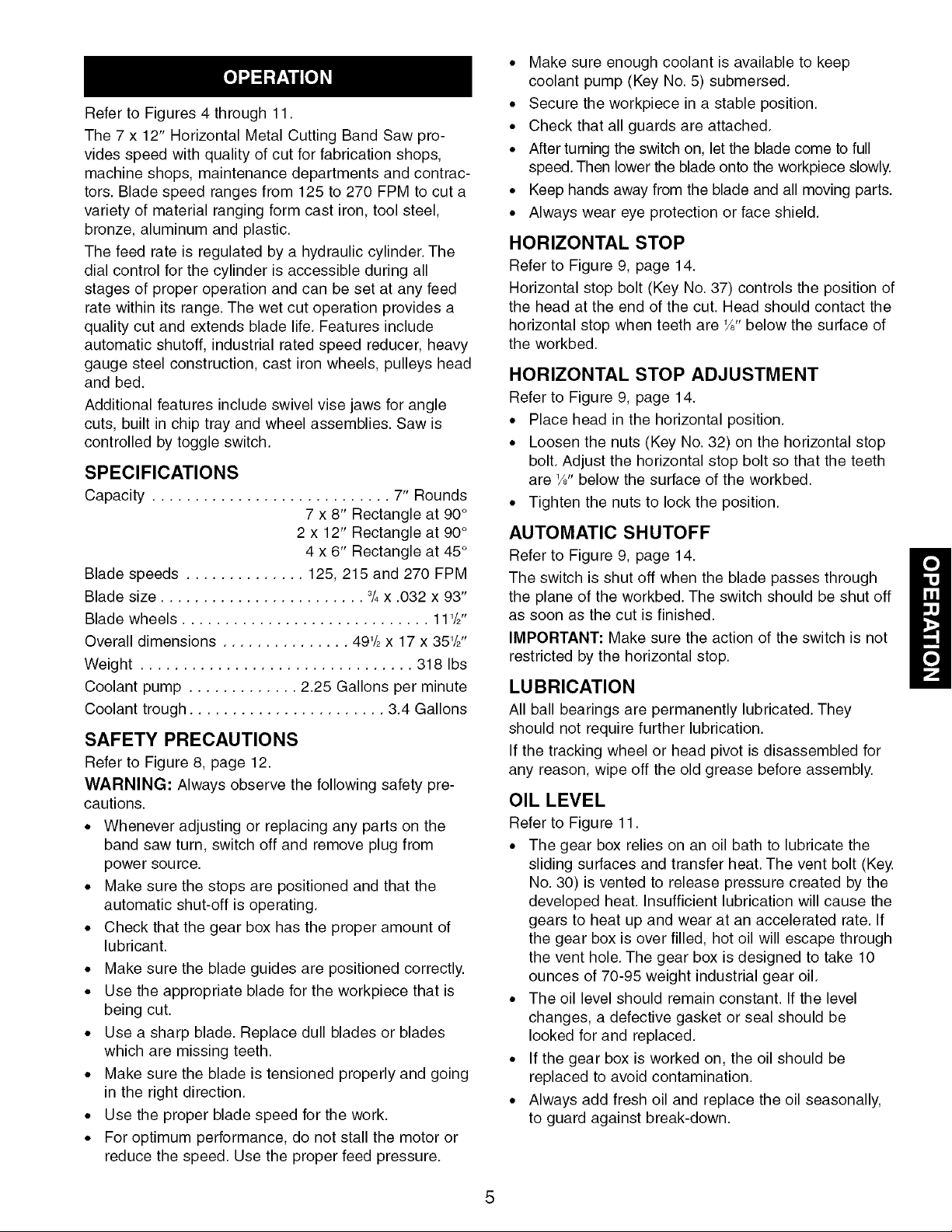
RefertoFigures4through11.
The7x12"HorizontalMetalCuttingBandSawpro-
videsspeedwithqualityofcutforfabricationshops,
machineshops,maintenancedepartmentsandcontrac-
tors.Bladespeedrangesfrom125to270FPMtocuta
varietyofmaterialrangingformcastiron,toolsteel,
bronze,aluminumandplastic.
