
1987
Arctic
Cat
Jag~Panther;.Super
Service
Manual
Jag
'
~~~rG~/
Certified Parts
Corporation
ARCTIC
CAT
4~~4t
'
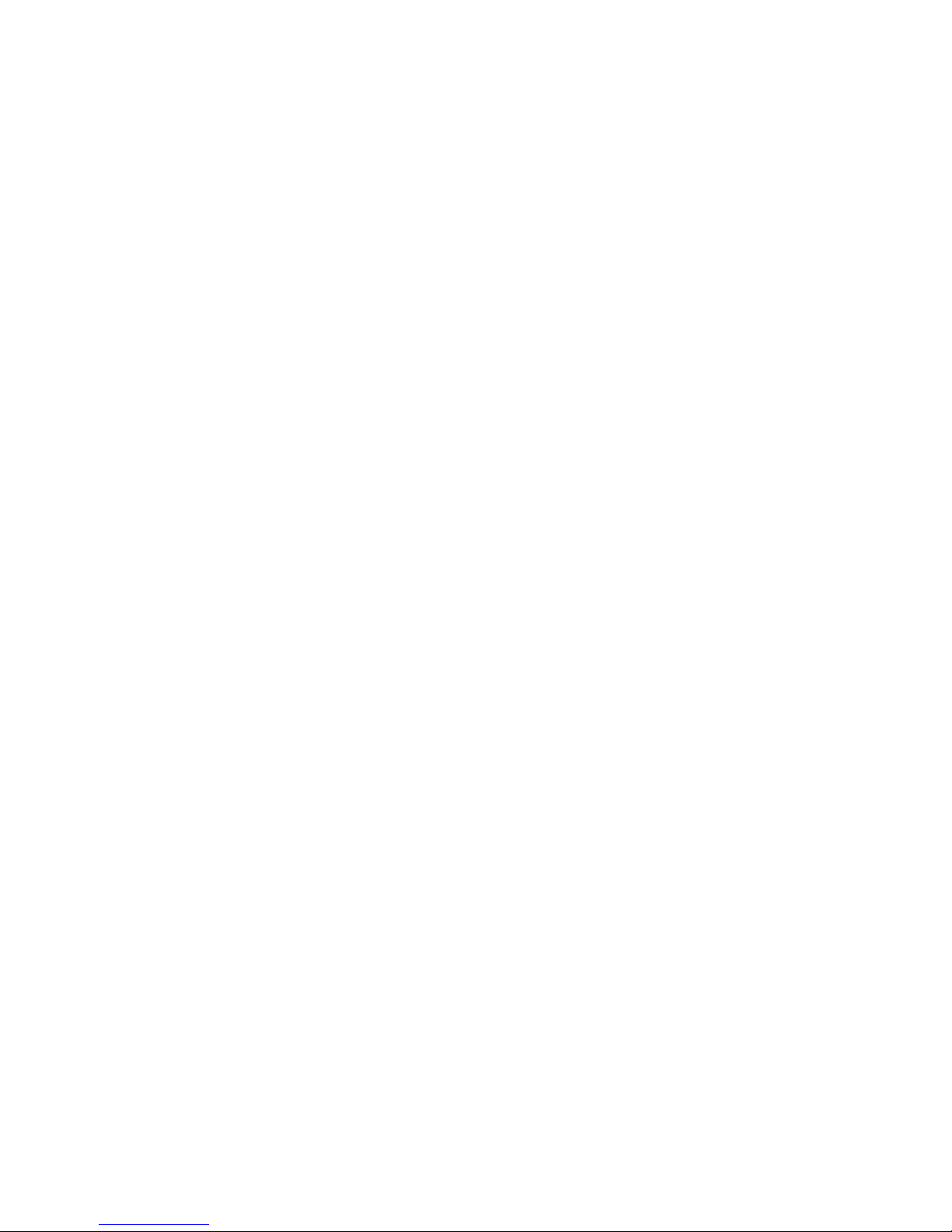
(
_____
This
manual
and Panther
tion
and may be used as a
The
manual is divided
nent
or
and
inspecting
F_o_R_E~
contains
Snowmobiles.
system and, in
instructions
..
W-O-R-D----'J
service, maintenance, and
The manual
textbook
into
sections. Each
addition
. A
to
troubleshooting
is
designed
for
serv ice
section
the standard service procedures,
troubleshooting
to
aid service personnel in service-oriented applica-
training
section
of
.
the
manual covers a
is
also
information
includes
in cluded in
for
the
1987 Jag,
specif
this
ic
snowmobile
assembling,
manual.
Super
disassembling,
Jag,
compo-
The service
or
system
the service
cy
not
only helps build
The procedures in
components. When
ed
to
correct any given cond
manual uses the
The
•
WARNING
because
~
related
(
'or
--"
The
At
Because
All
Keep
information.
parts
of
symbol .NOTE: identifies
the
time of
materials
this
technician
of
the
technician
• id
it
deals
the
snowmobile.
Arctco,
and
manual
should
Jag, Super Jag, and Panther by
in
consumer
this
manual
servicing,
words
entifies
with
the
Be sure
publication,
Inc.
constantly
speCifications
accessible
become
becoming
~
include
the
iti
on.
Warning, Caution, and Note
personal safety-related
possibility
to
read the directive because
If the directive is violated, the
supplementary
all
information,
refines and improves
subject
in the
familiar
more aware
confidence
the
comple
technician
of
shop
should
personal injury. The
to
change
area for reference.
with
the operat ion and
carefully
of
and
but also saves
te
disassembly
information
information
photographs, and
without
efficient
use
discretion
to
it
snowmobi
its
products, no
studying
time
emphasize
. Therefore, be sure
symbol.
deals
worthy
notice.
construction
this
manual.
with
servicing
and labor.
of
the
1987 Jag,
as
to
how
certain
CAUTION.
with
the
possibility
le
will
usually
of
particular
illustrations
retroactive
Service Department
of
This
manual
procedures.
Super
much
disassembly
information
to
read
identifies
of
sustain
attention
were
technically
obligation
each
component
will
Such
Jag, and
. The
the
directive
snowmobile-
damaging
major
.
damage.
is
incurred.
assis
effic
ien-
Panther
is need-
symbo
a part
correct.
t
l
l
CERTIFIED
PARTS
CORPORATION
1111
W.
RACINE
ST
.
PHONE
6081752-9441
JANESVILLE,
WISCONSIN
53545
November 1986
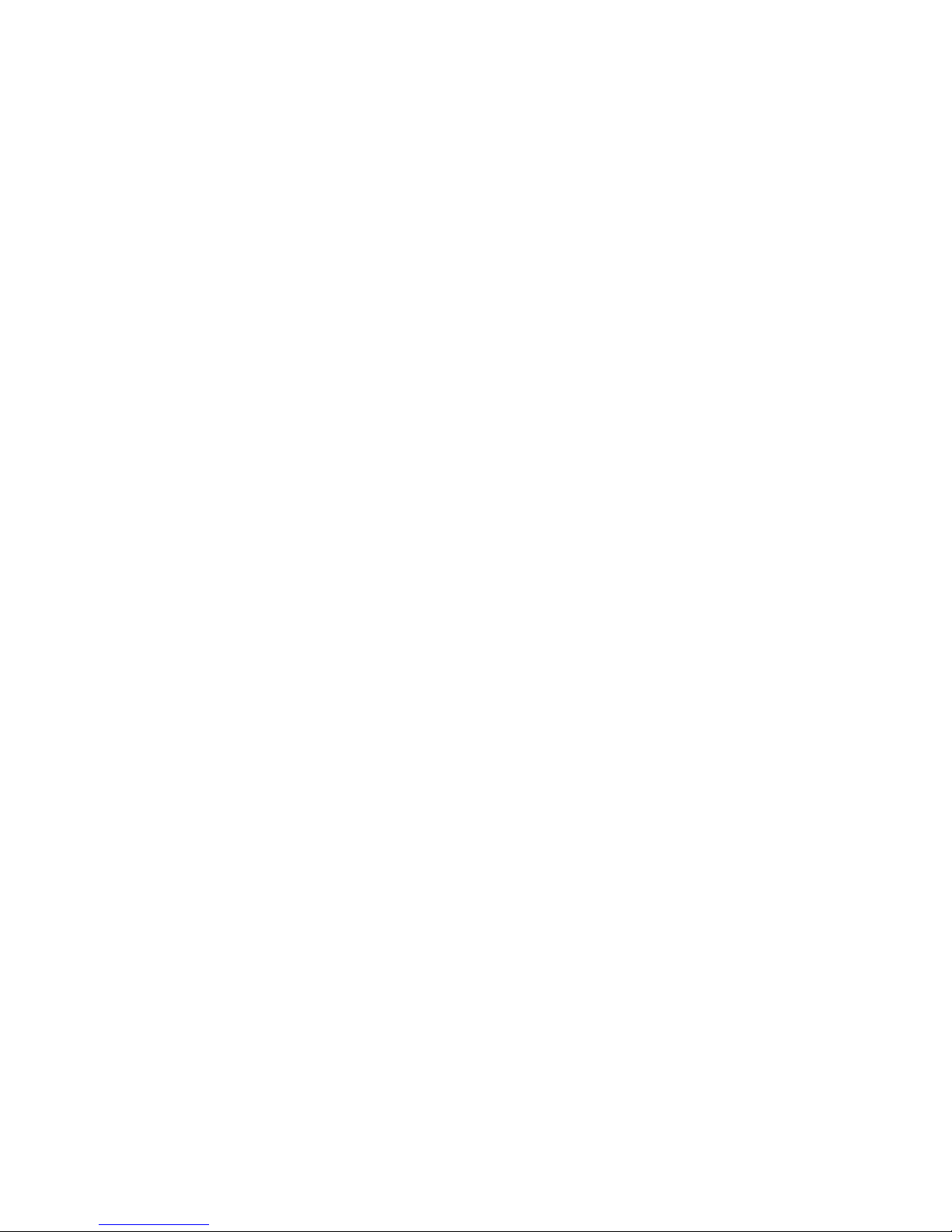
r
Section
1.
General
2.
Engine
3.
Fuel
4.
Drive
TABLE
CONTENTS
System
System
OF
Information
Page
1·5
D
7·37
EJ
39·53
EJ
55·85
II
5.
6.
7.
8.
9.
10.
Electrical
Steering
Track
Recoil
Aids
Troubleshooting
and
Starter
for
System
and
Maintenance
Body
Suspension
87·102
It
103·121
a
123·133
D
135·138
EJ
139·142
m
143·152
1m
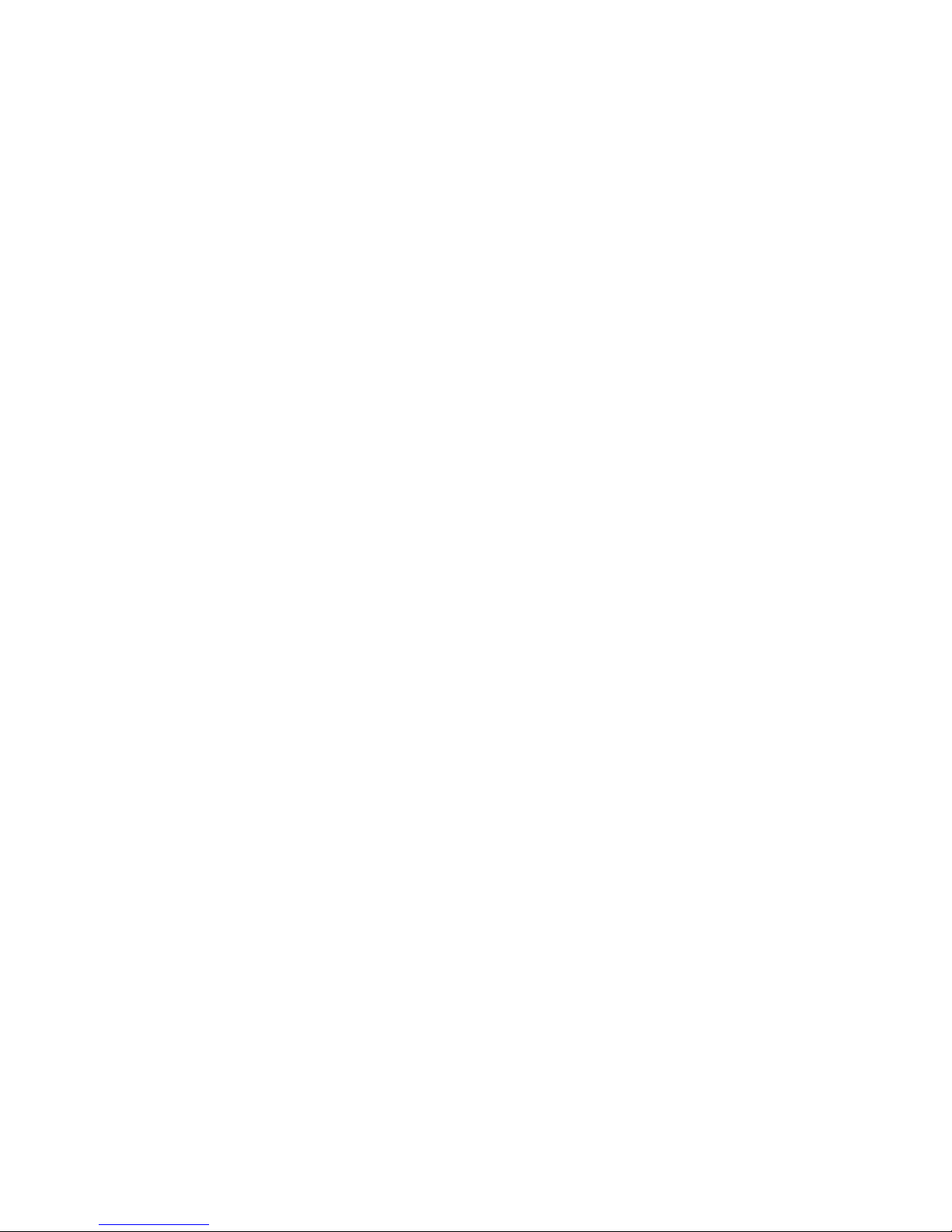
SECTION
1
-
GENERAL
INFORMATION
D
r
TABLE
CONTENTS
Specifications
Break-In Procedure
Recommended
Recommended Oil
Genuine Parts .
Summer
Preparation
. .
Gasoline
Storage
After
...
..............
..........................
Storage
OF
. . .
...
. . .
...
. . .
.....................
......
....................
..................
.
..........
. . ....
....
. .
.
.......
..
.... 4
...
.....
2-3
4
4
.4
4-5
5-6
1
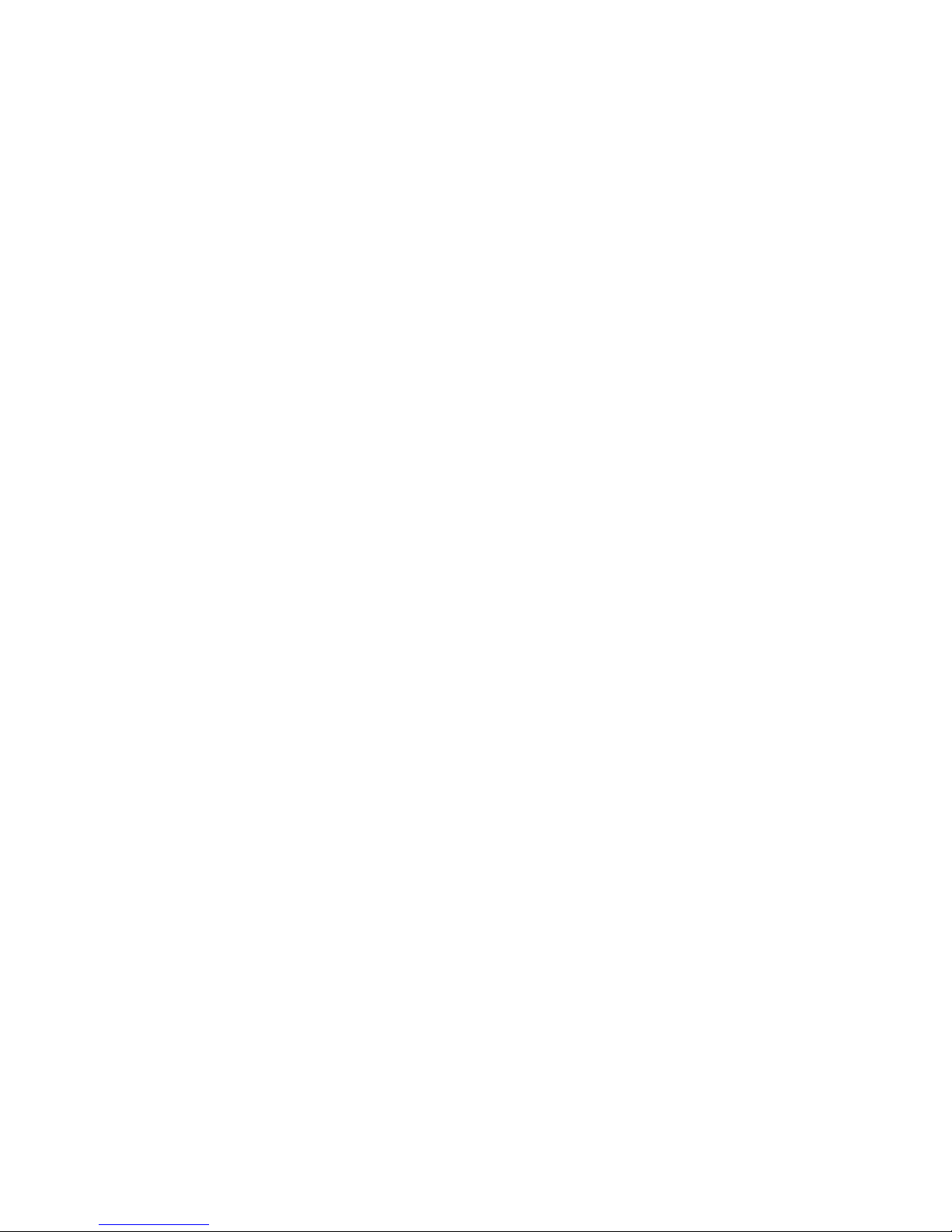
,
Speci,ications
ENGIN'E AND DRIVE
Engine
Displacement
Bore x
Comp
Piston-Ring End mm
P
Piston Pin
Pi
Connecting
Cranks
Crankshaft
Cylinder
Drive
Engagement Speed
Peak
Ramp
Spring (Green)
We
Cha in Pitch
S
Lighting
Ignition
Spark Plug
Brake Type
Track
Overall Track Length
Tr
Drive Belt
Model AF34A6 AG44A8 AL50A6 AG44A8
cc 339
(cu in.) (20.68) (26.29) (30.5) (26.29)
S
trok
e mm 60 x 60 65 x 65 70 x 65
ress ion Ratio 6.8:1 6.5
Gap Range (in.) (0.006-0.031 )
iston SkirtlCylind
Clearance
Range
ston - Pin Bore
Di
Diameter
Range
(Total
Pull ey
Center-to-Ce
ight
procket
ack
Diameter
ameter Range
-Rod Small End mm 21.00-21.01
haft
End Play
Runout (max.)
Indicator
Trueness (max.)
ClutchlDriven
Offset
RPM
Ratio
Coil
Type
Width
Length on Ground
er
Range (in.)
Range
Reading)
nter Dis
Output
tance
@ 3000
(in.) (2.362 x 2.362) (2.559 x 2.559)
mm
mm
(in .)
mm
(in.)
