
Leistung bei 100% ED:
350 A bei Mischgas
390 A bei CO
Draht Ø 0,8-1,2
Ausgerüstet für Draht Ø 1,2
Power at 100 % duty cycle
350 A with mixed gas
390 A with CO2
Wire dia. 0.8 - 1.2 mm
Equipped for 1.2 mm dia.
Facteur de marche à 100 %
350 A avec gaz mixte
390 A avec CO2
Diamètre de fil 0,8 à 1,2 mm
Equipé pour diamètre 1,2 mm
2
MHW 350 SZ
ERSATZTEILLISTE
SPARE PARTS LIST
LISTE DES PIECES DE RECHANGE
FÜR KÜNFTIGE VERWENDUNG AUFBEWAHREN
PLEASE KEEP SAFELY FOR FUTURE REFERENCE
A GARDER POUR FUTURE UTILISATION
MHW 350 SZ/12.00
CARL CLOOS
Schweißtechnik GmbH
Industriestr. • 35708 Haiger
Tel. +49 2773/85-0
Fax. +49 2773/85-275
http://www.cloos.de
info@cloos.de
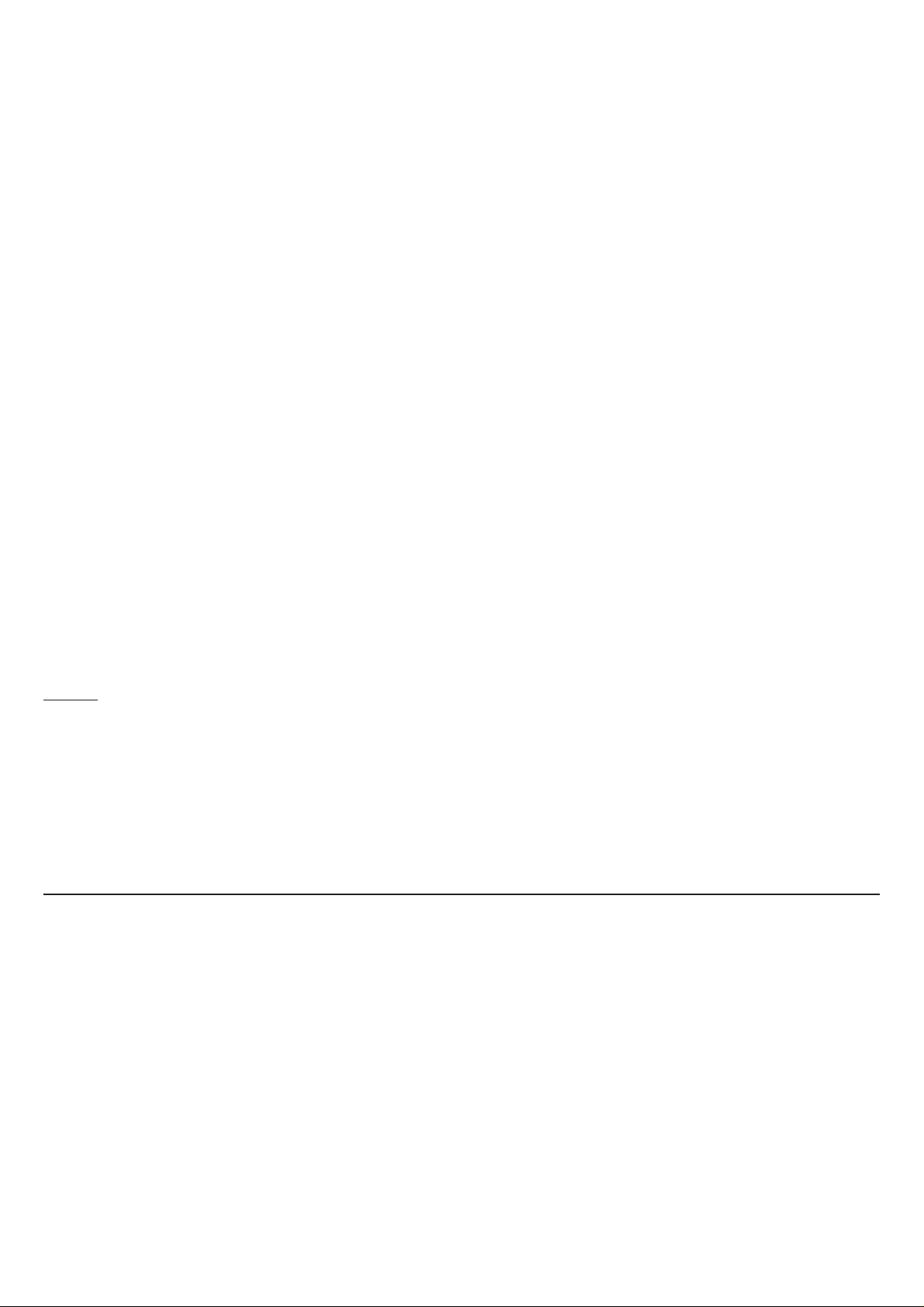
Betriebsanleitung MIG/MAG-Schweißbrenner
EN 50 078
* Schadhafte, deformierte oder verschlissene Teile auswechseln bzw.
zur Reparatur einschicken.
