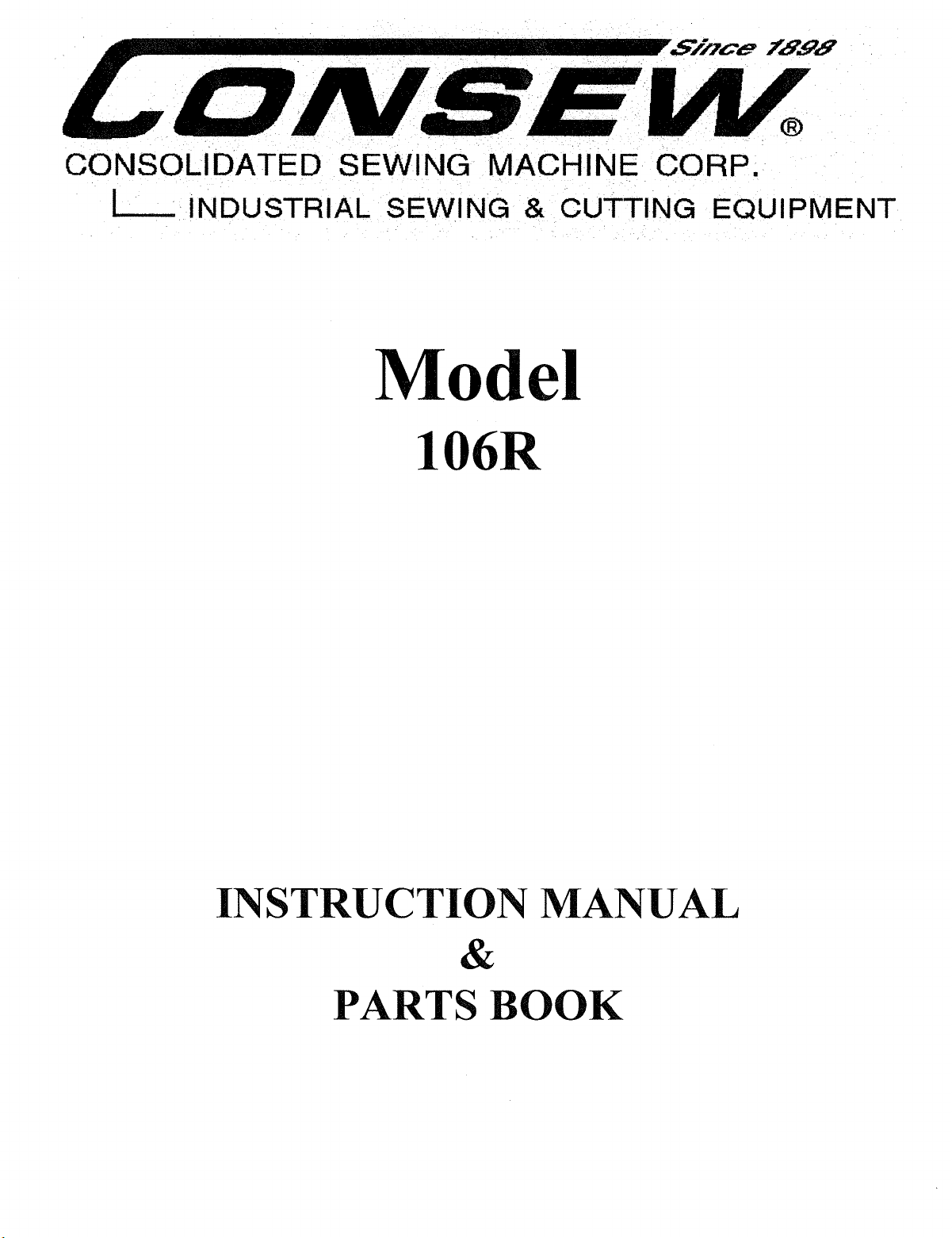
CONSOLIDATED SEWING MACHINE CORP.
I . .
INDUSTRIAL
SEWING
&
CUTTING
Model
106R
EQUIPMENT
INSTRUCTION
&
PARTS
BOOK
MANUAL
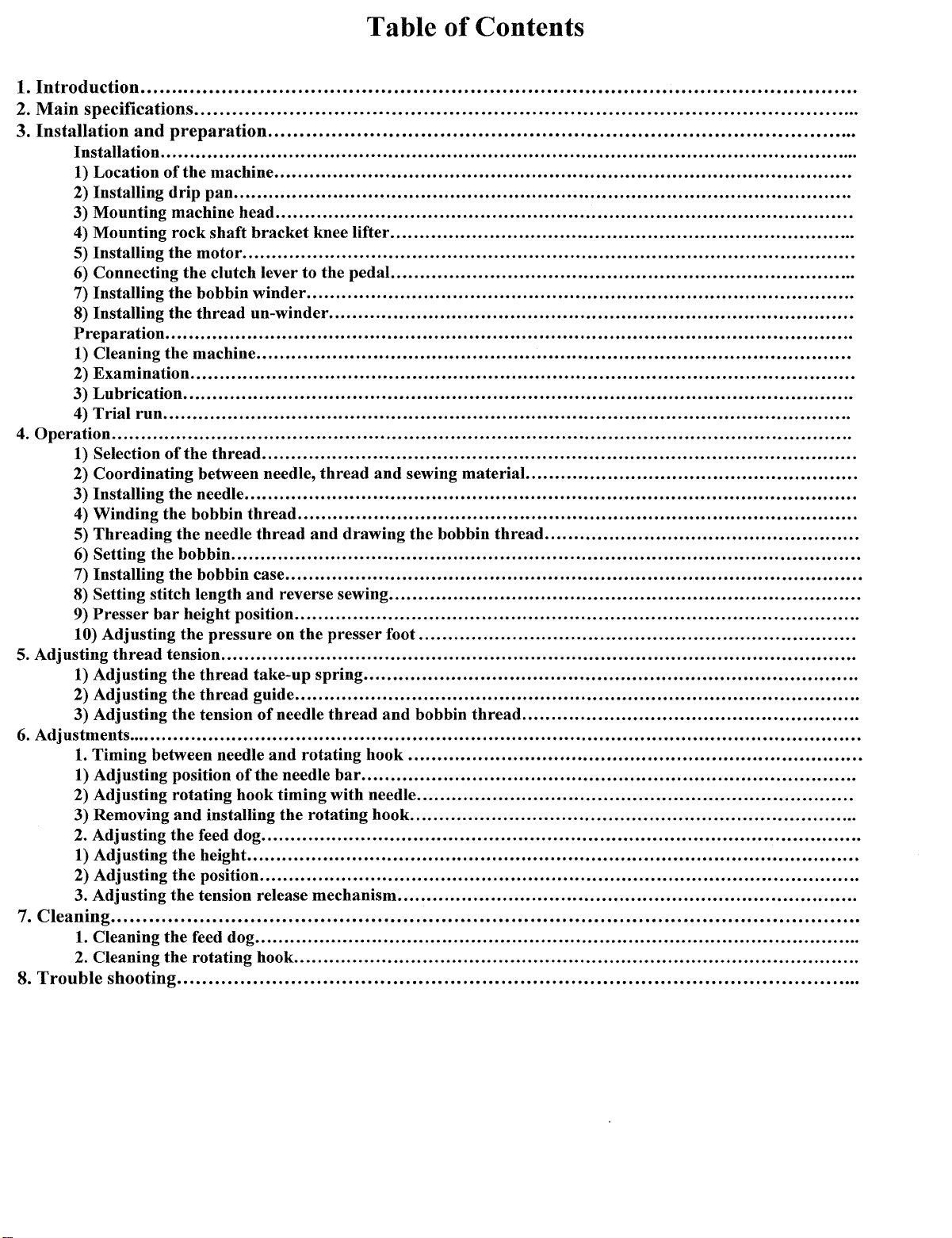
Table
of
Contents
1. Introduction
2. Main specifications
................................................................................................................
........................................................................................................
3. Installation and preparation
Installation
1) Location
2) Installing
3) Mounting machine head
4) Mounting
5) Installing
6) Connecting
7) Installing
8) Installing
Preparation
1) Cleaning
2) Examination
3) Lubrication
4) Trial run
4. Operation
5. Adjusting
6. Adjustments
7. Cleaning
8.
Trouble
..............................................................................................................................
1) Selection
2) Coordinating between needle,
3) Installing
4) Winding
5)
Threading
6) Setting the bobbin
7) Installing
8) Setting stitch length
Presser
9)
10) Adjusting the pressure on
thread
1) Adjusting
2) Adjusting
3) Adjusting
1. Timing between needle
1) Adjusting position
2) Adjusting rotating hook timing with needle
3) Removing
2. Adjusting
1) Adjusting
2) Adjusting
3. Adjusting
.....................................................................................................................
1. Cleaning
2. Cleaning
shooting
..•.•...........................................................................•.......................................
of
the
machine
drip
pan
.........................................................................................................
rock
shaft
bracket
the
motor
........................................................................................................
the
clutch lever to the pedal.
the
bobbin
the
thread
.....................................................................................................................
the
machine
.................................................................................................................
