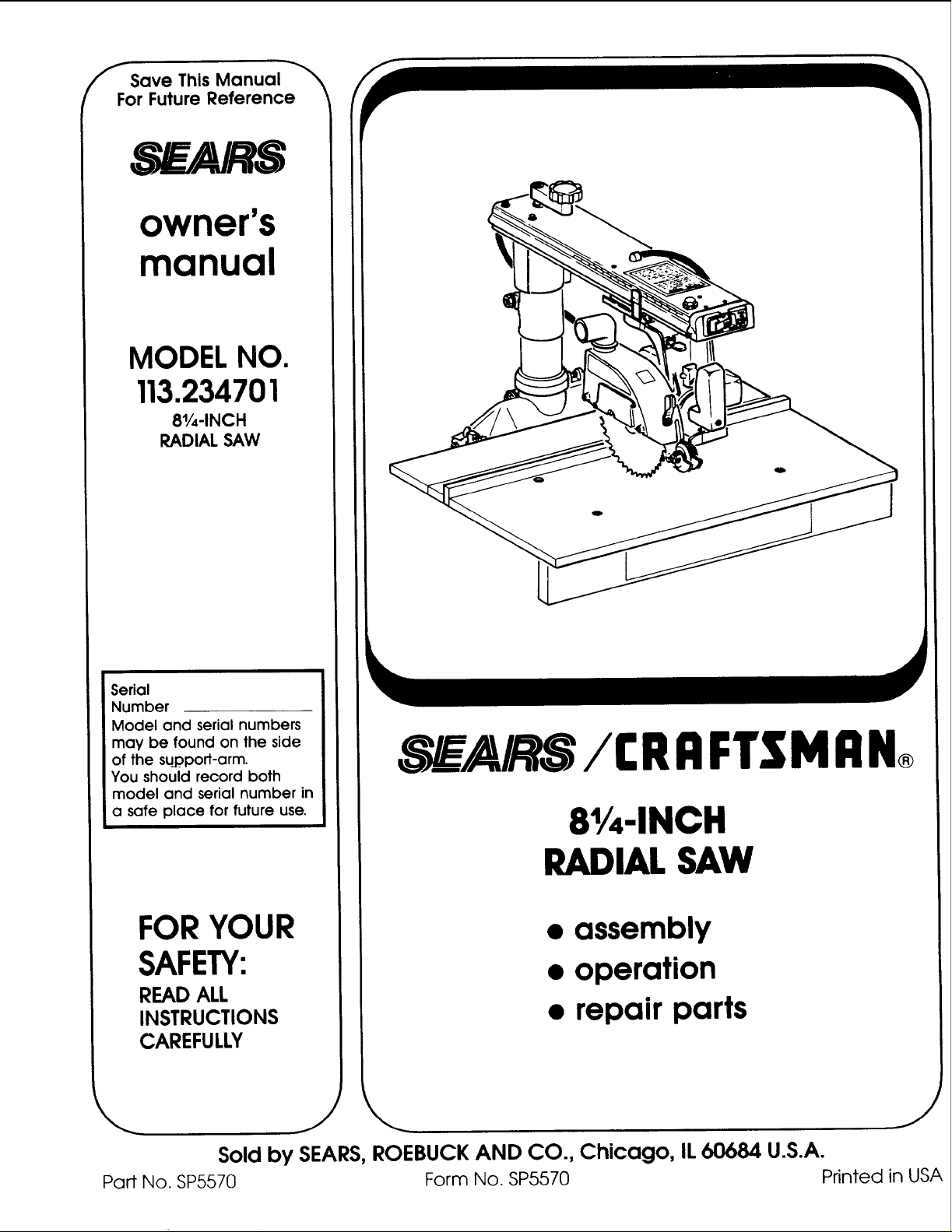
f
Save This Manual
For Future Reference
owner's
manual
MODEL NO.
113.234701
81/4-1NCH
RADIAL SAW
Serial
Number
Model and serial numbers
may be found on the side
of the support-arm.
You should record both
model and serial number in
a safe place for future use.
FOR YOUR
SAFETY:
READ ALL
INSTRUCTIONS
CAREFULLY
SIEAIRS/ r.RRFTSMRN®
81/4-1NCH
RADIAL SAW
• assembly
• operation
• repair parts
J
Sold by SEARS,ROEBUCK AND CO., Chicago, IL60684 U.S.A.
Pad No. SP5570
Form No. SP5570 Printed in USA

Table of Contents
Section Title .......................... Page
Safety ......................................... 3
Assembly ...................................... 12
Controls ....................................... 24
Alignment and Adjustment ............................ 28
Electrical Connections ............................... 39
Crosscutting ..................................... 40
Ripping ....................................... 50
Cutting Aides .................................... 63
Accessories ..................................... 67
Maintenance .................................... 69
Troubleshooting .................................. 73
Repair Parts ..................................... 78
Index ......................................... 87
FULL ONE YEAR WARRANTY ON CRAFTSMAN RADIAL ARM SAW
If within one year from the date of purchase, this Craftsman Radial Saw fails due
to a defect in material or workmanship, Sears will repair it, free of charge.
WARRANTY SERVICE IS AVAILABLE BY SIMPLY CONTACTING THE
NEAREST SEARS SERVICE CENTER/DEPARTMENT THROUGHOUT THE
UNITED STATES.
This warranty applies only while this product is used in the United States.
This warranty gives you specific legal rights and you may also have other rights
which vary from state to state.
SEARS, ROEBUCK AND CO. DEPT. 698/731A SEARS TOWER,
CHICAGO, IL 60684
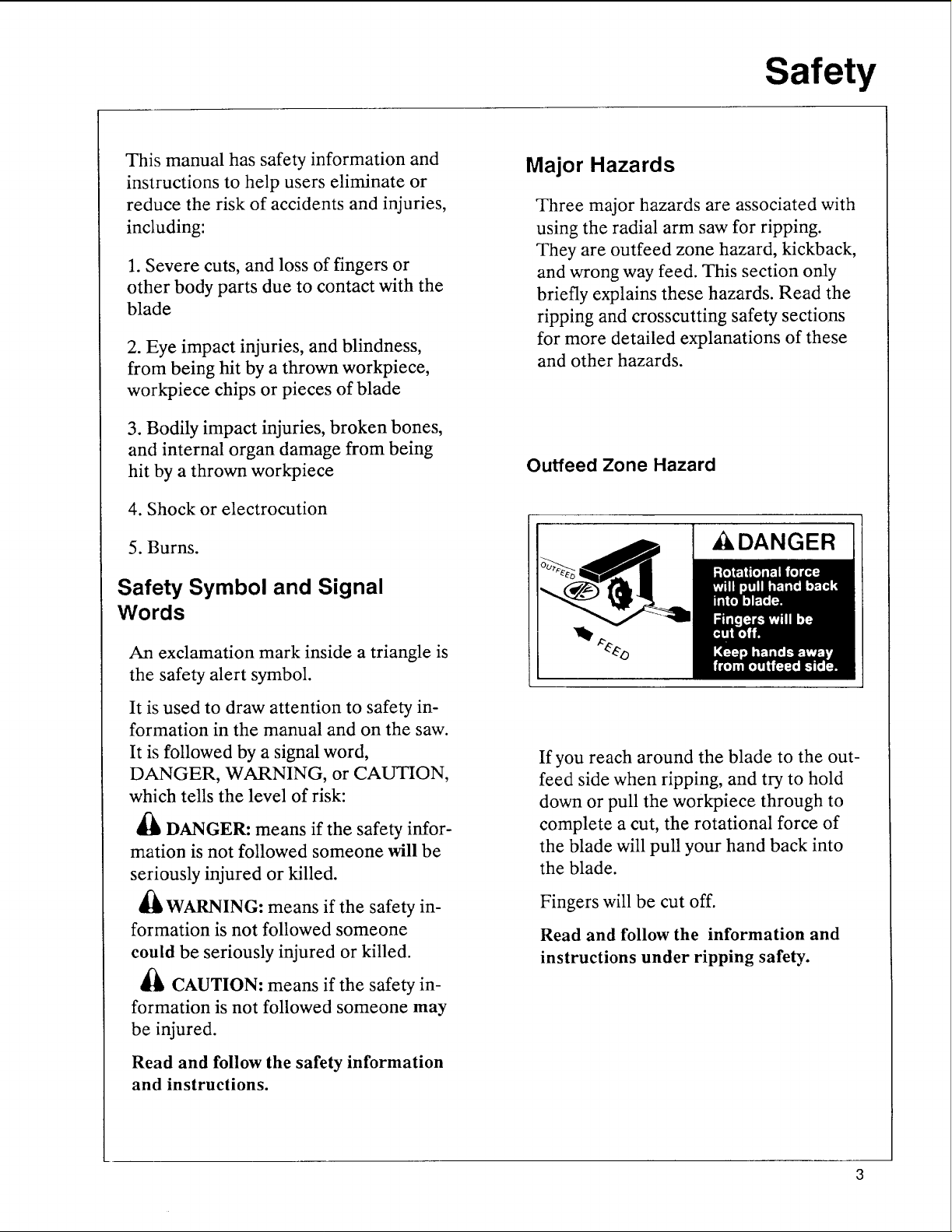
Safety
This manual has safety information and
instructions to help users eliminate or
reduce the risk of accidents and injuries,
including:
1. Severe cuts, and loss of fingers or
other body parts due to contact with the
blade
2. Eye impact injuries, and blindness,
from being hit by a thrown workpiece,
workpiece chips or pieces of blade
3. Bodily impact injuries, broken bones,
and internal organ damage from being
hit by a thrown workpiece
4. Shock or electrocution
5. Burns.
Safety Symbol and Signal
Words
Major Hazards
Three major hazards are associated with
using the radial arm saw for ripping.
They are outfeed zone hazard, kickback,
and wrong way feed. This section only
briefly explains these hazards. Read the
ripping and crosscutting safety sections
for more detailed explanations of these
and other hazards.
Outfeed Zone Hazard
_DANGER
An exclamation mark inside a triangle is
the safety alert symbol.
It is used to draw attention to safety in-
formation in the manual and on the saw.
It is followed by a signal word,
DANGER, WARNING, or CAUTION,
which tells the level of risk:
i_ DANGER: means if the safety infor-
mation is not followed someone will be
seriously injured or killed.
i_ WARNING: means if the safety in-
formation is not followed someone
could be seriously injured or killed.
CAUTION: means if the safety in-
formation is not followed someone may
be injured.
Read and follow the safety information
and instructions.
If you reach around the blade to the out-
feed side when ripping, and try to hold
down or pull the workpiece through to
complete a cut, the rotational force of
the blade will pull your hand back into
the blade.
Fingers will be cut off.
Read and follow the information and
instructions under ripping safety.
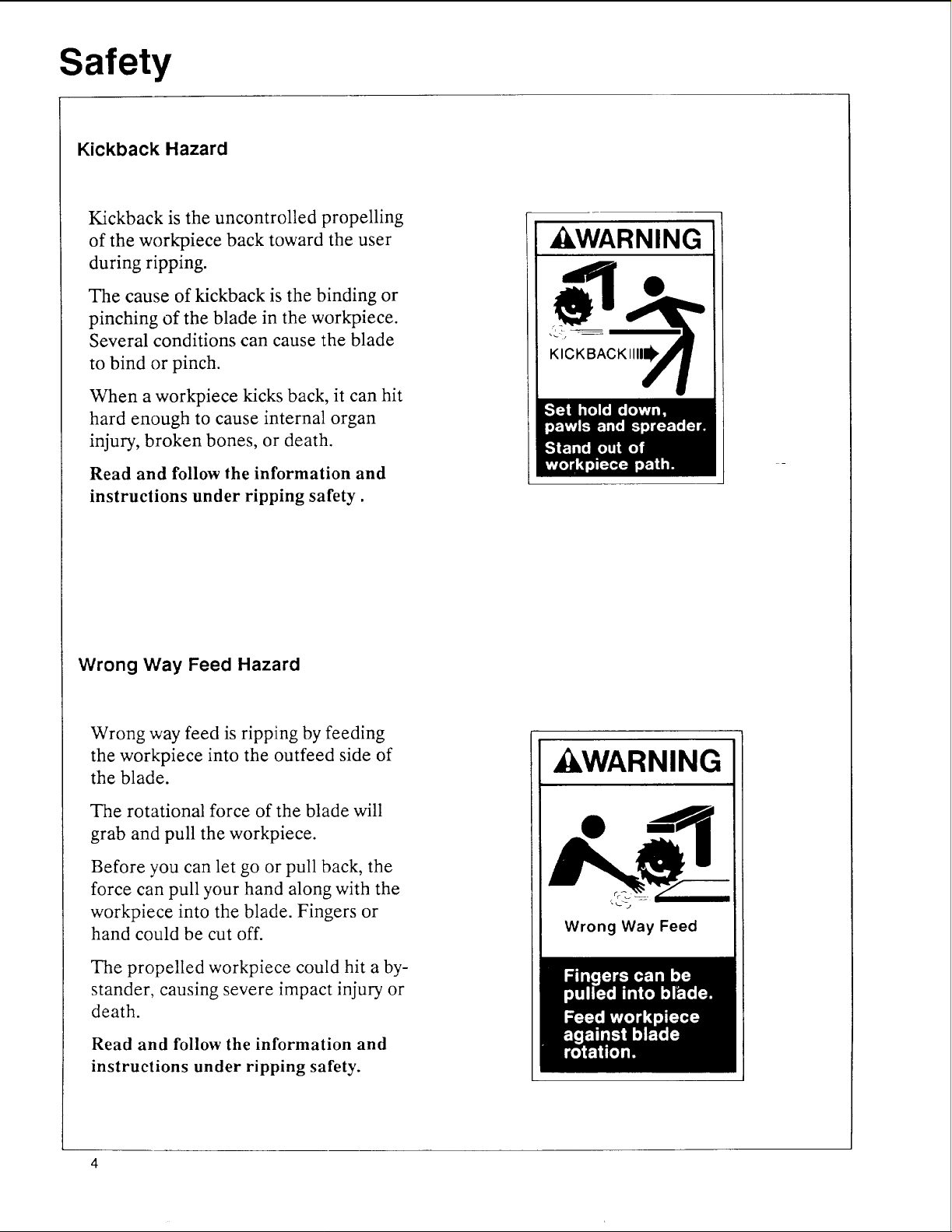
Safety
Kickback Hazard
Kickback is the uncontrolled propelling
of the workpiece back toward the user
during ripping.
The cause of kickback is the binding or
pinching of the blade in the workpiece.
Several conditions can cause the blade
to bind or pinch.
When a workpiece kicks back, it can hit
hard enough to cause internal organ
injury, broken bones, or death.
Read and follow the information and
instructions under ripping safety.
kWARNING
Wrong Way Feed Hazard
Wrong way feed is ripping by feeding
the workpiece into the outfeed side of
the blade.
The rotational force of the blade will
grab and pull the workpiece.
Before you can let go or pull back, the
force can pull your hand along with the
workpiece into the blade. Fingers or
hand could be cut off.
The propelled workpiece could hit a by-
stander, causing severe impact injury or
death.
