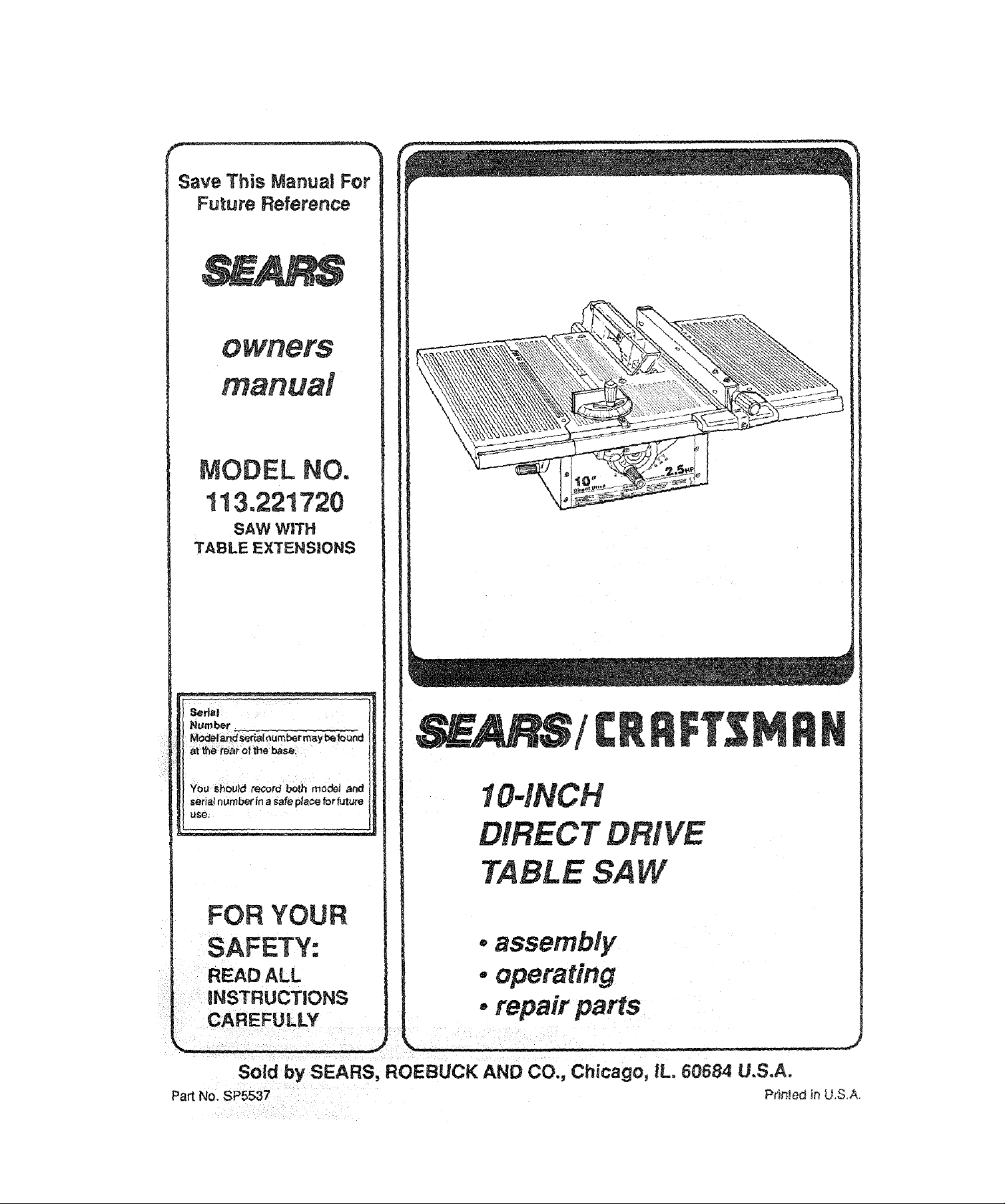
Save This Manual For
Future Reference
/
IOqNCH
DIRECT IVE
TABLE SAW
FOR YOUR
SAF TY.
BEAD ALL
INSTRUCTIONS
CAREFULLY
Part No. SP5537 Pr_n._eain U.S,A,
E
Sold by SEARS, ROEBUCK AND CO., Chicago, iL. 60684 U.S.A.
. assembly
. operating
• repair parts
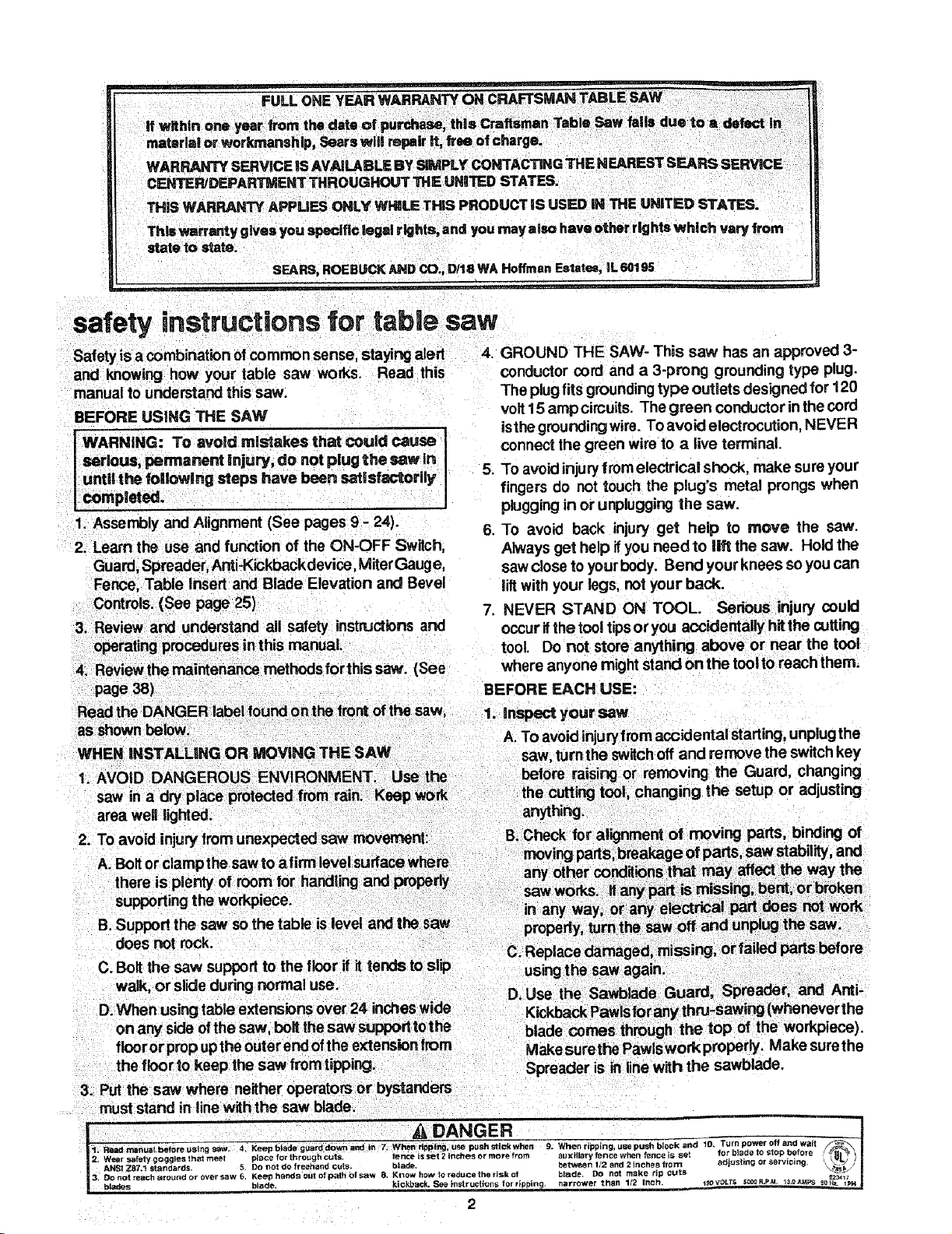
WARRANTY SERVICE iS AVAILABLE BY SIMPLY" CONTACTING "irHENEAREST SEARS SERV_E
CF_NTER/DEPARTMENTTHROUGHOUT THE UN|TED STATES.
THIS WARRANTY APPUES ONLY _IILETHiS PRODUCT IS USED IN THE UNITED STATES.
This warranty gives you specific legal rights, and you may als.= have other rig htswhich vary from
state to state.
SEARS, ROEBUCK ._ND CO., D/t8 WA Hoffman Estates, IL 60195
safety instructions for table saw
Safety isa combination ofcommon sense,staying alert
and knowing how your table saw works. Read this
manual to understand this saw.
BEFORE USING THE SAW
| WARNING: To avoid roistakes that could cause I
"_serious, permanent injury, do not plug the saw in
| until the following steps have been sat|sfactorily
I completed.
1. Assembly and Alignment (See pages 9- 24).
2. Learn the use and function of the ON-OFF Switch,
Guard, Spreader,Anti-Kickback device, MiterGauge,
Fence Table Insert and Blade Elevation and Bevel
Controls. (See page 25)
3 Review and understand all safety instructions and
operating procedures inthis manual.
4. Review the maintenance methods forthis saw. (See
page 38)
Read the DANGER label found on the front of the saw,
as shown below.
WHEN iNSTALLiNG OR MOVING THE SAW
1. AVOID DANGEROUS ENVIRONMENT. Use the
saw in a dry place protected from rain. Keep work
area well lighted.
4. GROUND THE SAW- This saw has an approved 3-
5. To avoidinjuryfrom electrical shock, make sure your
!
7. NEVER STAND ON TOOL. Serious injury could
conductor cord and a 3-pror_j grounding type plug.
The plugfits groundingtype outlets designed for 120
volt 15 amp cimuits. The green conductor inthe cord
isthe grounding wire. To avoid electrocution, NEVER
connect the green wire to a live terminal.
fingers do not touch the plug's metal prongs when
pluggingin orunplugging the saw.
6. To avoid back injury get help to move the saw.
Always get help if you need to lift the saw. Hold the
saw close to your body. Bend your knees soyou can
liftwith your legs, notyour back.
occur ifthe tooltipsor you accidentally hitthe cutting
tool. Do not store anything above or near the tool
where anyone might stand on the toolto reach them.
BEFORE EACH USE:
1. inspect your saw
A. To avoid injurytrom accidental starting, unplugthe
B. Support the saw sothe table islevel and the saw
does notrock.
C. Bolt the saw support to the floor if it tends to slip
walk, or slide during normal use.
D. When using table extensions over 24 incheswide
on any side of the saw, belt the saw supporttothe
flooror propupthe outer end of the extension from
the flcorto keep the saw fromtipping.
3. Put the saw where neither operators orbystanders
must stand in line with the saw blade.