(in .)
mm 0.0
(in.)
mm
(in.)
mm
(in.)
mm
(in.) (1.365)
cm
(in.)
pIn
pIn
pIn
RPM
cm
(in.)
cm
(in.)
cm 94
(in.)
pIn
*
JAG 340
0.15-0.80
0.058-0.15 0.084-0.15 0.084-0.15
(0.
0023-0.006) (0.0033-0.006)
15.994-16.000 15.994-16.000 17.995-18.000
(0
.6297 -0.6299) (0.6297-0.6299)
15.9
96-
(0.6298-0
(0
.8268-0.8273) (0.8268-0.8273)
5-0.1
(0.002-0.004)
0.05
(0.002)
0.1
(0.0039) (0.0039)
35
28
75
)
(11.3
3600-4000
6500
-67
0646-026
0146-068
0146-166
70
20 x 39
12V/15
0W
CDIINCI
NGKB
R8E
38
(15)
295
(116)
(37)
0227-100
JAG
4~0
431
:1
0.20-0.83
(0
.008-0.033)
16.004 15.996-16.004
.6301
) (0.6298-0.6301 )
21.00
-2
1.01
0
00
S
0.05-0.10 0.05-0.10
(0
.002-0.004)
0.05 0.05
(0.002)
0.1
35
(1.365)
28
(11.375)
3600-4000
6000-6200
0146-414
0146-068
0146-104
68
20 x 35
12V/1
50W
CDIINCI
NGKBR9
38
(15)
295
(11
94
(37)
0227-100
ES
Mecha
nical Disc w/Parking Brake
6)
PANTHER
500
(2
.756 x 2.559)
6.5
:1
0.20-0.83 0.20-0.83
(0
.008-0.033) (0.008-0.033)
(0
.0033-0.006) (0.0033-0.006)
(0
.7085-0.7087)
8.
-0
006
35
30
17.998-1
(0.7086-0.7089)
23.00-23.01
(0.
9056-0.9059)
(0
.002-0.004)
(0.002)
0.1
(0
.0039)
35
(1.365)
25.9
(10.2)
3600-4000
7000-7200
0146-414
0146-068
0146-104
68
20 x
12V/150W
CDIINCI
NGKBR9ES
40.5
(16)
307
(121)
94
(37)
0227
SUPER JAG
431
65 x 65
(2.559 x 2.559)
6.5:1
0.084-0.15
15.994-16.000
(0.
6297 -0.6299)
15.996-16.004
(0.6298-0.6301
1.01
21.00-2
(0
.8268-0.8273)
0.05-0.10
(0.002-0.004)
0.05
(0.002)
0.1
(0.0039)
35
(1
.365)
25.9
1
.2)
(10
3600-4000
-6
200
6000
0146-414
0146-068
0146-104
68
20 x 35
12V/150W
CDIINCI
j NGKBR9ES
.5
40
(16)
396
(156)
96.5
(38)
0227-030
)
•
2
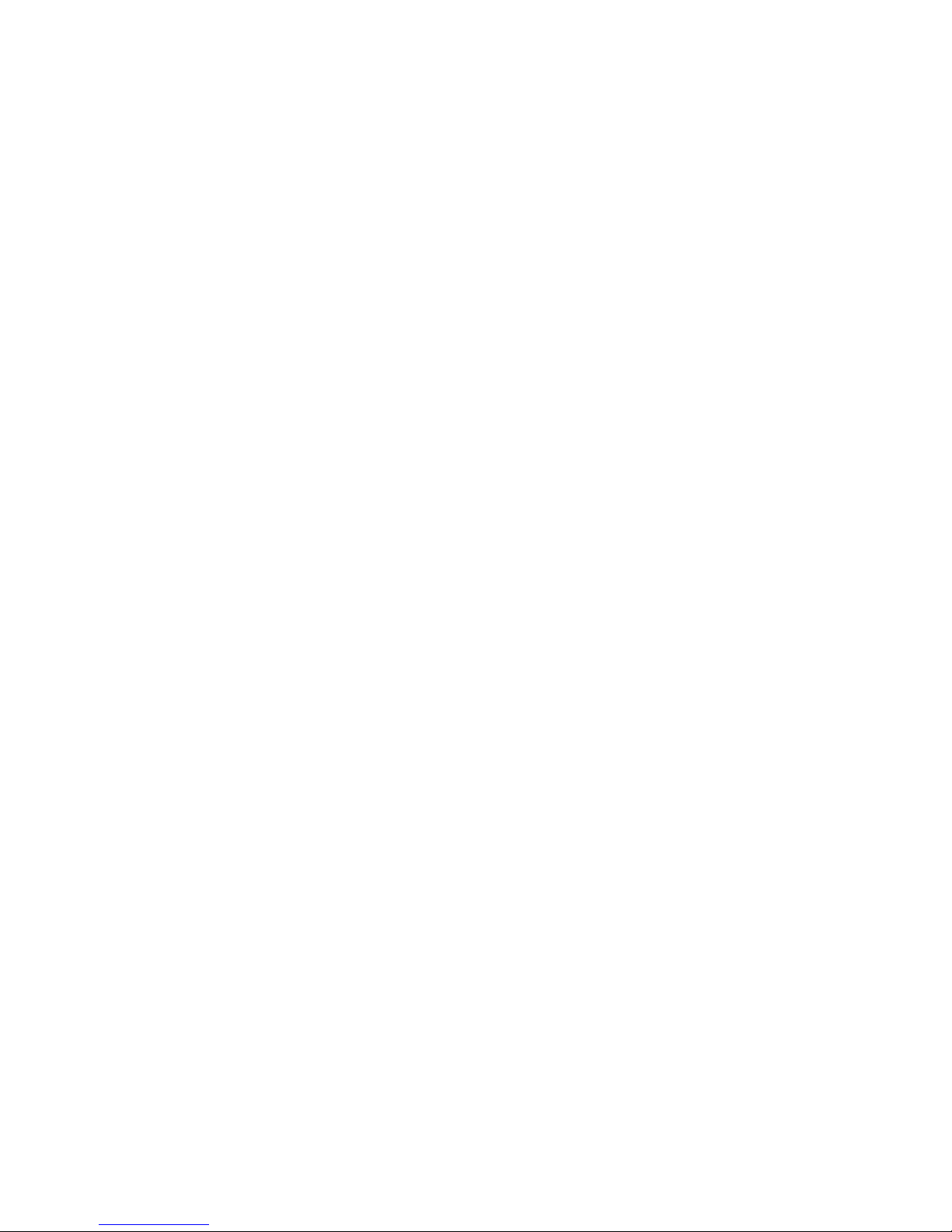
Pilot
Air
Screw
(Turns
CHASSIS
Length
Length
Height
Height
Overall
Ski "Center-to-Ce nter"
MISCELLANY
Curb
Dry
Fuel
Oil Ta nk
Chain
Gasoline
Engine Oil
Chain
Grease
Tai
Headlight
I
Spark-Plug
Gas/Oil
Gas/Oil
""Warm
w/Skis
w/o
Skis
w/Win
dsh
w/o
Windshield
Width
Distance
Weight (approx
Weight (appr
Tank
Capacity
Capacity
Case Level
Octane (rat
Case
Lubricant
II
ight/Brakelight
gnition
Timing""
0
18
BTDC @ 6000 RPM
Gap
Mixture
Mixture
"Specifications
engine
ield
ox.)
(Break-In)
(Aft
er
subject
spec
out
.)
ing)
Break-In)
ific
ations.
)
cm
(in.)
em
(in.)
cm
(in.) (43.2)
cm
(in .)
cm
(in.) (37.5)
I
cm
(in.) (30)
I
I
!
kg 202
(Ib)
kg 1
(I
b)
(U
(U.S. qt) (3.5)
I 28.4
.S. gal)
I 3.3
ml
(fl oz)
I
,
I
to
pIn 0109-460
pIn 0109-735
mm
(in.) (0.073)
mm
(i
n.)
change
without
1%
± %
JAG 340
258
(101.5)
233
(9
2)
110
76
(30)
95.2
76
JAG 340
(445)
81
(400)
(7.5)
236
(8)
minimum
88
1.860
0.7
(0.028)
notic
e.
1112
±
JAG 440
258
(101
.5)
233
(92)
110
(4
3.2)
76 76
(30)
95.2
(37.5)
76
(30) (30)
JAG 440 PANTHER
204 205
(449)
183 186
(404) (410)
28.4 26.8 26.8
(7.5)
3.3 1.7 1.7
(3.5)
236 236 236
8)
(
88
minimum
Arctco/Arctic
Arctco/Arctic
Low
0109-460
0109-735
2.032
(0.080) (0.080)
0.7
(0.028)
50:1
None
PANTHER
267
(1
05)
241
(95)
110
(43.
2)
(30)
95.2
(37.5)
76
(451)
(7.1) (7.1)
(1.
8)
(8)
88
minimum
Cat
Injection
Cat
Chainlube
Temperature
0109
-4
0109-735 0109-735
2.032
0.7
(0.028) (0.028)
+
Oil Injecti
- (Oil
Injection)
Oil
60
on
SUPER JAG
322
(1
27)
297
(117)
110
(43.2)
76
(30)
95.2
(37.5)
76
(30)
SUPER JAG
214
(4
70)
193
(4
25)
(1
.8)
(8)
88 m
0109-460
2.032
(0
.080)
0.7
D
inimum
3
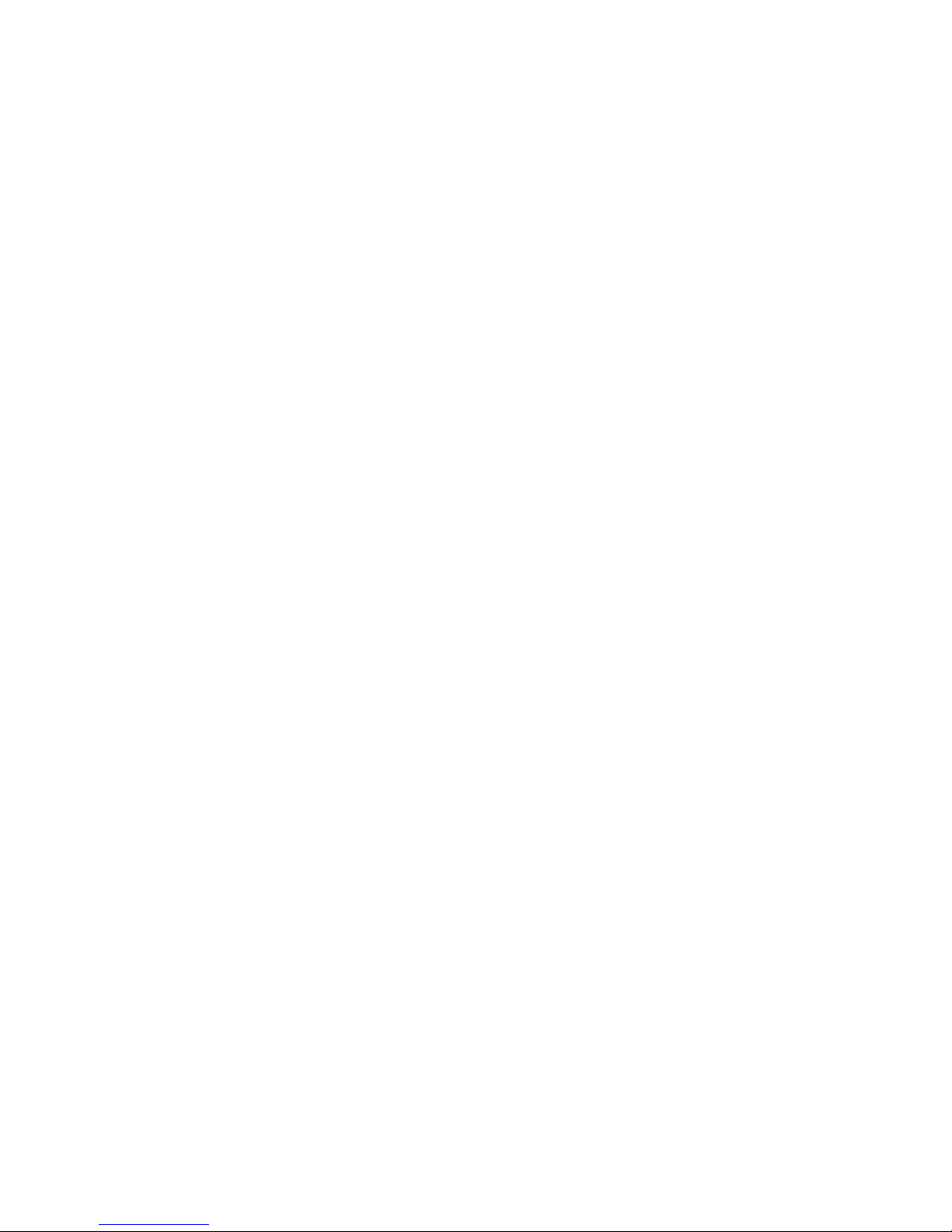
r
,
Break·ln
\..
New and overhauled Panther, Jag, and Super Jag
snowmobile
period
period, pre-mix the
in
conjunction
using
the
is
recommended. However,
celeration
tribute
Following
jet
Main
to
should
Jet
engines
(1
tankful
with
snowmobile, a maximum
and
variations
good
engine
the break-in period,
be
changed
Chart.
Procedure
require a short break-in
of
fuel). During the break-in
first
tank
of
fuel
at a 50:1
the oil-
injection
brief
in
driving
break-in.
the
in
accordance
system. When
of
1/2
full-throttle
speed con-
carburetor
with
ratio
throttle
ac-
main
the
,
Recommended
Gasoline
The recommended
octane
containing
ethanol.
(
......
regular leaded.
either
00
NOT
use
or
more
than
ditives,
MUST
engine
gasohol,
NOT
damage.
_R_e_c_o_m_m_e_n_d
gasoline
methanol
•
CAUTION
gasolines
5%
ethanol.
methanol
BE
USED;
to
DO
NOT use
or
containing
Also,
alcohol,
they
will
__
use is 88
•
either
and
eventually
minimum
gasolines
more than
methanol
gasoline
white
cause
ed_o_il
ad-
gas
__
5%
J
Genuine
When
genuine
precision-made
fit. Refer
correct
(~
Prior
must
component
you
the
1.
2. Clean
3.
4.
5.
replacement
ArctcolArctic
to
the
part
number,
__
s_u_m_m_e_r_S_t_o~r_a_g_e_~J
to
storing
be
properly
deterioration.
to
prepare
following
Remove
seat
cushion
place.
dirt, oil, grass,
the
Allow
NOT get
Place the rear
stand. Remove
the
Start
engine
server
haust
engine
silencer
Drain fuel
drain
the
cushion
with a damp
the
skid
frame,
the
water
carburetor.
the
idling,
into
starts
starts
boot.
the
of
parts
to
ensure
Illustrated
quantity,
the
snowmobile
serviced
the
snowmobile
procedure
passenger
from
the
snowmobile
and
tunnel,
snowmobile
into
of
the
the
engine
the
from
fuel
and
spray a
carburetor
to
smoke
to
drop
the
carburetor
tank
of
Cat
high
to
If a customer
:
strap; then remove the
tunnel.
cloth
other
to
any
snowmobile
intake
allow
two-cycle
in rpm.
all
Parts
is necessary, use
parts.
quality
Parts
and
for
prevent
and store in a dry
thoroughly
foreign
hood, and
dry
part
of
silencer
to
until
heavily,
Install
gasoline.
They
and
correct
Manual
description.
the
summer,
rusting
desires
for
storage, use
Clean
thoroughly.
float
matter
the
up on a
idle.
engine
the
or
the
by
belly
engine.
boot
With
engine
until
the
bowl;
for
hosing
intake
only
are
the
and
seat
from
pan.
DO
jack
from
the
pre-
ex-
the
then
..
it
-
..
The recommended
jection
are
requirements
4
Oil
or
specially
oils
to
Arctic
formulated
of
the
Cat
Arctic
use are
Injection
to
meet the
Cat engine.
either
Arctco
Oil. These
lubrication
In-
oils
6.
Remove the
where
end
of
two-cycle
oil is seen in
manifold
on
the
7.
Plug
clean
it
attaches
the
primer
oil and
or
T-fitting.
the
hole
cloth.
primer
the
carburetor.
in
line
to
the
line
into a small
pump
line
the
exhaust
from
fuel
the
primer
going
Install
the
T-fitting
line. Place
container
button
to
the
intake
the
primer
system
with
the
of
until
line
a
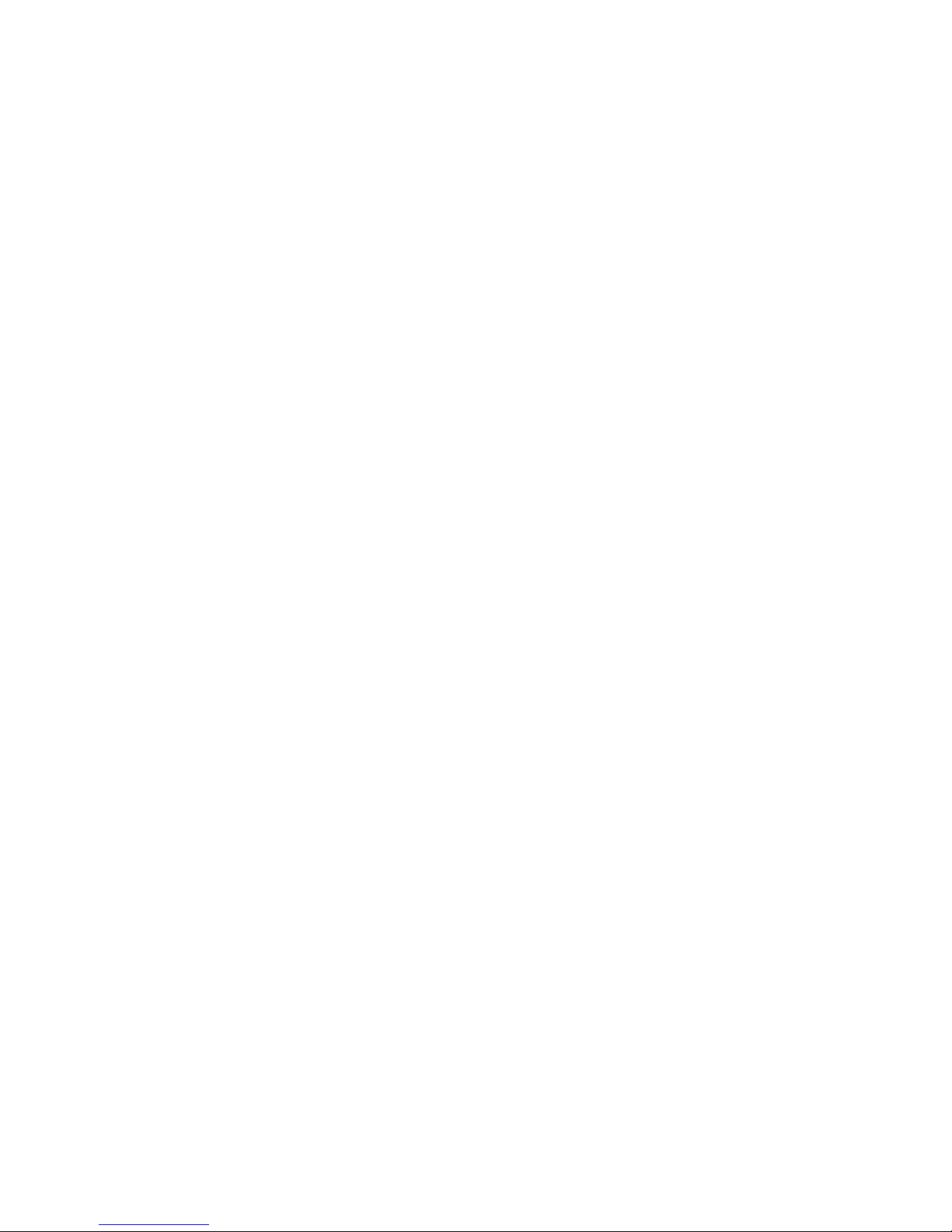
8.