Read and follow the information and
instructions under ripping safety.
kWARNING
e
Wrong Way Feed
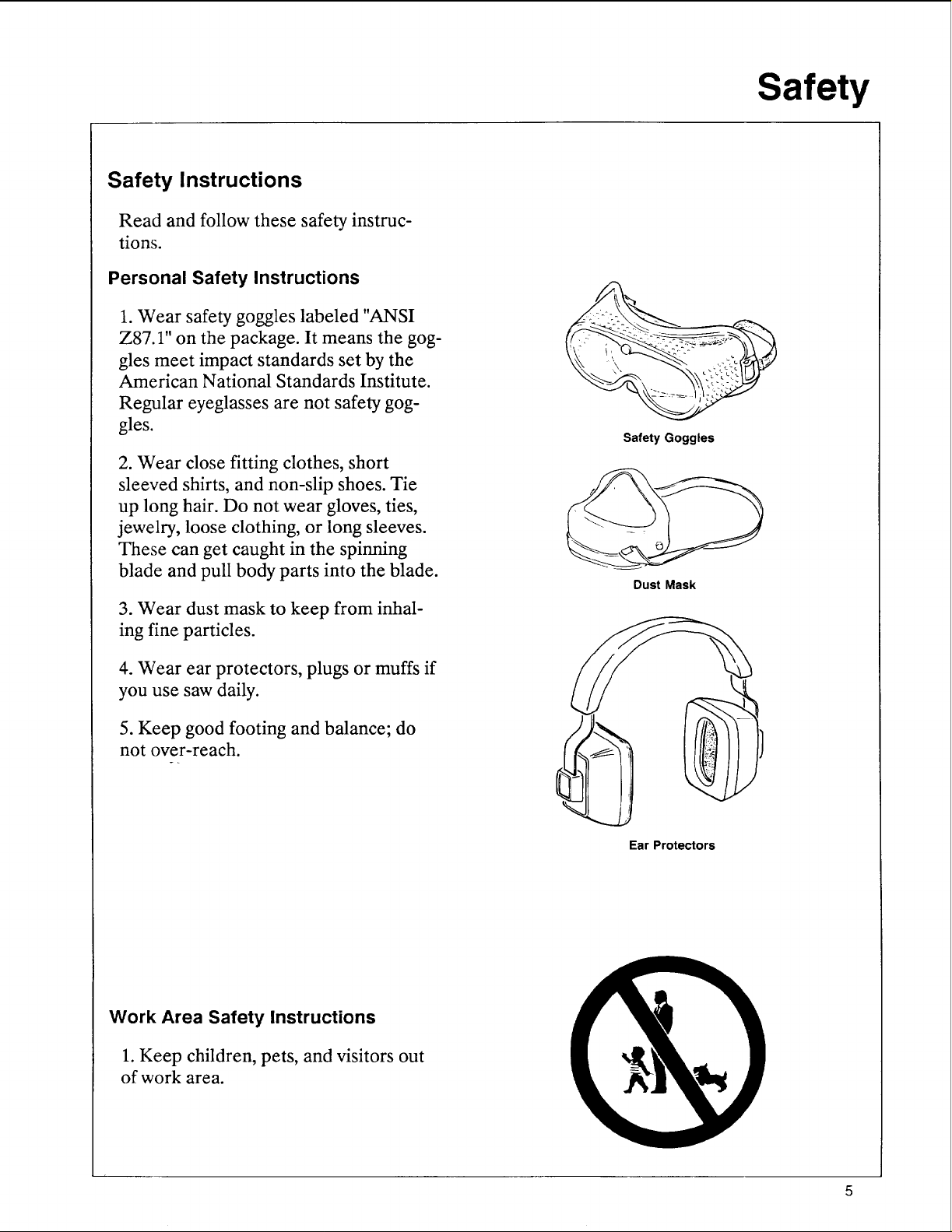
Safety Instructions
Read and follow these safety instruc-
tions.
Personal Safety Instructions
1. Wear safety goggles labeled "ANSI
Z87.1" on the package. It means the gog-
gles meet impact standards set by the
American National Standards Institute.
Regular eyeglasses are not safety gog-
gles.
2. Wear close fitting clothes, short
sleeved shirts, and non-slip shoes. Tie
up long hair. Do not wear gloves, ties,
jewelry, loose clothing, or long sleeves.
These can get caught in the spinning
blade and pull body parts into the blade.
Safety
Safety Goggles
Dust Mask
3. Wear dust mask to keep from inhal-
ing fine particles.
4. Wear ear protectors, plugs or muffs if
you use saw daily.
5. Keep good footing and balance; do
not over-reach.
Work Area Safety Instructions
of work area.
-L
1. Keep children, pets, and visitors out
Ear Protectors
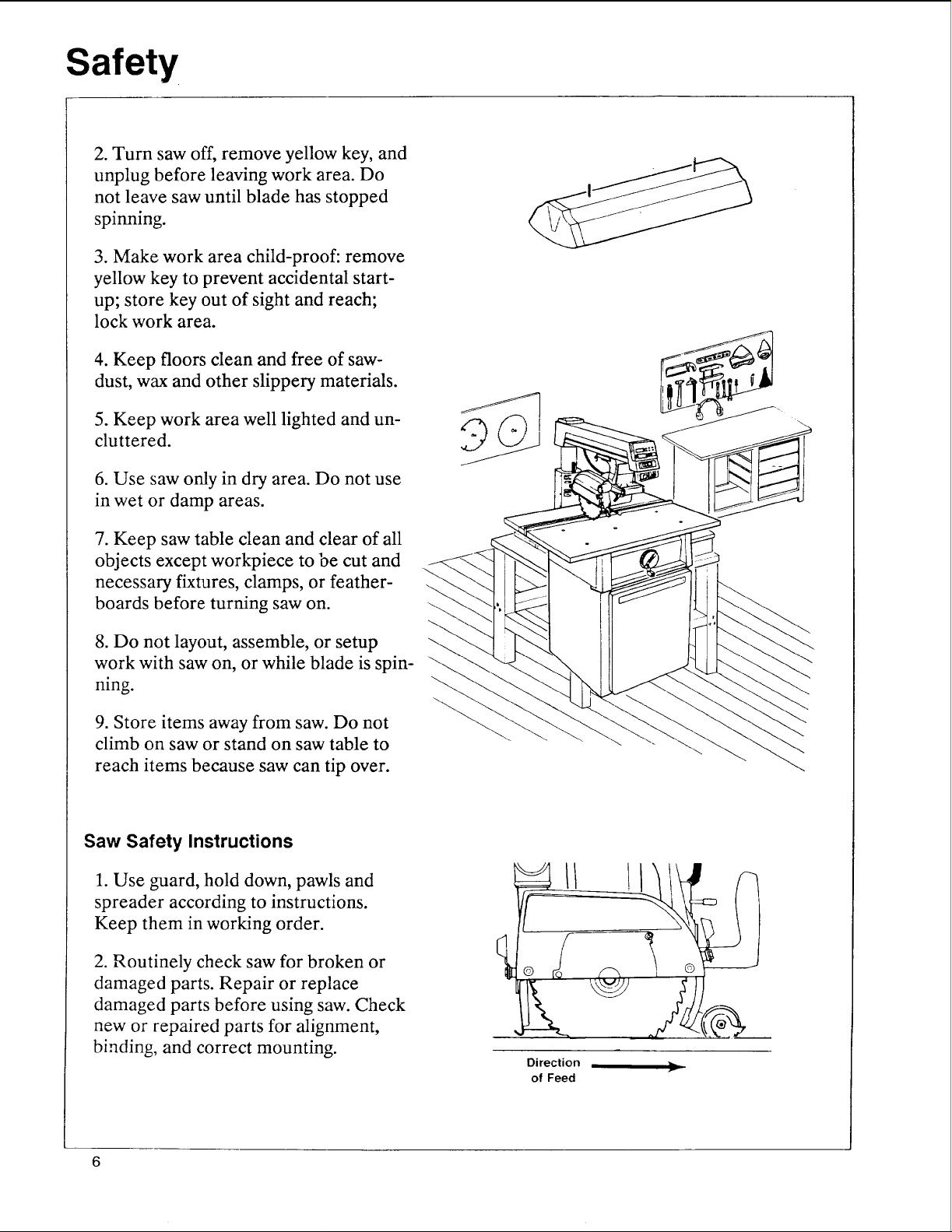
Safety
2. Turn saw off, remove yellow key, and
unplug before leaving work area. Do
not leave saw until blade has stopped
spinning.
3. Make work area child-proof: remove
yellow key to prevent accidental start-
up; store key out of sight and reach;
lock work area.
4. Keep floors clean and free of saw-
dust, wax and other slippery materials.
5. Keep work area well lighted and un-
cluttered.
6. Use saw only in dry area. Do not use
in wet or damp areas.
7. Keep saw table clean and clear of all
objects except workpiece to be cut and
necessary fixtures, clamps, or feather-
boards before turning saw on.
8. Do not layout, assemble, or setup
work with saw on, or while blade is spin-
ning.
9. Store items away from saw. Do not
climb on saw or stand on saw table to
reach items because saw can tip over.
Saw Safety Instructions
1. Use guard, hold down, pawls and
spreader according to instructions.
Keep them in working order.
2. Routinely check saw for broken or
damaged parts. Repair or replace
damaged parts before using saw. Check
new or repaired parts for alignment,
binding, and correct mounting.
Direction
of Feed
6
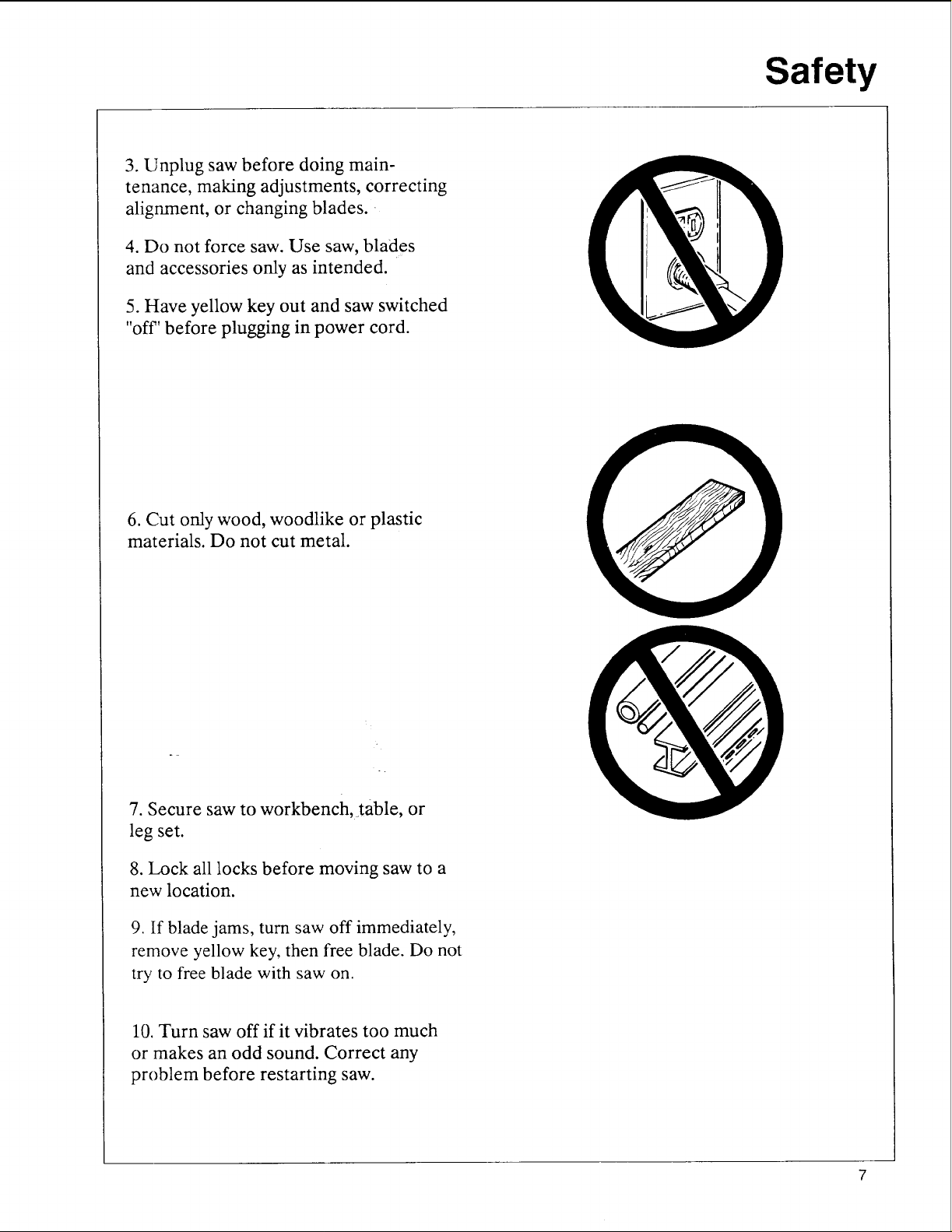
3. Unplug saw before doing main-
tenance, making adjustments, correcting
alignment, or changing blades.
4. Do not force saw. Use saw, blades
and accessories only as intended.
5. Have yellow key out and saw switched
"off' before plugging in power cord.
6. Cut only wood, woodlike or plastic
materials. Do not cut metal.
Safety
7. Secure saw to workbench, table, or
leg set.
8. Lock all locks before moving saw to a
new location.
9. If blade jams, turn saw off immediately,
remove yellow key, then free blade. Do not
try to free blade with saw on.
10. Turn saw off if it vibrates too much
or makes an odd sound. Correct any
problem before restarting saw.