Die Hand- und Maschinenschweißbrenner dieser Produktreihe sind
ausschließlich zum Schutzgasschweißen mit inerten bzw. aktiven Gasen
universell und in allen gängigen Schweißpositionen einsetzbar.
Standardausführung ist der Hand- bzw. Maschinengriff mit Steuereinrichtungen für max. 42V und 0,1 bis 1A. Schlauchpaketlängen von 3,4
oder 5m für Hand- sowie 1,2, 1,5, 2 und 3m für Maschinenbrenner.
Ausrüstvarianten wie z.B. Anschlüsse, Handgriffe, Verschleißteile sowie
sonstiges Zubehör entnehmen Sie bitte den aktuellen Bestellunterlagen.
Je nach Ausführung ist der MIG/MAG-Schweißbrenner gas- oder flüssiggekühlt.
Für die flüssiggekühlte Ausführung ist ein Kühlaggregat erforderlich.
Inbetriebnahme
Schlauchpaket ausrüsten:
Führungsspirale oder Kunststoffseele bei gerade ausgelegtem Schlauchpaket vom Zentralanschluß (Anschlußstück) einschieben und mit dem
Spannkonus klemmen.
Brennerhals ausrüsten:
1. Gasverteiler bzw. Spritzerschutz handfest aufschrauben.
2. Stromdüse mit Steckschlüssel anziehen.
3. Gasdüse mit Drehbewegung aufstecken.
Brenner anschließen:
Der maschinenseitige Anschluß hat serienmäßig bei flüssiggekühlten
Hand- und Maschinenbrennern „SZ“, bei gasgekühlten Brennern „Z“ Anschluß.
Kühlmittelvorlauf anschließen:
Der blau gekennzeichnete Schlauch ist der Vorlauf und darf am Kühlaggregat mit dem Wasserrücklauf nicht vertauscht werden. Bei Erstinbetriebnahme bzw. nach jedem Schlauchpaketwechsel ist der Wasserumlauf zu überprüfen.
Kühlmittelrücklauf anschließen
Schutzgase:
Das Schutzgas wird in der Regel aus Stahlflaschen oder Ringleitung
entnommen und die Gasmenge am Druckminderer eingestellt. Drossel
für manuellen und maschinellen Betrieb Ø 0,6. Drossel für Roboterbetrieb
Ø 0,85.
Zum MIG/MAG-Schweißen verwendbare Schutzgase sind:
Reinargon, CO2, Gemische aus Argon und CO2 bzw. Argon, CO2 und O2.
Verboten sind brennbare Gase oder Gase, die chemische Reaktionen
auslösen. Diese sind z.B.: Acetylen, Propan, reiner Wasserstoff, reiner
Sauerstoff.
Brenner mit Spannungsklasse L (bis 113V Scheitelwert)
Bedien- und Wartungshinweise
Schlauchpaket:
* Vor dem Anschließen an das Vorschubgerät kontrollieren, daß
entsprechend Drahtdurchmesser und -art die richtige Spirale oder
Seele eingesetzt ist.
* Den Drahtführungsschlauch bei jedem Drahtspulenwechsel mit
Preßluft durchblasen.
* Verschraubung auf festen Sitz überprüfen.
Brenner:
* Ausrüstteile daraufhin kontrollieren, daß entsprechend dem Draht-
durchmesser und der Drahtart die richtige Stromdüse eingesetzt ist.
* Bei jedem Drahtwechsel darauf achten, daß der Drahtanfang gratfrei
ist.
* Den Gasdüseninnenraum von Schweißspritzern reinigen und mit
Original-Cloos-Antihaftmittel einsprühen.
* Bei flüssiggekühlten Brennerausführungen die Funktion des Kühl-
gerätes sicherstellen.
Sicherheitsmaßnahmen
Der Umgang mit dem Schweißbrenner ist gefahrlos, wenn die einschlägigen Sicherheitsvorschriften beachtet und eingehalten werden z.B.:
* Die Inbetriebnahme ist nur Personen vorbehalten, die über entspre-
chende Kenntnisse im Umgang mit Lichtbogenschweißgeräten
verfügen.
* Lichtbogenschweißen kann Auge, Haut und Gehör schädigen!
Deshalb immer die vorgeschriebene Schutzkleidung, Augen- und
Gehörschutz gemäß UVV 26.0, VBG 15 tragen.