Thefeedrateisregulatedbyahydrauliccylinder.The
dialcontrolforthecylinderisaccessibleduringall
stagesofproperoperationandcanbesetatanyfeed
ratewithinitsrange.Thewetcutoperationprovidesa
qualitycutandextendsbladelife.Featuresinclude
automaticshutoff,industrialratedspeedreducer,heavy
gaugesteelconstruction,castironwheels,pulleyshead
andbed.
Additionalfeaturesincludeswivelvisejawsforangle
cuts,builtinchiptrayandwheelassemblies.Sawis
controlledbytoggleswitch.
SPECIFICATIONS
Capacity ............................ 7" Rounds
7 x 8" Rectangle at 90°
2 x 12" Rectangle at 90°
4 x 6" Rectangle at 45°
Blade speeds .............. 125, 215 and 270 FPM
Blade size ........................ 3/4x .032 x 93"
Blade wheels ............................. 111/2"
Overall dimensions ............... 491/2x 17 x 351/2',
Weight ................................ 318 Ibs
Coolant pump ............. 2.25 Gallons per minute
Coolant trough ....................... 3.4 Gallons
SAFETY PRECAUTIONS
Refer to Figure 8, page 12.
WARNING: Always observe the following safety pre-
cautions.
• Whenever adjusting or replacing any parts on the
band saw turn, switch off and remove plug from
power source.
• Make sure the stops are positioned and that the
automatic shut-off is operating.
• Check that the gear box has the proper amount of
lubricant.
• Make sure the blade guides are positioned correctly.
• Use the appropriate blade for the workpiece that is
being cut.
• Use a sharp blade. Replace dull blades or blades
which are missing teeth.
• Make sure the blade is tensioned properly and going
in the right direction.
• Use the proper blade speed for the work.
• For optimum performance, do not stall the motor or
reduce the speed. Use the proper feed pressure.
• Make sure enough coolant is available to keep
coolant pump (Key No. 5) submersed.
• Secure the workpiece in a stable position.
• Check that all guards are attached.
• After turning the switch on, let the blade come to full
speed. Then lower the blade onto the workpiece slowly.
• Keep hands away from the blade and all moving parts.
• Always wear eye protection or face shield.
HORIZONTAL STOP
Refer to Figure 9, page 14.
Horizontal stop bolt (Key No. 37) controls the position of
the head at the end of the cut. Head should contact the
horizontal stop when teeth are 1/8"below the surface of
the workbed.
HORIZONTAL STOP ADJUSTMENT
Refer to Figure 9, page 14.
• Place head in the horizontal position.
• Loosen the nuts (Key No. 32) on the horizontal stop
bolt. Adjust the horizontal stop bolt so that the teeth
are 1/8"below the surface of the workbed.
• Tighten the nuts to lock the position.
AUTOMATIC SHUTOFF
Refer to Figure 9, page 14.
The switch is shut off when the blade passes through
the plane of the workbed. The switch should be shut off
as soon as the cut is finished.
IMPORTANT: Make sure the action of the switch is not
restricted by the horizontal stop.
LUBRICATION
All ball bearings are permanently lubricated. They
should not require further lubrication.
If the tracking wheel or head pivot is disassembled for
any reason, wipe off the old grease before assembly.
OIL LEVEL
Refer to Figure 11.
• The gear box relies on an oil bath to lubricate the
sliding surfaces and transfer heat. The vent bolt (Key.
No. 30) is vented to release pressure created by the
developed heat. Insufficient lubrication will cause the
gears to heat up and wear at an accelerated rate. If
the gear box is over filled, hot oil will escape through
the vent hole. The gear box is designed to take 10
ounces of 70-95 weight industrial gear oil.
• The oil level should remain constant. If the level
changes, a defective gasket or seal should be
looked for and replaced.
• If the gear box is worked on, the oil should be
replaced to avoid contamination.
• Always add fresh oil and replace the oil seasonally,
to guard against break-down.