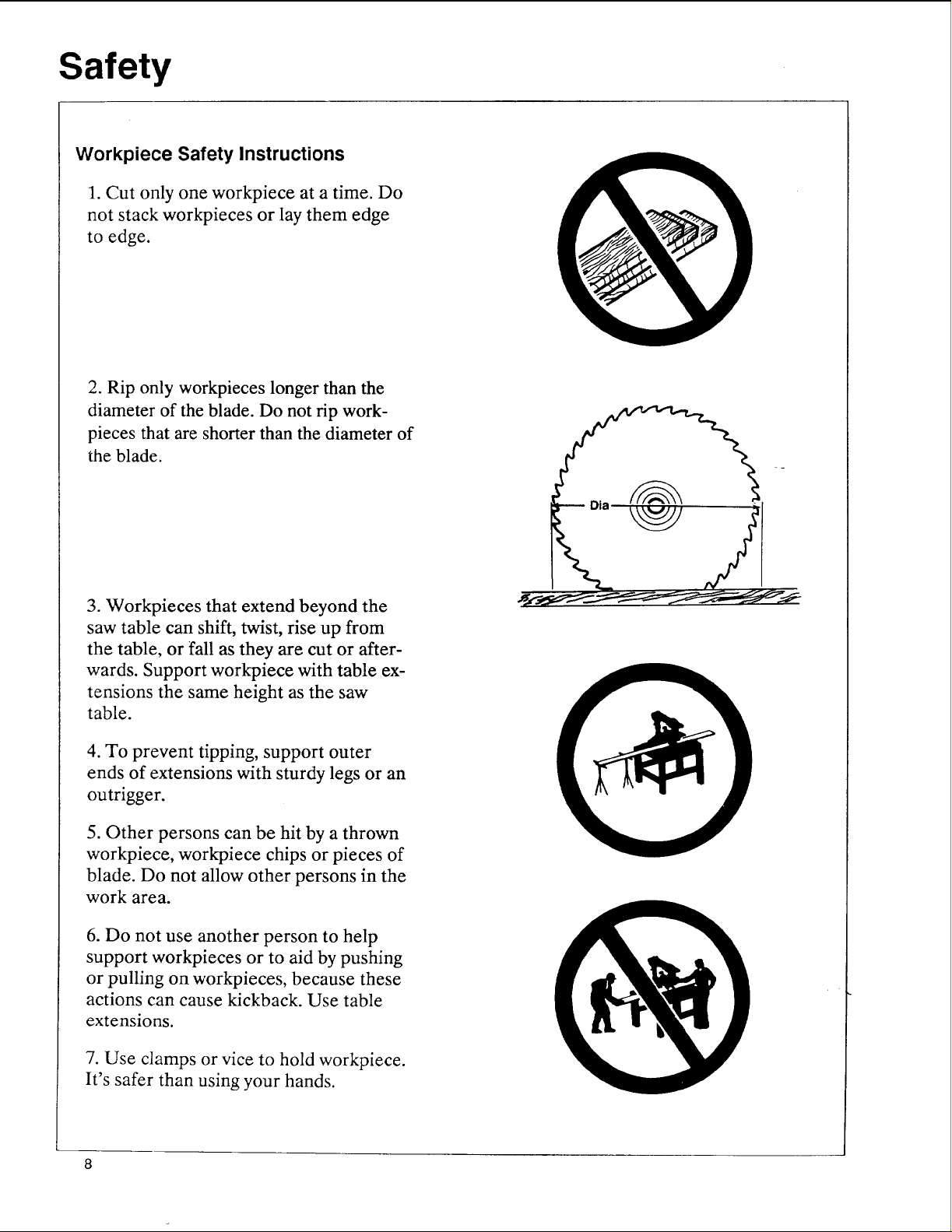
Safety
Workpiece Safety Instructions
1. Cut only one workpiece at a time. Do
not stack workpieces or lay them edge
to edge.
2. Rip only workpieces longer than the
diameter of the blade. Do not rip work-
pieces that are shorter than the diameter of
the blade.
3. Workpieces that extend beyond the
saw table can shift, twist, rise up from
the table, or fall as they are cut or after-
wards. Support workpiece with table ex-
tensions the same height as the saw
table.
4. To prevent tipping, support outer
ends of extensions with sturdy legs or an
outrigger.
5. Other persons can be hit by a thrown
workpiece, workpiece chips or pieces of
blade. Do not allow other persons in the
work area.
6. Do not use another person to help
support workpieces or to aid by pushing
or pulling on workpieces, because these
actions can cause kickback. Use table
extensions.
7. Use clamps or vice to hold workpiece.
It's safer than using your hands.
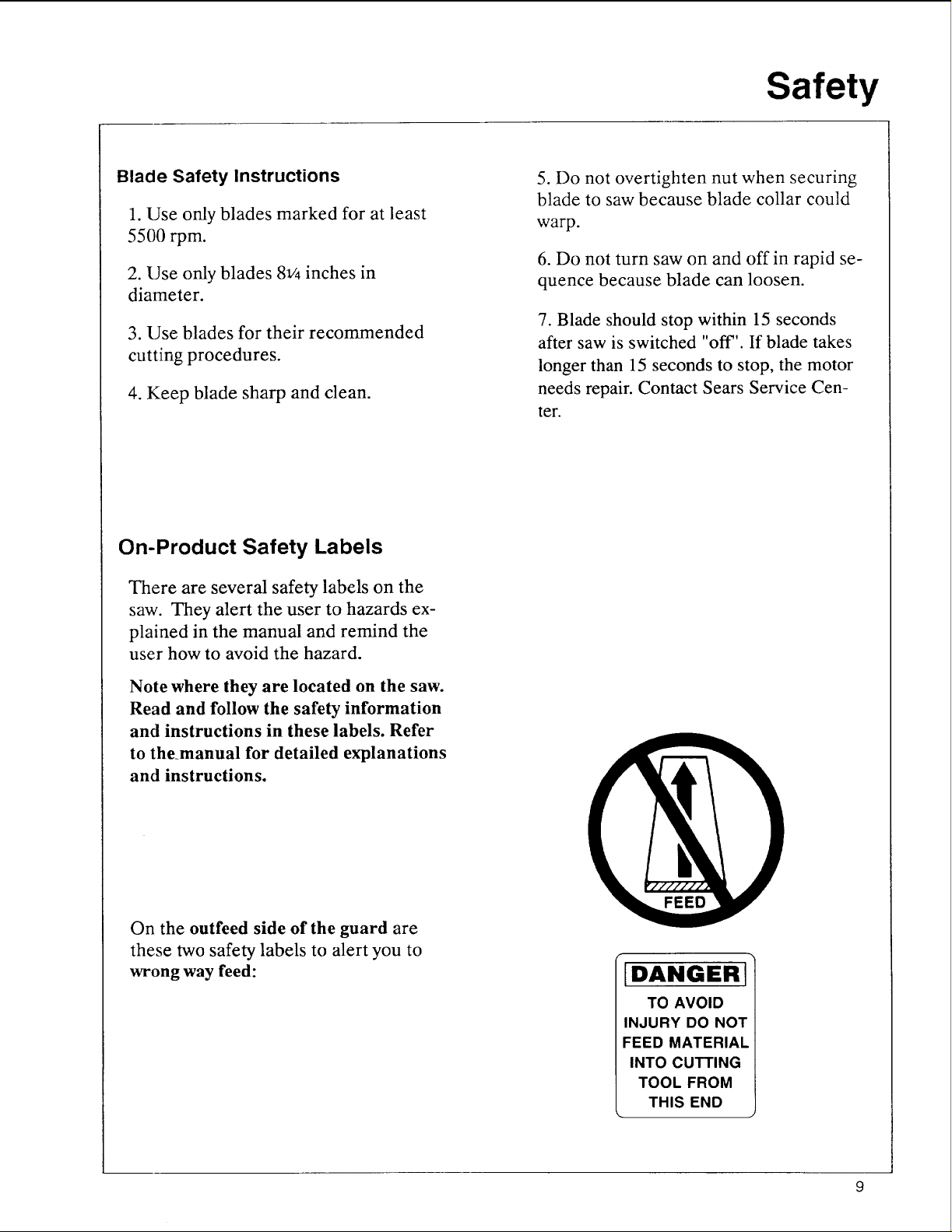
Safety
Blade Safety Instructions
1. Use only blades marked for at least
5500 rpm.
2. Use only blades 81/4inches in
diameter.
3. Use blades for their recommended
cutting procedures.
4. Keep blade sharp and clean.
On-Product Safety Labels
There are several safety labels on the
saw. They alert the user to hazards ex-
plained in the manual and remind the
user how to avoid the hazard.
5. Do not overtighten nut when securing
blade to saw because blade collar could
warp.
6. Do not turn saw on and off in rapid se-
quence because blade can loosen.
7. Blade should stop within 15 seconds
after saw is switched "off". If blade takes
longer than 15 seconds to stop, the motor
needs repair. Contact Sears Service Cen-
ter.
Note where they are located on the saw.
Read and follow the safety information
and instructions in these labels. Refer
to themanual for detailed explanations
and instructions.
On the outfeed side of the guard are
these two safety labels to alert you to
wrong way feed:
DANGERM
TO AVOID
INJURY DO NOT
FEED MATERIAL
INTO CUTTING
TOOL FROM
THIS END
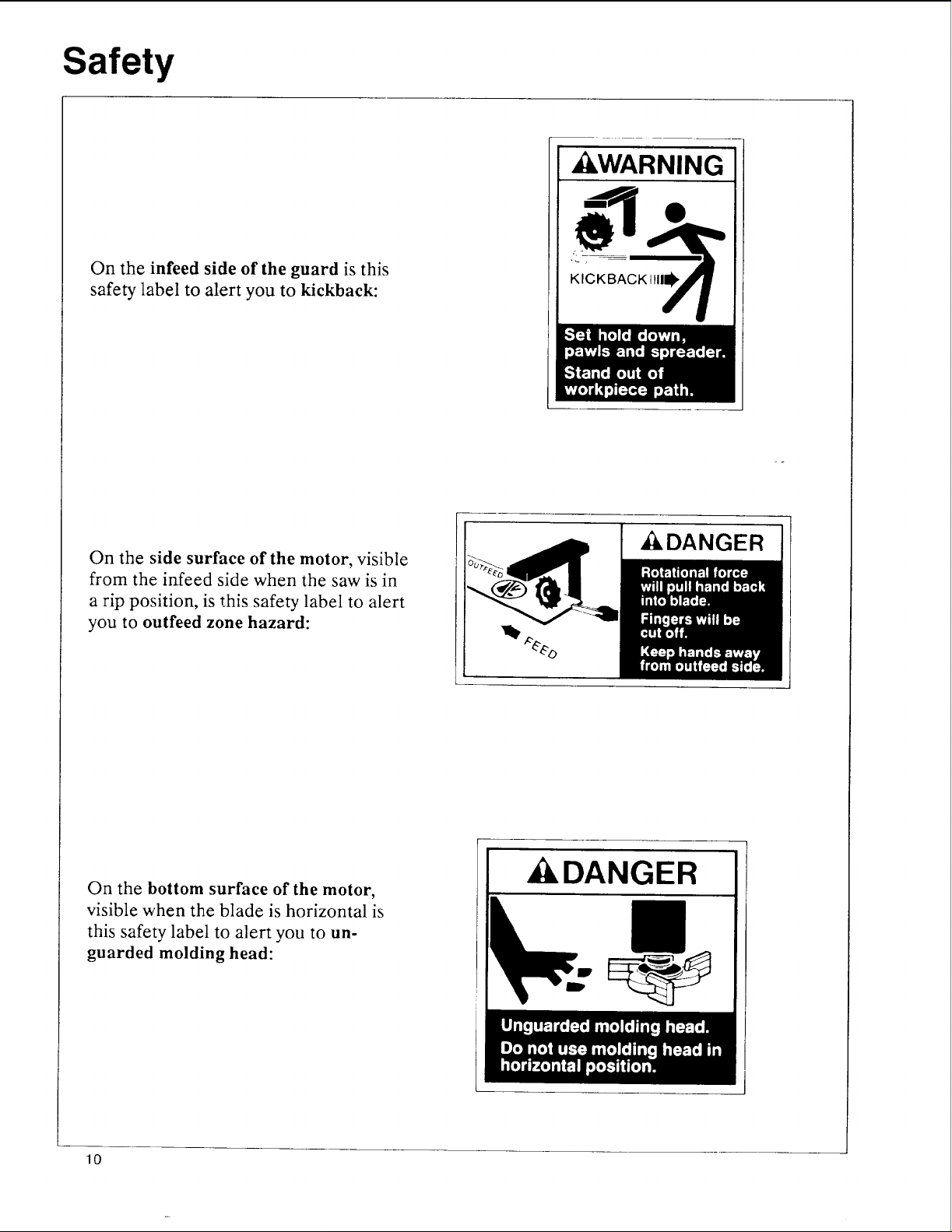
Safety
kWARNING
On the infeed side of the guard is this
safety label to alert you to kickback:
On the side surface of the motor, visible
from the in_feed side when the saw is in
a rip position, is this safety label to alert
you to outfeed zone hazard:
KICKBACK IIII
DANGER
On the bottom surface of the motor,
visible when the blade is horizontal is
this safety label to alert you to un-
guarded molding head:
10
kDANGER
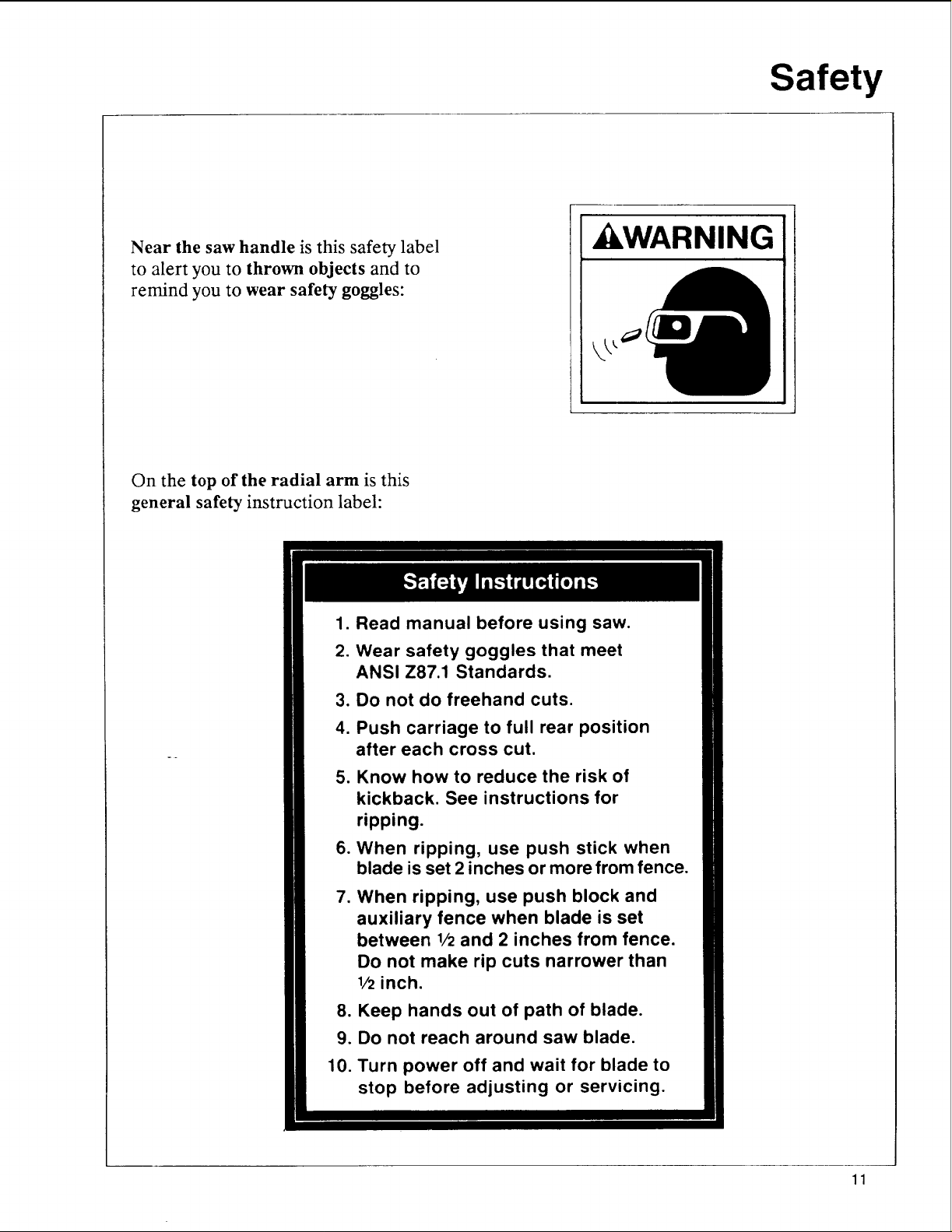
Safety
Near the saw handle is this safety label
to alert you to thrown objects and to
remind you to wear safety goggles:
On the top of the radial arm is this
general safety instruction label:
1. Read manual before using saw.
2. Wear safety goggles that meet
ANSI Z87.1 Standards.