..................................................................................................................
.....................................................................................................................
of
the
the
needle
the
bobbin
the
the
bobbin case
bar
height position
tension
the
thread
the
thread
the
tension
.............................................................................................................................
and
the
feed dog
the
height
the
position
the
tension release mechanism
the
feed dog
the
rotating hook
..............•.•.....................•..................................•.....•............•...............
winder
un-winder
.................................................................•....................................
thread
........................................................................................................
thread
needle
installing
thread
...........................................................................................................
and
............................................................................................................
take-up
guide
of
of
the
........................................................................................................
.............................•..............................................•..........................
.......................................................................................................
............................................................................................
...................•...................................•.........•.............•...................
..................................................................................................
knee lifter
.............................................................................................
.........................................................................................
.....................................................................................................
thread
...............................................................................................
and
..................................................................................................
reverse sewing
................................................................................................
the
presser
spring
................................................................................................
needle
and
the
......................................................................................................
thread
rotating hook
needle
bar
rotating hook
................................................................................................
...............................................................................
..............................................................................
and
sewing material.
drawing
....................................................................................
the
bobbin
................................................................................
foot
..........................................................................
....................................................................................
and
bobbin
.............................................................................
..........................................................................
............................................................................
..............................................................................
thread
.......................................................
thread
.....................................................
.........................................................
.
.
.
.
.
.
.
.
.
.
.
.
.
.
.
.
.
.
.
.
.
.
.
.
.
.
.
.
.
.
.
.
.
.
.
.
.
.
.
.
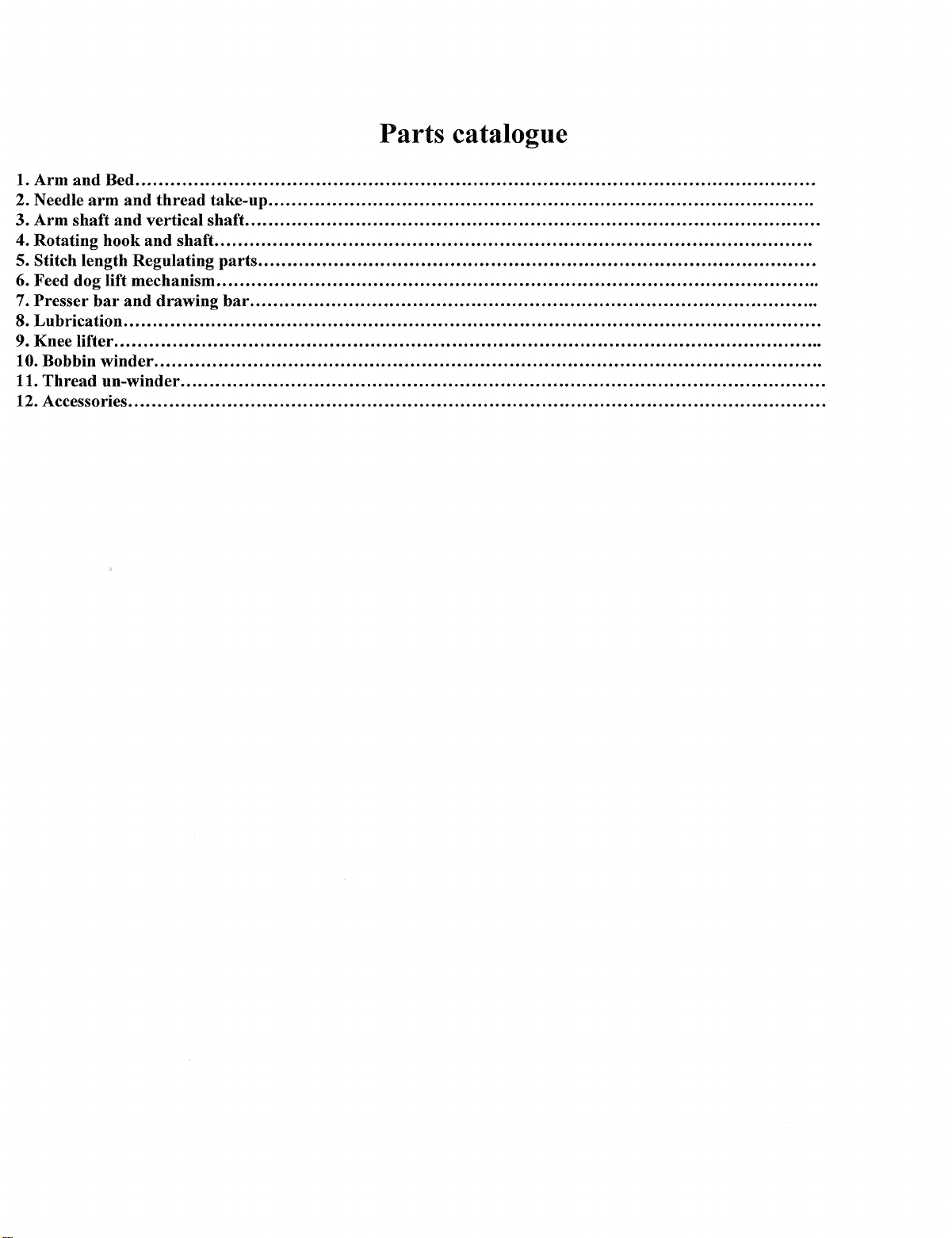
1.
Arm
and
Bed
..•.•••...•..•.....••••...•...•.......•......•.•..••...•.......•....•....••.•.............•...•.•..••.....•..•.......
2.
Needle
Arm
3.
4. Rotating
5. Stitch length Regulating
6. Feed dog lift mechanism
Presser
7.
Lubrication
8.
9. Knee lifter
10. Bobbin
11.
12. Accessories
shaft
Thread
arm
and
thread
and
vertical
hook
and
bar
and
drawing
..........•.............................................................................................................
....•....••.......•......•...•.......•...•.........••...•.......•.•....•..•..•.........••.........•..•....•....•.......•..
winder
un-winder
............................................................................•......................................
.......................................................................................................................
shaft
shaft
..•.•..•.....•.....•.........••.....••......•....................•................•..•..•...••...•.....•...••..
Parts
take-up
......................................................................................................
parts
.......................................................................................................
.............................................................................................
........................................................................•..........................
...............................................................................................
bar
.................................................................................................
catalogue
.
.
.
.
.
.
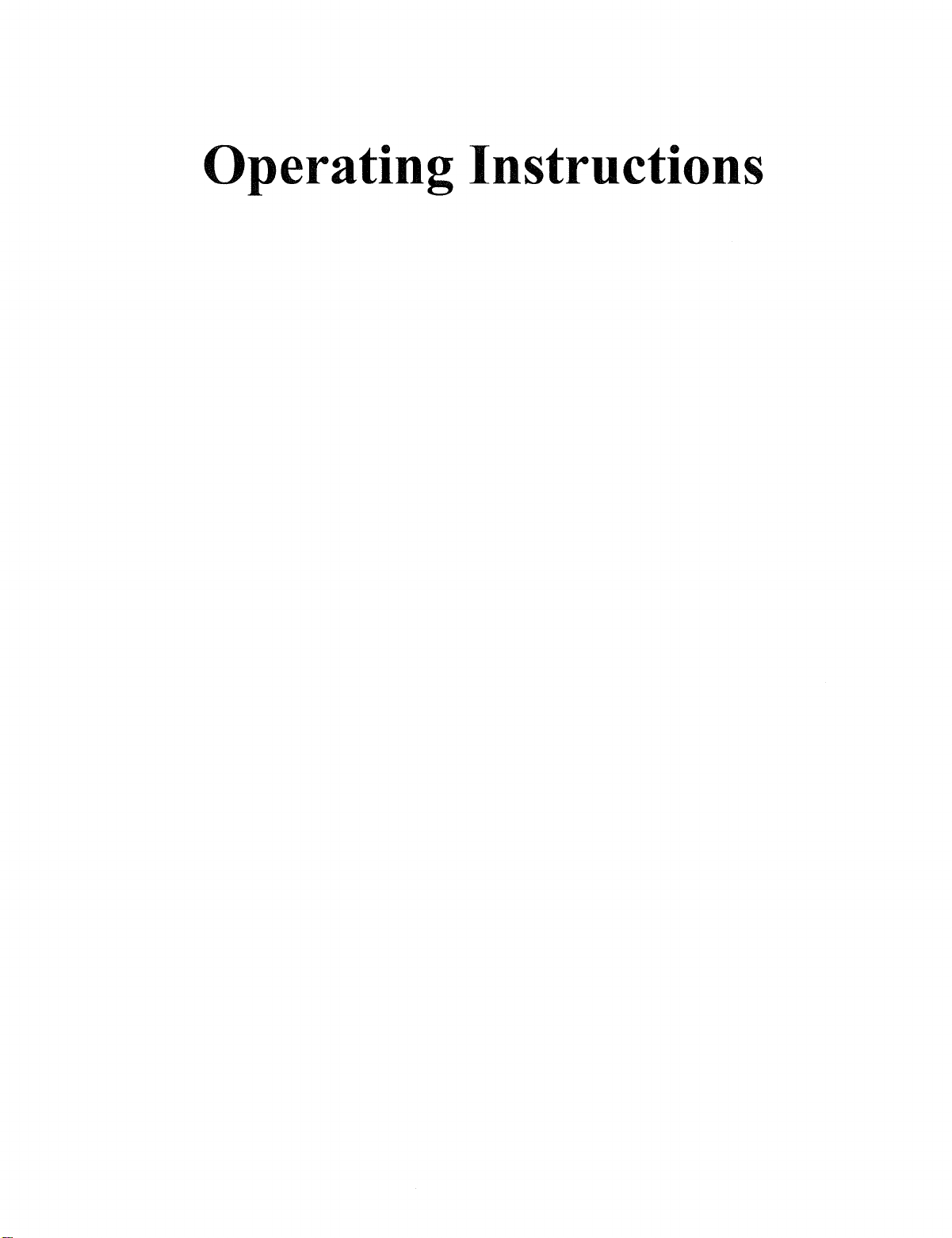
Operating Instructions

1.