With
the
tion
.
A.
Disconnect
the
B. Pour 29.5 ml
based
pull
times
ignition swit
the
spark
plugs;
(1
oil
into
the
recoil
.
ch key in
high
then
fl oz)
each
handle
tension
remove
of
SAE #30
spark
the
the
plug
slowly
OFF posi-
wires
from
plugs
petroleum
hole
and
about
.
10
with a machine
protect
18.
If
block
making
-
Loosen
track
heavy
and rain.
the
snowmobi
the
tension.
it
sure
the
tarpaulin
cover
from
dirt
entire
the
track-adjustment
Cover
or
and
le
must
snowmob
snowmobi
with a machine
to
protect
a heavy
dust.
be
stored
ile
it
tarpaulin
outdoors,
off
the
le
is
bolts
to
cover
from dirt, dust,
to
ground
secure.
reduce
or
a
C. Insta
9.
Every three years
chain
case
flow
chain,
for
stall
ml
Cat
10. Remove
/driven pulley. Lay
slide
warping
11
. Clean and
pulley.
)
Apply
bushing, ski
pivot
of the s
13.
Lubricate the
temperature
lower
temperature
14. Lightly sand
ing
bottom
ll spark
tension
case
cover and seal.
onto
rags
sprockets,
wear and
chain-case cover and seal and
(8
fl oz)
of
Chainlube
the
it
into a cardboard
or
inspect
light
bushings
hock
steering
black
paint
of
the skis.
plugs
wires.
lubricant
placed
chain
the
chain
either
Arctco
into
drive
belt
the
distortion
the
oil
to
spindles
of
the
absorbers.
rear
suspension
grease. On
post
grease.
the
bottom
pIn 0652-004,
and
connect
or
2000 miles,
by removing
Allow
in
the
belt
during
drive
the
and bolts,
ski frame, and
assembly
the
lubric
the
belly
pan . Insp
tensioner, and pads
for
proper
Chainlube
filler
hole
.
from
the
drive
on a
flat
sleeve
storage.
clutch
upper
the
of
steer
front
arm
Jag,
lubricate the
with a low
the ski
paint
the
high
drain
the
the
chain
ant
ect
tension
surface
to
and driven
with
s;
. Inpour
or
Arctic
clutch
prevent
ing
post
and rear
plungers
a low-
then us-
the
entire
236
to
or
-
-
-
NOTE:
II
ture
rusting
Taking
and
assure
snowmob
the
1.
2.
3.
.
correctly
following
Clean
exterior
tive-type
Clean all
Remove
Check
obstructions
Inspect
of
wear
cable
away from
Avoid
will
using a plastic
collect
on
Preparation
After
the
snowmobile
preparing it
many
mil
iling. To prepare
procedure:
the
snowmobi
of
the
cleaner
engine
the
exhaust
all
control
or
fraying. Replace
ties
or
hot
Storage
es and
snowmobile
wax.
cloth
system
.
tape
or
rotating
the
out
for
hours
the
le
thoroughly.
cooling
from
wires
to
route
cover
snowmobi
of
summer
another
of
snowmobile,
using
fins
the
exhaust
and
air
and
cables
if
necessa ry. Use
wires
parts.
as
mois·
le
causing
storage
season
trouble-free
Polish
an
and vents.
silencer
and
will
use
automo
system.
for
signs
cables
the
for
D
-
15.
Tight
en all nuts,
sure all ca
ed
to
components
loo
se rivets.
16.
Clean and
chassis
DO
CLEANERS.
DAMAGE THE FINISH.
17.
If
possible,
Raise
the
back
secure. Loosen
reduce
libr
specifications.
with
NOT
the
end
track
USE
track
bolts,
ated
nuts
and
Make sure rivets
together
polish
an
automotive-type
THE
sto
re
off
making
the track-adjus
tension.
are
the
SOLVENT
PROPELLENT
the
snowmobile
the
sure
Cover
and
screws
bolts
tight.
hood, console, and
S OR
floor
by
the
snowmobile
tment
the
making
are
tighten
holding
Replace all
cleaner
blocking
snowmobile
wax
SPRAY
WILL
indoors
up
bolts
is
to
-
.
.
4.
Inspect
Check belt
ed, worn,
drive belt.
5. Inspect
necessary.
fuel and
Oil.
6.
Inspect
disc
taillight,
bars, and
necessary.
7.
In
spect
clean as necessary.
the drive
or
the
the
brake-lever trave l, brake
clearance,
brakelight,
headlight aim;
the
belt
for
specifications.
not
within
in-line fuel
Fill
the
oil-
injection
spark
specifications
fuel
tank
all
controls,
ski
alignment,
plugs. Replace, gap,
cracks
Replace
filter
with
tank
adj
ust
and tears.
if
damag-
. In
sta
and replace
the
correct
with
Injection
puck/brake
headlight,
ski wear-
or
replace as
ll
if
or
5
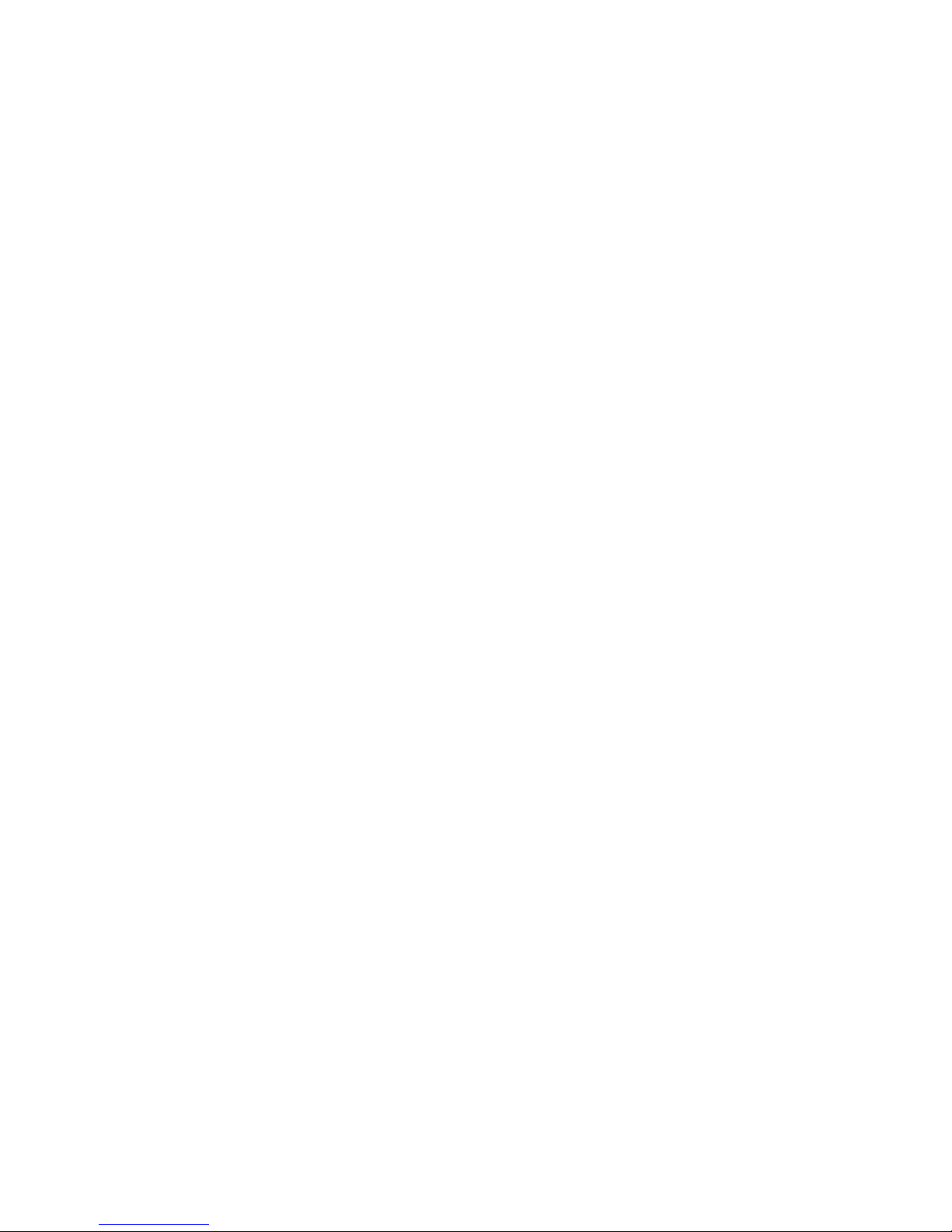
8.
Adjust
alignment.
9.
Adjust
choke
the
the
cable.
track
to
Lock the
carburetor,
the
jam
proper
nuts.
throttle
tension and
cable, and
10. Tighten all nuts, bolts, and screws
sure all
ed
calibrated
to
specifications.
nuts
and
bolt
s are
making
tighten-
•
6
..
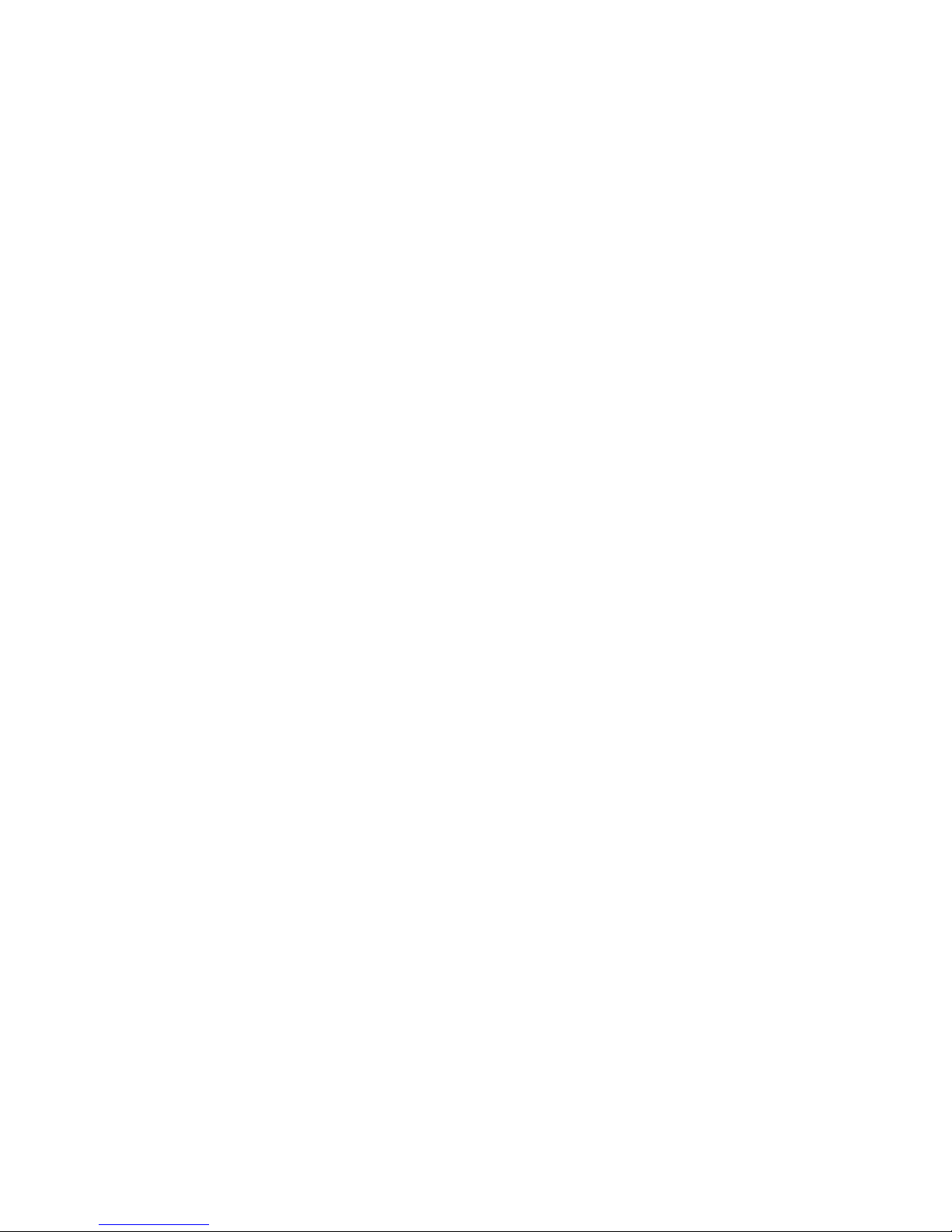
SECTION
2
-
ENGINE
r
TABLE
CONTENTS
Engine S
Removing Engine
Disasse
Disasse
Cleaning and Ins
Cylinder
Cylinders
Piston
Crankcase
Crankshaft ...
Measuring
Cylinder
Piston
Piston-Ring End
Piston Pin and Piston-Pin Bore .
Connecting-Rod
CrankshaftRunout
Asse
Asse
Disassembling
Inspecting
Assembling
Checking
Adjusting
Installing
pecifications ...........
....
mbling
mbling
mbling
mbling
Engine (Jag) .
Engine(Panther)
pecting
Heads . . . .
..............................
Assembly
Critical
Trueness
Skirt/Cylinder
Engine (Jag)
Engine (Panther)
Axial
Axial
Axial
Axial Fan-Belt Tension
Engine
......................
.............................
......
Components ...........
.......................
Gap
Small
Axial Fan
Fan
.....
Fan
Fan-Belt Tension .....
........................
. . .
...
Engine
...................
...
...
Clearance
.....................
End
.....
.......
......
..
...
....
OF
............
..............
...
........
...........
......
.........
......
..............
.............
........
..........
............
..... 18-2
............
.........
.
........
.
.........
.....
...
........
. . .
...
.
9-10
.. 10-14
14-18
18-19
19-20
20-21
21
-23
. . 22
...
23-28
28-33
33-34
....
. 34
34-35
..
. 35
36-37
8
1
19
20
21
21
22
22
23
35
7
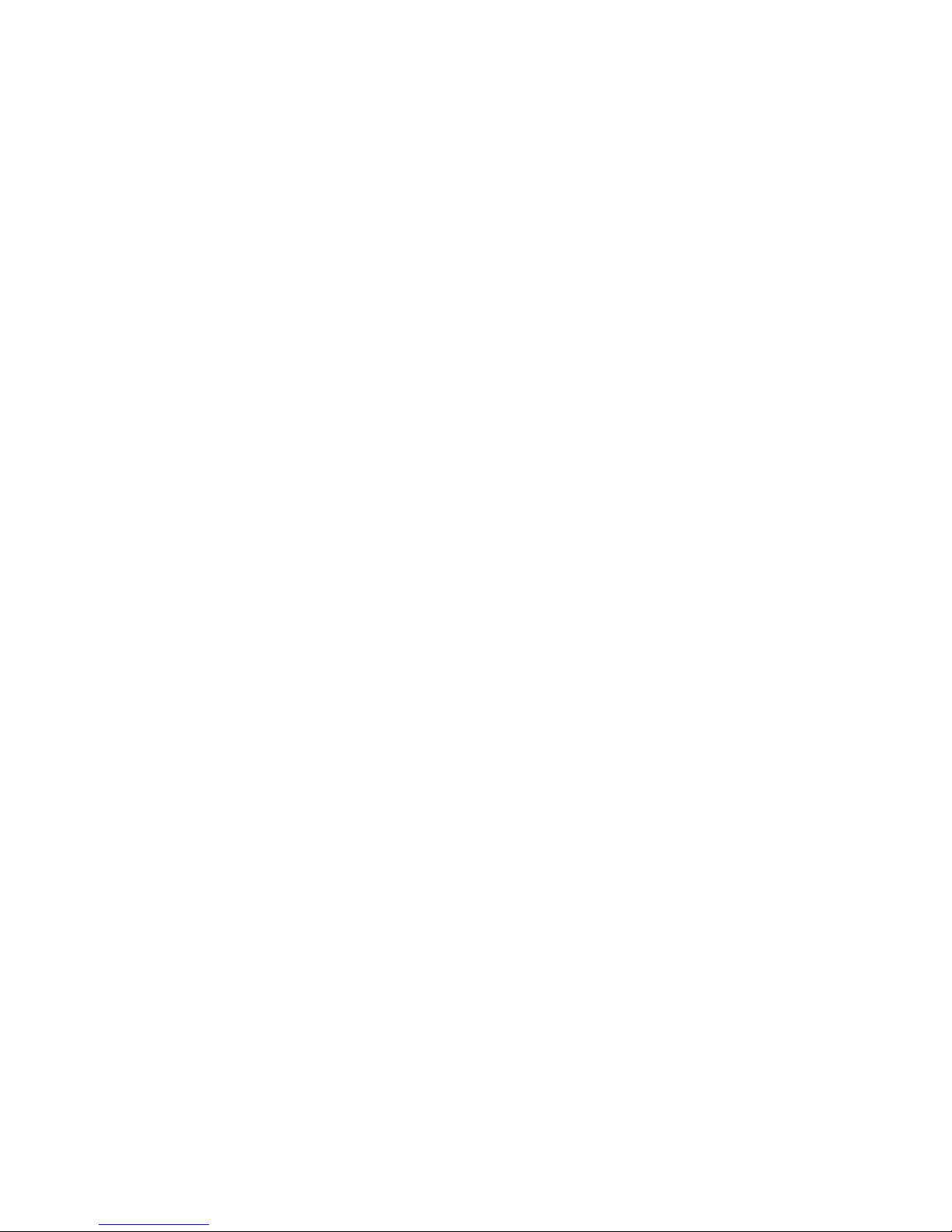
Engine Specifications
...
"""",
•
,
Piston
Clearance
Piston
Piston
Range
Connecting-Rod
Diameter
Crankshaft
Crankshaft
(Total
Cylinder
Skirt/Cylinder
Range
Pin
Diameter
-Pin Bore
Indicator
Trueness (max.)
Diameter
Small
End Play Range
Runout (max .)
Reading)
Range
End
60 x 60 65 x 65
mm
(in.)
(2.362 x 2.362) (2.5
cc
(cu in.) (20.68) (26.29)
339
mm
0.15·0.80
(in.)
(0.006-0.031)
mm
0.058-0.15
(in.)
(0
.0023-0.006)
mm 15.994-16.000
(in.) (0.6297-0.6299)
mm
15.996-16.004
(0.6298-0.
(in.)
mm
21.00-21.01
(in.) (0.8268-0.8273)
0.05-0.10
mm
(in.)
(0.002-0.004)
mm
0.05
(in.)
(0.602)
mm
0.1
(in.) (0.0039)
6301
)
59
431
0.20·0.83
(0
.008-0.033)
0.084-0.15 0.084-0.15
(0
.0033-0.006)
15
.994-16.000
(0.6297-0.6299)
15.996-16.004
(0
.6298-0.