* Die angegebenen Belastungsdaten sind maximale Grenzwerte.
Überlastungen führen zwangsläufig zu Brennerzerstörung.
* Zum Verschleißteilewechsel immer die Stromquelle ausschalten.
* Die Bedienungsanleitung der einzelnen schweißtechnischen Kompo-
nenten, wie z.B. Stromquelle, Drahtvorschub- und Kühlaggregat sind
zu beachten.
* Den Brennertaster erst dann bestätigen, wenn alle Voraussetzungen
zum gefahrlosen Schweißen erfüllt sind.
* Schlauchpaket niemals über scharfe Kanten ziehen, im Spritzer-
bereich oder auf heißen Werkstücken ablegen.
* Unbeteiligte Personen durch Vorhänge und Schutzwände gegen
optische Strahlung und Blendegefahr schützen.
* Die Handhabung von Gasflaschen ist den Anweisungen der Gaseher-
steller und der Druckgasverordnung zu entnehmen.
* Werkstücke, die mit chlorierten Lösungsmittel entfettet wurden,
müssen vor dem Schweißen mit klarem Wasser abgespritzt werden
sonst besteht die Gefahr der Phosgengasbildung. Aus dem gleichen
Grund dürfen keine chlorhaltigen Entfettungsbäder in der Nähe des
Schweißplatzes aufgestellt sein.
* Alle Metalldämpfe sind schädlich! Es wird besonders vor Blei, Nickel,
Chrom, Cadminum, Kupfer, Zink und Beryllium gewarnt. Durch
Belüftung oder Absaugung ist gegebenenfalls dafür zu sorgen, daß die
MAK-Werte nicht überschritten werden (MAK = Maximale Arbeitsplatz-
konzentration gesundheitsschädlicher Arbeitsstoffe).
* Beobachten Sie die Schweißstelle und die Umgebung auch nach
Beendigung der Schweißung. Brände können durch Schwelung auch
noch später entstehen.
Gewährleistung
Dieser MIG/MAG-Schweißbrenner ist ein Original Cloos-Erzeugnis. Die
Cloos Schweißtechnik GmbH garantiert eine fehlerfreie Herstellung und
übernimmt für diesen Schweißbrenner bei Auslieferung eine werkseitige
Fertigungs- und Funktionsgarantie entsprechend dem Stand der Technik
und der geltenden Vorschriften. Gewährleistungen können nur für
Fertigungsmängel, nicht aber für Schäden, die auf natürliche Abnutzung,
Überlastung oder unsachgemäße Behandlung zurückzuführen sind,
gegeben werden. Verschleißteile fallen generell nicht unter die Gewährleistung. Jeder Schweißbrenner darf nur mit Original-Cloos-Ersatzteilen
betrieben werden.
Störungsursache
Störung Mögliche Ursachen
Kein Lichtbogen - Stromzuleitung zu Werkstück oder Brenner unterbrochen
Lichtbogen zwischen Gasdüse und Werkstück - Brückenbildung im Gasdüseninnenraum durch Schweißspritzer
Brennerkörper oder Stromzuleitung überhitzt - Kühlmitteldurchfluß nicht ausreichend
Schweißdraht mit Stromdüse verschmolzen - Drahtvorschub setzt zu spät ein
Unregelmäßiger Drahtvorschub - Anpreßkraft der Andruckrolle zu gering
- Stromquelle oder Steuerung defekt
- Steuerleitung unterbrochen
- Schaltschutz in der Stromquelle wird nicht aktiviert
- Schweißstrom zu hoch
- Kühlmittelschlauch oder flüssiggekühltes Stromkabel verengt oder
verschlossen
- Stromdüse nicht richtig angezogen
- Draht blockiert im Drahtführungsschlauch infolge starker Verschmutzung
oder zu starker Krümmung
- Vorschubgeschwindigkeit zu niedrig
- Stromdüsenabstand zum Werkstück zu groß/ zu klein
- Störungen im Drahtführungsschlauch
- Falsche Führungsspirale oder -seele
- Störungen in der Steuerung
- Zu stark abgenutzte oder falsch gewählte Vorschubrollen

Operating instructions for MIG/MAG welding torches
EN 50 078
The manual and machine welding torches in this product series are
exclusively suitable for use with inert or active gases, universally and in
all common welding positions.
The standard design comprises: handle with controlling devices for max.
42 V and 0.1 to 1 A, cable assembly lengths of 3 m, 4 m or 5 m for
manual torches and 1.2 , 1.5 , 2 and 3 m for machine torches.
Please see the current order documents (sales documents) for various
fittings such as connections, handles, wear parts and other accessories.
MIG/MAG welding torches may be gas-cooled or water-cooled.