Introduction
The
Consew
usage.
a
large
smooth
beautiful,
tarps,
pillows,
106R
It
is
engineered
rotating
and
even
even,
hook
flat
shoes
2. Specifications
1)
Max.
Sewing
2) Max. stitch length:
3)
Presser
4)
Max. thickness
5) Needle:
6)Hook:
7)
Motor:
foot lift:
speed:
sewing
feed
stitches
of
material to be sewn:
machine
with a needle
with a double
when
and
sewing a single
and
worker
is a
thread
is
widely
safety
single
bearing,
capacity.
layer
used
items.
needle,
thread
of
in
the
lockstitch
link
take-up,
It
has
all
fabric
or a lap
manufacture
designed
spiral
the
advantages
seam.
of
suitcases,
for
medium
bevel
gear
of a low
The
Consew
leather
2000
9mm
6.5
w/knee lifter
up to 8 layers
a thickness
DPx5,
Large
double
Yz
Motor
to
heavy
transmission
torque,
106R
goods,
spm
mm-13mm
of
of
8 mm each
#18~22
rotating hook with
HP,
thread
1PH,
capacity
llOV
duty
and
low noise,
produces,
handbags,
leather, with
Clutch
3. Installation
1)
Placement
To
ensure smooth vibration free operation, the machine should be placed on
Placing
vibration.
2)
Installing
connecting rod (15)
hole to the table, (as depicted in Fig. 1) then drive nails (2) into both sides
figure on 9
of
the
drip
of
parts
and
the
machine
preparation
machine
pan
(Fig. 1). Fix
of
machine head, so they touch, also make sure dimensions
book).
stand
on a rubberized
drip
pan
mat
(1) into
is recommended to
the
table cutout, aligning knee lifting
further
reduce the noise
are
of
the cutout to secure the
an
even
at
30
and
firm floor.
and
rod
(3) with knee lifter
and
119.5mm from nail
drip
pan. (See
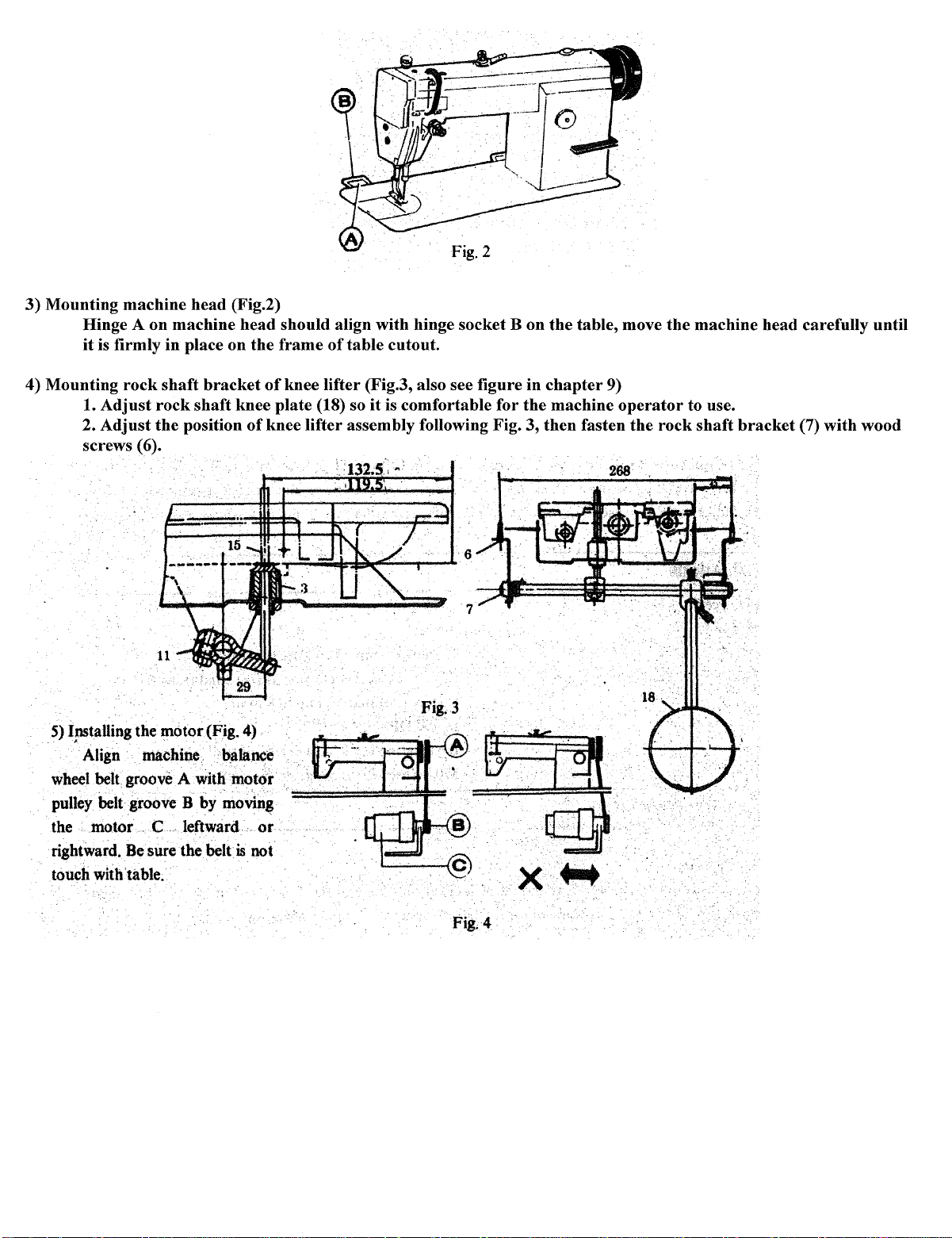
3)
Mounting machine head (Fig.2)
Hinge A on machine head should align with hinge socket B on
it
is firmly in place
4) Mounting
1.
Adjust
Adjust
2.
screws (6).
rock
shaft
rock
the
on
bracket
shaft knee plate (18) so
position
Fig.2
the
table, move
the
frame
of
of
knee lifter assembly following Fig. 3, then fasten
of
table cutout.
knee lifter (Fig.3, also see figure in
it
is comfortable for
7
the
chapter
machine
9)
operator
the
the
machine head carefully until
to use.
rock
shaft
bracket
(7) with wood
5)
Installing the motor(Fig. 4)
' . .
Align machine.
wheel
belt
groove A with
pulley belt groove B by
the motor .
rightward. Be sure the
with'tilble.
touch
C.
leftward
belt
~lance
motor
mo~n$
...
or
is
not
~
Ernl.
·.·.·.···.···.··.··~.~
.
.··
...
·
..
......
x. · ....