21.00-21.01
(0
.8268-0.8273)
0.05-0.10
(0.002-0.004)
0.05
(0.002)
0.1
(0
.0039)
x 2.559)
6301
65 x 65
(2.559 x 2.559)
(0
.0033-0.006) (0.0033-0.006)
17.995-18.000 15.994-16.000
(0.7085-0.7087)
17.998-18.006
)
(0.
7086-0.7089)
23.00-23.
(0.9056-0.9059)
0.05-0.10
(0.002-0.004)
0.05
(0.002)
0.1
(0
.0039)
01
0.084-0.15
(0.6297-0.6299)
15.996-16.004
(0.6298-0.6301)
21.00-21.01
(0
0.05-0.10
(0
0.05
(0
0.1
(0
.8268-0.8273)
.002-0.004)
.002)
.0039)
/
I
\
8
•
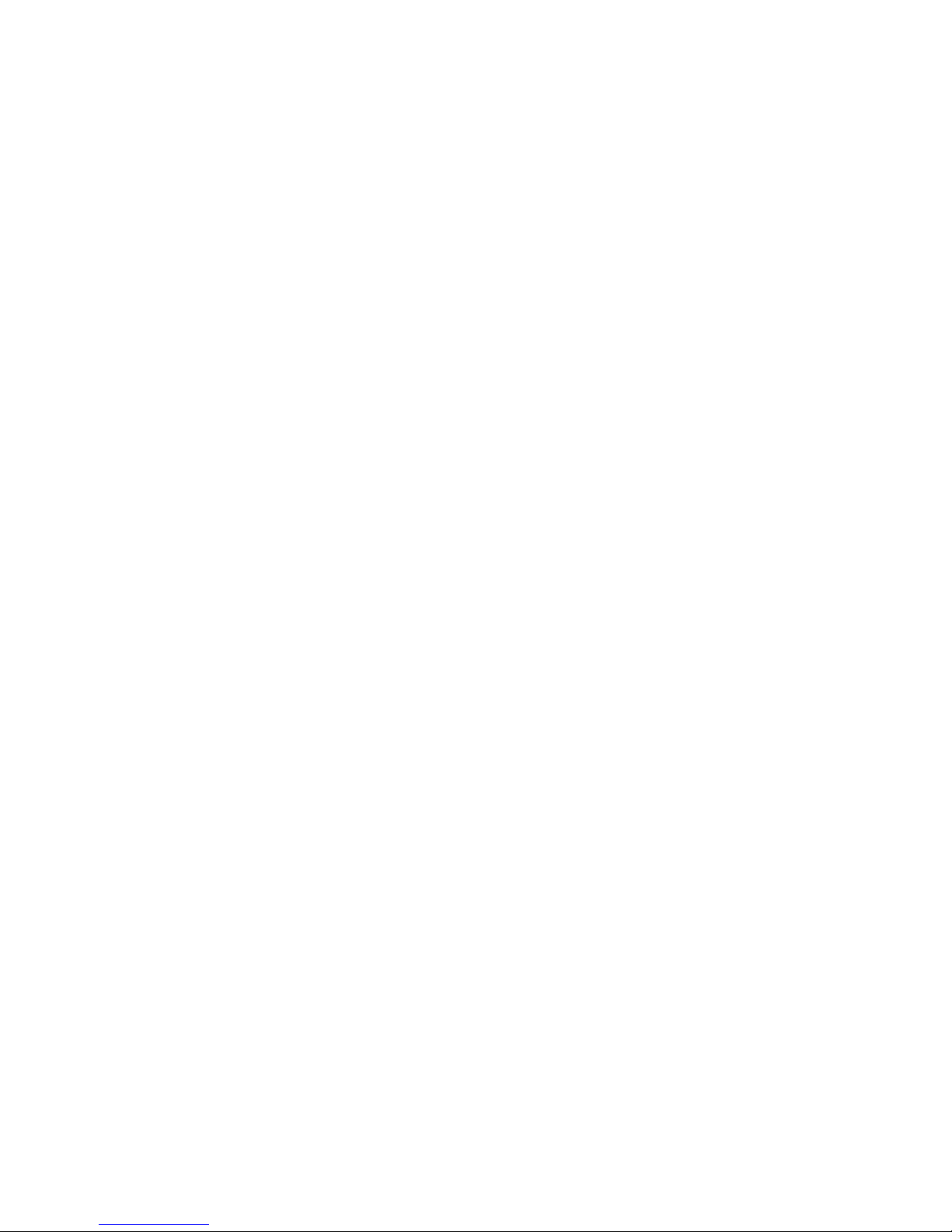
Removing
Engine
NOTE: Procedures designated
II
the Jag 340, Jag 440, and
cedures designated
1.
Open
the
clutch
belt.
2.
Remove
the
either
impact
Wrench (pIn
the
the
cedure
drive
the
wrench
drive
head
until
the
clutch
clutch
of
"B"
shield; then remove
bolt
and
to
the
Arctic
Drive
or a breaker bar and a Spanner
0144-007),
will
not
the
puller. Repeat
the
clutch
"A"
are for
Super Jag; pro·
are for the Panther.
the
lock
washer
crankshaft;
Clutch
tighten
release,
releases.
securing
then
Puller and an
the
puller:
sharply
complete
drive
using
If
stnke
pro-
5. Remove
securing
recoil in
the
the
the
four
recoil;
engine
bolts
then
and
lock
remove recoil. Leave
compartment.
washers
NOTE: Before installing the clutch puller,
II
apply oil
small amount of grease to the tip of the puller.
3. Remove
ment.
to the threads of the puller and a
the
clutch
from
the
engine
..
4.
A.
Remove
haust
the
front
B. Remove
haust
remove
charger
the
three
manifold
two
springs
end and remove
the
manifold
the
to
to
securing
three springs
to
two
springs
the
brackets
springs
the
muffler;
the
the
pulse
securing
.
the
compa
securing
then
muffler
muffler.
securing
charger;
the
rt-
the
ex-
remove
to
the
the
ex -
then
pulse
6.
Disconnect
7.
Disconnect
case
Disconnect
8.
jection
flange clamp
and
supply
to
prevent
the
the
.
the
pump;
air-intake
hose
from
oil
main
wiring
impulse
oil-injection
then
loosen
and
slide
silen cer.
the
pump
drainage
harness
hose
cable
the
carburetor
Disconnect
and plug
.
from
from
.
the
crank
the
carburetor
off
flange
the
oil-
the
hose
-
in-
-
9
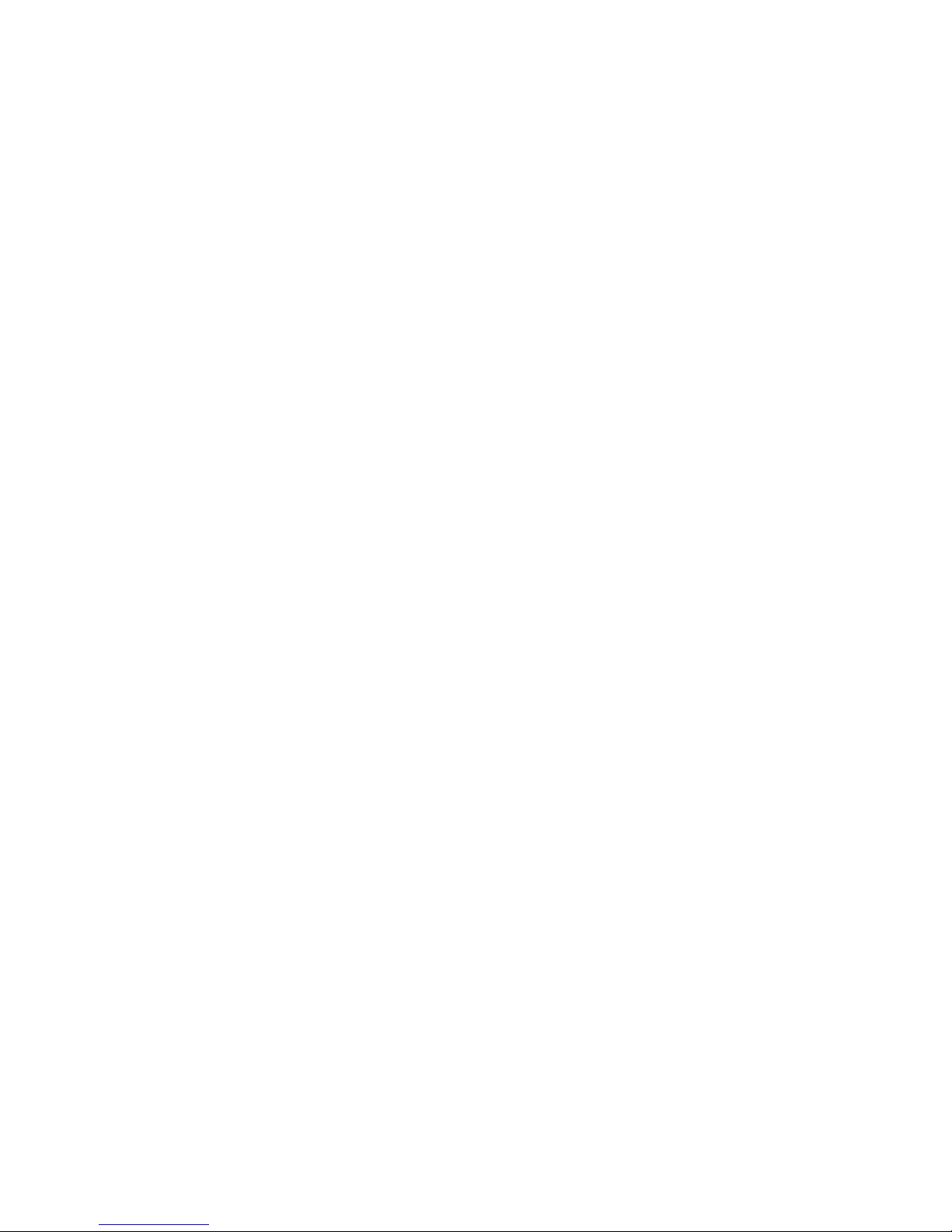
9.
Remove the
rear
count
washers.
two
cap-lock
of
the engine plate
for
two
female
screws
to
the
mounts
securing
front
end.Ac
and
the'
cup
r
-
Disassembling
(Jag
340,
Jag
440,
Engine
and
Super
Jag)
10.
Remove
engine
two
female
Fig.2·S
11.
Lift
the engine w/plate
engine
12
. Remove the
securing
then separate
the
two
cap-lo
support
compartment.
the
to
mounts
four
plate
engine
the
bolts
ck
screws
front
and
cup
assembly
and
assembly
and
plate
securing
end.
Account
washers.
out
lock
to
the
assembly.
the
for
of
the
washers
engine;
1.
Remove the
manifold;
Account
2.
Remove the 14
washers
cooling
3.
Disconnect
spark
the engine and
shroud
count
gaskets.
plugs.
nuts
then remove
for
two
securing
shrouds.
the
Lift
slide
off
the
exhaust-manifo
for
two
securing
the
gaskets.
bolts,
the
spark-plug
the
exhaust
lock
top
top
the
exhaust-side
the
exhaust
exhaust
and
caps
cooling
manifold/shroud
manifold.
washers
exhaust-side
from
shroud
cooling
ld
studs.
~
, and
the
off
Ac-
..
10
Fig. 2·8
I
4.
Disconnect
their
fittings
the
two
on the
oil-injection
intake
manifold.
hoses
B155
from
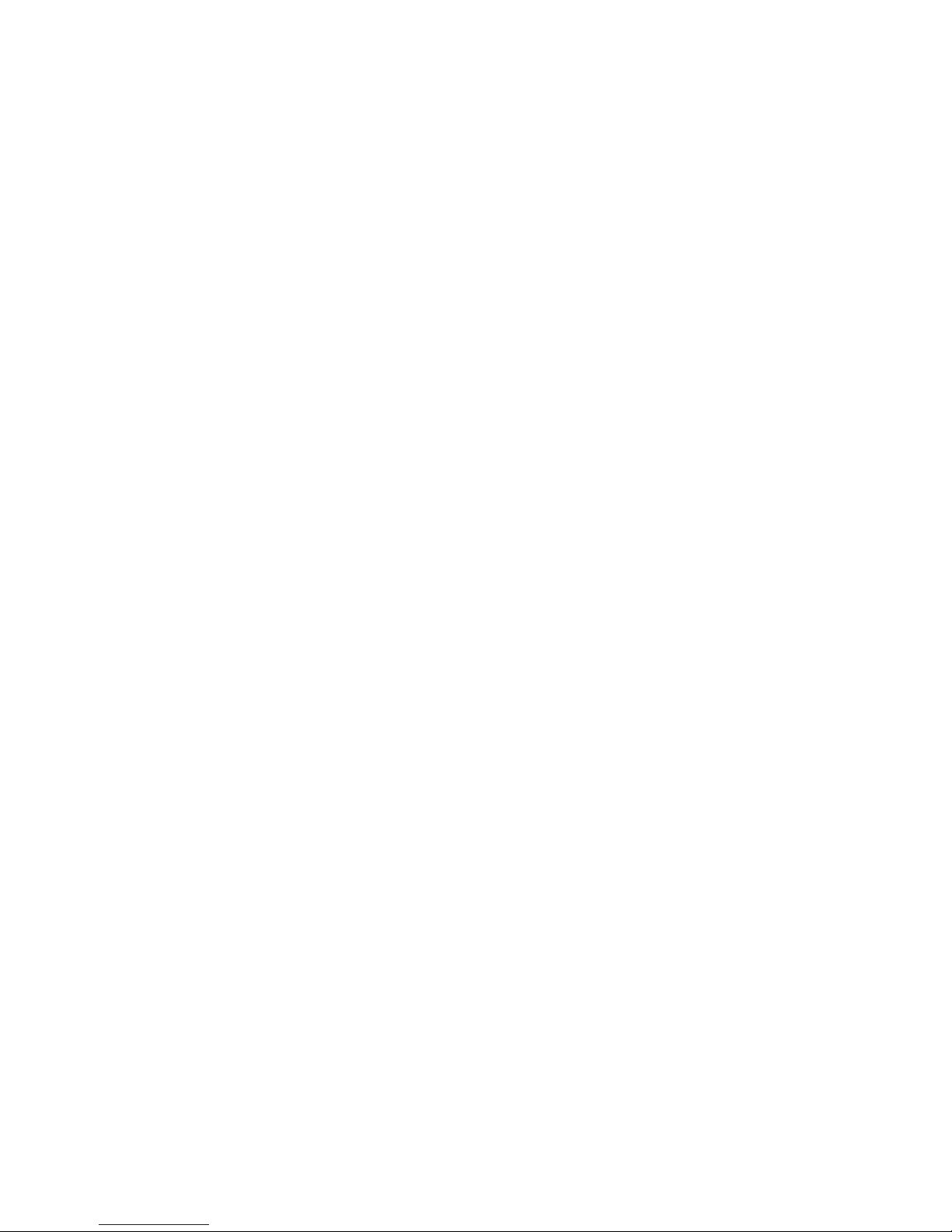
5.
Remove the six
manifold
from
the
nuts
and remove
engine.
Discard
securing
the
manifold
the
two
the
intake
w/flange
gaskets.
8.
Temporarily
flywheel
wrench
remove
Fig. 2·12
with
to
the
secure
install
three
the
flywheel
the
starter
bolts.
crankshaft,
nut
and
pulley on
Using a
loosen and
washers
the
spanner
.
EJ
Fig. 2·10
6.
Remove
from
7. Using a
shaft, remove
washers
flywheel. Remove
carefully
seated
the
the
engine.
spanner
position
intake-manifold
Discard
wrench
the
securing
pry
the
the
fan-belt drive
on
the
cooling
the
two
gaskets
to
secure
three
the
bolts
sta
rter
starter
flywheel and remove .
the
and
pulley
puliey; then
pulley
shroud
.
crank
lock
to
the
from
its
NOTE: If
III
use of a spanner wrench will not be
necessary.
9.
Remove
pulley
10. Remove
the
crankcase;
and
the
fan case. Remove
ment)
fan case.
NOTE: For further servicing of the axial fan
III
components, see page
Fig. 2·13
-
the
to
the
the
washer
the
ignition
an
impact wrench
three
bolts
flywheel
four
nuts
then
remove
securing
coil
is
secur
ing
and remove
securing
the
(if
and COl
33.
the
the
COl
in need
being used,
the
starter
the
pulley
fan
case
PTO-side
unit.
Remove
of
replace-
unit
from
.
to
bolt
the
...
- Fig. 2·11
11. In
stall a protective
crankshaft.
NOTE: A protective cap can be made
III
welding a 3
of a spare
flywheel nut.
mm
(118
cap
in
.) washer
onto
the
end
on
one side
of
the
by
11

Fig. 2·14
NOTE: The
II
LOCTITE
assembly. Before removing
two
stator
applied
to
plate
the
them,
blow to the head of each screw
TITE loose.
very
difficult
Fig. 2·
16
If
this
to
isn't
remove.
done,
screws
threads
apply a sharp
to
break the
the
screws
have had
during
LOC·
can
be
To
prevent
protective
must
crankshaft.
than
Damage
12.
Using
0144-310) or
flywheel
the
puller
bolt
again. Repeat
free .
crankshaft
Fig. 2·15
•
CAUTION
damage
cap
onto
bottom
12.7
with a brass
Account
to
the
from
on
Also,
mm
the
coils
Arctic
suitable
bolt,
.
the
do
(1/2 in.)
the
striking
procedure
for
to
the
crankshaft,
the
crankshaft.
cap
and
not
thread
puller
into
may
result.
Flywheel Pull
equivalent,
crankshaft
the head
hammer, and
until
the key in
•
The
not
bolts
the
by
the
the
thread
a
puller
on
the
more
flywheel.
er
(pin
remove the
tightening
of
the
puller
tighten
flywheel
end
of
ing
the
is
14. Remove
15. Remove
washers
remove
Account
Fig. 2·17
the
stator
the
two
securing
the
pump,
for
two
plate
bolts,
the
oil-injection
retainer,
gaskets
lock
.
from
the
washers, and
pump;
shim,
and gear.
engine.
then
NOTE: To ensure
II
wheel
magnets
13.
Scribe
crankcase
the
securing
12
magnets,
facing
a line on
two
screws,
the
upward) on a
to
place
aid
lock
stator
the
cleanliness
the
clean
the
stator
in
assembly;
washers, and
plate
.
flywheel
of
(with
bench_
plate
then
washers
the
fly
the
and
remove
16
. Remove
the
spark
plugs.
..
17.
