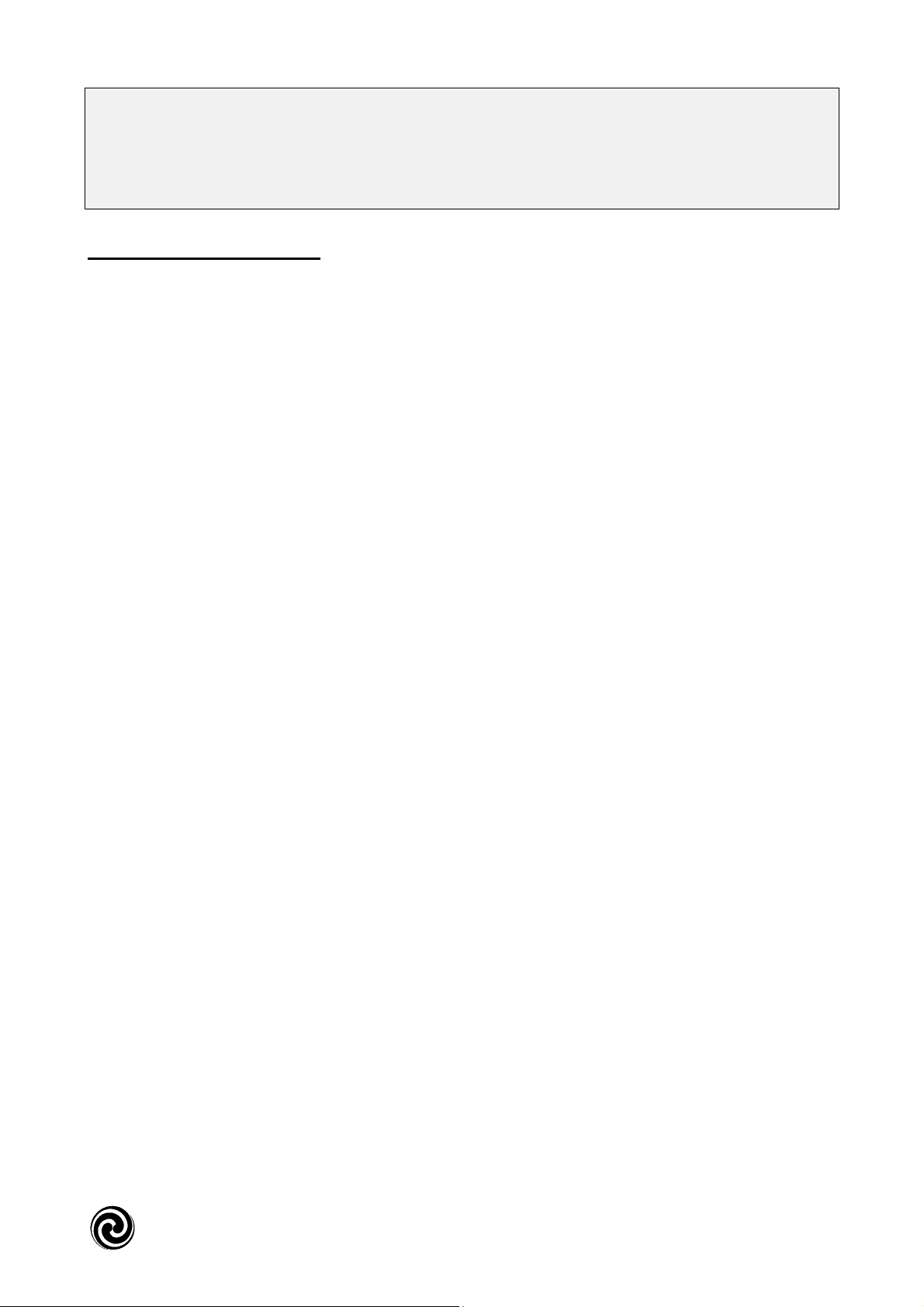
DETAILED ENGINEERING DESCRIPTION AND MECHANICAL
FEATURES OF CONTINENTAL INDUSTRIE MULTISTAGE CENTRIFUGAL
BLOWER MODEL 031A
I - BLOWER HOUSING
The centrifugal blower housing consists of an inlet head with special feature to direct air to
inlet of first impeller and outlet head of special design to eliminate friction and multiple
intermediate sections. These parts are made in cast iron EN-GJL-250 (ASTM A48-35B) (for
I/O heads) & cast aluminium (for intermediate sections) according to rigid Continental
Industrie specifications, extreme care to be exercised in assembly of interlocking cast
aluminium intermediate sections and annular diffusers (baffles).