FigA
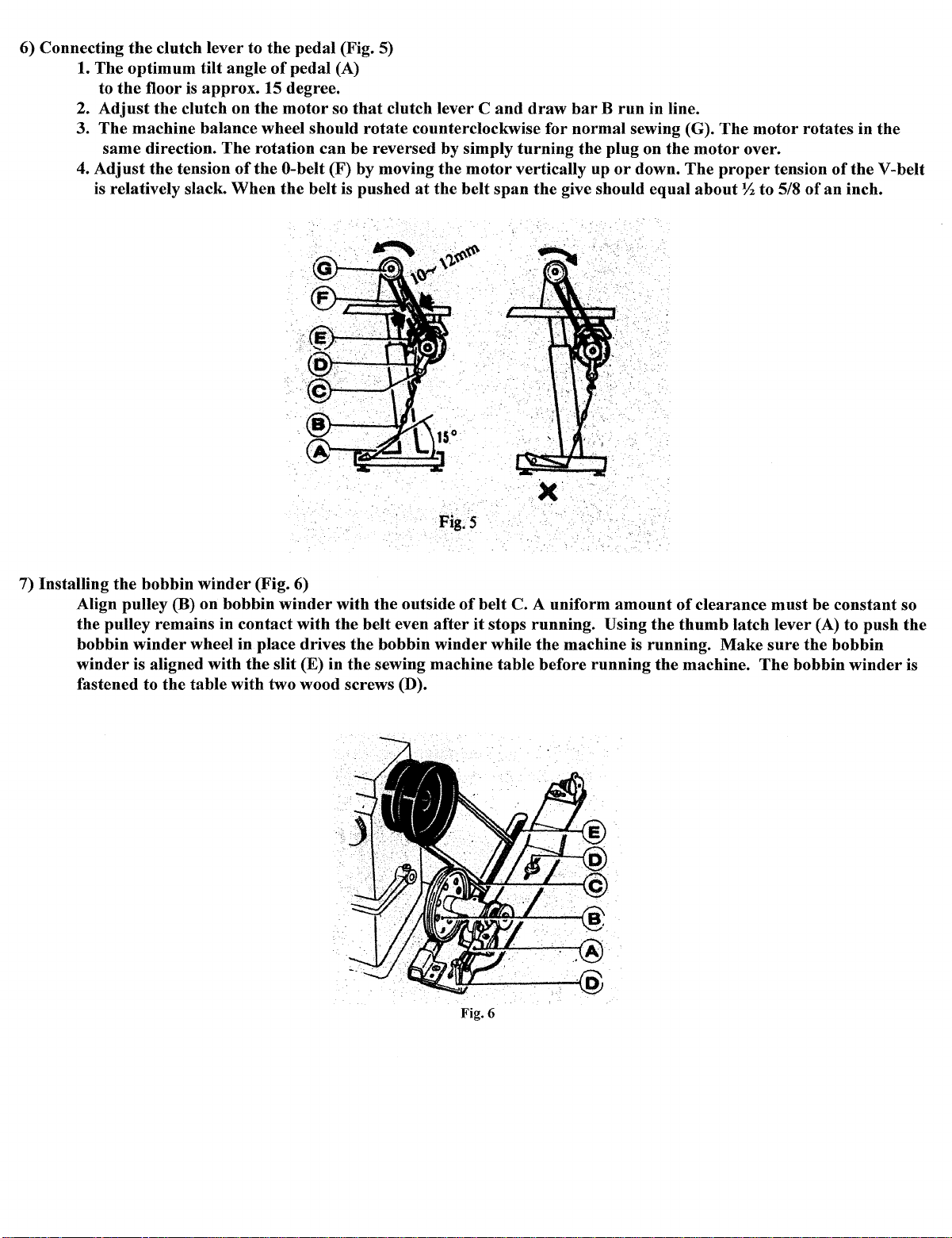
6) Connecting
The
1.
to
2.
Adjust
The
3.
same
Adjust
4.
is relatively slack.
the
clutch lever to
optimum
the
floor is approx. 15 degree.
the
clutch on
tilt angle
the
pedal (Fig. 5)
of
pedal (A)
the
motor
machine balance wheel should
direction.
the
The
tension
rotation
ofthe
When
can
0-belt (F) by moving
the
belt is pushed
so
that
clutch lever C
rotate
counterclockwise for
be reversed by simply
the
motor
at
the
belt
and
draw
turning
vertically up
span
the
barB
run
in line.
normal
the plug on
sewing {G).
the
or
down.
give should equal
motor
The
about
The
motor
over.
proper
Yz
to 5/8
rotates in
tension
of
of
an
the
inch.
the
V-belt
7) Installing
Align pulley
the pulley remains in contact with
bobbin
winder
fastened to
the
bobbin
(B) on bobbin
winder
wheel in place drives
is aligned with
the
table with two wood screws (D).
winder
(Fig. 6)
winder
the
slit (E) in
Fig.5
with
the
outside
the
belt even
the
bobbin
the
sewing machine table before
of
belt C. A uniform
after
it
stops running. Using
winder
while
amount
the
machine is running.
running
the
the
of
thumb
clearance
latch lever (A) to
Make
machine.
must
sure
The
be constant so
push
the
bobbin
bobbin
winder
the
is
Fig.6
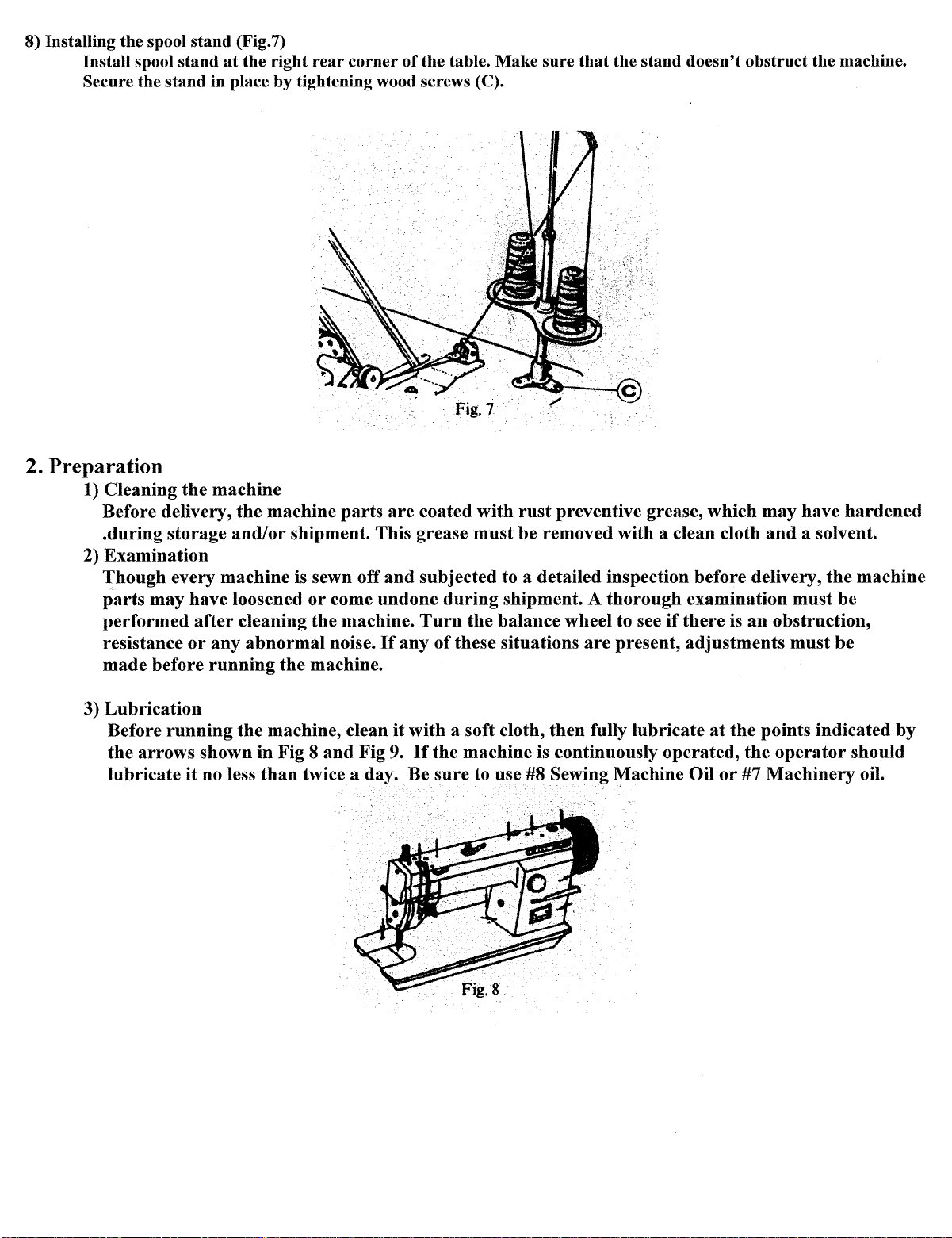
8) Installing
Install spool
Secure the
2.
Preparation
1) Cleaning
Before delivery,
.during
2) Examination
Though
p'arts may
performed
resistance
made
the
spool
stand
(Fig.7)
stand
at
the
right
rear
stand
in place by tightening wood screws (C).
the
machine
the
machine
storage
and/or
shipment. This grease
every machine is sewn off
have
after
or
before
loosened
cleaning
any
abnormal
running
or
the
the
machine.
corner
parts
come
undone
machine.
noise.
If
of
the
table.
Make
sure
that
the
stand
doesn't
are
coated
and
subjected to a detailed inspection before delivery,
Turn
any
with
rust
must
be removed
during
of
these situations
shipment. A
the
balance wheel to see
preventive grease, which
with
a clean cloth
thorough
are
present,
examination
if
there
is
adjustments
obstruct
may
have
and
a solvent.
must
an
obstruction,
must
the
machine.
hardened
the
be
be
machine
3)
Lubrication
Before
the
arrows
lubricate
running
shown
it
no less
the
machine, clean
in
Fig 8
than
twice a day. Be
and
it
Fig 9.
with
a soft cloth,
If
the
sure
then
fully lubricate
at
the
machine is continuously operated,
to use #8 Sewing Machine Oil
Fig.8
or
points indicated by
the
operator
#7
Machinery
should
oil.