Remove
heads
account
-
to
the
the
for
eight
nuts
cylinders
two
gaskets.
securing
. Remove
the
the
cylinder
heads
and
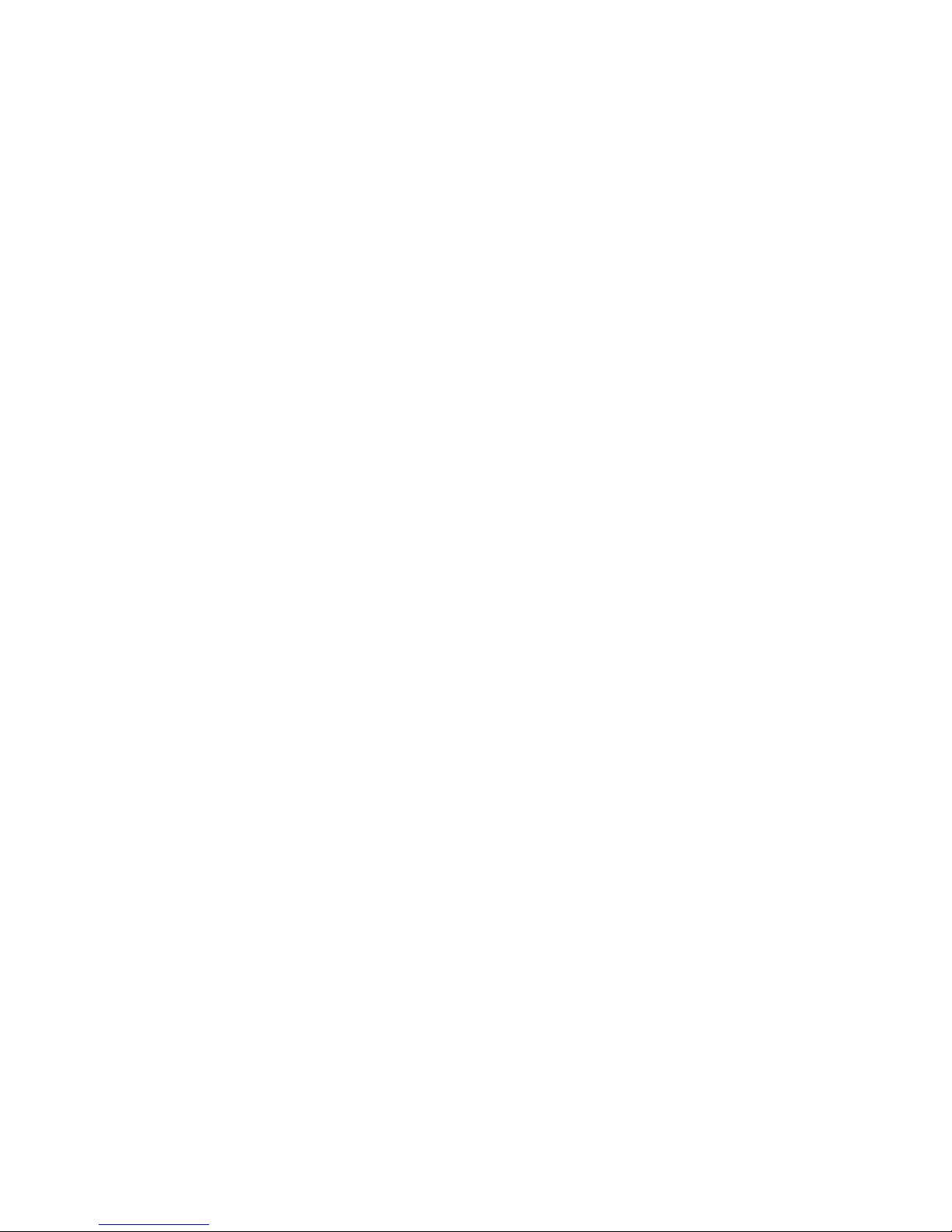
Fig. 2·
18
~~~~!!I!!II.
18.
Using a rubber hammer,
cylinders
lifting
Discard
and remove
them
the
straight
two
from
gaskets
CAUTION
•
When
removing a cylinder,
the
piston
so
it
will
not
be
""'
Using a felt-tipped marker, mark an M on
MAG- side
PTO-side
II
nents
sides.
NOTE:
side
separated.
cylinder
cylinder
For
proper
components
Assemble
and
and piston.
assembly,
and
gently
the
up
off
.
•
make
sure
damaged
piston
all
PTO·side
them
.
and a P on
keep
on
tap the
crankcase
their
to
support
all
their
studs.
MAG·
compo·
proper
by
the
the
Fig. 2·20
00
NOT
free
of
piston-pin
22
.
Lift
the pistons
and r
bearings;
each
pin, and
NOTE: Place
II
ing
rods
will
keep
the
crankcase.
Fig. 2·21
•
use
any
the
piston;
puller
emo
ve
then
piston
bearing
and
connecting
type
only
clear
the
remove
with
rubber
around
CAUTION
•
of
punch
to
damage
.
small
its
together
may
of
the
end
the piston
rings; keep each
as a set.
bands
the
rods
over
cylinder
from
A830
drive
the
pin
result.
connecting
Use
a
rods
connecting-rod
rings. Keep
piston,
the
connect·
studs.
damaging
This
EJ
the
20.
Remove
the
piston
Fig. 2·19
the
PTO-side
-pin
circlip
PTO-side pi
piston;
from
remove
the
ston
-pin
MAG- side
the
;,
1
Using
0144-003), remove
pistons
the
.
Arctic
Piston-Pin
the
piston
-pin s from both
circlip
MAG-side
piston.
Puller
from
A829
(pin
23.
Remove
washers securing
th e
position
the
of
14
the
bolts,
the
crankca
diff
erent-sized
lock
washers, and
se halves.
Note
bolts.
13
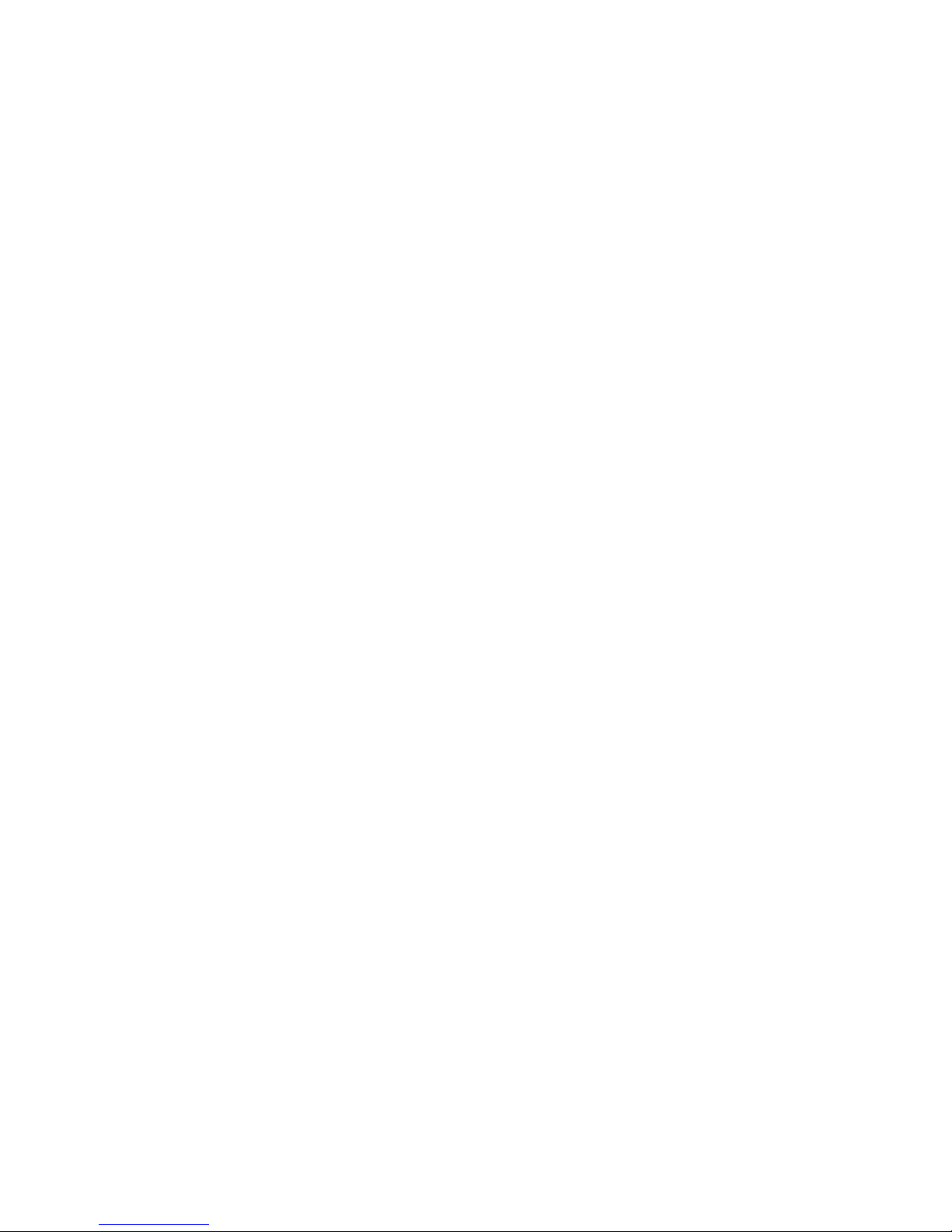
8160
3.
Disconnect
spark
4.
Loosen
injection
take
secure
remove
intake gaskets.
Fig. 2·24
plugs
.
the
hoses
manifold
the
intake
the
manifold.
the
spark-plug
clamps;
from
. Remove
manifold
caps
th en
pull
their
fittings
the
four
to
th e
Rem ove and
from
the
two
on
nuts
engine
discard
the
the
oil
in-
that
and
all
-
24. Using a rubber
separate
the
dowel
the
pins.
or
crank
CAUTION
•
00
NOT
drive
any
tool
between
the
crankcase.
will
result.
25.
Remove the rubber
ting
rods,
crankcase
seals
off
Disassembling
Damage
lift
the
half, and s
the crank shaft.
(Panther)
plastic-tipped
cas
e halves. Account
•
halves
to
to
the
sea
ling
bands
holding
crankshaft
lide
the
Account
free from
two
Engine
hammer,
for
separate
surfaces
the conn ec-
the
crankshaft
for a C-ring.
"""I
5. Remove
from
the
from
behind
Fig. 2·25
the
intake-manifold
eng in
e.
Remove
th e
shroud
the
and
coo
ling
int
ake
discard
023
shroud
gaskets
.
1. Remove
manifold; then remove
A
ccou
2.
Remove
washers securing
cooling
Fig. 2·23
14
the
nt
for
the
shro ud
nuts securing
the
two
gaskets.
12 bolts, l
the
top
s.
the
exhaust
ock
washers, and
and exhaust-side
exh
aust
manifold
022
.
024
6.
Lift
the
upper
coo
ling
S
lide
the
exhau stexhaust
exhaust-side
manifold stud
gaskets
behind
shroud from
cooling
s.
Account
the
the
shro
for
shroud.
engine.
ud
off
th e
the
two
•
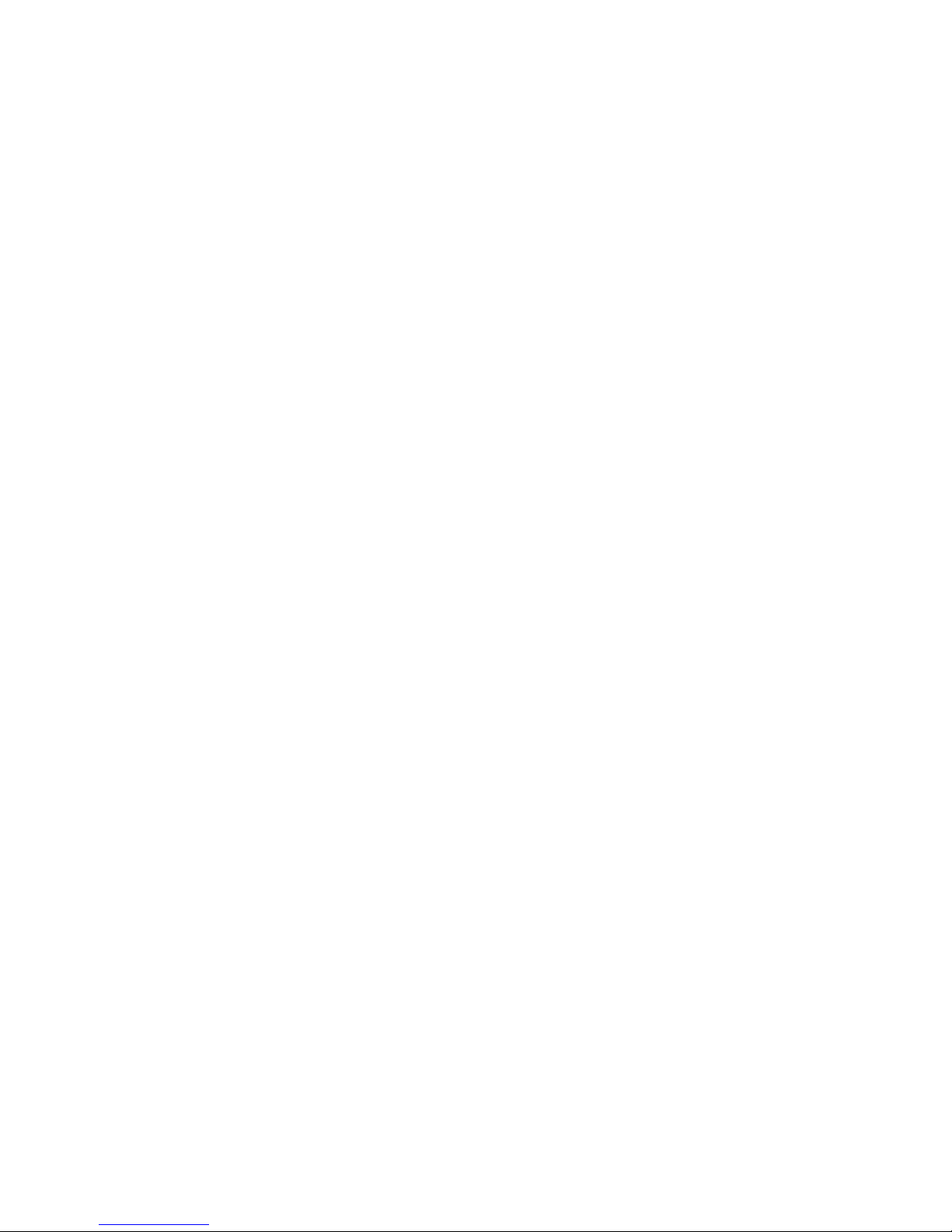
Fig. 2·26
7.
Using a
crankshaft,
washers
pulley
pulley.
spanner
remove
that
secure
to
the flywheel; then remove the
wrench
the
three
the
starter
to
bolts
pulley
025
secure the
and
lock
and fan
starter
9.
Temporarily
flywheel
wrench
re
to
move the flywheel
Remove the s
Fig. 2·29
install
with
secure
tart
thr
the
ee
bolts.
the
crankshaft,
er
pulley
starter
Using a
nut
from
pulley
and
the
on
spanner
loo
sen and
washers.
flywheel.
the
•
Fig. 2·27
8.
Using a screwdriver, pry the fan
the flywheel and remove.
Fig. 2·28
pulley
free
026
of
10. Remove the
to
the magn e
fan
housing
need
of
replacement) the CDI
tion
coil from
Fig. 2·30
_ NOT
-
11.
E:
For
components,
Install a protective
crankshaft.
six
nuts
to
backing
free
of
the
further
see
securing
plate
the
engine. Remove
fan housing.
servicing
page
33 .
cap
onto
the
and
unit
of
the
fan
housing
slide
and igni·
the
axial fan
end
of
(if
the
in
029
the
027
_ NOTE: A
-
welding
of
a spare
flywheel
protective
a 3
mm
nut.
(118
cap
in.)
can
washer
be
on
made
one
by
side
15

To
prevent
protective
must
shaft.
12
.7
the
coils
12.
Using
equivalent,
crankshaft
ing
the
hammer, and
cedure
the
key in
Fig. 2·31
bottom
Also,
mm
(1/2
may
the
head
until
•
damage
cap
onto
on
do
not
in
result.
Arctic
remove
by
tightening
of
the
the
end
CAUTION
to
the
crankshaft,
the
crankshaft.
the
cap
and
thread
puller
.)
into
the
flywheel.
Flywheel
the
the
puller
tightening
flywheel
of
the
•
thread
a
The
puller
not
on
the
crank
-
bolts
more
than
Damage
Puller
flywheel
the
puller
bolt
again. Repeat pro-
is free.
crankshaft.
to
or
sui
tabl
from the
bolt, strik-
with a brass
Account
e
031
for
NOTE: To
II
wheel
magnets
13. Scribe a
crankcase
the
securing
NOTE: The
II
LOCTITE
assembly.
blow
TITE
very
difficult
facing
two
to
the head
loose.
magnets,
Before
ensure
upward)
line
to
sc rews,
the
stator
two
applied
of
If
this
to
remove.
the
place
on a clean
on
the
aid in
removing
isn't
lock
stator
each
assemb
washers, and
plate
to
screw
done,
cleanliness
the
flywheel
bench.
sta
tor
ly; th en remove
to
the
crankcase.
plate
screws
the
threads
them,
apply a sharp
to
break
the
screws
of
the
(with
plate
washer
have
the
can
030
fly
the
and
had
during
LOC-
be
032
14.
Loosen
tainer
from
plate
Fig. 2·34
-
s
15.
Using
eight
the
on
from
the
screw
bracket
the
magneto
from the engine.
an
impact screwdriver, remove
screws
crankcase. Using a plastic
the
backside
the
crankcase.
that
. Remove
case
securing
of
the
secures
the
and
the
magneto
magneto
the
wiring
remove
hammer,
case
wire
grommet
the
stator
033
the
case
tap
to
free it
re-
to
16
NOTE:
II
sharp
break
screws
the
can
Before
blow
to
LOCTITE
be very
removing
the
head
loose.
difficult
If
the
of
this
to
remove.
screws,
each
isn't
done,
apply
screw
a
to
the
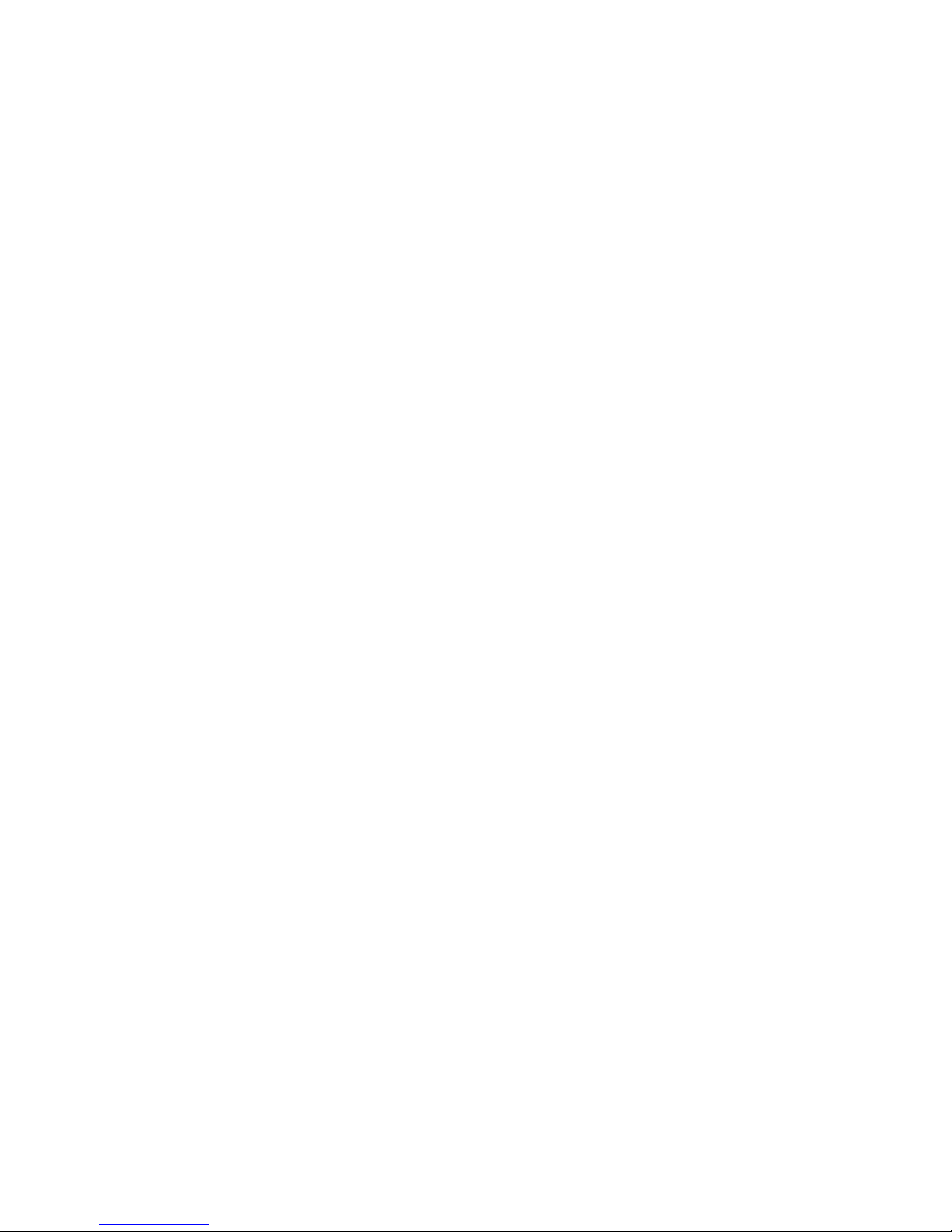
Fig. 2·35
16.
