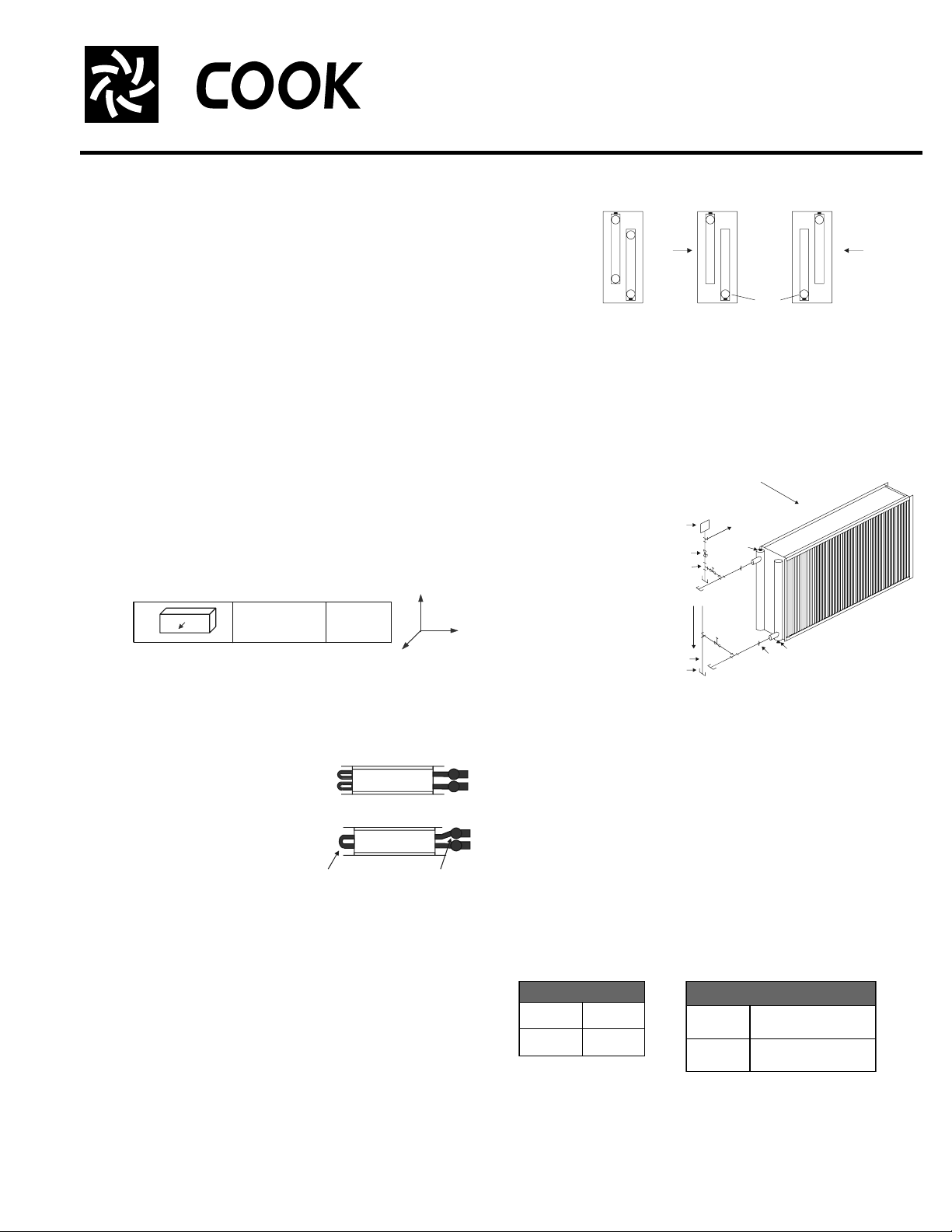
2.
3.
2.
3.
6.
4.
5.
3.
2
1
ERV Fluid Coil Supplement
ENERGY RECOVERY VENTILATOR
INSTALLATION, OPERATION, AND MAINTENANCE MANUAL
This publication contains supplemental installation, operation and maintenance instructions for an ERV-with optional
fluid coil.
Carefully read this publication and the installation, operation, and maintenance instruction for standard units of the
ERV- Energy Recovery Ventilators publication prior to any
installation or maintenance procedure.
Loren Cook catalog, ERV , provides additional information
describing the equipment, fan performance, available accessories,
and specification data.