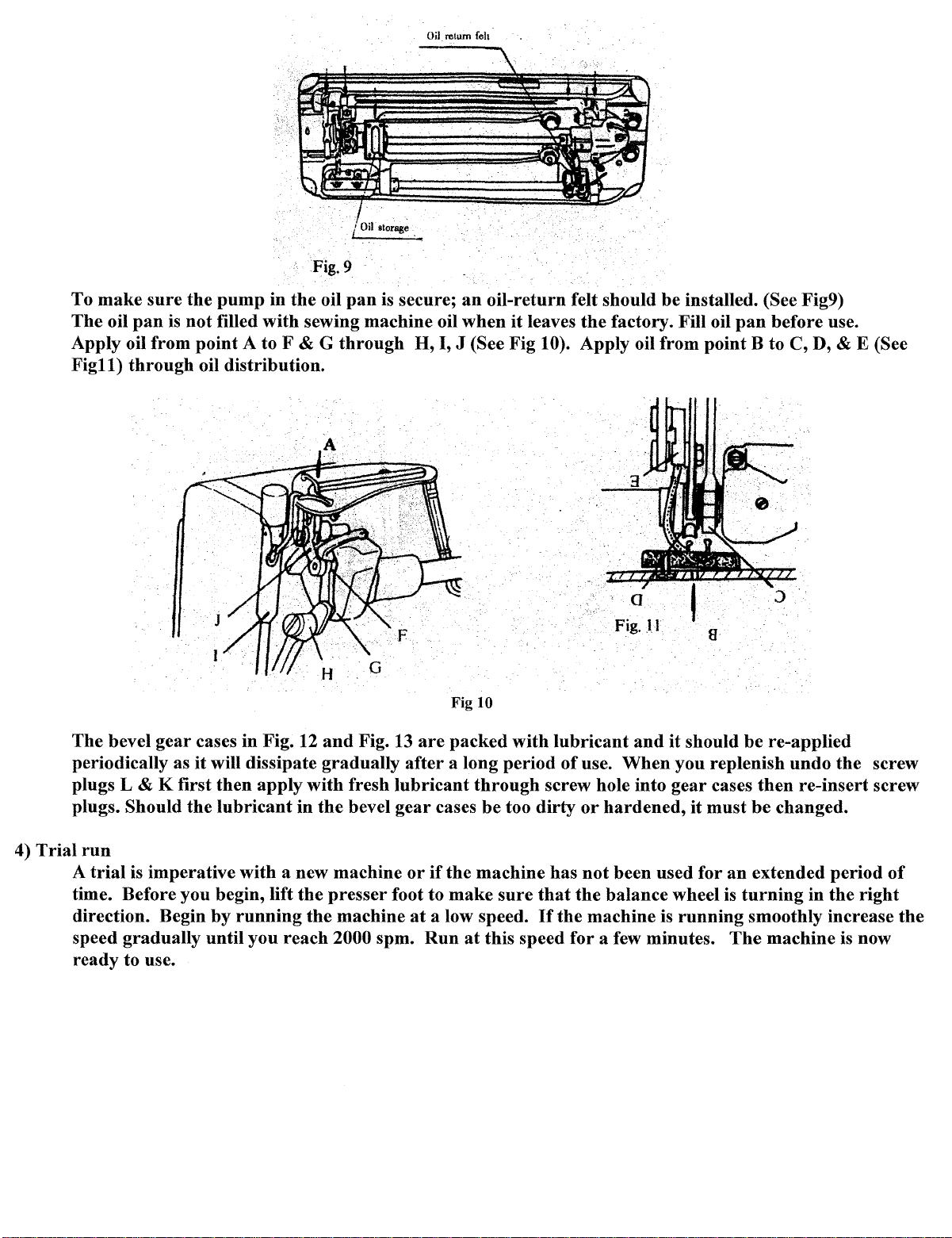
To
make
The
oil
sure
pan
is
the
not
pump
filled
in
with
Apply oil from point A to F
Figll)
through
oil distribution.
Fig.9
the
oil
pan
is
secure;
sewing machine oil
& G
through
H,
Oil return feb
an
oil-return felt should be installed. (See Fig9)
when
it
leaves
the
factory. Fill oil
pan
before use.
I, J (See Fig 10). Apply oil from point B to C, D, & E (See
4)
The
bevel
gear
cases
in
it
periodically as
plugs L
plugs. Should
Trial
run
A
trial
& K first
is imperative
will dissipate gradually
the
time. Before you begin, lift
direction. Begin by
Fig. 12
then
apply
lubricant
with
running
and
with
in
the
a new machine
the
presser
the
speed gradually until you reach 2000 spm.
ready
to use.
Fig. 13
fresh
bevel
lubricant
gear
foot to
machine
Fig 10
are
packed
after
a long period
through
cases be too
or
if
the machine has
make
at
a low speed.
Run
at
this speed for a few minutes.
with
lubricant
of
screw hole into
dirty
sure
that
If
the
Fig.ll
and
use.
When
or
hardened,
not
been used for
the
balance wheel is
machine is
it
should be re-applied
you replenish
gear
cases
it
must
an
turning
running
The
undo
then
re-insert screw
be
changed.
extended period
in
smoothly increase
machine
the
the
is
screw
of
right
the
now
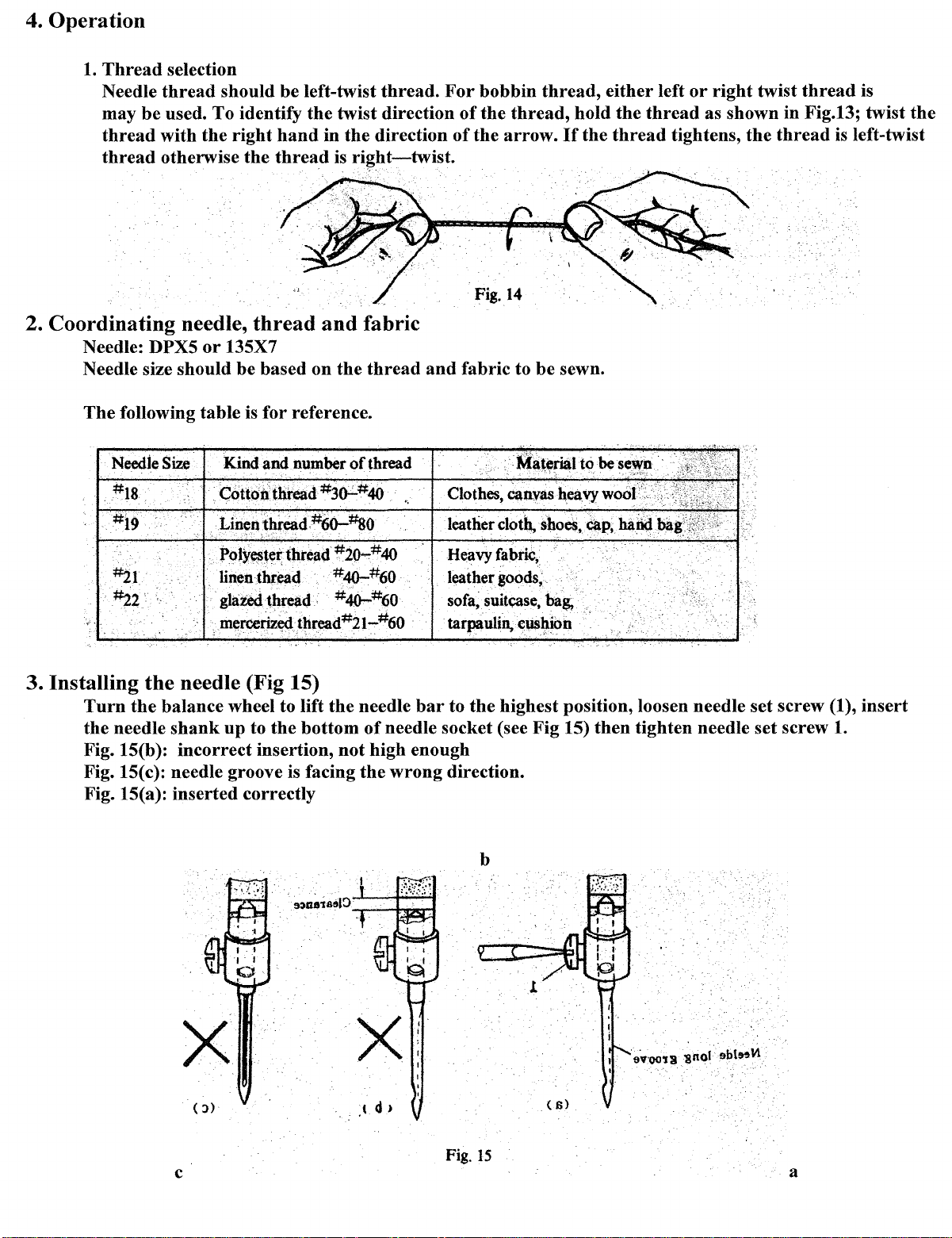
4.
Operation
1.
Thread
Needle
may
thread
thread
2.
