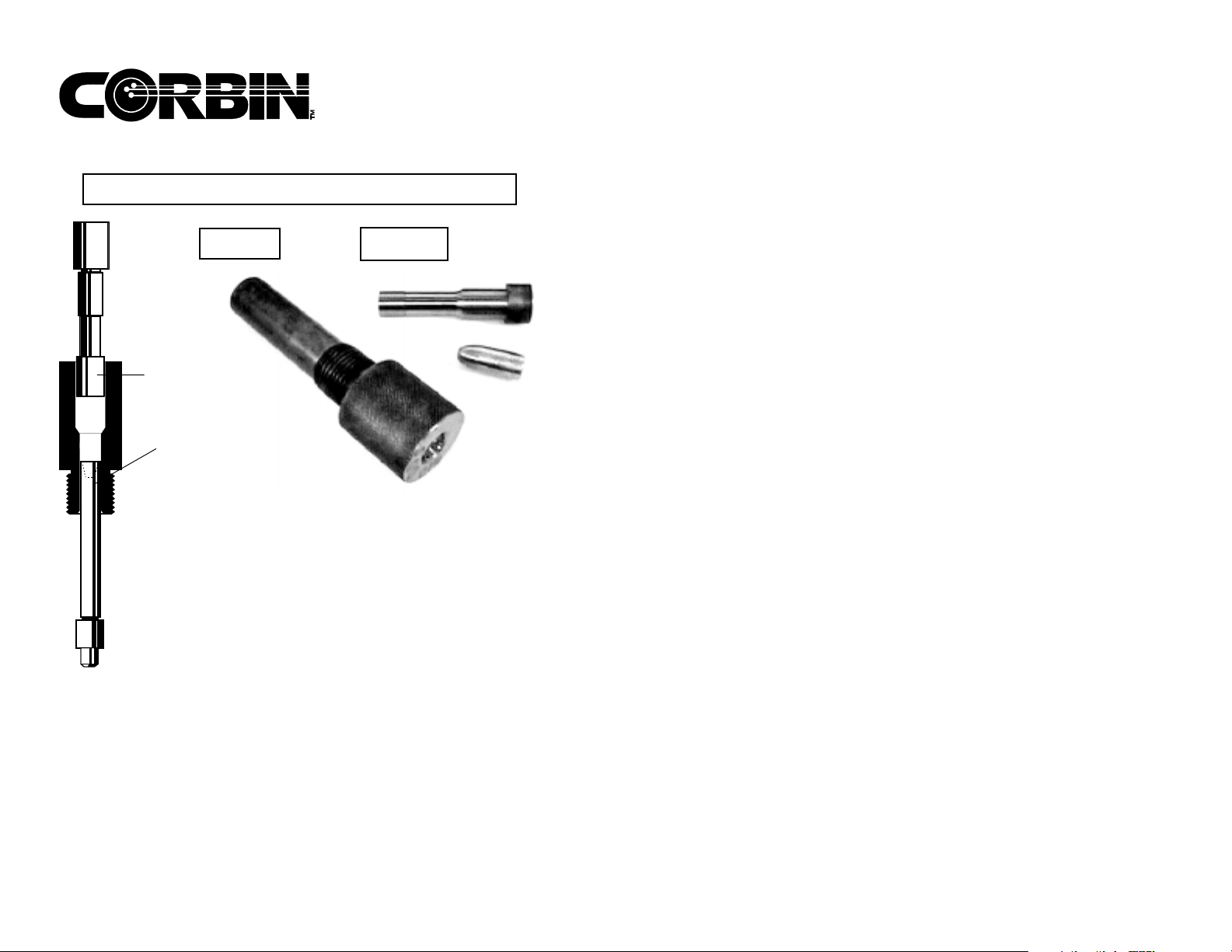
The DDS-1 die may be used for several purposes:
DDS-1
Dual Diameter Sizer Die
o DDS-1-M o DDS-1-S o DDS-1-H
Major Minor
Diameter: Diameter:
Type
-S
External punch
matches bullet base
shape *
Internal punch
matches bullet nose
shape *
* Base and nose punch shapes are reversed
for heel-base bullet-making.
The DDS-1 Dual Diameter Sizer reduces the forward por-
tion of a bullet so that it rides atop the rifling, while leav-
ing the base at full engagement diameter. It can also be
used, in a reversed nose/base punch design, for making
heel-type bullets.
The internal punch is machined to fit the nose of the
bullet. It can be changed to handle various shapes of bullets, in the
caliber of the die. The base or external punch is the same shape as
the bullet base (flat, cup, hollow, RBT, Base Guard, etc.) to main-
tain the shape during the sizing operation.
You can adjust the length of bullet shank to be reduced, simply by
setting the external punch to different positions relative to the end-
of-stroke position of the die. This lets you experiment to find the
perfect amount of rifling engagement for best accuracy and mini-
mum bore friction.
Type -H
Create bullets that will chamber easily in tight-throated barrels, by creating a
kind of free-bore on the bullet itself. This is often used for dangerous game
bullets, where sticking a bullet against the rifling could prevent the action from
closing at a critical moment.
Make heel-type bullet by using the die backward, to reduce the base section
instead of the nose, replicating early handgun cartridges or modern rimfire
rounds. This requires punches designed in reverse order, so the nose is exter-
nal, and the base is internal. A hollow heel can also be made. The bullet is first
formed in a LSWC-1 die, then the dual diameter created.
Produce airgun pellets that have a very small engagment band at the base, for
efficient use of the air pressure with minimal bore friction, yet are aligned
perfectly by the bore-riding shank section. First create the straight, full-diam-
eter pellet in a LSWC-1 or combination of the CSW-1 and CS-1 dies. Then
reduce all but the very edge of the base (skirt) in the DDS-1.
Reduce the pressure and friction, and obtain higher velocities, with any jack-
eted or lead bullet, while maintaining superior accuracy.
The usual reduction is twice the depth or rifling. This typically results in .008
inch reductions from full diameter in modern cartridge arms. For instance, a
DDS-1 die for .308 caliber usually reduces the forward portion of the shank to
.300 inches. A bore-riding .224 bullet would have the front portion reduced to
.216 inches. If you do not specify otherwise, this is the reduction that will be
used.
The finished bullet must match the internal punch of the DDS-1 die to avoid
deforming the tip. The DDS-1 can be substituted for a LT-1 lead tip forming die
in many cases, since the pressure required to reduce the bullet forward portion
is normally enough to reform the lead tip as well.
Lubricate the bullet with Corbin Swage Lube by lightly rolling it between
thumb and forefinger as you pick it up, with a drop of lube on your fingertip.
Push the bullet into the DDS-1 die, adjusting the punch closer to the die and
testing to see where the reduction ends, until you have the desired amount of
rotating band left at the back of the bullet. With airgun pellets and low pres-
sure loadings, the band can be very tiny. With higher velocities, the band
should be increased in length to prevent skidding across the rifling during
acceleration. Anything from half the bullet shank length to a fraction of a
caliber length has been used with good success in different applications.