, WARNING
3. Do not do freehand cuts.
4. Push carriage to full rear position
after each cross cut.
5. Know how to reduce the risk of
kickback. See instructions for
ripping.
6. When ripping, use push stick when
blade is set 2 inches or more from fence.
7. When ripping, use push block and
auxiliary fence when blade is set
between 1/2and 2 inches from fence.
Do not make rip cuts narrower than
1/2inch.
8. Keep hands out of path of blade.
9. Do not reach around saw blade.
10. Turn power off and wait for blade to
stop before adjusting or servicing.
11
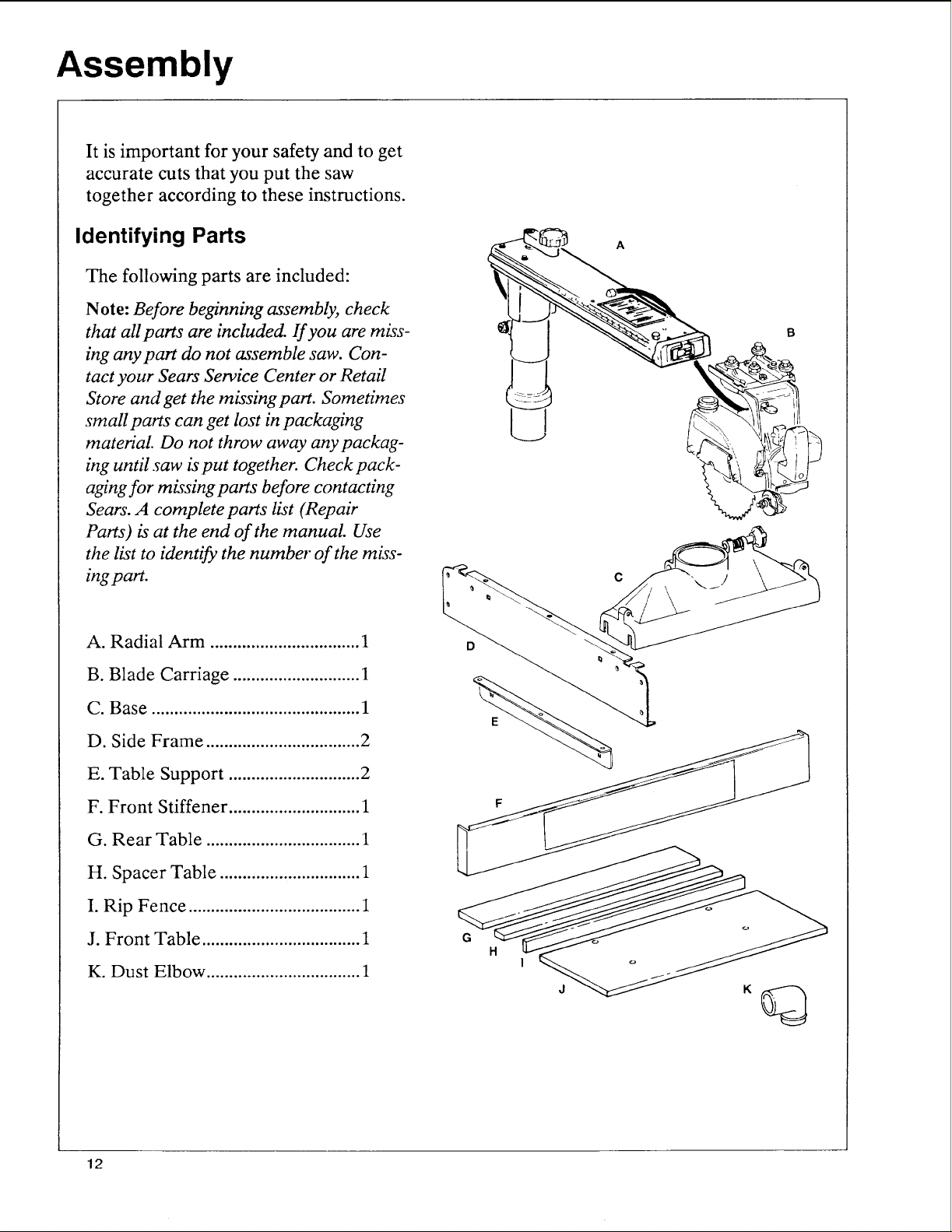
Assembly
It is important for your safety and to get
accurate cuts that you put the saw
together according to these instructions.
Identifying Parts
The following parts are included:
Note: Before beginning assembly, check
that aU parts are included. If you are miss-
ing any part do not assemble saw. Con-
tact your Sears Service Center or Retail
Store and get the missing part. Sometimes
small parts can get lost in packaging
material Do not throw away any packag-
ing until saw is put together. Check pack-
aging for missing parts before contacting
Sears. A complete parts list (Repair
Parts) is at the end of the manual Use
the list to identify the number of the miss-
ing part.
B
C
A. Radial Arm ................................. 1
B. Blade Carriage ............................ 1
C. Base .............................................. 1
D. Side Frame .................................. 2
E. Table Support ............................. 2
F. Front Stiffener ............................. 1
G. Rear Table .................................. 1
H. Spacer Table ............................... 1
I. Rip Fence ...................................... 1
J. Front Table ................................... 1
K. Dust Elbow .................................. 1
D
F
12
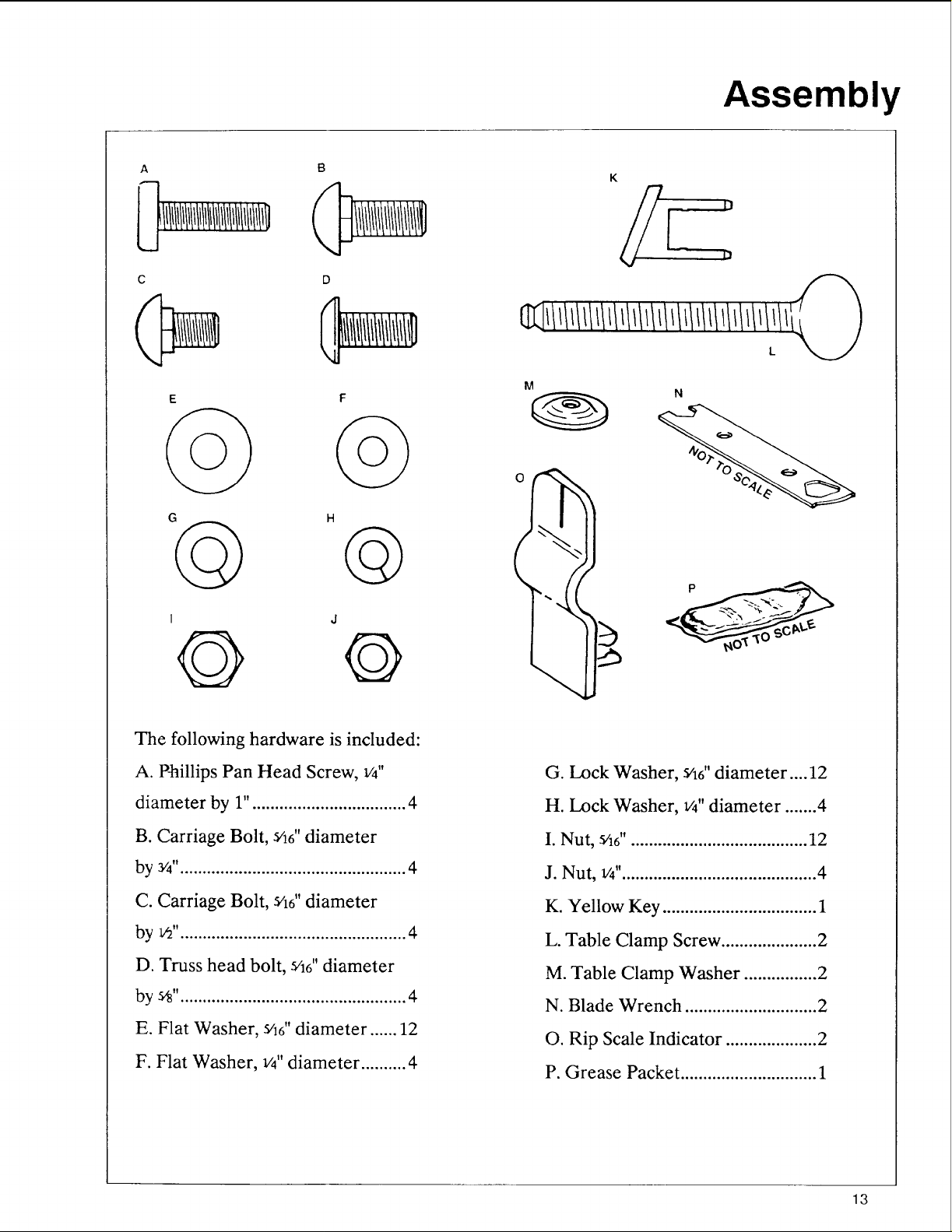
A
c D
Assembly
I]
E F
G H
@ @
I J
O o
The following hardware is included:
A. Phillips Pan Head Screw, v4"
diameter by 1" .................................. 4
M
O
G. Lock Washer, s¢16"diameter .... 12
H. Lock Washer, v4" diameter ....... 4
N
B. Carriage Bolt, Y,6"diameter
by a/4".................................................. 4
C. Carriage Bolt, Y16"diameter
by _" .................................................. 4
D. Truss head bolt, s/16"diameter
by s_". ................................................. 4
E. Flat Washer, Y16"diameter ...... 12
F. Flat Washer, v4" diameter .......... 4
I. Nut, s¢16"....................................... 12
J. Nut, v4"........................................... 4
K. Yellow Key .................................. 1
L. Table Clamp Screw ..................... 2
M. Table Clamp Washer ................ 2
N. Blade Wrench ............................. 2
O. Rip Scale Indicator .................... 2
P. Grease Packet .............................. 1
13
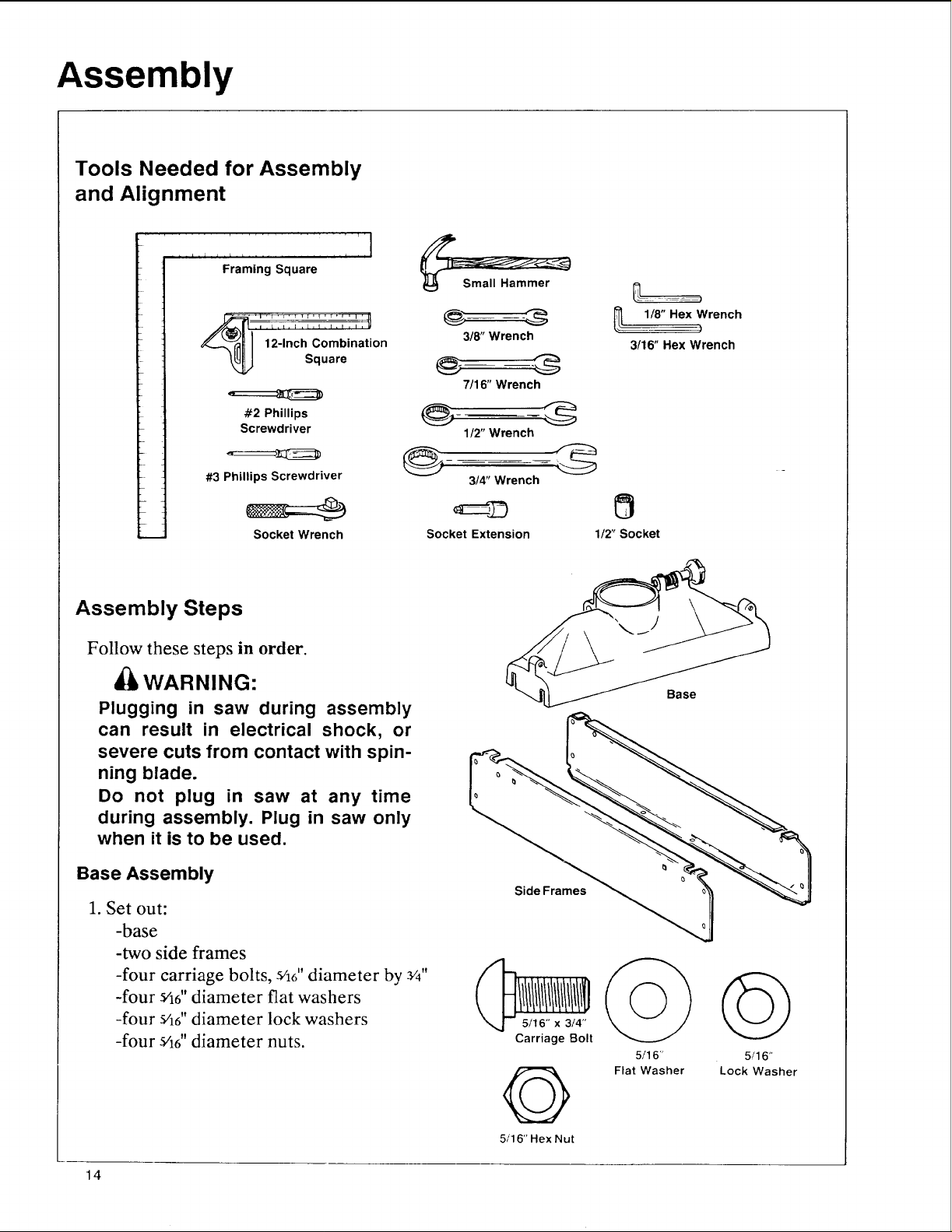
Assembly
Tools Needed for Assembly
and Alignment
1 • *l
iI ,lli I ,L,L,I ,i ,i , i, I,_,
Framing Square
12-Inch Combination
Square
#2 Phillips
Screwdriver
#3 Phillips Screwdriver
Socket Wrench
Assembly Steps
Follow these steps in order.
WARNING:
Plugging in saw during assembly
can result in electrical shock, or
severe cuts from contact with spin-
ning blade.
Do not plug in saw at any time
during assembly. Plug in saw only
when it is to be used.
Base Assembly
3/8" Wrench
@ G
7/16" Wrench
1/2" Wrench
6
3/4" Wrench
Socket Extension 1/2" Socket
_ 1/8" Hex Wrench
3/16" Hex Wrench
o
0
1. Set out:
-base
-two side frames
-four carriage bolts, _¢16"diameter by _4"
-four g16" diameter flat washers
-four s/16" diameter lock washers
-four s/16" diameter nuts.