I
2, Wear safety goggles that m p g " _ - ' " or servi i _UL;
AN_ Z87.t standards .... cuts _ _v ,
3. Do not reach _ro P .... OOORpM 130_, =-23_1_"
I " set ace for hrou hcuts fence is set 2 inches or more from au_ ary f_rlce v/heR fence S set ;or D!_O p _lore
_ad_s blade, kickback. See instructlor_s for rtpp=ng, narrower than 1/2 _nch. _o v_=_= =_-._.-. ,=_ ,_ _pH
und or over saw 5 Kee henclsoutofpathofsaw 8. Knowhow Or_aducetheriskot bla(fe. DO not make rip --J
5 DO _ot do fre_:ha_d cuts Oracle I_etwee;_ 2 and 2 riches f o_ ad ustmg _ rig. _
DANGER ..... T_..... . o.o._ tl
2
Spreader is in line with the sawblade,
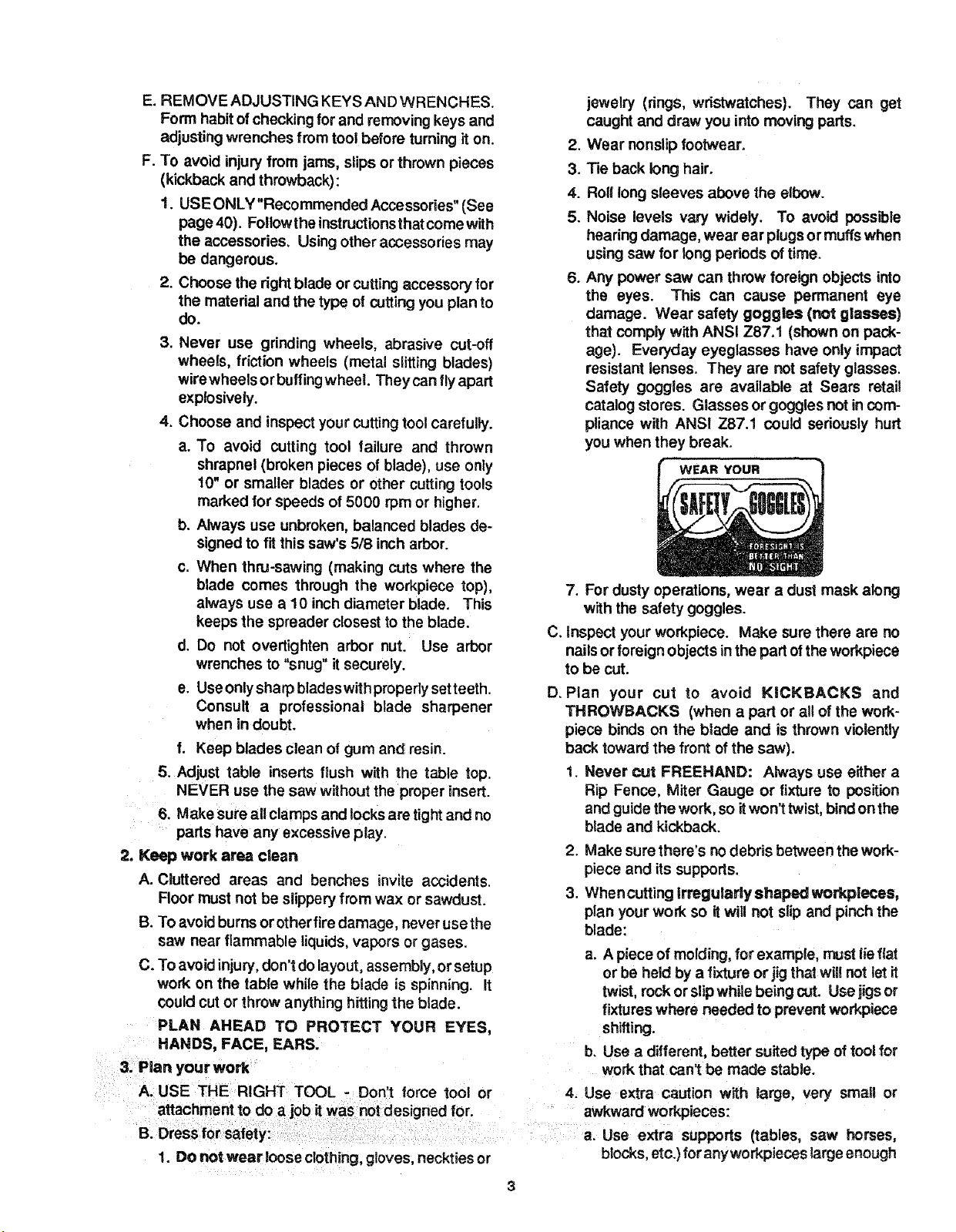
E. REMOVE ADJUSTING KEYS AND WRENCHES.
Form habit of checking for and removing keys and
adjusting wrenches from tool before turning it on.
F. To avoid injury from jams, slips or thrown pieces
(kickback and throwback):
1. USE ONLY"Recommended Accessories" (See
page 40). Follow the instructionsthat come with
the accessories. Using other accessories may
be dangerous.
2. Choose the right blade or cutting accessory for
the material and the type of cutting you plan to
do.
3. Never use grinding wheels, abrasive cut-off
wheels, friction wheels (metal slilting blades)
wirewheelsorbuffingwheel. Theycan fly apad
explosively.
4. Choose and inspect your cutting tool carefully.
a. To avoid cutting tool failure and thrown
shrapnel (broken pieces of blade), use only
10" or smaller blades sr other cutting tools
marked for speeds of 5000 rpm or higher.
b. Always use unbroken, balanced blades de-
signed to fit this saw's 5/8 inch arbor.
c. When thru-sawing (making cuts where the
blade comes through the workpiece top),
always use a 10 inch diameter blade. This
keeps the spreader closest to the blade.
d. Do not overtighten arbor nut. Use arbor
wrenches to "snug" it securely.
e. Use only sharp bladeswith properly setteeth.
Consult a professional blade sharpener
when in doubt.
f. Keep blades clean of gum and resin.
5. Adjust table inserts flush with the table top.
NEVER use the saw without the proper insert.
6. Make sure all clamps and locks are tight and no
parts have any excessive play.
2. Keep work area clean
A. Cluttered areas and benches invite accidents.
Floor must not be slippery from wax or sawdust.
B. To avoid burns or other fire damage, never usethe
saw near flammable liquids, vapors or gases.
C. To avoid injury,don't do layout, assembly, or setup
work on the table while the blads is spinning. It
could cut or throw anything hitting the blade.
PLAN AHEAD TO PROTECT YOUR EYES,
HANDS, FACE, EARS.
3. Plan your work
A. USE THE RIGHT TOOL - Don't force tool or
attachment to do a job it was notdesigned for.
1. DOnotwear looseclothing, gloves, neckties or
jewelry (rings, wristwatches). They can get
caught and draw you into moving pads.
2. Wear nonslip footwear.
3. Tie back long hair.
4. Rol! long sleeves above the elbow.
5. Noise levels vary widely. To avoid possible
hearing damage, wear ear plugs or muffs when
using saw for long periods of time.
6. Any power saw can throw foreign objects into
the eyes. This can cause permanent eye
damage. Wear safety goggles (not glasses)
that comply with ANSI Z87.f (shown on pack-
age). Everyday eyeglasses have only impact
resistant lenses. They are not safety glasses.
Safety goggtes are available at Sears retail
catalog stores. Glasses or goggles not in com-
pliance with ANSI Z87.1 could seriously hurt
you when they break.
WEAR YOUR
7. For dusty operations, wear a dust mask along
with the safety goggles.
C,
Inspect your workpiece. Make sure there are no
nailsor foreign objects inthe part of the workpiece
to be cut.
D.
Plan your cut to avoid KICKBACKS and
THROWBACKS (when a part or all of the work-
piece binds on the blade and is thrown violently
back toward the front of the saw).
1. Never cut FREEHAND: Always use either a
Rip Fence, Miter Gauge or fixture to position
and guide the work, so itwon't twist, bind onthe
blade and kickback.
2. Make sure there's no debris between the work-
piece and its supports.
3. Whencutting Irreguladyshaped workpleces,
plan your work so itwill not slip and pinch the
blade:
a. A piece of molding, for example, rr_st lie flat
or be held by a fixture or jigthat will not let it
twist, rock or slipwhile being cut. Usejigsor
fixtures where needed to prevent workpiece
shifting.
b, Use a different, better suited type of tool for
work that can't be made stable.
4. Use extra caution with large, very small or
awkward workpieces:
a. Use extra supports (tables, saw horses,
blocks, etc.)for anyworkpieces large enough
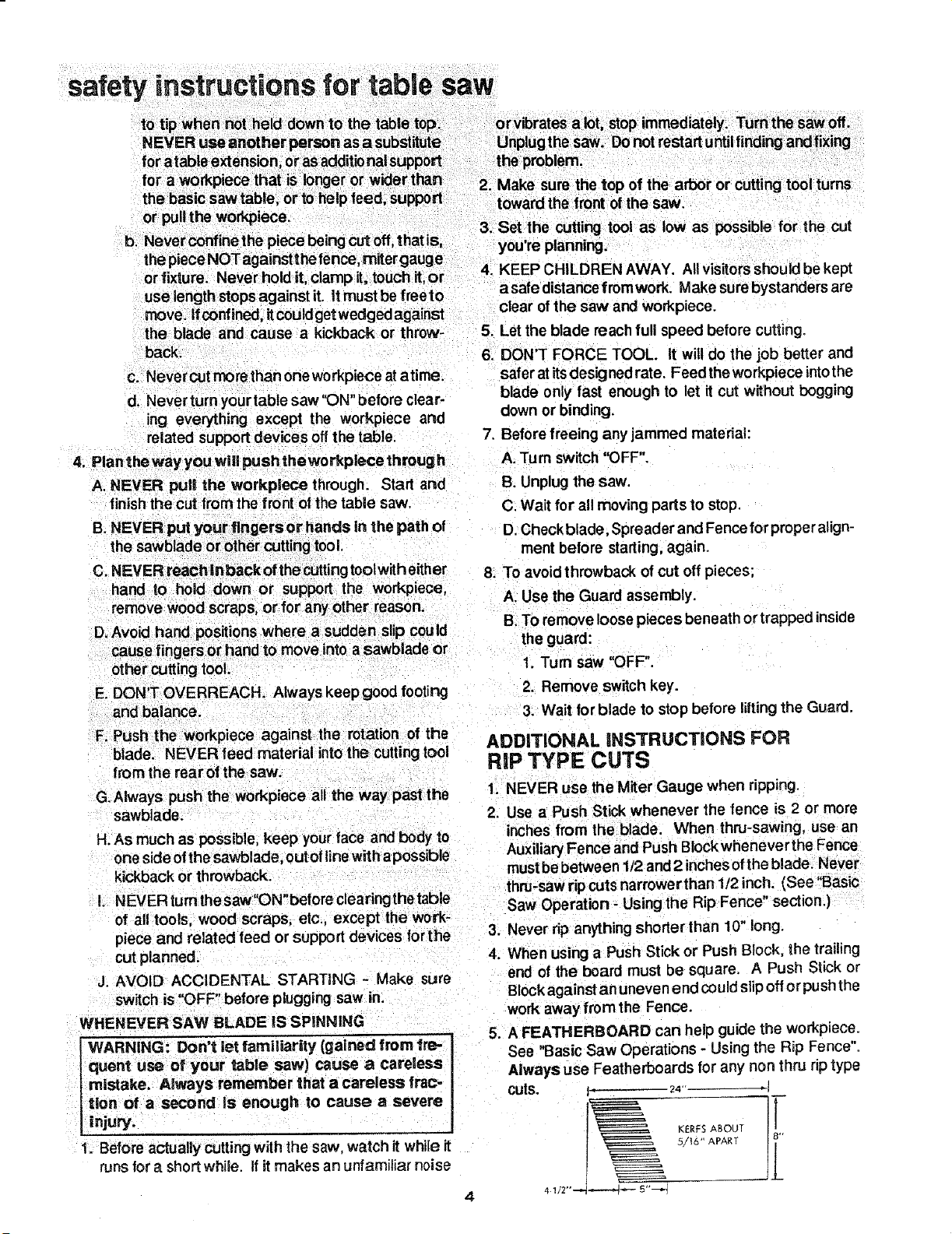
3. Set the cutting tool as low as possible for the cut
you're planning.