H
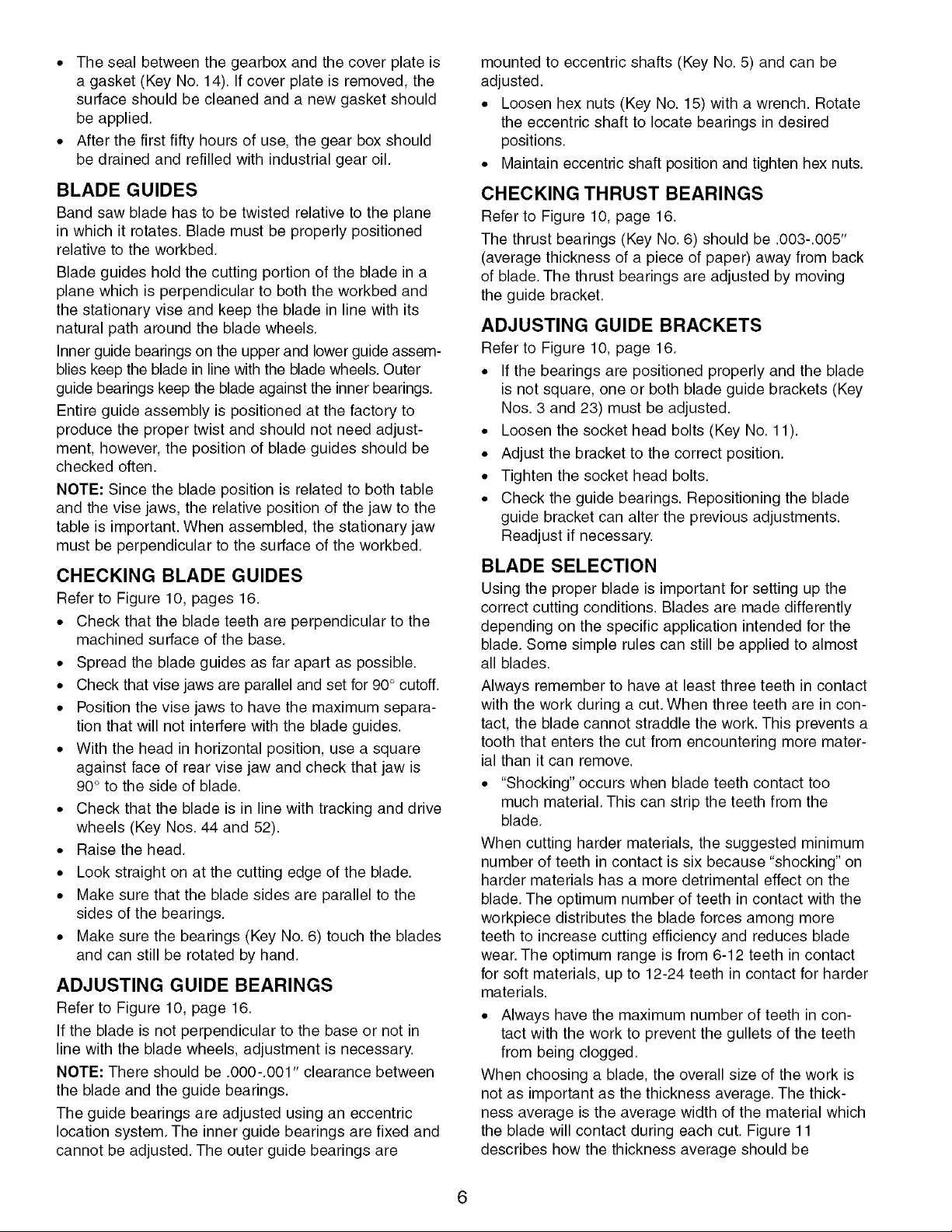
• Thesealbetweenthegearboxandthecoverplateis
agasket(KeyNo.14).Ifcoverplateisremoved,the
surfaceshouldbecleanedanda newgasketshould
beapplied.
• Afterthefirstfiftyhoursofuse,thegearboxshould
bedrainedandrefilledwithindustrialgearoil.