The entire assembly is securely held together actually with multiple tension rods which bind
the entire housing into a solid integral unit.
1.0 Inlet head
1.1 Flange connection DN 150, PN 10 (6”)
1.2 Cast iron EN-GJL-250 (ASTM A48-35B)
1.3 Minimum wall thickness: 8 mm (0.31”)
1.4 Can be supplied in various flange positions relative to the vertical centre line in
increments of 90° (option)
2.0 Outlet head
2.1 Flange connection DN 150, PN 10 (6”).
2.2 Cast iron EN-GJL-250 (ASTM A48-35B).
2.3 Minimum wall thickness: 8 mm (0.31”)
2.4 Can be supplied in various flange positions relative to the vertical centre line in
increments of 90° (option)
3.0 Intermediate section
3.1 Cast aluminium EN-AC-42000 (ASTM 360.1).
3.2 Each intermediate section is cast in one piece
4.0 Bearing housing
The outboard bearing housings are cast iron and bolted to the outside of the head sections
insuring cool operation of bearings.
4.1 Cast iron EN-GJL-250 (ASTM A48-35B).
4.2 Has cast fins to improve rigidity and increase heat dissipation
4.3 Labyrinth type grease seal
4.4 Provided with 2 tapped holes in the housing flange to act as bearing puller.
N.B.: When the inlet air or gas temperature is too high, we can adapt as option special
bearing housings with a water or air cooling system (technical drawing on request).
Values, dimensions and reference in this brochure are approximate and intended as guide only, not for construction and are subject to change without notice
DETAILED ENGINEERING DESCRIPTION - CONTINENTAL INDUSTRIE
DEB031EN – 04/2010
1/4
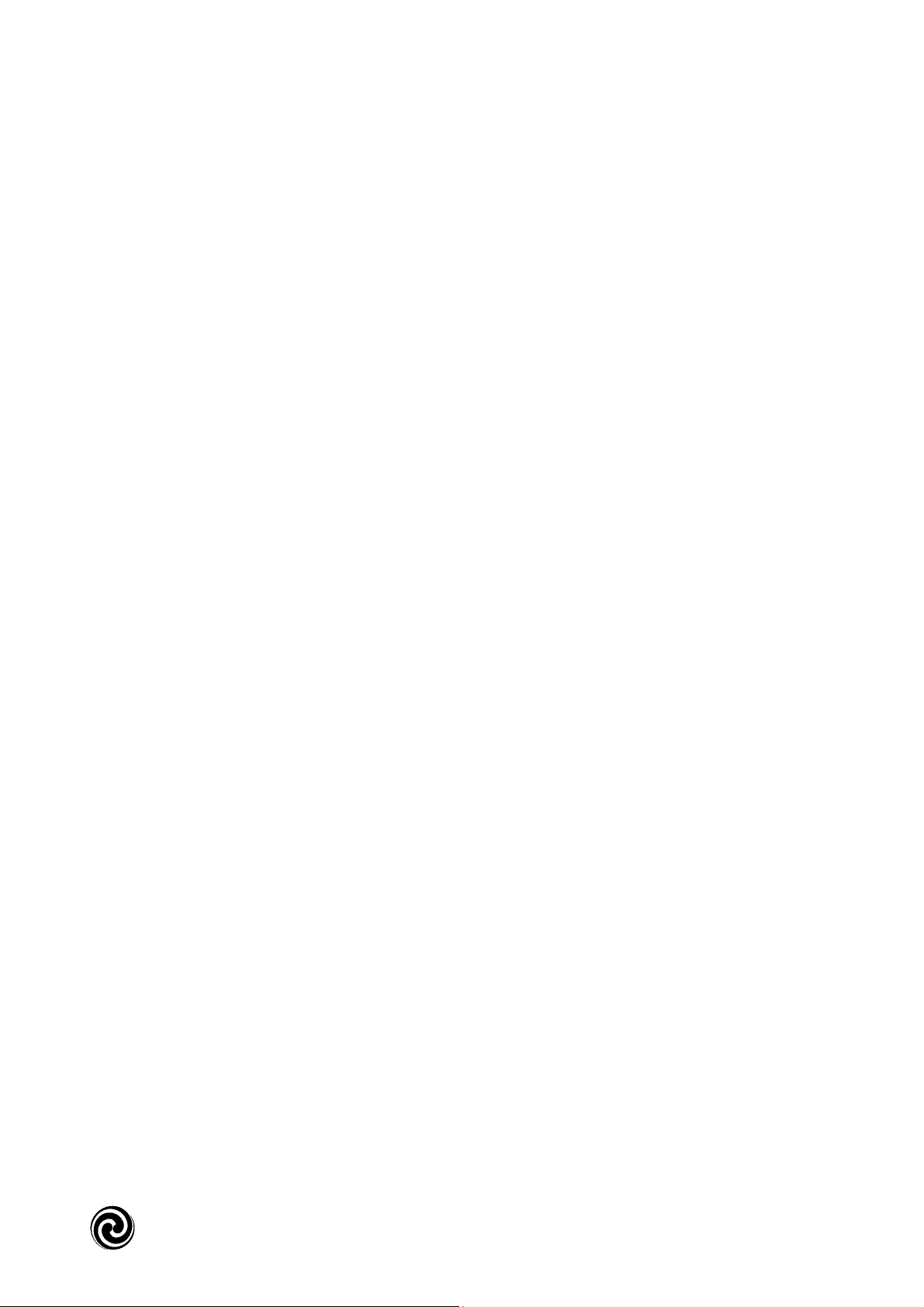
5.0 Bearings