4. KEEP CHILDREN AWAY. All visitors should be kept
uselength stopsagainst it. it must befreeto
move. If confined, itcouldgetwedged against
the blade and cause a kickback or throw-
back.
c. Never cut more than one workpiece ata time.
d. Never turn your table saw"ON" before clear-
ing everything except the workpiece and
related support devices off the table.
4. Planthewayyouwlil pushtheworkplecethrough
A. NEVER pull the workplece through. Start and B. Unplug the saw.
finish the cut from the front of the table saw,
B. NEVER put your fingers or hands in the path of
the sawb ade orother cutting tool.
C. NEVER reach !n back of the cuttingtool with either
hand to hold down or support the workpiece
remove wood scraps, or for any other reason,
D. Avoid hand positions where a sudden slip could
cause fingers or hand to move into asawblade or
other cutting tool.
F. Push the workpiece against the rotation of the
blade. NEVER feed material intothe cutting tool
from the rear of the saw.
G_Always push the workpiece all the way past the
sawblade.
H. As much as possible, keep your face and body to
one side of the sawblade, outer line with apossible
kickback or throwback.
I. NEVER tum the saw "ON"before clearingthe table
of all tools wood scraps, etc., except the work-
piece and related feed or support devices forthe
cut planned.
J. AVOID ACCIDENTAL STARTING - Make sure
switch is"OFF" before plugging saw in,
WHENEVER SAW BLADE IS SPINNING
I WARNING: Don't let familiarity (gained from fre-_
quent use of your table saw) cause a careless j
1 mistake, Always remember that a careless frac- J
tlon of a second Is enough to cause a severe j
I injury. J
t. Before actually cutting with the saw, watch it while it
runs for a short while. If it makes an unfamiliar noise
a safe distance fromwork. Make sure bystanders are
clear ofthe saw and workpiece.
5. Let the blade reach full speed before cutting.
6. DON'T FORCE TOOL. It will do the job better and
safer atitsdesignedrate. Feedtheworkpiece intothe
blade only fast enough to let it cut without bogging
down or binding.
7. Before freeing any jammed material:
A. Turn switch "OFF".
C. Wait for all moving parts to stop.
D. Check blade, Spreader and Fence for proper align-
ment before starting, again.
8, To avoid throwback of cut off pieces;
A. Use the Guard assembly.
B. To remove loose pieces beneath or trapped inside
the guard:
1. Turn saw "OFF".
2. Remove switch key.
3. Wait forblade to stop before lifting the Guard,
ADDITIONAL INSTRUCTIONS FOR
RiP TYPE CUTS
1. NEVER use the Miter Gauge when ripping.
2. Use a Push Stick whenever the fence is 2 or more
inches from the blade. When thru-sawing, use an
Auxiliary Fence and Push Blockwheneverthe Fence
mustbe between 112and2 inchesofthe blade. Never
thru-sawrip cuts narrower than 1t2 inch. (See "Basic
Saw Operation - Using the Rip Fence" section.)
3. Never rip anything shorter than 10"long.
4. When using a Push Stick or PuSh Block, the trailing
end of the board must be square. A Push Stick or
Blockagainst an uneven end could slipoffor pushthe
work away from the Fence.
5. A FEATHEABOARD can help guide the workpiece.
See "BasicSaw Operations - Using the Rip Fence".
Always use Featherboards forany non thru rip type
CUTS. I' 24" _1
1 JL
4.112""--_-=-----_J 5"_,-_
KERFS ABOUT
I_ 5/16" APART I "
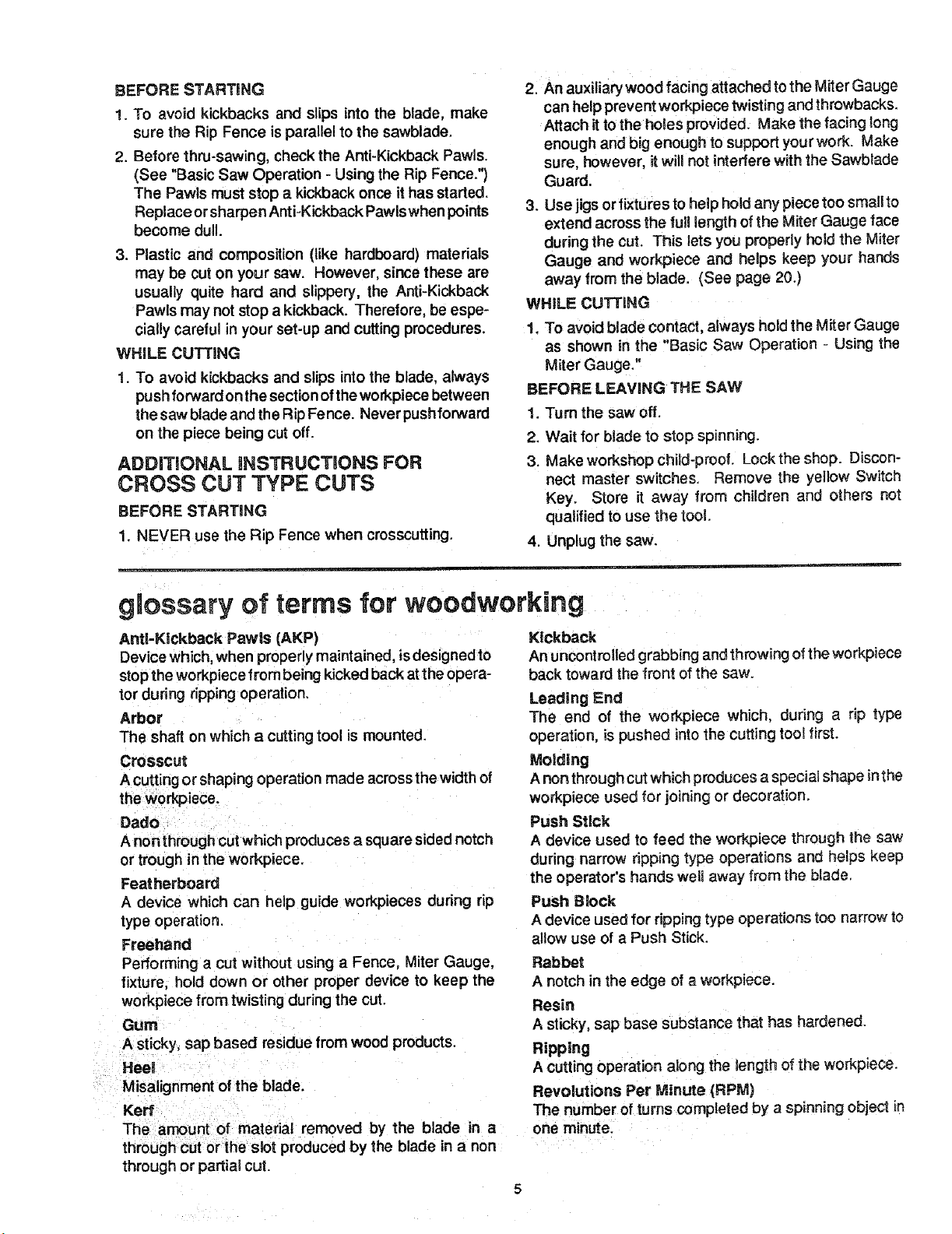
BEFORE STARTING
1. To avoid kickbacks and slips into the blade, make
sure the Rip Fence is parallel to the sawblade.
2. Before thru-sawing, check the Anti-Kickback Pawls.
(See "Basic Saw Operation - Using the Rip Fence.")
The Pawls must stop a kickback once it has started.
Replace or sharpen Anti-Kickback Pawiswhen points
become dull.
3. Plastic and composition (like hardboard) materials
may be cut on your saw. However, since these are
usually quite hard and slippery, the Anti-Kickback
Pawls may not stop a kickback. Therefore, be espe-
cially careful in your set-up and cutting procedures.
WHILE CUTTING
1. TO avoid kickbacks and slips into the blade, always
pushforwardon the sectionofthe workpiece between
the saw bladeand the RipFence, Never pushforward
on the piece being cut off.
ADDITIONAL iNSTRUCTiONS FOR
CROSS CUT TYPE CUTS
BEFORE STARTING
1. NEVER use the Rip Fence when crosscutting.
2. An auxiliary wood facing attached to the Miter Gauge
can help prevent workpiece twisting and throwbacks.
Attach ittothe holes provided. Make the facing !ong
enough and big enough to support your work. Make
sure, however, it will not interfere with the Sawbiade
Guard.
3. Use jigs or fixtures to help hold any piece too small to
extend across the full length of the Miter Gauge face
during the cut. This lets you properly hold the Miter
Gauge and workpiece and helps keep your hands
away from the blade. (See page 20.)
WHILE CUTTING
1. To avoid blade contact, always hold the Miter Gauge
as shown in the "Basic Saw Operation - Using the
Miter Gauge."
BEFORE LEAVING THE SAY#
1. Turn the saw off.
2. Wait for blade to stop spinning.
3. Make workshop child-proof. Lockthe shop. Discon-
nect master switches. Remove the yellow Switch
Key. Store it away from children and others not
qualified to use the tool.
4. Unplug the saw.
gmossary of terms for woodworking
Anti-Kickback Pawls (AKP)
Device which, when properly maintained, isdesigned to
stop the workpiece from being kicked back atthe opera-
tor during ripping operation,
Arbor
The shaft on which a cutting tool is mounted.
Crosscut
A cuttingor shaping operation made acrossthe widthof
theworkpiece.
Dadc
Anon through cut which produces a square sided notch
or trough inthe workpiece.
Featherboard
A device which can help guide workpieces during rip
type operation.
Freehand
Performing a cut without using a Fence, Miter Gauge,
fixture, hold down or other proper device to keep the
workpiece from twisting during the cut
Gum
A sticky, sap based residuefrom wood products.
Heel
Misalignment of the blade.
Kerr
The amount of matedat removed by the blade in a
through cut or the slot produced by the blade in a non
through or partial cut.
Kickback
An uncontrolled grabbing and throwing of the workpiece
back toward the front of the saw.
Leading End
The end of the workpiece which, during a rip type
operation, is pushed intothe cutting tool first.
Molding
Anon through cut which produces aspecial shape inthe
workpiece used for joining or decoration.
Push Stick
A device used to feed the workpiece through the saw
during narrow ripping type operations and helps keep
the operator's hands well away from the blade.