Remove
washers
remove
Account
Fig. 2·36
the
two
bolts,
securing
the
for
the
pump, retainer, shim, and gear.
two
gaskets.
lock
washers, and
oil-injection
pump; then
19. Remove
cylinder.
on
the
crankcase
Remove and
Fig. 2·38
the
four
cylinder
Using a rubber
side
of
each
by
lifting
discard
base
hammer,
cylinder
straight
gaskets.
nuts
from
gently
and remove
up
off
the
each
tap
from
studs.
EJ
17
. Remove
18.
Remove the 12
heads
account
Fig. 2·37
to
the
spark plugs.
nuts
the
cylinders. Remove
for
two
gaskets.
securing
the
the
heads and
cylinder
When
removing a cylinder,
the
piston
20.
Using a
MAG-side
PTO-side
NOTE:
II
side
components
nents
sides_
21. Remove
Fig. 2·39
separated.
the
PTO-side
piston
·pin
•
CAUTION
so
it
will
felt·tipped
cylinder
cylinder
For
proper
Assemble
the
PTO-side
piston;
circlip
make
not
be
damaged.
marker,
and
piston
and
piston.
assembly,
and
piston
remove
from
the
•
sure
mark
all
PTO·side
them
on
-pin
MAG-side
to
support
an M on
and a P on
keep
all
MAG·
compo·
their
proper
circlip
the
MAG-side
piston.
the
the
from
22. Using the
0144-003), remove
pistons.
Arctic
the
Piston
piston
-Pin
pins
Puller
from
037
(pIn
both
17

Fig. 2·40
25.
Using a rubber
separate
the
dowel
the
pins.
or
crankca
plastic-tipped
se halves.
Account
hammer,
for
23.
Lift
the
and remove
bearings;
each
pin, and
_ NOTE:
-
ing
rods and
will
keep
the
crankcase.
Fig. 2·41
pistons
then remove
piston
with
bearing
Place
connecting
clear
the
small
its
together
rubber
around
of
the
connecting
end
connecting-rod
the
piston
rings; keep each
as
bands
the
cylinder
rods
from
a set.
over
the
damaging
rings. Keep
studs.
038
rods
piston,
connect-
This
the
DO
NOT
the
crankcase.
will
result.
24.
Remove
ting
rods,
crankcase
seals
off
Be sure
dropping
lower
crankcase
Inspecting
_ NOTE:
-
cracked,
replacement
•
CAUTION
drive
any
tool
between
Oamage
the
rubber
lift
half, and
the
crankshaft.
to
prevent
onto
Cleaning
Whenever a part
defective,
is
necessary.
bands
the
crankshaft
the
the
half.
to
slide
sealing
or
•
halves
to
the
sealing
holding
free
the
two
Account
connectinq
surface
and
Engine
is
worn
damaged
separate
surfaces
the
connec-
from
the
crankshaft
for
a C-ring.
rods
from
of
the
excessively,
in
any
way,
24.
Remove
washers
the
Fig. 2·42
the
securing
position
of
14
bolts,
the
crankcase
the
different-sized
lock
washers, and
halves.
bolts.
CYLINDER
1.
Using
remove any
tion
scrape,
or
2.
Inspect
039 threads. Repair
"heli-coil"
Note
3.
In turn,
plate
paper.
head in a
sealing
spots. A high
metallic
assembly
head in a
bright
HEADS
a non·
chambers
or
the
sealing
the
place
covered
Using
metallic
carbon
damage
spark·plug
insert.
figure
surface
finish.
by
figure
metallic
buildup
being
the
surface.
damaged
each
cylinder
with
#400
light
pressure,
eight
for
any
spot
can
Correct
continuing
eight
finish
is
carbon
careful
combustion
holes
grit
motion.
be
any
to
motion
attained
removal tool,
from
for
any
threads
head on a
wet-or-dry
move
indication
noted
high
move
until a uniform
the
combus·
not
chambers
damaged
the
Inspect
by a
spots
the
.
to
nick,
using
surface
sand
cylinder
the
of
high
bright
before
cylinder
a
-
"
18
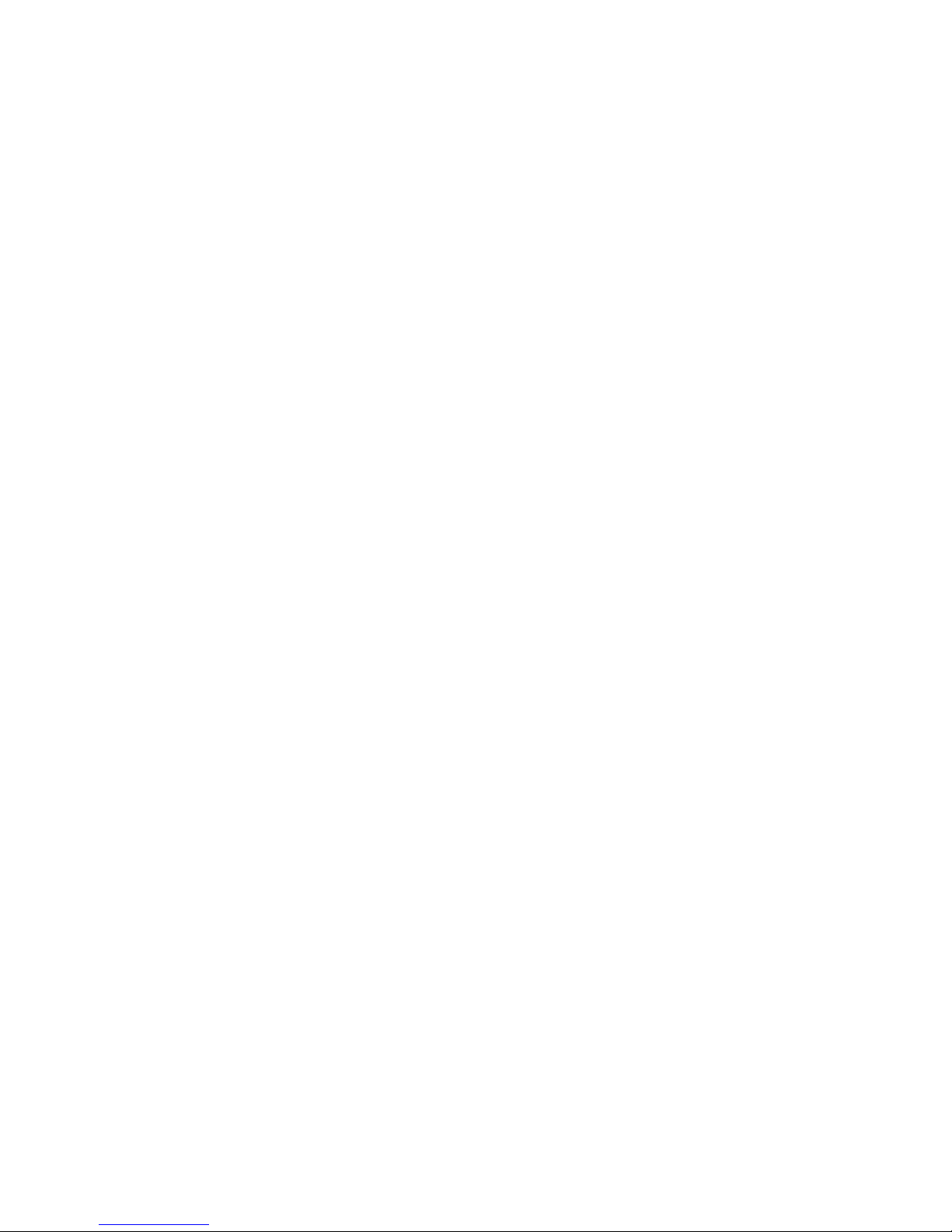
Fig. 2·43
soap
and
then
immediately
a bore
cylinder
4.
Place
surface
sandpaper.
cylinder
surface
high
finish.
ly by
figure
metallic
hot
water
is
severely
will
have
the
head
plate
Using
in a
for
spot
can be
Correct
continuing
eight
finish
and
apply
to
be
surface
covered
figure
any
indication
any
motion
is
attained.
dry
with
oil
to
the
cylinder
damaged
replaced.
with
light
eight
noted
high
to
move
until a uniform
or
of
each
#400
pressure, move
motion.
of
by a
spots
the
compressed
bores.
gouged,
cylinder
grit
wet-or-dry
Inspect
high
bright
before assemb-
cylinder
the
on a
each
the
spots.
metallic
in a
bright
air;
If
A
Water
or
junction
damage
CYLINDERS
1.
Using a
remove
ports.
2.
Wash the
3.
Inspect
scuffing,
repair
#500
Fig. 2-44
the
grit
•
cleaning
with
to
the
non-metallic
carbon
the
and
stones
solvent
the
sealing
cylinders
cylinders
corrosion.
surface
and
CAUTION
•
must
be
wet-or-dry
surface
buildup
in
with a surface
may
carbon
from
cleaning
for
If
honing
marks
used
in
con-
sandpaper
result.
removal tool,
the
exhaust
solvent.
pitting,
oil.
scoring,
are found,
hone
or
with
•
Water
or
cleaning
junction
damage
PISTON ASSEMBLY
1.
Using a non-
remove
piston
2.
Inspect
pin and
Inspect
3.
fing. Repair
paper and
Fig. 2·
45
with
to
the
carbon
.
each
skirt
each
the
sealing
metallic
piston
areas.
piston
with
water
CAUTION
solvent
wet-or-dry
surface
buildup
for
for
#400
or
honing
•
must
be
may
carbon
from
cracks
seizure
grit
oil.
used
in
sandpaper
result.
removal
the
dome
in
the
marks
wet-or-
dry
con-
or
of
piston
or
EJ
tool,
each
scuf-
sand-
- _ NOTE:
•
hatch"
...
t
the
rate
not
available, use a
oil.
Thoroughly
To
pattern,
of
30
produce
use a low
strokes
lightweight
clean
cylinders
the
per
proper
rpm
drill
minute.
If
petroleum-based
after
60°
(600
honing
honing
"cross-
rpm)
oil
using
is
II
NOTE:
deep
necessary
4.
Inspect
of
excessive
indicates
cylinder
If
to
correct
to
replace
the
worn
.
scuffing
with
the
perimeter
"blowby".
piston
or
seizure
the
sandpaper,
piston.
of
each
Excessive
rings
piston
or
an
marks
A840
are
too
it
may
be
for
signs
"blowby"
out-of-round
19
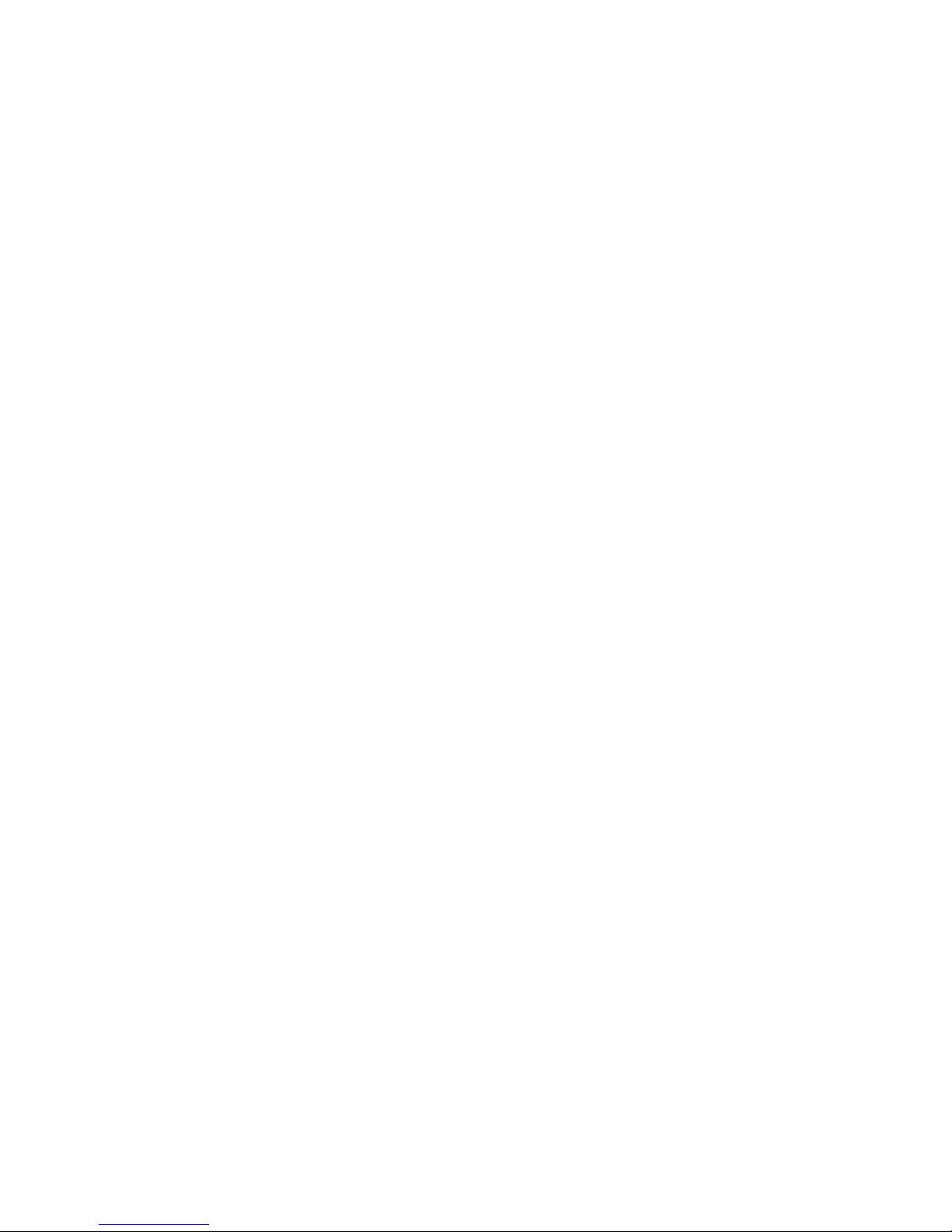
5.
Using a piece
clean
each
letter stamped
the
ring
CRANKCASE
1.
Wash
vent.
_
- halves,
have been removed and
2.
Inspect
scuffing, or
3.
Inspect
stripped
the
NOTE:
crankcase
of
piston-ring
on
faces
upward
crankcase
Before
make
sure
any
all
threaded
threads.
an
the top (inclined surface)
washing
imperfections
old
"keystone-type"
groove.
.
halves
all
six
bearing
accounted
halves
for
areas
Make
in
cleaning sol-
the
crankcase
dowel
for
_
scoring,
in
the
for
damaged
ring,
sure
the
of
pins
pitting,
casting.
or
Water
or
cleaning
Junction
damage
CRANKSHAFT
1.
Wa
solvent.
2.
Inspect
ing,
bearings.
must
condition
Fig. 2-47
to
sh
the
the
damage,
not
with
CAUTION
•
solvent
the
wet-or-dry
the
sealing
crankshaft
bearings
Bearings
bind
is
noted, replace
surface
or
discoloration.
or
feel rough. If
•
must
be
sandpaper
may. result.
w/bearings
for
wear,
must
rotate
the
used
in
in
scoring,
Rotate
freely
any
abnormal
bearing
con-
or
cleaning
scuff-
the
and
.
4.
Inspect
cessive
cessive
peening
tooth)
5.