5.1 The rotor assembly is supported by 2 heavy duty grease lubricated ball bearings,
single row, sized to withstand the thrust load also type SKF or FAG.
5.2 Sized for minimum 10 years of operation (Direct Drive only), following SKF L10
bearing life calculation method.
5.3 Bearings are mounted in outboard type bearing housings and located so that
bearings may be serviced without disassembling the blower casing or piping.
6.0 Shaft
6.1 C35 (AISI 1035) carbon steel shaft, straightened and stressreleved
6.2 Shaft is ground all over
6.3 Stiff shaft design to minimize vibration
6.4 The diameter of the shaft end is 45 mm (1.77”)
7.0 Shaft seals
7.1 Shaft sealing is accomplished using graphite ring seals or carbon ring seals.
8.0 Impellers
8.1 The impellers are in cast aluminium, in EN AC-43100 (AISI 360.1).
8.2 For minimum corrosion all aluminium alloys are non copper alloys
8.3 The outer diameter of the impeller is 610 mm (24”)
8.4 Each impeller is automatically sanded or shotted when leaving the foundry before
the machining
8.5 Each impeller is statically balanced.
8.6 Impeller tip speed: 114 m/sec (374 FPS) at 3600 rpm.
8.7 First critical speed (9 stages) 3747 rpm.
8.8 Impeller assembly: to consist of a heavy steel shaft accurently machined and one or
more aluminium alloy cast impeller(s), statically balanced, securely keyed to shaft
and held in place by lock washers and locknuts.
Values, dimensions and reference in this brochure are approximate and intended as guide only, not for construction and are subject to change without notice
DETAILED ENGINEERING DESCRIPTION - CONTINENTAL INDUSTRIE
DEB031EN – 04/2010
2/4