Push Block
A device used for rippingtype operation_ too narrow to
allow use of a Push Stick.
Rabbet
A notch in the edge of a workpiece.
Resin
A sticky, sap base substance that has hardened.
Ripping
A cutting operation along the length of the workpiece.
Revolutions Per Minute (RPM)
The number of turns completed by a spinning object in
one minute.
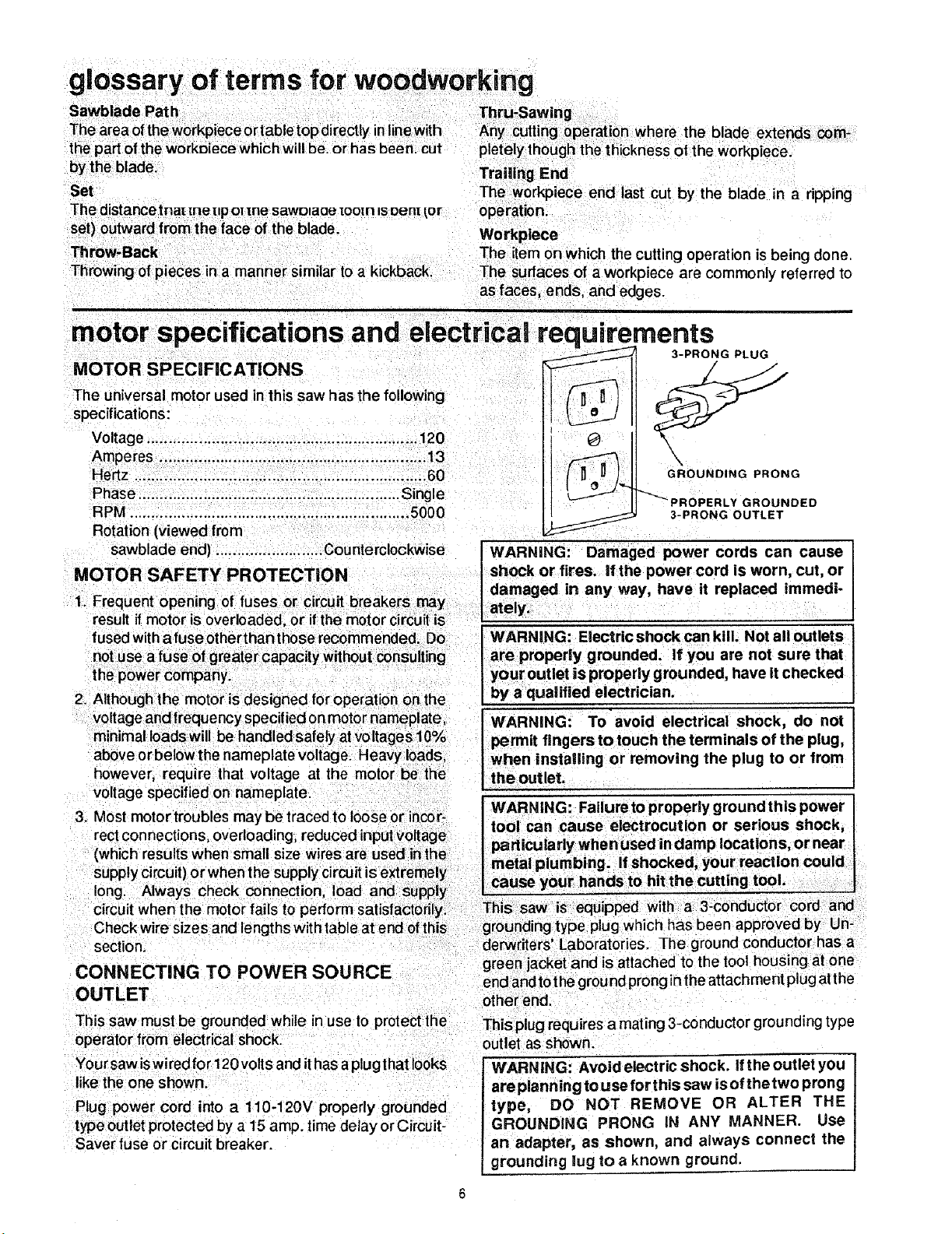
glossary of terms for woodworking
h
thepart of the workDiece which will be.or has been_cut
by the blade. Trail End
Set , the =n a npping
The distance thai [ne upoi [ne sawo_aoe _oo_n_soem to r
set) outward from the face of the blade. Workpiece
Throw-Back The item on which the cuttingoperation is being done.
are commonly referred to
specifications:
Voltage ............................................................... 120
Amperes .............................................................. 13
Hertz ................................................. i.................. 60
Phase ........................................................... Single
RPM ......................... 5000
Rotation (viewed from
sawblade end) ......................... Counterclockwise WARNING: Damaged power cords can cause
MOTOR SAFETY PROTECTION shock or fires, if the power cord is worn, cut, or
damaged in any way, have it replaced immedi-
1. Frequent opening of fuses or circuit breakers may ately.
result il motor is overloaded or if the motor circuitis .
WARNING: Electricshock can kill. Not all outlets
are property grounded. If you are not sure that
youroutlet is properly grounded, have it checked
2. Although the motor is designed for operation on.the
voltage and frequency spec lied on motor nameplate,
minimal loads will be handled safely atvoltages 10%
above or below the nameplate voltage. Heavy loads,
however, require that voltage at the motor be the
voltage specified on nameplate.
3. Most motor troubles may be traced to loose or incor:
rectconnections overloading reduced input voltage
(which results when small size wires are used inthe
supply circuit) or when the supply circuitis extremely
long. Always check connection, load and suppl,/
circuit when the motor fails to perform satisfactorily.
Check wire sizes and lengthswithtable at endof this
section.
CONNECTING TO POWER SOURCE
OUTLET
This saw must be grounded while in use to protect the This plug requires a mating 3-conductor grounding type
operatorfrom electrical shock.
Your saw iswired for 120 volts and ithas aplug that looks
like the one shown.
Plug power cord into a 110-120V properly grounded
typeoutlet protected by a 15 amp. time delay orCircuit-
Saver fuse or circuit breaker.
by a qualified electrician.
WARNING: Toavoid electrical shock, do not
permit fingers totouch the terminals of the plug,
when installing or removing the plug to or from
the outlet.
tool can cause electrocution or serious shock,
particularly when used indamp locations, or near
I WARNING: Failureto properly groundthis power 1
metal plumbing, if shocked, your reaction could
cause your hands to hit the cutting tool.
This saw is equipped with a 3-conductor cord and
grounding type plug which has been approved by Un-
derwriters' Laboratories. The ground conductor has a
greenjacket and is attached to the tool housing at one
end andtothe ground prong in the attachment plug atthe
other end.
3utlet as shown,
WARNING: Avoid electric Shock. If the outlet you
are planning to use for this saw isof the two prong
type, DO NOT REMOVE OR ALTER THE
GROUNDING PRONG IN ANY MANNER. Use
an adapter, as shown, and always connect the
grounding lug to a known ground.
\
GROUNDING PRONG
3-PRONG OUTLET
UNDED
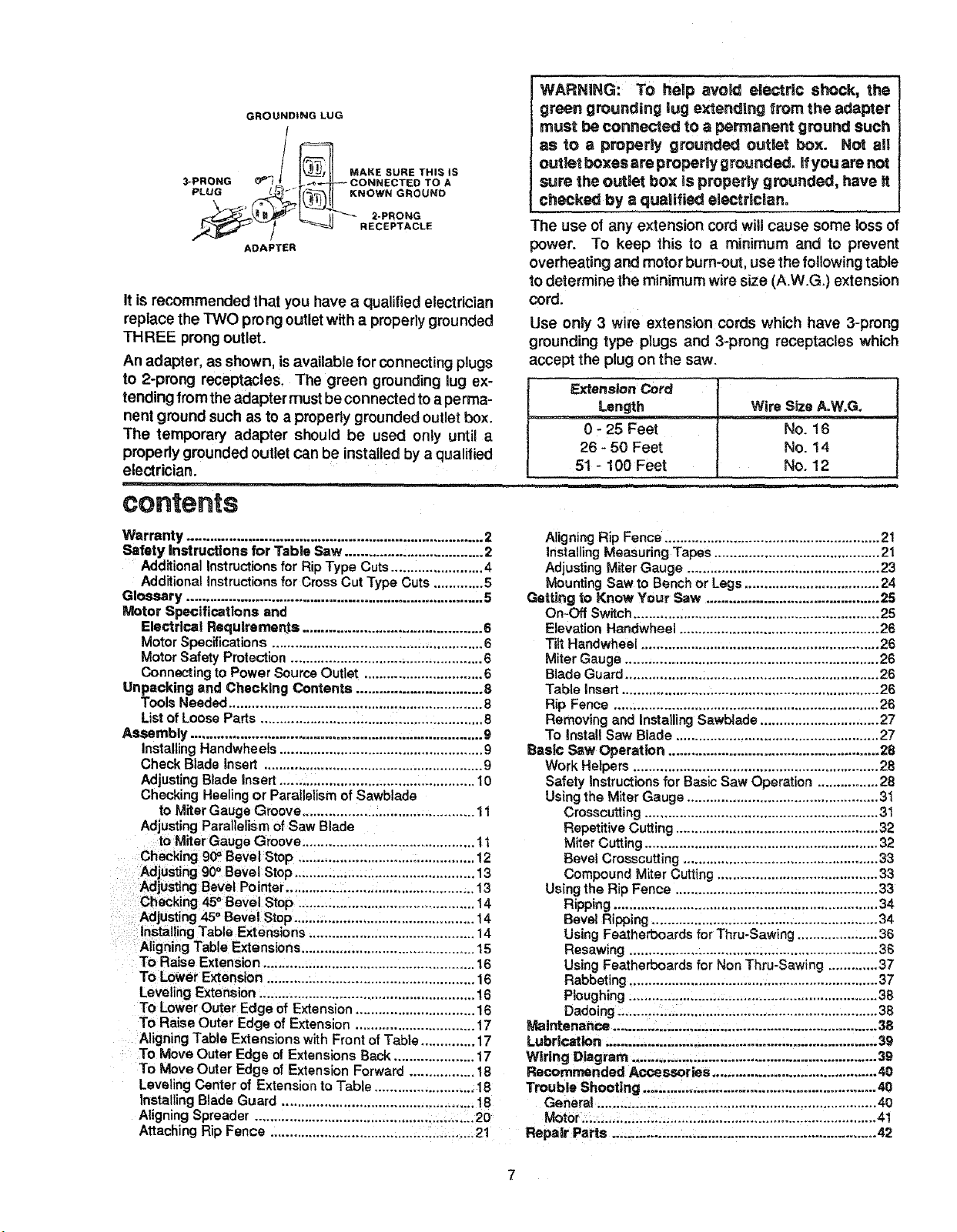
GROUNDING LUG
PLUG i_ _ KNOWN GROUND
-_ RECEPTACLE
ADAPTER
It is recommended that you have a qualified electrician
replace the TWO prong outlet with a properly grounded
THREE prong outlet.
An adapter, as shown, is available for connecting pgugs
to 2-prong receptacles. The green grounding lug ex-
tending from the adapter must be connected to a perma-
nent ground such as to a properly grounded outlet box.