For additional safety information, refer to AMCA Publication
410-96, Safety Practices for Users and Installers of Industrial and
Commercial Fans .
All of the publications listed above can be obtained from Loren
Cook Company by phoning (417)869-6474, extension 166; by FAX
at (417)832-9431; or by e-mail at info@lorencook.com.
For information on special equipment, contact Loren Cook Company Customer Service Department at (417)869-6474.
Mounting
1. All water and glycol coils are designed to be fully drainable
when properly mounted.
2. Vertical air-flow is not recommended for dehumidifying coils.
Horizontal Air Flow
Horizontal Tubes
Level with
the y-axis
and x-axis.
Y
X
Z
Coil Types
Standard Fluid Coils
Type “M” coils are used for one and two row applications that
require same end connections. For type “M” coils the supply and
return headers are offset or
“splayed”. This orientation allows
for the supply and return headers
to be placed side by side.
Installation
. It is recommended that the
coils be cleaned with a commercially available coil cleaner prior
to installation.
. Check the coil hand designation to insure that it matches the
system. Water and glycol coils are generally plumbed with the
supply connection located on the bottom of the leaving air-side of
the coil and the return connection at the top of the entering air-side
of the coil (Figure 1 - Coil Connection Diagram). This arrangement
provides counter flow heat exchange and positive coil drainage. If
a universal coil is supplied, cap off the two unused connections.
Once installed, the coil should be pressurized to 100 psig
with dry nitrogen or other suitable gas. The coil should be left pressurized for a minimum of 10 minutes. If the coil holds the pressure,
the hook-up can be considered leak free. If the pressure drops by
5 psig or less re-pressurize the coil and wait another 10 minutes. If
the pressure drops again, there is more than likely one or more
small leaks which should be located and repaired. Pressure
losses greater than 5 psig would indicate a larger leak that should
be isolated and repaired. If the coil itself is found to be leaking,
Return Bends Splayed Heade
W Type
> 2 Row
M Type
contact your local representative. Unauthorized repair to the coil
may void the coil’s warranty (see warranty policy on back cover).
Return
Air Ai
Supply
Figure 1 - Coil Connection Diagram
All field brazing and welding should be performed using high
quality materials and an inert gas purge (such as nitrogen) to
reduce oxidation of the internal surface of the coil.
All field piping must be self supporting. System piping should
be flexible enough to allow for thermal expansion and contraction of
the coil.
General piping diagrams can be found in Figure 2 - Horizontal
Airflow.
Operation
Initial Start-Up
1. Open all air
vents so that air is
eliminated from within
the coil circuitry and
Air Vent
Gate Valve
u
t
e
R
Tee
n
r
Vent Plug
i
r
F
l
o
w
headers. Verify that
all vents and drains
are not obstructed
and do discharge a
stream of water.
Fill the coil with
water then close all
Dirt Leg
Cap
Supply
Drain Plug
Union
Figure 2 - Horizontal Airflow Diagram
vents.
Perform an initial hydrostatic leak test of all brazed, threaded
or flanged joints, valves and interconnecting piping. Recheck the
coil level and correct if necessary. When the setup is found to be
leak free, discharge and discard initial water charge. It is important
that all grease, oil, flux and sealing compounds present from the
installation be removed.
General
1. Proper air distribution is vital to coil performance. Air flow any-
where on the coil face should not vary by more than 20%.
The drain pan and associated piping (drain line and trap)
should be installed so that there is no standing water in the drain
pan and that no blow-through occurs.
Fluid and air velocities should be maintained within recommended values.
retaWspf8ot1
locylGspf6ot1
yticoleVdiulF
slioCgnilooC
slioCgnitaeHmpf0051-002
yticoleVriA
mpf008-002:ecafruSyrD
mpf055-002:ecafruSteW
Maintenance
General
1. Filters should be inspected on a regular basis and changed as
needed. Maintaining clean filters is a cost effective way to help
maintain maximum coil performance and service life.