BLADE GUIDES
Band saw blade has to be twisted relative to the plane
in which it rotates. Blade must be properly positioned
relative to the workbed.
Blade guides hold the cutting portion of the blade in a
plane which is perpendicular to both the workbed and
the stationary vise and keep the blade in line with its
natural path around the blade wheels.
Inner guide bearings on the upper and lower guide assem-
blies keep the blade in line with the blade wheels. Outer
guide bearings keep the blade against the inner bearings.
Entire guide assembly is positioned at the factory to
produce the proper twist and should not need adjust-
ment, however, the position of blade guides should be
checked often.
NOTE: Since the blade position is related to both table
and the vise jaws, the relative position of the jaw to the
table is important. When assembled, the stationary jaw
must be perpendicular to the surface of the workbed.
CHECKING BLADE GUIDES
Refer to Figure 10, pages 16.
• Check that the blade teeth are perpendicular to the
machined surface of the base.
• Spread the blade guides as far apart as possible.
• Check that vise jaws are parallel and set for 90° cutoff.
• Position the vise jaws to have the maximum separa-
tion that will not interfere with the blade guides.
• With the head in horizontal position, use a square
against face of rear vise jaw and check that jaw is
90° to the side of blade.
• Check that the blade is in line with tracking and drive
wheels (Key Nos. 44 and 52).
• Raise the head.
• Look straight on at the cutting edge of the blade.
• Make sure that the blade sides are parallel to the
sides of the bearings.
• Make sure the bearings (Key No. 6) touch the blades
and can still be rotated by hand.
ADJUSTING GUIDE BEARINGS
Refer to Figure 10, page 16.
If the blade is not perpendicular to the base or not in
line with the blade wheels, adjustment is necessary.
NOTE: There should be .000-.001" clearance between
the blade and the guide bearings.
The guide bearings are adjusted using an eccentric
location system. The inner guide bearings are fixed and
cannot be adjusted. The outer guide bearings are
mounted to eccentric shafts (Key No. 5) and can be
adjusted.
• Loosen hex nuts (Key No. 15) with a wrench. Rotate
the eccentric shaft to locate bearings in desired
positions.
• Maintain eccentric shaft position and tighten hex nuts.
CHECKING THRUST BEARINGS
Refer to Figure 10, page 16.
The thrust bearings (Key No. 6) should be .003-.005"
(average thickness of a piece of paper) away from back
of blade. The thrust bearings are adjusted by moving
the guide bracket.
ADJUSTING GUIDE BRACKETS
Refer to Figure 10, page 16.
• If the bearings are positioned properly and the blade
is not square, one or both blade guide brackets (Key
Nos. 3 and 23) must be adjusted.
• Loosen the socket head bolts (Key No. 11).
• Adjust the bracket to the correct position.
• Tighten the socket head bolts.
• Check the guide bearings. Repositioning the blade
guide bracket can alter the previous adjustments.
Readjust if necessary.
BLADE SELECTION
Using the proper blade is important for setting up the
correct cutting conditions. Blades are made differently
depending on the specific application intended for the
blade. Some simple rules can still be applied to almost
all blades.
Always remember to have at least three teeth in contact
with the work during a cut. When three teeth are in con-
tact, the blade cannot straddle the work. This prevents a
tooth that enters the cut from encountering more mater-
ial than it can remove.
• "Shocking" occurs when blade teeth contact too
much material. This can strip the teeth from the
blade.
When cutting harder materials, the suggested minimum
number of teeth in contact is six because "shocking" on
harder materials has a more detrimental effect on the
blade. The optimum number of teeth in contact with the
workpiece distributes the blade forces among more
teeth to increase cutting efficiency and reduces blade
wear. The optimum range is from 6-12 teeth in contact
for soft materials, up to 12-24 teeth in contact for harder
materials.
• Always have the maximum number of teeth in con-
tact with the work to prevent the gullets of the teeth
from being clogged.
When choosing a blade, the overall size of the work is
not as important as the thickness average. The thick-
ness average is the average width of the material which
the blade will contact during each cut. Figure 11
describes how the thickness average should be
6