The temporary adapter should be used only until a
propedy grounded outlet can be installed by a qualified
electrician.
contents
WARNING: To help avoid electric Shock, the
green grounding lug extending from the adapter
must be connected tO a permanent ground such
as to a properly grounded outlet box. Not all
outlet boxes are properly grounded, if you are not
sure the outlet box is properly grounded, have H
checked by a qualified electrlclano
The use of any extension cord will cause some loss of
power. To keep this to a minimum and to prevent
overheating and motor burn-out, use the foflowing table
to determine the minimum wire size (A.W.G.) extension
cord.
Use only 3 wire extension cords which have 3-prong
grounding type plugs and 3-prong receptacles which
accept the plug on the saw.
F._ension Cord
Length Wire Size A.W.G.
0 - 25 Feet No. 16
26 - 50 Feet No. 14
51 - 100 Feet No. 12
Warranty ............................................................................. 2
Safety Instructions for Table Saw .................................... 2
Additional Instructions for Rip Type Cuts ........................ 4
Additional Instructions fGr Cross Cut Type Cuts ............. 5
Glossary ............................................................................. 5
Motor Specifications and
Electrical Requirements ............................................... 6
Motor Specifications ....................................................... 6
Motor Safety Protection .................................................. 6
Connecting to Power Source Outlet ............................... 6
Unpacking and Checking Contents ................................. 8
Tools Needed .................................................................. 8
List of Loose Parts .......................................................... 8
Assembly ............................................................................ 9
Installing Handwheels ..................................................... 9
Check Blade Insert ......................................................... 9
Adjusting Blade insert ................................................... 10
Checking Heeling or Parallelism of Sawblade
to Miter Gauge Groove ............................................. 11
Adjusting Parallelism of Saw Blade
to Miter Gauge Groove ............................................. 11
Checking 90=Bevel Stop ............................................. 12
Adjusting 90° Bevel Stop ............................................... 13
Adjusting Bevel Pointer ................................................. 13
Checking 45° Bevel Stop .............................................. 14
Adjusting 45° Bevel Stop ............................................... 14
Installing Table Extensions ........................................... 14
Aligning Table Extensions ............................................. 15
To Raise Extension ....................................................... 16
To Lower Extension ...................................................... 16
Leveling Extension ....................................................... 16
To Lower Outer Edge of Extension ............................... 16
To Raise Outer Edge of Extension ............................... 17
Aligning Table Extensions with Front of Table .............. 17
To Move Outer Edge of Extensions Back ..................... 17
To Move Outer Edge of Extension Forward ................. 18
Leveling Center of Extension to Table .......................... 18
Installing Blade Guard .................................................. 1B
Aligning Spreader ......................................................... 20
Attaching Rip Fence ..................................................... 21
Aligning Rip Fence ........................................................ 21
Installing Measuring Tapes ........................................... 2t
Adjusting M_terGauge .................................................. 23
Mounting Saw to Bench or Legs ................................... 24
Getting to Know Your Saw ............................................. 25
On-Off Switch ................................................................ 25
Elevation Handwheel .................................................... 26
Tilt Handwheel .............................................................. 26
Miter Gauge .................................................................. 26
Blade Guard .................................................................. 26
Table Insert ................................................................... 26
Rip Fence .................................................................... 26
Removing and installing Sawblade ............................... 27
To install Saw Blade ..................................................... 27
Basic Saw Operation ....................................................... 28
Work Helpers ................................................................ 28
Safety Instructions for Basic Saw Operation ................ 28
Using the Miter Gauge .................................................. 31
Crosscutting ............................................................. 31
Repetitive Cutting ..................................................... 32
Miter Cutting ............................................................. 32
Bevel Crosscutting ................................................... 33
Compound Miter Cutting .......................................... 33
Using the Rip Fence ..................................................... 33
Ripping ..................................................................... 34
Bevel Ripping ........................................................... 34
Using Featherboards for Thru-Sawing ..................... 36
Resawing ................................................................. 36
Using Featherboards for Non Thru-Sawing ............. 37
Rabbeting ................................................................. 37
Ploughing ................................................................. 38
Dadoing .................................................................... 38
Maintenance ..................................................................... 38
Lubdcartion ...................................................................... 39
Wiring Diagram ................................................................ 39
Recommended Accessories .......................................... 40
Trouble Shooting ............................................................ 40
General ......................................................................... 40
Motor .............................................................................. 41
Repair Parts .................................................................... 42
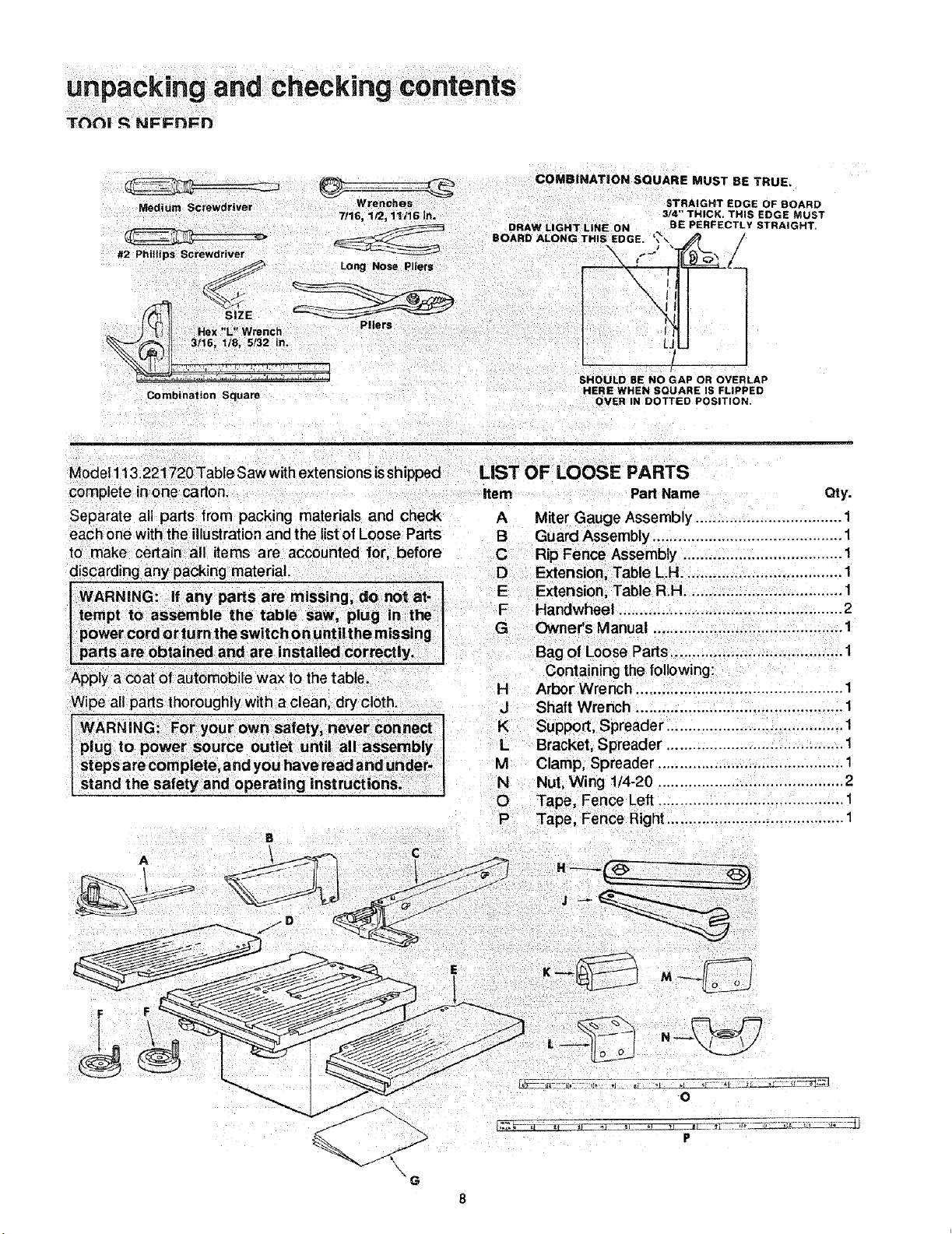
Medium Screwdriver 7/16, 1/2,11/16 in.
#2 Phi ips Screwdriver
"J' _ " " h P ers
, 3/lf6, I/8, 5/32 in.
Combination Square
._ Long Nose P ers
Hex 'L ' wrenc
COMBINATION SQUARE MUST BE TRUE.
STRAIGHT EDGE OF BOARD
3/4" THICK. THIS EDGE MUST
DRAW LIGHT LINE ON % BE PERFECTLY
BOARD ALONG THIS EDGE, ',, \ ,_ /
I
x.,ll
11
SHOULD BE NO GAP OR OVERLAP
HERE WHEN SQUARE JS FLIPPED
OVER IN DOTTED POSITION,
STRAIGHT,
Model 113.221720 Table Saw withextensions is shipped
complete inone carton.
Separate all parts from packing materials and check
each one with the illustrationand the list of Loose Parts
to make certain all items are accounted for, before
discarding any packing material.
t WARNING: If any parts are missing, do not at-
I tempt to assemble the table saw, plug in the ]
power cord or turn the switch on until the missing I
parts are obtained and are installed correctly. I
Apply a coat of automobile wax to the table.
Wipe all parts thoroughly with a clean, dry cloth.
WARNING: For your own safety, never connect
plug to power source outlet until all assembly t
steps are complete, and you have read and under
stand the safety and operating instructions. I
A
LIST OF LOOSE PARTS
Item PartName Qty.