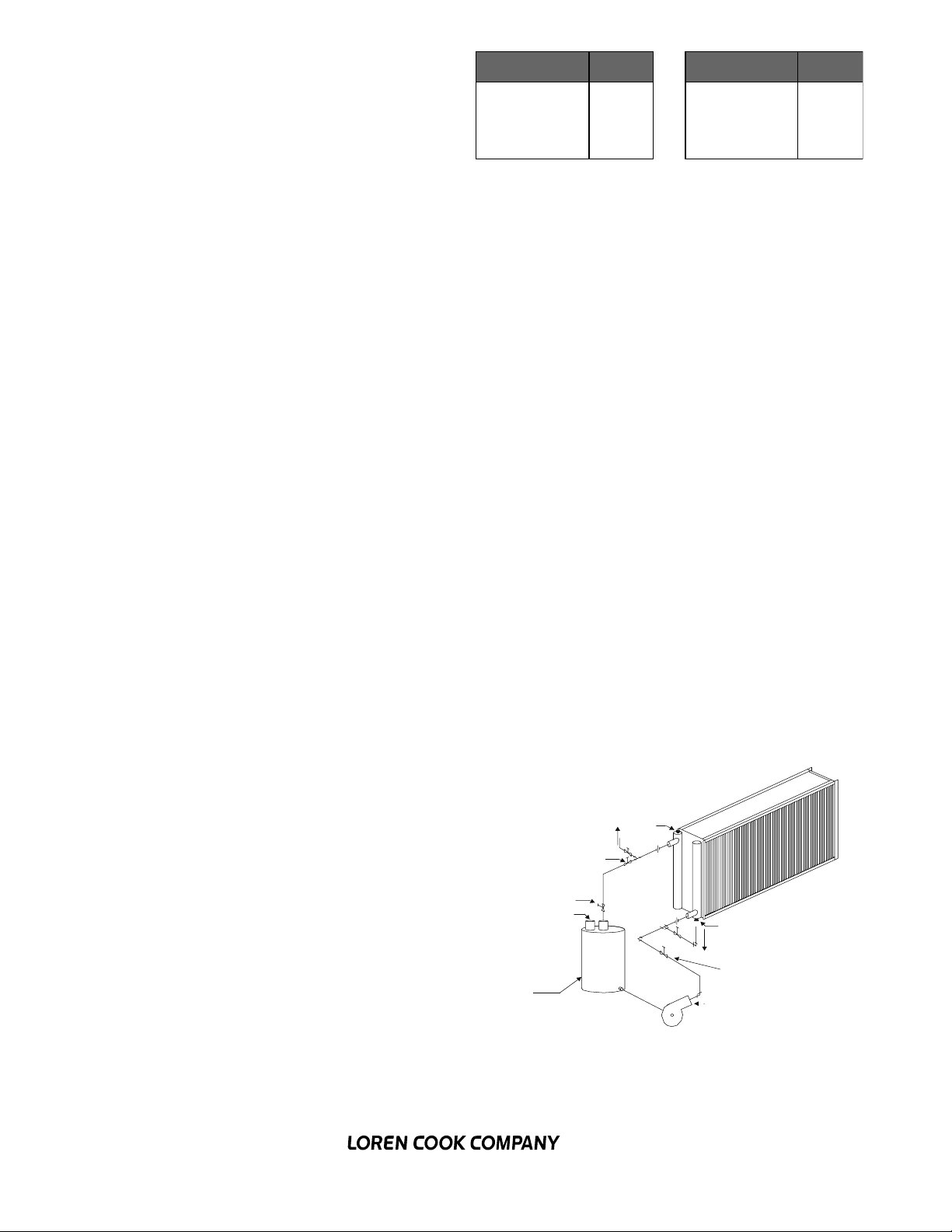
4.
3.
2.
6.
7.
4.
5.
2.
3.
2.
9.
7.
8.
4.
5.
6.
3.
maintain maximum coil performance and service life.
Periodic inspection of the coil for signs of corrosion and/or
leaks is recommended. Repair and replacement of the coil and the
connecting piping, valves, etc., should be performed as needed by
a qualified individual(s).
Should the coil surface need cleaning, caution should be
exercised in selecting the cleaning solution as well as the cleaning
equipment. Improper selection can result in damage to the coil
and/or health hazards. Clean the coil from the leaving air-side so
that foreign material will be washed out of the coil rather than
pushed further in. Be sure to carefully read and follow the manufacturer’s recommendations before using any cleaning fluid.
Maintain the circulated fluid free of sediment, corrosive
products and biological contaminants. Periodic testing of the fluid
followed by any necessary corrective measures along with maintaining adequate fluid velocities and proper filtering of the fluid will
help to satisfy this goal.