14
5/16" x 3/4"
Carriage Bolt
5/16" 5/16"
Flat Washer Lock Washer
5/16" Hex Nut
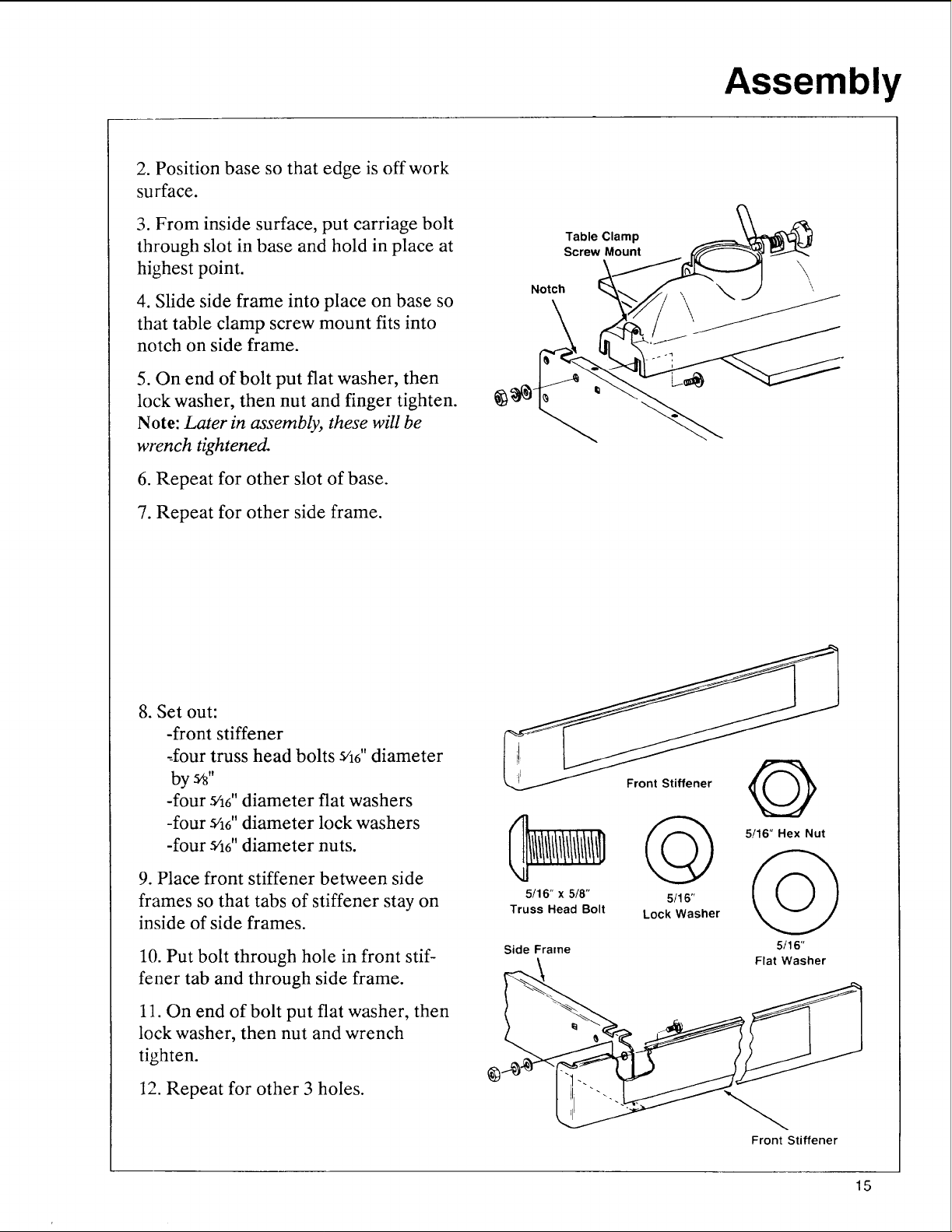
2. Position base so that edge is off work
surface.
Assembly
3. From inside surface, put carriage bolt
through slot in base and hold in place at
highest point.
4. Slide side frame into place on base so
that table clamp screw mount fits into
notch on side frame.
5. On end of bolt put flat washer, then
lock washer, then nut and finger tighten.
Note: Later in assembly, these will be
wrench tightened.
6. Repeat for other slot of base.
7. Repeat for other side frame.
Table Clamp
Screw Mount
Notch
8. Set out:
-front stiffener
,four truss head bolts 5/16'' diameter
by s_"
-four s'16"diameter flat washers
-four 5/16"diameter lock washers
-four s'16"diameter nuts.
9. Place front stiffener between side
frames so that tabs of stiffener stay on
inside of side frames.
10. Put bolt through hole in front stif-
fener tab and through side frame.
11. On end of bolt put flat washer, then
lock washer, then nut and wrench
tighten.
12. Repeat for other 3 holes.
_ 5/16" Hex Nut
5/16" x 5/8" 5/16" _ _ ,) _
Truss Head Bolt Lock Washer
Side Frame 5116"
\ Flat Washer
Front Stiffener
15
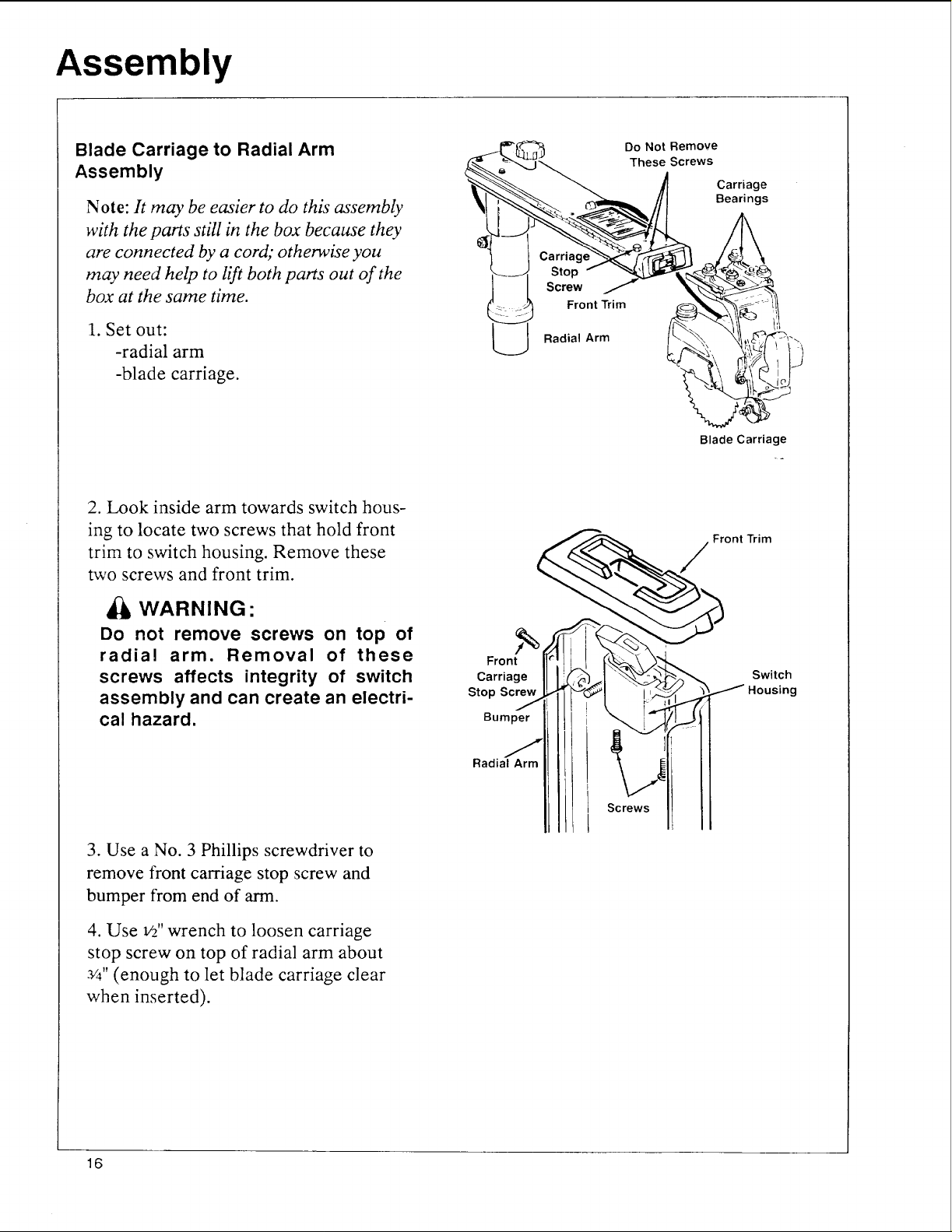
Assembly
Blade Carriage to Radial Arm
Assembly
Note: It may be easier to do this assembly
with the parts still in the box because they
are connected by a cord; otherwise you
may need help to lift both parts out of the
box at the same time.
1. Set out:
-radial arm
-blade carriage.
2. Look inside arm towards switch hous-
ing to locate two screws that hold front
trim to switch housing. Remove these
two screws and front trim.
Do Not Remove
These Screws
Carriage
Bearings
Stop
Screw
Front Trim
Radial Arm
Blade Carriage
WARNING-
Do not remove screws on top of
radia! arm. Removal of these
screws affects integrity of switch
assembly and can create an electri-
cal hazard.
3. Use a No. 3 Phillips screwdriver to
remove front carriage stop screw and
bumper from end of arm.
4. Use v2"wrench to loosen carriage
stop screw on top of radial arm about
a/4"(enough to let blade carriage clear
when inserted).
20: )..
St°BPuS:;eer_ / _
Radial A_rm
Screws
/F_ont Trim
Switch
Housing
16
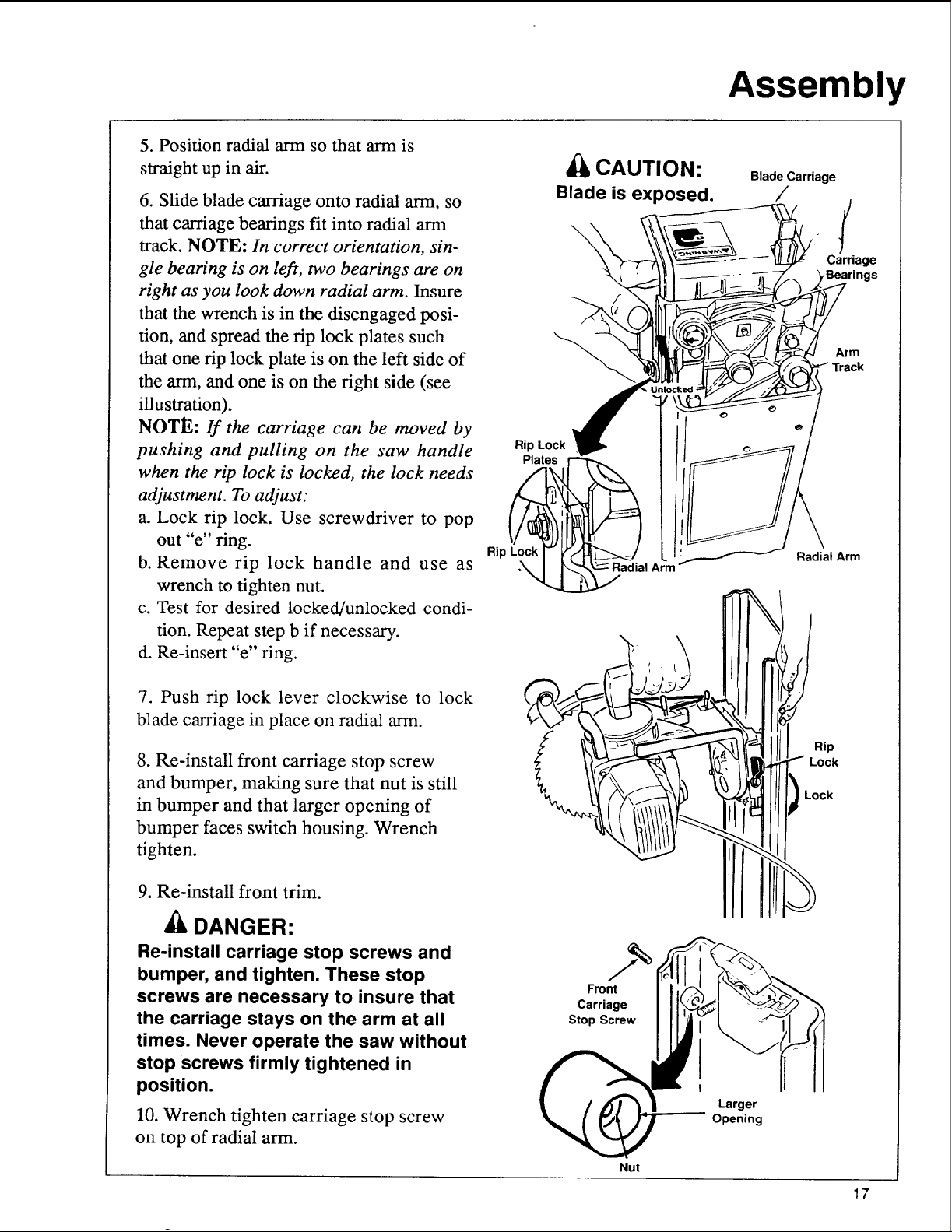
5. Position radial arm so that arm is
straight up in air.
6. Slide blade carriage onto radial arm, so
that carriage bearings fit into radial arm
track. NOTE: In correct orientation, sin-
gle bearing is on left, two bearings are on
right as you look down radial arm. Insure
that the wrench is in the disengaged posi-
tion, and spread the rip lock plates such
that one rip lock plate is on the left side of
the arm, and one is on the right side (see
illustration).
NOTE: If the carriage can be moved by
pushing and pulling on the saw handle
when the rip lock is locked, the lock needs
adjustment. To adjust:
a. Lock rip lock. Use screwdriver to pop
out "e" ring.
b. Remove rip lock handle and use as
wrench to tighten nut.
c. Test for desired locked/unlocked condi-
tion. Repeat step b if necessary.
d. Re-insert "e" ring.
Assembly
CAUTION:
Blade is exposed.
\
Rip Lock ¢
Rip Radial Arm
. _._adia
Blade Carriage
/
(
Carriage
,Bearings
Arm
Track
7. Push rip lock lever clockwise to lock
blade carriage in place on radial arm.
8. Re-install front carriage stop screw
and bumper, making sure that nut is still
in bumper and that larger opening of
bumper faces switch housing. Wrench
tighten.
9. Re-install front trim.
DANGER:
Re-install carriage stop screws and
bumper, and tighten. These stop
screws are necessary to insure that
the carriage stays on the arm at all
times. Never operate the saw without
stop screws firmly tightened in
position.
10. Wrench tighten carriage stop screw
on top of radial arm.
(.