Water-cooled torches require a cooling radiator.
Commissioning
Prepare cable assembly:
The guide liner or plastic liner is pushed through the straight cable
assembly from the central connection (connection piece) and is clamped
with the clamping cone.
Prepare torch neck:
1. Manually screw on the gas distributor or spatter protection.
2. Use a spanner to tighten the current tip.
3. Fasten the gas shroud with a rotary motion (movement).
Connect torch:
The standard connection on the machine side is a „SZ“ connection for
water-cooled manual and machine torches and a „Z“ connection for gascooled torches.
Connect cooling liquid advance:
The water advance hose is marked blue and must not be mixed up with
the water return hose on the cooler. The water circulation must be
checked during the first commissioning and after each change of the
cable assembly.
Connect cooling liquid return.
Shielding gases:
The shielding gas is taken from steel bottles or a closed circular pipeline.
The gas quantity is set on the pressure reducing valve. Choke diameter
for manual and automatic operation is 0.6 and for robot operation 0.85.
The following gases are used for MIG/MAG welding:
Pure Argon, CO2, mixtures of Argon and CO2 or Argon, CO2 and O2.
Flammable gases or gases which induce a chemical reaction, such as
Acetylene, Propane, pure Hydrogen, pure Oxygen are prohibited.
Torch of the voltage class L (up to a peak value of 113V)
Operating and maintenance instructions
Cable assembly:
* Prior to connection to the wire feed unit make sure that the correct
liner is used in accordance to the wire type and diameter.
* Compressed air should always be blown through the wire guide hose
when the wire coil has been exchanged.
* Make sure that the screwed connections are correctly tightened.
* Damaged, deformed or worn parts have to be exchanged or returned
for repair.
Torch:
* Make sure that the correct current tip is used with regard to the wire
diameter and type of wire.
* When changing the wire coil it is important that the wire beginning
is without burr.
* Remove the weld spatters from the interior of the gas shroud and
spray with original Cloos torch spray.
* When water-cooled torches are used the function of the cooler
must be guaranteed.
Safety precautions
The use of the welding torches is safe when the common safety
regulations are kept:
* Commissioning is reserved to qualified persons who are familiar with
the use of arc welding machines.
* Arc welding may be harmful for eyes, skin and ears ! Protective
clothing, eye and ear protection according to UVV 26.0, VBG 15 rules
should be worn.
* The given load data are maximum limit values. Overload will
inevitably damage the torch.
* The power source must always be switched off when wear parts
are exchanged.
* The operating instructions for the individual welding components
such as power source, wire feed unit and cooler must be
adhered to.
* The torch trigger should only be pressed when all conditions for
a safe welding are fulfilled.
* Never pull the cable assembly over feather edges or deposit it within
the range of spatters or on hot workpieces.
* Protect other persons by curtains and protective walls against optical
rays and the danger of glare.
* The instructions of the gas manufacturers and the high-pressure gas
rules are important for handling the gas bottles (cyliders).
* Workpieces which have been degreased with a chlorinated solvent
must be washed down with clear water before welding to avoid the
danger of phosgen gas formation. For the same reason chloric
degreasing bathes are not allowed in the proximity of the welding
location.
* All metal vapours are toxic! Be careful with lead, nickle, chrome,
cadmium, copper, zinc, berillium. If necessary a ventilation or
aspiration must be used to avoid that the MAK values are exceeded
(MAK „ maximum concentration of harmful working materials on the
work place).
* Please observe the weld area and its surroundings when welding
has finished. Fire may break out later due to smoldering.
Warranty
This MIG/MAG welding torch is an original Cloos product. Cloos
Schweißtechnik GmbH guarantee for a faultless production and function
according to the state of art and the existing provisions. Guarantee can
only be claimed for defective material but not for damages due to normal
wear, overload or inexpert handling. There is no warranty against wear
parts. Original Cloos spare parts must be used only for each welding
torch.
Problems during operation
Faults Possible causes
No arc - Current supply to the workpiece or torch is interrupted
Arc between gas shroud and workpiece - Bridge formation inside the gas shroud due to weld spatters
Overheated torch body or supply lead - Insufficient flow of cooling liquid
Welding wire melted with current tip - Wire feed starts too late
Irregular wire feed - Too low pressure of pinch roller
- Faulty power source or control
- Control lead interrupted
- Switching protection in the power source is not activated
- Welding current too high
- Cooling liquid hose or water-cooled current cable too narrow or
closed
- Current tip is not correctly tightened
- Wire is jammed in the wire guide hose due to severe contamination
or too strong bending
- Wire feed speed is too low
- Current tip distance to the workpiece is too large/too small
- Faults in the wire guide hose
- Wrong guide liner or liner (core)
- Problems in the control
- Wrong wire feed rollers or rollers too severely worn