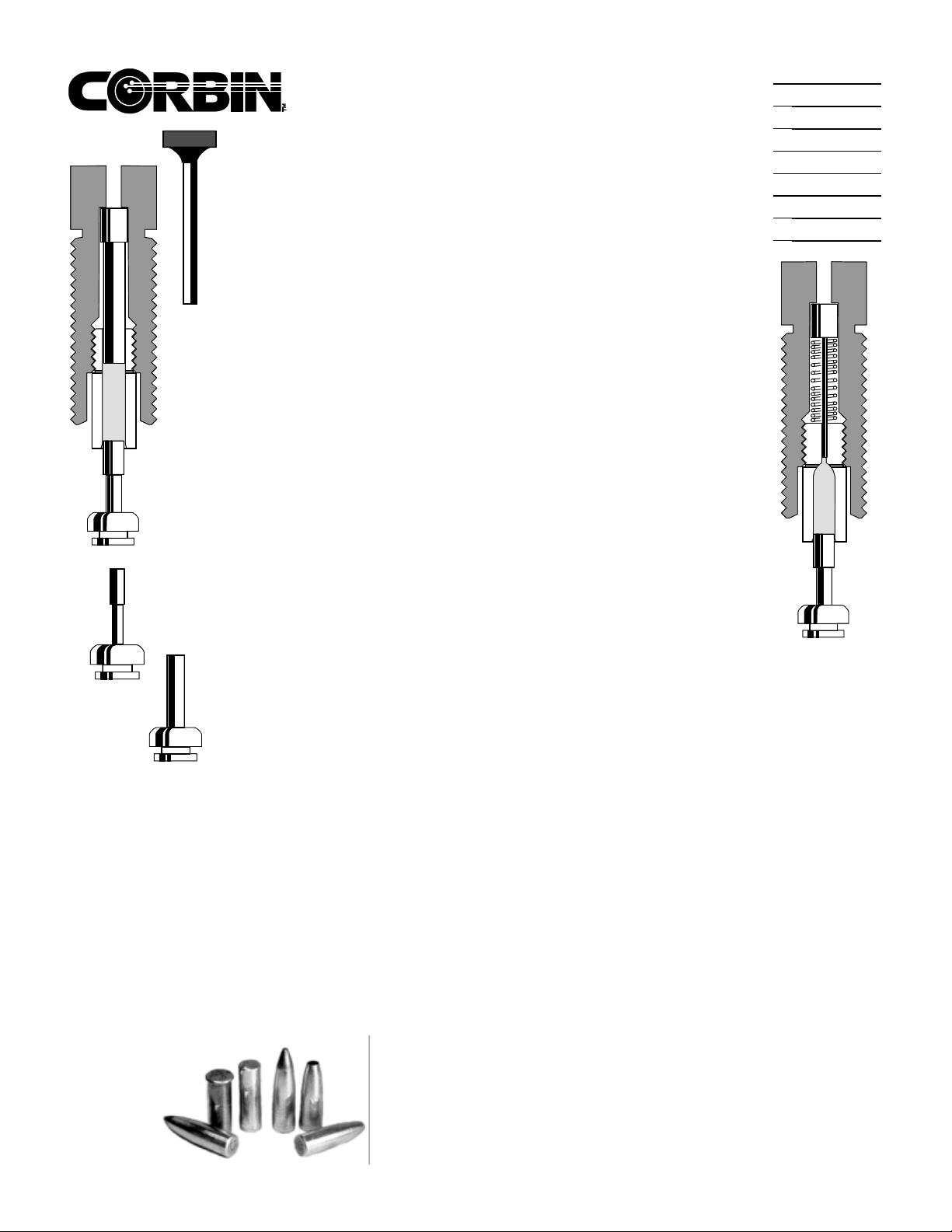
2-Die Set for Reloading Press
The first die is the CORE
SEATER. It is used to expand
the jacket to proper diameter
while pressing (seating) the
lead filling (core) into the
jacket.
The INTERNAL punch stays
inside the die body and is used
to push the bullet out. A knockout rod slips into the top of the die.
Tapping the head of this rod pushes
the bullet out.
The EXTERNAL punch can be different diameters and shapes on the tip,
depending on what it must do. For jacketed rifle bullets with open tips, the
punch fits inside the jacket you plan to
use and presses the lead firmly enough
to expand the jacket.
The diameter of the external punch has
to fit the point where the jacket and lead
will be seated. If you use too big
a punch it will dig into the jacket
wall and you cannot press the
lead firmly, so the bullet will be
undersized and have a ring in it
where the punch hits it.
If you use too small a punch di-
ameter, lead can spurt out
around it and the pressure cannot rise enough, also
making an undersized bullet. The right size punch
presses the lead without letting it leak out, and without digging into the jacket.
The ideal fit will just go into the jacket firmly by hand.
A .22 LR case used for 224 or 6mm jacket often has
a roll crimped mouth that makes the ID appear smaller
than it really is. A punch of about .204-inch diameter will fit into most .22 cases after they are drawn
to size (a range of .202 to .205 would be OK). A
commercial benchrest jacket would probably use a
.196 to .201 inch diameter core seating punch.
o BSD-224R
o BSD-243R
o BSD-251R
To seat a core, first cut or cast the
lead core to a weight which, when
combined with the jacket, gives
you the total bullet weight. Clean
the cores by boiling in hot water
with a little detergent added, rinse
and dry them to remove all grease
and oil. Put the clean cores into
the jackets. Then put a little Corbin
Swage Lube on your fingertips
and pick up the jacket and core,
placing it over the core seating
punch (which snaps into the slotted ram of your reloading press -do not use a shell holder with it).
Screw the core seating die into the
top of the press a few turns, and
raise the ram with the jacket, core
and punch all the way to the top
without encountering any resistance. Lower the die until you cannot turn it by hand (internal punch
comes up against the jacket).
Then lower the ram slightly, and
give the die about 1/8 to 1/4 turn lower (closer to the
ram). Raise the ram and see if you feel any resistance. If so, eject the seated core and jacket. If the
diameter is about .0002 to .0005 inches smaller than
the final desired diameter, you did well. If the jacket
sticks on the punch, then probably the punch is either too loose, too tight, or the core is too short (light)
for that jacket. You can probably remove it by simply
pressing a little harder until it comes off in the die.
After making a quantity of seated cores, remove the
core seating die and punch, and screw in the point
forming die and its larger diameter punch. Do not
use a core seating punch, as the bases will be severely damaged by the undersized punch tip. Apply
a little more lube to the jacket, and push it into the
point forming die. Eject it and see if the tip is closed
enough. The tip should be about the size of the ejection pin (.081 inches is typical). For more information on rifle and handgun bullets, removing stuck
bullets, and making FMJ and lead tips, see the Corbin
Handbook of Swaging, No. 8.
o BSD-308R
o BSD-312R
o BSD-314R
o BSD-355R
o BSD-257R