Front
Carriage
Stop Screw
Larger
Opening
Nut
17
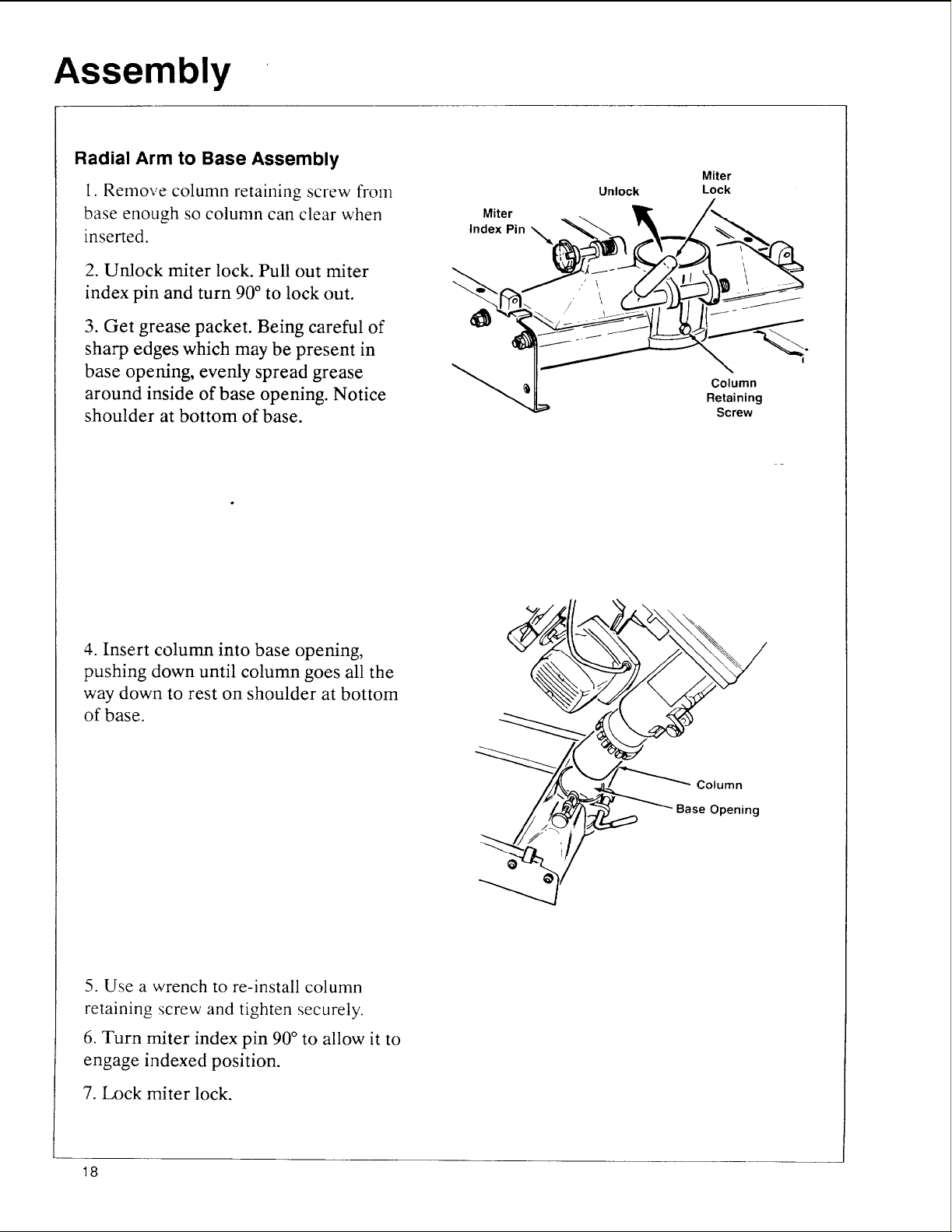
Assembly
Radial Arm to Base Assembly
1. Remove column retaining screw from
base enough so column can clear when
inserted.
2. Unlock miter lock. Pull out miter
index pin and turn 90 ° to lock out.
3. Get grease packet. Being careful of
sharp edges which may be present in
base opening, evenly spread grease
around inside of base opening. Notice
shoulder at bottom of base.
IndMeitxepin"_-_"_ _--i
"-4
Unlock
Miter
Lock
€
\ ,
Column
Retaining
Screw
4. Insert column into base opening,
pushing down until column goes all the
way down to rest on shoulder at bottom
of base.
5. Use a wrench to re-install column
retaining screw and tighten securely.
6. Turn miter index pin 90° to allow it to
engage indexed position.
7. Lock miter lock.
18
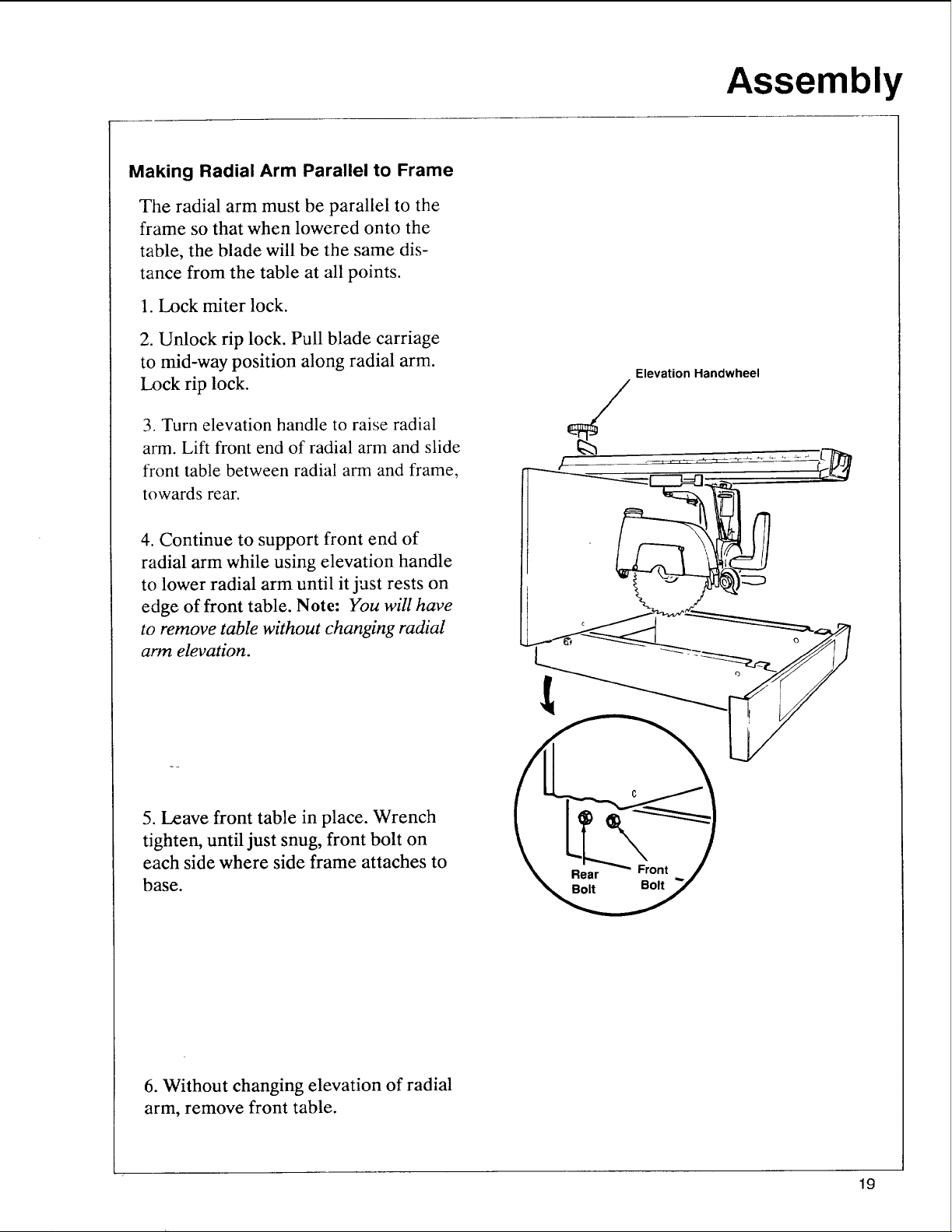
Making Radial Arm Parallel to Frame
The radial arm must be parallel to the
frame so that when lowered onto the
table, the blade will be the same dis-
tance from the table at all points.
1. Lock miter lock.
2. Unlock rip lock. Pull blade carriage
to mid-way position along radial arm.
Lock rip lock.
3 Turn elevation handle to raise radial
arm. Lift front end of radial arm and slide
front table between radial arm and frame,
towards rear.
Assembly
Elevation Handwheel
4. Continue to support front end of
radial arm while using elevation handle
to lower radial arm until it just rests on
edge of front table. Note: You will have
to remove table without changing radial
arm elevation.
5. Leave front table in place. Wrench
tighten, until just snug, front bolt on
each side where side frame attaches to
base.
6. Without changing elevation of radial
arm, remove front table.
19
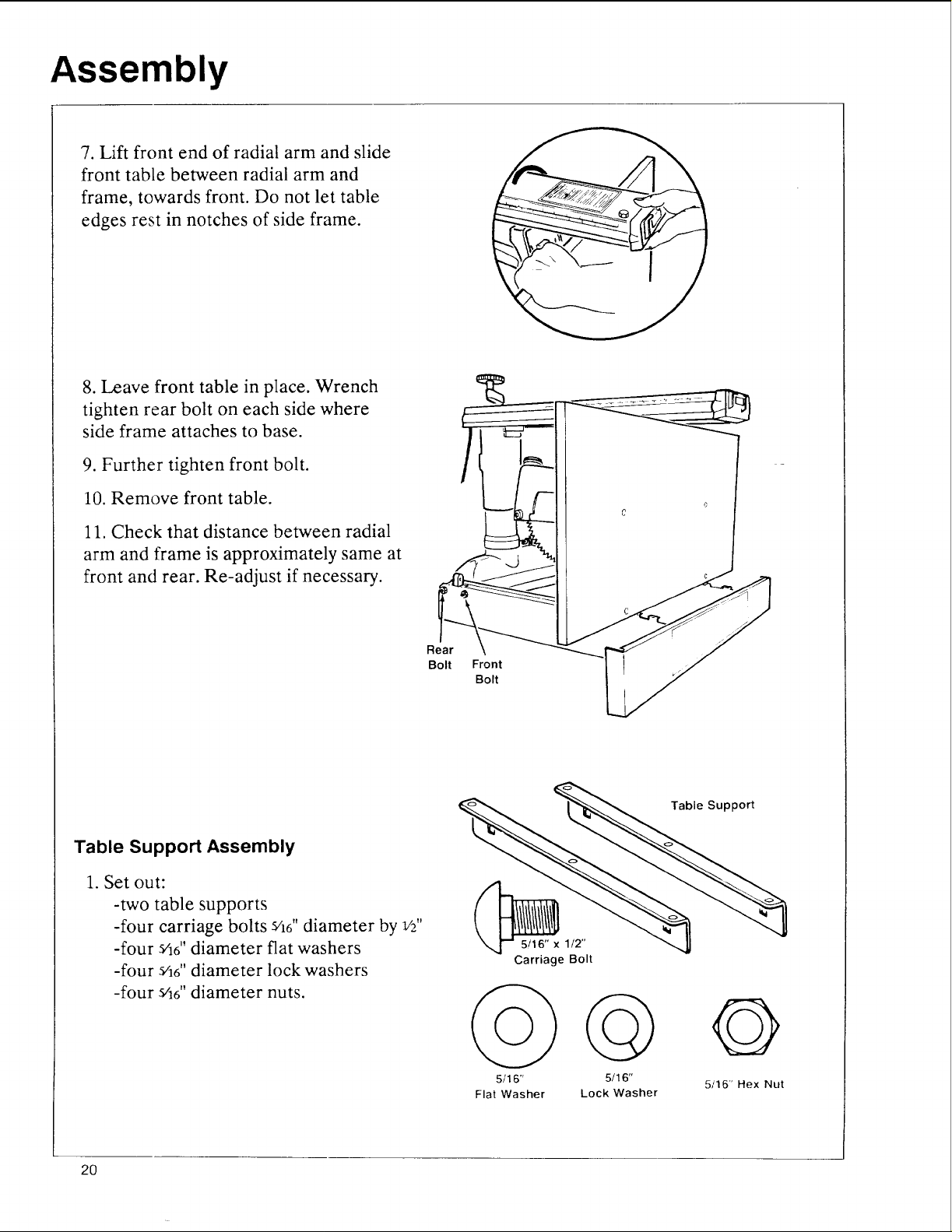
Assembly
7. Lift front end of radial arm and slide
front table between radial arm and
frame, towards front. Do not let table
edges rest in notches of side frame.
8. Leave front table in place. Wrench
tighten rear bolt on each side where
side frame attaches to base.
9. Further tighten front bolt.
10. Remove front table.
11. Check that distance between radial
arm and frame is approximately same at
front and rear. Re-adjust if necessary.
Table Support Assembly
1. Set out:
-two table supports
-four carriage bolts s/16"diameter by v'2"
-four s/16"diameter flat washers
-four 5/16"diameter lock washers
-four s/16"diameter nuts.
Rear
Bolt Front
Bolt
Table Support
5/16" x 1/2"
Carriage Bolt
2O
5/1 6"
Flat Washer
5/16"
Lock Washer
Q
5116" Hex Nut
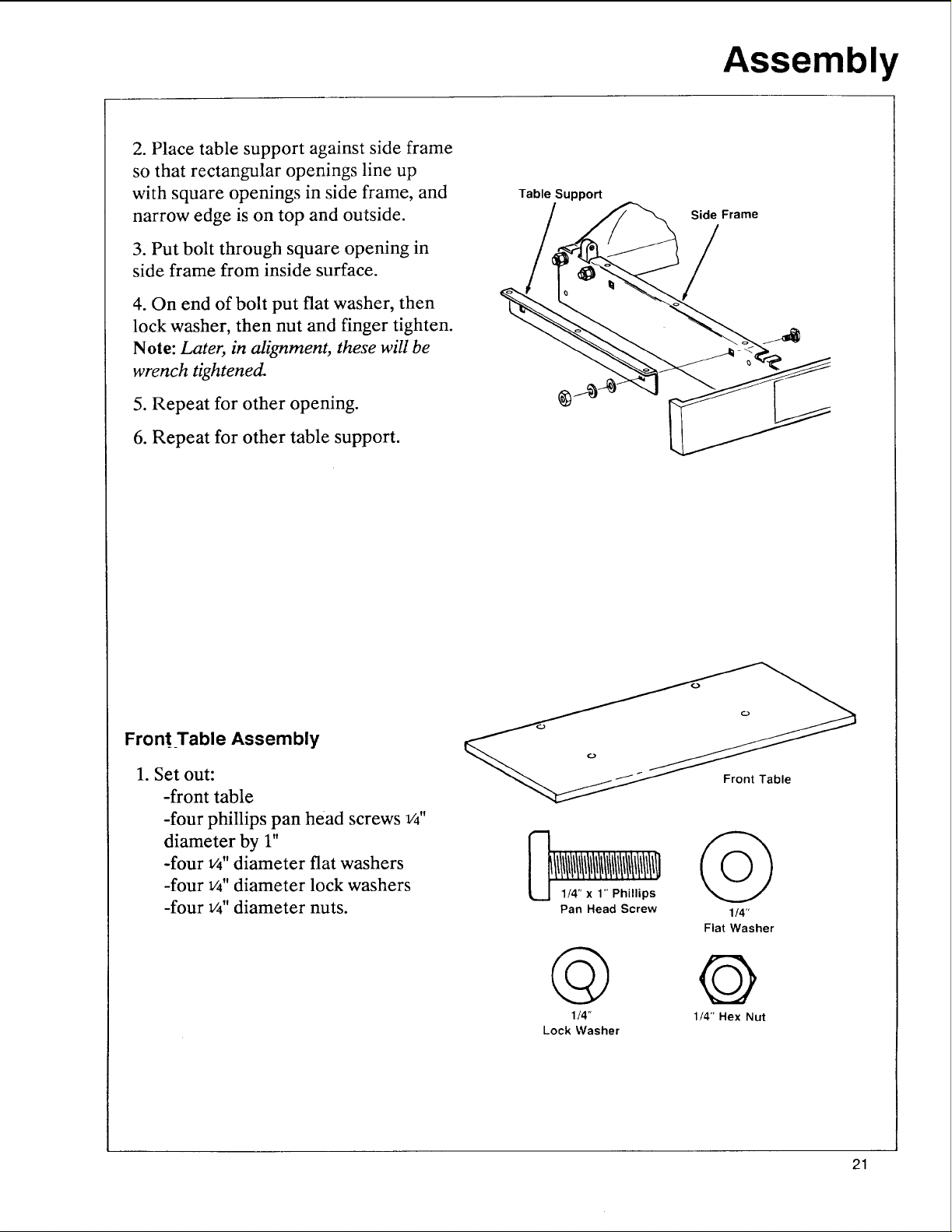
2. Place table support against side frame
so that rectangular openings line up
with square openings in side frame, and
narrow edge is on top and outside.