Coordinating
Needle: DPX5
Needle size should be based
The
following table is for reference.
selection
thread
be
used.
with
otherwise
needle,
should be left-twist
To
the
or
identify
right
the
thread
135X7
the
hand
thread
on
in
and
thread.
twist direction
the
direction
is
ri~ht-twist.
For
of
of
bobbin
the
the
Fig. 14
fabric
the
thread
and
fabric to be sewn.
thread,
thread,
arrow.
hold
If
the
either
the
thread
thread
left
or
right
twist
thread
as shown in Fig.13; twist
tightens,
the
thread
is
is
left-twist
the
Needle
~1
·~2·
3. Installing
Turn
the
the
needle
Fig. 15(b ): incorrect insertion,
Fig. 15(c): needle groove is facing
Fig. 15(a): inserted correctly
Size
Kind and number
cottoxt'
)>oly~~er
. linen
thread
thread #2o-#40
thr~d
gtazedthread
.mercerlze,d
the
needle (Fig 15)
balance wheel to lift
shank
up
to
the
of
thread
~~#40
#40-:#60
#40-:#60
thread#2t-#60
the
needle
bottom
of
needle socket (see Fig 15)
not
high enough
the
wrong
..
Heavy
fabric,
leather
sofa~.suitcase,
tarpaulin,
bar
to
direction.
goods,
ba~
eu.sltion
the
highest position, loosen needle set screw (1),
b
··
then
tighten needle set screw 1.
insert
X
( :>)
Fig.
15
c
a
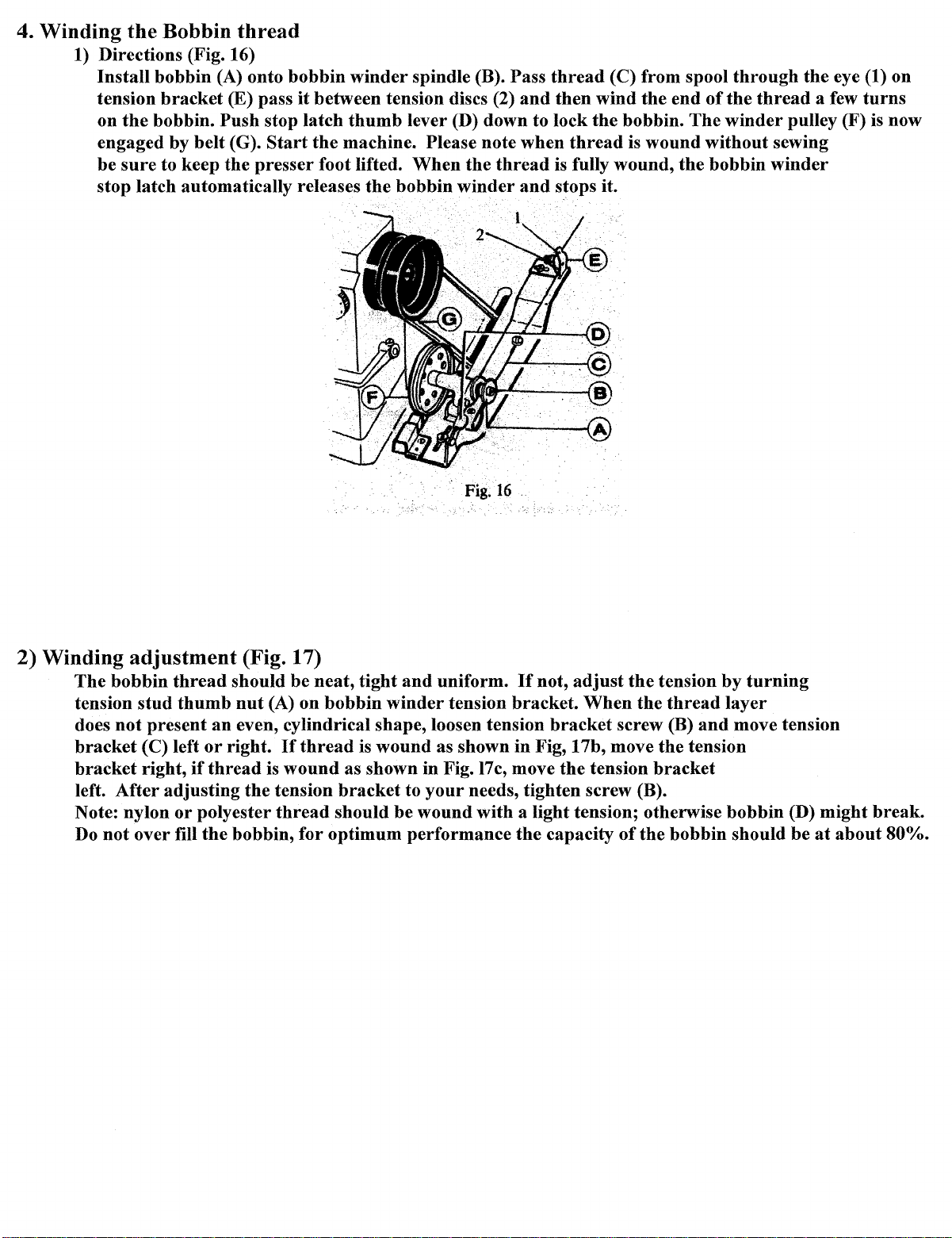
4. Winding
1)
Directions (Fig. 16)
Install
tension
on
engaged by
be
stop latch automatically releases
the
Bobbin
bobbin (A) onto
bracket
the
bobbin.
belt
sure
to keep
thread
(E) pass
Push
stop latch
(G).
Start
the
presser
bobbin
it
winder
between tension discs (2)
thumb
the
machine. Please note
foot lifted.
spindle (B). Pass
lever (D) down to lock
When
the
bobbin
the
thread
winder
Fig.
16
thread
and
then
when
is
and
stops it.
.
(C) from spool
wind the
the
bobbin.
thread
fully wound,
is
wound
end
The
the
through
of
the
thread
winder
without
bobbin
the
eye (1) on
a few
turns
pulley (F) is now
sewing
winder
2) Winding
The
bobbin
tension
does
not
bracket
bracket
left.
After
Note: nylon
Do
not
adjustment
thread
stud
thumb
present
(C) left
right,
over fill
an
or
right.
if
thread
adjusting
or
polyester
the
(Fig. 17)
should be
nut
even, cylindrical shape, loosen tension
the
bobbin,
(A) on
If
thread
is
wound
tension
thread
for
neat,
tight
and
uniform.
bobbin
bracket
should be wound with a light tension; otherwise
optimum performance
winder
is
wound
as shown
to
tension bracket.
as shown in Fig, 17b, move the tension
in
Fig.
your
needs, tighten screw (B).
17c,
If
move
the
not,
adjust
When
bracket
the
tension
capacity
the
tension
the
thread
screw (B)
bracket
of
the
bobbin
by
turning
layer
and
move tension
bobbin
should be
(D) might
at
about
break.
80%.
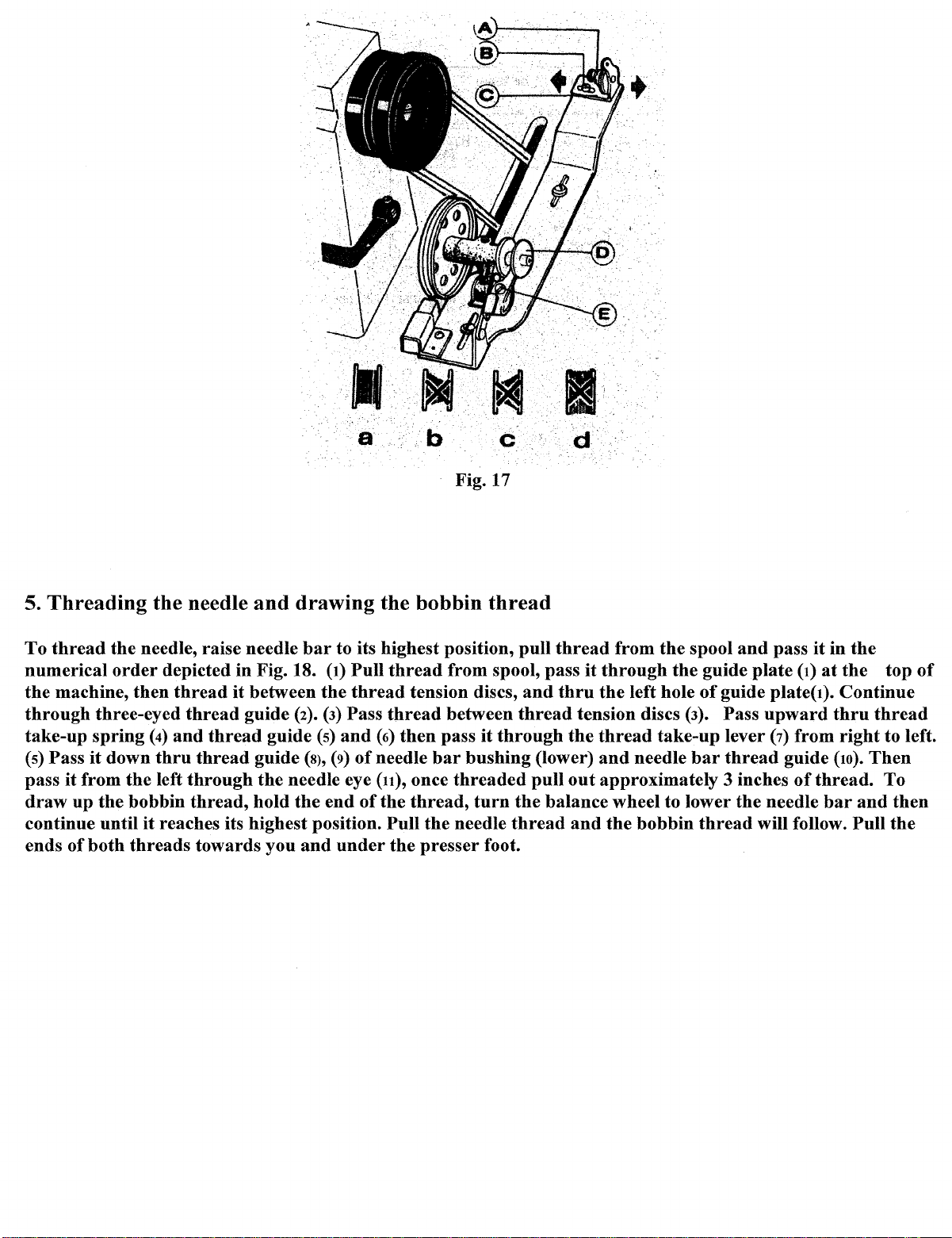
5.