A Miter Gauge Assembly .................................. 1
B Guard Assembly ............................................ 1
C Rip Fence Assembly ..................................... 1
D Extension, Table LH ..................................... 1
E Extension, Table R.H.................................... 1
F Handwheel .................................................... 2
G Owner's Manual ............................................ 1
Bag of Loose Parts ....................................... 1
Containing the following:
H Arbor Wrench ................... 1
J Shaft Wrench ................................................ 1
K Support, Spreader ......................................... 1
L Bracket, Spreader ......................................... 1
M Clamp, Spreader ........................................... 1
N Nut, Wing 1/4-20 ........................................... 2
O Tape, Fence Left ........................................... 1
P Tape, Fence Right ......................................... 1
N
o
P
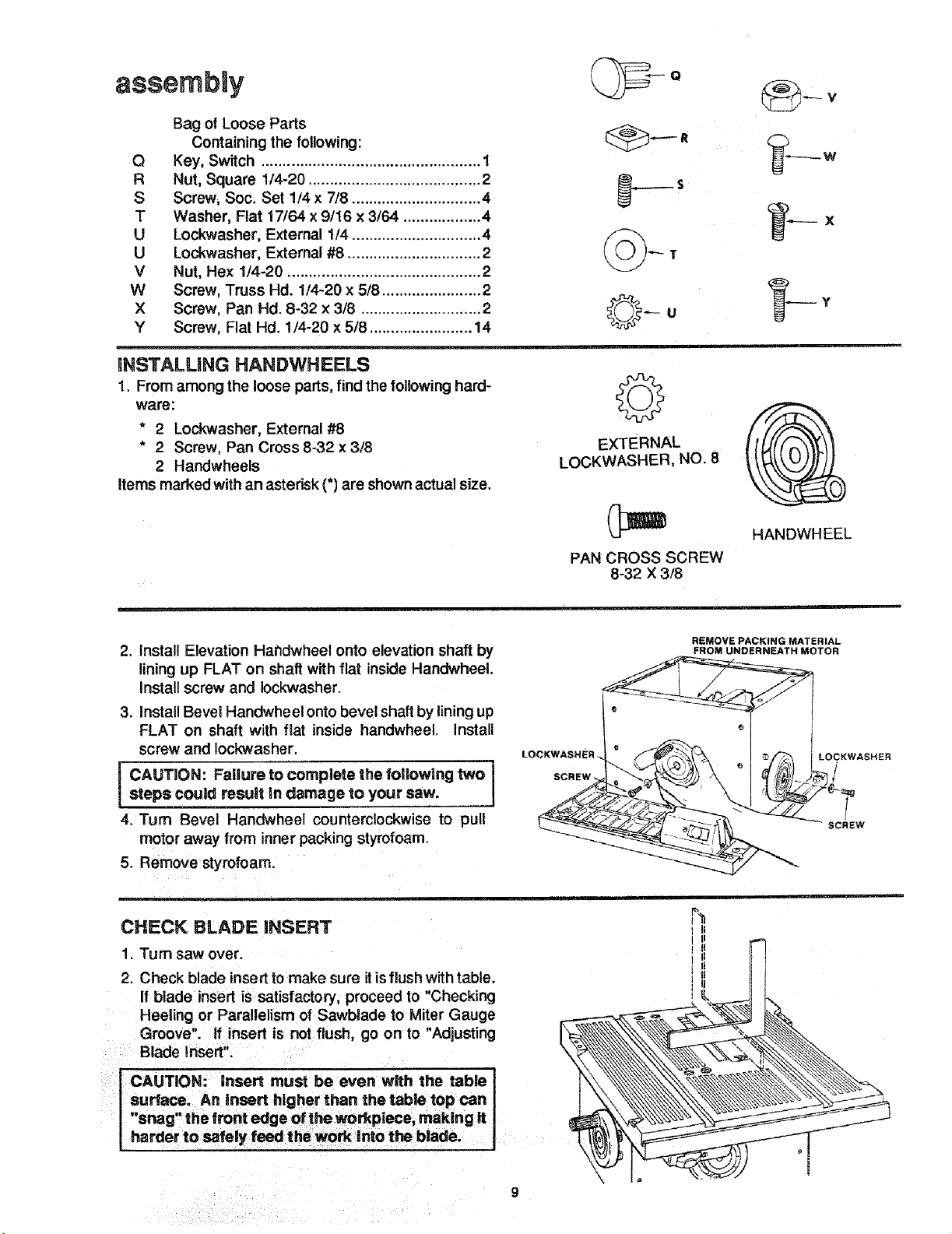
assembly
Bag of Loose Parts
Containing the following:
Q Key, Switch ................................................... 1
R Nut, Square 1/4-20 ........................................ 2
S Screw, Soc. Set 1/4x 7/8 ........................ ......4
T Washer, Flat 17/64 x9/16 x 3/64 .................. 4
U Lockwasher, External 1/4 .............................. 4
U Lockwasher, External #8 ............................... 2
V Nut, Hex 1/4-20 ............................................. 2
W Screw, Truss Hd. 1/4-20 x 5/8 ....................... 2
X Screw, Pan Hd. 8-32 x 3/8 ............................ 2
Y Screw, Flat Hd. 1/4-20 x 5/8 ........................ 14
mNSTALUNG HANDWHEELS
1. From among the loose parts, find the following hard-
ware:
* 2 Lockwasher, External #8
* 2 Screw, Pan Cross 8-32 x 3/8
2 Handwheels
Items marked with an asterisk (*) are shown actual size.
_Q
V
%w
EXTERNAL
LOCKWASHER, NO. 8
HANDWHEEL
PAN CROSS SCREW
8-32 X 3/8
2. install Elevation Hahdwheel onto elevation shaft by
lining up FLAT on shaft with flat inside Handwheel.
install screw and Iockwasher.
3. install Bevel Handwheelonto bevel shaft by lining up
FLAT on shaft with fiat inside handwheel, install
screw and Iockwasher.
CAUTION: Failure to complete the foflowing two
steps could result _ndamage to your saw.
4. Turn Bevel Handwheel counterclockwise to pull
motor away from inner packing styrofoam.
5. Remove styrofoam.
CHECK BLADE INSERT
1. rum saw over.
2. Check blade insert to make sure it is flush with table.
If blade insert is satisfactory, proceed to "Checking
Heeling or Parallelism of Sawbiade to Miter Gauge
Groove". If insert is not flush, go on to "Adjusting
Blade Insert".
CAUTION: insert must be even with the table J
surface. An insert higher than the table top can
"snag" the front edge of the workpiece, making it
harder to safely feed the work into the blade.
I
LOCKWASHER.
REMOVEPACKING MATERIAL
FROM UNDERNEATH MOTOR
I II
LOCKWASHER
SCREW
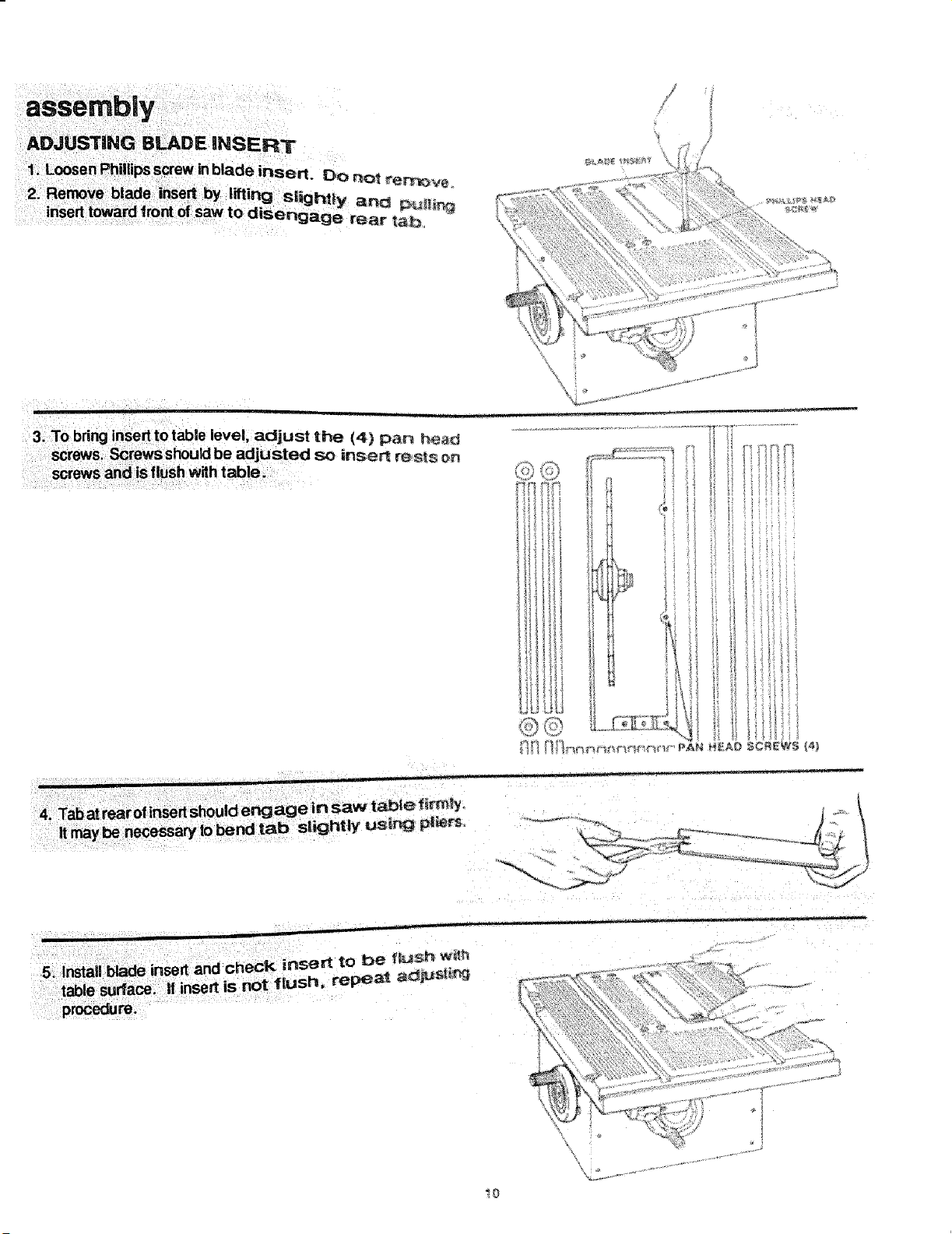
TI
ge in saw table t_y.
b sligl_ly using pi_rs
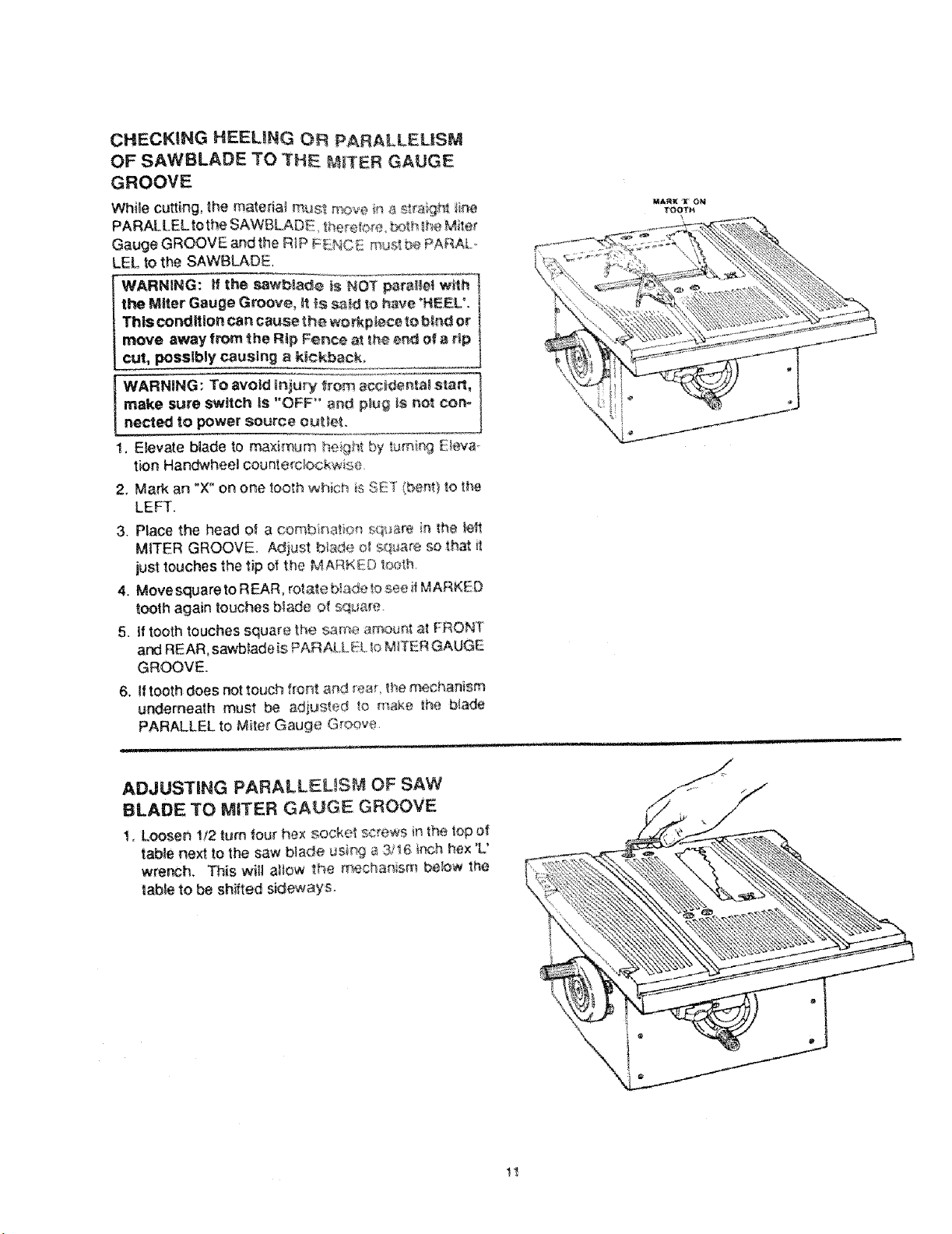
CHECKING HEELING OR PARALLELISM
OF SAWBLADE TOTHE ?4_TER GAUGE
GROOVE
Whi_ecutting, the materia_ must _:_e _ _ _Vai_h__
PARALLEL to the SAWBLADE there,'o_e_t;<_thtr_eMi_er
Gauge GROOVE and the R_P F_NCE m_Jstbe PARAL_
LEL to the SAWBLADE.