3. Put bolt through square opening in
side frame from inside surface.
4. On end of bolt put flat washer, then
lock washer, then nut and finger tighten.
Note: Later, in alignment, these will be
wrench tightened.
5. Repeat for other opening.
6. Repeat for other table support.
Assembly
Table Suppo_
Side Frame
FrontTable Assembly
1. Set out:
-front table
-four phillips pan head screws v'4"
diameter by 1"
-four 1/4"diameter flat washers
-four 1/4"diameter lock washers
-four 1/4"diameter nuts.
1/4" x 1" Phillips
Pan Head Screw
Flat Washer
Q Q
1/4" 1/4" Hex Nut
Lock Washer
1/4"
21
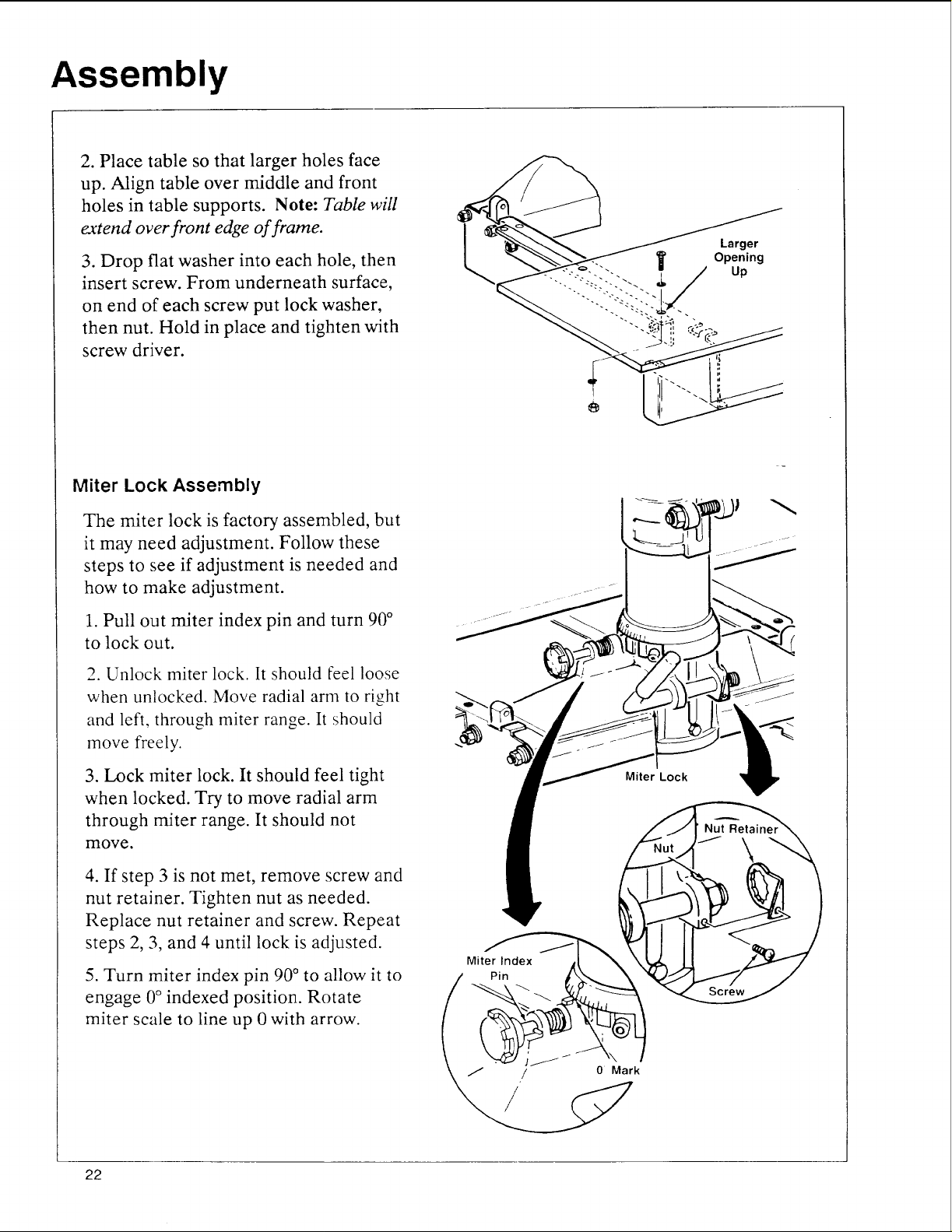
Assembly
2. Place table so that larger holes face
up. Align table over middle and front
holes in table supports. Note: Table will
extend over front edge of frame.
3. Drop flat washer into each hole, then
insert screw. From underneath surface,
on end of each screw put lock washer,
then nut. Hold in place and tighten with
screw driver.
Miter Lock Assembly
The miter lock is factory assembled, but
it may need adjustment. Follow these
steps to see if adjustment is needed and
how to make adjustment.
Larger
Opening
Up
®
1. Pull out miter index pin and turn 90 °
to lock out.
2. Unlock miter lock. It should feel loose
when unlocked. Move radial arm to right
and left, through miter range. It should
move freely.
3. Lock miter lock. It should feel tight
when locked. Try to move radial arm
through miter range. It should not
move.
4. If step 3 is not met, remove screw and
nut retainer. Tighten nut as needed.
Replace nut retainer and screw. Repeat
steps 2, 3, and 4 until lock is adjusted.
5. Turn miter index pin 90 ° to allow it to
engage 0 ° indexed position. Rotate
miter scale to line up 0 with arrow.
Miter Lock
Miter Index
0 Mark
22
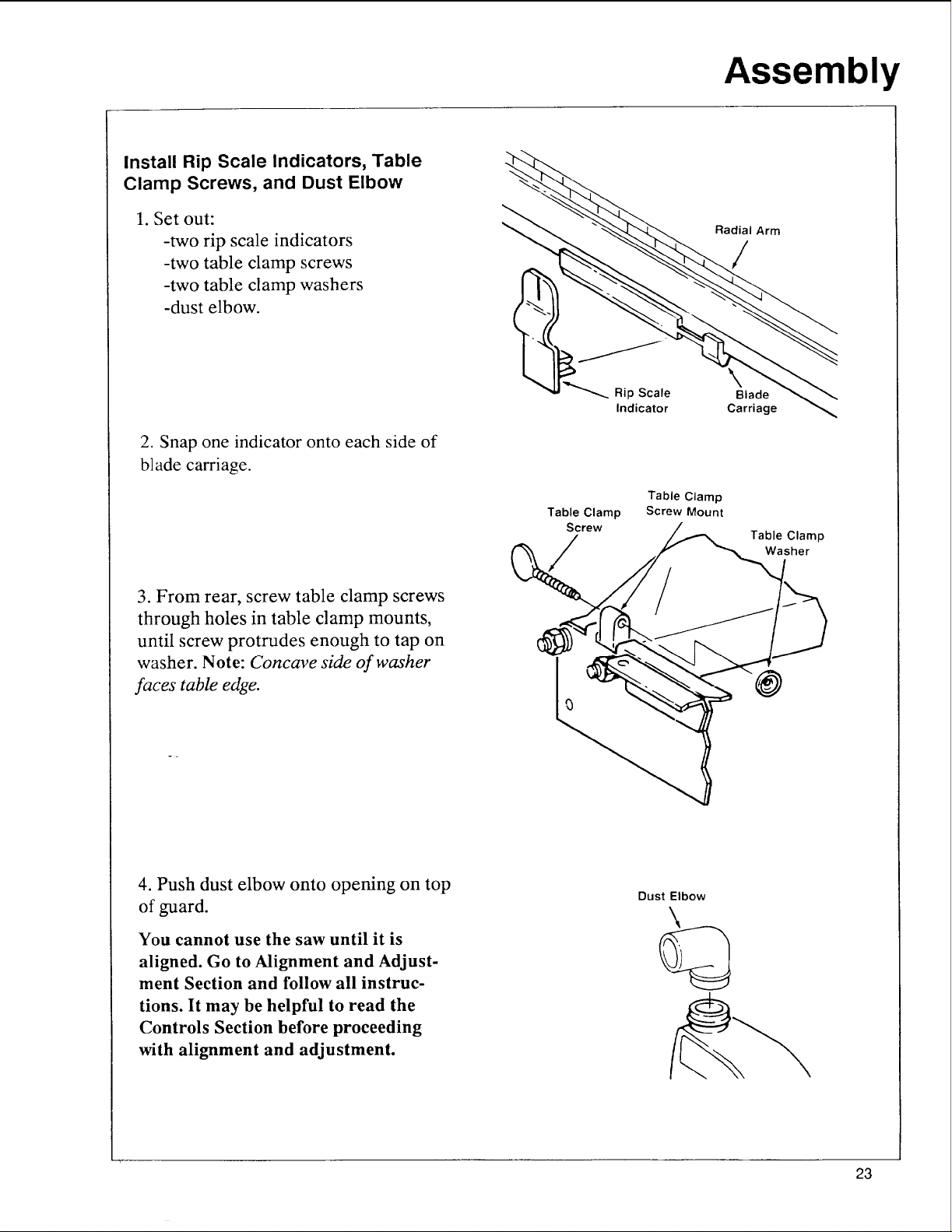
Install Rip Scale Indicators, Table
Clamp Screws, and Dust Elbow
Assembly
1. Set out:
-two rip scale indicators
-two table clamp screws
-two table clamp washers
-dust elbow.
2. Snap one indicator onto each side of
blade carriage.
3. From rear, screw table clamp screws
through holes in table clamp mounts,
until screw protrudes enough to tap on
washer. Note: Concave side of washer
faces table edge.
i_"_ Rip Scale
Indicator
Table Clamp
Screw
/
Radial Arm
/
Blade
Carriage
Table Clamp
Screw Mount
Table Clamp
Washer
4. Push dust elbow onto opening on top
of guard.
You cannot use the saw until it is
aligned. Go to Alignment and Adjust-
ment Section and follow all instruc-
tions. It may be helpful to read the
Controls Section before proceeding
with alignment and adjustment.
Dust Elbow
23
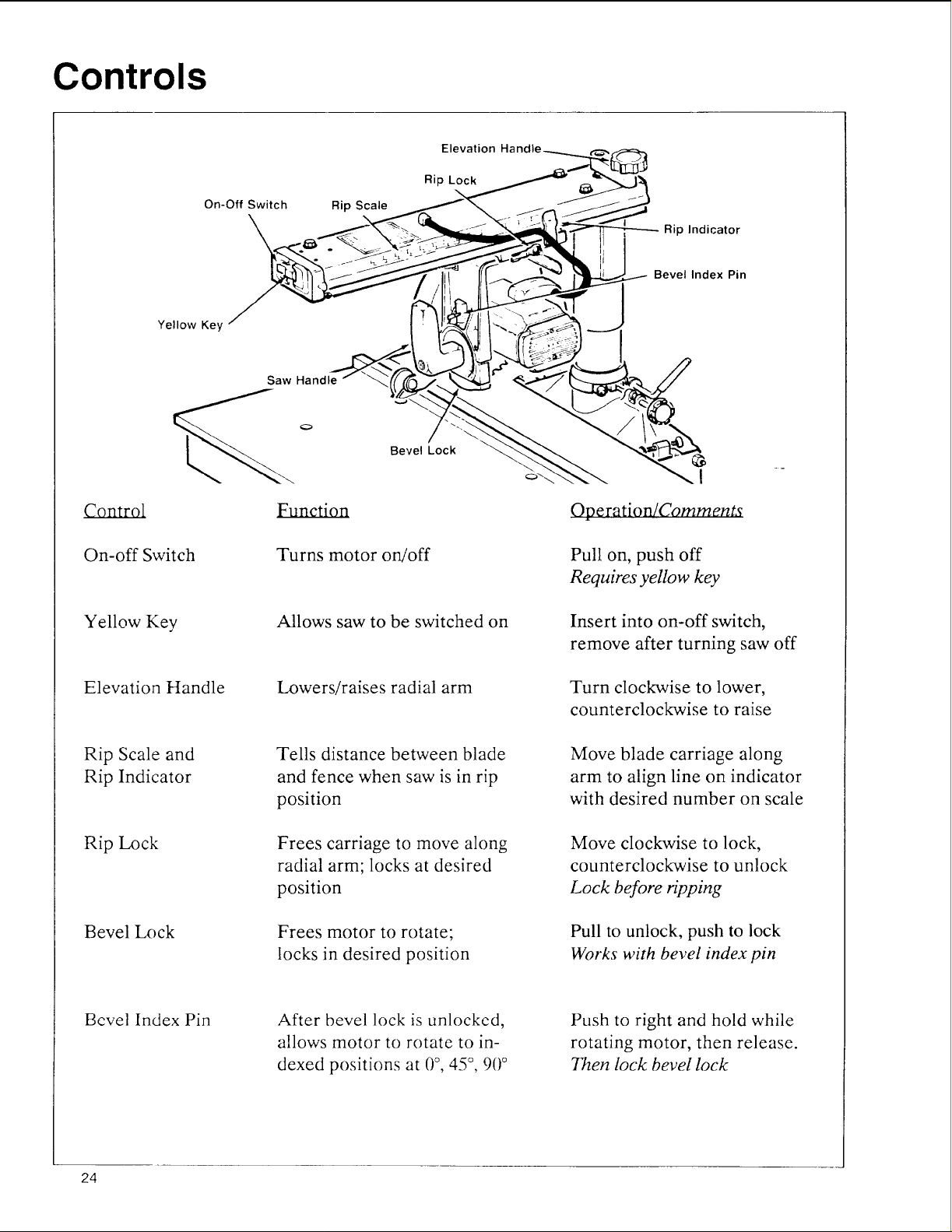
Controls
Yellow Key
On-Off Switch
\
Elevation
Rip Lock
Rip Scale
Rip Indicator
Bevel Index Pin
Saw Handle
Bevel Lock
I
Control
On-off Switch
Yellow Key
Elevation Handle
Rip Scale and
Rip Indicator
Rip Lock
Bevel I_x)ck
Turns motor on/off
Allows saw to be switched on
Lowers/raises radial arm
Tells distance between blade
and fence when saw is in rip
position
Frees carriage to move along
radial arm; locks at desired
position
Frees motor to rotate;
locks in desired position
Operation/Commentt
Pull on, push off
Requires yellow key
Insert into on-off switch,
remove after turning saw off
Turn clockwise to lower,
counterclockwise to raise
Move blade carriage along
arm to align line on indicator
with desired number on scale
Move clockwise to lock,
counterclockwise to unlock
Lock before ripping
Pull to unlock, push to lock
Works with bevel index pin
Bevel Index Pin
24
After bevel lock is unlocked,
allows motor to rotate to in-
dexed positions at 0°, 45 °, 90 °
Push to right and hold while
rotating motor, then release.