Inspect
6. Inspect the
halves
crankcase
with
light
eight
any
be
spots
figure
metallic
Fig. 2·46
the
bearing
bearing
the
pattern
the
for
#400
pressure, move
motion
indication
noted
by a
by
eight
finish
bearing
movement.
movement
bearing
using a center
bearing
sealing
trueness
half
on a
grit
wet-or-
. I
nspect
of
high
metallic
continuing
motion
is
atta
areas
dowel
surfaces
ined .
for
If
evidence
is
noted, repair by
area in a
punch.
pins
of
the
by
plac
surface
dry
each
the
spots
finish.
to
until a uniform
plate
sandpaper.
half
sealing
. A
high
Correct
move the
cracks
pinking
for
wear.
crankcase
i ng
covered
in a
surface
spot
any
half
or
ex-
of
ex-
(saw
each
Using
figure
for
can
high
in a
bright
_ NOTE:
- a
install a bearing,
using a propane
bearing
the
bearing)
ing
sure
properly
the
crankcase_
Fig. 2·48
To
Bearing
(until
slight
and
the
dowel-pin
positioned
replace
Puller
squirt
torch,
smoke
slide
and
crankshaft
to
remove
oil
into
heat
the
is
it
onto
the
hole
in
will
align
bearings,
the
the
bearing;
inner
noted
crankshaft
the
with
bearings_
race
of
coming
outer
race
its
hole
A521
use
To
then
the
from
mak
is
in
(
-
•
20
A656
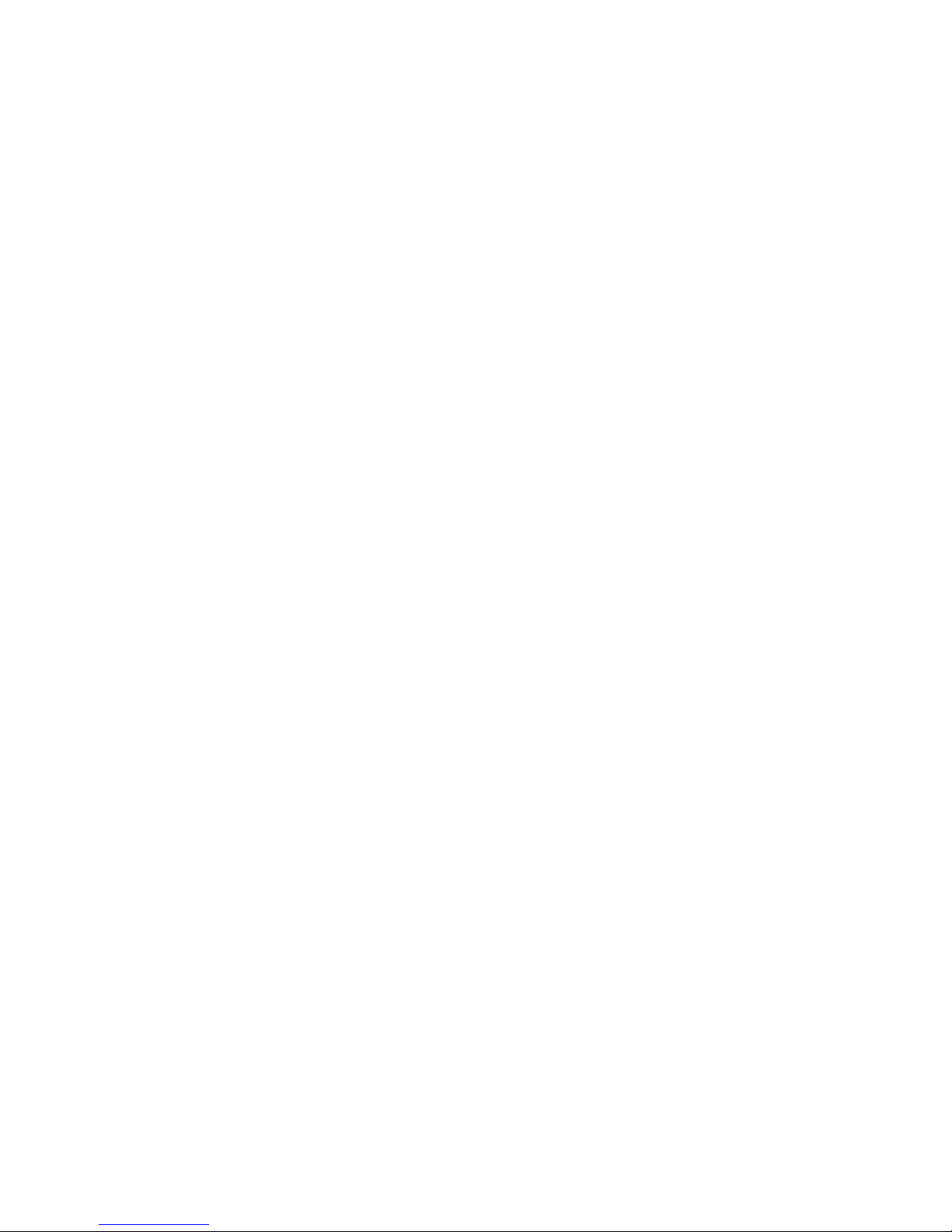
Fig. 2·49
Fig. 2·50
A659
•
CAUTION
DO
NOT
overheat
3.
Inspect
rotating
and
ing-rod
connecting
replaced.
NOTE: Lubricate bearings thoroughly prior
11
to assembly.
Measuring
must
the
connecting-rod
them.
bearing
Bearings
not
bind
-rod and
or
must
crank
•
the
bearing.
bearings
must
feel rough. If a connect-
be replaced,
Critical
pin
rotate
must
Components
CYLINDER TRUENESS
1.
Me asure eac h
shown
a
roundness)
highest
trueness
specifications
total
from
of
cylinder
front
six
readings
is
the
and
low
(out-of-roundness)
listed.
in
to
back
. The
difference
est
the
and
reading.
three
side
trueness
between
must
by
fre
ely
the
also
be
locati
ons
to
side
for
(out-of-
the
Maximum
not exceed
CYLINDER TRUENESS LIMIT
mm
0.1
PISTON SKIRT/CYLINDER CLEARANCE
1.
Measure
cm
2.
Measure
at a pOint 1 cm (0.394 in.) above
skirt
Subtract
urement
must
Fig. 2·52
each
(1
in.) from
the
at a right
this
in
be
within
cyl
inder
the
bottom
corresponding
angle
measurement
step
1. The
specifications.
front
to
the
difference
in.
0.0039
to
back
of
each
piston
piston-pin
from
the
(clearance)
about
cylinder.
diameter
piston
bore.
the
meas-
2.5
Fig. 2·51
0726·307
A671
PISTON SKIRT/CYLINDER CLEARANCE RANGE
Jag 340
Jag 440
Panther
Super Jag
mm
0.058-0.15
0.084-0.15
0.084-0.15
0.084-0.15
in.
0.0023-0.0060
0.0033-0.0060
0.0033-0.0060
0.0033-0.0060
21
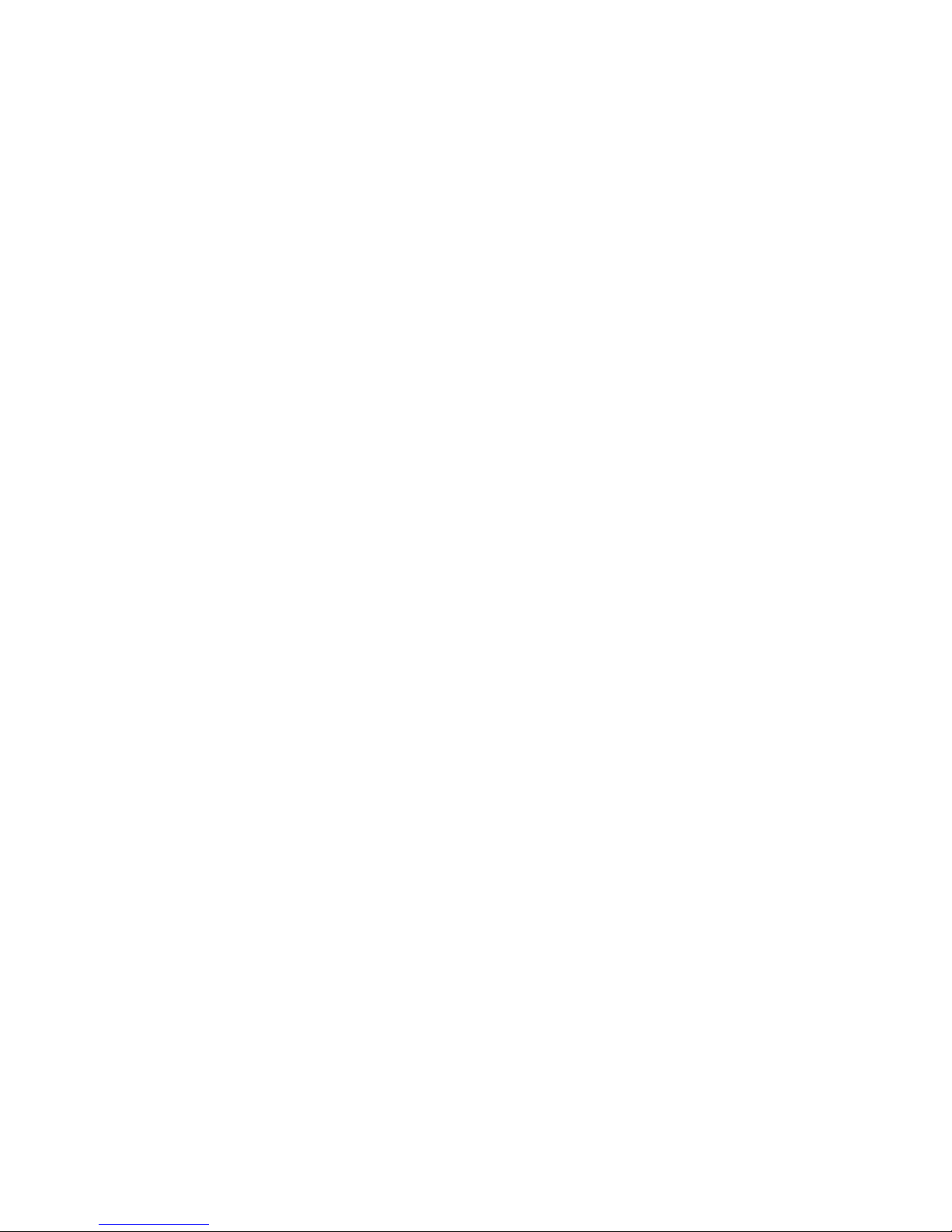
PISTON-RING END GAP
1.
Place
each
piston
above the exhaust port
cylinder
square
. Use
the
ly in
each cylinder.
piston
ring
in
the
of
to
position
wear
its
respective
portion
each
ring
2.
Insert a snap
then
remove
micrometer. Diam
cations.
accuracy
Take
.
gauge
the
gauge
two
into
each
and
measure
eter
must
be
measurements
piston
within
-pin bore;
it
with
specifi·
to
ensure
a
2.
Using a feeler
ring end gap.
fall
within
Fig. 2-53
PISTON·RING END GAP RANGE
gauge,
Acceptable
specificat
ions.
mm
Jag
340
Jag 440 & Super Jag 0.20-0.83
Panther
PISTON PIN
1.
Measure
places.
than
bearing
0.02
AND
the
If any
mm
must
0.15-0.80
0.20-0.83
PISTON-PIN BORE
piston
pin
measurement
(0.001 in.),
be
replaced
measure
ring end
diameter
varies by
the
piston
as a set.
each
piston
gap
must
in
.
0.006-0.031
0.008-0.033
0.008-0.033
in several
more
pin and
Fig. 2-55
-
Jag
340,
Super
Panther
CONNECTlNG·ROD
Insert a snap
1.
small
measure
be
within
Fig. 2·56
PISTON·PIN BORE DIAMETER RANGE
mm
Jag
440, &
Jag
end bore; then remove the
it
with
specifications.
15.996-16.004
17.998-18.006
SMALL
gauge
c..
micrometer.
into
END
each
connecting-rod
Diameter
0.6298-0.6301
0.7086-0.7089
gauge
A676
in.
and
must
Fig. 2-54
PISTON PIN DIAMETER RANGE
mm
Jag
340,
Jag
440, &
Super
Jag
Panther
15.994-16.000
17.995-18.000
0.6297
0.7085-0.7087
22
A674
in.
-0.6299
CONNECTING·ROD
Jag
340,
Jag
440, &
Super
Jag
Panther
SMALL
21
23.00·23.01
END DIAMETER RANGE
mm
I
.00-21.01
in.
0.8268·0.8273
0.9056-0.9059
r
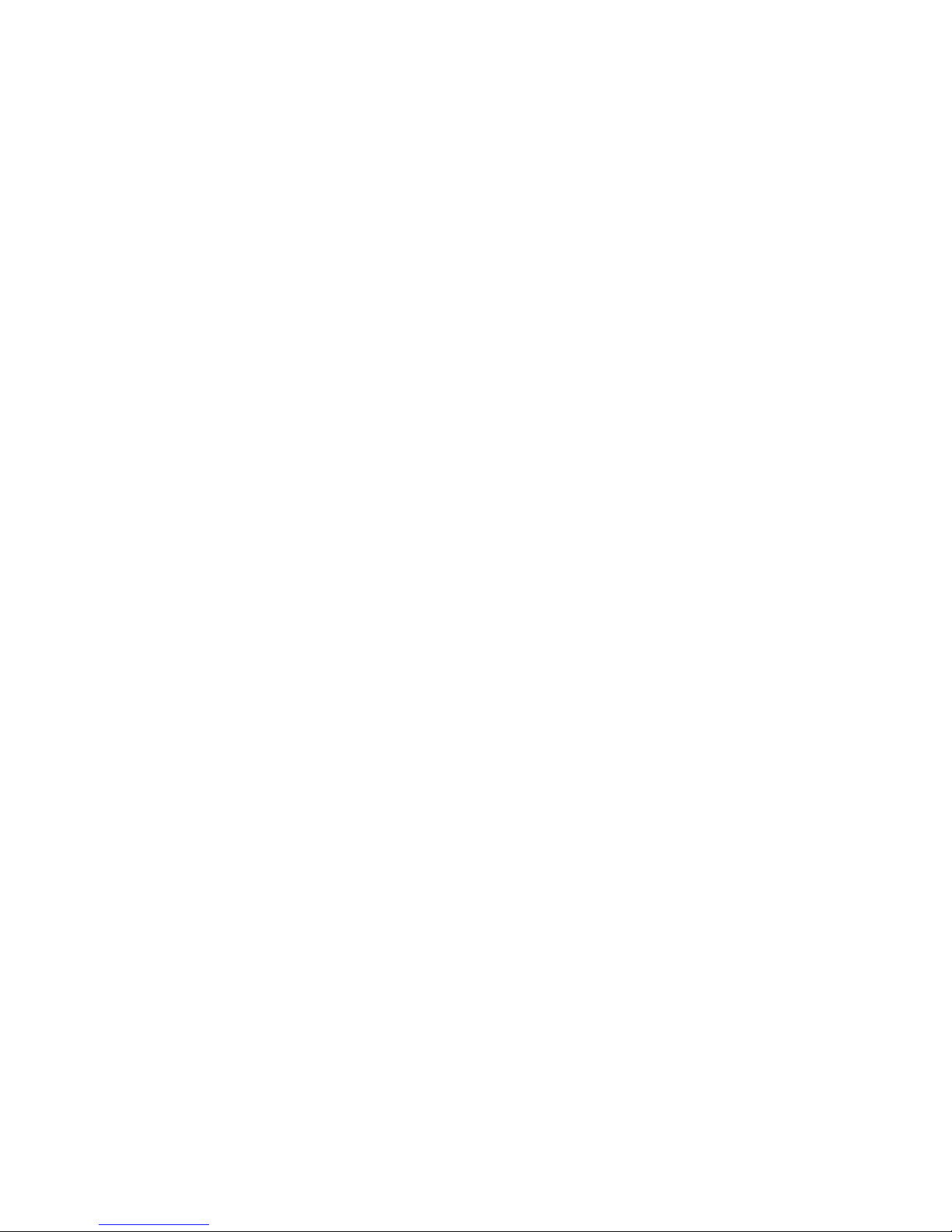
CRANKSHAFT RUNOUT
1. Using a set
s
haft
on a s
_ NOTE:
-
crankshaft
Mount a dial
2.
face plate.
point
against
•
end) from the
indicator
the
ly.
Note
(total
indicator
Jag
340,
Jag
of V-block
urface
The
on
Position
the
V·block
the
indicator
the
crankshaft
and
amount
s, s
plate.
s s
hould support the
outer
bearings.
and base on
the
crankshaft
counterweight.
rotate
the
of
reading).
440, & Super
A
B
Panther
A
B 41.3
Jag
upport the
indicator
distance
crankshaft
crankshaft
mm
37.6 1.50
25.4 1.00
mm
41
.3 1.62
crank
the
sur-
contact
A (PTO
Zero
slow-
runout
in.
in
.
1.62
-
ASSEMBLING
(Jag
_ NOTE: When use
-
Three
1.
2.
Fig. 2·58
340,
dicated,
Bond
Install
the
lower
Lubricate
seals
the
crankshaft
Jag
use
Sealant.
the Coring and
crankcase
the
inner
with
grease; then
each seal faces
either
making
the
ENGINE
440,
&
Super
of a silicone
RTV
Silicone
the
six
half.
lips
of
the
slide
sure
center
of
sealer
dowel
crankshaft
the seals
the
spring
the
Jag)
is in·
Sealant
pins
crankshaft.
into
onto
side
or
oil
of
3.
Position
the
crankshaft
and rotate
amount
reading).
Fig. 2·57
•
4. If runout exceeds
crankshaft
the
replaced .
the
crankshaft
counterweight.
the
of
crankshaft
indicator
distance
crankshaft
specifications
must
be
contact
point
against
B (MAG-end) from the
Zero
the
indicator
slowly.
runout (total
either
straightened
at
either
Note
indicator
A664
end,
the
or
3.
Apply
stall
oil
the
half. Be sure
ing
is
positioned
in the crankcase;
Fig. 2·59
to
the
crankshaft
crankshaft
the
alignment
over
then
into
the
its
respective
seat the
A685
bearings; then in-
lower
crankcase
hole in each bear-
dowel
pin
crankshaft.
CRANKSHAFT RUNOUT
(Total
Indicator
M
axim
um
Reading)
mm
0.05
in
.
0.002
23
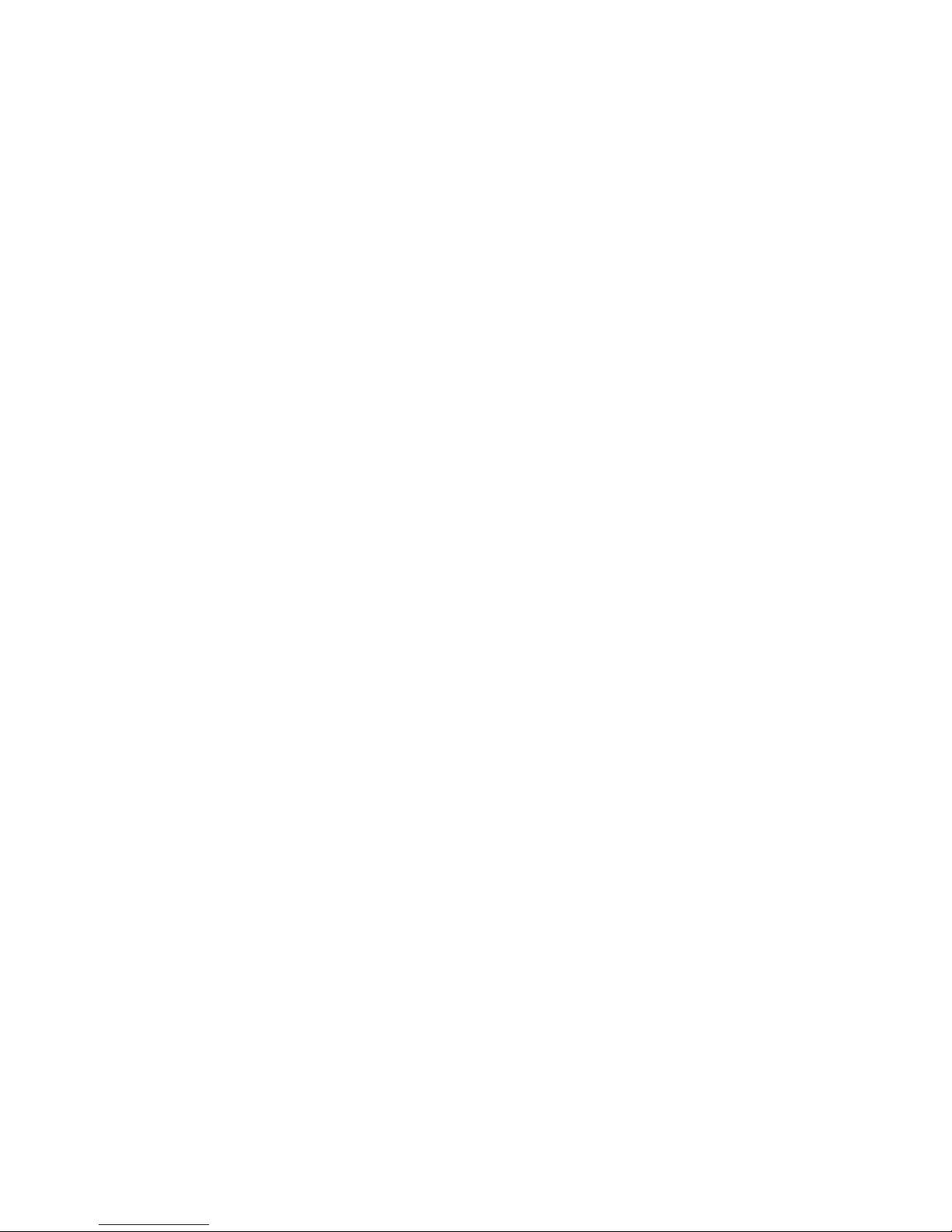
Fig. 2-62
•
If
the
bearings
assembly,
together
4.