WARNING: If the sawb_ade _sNOT para_letw_th
the Miter Gauge Groove, _ _s_td _ohave _HEEL',
This cond fUoncan cau_ the wo_kp_ce to b_nd o_"
move away from the Rip Fence _ th4_er_dof 8 rip
cut, possibly causing a k_¢kback.
WARNING: To avoid Injury _rom acc_n_al start,
make sure switch Is "OFF" and p_ug is not corn
nected to power source ou_et,
1. Elevate blade to ma×imum t_e _h_by tumi{_g E_eva_
t_onHandwheel counte_cbc:kwis_
2, Mark an "X" on ore _oothwhich i_SE!t (beret)to _he
LEFT.
3. Place the head of a comb Rat;o# sq_;_re {n _he _t
MITER GROOVE. Adjust b_e ol squsre so _hat i_
just touches the tip of the MAnKinD V._oth.
4. Movesquareto REAR, rotate bi_detosee # MARKED
tooth again touches blade of sqL_are.
5. iftooth touches square the s_me a_:_ur_tat FRONT
and REAR, sawb_adeis PAR AL.LEL,_oM_ER GAUGE
GROOVE.
6. If tooth does nottouch fro_t and rear _hem_han_sm
underneath must be adiusted _o make #_e b_ade
PARALLEL to M_ter Gauge G#oove.
M_RK "x o_
T_3OTN
ADJUSTING PARALLELISM OF SAW
BLADE TO MITER GAUGE GROOVE
1, Loosen 1/2 turn _our hex socket screws ir_the _opof
table next to the saw blade #si#.g _ 37t6 ir_chhex 'L'
wrench, This "will allow the rr_chanism betow _he
labie to be sh_fted sideways.
\
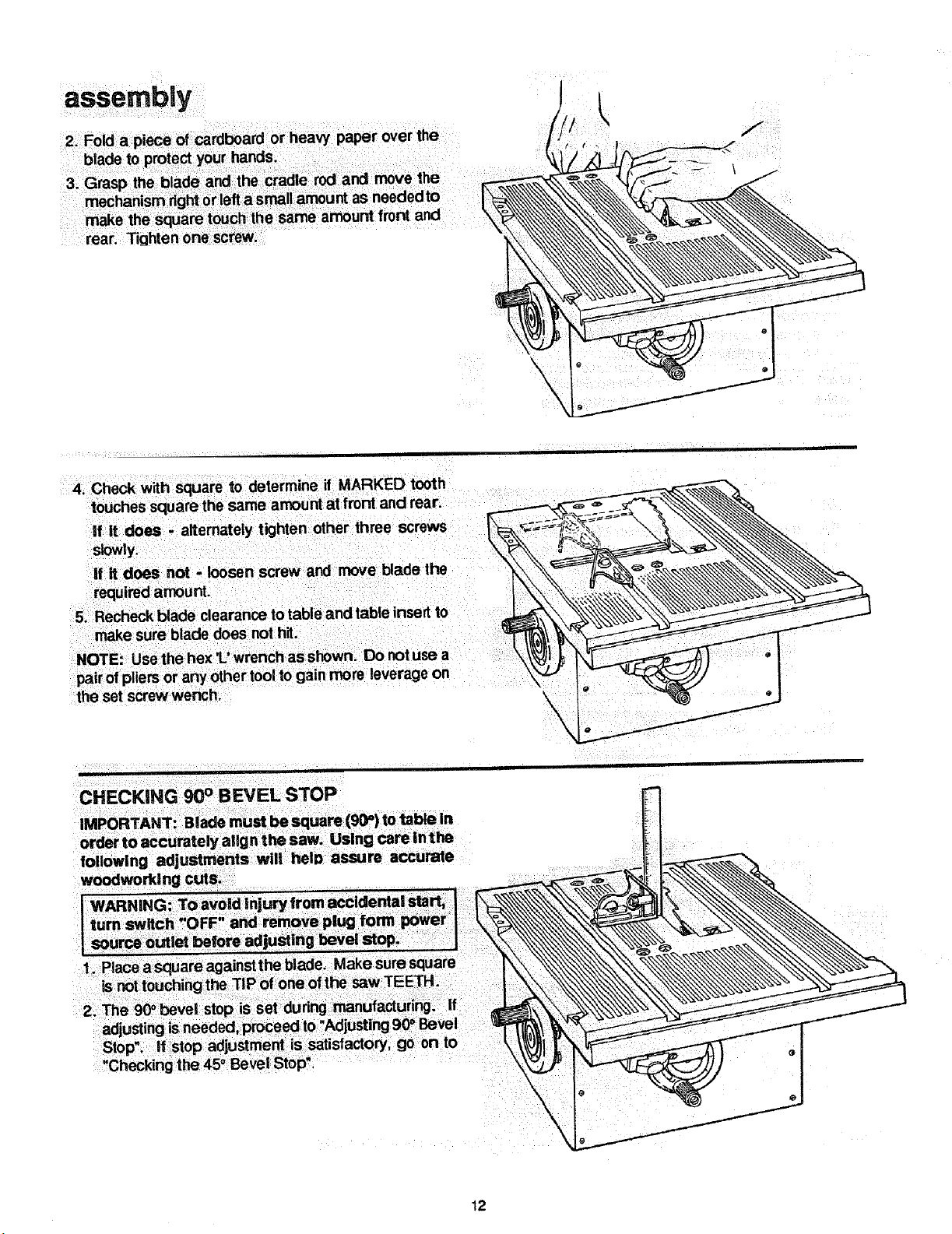
if It does - alternately tighten other three screws
slowly.
\
\
\
\
12
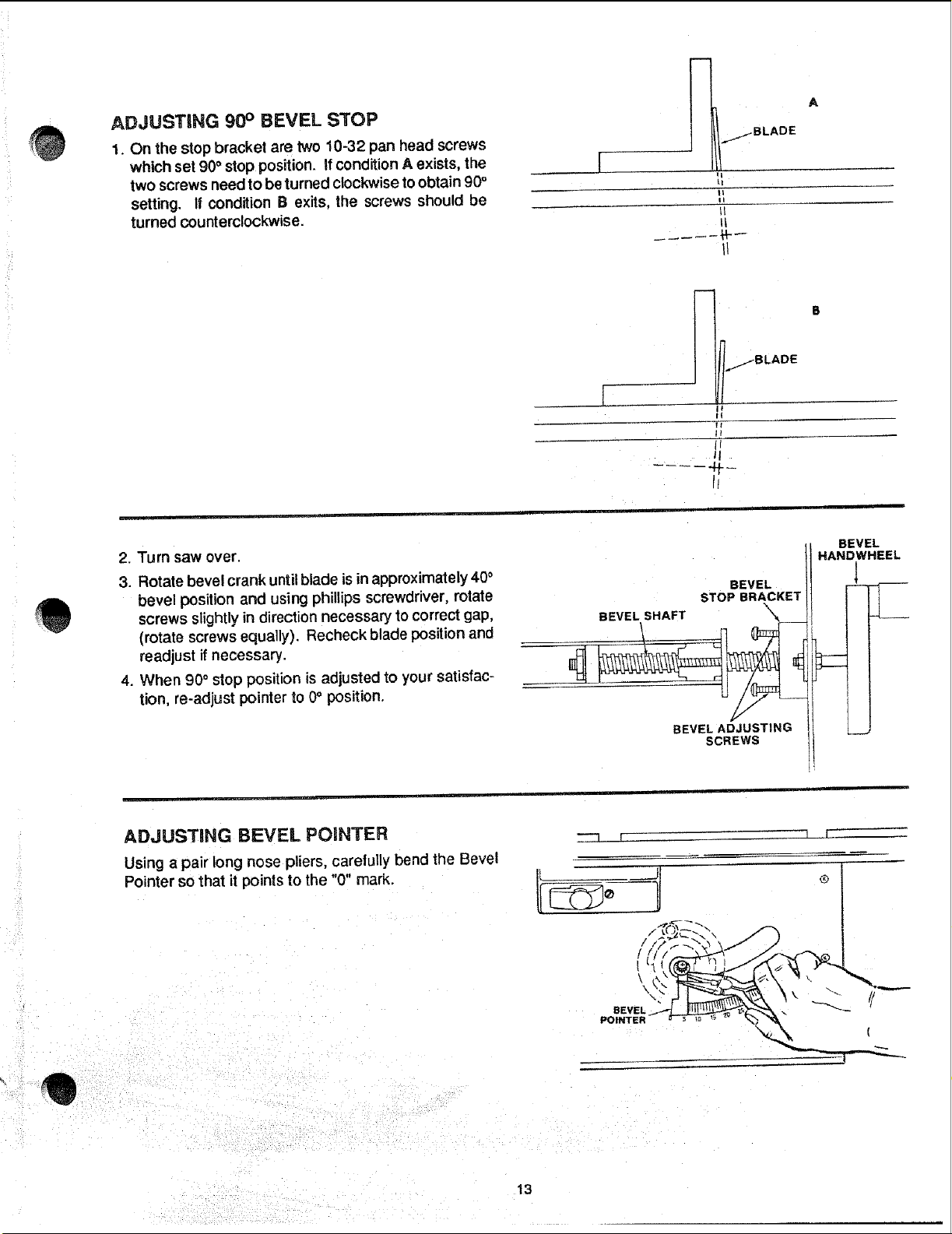
ADJUSTING 90 ° BEVEL STOP
1. On the stop bracket are two 10-32 pan head screws
which set 90° stop position. If condition A exists, the
two screws need to beturned clockwise toobtain 90=
setting. If condition B exits, the screws should be
turned counterclockwise.