5. If automatic air vents are not utilized, periodic venting of the
coil is recommended to remove accumulated air. Caution should
be exercised to avoid injury. High pressure and/or high temperature fluids can cause serious personal injury.
Freeze Protection
During the winter, chilled water coils need to be protected
against freezing. The two predominant protective measures are
covered below.
Blowing-Out Coils
1. Isolate the coil from the rest of the system by closing the
valves on both the supply and return lines (gate valves in Figure 2
- Horizontal Airflow Diagram).
Drain the coil by opening all drain valves and/or the drain
plug. Remove the vent plug to aid the draining process.
Once the coil has been fully drained, the blower can be
hooked-up. Caps installed in the piping on straight runs going to
the supply and return connections are ideal points to hook-up the
blower. The air vent and drain plug are not suitable locations for
hooking up the blower. Caution should be exercised when installing the blower. The blower operator must take precautions to
insure that water does not come into contact with any of the electrical components of the blower. Failure to do so may result in
damage to the equipment and serious injury.
Close the vent or drain plug on the header which the blower
is connected and open the drain valve or cap on the other header.
Operate the blower for 45 minutes and then check the coil to
see if it is dry. A mirror placed in the discharge will become fogged
if moisture is present. Repeat this procedure until the coil is dry.
Let the coil stand for several minutes then blow it out again. If
water comes out, repeat the blowing operation.
Leave all plugs out and drains open until the threat of freezing has passed.
Flushing Coils
1. Recommend the use of inhibited glycol designed for HVAC
applications for corrosion protection. The use of uninhibited glycol
has produced formicary corrosion in copper tubing. The complete
filling of water coils with an inhibited glycol solution for freeze protection can be expensive. In some instances, it is more cost effective to flush the coils with an appropriate concentration of inhibited
glycol solution. Residual fluid can be left in the coil without the
threat of freeze damage provided the correct concentration of
inhibited glycol was used. The recovered fluid can then be used to
flush other coils. Select an inhibited glycol solution that will protect
the coil from the lowest possible temperatures that can occur at
the particular coil’s locality. The following tables have been provided for your convenience.
yBlocylGenelyhtE%
emuloV
0
10
20
30
40
50
60
ezeerF
1
tniop
o
23
F
o
52
F
o
F
61
o
F
3
o
F
31-
o
F
43-
o
F
55-
yBlocylGenelyporP%
emuloV
0
10
20
30
40
50
60
ezeerF
1
tniop
o
23
F
o
62
F
o
91
F
o
8
F
o
F
7-
o
F
82-
o
F
06-
Estimate the volume of the coil in gallons.
For 5/8” tubes (1.5” face tube spacing)
(finned height in inches)x(finned length in inches)x(# of
rows)x 0.0011 = gallons
For 1/2” tubes (1.25” face tube spacing)
(finned height in inches)x(finned length in inches)x(# of
rows)x 0.00083 = gallons
Isolate the coil from the rest of the system by closing the
valves on both the supply and return lines (gate valves in Figure
1 - Horizontal Airflow).
Drain the coil by opening all drain valves and/or the drain
plug. Remove the vent plug to aid the draining process.
Close the drain valve(s) and drain plug.
Connect the flushing system to the coil. A typical system is
shown in Figure 3 - Flushing System Diagram.
With the throttling valve closed, start the pump and operate until the air is vented from the coil. Next, close the air vent.
Open the throttling valve about half-way and circulate the
fluid through the coil for 15 minutes. Check the strength of the
fluid. A hydrometer or test kit from the fluid manufacturer is suit-
able for this application.
Adjust the solution strength as needed and circulate the
fluid for another 15 minutes.
10. Repeat steps 8 and 9 until the desired concentration is
reached.
11. Shut the pump down and drain the inhibited glycol from
the coil.
12. The recaptured fluid can be used to flush other coils.
Note: Be sure to follow the manufactures’ recommendations
before utilizing any glycol based antifreeze solution. Additional
fluid will be required for the pump, connected piping and fluid
reservoir. Formulae are for estimation purposes only.
Ven t
Shut-off Valve
w/Hose Connection
Throttling
Val ve
Ven t
Hole
Inhibited
Glycol
Reservoir
Figure 3 - Flushing System Diagram
Drain
Shut-off Valve
w/Hose Connection
Pump
Corporate Offices: 2015 E. Dale Street Springfi eld, MO 65803 417.869.6474
lorencook.com
2
ERV Fluid Coil IOM Supplement- December 2002