Threading
To
thread
numerical
the
machine,
through
take-up
(s)
Pass
pass
draw
continue until
ends of
the
three-eyed
spring
it
down
it
from
up
the
both
order
the
bobbin
threads
the
needle
needle, raise needle
depicted in Fig. 18.
then
thread
thread
(4)
and
thru
thread
left
through
thread,
it
reaches its highest position.
towards you
and
it
between
guide
thread
hold
drawing
(2).
guide
guide
the
needle eye
the
bar
(s)
(s),
and
b c
Fig. 17
the
bobbin
to its highest position, pull
(1)
Pull
thread
the
(3)
Pass
and
(9)
end
under
thread
of
of
tension discs,
thread
(6)
then
pass
needle
(11),
the
once
thread,
Pull
the
bar
the
presser
thread
from spool, pass
between
it
through
bushing
threaded
turn
needle
thread
foot.
d
thread
and
thru
thread
(lower)
pull
the
balance wheel to lower
from
the
it
through
the
left hole
tension discs
the
thread
and
out
approximately 3 inches
and
the
take-up
needle
bobbin
spool
the
(3).
and
pass
it
in
guide
of
bar
thread
plate
(1)
at
the
guide plate( I). Continue
Pass
upward
lever
(7)
thread
the
needle
will follow.
guide
from
of
thread.
bar
thru
right
(10).
the
thread
Then
and
Pull
top
of
to left.
To
then
the
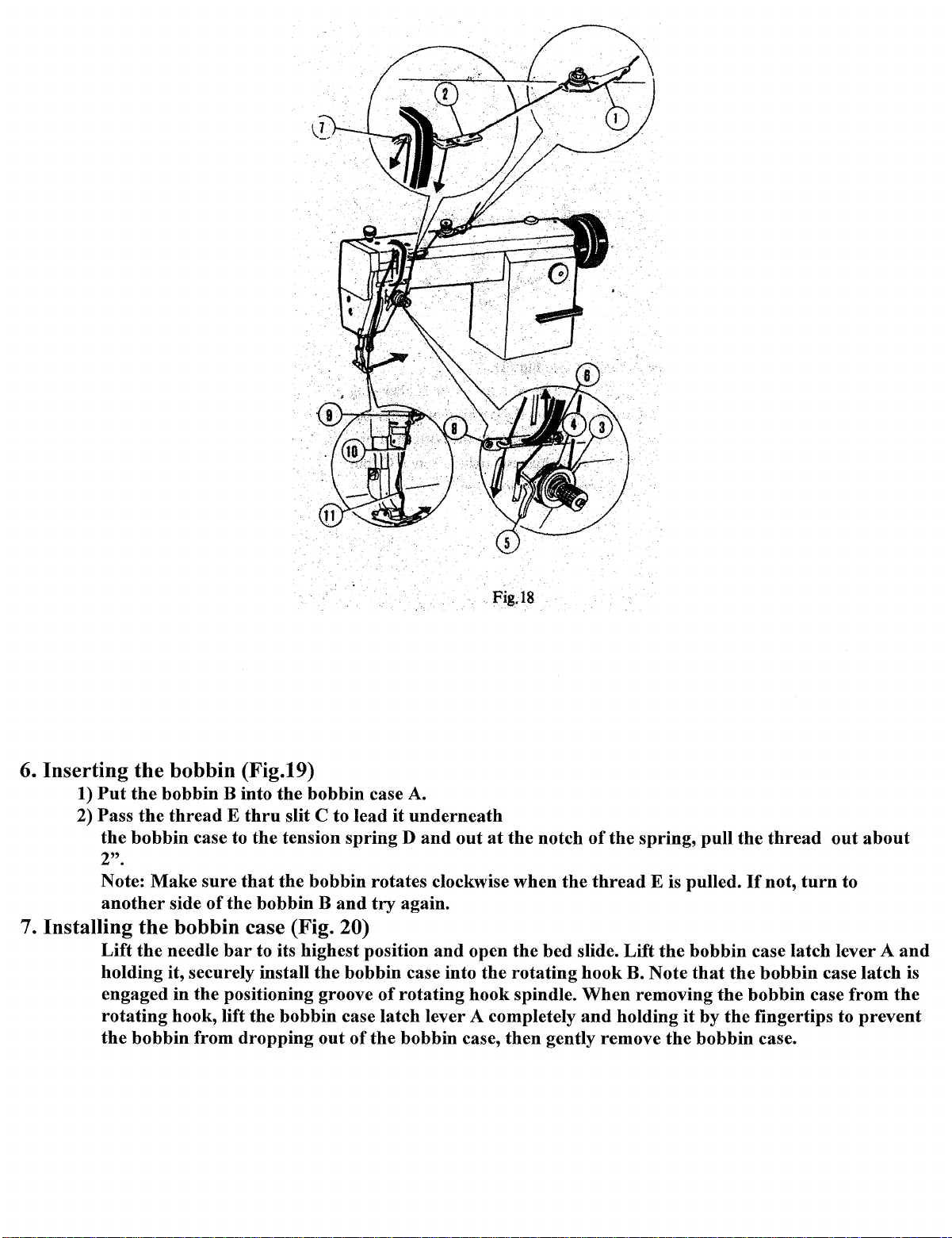
6.
Inserting
1)
Put
2) Pass
the
2".
Note:
another
7. Installing
Lift
holding it, securely install
engaged in
rotating
the
the
bobbin
the
bobbin B into
the
thread E thru
bobbin
the
the
bobbin
case to
Make
side
bobbin
needle
the
hook, lift
from
sure
(Fig.19)
the
bobbin case A.
slit C to lead
the
tension
that
the
bobbin rotates clockwise when
of
the
bobbin B
case (Fig. 20)
bar
to its highest position
the
positioning groove
the
bobbin
dropping
out
Fig.l8
it
underneath
spring D and
and
try
again.
bobbin case into
of
rotating
case latch lever A completely
of
the
bobbin case,
out
and
at
open
the
hook
the
notch
the
bed
rotating
spindle.
then
gently remove
of
the
the
thread
slide. Lift
hook
When
and
holding
spring, pull
E is pulled.
the
bobbin
B. Note
removing
that
it
by
the
bobbin case.