Then lock bevel lock
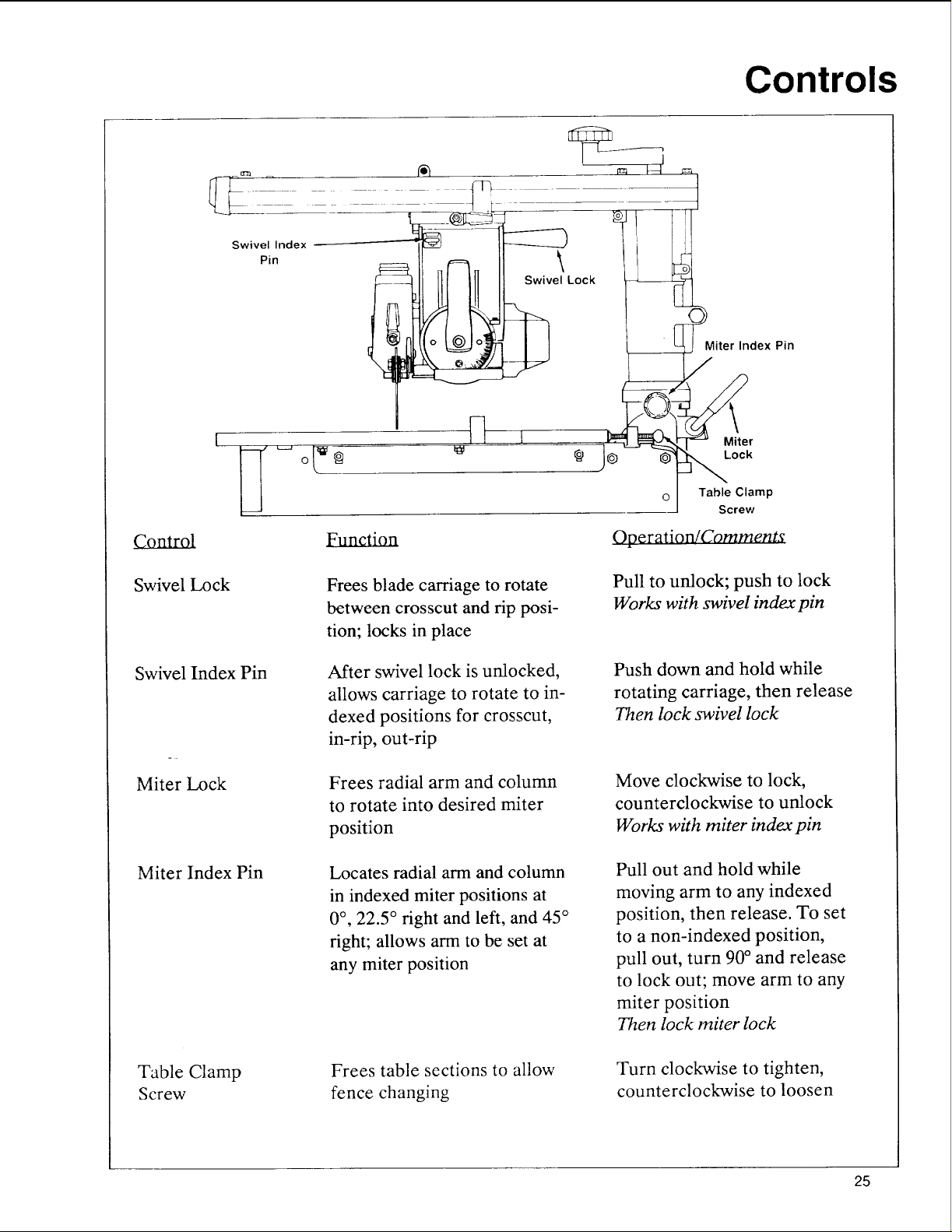
Swivel Index _
Pin
Controls
Swivel Lock
Miter Index Pin
Miter
_ Lock
Control
Swivel Lock
Function
Frees blade carriage to rotate
between crosscut and rip posi-
tion; locks in place
Swivel Index Pin
After swivel lock is unlocked,
allows carriage to rotate to in-
dexed positions for crosscut,
in-rip, out-rip
Miter Lock
Frees radial arm and column
to rotate into desired miter
position
Miter Index Pin Locates radial arm and column
in indexed miter positions at
0 °, 22.5 ° right and left, and 45 °
right; allows arm to be set at
any miter position
o Table Clamp
Screw
Operation!Comments
Pull to unlock; push to lock
Works with swivel index pin
Push down and hold while
rotating carriage, then release
Then lock swivel lock
Move clockwise to lock,
counterclockwise to unlock
Works with miter index pin
Pull out and hold while
moving arm to any indexed
position, then release. To set
to a non-indexed position,
pull out, turn 90° and release
to lock out; move arm to any
miter position
Then lock miter lock
Table Clamp
Screw
Frees table sections to allow
fence changing
Turn clockwise to tighten,
counterclockwise to loosen
25
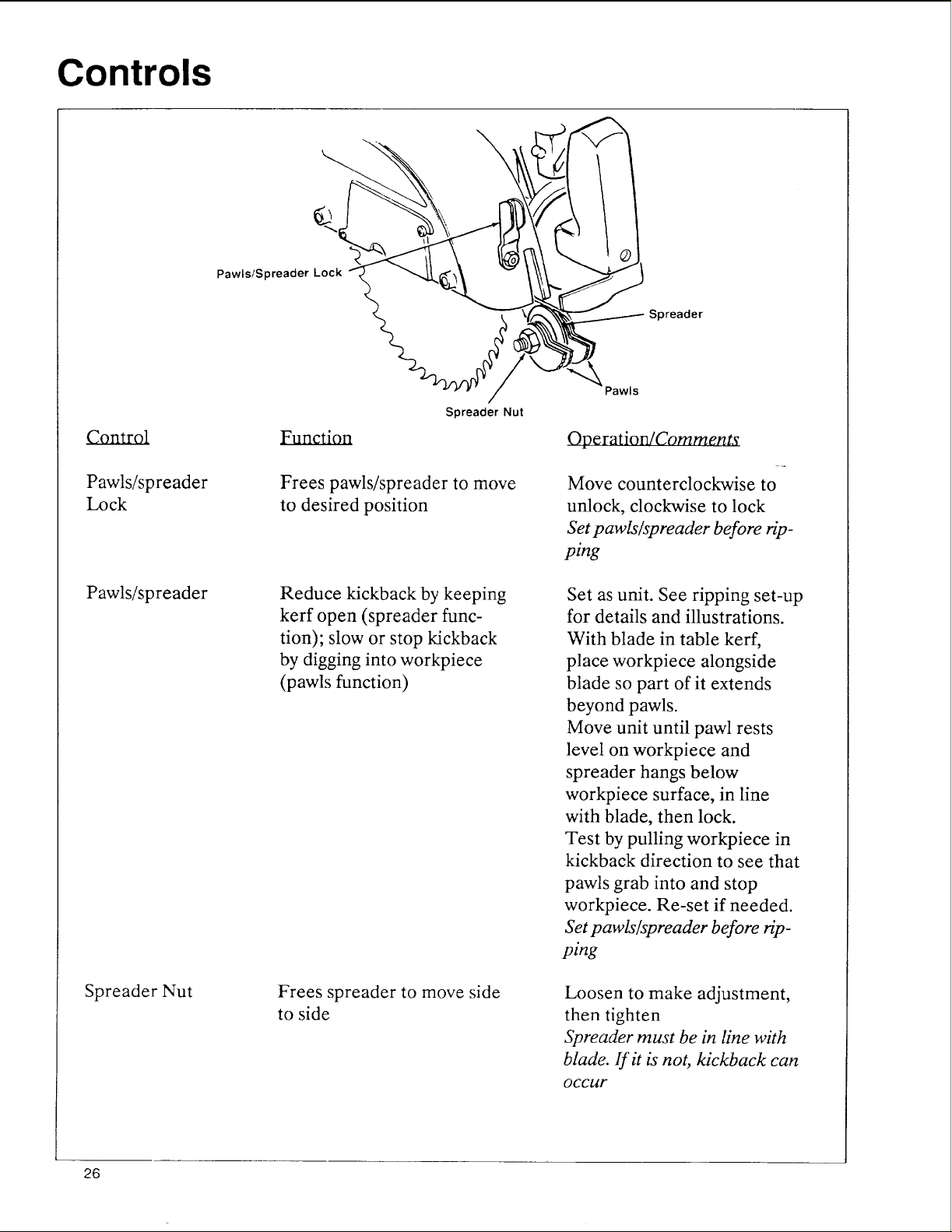
Controls
Control
\
Pawls/Spreader Lock
Spreader
Pawls
Spreader Nut
Operation/Comments
Pawls/spreader
Lock
Pawls/spreader
Frees pawls/spreader to move
to desired position
Reduce kickback by keeping
kerr open (spreader func-
tion); slow or stop kickback
by digging into workpiece
(pawls function)
Move counterclockwise to
unlock, clockwise to lock
Set pawls/spreader before rip-
ping
Set as unit. See ripping set-up
for details and illustrations.
With blade in table kerr,
place workpiece alongside
blade so part of it extends
beyond pawls.
Move unit until pawl rests
level on workpiece and
spreader hangs below
workpiece surface, in line
with blade, then lock.
Test by pulling workpiece in
kickback direction to see that
pawls grab into and stop
workpiece. Re-set if needed.
Set pawls/spreader before rip-
ping
Spreader Nut
26
Frees spreader to move side
to side
Loosen to make adjustment,
then tighten
Spreader must be & line with
blade. If it is not, kickback can
OCClAF
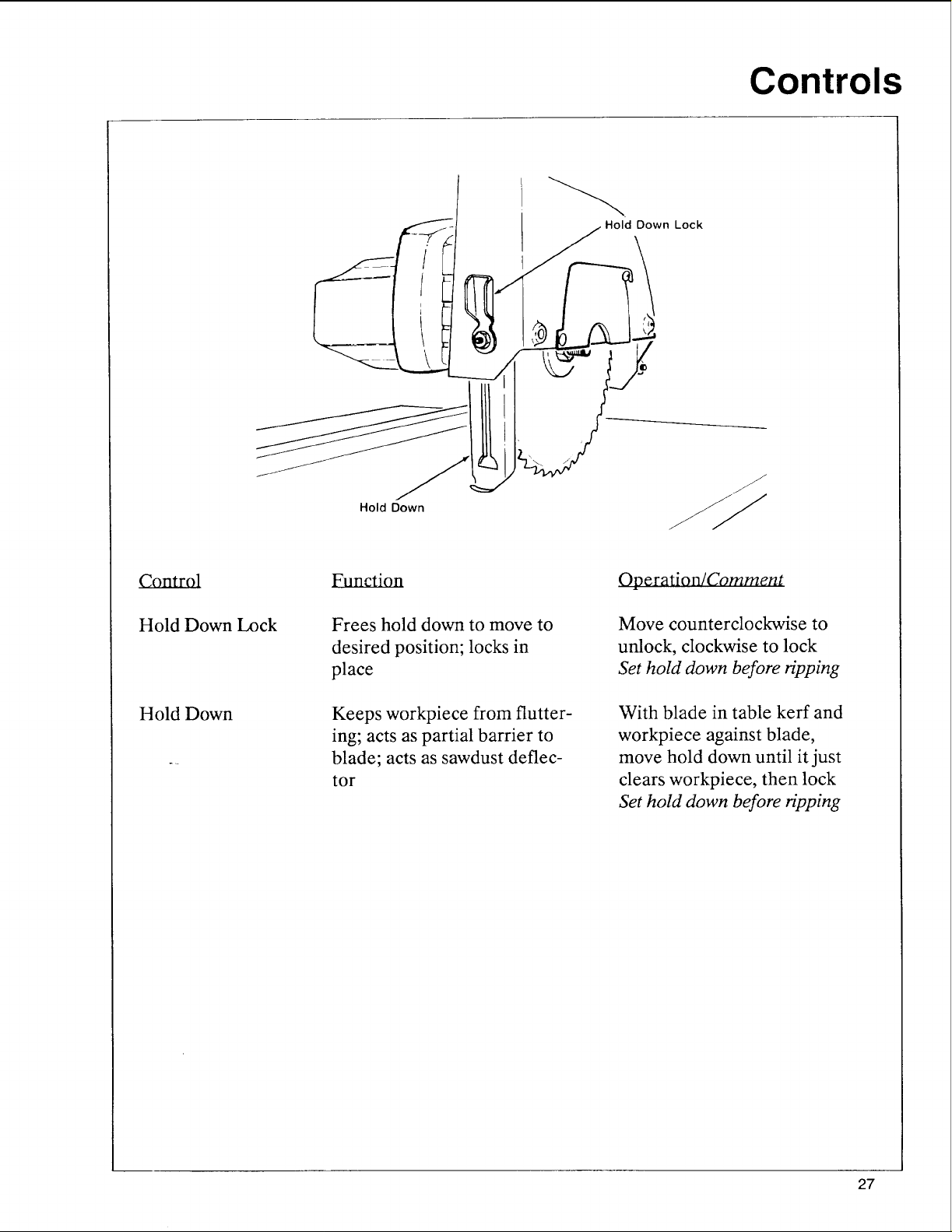
Hold Down
Controls
/Hold Down Lock
Control
Hold Down Lock
Hold Down
Frees hold down to move to
desired position; locks in
place
Keeps workpiece from flutter-
ing; acts as partial barrier to
blade; acts as sawdust deflec-
tor
Operation/Comment
Move counterclockwise to
unlock, clockwise to lock
Set hold down before ripping
With blade in table kerf and
workpiece against blade,
move hold down until it just
clears workpiece, then lock
Set hold down before ripping
27