/BLADE
_t
tl
It
II
/BLADE
2. Turn saw over.
3. Rotate bevel crank until blade is in approximately 40°
bevel position and using phillips screwdriver, rotate
screws slightlyin direction necessary to correct gap,
(rotate screws equally). Recheck blade position and
readjust if necessary.
4. When 90° stop position is adjusted to your satisfac-
tion, re-adjust pointer to 0° position.
....... ! _
ADJUSTING BEVEL POINTER
Using a pair long nose pliers, carefully bend the Bevel
Pointer so that it points to the "0" mark.
I
STOP BRACKET
BEVEL .A T \
BEVEL ADJUSTING
SCREWS
_---3 f
ti
I
I I
Ir
I
BEVEL
BEVEL
HANDWHEEL
1
r
®
I
I
13
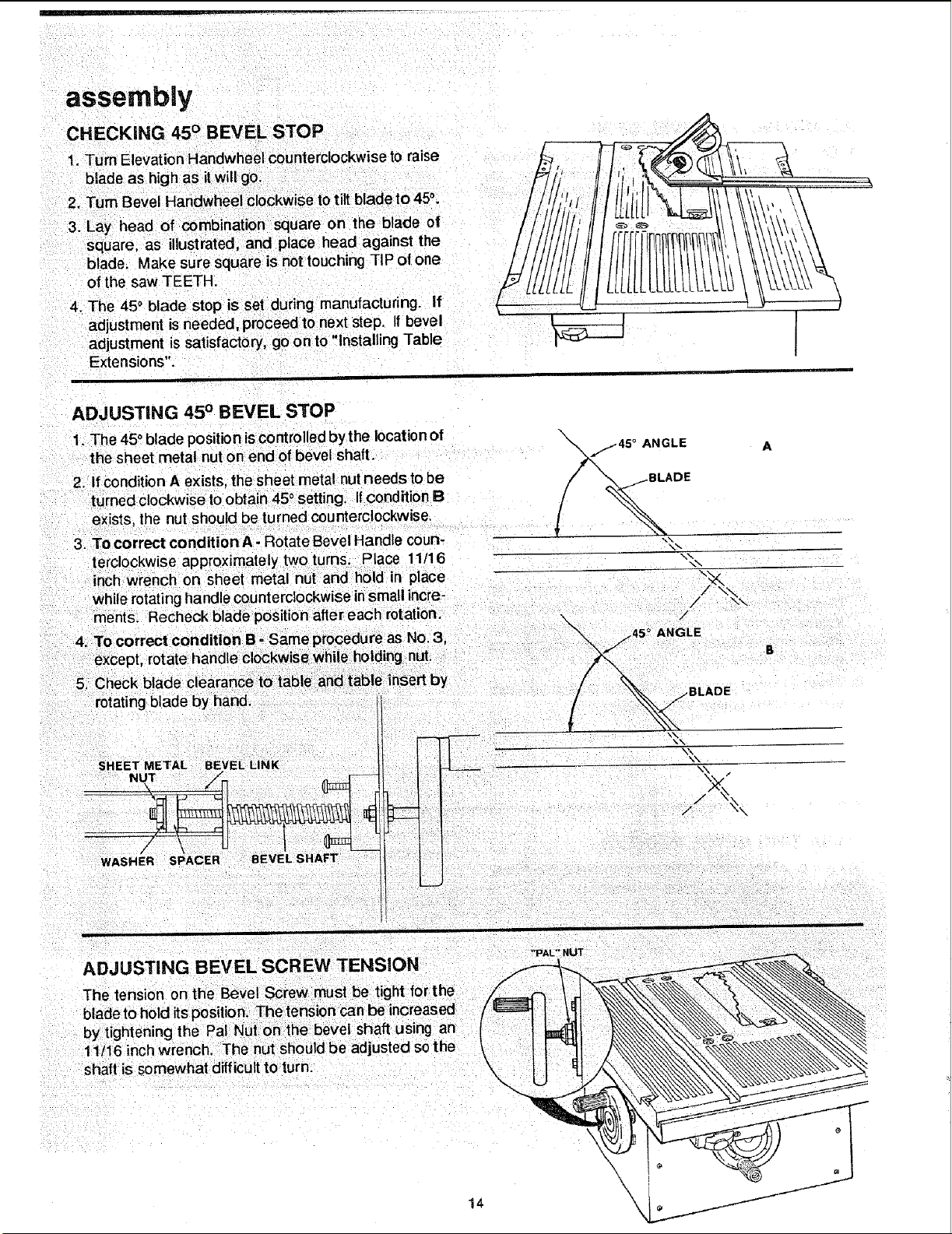
assembly
CHECKING 45° BEVEL STOP
1. Turn Elevation Handwhee counterc ockwise to raise
blade as high as itwill go.
2. Turn Bevel Handwheel clockwise to tilt blade to 45_.
3. Lay head of combination square on the blade of
square, as ustrated, and place head against the
blade. Make sure square is not touching TIP of one
of the saw TEETH.
4. The 45o blade stop is set during manufacturing. If
adjustment s needed, proceed to next step. If bevel
adjustment is satisfactory, go on to" nstalling Tab e
Extensions".
ADJUSTING 45 ° B EVEL STOP
1. The 450blade position iscontrolled by the locationof
the sheet metal nut on end of bevel shaft.
2. If conditionA exists, the sheet metal nutneeds to be
turned clockwise to obtain 45° setting_ if conditionB
exists, the nut should be turned counterclockwise,
3. To correct conditionA - Rotate Bevel Handle coun-
terc ockwse approximately two turns. Place 11/16
inch wrench on sheet meta nut and hold n place
while rotatinghandle counterclockwiseinsmall incre-
ments, Recheck blade positionaftereach rotation.
/
X
°ANGLE
ILADE
\\
J
ADJUSTING BEVEL SCREW TENSION
The tension on the Beve Screw must be tight for then ['_J_
by tightening the Pa Nut on the bevel shaft using a |
11/16 inch wrench. The nut should be adjusted so the
shaft is somewhat difficult to turn. k
"PAL" NUT
jBLADE
E
\\
\\
/"
/
14
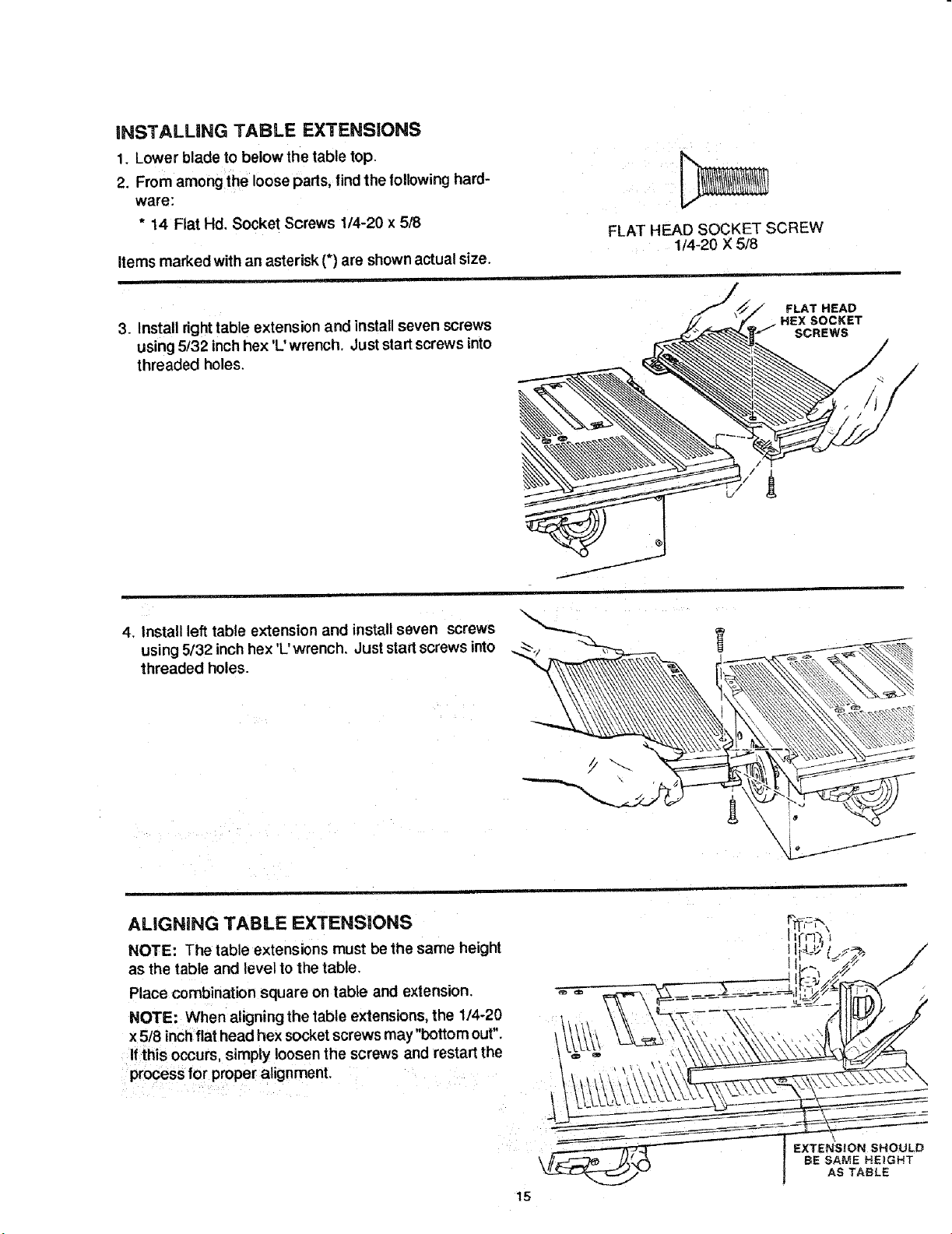
iNSTALLiNG TABLE EXTENSIONS
1. Lower blade to below the table top.
2. From among the loose parts, find the following hard-
ware:
* 14 Flat Hd. Socket Screws 1/4-20 x 5/8
Items marked with an asterisk {*) are shown actual size.
i
3. Install right table extension and installseven screws
using 5/32 inch hex 'L' wrench. Just start screws into
threaded holes.
FLAT HEAD SOCKET SCREW
1/4-20 X 5/8
i
FLAT HEAD
HEXSOCKET
SCREWS
4. Install left table extension and install seven screws
using 5/32 inch hex 'L'wrench, Just start screws into
threaded holes.
ALiGNiNG TABLE EXTENSIONS
NOTE: The table extensions must be the same height
as the table and level to the table.
Place combination square on table and extension.
NOTE: When aligning the table extensions, the 1/4-20
x 5/8 inchflathead hex socketscrews may "bottomout".
Ifthis occurs, simply loosen the screws and restart the
process for proper alignment.
\
EXTENSION SHOULD
BE SAME HEIGHT
AS TABLE
15