the
thread
If
not,
turn
case latch lever A
the
bobbin
the
bobbin case from
the
fingertips to
out
about
to
and
case latch is
the
prevent
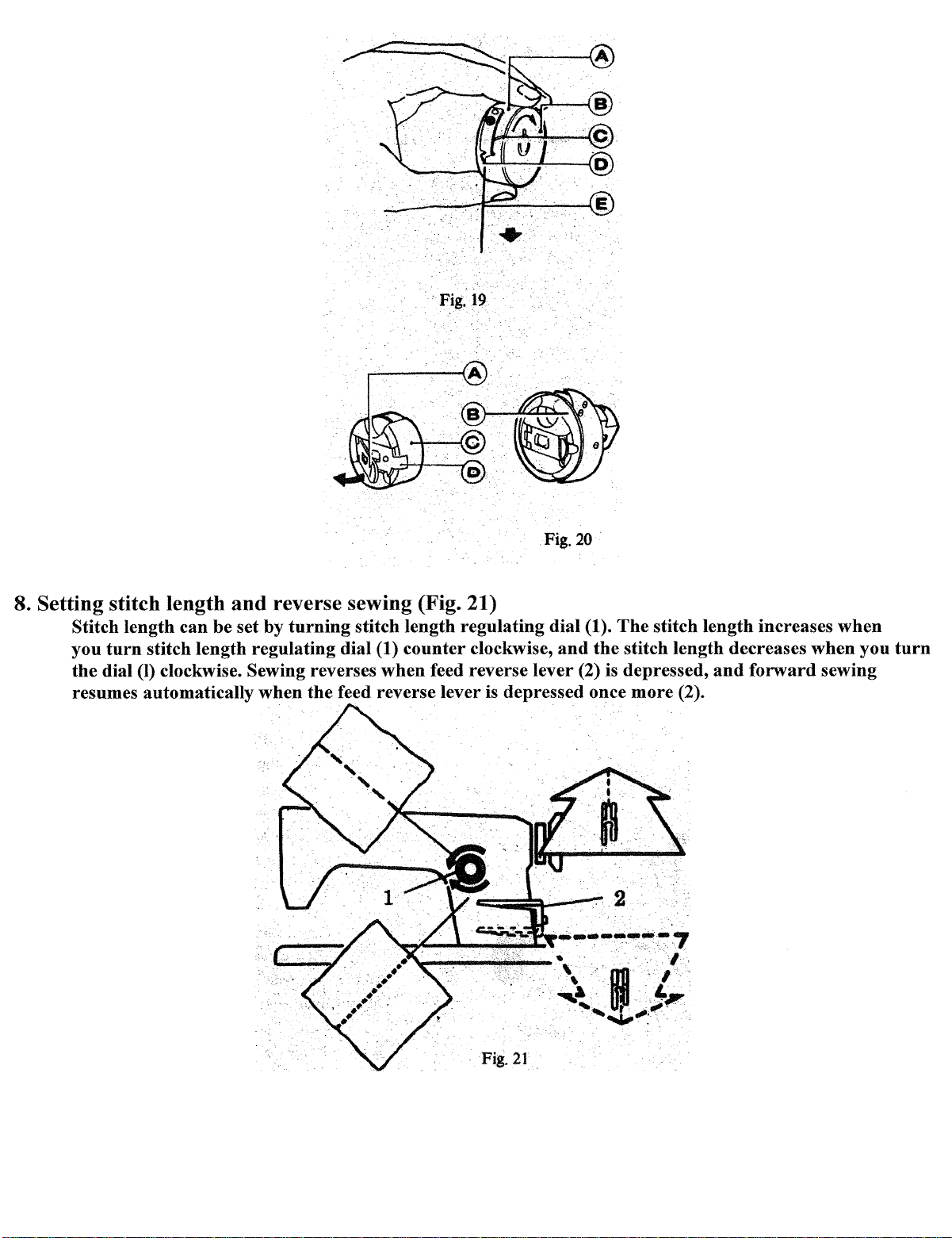
·Fig.
'.
19
Fig. 20
8. Setting stitch length
Stitch length can be set by
you
turn
stitch length regulating dial (1)
the
dial
(I)
clockwise. Sewing reverses
resumes automatically
and
reverse sewing (Fig. 21)
turning
stitch length regulating dial (1).
counter
when
when
the
feed reverse lever
The
stitch length increases
clockwise,
and
the
stitch length decreases
feed reverse lever (2) is depressed,
is
depressed once
more
(2).
2
Fig.
21
.
and
forward
when
when
sewing
you
turn
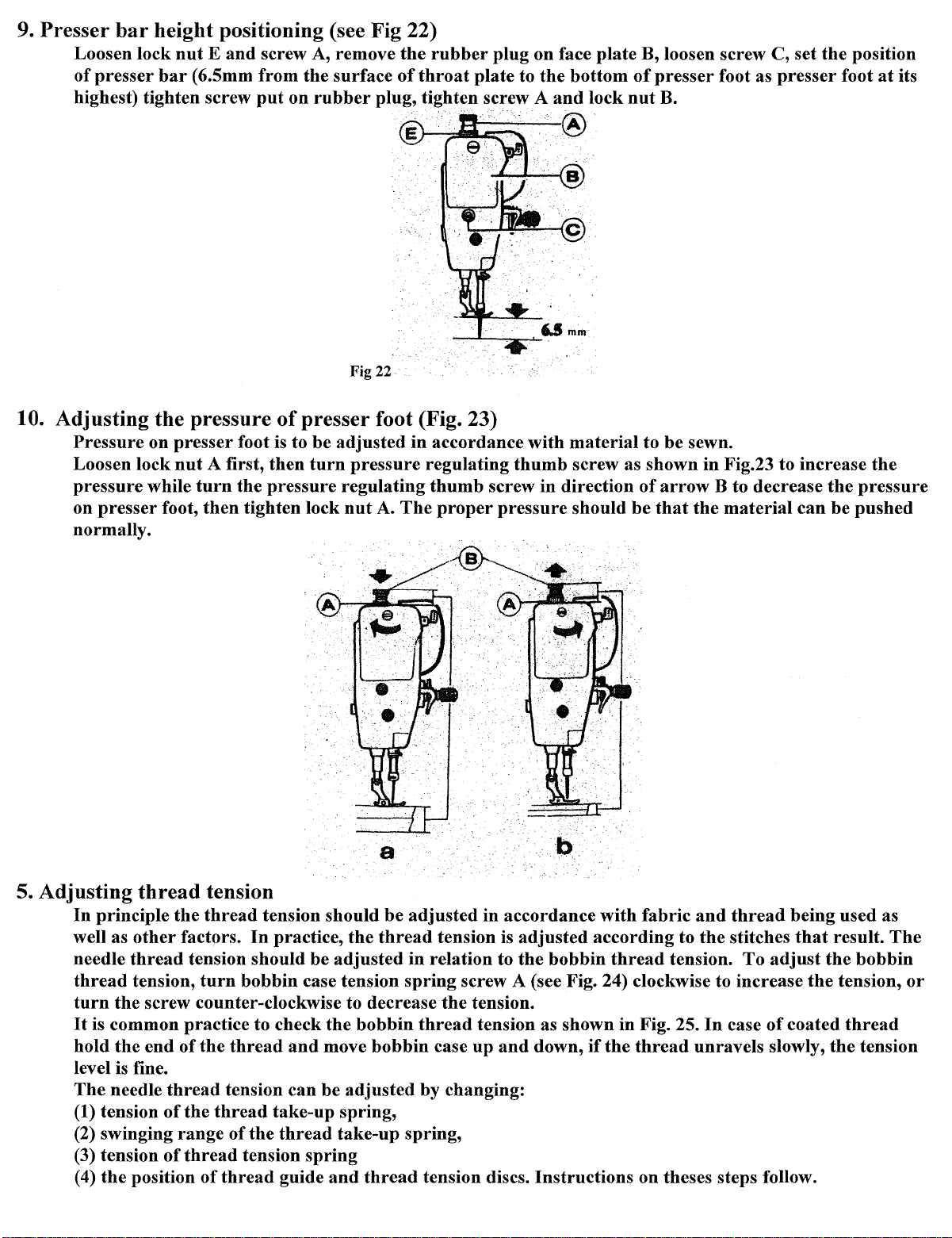
9.
Presser
bar
height positioning (see Fig 22)
Loosen lock
of
presser
highest) tighten screw
nut E and
bar
( 6.5mm
screw A, remove
from
the
surface
put
on
rubber
plug, tighten screw A
Fig22
the
of
rubber
throat
plug
plate to
on face
the
bottom
and
plate
lock
1=1-'-...........__,®
B, loosen screw C, set
of
nut
presser
B.
foot as
presser
the
foot
position
at
its
10. Adjusting
Pressure
Loosen lock
pressure
on
presser
normally.
the
on
presser
nut
while
foot,
pressure
foot is to
A first,
turn
the
then
tighten lock
of
presser
be
then
turn
pressure
foot (Fig. 23)
adjusted
pressure
regulating
nut
A.
The
in accordance
regulating
thumb
proper
thumb
screw in direction
pressure
with
material
screw as shown
should
to
of
be
be
sewn.
arrow
that
in
Fig.23 to increase
B to decrease
the
material
can
the
pressure
be
pushed
the
5. Adjusting
In
well as
needle
thread
turn
It
hold
level is fine.
The
(1) tension
(2) swinging
(3) tension
(4)
thread
principle
other
thread
tension,
the
screw counter-clockwise to decrease
is common practice to check
the
end
needle
the
position
tension
the
thread
factors.
tension should
turn
bobbin
of
the
thread
thread
of
of
the
thread
range
thread
of
tension
of
tension
thread
tension should
In
practice,
be
case tension
and
can
take-up
the
thread
spring
guide
the
adjusted
the
bobbin
move
be
bobbin
adjusted
spring,
take-up
and
thread
be
adjusted
thread
in
relation to
spring
thread
by
spring,
tension discs.
in accordance
tension is
screw A (see Fig. 24) clockwise to increase
the
case
changing:
adjusted
the
tension.
tension as shown
up
and
down,
Instructions
according
bobbin
if
with
fabric
thread
in
Fig. 25.
the
thread
on theses steps follow.
and
to
the
tension.
In
case
unravels slowly,
thread
stitches
To
adjust
of
being used as
that
result.
the
bobbin
the
tension,
coated
thread
the
tension
The
or