Apply a thin
crankcase sealing surfaces; then lay a length
of
#50
and along the
case half.
Fig. 2·60
the
tightly
cotton
CAUTION
are
not
properly
crankcase
and
coat
thread next
full
halves
engine
damage
of
silicone sealer to
leng th
to
of
•
seated
will
will
the
inner edge
the
lower crank-
during
not
result.
o 0
bolt
0725·549
the
of
Incorrect
in
engine
8.
Apply
bearings; then
9.
Place each
the
arrow on
the
exhaust
pin.
CAUTION
•
installation
damage.
oil
to
of
the
install
piston
the
port; then secure
the
•
piston
rings
connecting-rod
the
small-end bearings.
over
the
connecting
piston
dome
E454
will
result
small
points
with a piston
end
rod
so
toward
It
5.
Assemble
the
dowel
apply LOCTITE LOCK N' SEAL
case
6.
Install
and washers
bolts
steps
Ib)
and the 6 mm
using
Fig. 2·61
the
pins
bolts
.
the
14
crankcase bolts,
are in
the
the
8 mm
the
pattern shown.
crankcase
are properly positioned; then
making
proper holes.
bolts
to
bolts
'~jA
---
14
I
~
8
NOTE: Secure
II
ber bands on
the
connecting
the
cylinder
halves making sure
to
the crank-
lock
washers,
sure
the
proper-sized
Tighten
1.8-2.2 kg-m (13-16 ft-
to
0.8-1.2 kg-m (6-9 ft-
in three
v
. \
! I
rods
with
studs_
Ib)
0726·412
rub-
NOTE:
II
installing.
10. Install the
either
Fig. 2·63
Make
end
ing
down
sure
is
directed
with
Apply
assembly.
circlips
or up.
•
circlips
either
oil
to
so
the open end
CAUTION
are
firmly
down
the
seated
or
up
piston
•
and
before
pin
is
directed
the
open
continu-
before
...
..
8324
7.
Install
letter on
ring faces the
the
the top
piston
dome
rings on
(inclined
of
the
each
surface)
piston.
24
piston
of
so
each
the
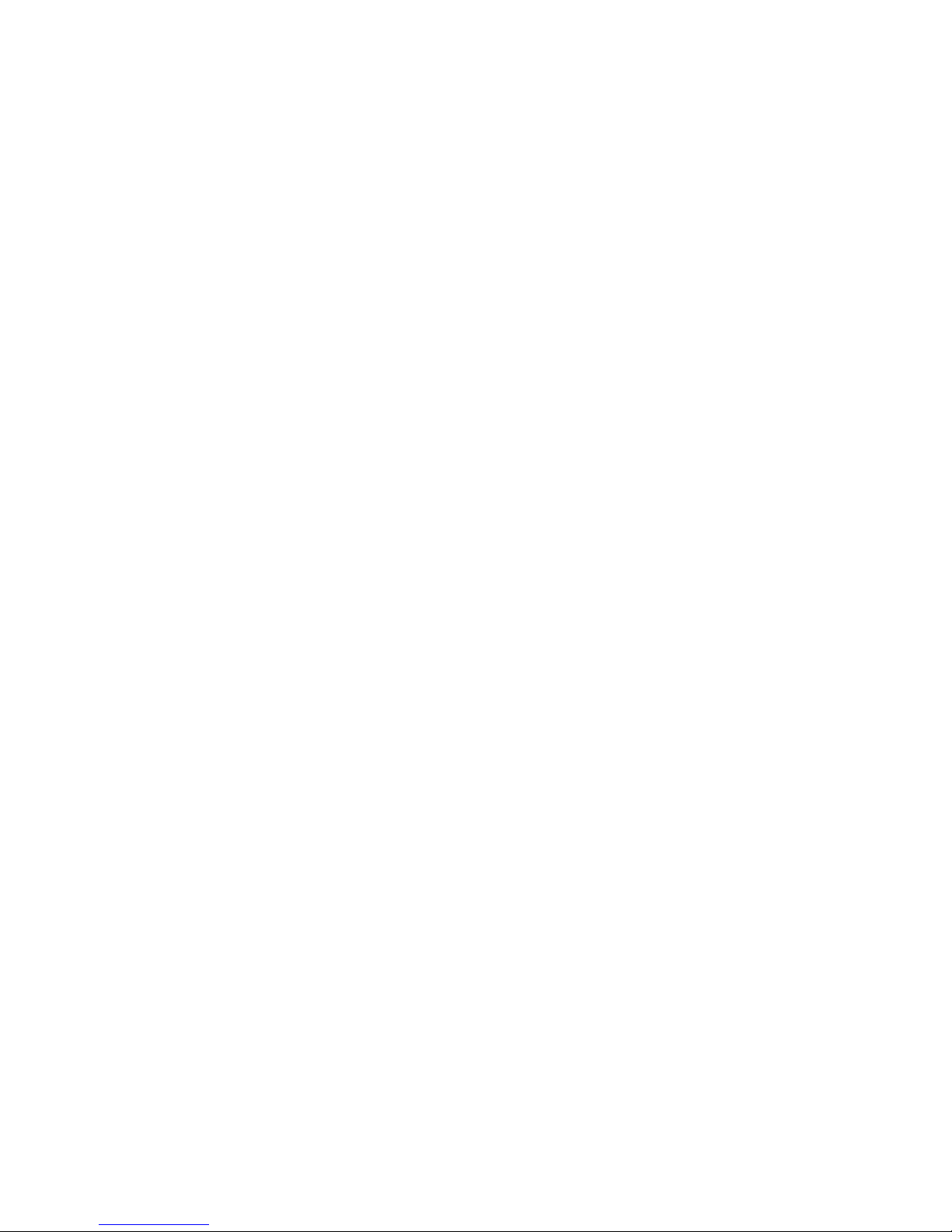
11.
Apply a thin
sides
stall
gaskets
each
passages.
12. Rotate
properly
keeper;
assemblies
rubber
_ NOTE:
-
surfaces
bores.
coat
of
of
each
cylinder
onto
the
gasket
each
bands
aligns
piston
positioned
then
and
Apply a generous
of
from
the
ring
on
apply
cylinder
the
pistons,
silicone
-base gasket;
crankcase
with
until
either
oil
connecting
sealer
crankcase
the
side
to
bores. Remove
amount
rings, and
to
both
then
in-
making
ring ends are
the
of
transfer
of
the
piston
rods.
oil
cylinder
sure
to
ring
the
the
NOTE:
_
-
crankcase,
installed
tightened.
the
cylinders,
upper
15.
16.
crankcase
Install
kg-m (18-
Apply a thin
sides
order,
gasket, and
two
Tighten
To
and
torqued
When
the
22 ft-Ib).
of
the
install
bolts,
and then
properly
the
intake
the
intake
the
cylinders,
will
be
spark
plugs
coat
oil-injection
the
gear,
oil-injection
lock
torque
align
the
cylinders
manifold
before
the
manifold
intake
properly
and
of
silicone
shim,
pump.
washers, and washers.
to
must
cylinder
is
manifold,
aligned.
tighten
sealer
pump
gasket, retainer,
Secure
0.7 kg-m
on
first
nuts
secured
to
2.5·3.0
to
gaskets
(5 ft-Ib).
the
be
are
to
and
both
. In
with
Fig. 2·64
1
3.
In
turn
(or
suitab
skirt
and square
crankcase; then
the
fingers,
cylinder
holder
crankcase
Fig. 2·65
on each
le
substitute)
compre
over
the
and
seat
.
piston,
the
piston
using
ss
piston
the
cylinder
place a piston
beneath
a ring
the
rings and s
. Remove
the
in
respect
compressor
firmly
lide the
the
onto
0726·306
holder
piston
to
the
or
piston
the
Fig. 2·66
Be
of
pump
aligned.
sure
the
the
oil-injection
will
•
gear
be
damaged
CAUTION
is
properly
pump
if
aligned
shaft.
these
•
two
with
The
parts
the
slot
injection
are
not
B
14. Place each head
install
THIS TIME.
the
eight
w/gaskets
nuts. DO
into position
NOT TIGHTEN AT
and
17.
18.
If
removed,
unit
to
the
Align
th en
head
N' SEAL),
the
secure
cap
secure
fan case.
marks
the
screws
lock
the
ignition
made
sta
(coated
washers, and washers.
tor
during
plate
with
coil
and COl
disa
ssemb
with
two
socket·
LOCTITE LOCK
ly;
25
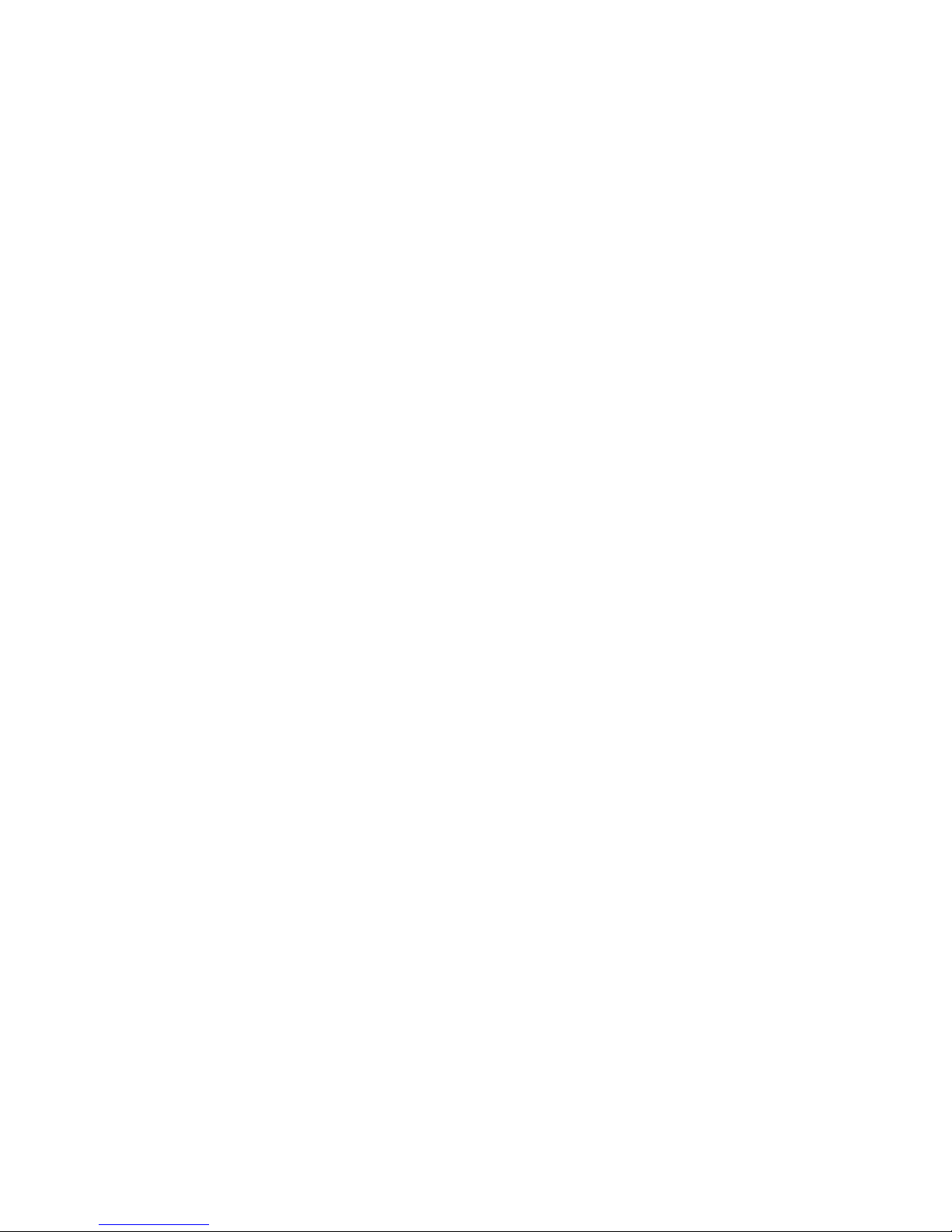
Fig. 2·67
23. Secure
Tighten
ft
-I
b).
Fig. 2·
69
the
nuts
intake
in three
manifold
steps
to 0.8-1
with
six
.2 kg-m (6-9
nuts.
19.
Install
flywheel
keyways
20. Place
with
m
(11
I G
NITI
ON
the
key in
onto
match
the
fan
four
nuts.
-14 ft-Ib).
TIMIN
G CH
the
the
crankshaft
.
case
Tighten
ECKED
AT
boaa
crankshaft
into
position
the
IGNITION TIM
BiOC 18"/60
R.!'.M.
making
nuts
ING
00
R . P
.M.
BT
OC 22'
BT
De
20'
BT
OC
18 '
BT
De
16 '
0726·863
and slide
sure
and secure
to 1.5·1.9
the
the
kg-
24. Tighten
c
risscross
25.
Attach
manifold
Fig. 2·70
the
the
. T
head
pattern
oil
injection
ighten
nuts
in three
to
1.8-2.2 kg·m
hoses
screw
clamps.
steps
(13-16
to
the
using
ft-Ib).
intake
•
a
Fig. 2·68
21.
Secure
bolt
22.
Apply a thin
sides
then
port),
the
the
and
lock
of
in order,
shroud,
intake
COl
unit
washer.
coat
of
the
four
install a gasket
gasket
manifold.
to
the
crankcase
silicone
sealer
intake-manifold
(one on each
(one on
each
with
the
to
both
gaskets;
port), and
26. Test
ing procedure:
a.
Install
tighten
the
engine
for
an
intake-manifold
the
flange
air
clamp
leaks
using
the
port
plug
securely.
follow
and
..
26
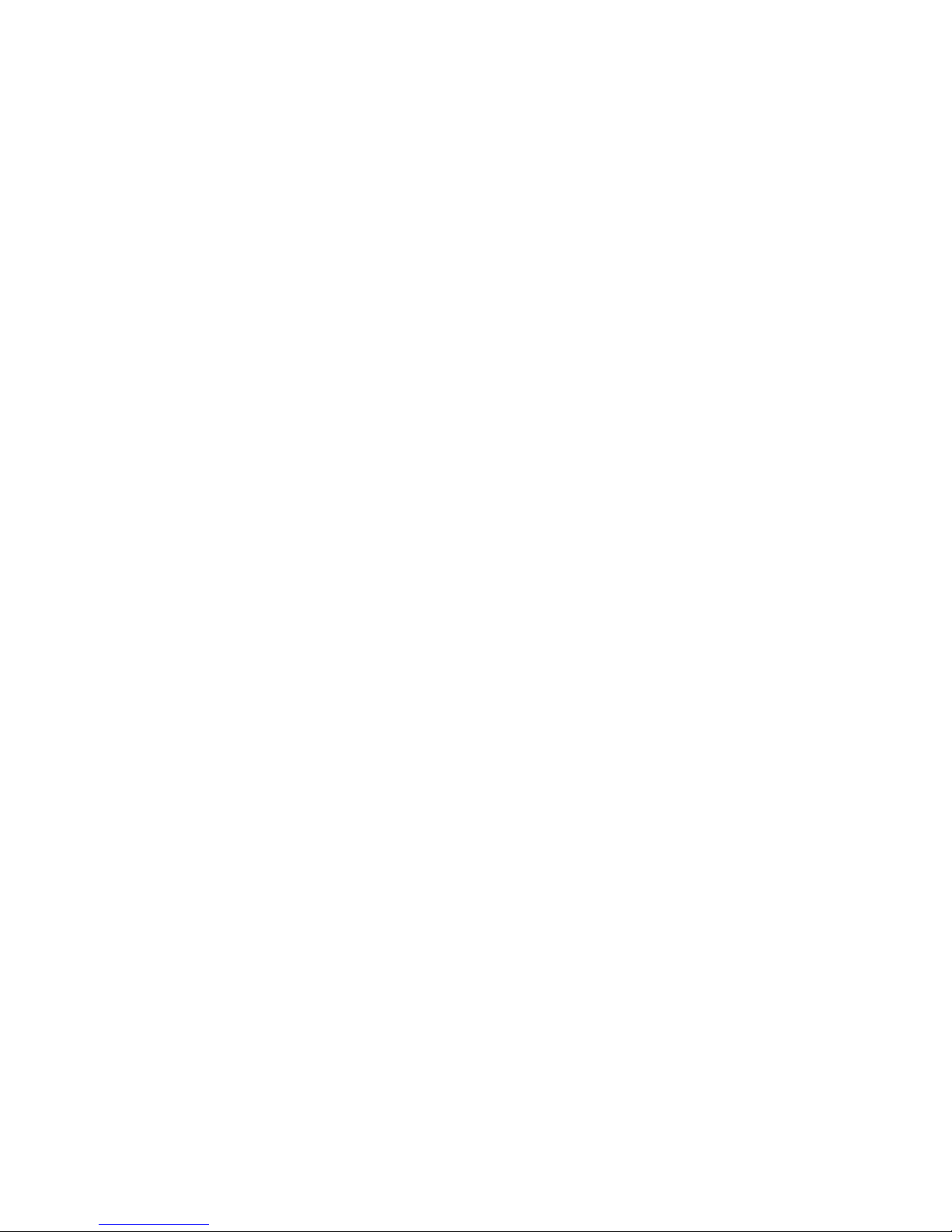
Fig. 2·
71
b. Place a rubber
haust port and
Fi
g. 2·72
plug
and cover on eac h ex·
secure.
A873
•
DO
NOT
exceed
the
seals
will
d.
Monitor
must
not
per
minut
e.
If the pressure drops fas ter than specifi
spec
in
co
engine in
needed.
t for an air leak
mpl
ete
CAUTION
15
psi
of
pressure
resuR.
the
, pr
essure gauge. Pre
drop
at
a rate
e.
with
ly subm
clean fres h wate
erge the press
CAUTION
•
or
damage
of
more
soapy water
r.
•
•
When
the
CDI
submerging
unit
should
the
engine
be
removed
to
test
to
avoid
for
air
damage.
to
than
Repa
leaks,
ssure
1 psi
ed,
or
urized
ir
as
EJ
NOTE: A pressure
II
drilling
fitting
and a
sure tester, the
and the pres sure
the spark
position
A875
c. Conn ect a tester
ting
on the crankcase; then press uri
cr
ankcase to 12 psi and close the valv
Fig. 2·73
1
pump
to th e impulse
ze
fit
the
e.
A876
·
27. Te
to
valve stem. When
Fig. 2·74
mpor
flywhe
washe
LOCK
befor
wrench
flywh
out
an
it;
then
install
impulse
tester
plug
hol
es
.
arily sec ure the
el
with
three
r,
lock
washer,
N' SE
e insta
eel
AL
lling
to secure the cranksh
nut
to 9.0-11
tester
old
spark
a tee
(with
using
fitting
must
be
with that pis
start
bolt
s.
Install
and nut.
to
the
crankshaft
the
nut. Using a
.0 kg-m
can be
plug
a gauge), valve,
this
must
installed
ton
er
Apply
(65-79 ft-Ib).
made
and brazing a
type
be
in
pulley
the
LOCTITE
aft,
torque
by
of
pres·
plugged
in
one
of
the BOC
0725·108
on the
flywheel
threads
spann
er
the
27